Zinc Coating Process: Techniques and Applications
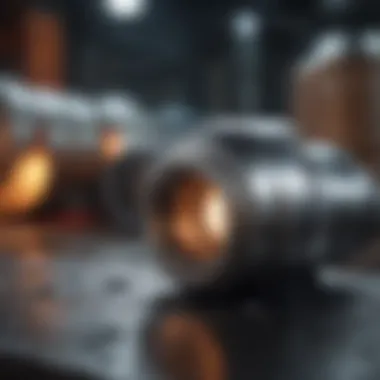
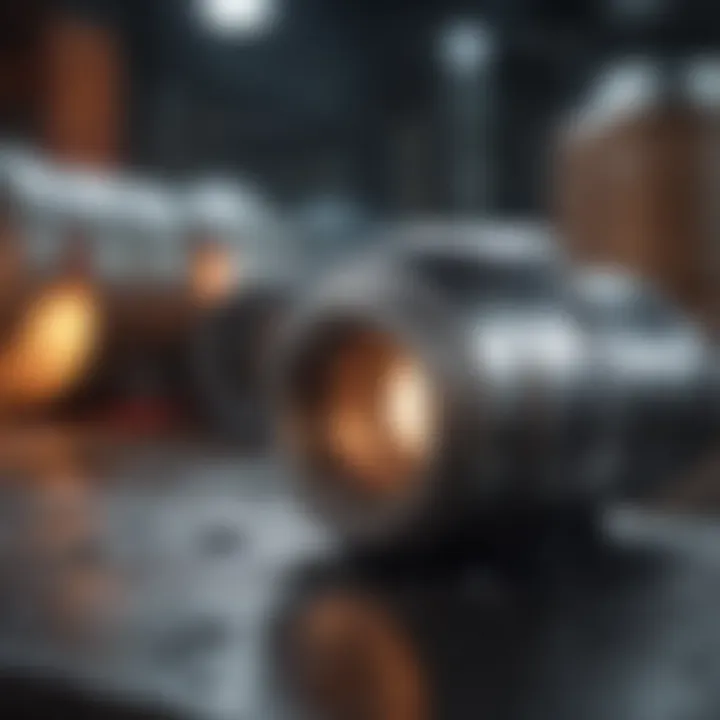
Intro
Zinc coating is a pivotal process in metal protection, primarily aimed at preventing corrosion. When metals are exposed to the open air and moisture, they are prone to rust and deterioration. Therefore, utilizing zinc as a sacrificial barrier enhances the longevity of various metal products, ensuring they withstand the test of time and environmental challenges. This article seeks to explore the intricacies of the zinc coating process, highlighting the techniques, applications, and important considerations that surround this essential method.
Understanding the basics of zinc coating is crucial for professionals across diverse industries, including construction, automotive, and electronics. The insights presented will cover not only the technical aspects, such as methodologies and performance factors, but also the innovations shaping the future of this practice. As the demand for corrosion-resistant materials rises, so does the innovation in the techniques used for zinc coating.
Key Findings
Major results and insights into the zinc coating process are centered on its effectiveness, quality, and areas of application.
- Effectiveness: Zinc coatings are proven to significantly enhance the corrosion resistance of metal substrates due to their electrochemical properties.
- Quality: The performance of zinc-coated products largely depends on the thickness and uniformity of the coating applied.
- Applications: Industries that rely on zinc coatings include construction (for steel beams and connectors), automotive (for parts exposed to harsh environments), and even household products (like plumbing fixtures).
Zinc coatings not only protect metal surfaces but also enhance aesthetic appeal, providing a finish that can withstand environmental stresses.
Discussion of Findings
The findings indicate a clear trend toward the increasing use of zinc coatings in more industries, largely driven by both environmental regulations and a growing understanding of their benefits. Recent advancements include the development of more efficient application processes and the introduction of environmentally friendly solutions.
Methodology
To thoroughly understand the zinc coating process and its implications, a combination of research design and data collection methods is essential.
Research Design
The approach taken here involves both qualitative and quantitative analyses of existing literature, case studies, and industry reports. This ensures a rounded view of the current landscape, challenges, and future directions of zinc coating technologies.
Data Collection Methods
Various methods were employed to gather relevant data:
- Literature Reviews: Examined academic papers and industry publications to gather insights on the techniques and performance.
- Interviews with Experts: Engaged with professionals from related industries to acquire firsthand knowledge about practical applications and innovations.
- Field Studies: Observations were made on production processes and outcomes in real-world settings to assess efficiency and effectiveness.
Through this investigation, the article aims to provide a comprehensive guide that not only highlights key aspects of the zinc coating process but also stimulates thought-provoking discussions on its implications and future developments.
Understanding Zinc Coating
Zinc coating is a pivotal process in the preservation and longevity of metallic structures, acting as a protective barrier against the ravages of corrosion. Its significance extends beyond mere aesthetics; it serves a crucial role in ensuring the durability and reliability of materials utilized across various industries. Understanding zinc coating involves a deep dive into both its functional attributes and practical applications.
The primary benefit of zinc coating lies in its ability to prevent rust or corrosion on iron and steel surfaces. Corrosion, if left unchecked, can lead to catastrophic failures in structures such as bridges, buildings, and machinery. By applying a layer of zinc, manufacturers can extend the life of these materials significantly. Moreover, the zinc layer acts as a sacrificial element, meaning that it will corrode preferentially over the underlying metal, thus protecting it from exposure to harsh environmental factors.
To grasp the importance of zinc coating fully, one must also consider various techniques employed in its application. Each method carries distinct advantages and challenges, which directly affect not only the performance but also the cost-effectiveness of the treatment. When one looks at surface preparations, application methods, and post-treatment processes, a clear picture emerges on how vital each step is in achieving optimal results and ensuring longevity.
In studying zinc coating, it’s crucial to balance economic considerations with performance outcomes. Costs can vary widely depending on the chosen technique, and understanding the trade-offs can lead to better decision-making. This is particularly true in industrial contexts where large volumes of materials are coated.
What is Zinc Coating?
Zinc coating involves the deposition of a layer of zinc onto a metal surface. This coating serves several purposes, most notably corrosion resistance, which enhances the lifespan of the treated metal. Such coating can be achieved through various methods such as hot-dip galvanizing, electroplating, and even painting with zinc-rich formulations.
Zinc contains natural properties that allow it to chemically protect bare metal beneath the coating. Even during the coating process, if the zinc layer gets scratched, it can still protect the base metal. That’s because zinc oxidizes much slower than iron or steel, keeping the underlying structure from showing signs of rust for a much longer time.
The thickness and uniformity of the zinc layer are important factors that influence its effectiveness. Generally, a thicker coating provides better protection, although it may also increase the overall weight and cost. Thus, companies must consider the balance between protection and operational feasibility.
Historical Context
Historically, the use of zinc as a protective measure dates back to ancient times, but its application in coating metals became prevalent in the 19th century. The first known usage of zinc to prevent corrosion occurred in Asia, where zinc ores were smelted down to coat other metals. The galvanizing process was formally developed in France in the 1830s and later gained traction globally.
In the early days, zinc coatings were primarily utilized in marine environments and in agricultural equipment, but as industries grew, the applications expanded significantly. Today, zinc coating is standard in construction, automotive manufacturing, and more, owing to its cost-effectiveness and reliability.
The historical evolution of zinc coating showcases not only its increasing importance but also innovations in its application methods and formulations, continuously adapting to meet the demands of modern engineering challenges. These advancements not only improve the quality of the coating but also align with growing sustainability practices, adapting to meet the needs of a changing world.
Importance of Zinc Coating
Zinc coating plays a significant role in the longevity and durability of metal structures. This section delves into the crucial aspects that underline the necessity of zinc coatings, especially in environments where corrosion presents a formidable challenge. With their myriad benefits, these coatings can extend the lifespan of materials, which is undoubtedly vital for sectors ranging from construction to manufacturing.
Corrosion Resistance
One of the standout features of zinc coatings is their ability to resist corrosion. When exposed to moisture and oxygen, metals tend to oxidize, leading to rust and degradation. This is where zinc comes into play; it creates a protective barrier that acts as a sacrificial anode. Essentially, if the coating gets compromised, the zinc continues to dissolve, thereby protecting the underlying metal from corrosion. This phenomenon illustrates why zinc-coated materials are particularly valuable in harsh conditions, such as coastal environments where salt and humidity can be particularly aggressive.
Moreover, the application of zinc not only protects the metal from rust but also slows down the rate of corrosion. Studies suggest that galvanized steel can remain intact for many years, far surpassing uncoated metal products. For example, a freshly galvanized piece of steel may retain its integrity and aesthetic appeal for over 50 years, proving the effectiveness of this coating in preventing the adverse effects of rust and corrosion.
Longevity of Metal Structures
When we discuss the longevity of metal structures, zinc coating emerged as a key player in ensuring that these investments do not decay prematurely. Metals subjected to harsh environments face significant wear and tear, which can lead to structural failures. By applying a layer of zinc, not only is the metal shielded, but its overall lifespan is vastly enhanced.
Consider the case of bridges and other civil infrastructure. These structures often encounter dynamic loads and environmental stressors. Incorporating zinc coatings can dramatically extend their service life, saving costs related to repairs and replacements.
“Investing in zinc coating is like adding an insurance policy to your structural assets.”
Furthermore, the benefits extend beyond mere protection. A well-maintained zinc-coated structure often requires less frequent maintenance, translating to reduced operational costs in the long run. This is particularly pertinent for industries where downtime can result in significant financial losses.
In summary, zinc coating emerges as a vital consideration for anyone involved in the lifecycle of metal products. Its ability to combat corrosion and elevate the longevity of structures is a testament to its importance in modern engineering and architectural practices.
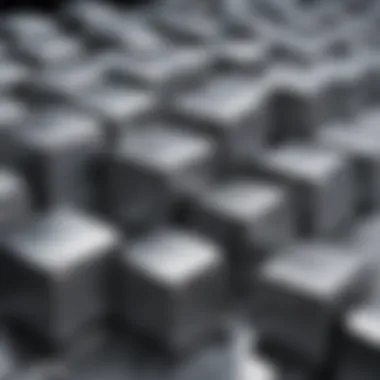
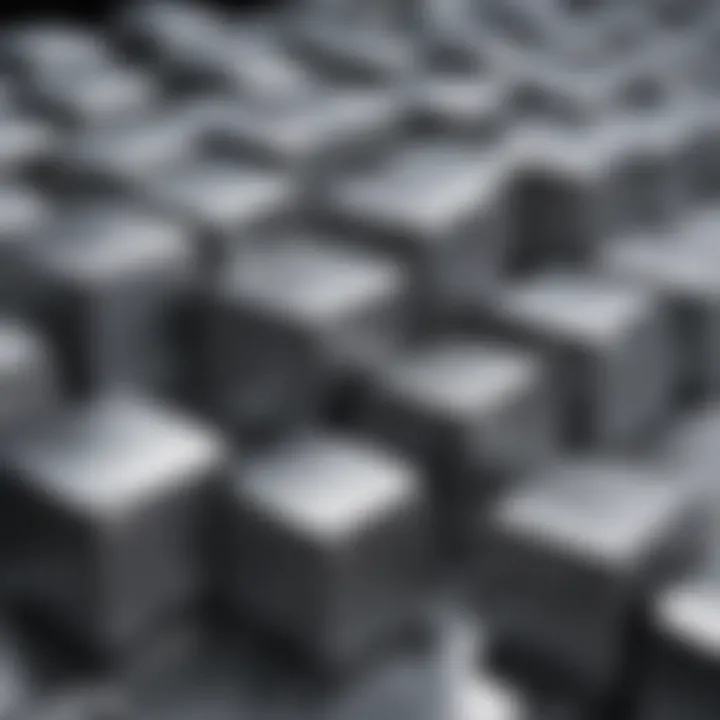
Types of Zinc Coatings
Understanding the various types of zinc coatings is essential for anyone vested in metal protection against corrosion. The choice of coating influences not just the longevity of metal structures, but also determines how well they can resist challenging environmental conditions. Each method has its own set of techniques, applications, and factors to weigh before implementation.
Hot-Dip Galvanizing
Process Overview
Hot-dip galvanizing involves immersing clean steel in molten zinc to create a metallurgically bonded coating. This process is notable for its thorough protection, as it envelops the steel completely. The high temperature promotes a reaction between the zinc and the iron in the steel, forming zinc-iron alloy layers that improve adhesion. Considering its robustness, it has carved a space as a popular choice in infrastructure projects, especially when long-term protection is a priority.
The feature that stands out in this method is its high resistance to corrosion, even in severe environments. However, the thickness of the coating can also vary, which might be seen as a disadvantage in specific applications, as overly thick coatings can lead to issues like flaking.
Advantages
The durability of hot-dip galvanizing is second to none. This method provides a long-lasting barrier that can withstand physical damage as well as corrosive agents. Its ability to heal minor scratches is another characteristic that makes it favorable for outdoor applications, where exposure is constant.
Moreover, the process is relatively cost-effective when looking at the total lifecycle of the coated metal. By offering such permanence, the need for frequent re-coating is significantly minimized, making it an excellent choice for budget-conscious projects.
Limitations
Nevertheless, there are some trade-offs to consider. For one, hot-dip galvanizing can be less aesthetically pleasing compared to other coatings, which might come in various colors or finishes. Additionally, pre-treatment of metal surfaces is critical, as any contamination can affect the final coating.
Another point worth mentioning is that not all metals can be galvanized. Some aluminum or stainless steel materials don't react well with zinc, limiting the versatility of this method.
Electroplating
Process Overview
Electroplating is a method where a layer of zinc is deposited onto a metal substrate through electrochemical processes. This technique tends to produce thinner coatings compared to hot-dip galvanizing, allowing for more precise applications. It is widely used in industries where appearance and coating uniformity are paramount, such as in automotive parts and electronic components.
The fine control this method provides ensures that even the most intricate shapes can be coated evenly, which is a key element in meeting industry standards for aesthetic finish and corrosion resistance.
Advantages
One of the standout advantages of electroplating is its capability in providing a thin, uniform layer of zinc without adding excessive weight to the substrate. This feature makes it particularly suitable for small or intricate components that need surface protection but no significant bulk.
It is also ecologically more favorable, as the process can yield less waste. For manufacturers aiming for sustainable practices, eligible electroplating solutions can benefit both performance and environmental impact.
Limitations
However, the thinner layer does impart some limitations, especially in environments where heavy exposure to moisture and chemicals is expected. The protection level might not be sufficient in harsher conditions, leading to the possibility of faster degradation compared to thicker coatings.
Moreover, the process requires precise operating conditions, or else the coating may not adhere effectively, leading to flaking or peeling, which are seen as significant disadvantages in quality control.
Zinc Rich Paints
Zinc rich paints are another form of zinc coating but differ distinctly from the aforementioned methods. This technique involves applying a paint that contains a significant concentration of zinc dust, which provides galvanic protection to the underlying metal. This paint is often used as a primary rather than secondary protective coat.
These paints offer versatility in application methods, ranging from spray to brush, and are used widely in situations where traditional coating methods may be impractical. While they can be employed in a variety of settings, they are particularly favored in maintenance and repair work, offering a quick solution without long downtimes.
However, it is important to note that zinc rich paints often require proper surface preparation and may necessitate reapplication every few years, depending on environmental conditions. Though not as robust as galvanizing methods, they serve as a practical solution for budget-limited projects that still demand some level of corrosion resistance.
In summary, the choice of zinc coating method is crucial and should align with specific project requirements and environmental conditions. Employing the right type can substantially improve the longevity and durability of metal structures by creating a stronger defense against corrosive elements.
The Zinc Coating Process
The zinc coating process holds pivotal importance in shielding metals from the relentless grip of corrosion. This method essentially lays down a protective barrier, ensuring that various metal structures can withstand the test of time and natural elements. Through this section, we will delve into specific elements that comprise the zinc coating process, including surface preparation, methods of application, and post-treatment processes. Each of these elements plays a critical role in determining not only the effectiveness of the coating but also its longevity and performance under different conditions.
Surface Preparation
Surface preparation acts as the first line of defense in the zinc coating process. It can determine how well the coating adheres to the substrate, which is crucial for achieving optimal performance.
Cleaning Techniques
Cleaning techniques are vital for ensuring that metals are free from contaminants such as rust, dirt, or oils before applying the zinc layer. This ensures a clean surface for the coating to bond effectively. Key methods include sandblasting, acid pickling, and mechanical abrasion.
- Sandblasting: This involves shooting abrasives at high speeds to remove oxide layers and other impurities. This method is particularly effective because it provides a rough surface, allowing for better adhesion of zinc.
- Acid Pickling: This process uses acidic solutions to dissolve surface contaminants. It is fast and can clean the surface thoroughly, but one must be cautious with the substrate type since some materials could be damaged by the acid.
In short, effective cleaning techniques boost the adhesion of zinc, making the overall coating process more reliable.
Substrate Material Considerations
The type of substrate material significantly impacts how the zinc coating performs. Different metals respond differently to zinc application, thus choosing the right substrate can be a game-changer. For instance, steel and iron are commonly coated, but not all grades behave alike.
- Corrosion Resistance: Zinc has a sacrificial property, which means it protects the underlying metal even if the coating has been scratched. This makes steels like hot-rolled or cold-rolled exceptionally good candidates.
- Unique Features: Some substrates may require pre-treatment to enhance adhesion, which can complicate the process. It’s vital to assess the properties of the substrate before proceeding with the coating to avoid complications down the line.
Application Methods
Application methods are the crux of the zinc coating process. How zinc is applied can range from large-scale industrial techniques to small-scale applications, all of which contribute to the final outcome.
Methods of Application
Several application methods exist, including hot-dip galvanizing, electroplating, and spray techniques. Each method comes with its approach and suitability.
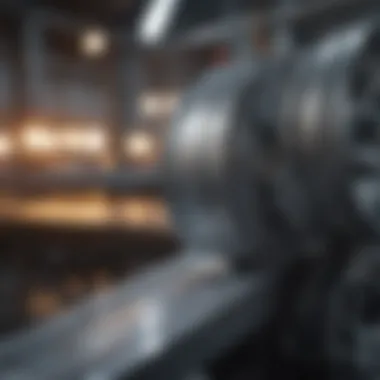
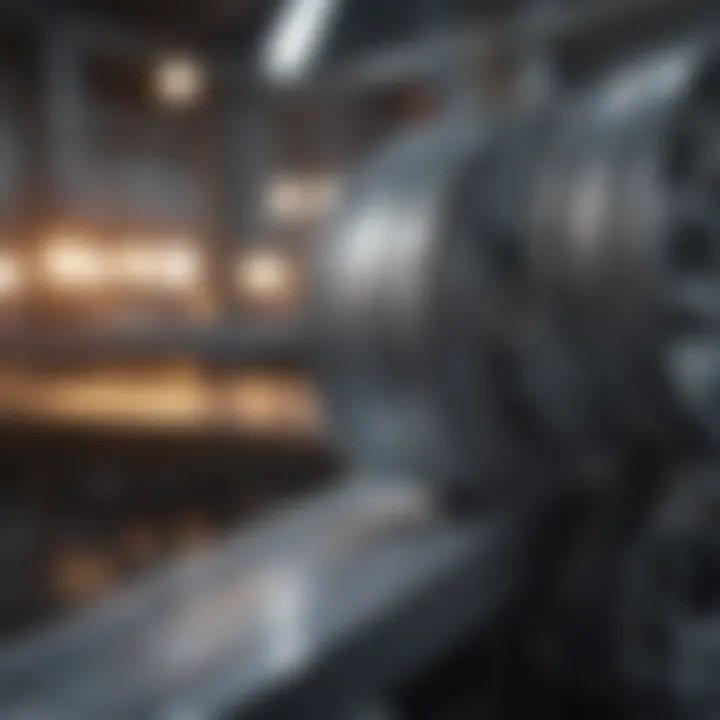
- Hot-Dip Galvanizing: This method involves immersing steel in molten zinc. It provides a thick layer of zinc, which offers superior protection against rust.
- Electroplating: This method involves using electrical current to deposit a thin layer of zinc onto a substrate. It's a cost-effective choice for smaller parts that need a uniform coating.
In essence, the method selected impacts the thickness and durability of the zinc layer, making its choice a significant aspect of the process.
Equipment Used
The equipment utilized during the zinc coating process can influence the effectiveness of the application methods. Different pieces of equipment are designed for specific techniques.
- Galvanizing Tanks: These are specifically made for hot-dip galvanizing, filled with molten zinc. It's crucial for temperature control to prevent premature solidification.
- Electroplating Tanks: These feature solutions of zinc salts and are equipped with anodes to ensure even distribution of zinc on the substrate.
Choosing the right equipment, therefore, not only enhances the application but also minimizes operational risks, ensuring a smoother coating process.
Post-Treatment Processes
Post-treatment processes play a significant role in refining the zinc coating application, ensuring the best possible outcome in terms of quality and durability.
Inspection Techniques
Inspection techniques are essential for quality control. By assessing the final coating, one can determine its reliability in providing protection.
- Adhesion Testing: Methods such as pull-off tests can reveal the strength of the bond between the zinc and the substrate.
- Thickness Measurement: This helps in ensuring that the zinc layer meets specifications, as inadequate thickness can lead to premature failure.
Thus, employing proper inspection techniques helps catch potential issues early, leading to better long-term performance.
Finishing Options
After inspection, various finishing options can enhance the zinc coating's performance. These can include passivation and painting.
- Passivation: This involves applying a protective layer to prevent white rust formation, which is critical in maintaining the aesthetic and functional properties of the coating.
- Painting: This gives an additional protective layer and can enhance the substrate's aesthetics. However, one must ensure compatibility with the zinc layer to avoid issues later.
Understanding the entire zinc coating process is not just about applying zinc; it’s about creating a durable and effective barrier against corrosion. Proper surface prep, application methods, and post-treatment are all key to achieving the best results.
Performance Characteristics
Understanding the performance characteristics of zinc coatings is essential for discerning their role in metal protection. These characteristics not only highlight the effectiveness of the coating but also help in selecting the appropriate method of application based on specific requirements. Two critical aspects often discussed in this realm are adhesion strength and thickness measurement.
Adhesion Strength
Adhesion strength refers to how well the zinc coating bonds to the substrate material. This is a critical factor because a weak bond can lead to premature delamination or peeling, ultimately rendering the protective features of the coating ineffective.
There are several elements that contribute to adhesion strength, including:
- Surface Preparation: Before application, the metal surface must be meticulously cleaned. Any grease, oil, or rust can severely compromise the bonding process. The use of techniques like sandblasting or chemical cleaning is common to enhance surface conditions.
- Coating Methods: Different application methods, such as hot-dip galvanizing versus electroplating, can affect how well the zinc adheres to the substrate. For instance, hot-dip galvanizing typically provides a more robust bond due to the metallurgical reaction between the molten zinc and the steel surface.
- Environmental Factors: Conditions post-application also play a role. Factors such as humidity and temperature can impact the curing process, influencing adhesion strength.
In evaluating adhesion strength, professionals often perform tests that measure the force required to pull the coating away from the substrate, providing a clear indication of its reliability.
Thickness Measurement
Thickness measurement is another key performance characteristic that impacts the longevity and effectiveness of zinc coatings. Too thin a coating may not offer sufficient protection against corrosion, while an overly thick layer can result in issues such as white rust formation or masking of the substrate's natural qualities.
To ensure the right balance, several methods are utilized to measure coating thickness:
- Magnetic Gauge: Primarily used for iron and steel substrates, this device measures the magnetic field, determining the zinc layer's thickness accurately.
- Ultrasonic Testing: A more advanced technique that can be employed on various substrate materials. It uses high-frequency sound waves to detect the thickness of the coating.
- X-Ray Fluorescence: This method uses X-rays to measure the elemental composition, which can indirectly indicate coating thickness.
Monitoring the thickness is not just a matter of ensuring quality; it can significantly influence the overall performance and durability of the coating under environmental stressors.
In summary, both adhesion strength and thickness measurement play pivotal roles in the performance characteristics of zinc coatings, influencing their protective abilities and longevity.
By understanding these factors, industry professionals can make informed decisions that optimize application techniques and ensure the lasting effectiveness of zinc coatings.
Applications of Zinc Coating
Zinc coating plays a pivotal role across diverse sectors, primarily due to its unique properties that combat corrosion. This coating acts as a sacrificial layer, protecting the underlying metal, which ensures the longevity and durability of various structures. Its applications touch both everyday items and critical industrial components, making a clear understanding essential for students, researchers, and professionals alike. The benefits of zinc coatings are multifold: they enhance the lifespan of products, reduce maintenance costs, and contribute to safety in construction and manufacturing activities. Herein, we will examine the applications of zinc coatings in the construction industry, automotive sector, and manufacturing arena.
Construction Industry
In the construction domain, zinc coating is indispensable. With steel being a fundamental material for structural applications, protecting it against the hazards of oxidation is paramount. Notably, buildings and bridges are subject to harsh environmental conditions, which can deteriorate materials if they are not adequately shielded.
- Corrosion Protection: Zinc acts as a protective barrier. If the zinc layer gets damaged, it still guards the underlying steel by corroding first. This unique feature is fundamentally why many construction entities choose zinc coatings for rebar and structural steel during projects.
- Aesthetic Appeal: In addition to functionality, zinc coatings can also provide a pleasing aesthetic finish to structures.
- Sustainability: As the world moves toward greener practices, zinc coatings contribute by extending the life cycle of materials, which means lesser frequent replacements. Businesses that adopt these coatings find they not only save on costs but also improve their sustainability footprint.
Automotive Industry
The automotive sector heavily relies on zinc coating to protect vehicles against corrosion. Every part, from the chassis to smaller components, benefits from this protective medium.
- Durability and Safety: Vehicles encounter a range of corrosive threats, including road salts and moisture. Zinc-coated parts are less likely to degrade, thus enhancing safety and reliability.
- Enhanced Resale Value: Cars with better corrosion resistance generally maintain their aesthetic appeal and functional integrity for longer, which bodes well for resale potential.
- Diverse Applications: From body panels to intricate engine parts, zinc can be applied via several methods, including electroplating and hot-dip galvanizing, catering to various automotive requirements.
Manufacturing Sector
Manufacturing industries have garnered immense benefits from zinc coating due to the protection it offers to machinery and equipment.
- Protection for Tools and Equipment: Tools subject to moisture and abrasion can suffer swift deterioration. Zinc coatings often extend the operational life of these tools.
- Cost-Effective Solution: Considering the longevity provided by zinc coatings, manufacturers often find that the initial investment pays off over time with reduced repair costs.
- Versatility: The ability to apply zinc coatings on diverse materials makes it a preferred choice in the manufacturing realm. Whether it's for large machinery or small components, there's a suitable zinc application method available.
The strategic use of zinc coatings across industries underscores their importance in preventing corrosion and ensuring the integrity of metal products over time.
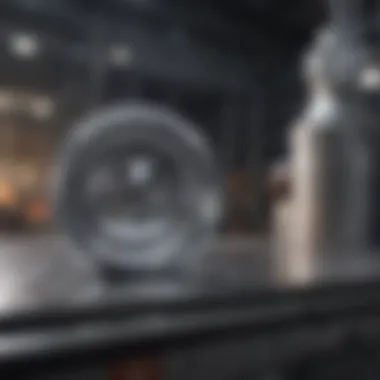
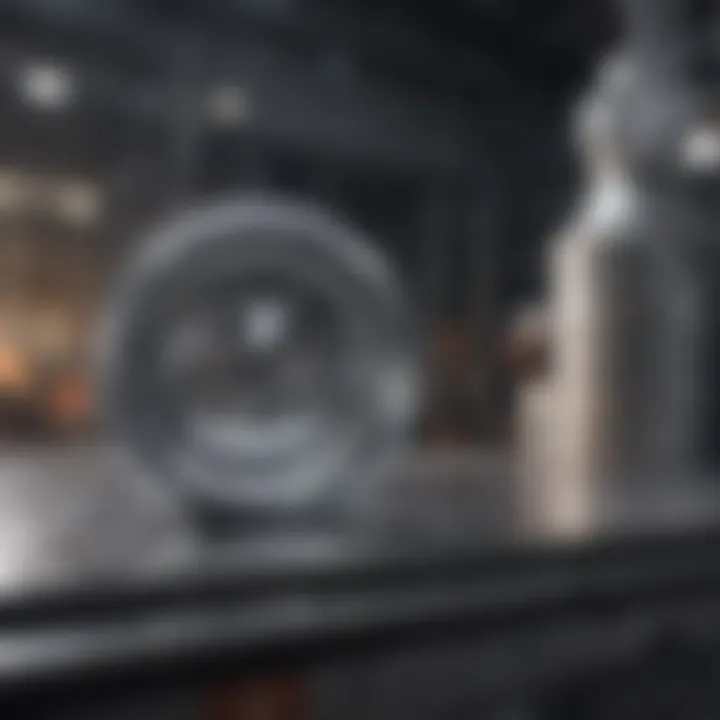
In summary, the applications of zinc coating are comprehensive, impacting construction, automotive, and manufacturing sectors profoundly. As the demand for corrosion resistance grows, the role of zinc coatings will only become more critical in safeguarding assets, contributing to safety, sustainability, and cost-efficiency.
Environmental Considerations
Impact on Ecology
The environmental repercussions of zinc coatings provoke considerable discourse among industries that utilize them. Zinc, while essential for corrosion protection, can pose threats to ecosystems if not managed appropriately. Zinc runoff can seep into water bodies, affecting aquatic life and impacting flora and fauna. To grasp the full extent of its impact on ecology, one must recognize that zinc, when present in high concentrations, may lead to toxicity in various species. Fish, for instance, can experience respiratory issues and reproductive challenges due to elevated zinc levels. Additionally, it can hinder the growth of aquatic plants, altering habitats and disrupting ecosystems.
It's crucial for companies to properly implement zinc management practices. Regular monitoring of emissions and runoff, alongside adherence to local regulations, can mitigate many ecological threats. In essence, the balance between utilizing zinc for its protective qualities and ensuring environmental conservation is not just desirable but necessary. Indeed, proactive measures can lead to a win-win scenario, maintaining both industrial efficacy and ecological health.
Sustainability Practices
Amidst growing concerns about environmental sustainability, the zinc coating industry has started to adapt its practices. One of the foremost considerations is the development of sustainable materials and processes. Moving away from traditional methods, like hot-dip galvanizing, which can produce significant waste heat and emissions, has led to innovations in various areas. For example, electroplating can be executed with less energy consumption and lower greenhouse gas emissions.
Furthermore, resource recovery methods, like capturing and recycling zinc dust or off-cuts from manufacturing processes, are becoming more common. Companies are now looking toward closed-loop systems, where waste materials are repurposed, creating a more sustainable cycle.
Moreover, embracing environmentally friendly coatings that employ biodegradable additives or reduced hazardous materials can further lessen the ecological footprint of zinc coatings. In this respect, manufacturers and applicators need to prioritize sustainable product choices while ensuring that they still provide robust corrosion resistance. The transition towards sustainability not only fulfills regulations but also caters to an increasingly eco-conscious market that values responsible industrial practices.
"Implementing sustainable practices in zinc coating can lead to a healthier environment while safeguarding the performance required in various applications."
In sum, the focus on sustainability in zinc coating processes has the potential to foster innovative approaches that protect the planet, enhancing the long-term viability of both the industry and our natural ecosystems.
Future Trends in Zinc Coating Technologies
The world of zinc coating is evolving, just like a river finding its way through rocky terrain. As industries strive for increased efficiency and sustainability, innovations within zinc coating processes become essential. These advancements are not just about keeping up with the times; they represent a commitment to superior corrosion protection, environmental responsibility, and cost-effectiveness. With pressures mounting from regulation and environmental advocacy, exploring future trends in zinc coating technologies is crucial for metal industries across the globe.
Innovations in Processes
The landscape of zinc coatings is on the brink of a technological revolution. One of the key areas of development is the refinement of hot-dip galvanizing methods. New approaches such as twin-screw extruder galvanizing aim to improve coating consistency and reduce waste. This method blends efficiency with environmental considerations, reducing the need for excessive post-treatment adjustments.
Another innovation to note is the trend towards metal matrix composites in zinc coatings. By integrating zinc with other materials like polymers or ceramics, manufacturers can enhance the coating's properties. This fusion results in coatings that are not only aesthetically pleasing but also incredibly durable.
- Advantages of these emerging processes include:
- Improved adhesion: Innovative techniques now allow for better bonding between zinc and metal substrates.
- Reduced environmental impact: Modern processes minimize hazardous waste, supporting more sustainable practices.
- Adaptability: Processes can be customized for various applications, expanding the utility of zinc coatings.
Emerging Applications
The utilization of zinc coatings is broadening beyond traditional boundaries. One area gaining traction is renewable energy, particularly in solar and wind industries. Zinc-coated metals are becoming a preferred choice for structures like solar panels and wind turbines due to their exceptional resistance to the elements. The longevity offered by zinc coatings helps ensure that these energy sources remain reliable, reducing maintenance expenses over time.
Another area ripe for growth is in the aerospace sector. As aircraft manufacturers seek lightweight materials that lack susceptibility to corrosion, zinc coatings offer an appealing solution. By applying zinc in thin films, engineers can reduce overall weight while maintaining structural integrity, thereby increasing fuel efficiency.
"Innovative applications of zinc coatings are redefining industries, proving that the future holds not just resilience but also versatility."
Challenges in Zinc Coating
The process of zinc coating, while effective at providing protection against corrosion, is not without its tribulations. Understanding these challenges sheds light on what professionals face in ensuring the quality, performance, and sustainability of coated products. Various aspects can impede the effectiveness of the zinc coating process, and confronting these issues is imperative for manufacturers and users alike.
Quality Control Issues
Quality control stands out as a critical challenge in the zinc coating realm. Achieving a consistent coating thickness is essential; if the layer is too thin, the metal underneath can corrode rapidly. Conversely, if it's too thick, it could lead to issues of flaking or cracking, diminishing the protective benefits intended.
In the factory, some common problems can arise:
- Surface Contaminants: Any dirt, oil, or unwanted residues can hinder the bonding of the zinc layer to the substrate. Without adequate cleaning, these particles create weak spots, undermining the entire purpose of zinc coating.
- Inconsistent Heating: For processes like hot-dip galvanizing, the temperature of the zinc bath needs careful monitoring. If the temperature fluctuates too much, uneven coating results.
To combat these issues, some manufacturers employ advanced techniques such as X-ray fluorescence, which allows for real-time monitoring of coating thickness. However, the investment in such technology can be daunting for smaller operations.
Economic Factors
Economic considerations also weigh heavily on the zinc coating process. The costs associated with materials, labor, and equipment maintenance can mount quickly. For example, the price of zinc itself can be volatile, influencing the overall budgeting of projects that depend heavily on zinc coatings.
Additionally, there are questions of return on investment. While zinc-coated materials offer significant longevity compared to uncoated alternatives, the initial expenses can deter decision-makers from opting for these solutions. It's critical for businesses to:
- Conduct Cost-Benefit Analyses: This includes evaluating the increased lifespan of coated products against initial investments.
- Explore Alternatives: Frequently examining the market for other protective coatings can also unveil potential savings or innovation opportunities.
By staying informed about trends in material costs and processing innovations, companies can better navigate the economic landscape surrounding zinc coating, ensuring they make sound investments that protect both their assets and their bottom lines.
Quality control and economic factors play a vital role in determining the success and reliability of zinc coating processes, making it essential for industries to address these issues effectively.
The End
In the realm of metal protection, the zinc coating process stands as a pillar of integrity and durability. The significance of this process cannot be overstated, particularly when considering its multifaceted benefits that directly contribute to the longevity of structures and materials. To sum it up succinctly, zinc coating acts not only as a barrier against corrosion but also enhances the aesthetic appeal of metal products, safeguarding them from the ravages of time and environmental elements.
Summary of Key Insights
Through this article, we've traversed the intricate landscape of zinc coating, identifying several key insights about its application and efficacy:
- Corrosion Resistance: Zinc plating forms a protective layer that effectively combats oxidation, which is arguably one of metal’s biggest enemies.
- Versatile Techniques: Techniques such as hot-dip galvanizing, electroplating, and zinc-rich paints each present unique advantages tailored to specific applications, making them suitable across various industries.
- Economic Viability: The protective qualities of zinc coating translate to lower maintenance costs, thereby providing economic advantages over its lifespan.
- Environmental Strategies: Sustainable practices in zinc coating are becoming increasingly prioritized, ensuring that technological advancements align with ecological concerns.
While it's relatively straightforward to appreciate the benefits of zinc coating, one must also recognize the challenges associated with its application. Factors such as quality control and economic dynamics continuously shape the landscape of this field.
Future Directions in Research
As zinc coating technologies evolve, several avenues for future research emerge:
- Innovative Materials: The exploration of alternative alloys or composites that could enhance the effectiveness of zinc against corrosion is a promising area. Researchers may delve into blending zinc with other metals for hybrid solutions.
- Eco-Friendly Alternatives: Developing environmentally friendly zinc coating options that offer equal or superior performance compared to conventional methods will likely be a focal point in future studies.
- Performance Analytics: Employing advanced technologies like AI to predict the longevity and durability of zinc coatings in varying environmental conditions may lead to breakthroughs in application techniques.
- Global Standards: Establishing unified international standards for zinc coating applications can help mitigate discrepancies in quality, fostering a more consistent approach across industries.
In essence, the evolution of zinc coatings is an ongoing conversation, one that beckons further inquiry and innovation. Thus, the body of knowledge surrounding this topic will continue to expand, reflecting the increasing importance of durable materials in our modern age.