Understanding Liquid CO2 Flow Meters: Insights and Applications
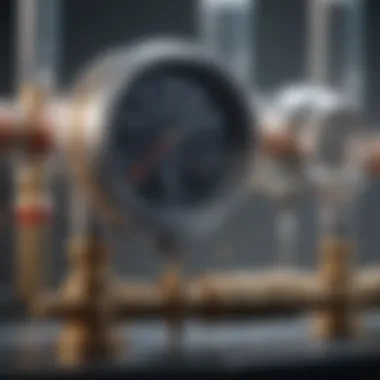
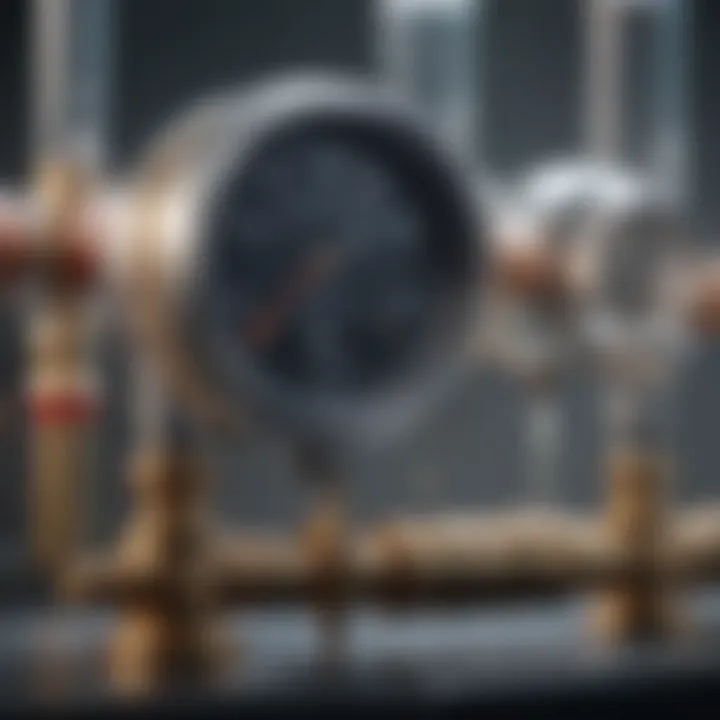
Intro
Liquid carbon dioxide flow meters are essential tools in various sectors, including food processing, beverage production, and chemical manufacturing. These instruments measure the flow rate of liquid CO2 accurately and reliably, a requirement for processes where precise gas dosing is crucial.
In the subsequent sections, this article will explore the key findings related to liquid CO2 flow meters, including their technical aspects, applications, and maintenance practices. It will delve into the methodologies employed in measuring CO2 flow, providing a comprehensive perspective necessary for industry professionals and researchers.
Intro to Liquid CO2 Flow Meters
Liquid CO2 flow meters are instruments that measure the flow of liquid carbon dioxide in various applications. Their importance spans several sectors, including the food and beverage industry, chemical processing sectors, and environmental monitoring. With a rising interest in sustainability and the efficient management of resources, these flow meters hold a critical role in ensuring accurate measurements and optimal process control.
The utilization of liquid CO2 has expanded, especially in the beverage industry where it is used for carbonation. Therefore, understanding how flow meters function, their specifications, and their applications is paramount for professionals aiming to ensure robust operational efficiency.
Definition and Importance
Liquid CO2 flow meters are devices designed to assess the flow rate of liquid carbon dioxide. Unlike gas flow meters, the measurement of liquid CO2 involves distinct physical and chemical properties, which necessitate specialized technology. The data from these meters can inform process controls and enhance productivity in various sectors.
The importance of these meters lies in their ability to provide precise data on flow rates. This is critical for production consistency, cost management, and ensuring compliance with safety standards. Accurate measurement of CO2 flow can significantly affect products, especially in industries where purity and concentration matter, such as food preservation and beverage production.
Historical Context
The early development of flow meters dates back to the industrial revolution, driven by the need for more efficient processes. Initially, the focus was on measuring gases. However, as industries discovered the advantages of liquid CO2 in refrigeration and various chemical processes, the demand for accurate flow measurement of liquids increased. The transition from mechanical to electronic measurement techniques marked a significant milestone. As technology continued to advance, the integration of digital displays and smart sensors revolutionized how flow meters operated and provided data, thereby cementing their position in modern industry.
Flow meters now not only assist in traditional applications but also play a role in innovative sectors such as greenhouse gas monitoring and carbon capture initiatives. The historical advancement of these devices underscores their vital role in a world that increasingly values efficiency and environmental care.
Principles of Operation
Understanding the principles of operation for liquid CO2 flow meters is essential for grasping how these instruments function in various applications. The effectiveness of flow measurement is heavily influenced by the methodology employed. In this section, we will explore the measurement techniques available, sensor technology, and their implications in the use of liquid CO2 flow meters.
Measurement Techniques
Mass Flow Measurement
Mass flow measurement is vital as it provides a direct measurement of the mass of liquid CO2 passing through the meter over time. This technique is particularly significant in industries where precise dosing is crucial for efficiency and safety. One key characteristic of mass flow measurement is its ability to remain unaffected by variations in temperature and pressure. This makes it a popular choice for applications involving liquid CO2, where environmental conditions can change unexpectedly.
The unique feature of mass flow meters is their reliance on the Coriolis effect. The meter consists of a vibrating tube. When liquid CO2 flows through the tube, it causes a change in the vibration frequency. This change is directly proportional to the mass flow rate, enabling accurate measurements. A notable advantage of this method is its high accuracy and rapid response time. However, it may come at a higher cost compared to other measurement types.
Volumetric Flow Measurement
Volumetric flow measurement focuses on determining the volume of liquid CO2 flowing through the meter per unit of time. This method is common in situations where monitoring the total quantity of fluid is vital, such as in beverage carbonation processes. A primary characteristic of volumetric flow meters is their ability to provide continuous flow data, making them suitable for various applications.
Volumetric flow meters often utilize positive displacement or turbine principles. This means they measure the flow by capturing a known volume of liquid and counting how often it fills. One unique benefit of volumetric measurement is its simpler design, making it potentially less expensive than mass flow technology. However, its accuracy can be compromised by changes in fluid density, which can lead to measurement inconsistencies.
Sensor Technology
Mechanical Sensors
Mechanical sensors have long been used in liquid CO2 flow measurement. They often incorporate moving parts that react to the flow of liquid. Their main contribution lies in providing simple and reliable measurements. The key characteristic of mechanical sensors is their straightforward operation, well-versed in various industrial applications.
A unique aspect of mechanical sensors is their durability and ability to function in harsh environments. They can withstand high pressures and extreme temperatures typically found in industrial processes involving liquid CO2. However, one downside is the potential for wear and tear over time, which may necessitate regular maintenance or replacement.
Electronic Sensors
In contrast, electronic sensors offer advanced features and improvements in liquid CO2 flow measurement. These sensors can provide high precision and enhanced data analysis capabilities. A key characteristic of electronic sensors is their ability to integrate with digital systems, offering real-time monitoring and control, which is becoming increasingly important in modern industries.
One significant advantage of electronic sensors is their flexibility in operational parameters. They can be calibrated for different types of liquids and conditions. However, their reliance on electronic components might pose drawbacks, such as susceptibility to environmental interference or higher initial costs. The future of flow measurement will likely favor the integration of electronic sensors, aligning with trends toward automation and data-driven decision-making in industries involving CO2.
Understanding these principles not only enhances operational efficiency but also ensures safety in handling liquid CO2 across various applications.
Through a comprehensive examination of both measurement techniques and sensor technology, one can appreciate how these factors contribute to the successful application of liquid CO2 flow meters in diverse settings.
Technical Specifications
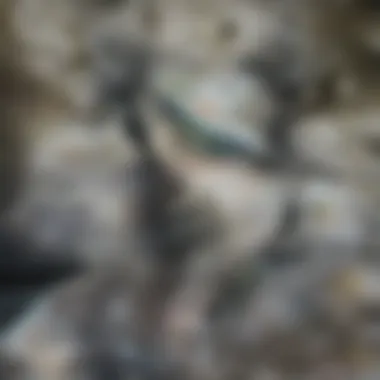

Technical specifications are essential to understanding the performance and suitability of liquid CO2 flow meters. These specifications provide valuable insights into how these instruments operate under various conditions. For engineers and industry professionals, knowing these details can inform better decisions regarding equipment selection and implementation.
Flow Rate Range
The flow rate range of a liquid CO2 flow meter is critical for determining its applicability in specific processes. This parameter indicates the maximum and minimum flow rates the meter can measure accurately. Depending on the industry and operational requirements, flow rates can vary significantly.
A broad flow rate range affords flexibility. For instance, industries such as food and beverage may require high precision in low flow situations. Conversely, chemical processing might necessitate a broader range to handle varying production rates.
- Typical flow rate ranges of liquid CO2 flow meters can span from a few liters per minute to several hundred liters per minute.
- It's important to choose a flow meter that satisfies the operational demands to ensure effective monitoring and control of processes.
Pressure and Temperature Ratings
Pressure and temperature ratings play a vital role in ensuring the reliability of a liquid CO2 flow meter. These ratings specify the conditions under which the meter can operate without risk of failure. CO2, when in liquid form, is typically under high pressure and may experience significant temperature variations.
- Pressure ratings usually range from low-pressure systems at approximately 10 bar to systems that handle upwards of 100 bar.
- Temperature ratings often vary from -30Β°C to 50Β°C. Therefore, it is crucial to select a flow meter that can withstand the specific operating environment.
Miscalculating these specifications can lead to equipment failure, resulting in downtime and costs.
Accuracy and Calibration
Accuracy is paramount in flow measurement. Liquid CO2 flow meters are expected to deliver reliable readings to facilitate precise control of operations. The specifications around accuracy often indicate a percentage of reading, which can be critical in compliance with industry standards.
Calibration procedures are equally important for maintaining the accuracy of flow meters. Using established calibration methods ensures that the readings reflect true flow rates. Regular calibration helps to detect drift in measurements and guarantees the longevity of the instruments.
- Common accuracy specifications might indicate an accuracy range of +/- 0.5% to +/- 5% of the reading.
- Calibration should be performed following a schedule based on the operational conditions and specifics of the equipment.
Regular calibration not only ensures accuracy but also mitigates the risks associated with erroneous measurements in critical processes.
Applications of Liquid CO2 Flow Meters
The applications of liquid CO2 flow meters are significant across various industries. Understanding these applications can reveal how liquid CO2 flow meters bring advantages and enhance operational efficiency in processes where accurate measurement is crucial. Their role extends beyond simple measurement; they are integral to optimizing processes, ensuring product quality, and adhering to safety standards. Through various sectors, liquid CO2 flow meters provide specific benefits that merit exploration.
Food and Beverage Industry
In the food and beverage sector, liquid CO2 flow meters are essential for maintaining product quality. Carbon dioxide plays a critical role in food preservation and carbonation. These flow meters ensure that the right amount of CO2 is used in manufacturing carbonated beverages. Precision is key here, as inconsistencies in CO2 levels can affect the taste and quality of drinks.
Additionally, liquid CO2 is utilized in freezing and chilling processes, requiring careful monitoring of flow rates. The use of flow meters allows for optimized usage of CO2, reducing waste and enhancing efficiency, which is vital given the industry's focus on sustainability.
Chemical Processing
Liquid CO2 flow meters are also prominently used in chemical processing. In this industry, CO2 serves as a solvent and refrigerant, among other purposes. Accurate flow measurement helps ensure that chemical reactions proceed under optimal conditions, directly impacting yield and safety.
Proper utilization of flow meters can help manage production lines effectively. Industries can prevent overuse or shortage of CO2, leading to better control over costs and increased profit margins.
Greenhouse Gas Monitoring
Another critical application of liquid CO2 flow meters is in greenhouse gas monitoring. With growing concerns about climate change, precise measurement of CO2 emissions is vital for regulatory compliance and environmental protection. These flow meters enable organizations to accurately track CO2 emissions, identify leakages, and ensure that emissions remain within set limits.
Reliable data from liquid CO2 flow meters aids in creating better strategies for emission reduction. This is not only important for meeting regulatory standards but also contributes to overall sustainability efforts within the industry.
The integration of liquid CO2 flow meters in various applications illustrates their role in enhancing safety, ensuring quality, and supporting environmental goals across sectors.
Selection Criteria for Flow Meters
Selecting the right flow meter for liquid CO2 measurement requires a thoughtful approach. It lies at the intersection of multiple factors that define operational efficiency and the specific needs of an industry. A proper selection of flow meters ensures accurate readings, enhances system safety, and optimizes overall processes.
Industry Requirements
Different industries have unique needs when it comes to liquid CO2 flow meters. The food and beverage sector, for instance, requires strict compliance with hygiene standards and precise measurements to maintain product quality. The chemical processing industry, on the other hand, focuses on resilience and the ability to handle corrosive materials.
Key aspects to consider include:
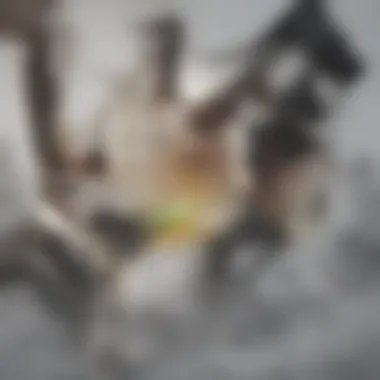
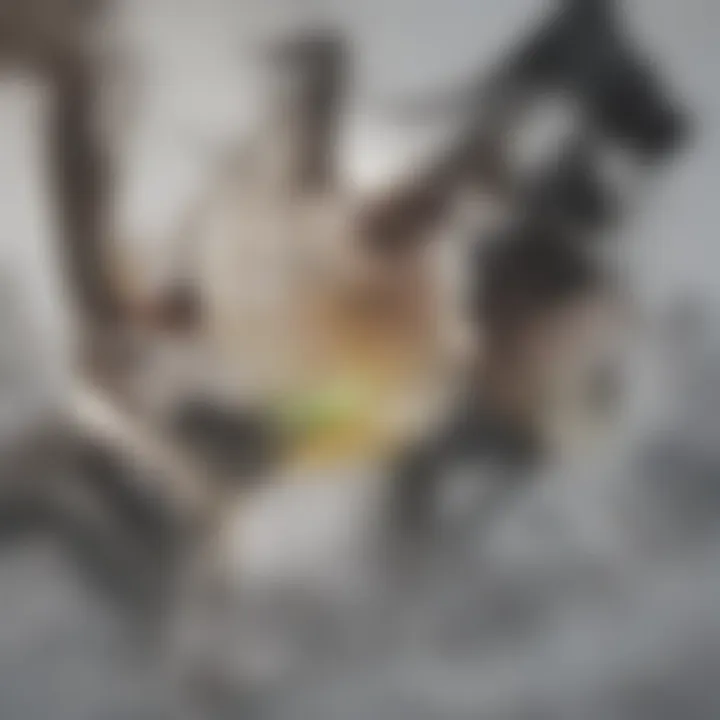
- Regulatory compliance: Ensure that the selected flow meter meets industry standards set by organizations like the FDA or EPA.
- Sealing and materials: Choose materials that withstand specific conditions, such as high pressure or temperature, depending on the application.
- Customization options: Some industries may require specialized features, allowing tailored solutions.
Understanding these requirements makes it easier to narrow down the choices effectively.
Operational Conditions
The environment in which a liquid CO2 flow meter operates plays a crucial role in its performance. Factors like temperature, pressure, and even the nature of the liquid influence device selection.
Consider these operational factors:
- Pressure levels: Ensure that the flow meter can handle the maximum pressure it will encounter.
- Temperature range: Verify that the device is rated for the ambient temperature in the operational setting.
- Flow characteristics: Understand whether the measurement will involve consistent flow or variable flow conditions, which can affect accuracy.
These operational conditions are pivotal in maintaining the integrity and accuracy of flow measurement.
Cost Considerations
Cost is always a determining factor in any purchasing decision, and flow meters are no exception. However, it is crucial not to compromise quality for a lower price.
Key points about cost considerations include:
- Initial investment: Evaluate the upfront costs associated with each model that meets the desired specifications.
- Long-term savings: Higher quality flow meters may save money over time through increased reliability and reduced maintenance costs.
- Total cost of ownership: This includes installation, calibration, and any potential downtime due to equipment failure.
Maintenance Practices
Maintaining liquid CO2 flow meters is critical for ensuring their accuracy, longevity, and reliability in various applications. These devices face unique challenges due to the physical properties of CO2 and the environments in which they operate. Proper maintenance can prevent costly downtime and the need for expensive repairs.
Routine Inspections
Routine inspections involve regular checks of the flow meter to identify any issues before they escalate. This includes visual examinations of the physical condition of the equipment, connections, and any signs of leakage. Inspecting the flow sensors for wear and tear can prevent inaccuracies in flow measurement.
Regular checks also involve assessing the electronic components and software systems for proper function. These inspections may encompass:
- Verifying connections for any signs of corrosion.
- Ensuring that seal integrity is intact to prevent gas release.
- Confirming that display units and indicators function correctly.
Establishing a schedule for these inspections, depending on the usage intensity, can safeguard the effectiveness of flow meters.
Calibration Procedures
Calibration is essential to ensure that the liquid CO2 flow meter provides accurate readings. This process involves adjusting the meter's output to match a known standard or reference. Calibration should be performed at regular intervals or whenever there is a significant change in operating conditions.
The procedures for calibration typically involve:
- Establishing the standard to compare against, which can be a certified flow calibrator.
- Running liquid CO2 through the meter at various flow rates to identify discrepancies.
- Adjusting the settings of the meter to minimize the differences between the meter's reading and the standard.
Documentation of calibration results is crucial. It provides traceable evidence of accuracy and helps in audits or quality checks.
Troubleshooting Common Issues
Despite regular maintenance, users may encounter common issues with liquid CO2 flow meters. Understanding these problems and their solutions is vital for efficient operation.
Some typical problems include:
- Inaccurate Measurements: This may stem from improper calibration, buildup in the flow path, or sensor malfunction.
- Sensor Failures: Mechanical wear or electronic failures can lead to sensor issues. Replacing sensors promptly can prevent measurement errors.
- Leakage: As CO2 is pressurized, any leakage can not only compromise measurement but also pose safety risks. Regular inspections help identify potential leak points.
Troubleshooting involves:
- Checking and recalibrating the meter if measurements cannot be trusted.
- Inspecting for signs of wear in seals and sensors.
- Engaging technical support if issues persist, potentially necessitating professional servicing.
Maintaining liquid CO2 flow meters should not be viewed as an optional task but rather a necessary commitment to quality and safety.
By adhering to diligent maintenance practices, users can elude significant operational disruptions, ensuring that the CO2 flow meters perform optimally throughout their life span.
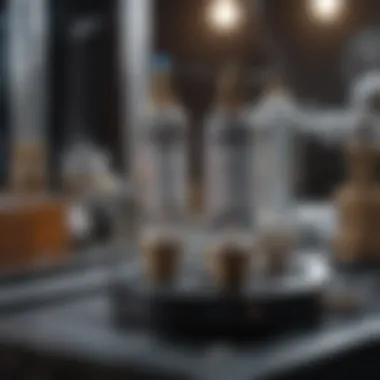
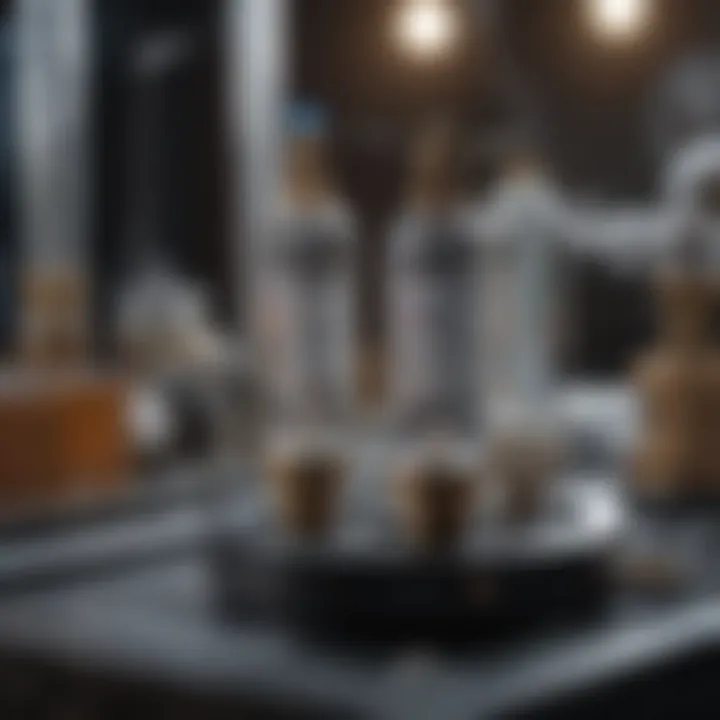
Safety Considerations in CO2 Measurement
Safety considerations are essential in the measurement of liquid CO2 due to the unique risks associated with carbon dioxide. Understanding these risks not only protects the individuals who handle this substance but also ensures the effective monitoring and management of CO2 flow systems in various applications. This section outlines key elements regarding CO2 risk factors and the necessary personal protective equipment required for safe operations.
Understanding CO2 Risk Factors
Carbon dioxide presents several risks, primarily because it is colorless and odorless, making it difficult to detect without proper instrumentation. Elevated levels of CO2 can lead to suffocation or impaired cognitive function due to decreased oxygen availability. When working with liquid CO2, the following risk factors must be considered:
- Asphyxiation: In confined spaces, CO2 can displace oxygen, leading to dangerous environments. Continuous monitoring is vital in these situations.
- Cold Burns: Liquid CO2 exists at extremely low temperatures. Contact with skin can cause frostbite or other thermal injuries, thus requiring safe handling procedures.
- Pressure Hazards: CO2 is stored under pressure, and sudden release can lead to hazardous conditions. Failure to manage pressure can result in leaks or explosions. Any system handling liquid CO2 must be designed with proper safety valves and relief systems.
In summary, awareness of these risk factors is crucial for ensuring the safety of personnel and the safe operation of equipment.
Personal Protective Equipment (PPE)
To mitigate the risks associated with CO2 measurement and handling, appropriate personal protective equipment must be worn by workers. The following PPE items are essential:
- Gas Detectors: Portable CO2 detectors alert workers to elevated gas levels, helping in immediate reactions.
- Respiratory Protection: When there is a risk of high concentrations, users should wear respirators with adequate filters designed for CO2.
- Cold-Resistant Gloves: To protect hands from cold burns, gloves specifically rated for low-temperature handling are necessary.
- Safety Goggles: Eye protection is crucial to prevent injuries from splashes when transferring liquid CO2.
- Protective Clothing: Insulated coveralls can shield against cold burns and also provide a layer against any accidental spills.
Using the appropriate PPE not only prioritizes safety but is also a regulatory requirement in many industries.
Adhering to safety measures and regulations can significantly reduce the risk of accidents and ensure that liquid CO2 handling is conducted effectively and responsibly.
Emerging Trends in Flow Meter Technology
The field of flow meter technology is rapidly evolving. Emerging trends signify shift towards increased efficiency, accuracy, and sustainability in measuring liquid CO2 flows. These advancements are crucial as industries begin to recognize the need for integrated systems that enhance productivity while minimizing environmental impact. The importance of these trends cannot be overstated, as they inform both current practice and future developments in CO2 measurement.
Digital and Smart Technology Integration
Digital transformation is fundamentally reshaping the approach to flow measurement. The integration of smart technologies allows for real-time data collection and analysis. This technology enables operators to monitor flow rates from remote locations, reducing the need for manual checks. The efficiency achieved through automation translates into lower labor costs and reduced operational errors.
Moreover, digital flow meters are equipped with advanced algorithms that enhance measurement accuracy, even under varying operational conditions. This level of precision is essential for applications where even minor discrepancies can result in significant product loss or safety hazards.
- Key benefits of digital integration include:
- Enhanced accuracy in measurements
- Improved data accessibility and monitoring
- Reduction in operational costs
- Greater operational flexibility
Implementing these systems can also facilitate predictive maintenance. By analyzing flow data trends, companies can preemptively address potential issues before they lead to failures, further optimizing performance.
Sustainability and Environmental Impact
With growing awareness of environmental issues, sustainability is a critical focus in flow meter technology. The emphasis on reducing carbon footprints drives innovations aimed at supporting eco-friendly practices. Liquid CO2 flow meters are at the forefront of this movement.
Brands are now developing meters that consume less energy while still providing reliable and accurate readings. Additionally, manufacturers are often utilizing recyclable materials in their products. These designs not only contribute to sustainability but also appeal to environmentally conscious consumers.
- Considerations regarding sustainability include:
- Utilization of energy-efficient technologies
- Adoption of recyclable materials in products
- Minimizing waste throughout the manufacturing process
The commitment to sustainability directly influences operational practices across many industries. Utilizing advanced flow meters that focus on reducing environmental impacts aligns with global efforts towards a greener future. Hence, these advancements shape not just management practices but also corporate responsibilities within various sectors.
"Integrating modern technology with sustainability practices defines the future of industrial measurement systems."
Closure
In this article, we explored the fundamental aspects of liquid CO2 flow meters, emphasizing their role across various industries. This conclusion highlights the importance of liquid CO2 flow meters as vital instruments in ensuring accurate measurement and control of carbon dioxide flow, which is crucial for many applications, including chemical processing and food production.
Summary of Key Points
Liquid CO2 flow meters are essential tools that offer a range of functionalities. They are designed to deliver precise measurements of CO2 flow, which aids in process optimizations. Key points covered include:
- Principles of Operation: Understanding how these devices function, including measurement techniques like mass and volumetric flow.
- Technical Specifications: Knowledge of flow rate ranges, pressure, temperature ratings, and accuracy requirements.
- Applications: A diverse range of uses, from the food and beverage sector to monitoring greenhouse gases.
- Selection Criteria: Factors like industry requirements, operational conditions, and cost that inform the choice of flow meter.
- Maintenance Practices: Procedures that ensure long-term reliability and performance of flow meters.
- Safety Considerations: Awareness of risk factors associated with CO2 and the importance of using personal protective equipment.
- Emerging Trends: The integration of digital technologies and sustainability practices that shape the future of liquid CO2 flow meters.
Overall, the careful consideration of these points helps professionals make informed decisions regarding the implementation and maintenance of liquid CO2 flow meters.
Future Directions
As technology progresses, the future of liquid CO2 flow meters is poised for innovative developments. Several directions are noteworthy:
- Advancements in Sensor Technology: The evolution of sensors will lead to more accurate and real-time monitoring of liquid CO2 flow.
- Increased Automation: Automation will enhance user experience and efficiency, enabling better data analysis and reporting.
- Sustainable Practices: With an emphasis on reducing carbon footprints, further interest in eco-friendly materials and methods will shape design and usage.
- Integration with IoT: The incorporation of Internet of Things (IoT) technology opens avenues for more connected and intelligent flow monitoring systems.