Understanding Positive Displacement Pumps Mechanics
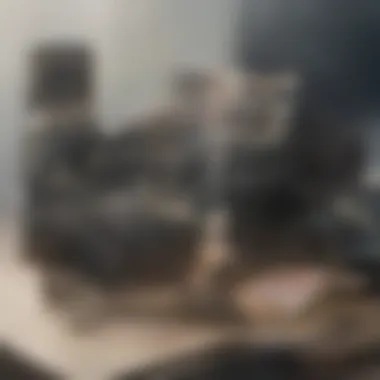
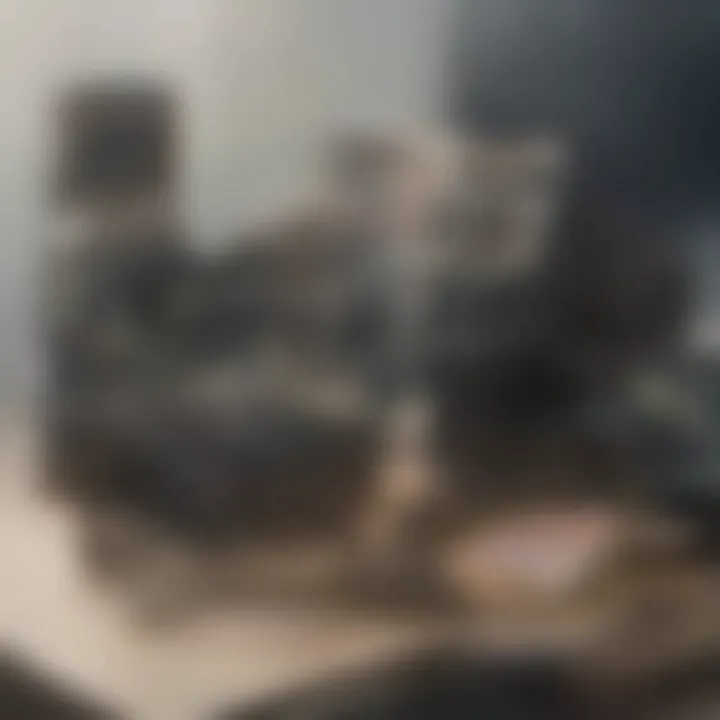
Intro
Positive displacement pumps are essential components in fluid transport systems across diverse industries. Understanding their mechanics, design, and applications is crucial for professionals and students alike. This section aims to provide a foundational overview of these pumps, setting the stage for detailed discussions in subsequent sections.
Key Findings
Major Results
In exploring positive displacement pumps, several key findings emerge:
- Efficacy in Fluid Transport: Unlike dynamic pumps, positive displacement pumps move a fixed volume of fluid with each cycle. This characteristic ensures reliable and consistent flow, making them suitable for various applications.
- Design Variations: These pumps come in multiple forms, such as gear, diaphragm, and screw pumps, each with unique features tailored for specific tasks.
- Advantages Over Other Pumps: One significant benefit of positive displacement pumps is their ability to handle high-viscosity fluids. They also maintain performance under varying pressure conditions.
Discussion of Findings
The efficacy of positive displacement pumps can be seen prominently in industries such as oil and gas, chemical manufacturing, and food processing. For instance, in the food industry, pumps need to handle viscous liquids while maintaining hygiene standards. The ability to meter the flow precisely is another advantage that aligns with industry needs.
This consistency of flow, coupled with adaptability to different fluid characteristics, illustrates why many sectors opt for positive displacement solutions. However, while advantageous, these pumps also come with specific maintenance requirements that must be managed to ensure long-term reliability.
Methodology
Research Design
To understand positive displacement pumps comprehensively, a combination of qualitative and quantitative research methods was utilized. This approach allows for an in-depth analysis of both theoretical principles and practical applications.
Data Collection Methods
Data were gathered from multiple sources, including:
- Peer-reviewed journals that focus on fluid dynamics and pump technology.
- Industry reports that provide insights into design and operational efficiency.
- Technical documentation from manufacturers, aiding in understanding design specifics and maintenance protocols.
Combining these resources offers a robust framework for grasping the complexities of positive displacement pumps.
In the next sections, we will fully delve into the operational principles and specific applications, expanding on the initial key findings and consolidating understanding across different contexts.
Prologue to Positive Displacement Pumps
Positive displacement pumps function by trapping a fixed amount of fluid and forcing it into the discharge pipe. This characteristic ensures that fluid flow is consistent, which is essential when precision is needed in applications such as chemical processing or food production.
Definition and Characteristics
Positive displacement pumps are defined by how they manipulate fluids. The main characteristic is their capability to move a specific volume of fluid with each rotation or cycle. Unlike dynamic pumps, which rely on the kinetic energy generated by impellers, positive displacement pumps rely on mechanical action.
Key characteristics include:
- Fixed Volume: Each cycle of the pump moves a determined volume of fluid regardless of resistance.
- Pressure Generation: They can generate high pressures, making them suitable for viscous fluids.
- Versatility: They can handle various fluid types, from water to viscous substances like oils and slurries.
Historical Background
The development of positive displacement pumps dates back several centuries. The concept traces its origins to the ancient times when mechanical devices were crafted to move water. Archimedes' screw, a device thought to be one of the earliest forms of a pump, demonstrated the basic principles of fluid movement.
In the 19th century, advancements in engineering led to more sophisticated designs. The introduction of various pump types, such as gear and diaphragm pumps, expanded their applicability across different industries. Each design offered unique advantages, which contributed to their adoption in sectors such as agriculture, manufacturing, and later, in medical applications.
Operational Principles
Understanding the operational principles of positive displacement pumps is crucial for effective application in various industries. This knowledge allows users to select the right pump for their specific needs while also ensuring efficient performance. Positive displacement pumps operate on a straightforward fundamental: they move fluid by trapping a fixed amount and forcing it through the discharge. This design offers several advantages that make them suitable for handling various substances, including those with high viscosity and shear-sensitive fluids.
Mechanics of Positive Displacement
In essence, positive displacement pumps create a vacuum that draws fluid into a chamber and then mechanically pushes it out. This process occurs in two main phases: filling and discharging. During the filling phase, a mechanism, typically a rotor or diaphragm, creates a low-pressure area that draws fluid into the pumping chamber. Next, the discharge phase expels the trapped fluid into the outlet.
A significant characteristic here is that the flow rate remains constant regardless of the discharge pressure. This feature allows for precise control over fluid transfer. Furthermore, positive displacement pumps can maintain steady flow rates even when faced with variations in pressure, making them ideal for applications requiring consistent output, such as in oil and gas or chemical processing.
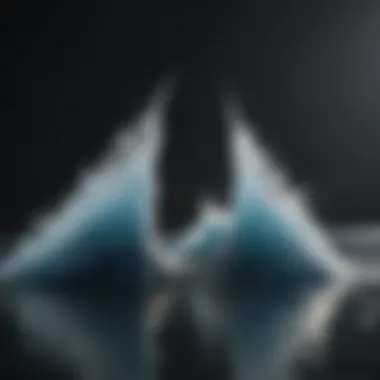
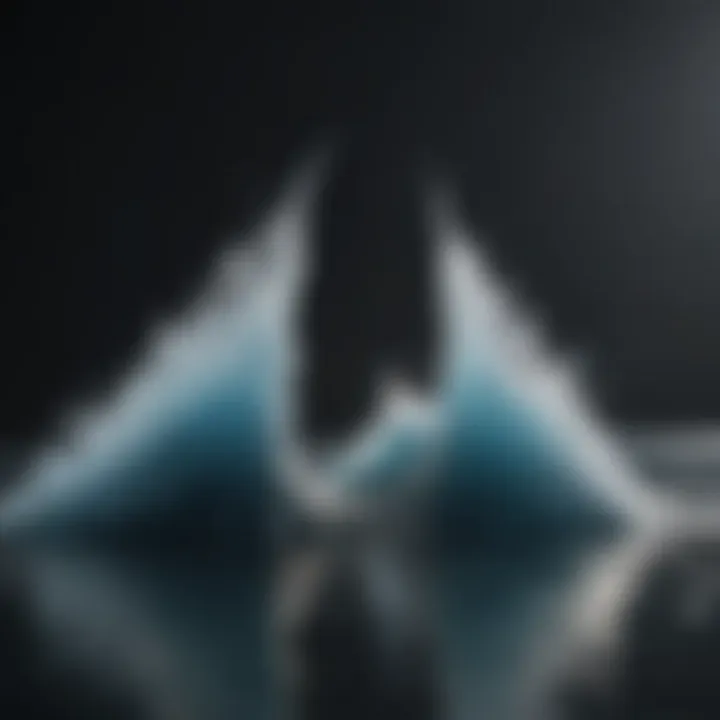
Types of Positive Displacement Pumps
Positive displacement pumps come in various types, each designed for specific applications and fluid types.
Gear Pumps
Gear pumps are one of the most common types of positive displacement pumps. They consist of two or more gears meshing together to move fluid. The primary contribution of gear pumps is their efficiency in transferring viscous fluids. They are popular for their ability to provide consistent flow and high pressure.
The key characteristic of gear pumps lies in their simplicity and compact design. This pump type does not require any valves, reducing maintenance needs. A unique feature of gear pumps is their quiet operation, making them suitable for sensitive environments. However, they can struggle with fluid containing entrained air, which may lead to loss of efficiency.
Diaphragm Pumps
Diaphragm pumps utilize a flexible diaphragm that separates the pump chamber from the fluid being transferred. This construction is particularly advantageous for applications requiring the handling of corrosive or abrasive materials, as it keeps the fluid entirely contained and minimizes the risk of leaks.
The key characteristic of diaphragm pumps is their suitability for a broad range of applications, including those in medical and food industries. The unique feature of these pumps is their ability to operate in dry conditions without damage. Nevertheless, diaphragm pumps can be less efficient when it comes to high-pressure applications compared to other types.
Piston Pumps
Piston pumps operate by using a piston to create a vacuum that draws fluid into a chamber and then pushes it out. They are known for their capability to handle high pressure and provide significant flow rates. The contribution of piston pumps is notable in industries requiring precise fluid measurement, such as pharmaceuticals.
The key characteristic of piston pumps is their versatility, allowing them to work with a variety of fluids, from water to thick slurries. Their unique feature rests in the ability to produce high-pressure outputs. Inevitably, they can face limitations with very viscous fluids, as well as requiring regular maintenance to ensure optimal performance.
Rotary Vane Pumps
Rotary vane pumps consist of vanes that slide in and out of a rotor housed within a cavity. They are particularly effective in creating a vacuum and are often used in applications requiring smooth and constant flow.
The key characteristic of rotary vane pumps is their efficiency in transferring low-viscosity fluids. Their unique feature is simple construction leads to easy maintenance and operation. However, they may not be suitable for high-viscosity fluids, which can hinder their performance.
By understanding these characteristics and operational principles of positive displacement pumps, users can make informed decisions regarding their applications and achieve optimal results.
Design Variations
Design variations in positive displacement pumps are crucial for making them suitable for different applications and environments. Each design has its unique features that cater to specific operational needs. This section will explore how various design elements impact the functionality, efficiency, and adaptability of these pumps. Understanding these variations enables professionals to select the most appropriate pump for their specific fluid handling requirements.
Construction Details
The construction of positive displacement pumps can vary significantly based on their design type. Key elements in the construction include:
- Pump Casing: The outer shell is usually made from sturdy materials like cast iron, stainless steel, or plastic. The choice of material affects the pump's durability and resistance to corrosion.
- Rotors and Gear Sets: These components are integral in determining the pump's operation. For instance, in gear pumps, precise gear shapes create efficient fluid transfer systems.
- Seals and Gaskets: Quality sealing materials prevent leaks and maintain pressure, which is essential for optimal pump performance.
The assembly process is also critical. Each component must be carefully engineered and fitted to ensure meets the necessary tolerances. Designs that allow easier access for maintenance can significantly reduce downtime.
Material Considerations
Material selection is a significant aspect of the design variations for positive displacement pumps. Factors that influence this choice include:
- Chemical Compatibility: The materials used must be suitable for the specific fluids being transported. For example, corrosive liquids require pumps made from materials like polypropylene or various alloys.
- Temperature Resistance: High-temperature fluids necessitate materials that can withstand thermal stress, such as special steel grades or ceramics.
- Durability Requirements: Settings that involve high wear must consider using tougher materials to prolong the lifespan of the pump.
Choosing the right materials ensures efficiency, longevity, and operational efficiency. Itβs vital for manufacturers to pay attention to these elements to offer pumps that withstand industrial challenges.
"The right design and materials not only enhance a pump's performance but also its applicability across a wider range of industries."
In summary, understanding the design variations in positive displacement pumps leads to smarter selection and application. Knowledge of construction details and material considerations plays a critical role in enhancing the functionality and reliability of these pumps.
Applications of Positive Displacement Pumps
The realm of positive displacement pumps extends into various vital industries. Their design and operation make them well-suited for numerous applications. Understanding these applications is crucial for selecting the right pump for specific tasks. The efficiency, precision, and reliability of these pumps highlight their significance. From industrial needs to food processing, their roles cannot be overstated. This section elaborates on the various sectors that utilize these pumps, illustrating their versatility.
Industrial Use Cases
In industrial settings, positive displacement pumps are often the backbone of fluid transport. They excel in moving viscous fluids, which are common in industries such as oil and gas, chemicals, and manufacturing. Here are some key applications:

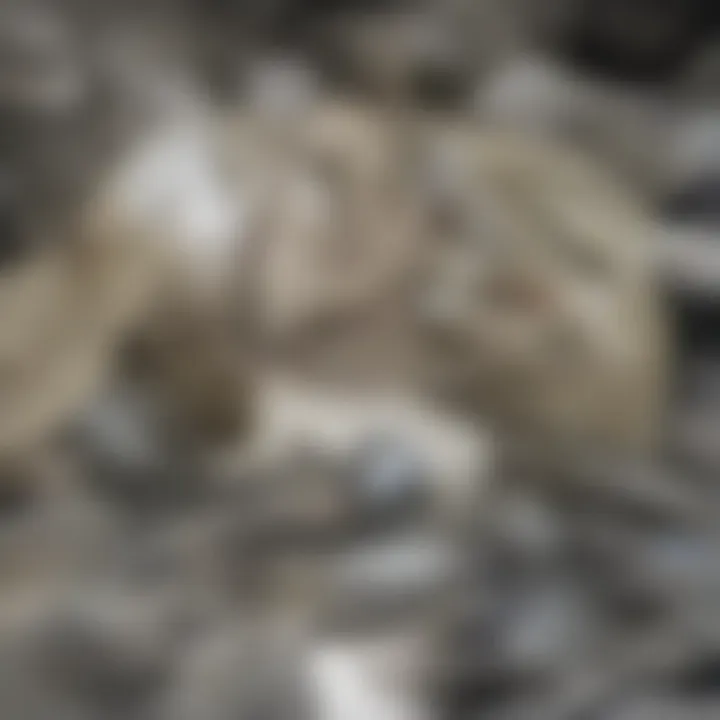
- Oil and Gas: These pumps transport crude oil and other viscous materials. They handle changing pressure levels effectively, maintaining consistent flow rates.
- Chemical Processing: In this sector, precise chemical additions are essential. Positive displacement pumps ensure accurate transfer, which is vital for safety and quality control.
- Wastewater Treatment: Pumping sewage and other by-products requires reliability. The capability of positive displacement pumps to handle solid content enhances their appeal in this area.
Each of these use cases showcases how fluid properties and pumping characteristics mesh to lower downtime and improve productivity.
Medical and Laboratory Applications
Positive displacement pumps find their way into the medical field as well. In laboratories and healthcare settings, precision is paramount. Here are some applications within these domains:
- Drug Delivery Systems: They ensure accurate dosages of medications. This precision is crucial to avoid dosing errors that could impact patient health.
- Biotechnology: In the production of biological materials, maintaining specific flow rates is necessary. Positive displacement pumps meet these demands effectively.
- Laboratory Processes: Many analytical instruments require precise liquid handling. These pumps provide the consistency necessary for reliable results.
Their role in these sensitive environments underscores their importance, where accuracy can mean the difference between success and failure.
Food and Beverage Industry
The food and beverage industry also benefits significantly from positive displacement pumps. Here, sanitary conditions and product integrity are key. Important applications include:
- Liquid Food Products: These pumps are used for transferring sauces, dairy, and other viscous food products. They maintain flavor and texture by ensuring gentle handling.
- Beverage Processing: In the production of juices, beers, and soft drinks, maintaining quality during transfer is critical. Positive displacement pumps facilitate this while adhering to hygiene standards.
- Cleaning Processes: Efficient cleaning and sanitation of equipment are paramount. Positive displacement pumps can effectively remove residues and maintain cleanliness.
In summary, the applications of positive displacement pumps are extensive and varied. Their ability to manage a range of fluids under different conditions establishes them as essential equipment across multiple industries.
"The efficient functioning of positive displacement pumps defines productivity in many sectors, highlighting their importance beyond just fluid transport."
Understanding these applications helps professionals make informed decisions for their specific operational needs. This knowledge is key to optimizing processes and achieving better outcomes in various fields.
Advantages of Positive Displacement Pumps
Positive displacement pumps offer unique advantages that make them essential in various applications. Their design and operational characteristics give them distinct benefits compared to other types of pumps. Understanding these advantages is crucial for selecting the right pump for a specific task. This section highlights the core advantages, focusing on efficiency in handling viscous fluids and precision in fluid transfer.
Efficiency in Handling Viscous Fluids
One significant advantage of positive displacement pumps lies in their ability to efficiently handle fluids with high viscosity. Many industrial processes require the movement of thick or viscous materials, such as oils, syrups, or polymers. Unlike centrifugal pumps, which may struggle with such fluids due to their design principles, positive displacement pumps can maintain a constant flow rate regardless of viscosity variations.
These pumps operate by trapping a fixed volume of fluid in each cycle and then displacing it through the pump's outlet. This method allows them to deliver consistent flow, even when the fluid's resistance increases. Moreover, they exhibit a high tolerance for changes in fluid characteristics, which is important in many manufacturing processes where formulations may vary.
In addition, positive displacement pumps reduce the risk of cavitation, a common issue when handling viscous fluids. Cavitation can lead to pump damage and inefficiencies, which are often exacerbated in centrifugal pumps. By maintaining a stable pressure and flow, positive displacement pumps enhance operational reliability.
Precision in Fluid Transfer
Precision in fluid transfer is another hallmark of positive displacement pumps. These pumps provide accurate and repeatable flow rates, which is vital in applications like pharmaceuticals, food processing, and chemical manufacturing. Here, precision ensures that exact amounts of material are dispensed, which can affect the quality of the final product.
The design of positive displacement pumps allows for fine control over the flow rates. Adjustments can be made with relative ease, enabling operators to modify fluid transfer as needed without compromising system integrity. This feature is particularly beneficial in laboratory settings where exact quantities are mandatory for experiments or formulations.
Furthermore, positive displacement pumps minimize product shear. For sensitive or delicate fluids, high shear stresses can alter properties or change product formulations. Their design minimizes shear, ensuring that the integrity of the fluid is maintained during transfer.
"The precise operation of positive displacement pumps positions them as a perfect choice in numerous applications requiring accuracy and reliability."
Comparative Analysis
Comparative analysis of positive displacement pumps plays a critical role in understanding their advantages in various applications. In this section, we explore the distinct characteristics of positive displacement pumps in contrast to their dynamic counterparts. This analysis not only helps to clarify the functional principles but also aids users in making informed decisions regarding the selection of pumps for specific processes.
Positive vs. Dynamic Pumps
The main distinction between positive displacement pumps and dynamic pumps lies in their operation mechanisms. Positive displacement pumps work by trapping a fixed volume of fluid and then forcing it out. This leads to consistent flow rates that are largely unaffected by discharge pressure, thus making them ideal for handling viscous fluids. In contrast, dynamic pumps, such as centrifugal pumps, rely on velocity to move fluid. The flow rate in dynamic pumps can vary significantly based on the system pressure, presenting challenges when precise control is required.
Key differences include:
- Flow Rate Stability: Positive displacement pumps maintain a steady flow, even under varying pressures.
- Viscosity Handling: Positive displacement pumps excel in transporting high-viscosity fluids without compromising performance.
- Design Complexity: Generally, dynamic pumps have simpler designs and may require less robust materials, but positive displacement pumps offer versatility in complex environments.
Selecting between these pumps often comes down to the specific application needs, making this analysis essential for engineers and operators.
"Understanding the operational differences can significantly reduce misapplication and enhance system efficiency."
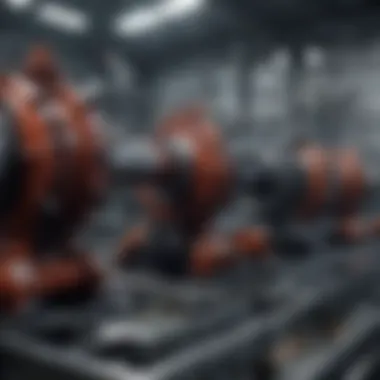
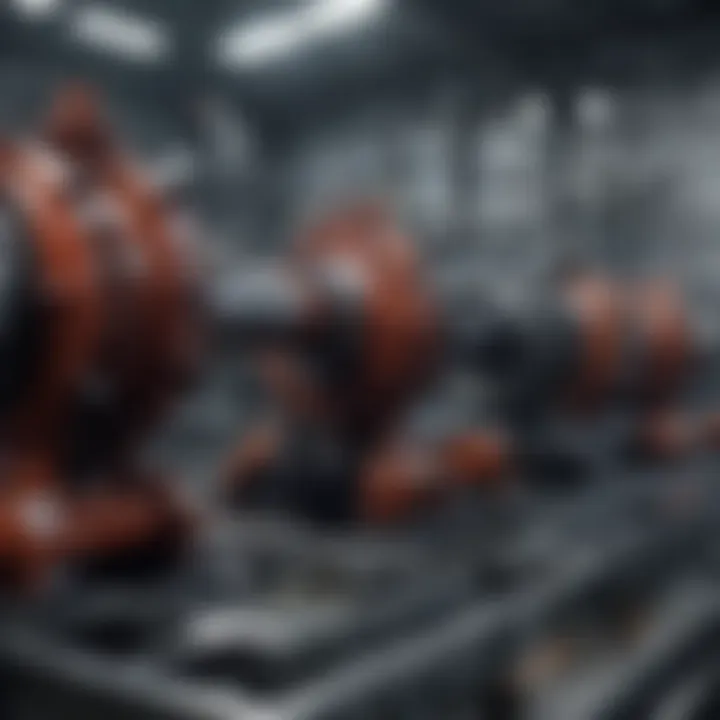
Selection Criteria
When selecting between positive displacement and dynamic pumps, several key factors must be considered:
- Fluid Properties: Consider the viscosity, temperature, and chemical composition of the fluid. Positive displacement pumps are often better suited for viscous or shear-sensitive fluids.
- Required Flow Rate: Establish the desired flow rate and pressure. Positive displacement pumps can deliver a consistent flow, perfect for applications requiring precision.
- Operational Environment: Assess the surrounding conditions. Harsh environments may demand robust construction found in many positive displacement models.
- Maintenance Needs: Evaluate the maintenance requirements. Some pumps may have different servicing times, which can affect overall operational efficiency.
- Cost and Budget: Finally, consider the initial investment and long-term operational costs, as these can vary significantly between pump types.
A thorough comparative analysis equips industry professionals, researchers, and students with the knowledge to select the right pump for their needs, ensuring optimal performance and reliability.
Maintenance and Troubleshooting
Maintaining positive displacement pumps is crucial for ensuring their long-term performance and reliability. Regular maintenance practices help prevent unexpected failures that can lead to downtime, costly repairs, and disruption of operations. Understanding the typical issues that can arise and how to address them is equally important for efficiency.
The benefits of good maintenance practices include prolonged equipment life, reduced operational costs, and improved safety. By routinely inspecting and servicing these pumps, operators can identify potential problems early and implement solutions before they escalate. In addition, a well-maintained pump operates at optimal efficiency, ensuring consistent fluid transfer and minimizing energy consumption.
Routine Maintenance Practices
Effective maintenance involves several key practices that contribute to pump longevity. Here are some essential routine maintenance tasks for positive displacement pumps:
- Regular Inspections: Conduct visual inspections to check for leaks, unusual noises, or vibrations.
- Lubrication: Ensure that bearings and other moving parts are adequately lubricated to reduce wear and friction. Using the right type of lubricant is crucial for specific pump designs.
- Sealing Checks: Inspect seals and gaskets for wear or damage. Replacing these components periodically can prevent leaks and maintain efficiency.
- Filtering: If the pump draws fluid from a reservoir, ensure that filters are clean and functional to avoid contamination of the pumped fluid.
- Alignment Verification: Ensure that the pump and motor shafts are properly aligned to prevent excessive wear and increase efficiency.
These simple yet effective maintenance practices can result in significant savings in operating costs by reducing the incidence of breakdowns and extending the pump's operational lifespan.
Common Issues and Solutions
Despite rigorous maintenance, common issues can still emerge with positive displacement pumps. Understanding these problems and their solutions can help maintain efficient pump operation.
- Leakage
Leakage is often caused by worn seals or damaged fittings. Regular inspection and timely replacement of seals can help mitigate this issue. - Cavitations
Cavitation can occur when the pump is not supplied with sufficient fluid. This leads to damage over time. Make sure the suction line is unobstructed and the pump inlet is properly submerged. - Excessive Noise
Unusual noise may indicate loose components or misalignment. Tighten fasteners and check alignment to resolve this issue. - Reduced Flow Rate
A decrease in flow can result from blockages or wear inside the pump. Inspecting the pump's internal mechanisms can highlight areas that need attention. - Temperature Fluctuations
High temperatures may indicate excessive friction or inadequate cooling. Regular checks to lubricate bearings or enhance cooling can help maintain proper temperatures.
By identifying common issues and understanding their respective solutions, operators can maintain positive displacement pumps more effectively, leading to better overall performance. Regular monitoring and adherence to maintenance techniques can prevent many issues, ensuring these pumps serve their intended purpose efficiently and reliably.
Innovations and Future Trends
Innovations in positive displacement pumps are crucial for maintaining their relevance in a rapidly advancing industrial landscape. As industries continue to seek higher efficiency and environmental sustainability, these pumps undergo significant technological upgrades. Such innovations are essential not only to meet market demand but also to comply with stricter regulations regarding energy usage and waste management.
Technological Advances
Recent developments in sensor technology and automation have transformed the functionality of positive displacement pumps. Smart sensors now enable real-time monitoring of operational parameters, providing data on flow rates, pressure, and even wear conditions of various components. These advancements facilitate predictive maintenance, reducing downtime and optimizing performance.
Additionally, advancements in materials science have led to the development of more resilient and corrosion-resistant materials. This is particularly vital in industries where pumps handle aggressive fluids. For example, certain polymer composites can withstand harsh chemicals without degrading, improving the pumps' longevity.
Moreover, the integration of IoT technology has introduced remote management capabilities. Operators can now control and monitor pumps from afar, allowing for quick adjustments and troubleshooting without requiring physical presence. This level of control leads to increased efficiency and a higher response rate to any operational issues.
Sustainability Considerations
Sustainability is becoming a central theme in many industrial processes, and positive displacement pumps are no exception. Innovations in this area focus on reducing the carbon footprint and increasing energy efficiency. For instance, the development of energy-efficient motor drives helps to minimize energy consumption during pump operation. Such motors can adjust their output based on real-time demand, which helps in conserving energy.
Another significant trend is the move towards eco-friendly lubricants and sealants. Traditional lubricants may contain environmentally harmful compounds. New biobased or synthetic options diminish the environmental impact when spills occur, aligning with global sustainability goals.
"The future of positive displacement pumps lies in their adaptability to new technologies and sustainable practices, ensuring their role in a greener future."
In response to changing consumer preferences and regulatory pressures, many manufacturers are also focusing on the recyclability of pump components. Making parts out of materials that are easier to recycle aids in reducing overall waste generated by the equipment at the end of its operational life.
With these innovations, positive displacement pumps are set to evolve continuously, responding to both technological challenges and the pressing need for sustainability in the world of industrial applications.
Ending
The conclusion serves as a pivotal closing segment that encapsulates the vital elements explored throughout the article on positive displacement pumps. Its role is not merely to summarize, but to illuminate the significance of the topics covered, reinforcing their relevance in various contexts.
Positive displacement pumps are essential tools in a myriad of industries, from pharmaceuticals to food manufacturing. Understanding their mechanics, design variations, and applications is crucial in making informed decisions regarding their usage. This conclusion synthesizes the insights gained, showcasing how these pumps offer efficient fluid handling, especially when dealing with viscous substances.
Summarizing Key Insights
In reviewing the entirety of the article, several key insights emerge:
- Mechanics and Types: Positive displacement pumps operate on specific mechanics that differentiate them from dynamic pumps. The distinct types, such as gear pumps, diaphragm pumps, and piston pumps, cater to various operational needs.
- Design Importance: The choice of materials and construction details significantly impacts the pump's performance and longevity. Selecting the right design variation is essential for optimal operation in specific applications.
- Wide Applications: Applications span multiple fields, including industrial settings and medical laboratories, further demonstrating the versatility of positive displacement pumps.
- Advantages and Efficiency: Advantages like precision in fluid transfer and efficiency in handling viscous fluids reinstate their value versus alternative pumping solutions.
- Maintenance Necessity: Regular maintenance and awareness of common issues significantly enhance operational lifespan, reducing downtime and repair costs.
- Future Trends: Innovations in technology and sustainability considerations are reshaping the landscape for positive displacement pumps, paving the way for future advancements.
Ultimately, a thorough grasp of positive displacement pumps is invaluable for students, researchers, educators, and professionals. Their critical role in fluid transport cannot be overstated, and a well-rounded understanding leads to improved application, maintenance, and innovation in the field.