Shearography Testing: A Comprehensive Analysis
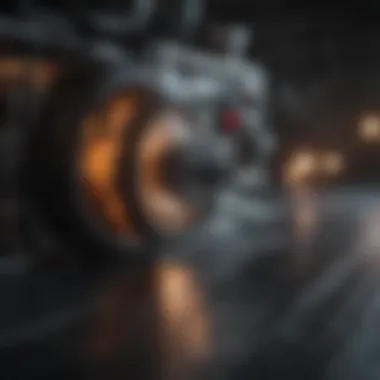
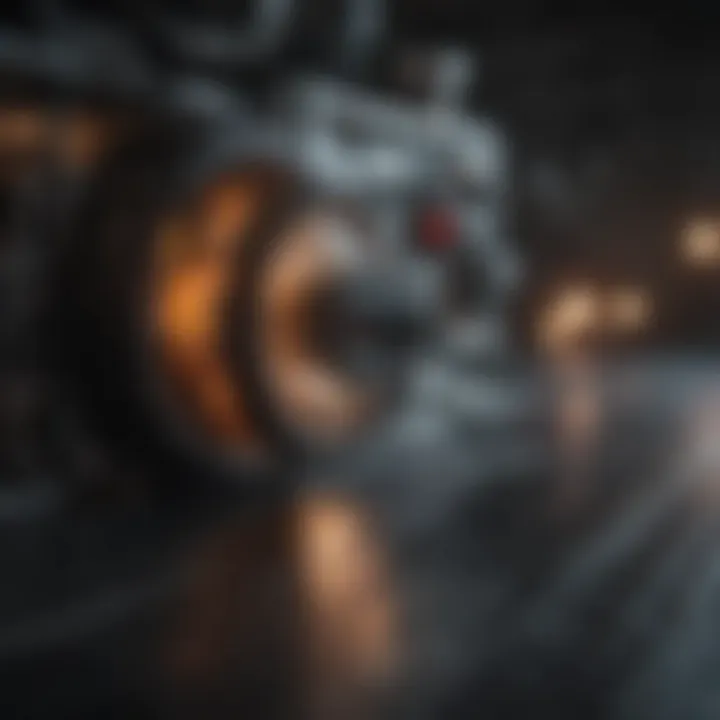
Intro
Shearography testing has emerged as a significant non-destructive evaluation method in various industrial sectors. This technique leverages laser technology to assess the integrity of materials by identifying both surface and subsurface flaws. Specifically, it has gained prominence in the aerospace, automotive, and civil engineering fields, where the integrity of materials is paramount.
Understanding shearography entails grasping its fundamental principles, methodologies, and applications. As industries continue to advance, the need for reliable testing methods becomes more pressing. This article aims to provide a thorough analysis of shearography, outlining its key aspects and contributions to modern engineering practices.
Key Findings
Major Results
- Effectiveness: Shearography is effective in detecting minute defects that could compromise material integrity, especially in composite materials.
- Versatility: The technique is applicable across multiple sectors, demonstrating adaptability to varied material types and structural configurations.
- Real-time Analysis: Shearography allows for immediate results, enhancing efficiency in inspection processes.
Discussion of Findings
The findings indicate that shearography testing is not only a valuable tool for quality assurance but also contributes to safety and reliability in critical applications. For instance, in aerospace, even the smallest flaw can have catastrophic consequences. The ability to perform inspections quickly without damaging the material makes shearography a sought-after method.
"Shearography testing bridges the gap between thorough inspection and minimal disruption, paving the way for safer industrial practices."
Methodology
Research Design
This article draws on a comprehensive review of existing literature on shearography, highlighting its principles, methodologies, and applications. The research encompasses analysis from various journals, industry reports, and case studies to provide a well-rounded understanding of the topic.
Data Collection Methods
Data was gathered through:
- Literature Review: Examining academic papers and technical manuals that detail shearography technology and its use.
- Case Studies: Analyzing real-world applications of shearography in industries such as aerospace and automotive.
- Expert Interviews: Engaging with professionals who utilize shearography in their work to gain insight regarding best practices and advancements in technology.
The combination of these methods allows for a thorough examination of shearography testing, addressing both its historical context and contemporary relevance.
Intro to Shearography Testing
Shearography testing is a pivotal non-destructive evaluation technique. This method is widely utilized in various industrial applications, particularly where material integrity is crucial. Understanding shearography is essential for professionals involved in industries such as aerospace, automotive, and civil engineering. Its ability to detect surface and subsurface flaws in composite structures highlights its importance.
Definition and Purpose
Shearography is defined as a laser-based optical technique used for assessing the integrity of materials. Its primary purpose is to identify flaws that may not be visible to the naked eye or detectable by other methods. This is particularly critical in high-stakes sectors, where even the smallest flaw can lead to disastrous outcomes.
The technique evaluates the deformation of an object under stress. When a force is applied, any existing defects will cause irregularities in the surface. Shearography measures these irregularities by analyzing fringe patterns produced when coherent light from a laser source interacts with the material being inspected. The resulting data enable engineers to make informed decisions about the safety and reliability of components.
Historical Background
The origins of shearography can be traced back to the early 1960s. During this period, researchers began exploring the potential of laser interferometry for industrial applications. The initial focus was on military applications, primarily in assessing aircraft structures. The desire for a non-destructive method surged as the aerospace industry sought reliable ways to ensure the integrity of composite materials.
Over the decades, shearography has evolved significantly. Advancements in laser technology and imaging techniques have broadened its application scope. Today, shearography is not limited to aerospace but is also prevalent in automotive sectors, manufacturing, and civil engineering. Its historical progression underscores the importance and adaptability of the technique within modern non-destructive evaluation methodologies.
Understanding shearography and its development is vital for grasping its impact in various domains. As industries continue to emphasize safety and quality, this tester remains a formidable tool for engineers and researchers alike.
Fundamental Principles of Shearography
Understanding the fundamental principles of shearography is crucial to grasp the effectiveness and functionality of this non-destructive testing method. This segment focuses on the mechanics of laser interferometry and the operational components that make shearography a preferred choice for many industries. By illuminating these principles, the article aims to convey how they bolster quality assessments in various applications, contributing to better safety and durability in materials and structures.
Laser Interferometry Basics
Laser interferometry serves as the backbone of shearography testing. This technique utilizes the interference patterns created by coherent light sources. When two or more light beams overlap, their phases combine, creating a pattern that visualizes minute changes on a material's surface. This property is vital as it allows operators to identify even the smallest deformations or flaws.
In shearography, lasers like helium-neon or Nd:YAG produce precise and stable light, ensuring reliable measurements. The sensitivity of this method is its key characteristic. It can detect mechanical displacements as small as a few nanometers, making it particularly useful in evaluating advanced materials.
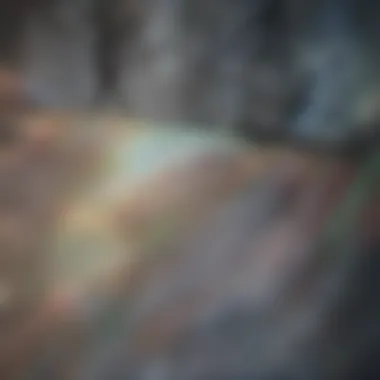
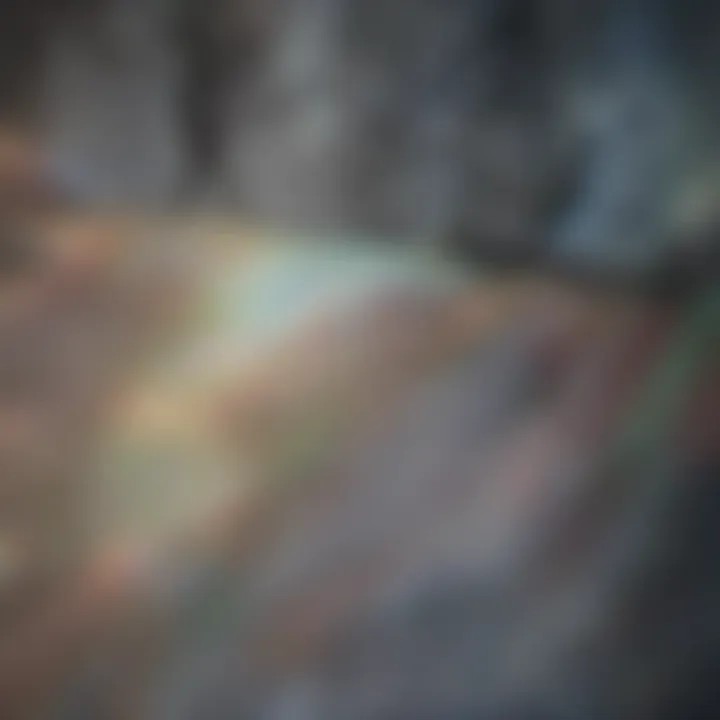
Applications span across aerospace and automotive sectors, where high reliability is non-negotiable. The detailed data obtained through laser interferometry not only enhances flaw detection capabilities but also supports maintenance strategies in these critical fields.
Shearography Mechanism
Shearography employs a systematic mechanism that includes the laser source, optical setup, and detection methods. Each part plays a significant role in achieving accurate and efficient results.
Laser Source
The laser source is a critical element in producing coherent light essential for interferometric measurements. The choice of laser, such as Nd:YAG, is common because it provides a powerful output that has good penetration, ideal for examining thick materials. Its coherence length ensures that the interference patterns remain stable, which is necessary for accurate measurements.
Additionally, the wavelength of the laser contributes to the resolution of the test. Shorter wavelengths can detect finer details, which is an advantage in applications where precision is paramount. However, the higher energy output can sometimes create safety concerns, necessitating careful handling and protective measures during testing.
Optical Setup
The optical setup is designed to manipulate the laser beam effectively. This setup includes beam splitters, lenses, and mirrors, which help direct the laser to the target surface and collect the reflected light.
One key characteristic of the optical setup is its simplicity and adaptability. The setup can be modified to fit various test scenarios, making it versatile for different types of materials and configurations. However, this adaptability can also lead to challenges, as improper alignment can result in inconsistent data. The arrangement must be meticulously calibrated to obtain reliable results, emphasizing the skill required in setting up the equipment properly.
Detection Methods
Detection methods in shearography involve capturing and interpreting the interference patterns produced during testing. Common approaches involve CCD cameras that can quickly record high-resolution images of fringe patterns.
The ability to analyze dynamic changes in the material during testing is one of the primary advantages of these detection methods. By observing changes in real-time, operators can make immediate assessments regarding the integrity of the material being evaluated. However, the choice of detection equipment can also impose limitations; lower-quality cameras may not provide the necessary resolution to identify subtle defects, impacting the overall effectiveness of the shearography test.
Technical Methodology
The technical methodology in shearography testing forms the backbone of its application. It incorporates a systematic approach to setup, data acquisition, and analysis, ensuring precise and reliable evaluations of potential flaws. Understanding each component allows professionals to harness this non-destructive evaluation technique effectively. The methodology brings together various elements that emphasize accuracy and efficiency in detecting material defects.
Setup Requirements
Before initiating shearography testing, specific setup requirements must be met. These include the selection of appropriate laser systems and the configuration of optical components. The environment should be controlled to minimize external influences on results. This includes ensuring stable couplings between the laser and the material surface. Proper alignment of the optical setup is also crucial.
Data Acquisition Techniques
The data acquisition techniques are vital for capturing the necessary information during shearography testing. These techniques can be categorized into static or dynamic shearography.
Static Shearography
Static shearography focuses on capturing the fringe patterns of a material under controlled conditions. The key characteristic is its ability to detect flaws without movement. It is a beneficial method because it provides a clear snapshot of potential defects. Static shearography is popular in situations where materials can be inspected without subjecting them to operational conditions.
A unique feature of static shearography is that it can achieve high precision in detecting even minute cracks or inconsistencies in material structure. However, it may not be suitable for all applications. The lack of dynamic response might miss anomalies that only manifest under stress or strain.
Dynamic Shearography
Dynamic shearography, on the other hand, assesses materials under operational conditions. It uses fluctuating loading methods to evaluate the material's response in real-time, making it a preferred choice for industries where materials undergo constant stress. The key characteristic of this technique is the ability to capture both surface and subsurface defects in actual operational scenarios.
Dynamic shearography's unique ability is its responsiveness to changing conditions, which provides insight into how materials behave under varying stresses. However, it demands highly controlled environments to reduce the variables that can obscure results. Consideration of these factors is essential in making it an effective tool for defect detection.
Data Analysis and Interpretation
Data analysis in shearography testing is crucial for interpreting the captured images accurately. It involves sophisticated techniques to convert fringe patterns into meaningful information about material integrity.
Fringe Pattern Analysis
Fringe pattern analysis is a core part of interpreting shearography results. This process involves examining the fringe patterns created by laser interference to identify imperfections in a material. The key characteristic is its ability to visual and quantify deviations from the ideal condition. This analysis gives a clear view of the condition of the material being tested.
Fringe pattern analysis is beneficial because it allows for a non-intrusive examination, providing detailed insights into defect location and size. However, it can be complex and requires skilled personnel for effective interpretation.
Image Processing Techniques
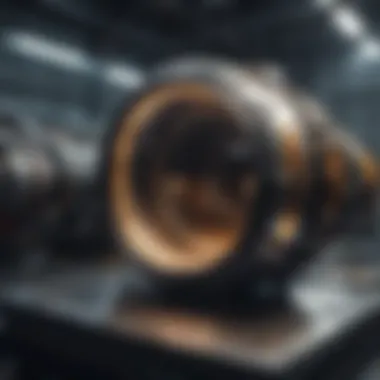
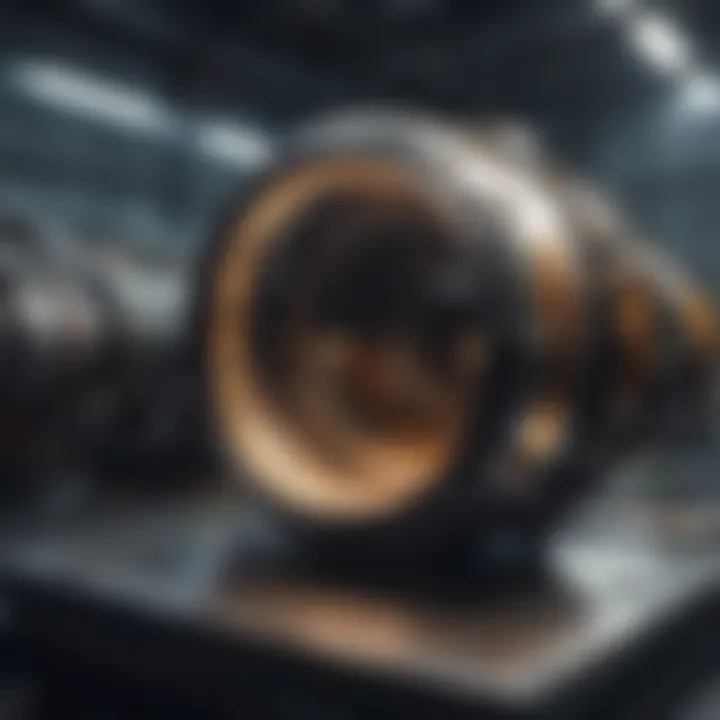
Image processing techniques enhance data analysis in shearography testing. These methods apply algorithms to enhance the clarity and interpretability of the captured fringe patterns. The key characteristic of image processing is its ability to manipulate data for better visual representation.
These techniques simplify the interpretation process, making them widely favored in shearography testing. However, the reliance on software can introduce risks, such as potential misinterpretation of enhanced images. Awareness of such limitations is important for maintaining the integrity of the testing process.
Applications of Shearography Testing
Shearography testing is a crucial tool in non-destructive evaluation across several industries. Its effectiveness in identifying flaws in materials without causing damage plays a significant role in enhancing safety and performance. The use of shearography spans various sectors, each with unique requirements and considerations. This section will detail the significance of shearography in the aerospace industry, automotive sector, civil engineering, and manufacturing processes.
Aerospace Industry
In the aerospace sector, shearography testing is utilized to ensure the integrity of critical components such as wings, fuselage, and engine parts. The lightweight materials commonly used in aviation, like composite structures, require specific methods to detect flaws without compromising the material's integrity. Shearography's ability to detect delaminations, micro-cracks, and voids in these structures makes it invaluable. Furthermore, the technique supports compliance with strict safety regulations mandated for commercial and military aircraft.
Automotive Sector
The automotive industry benefits significantly from shearography testing, particularly in the assessment of composite components and assemblies. With the rising use of advanced materials to improve vehicle efficiency and safety, the demand for effective quality control methods has increased. Shearography serves this need by providing quick and accurate evaluations of structural integrity. It helps ensure that parts such as body panels and structural reinforcements meet quality standards and perform reliably throughout their lifespan. By identifying defects early, manufacturers can avoid costly recalls and ensure consumer safety.
Civil Engineering and Infrastructure
In civil engineering, shearography testing finds applications in evaluating the health of infrastructure, including bridges and buildings. It helps engineers detect subsurface defects, voids, and structural anomalies that may not be visible through traditional inspection techniques. With increasing concerns about aging infrastructure and the potential for catastrophic failures, implementing shearography as a regular maintenance tool can provide early warnings of problems. This proactive approach is essential for preserving public safety and extending the lifespan of critical structures.
Manufacturing Processes
Within manufacturing processes, shearography aids in the quality assurance of products and components. It is particularly useful in industries where precision is paramount, such as aerospace and automotive manufacturing. By integrating shearography into production lines, manufacturers can perform real-time inspections and ensure that any defects are identified and addressed immediately. This continuous monitoring not only improves product quality but also optimizes production efficiency.
Shearography testing minimizes the risk of failures and enhances safety across various applications, making it a vital tool in modern industry.
Advantages of Shearography Testing
Shearography testing presents numerous advantages that make it a preferred non-destructive evaluation method across various industries. A detailed understanding of these benefits reinforces the importance of shearography in ensuring material integrity. This section outlines the key elements that highlight the value of shearography testing.
Non-Destructive Nature
One of the primary advantages of shearography testing is its non-destructive nature. Unlike traditional testing methods, shearography does not compromise the integrity of the material being examined. This is essential, especially in industries where maintaining the structural integrity of components is paramount. By using optical techniques without physically altering the material, shearography allows for repeated testing and monitoring over a product's lifecycle.
This characteristic significantly enhances its usability. For instance, aerospace components, often made from sensitive composites, can undergo rigorous testing without the risk of inducing damage. This capability does not just preserve the material for future use; it also saves costs associated with repairs or replacements.
Sensitivity to Flaws
Another critical advantage of shearography is its sensitivity to a wide range of flaws. This method effectively detects surface and subsurface defects, including cracks, delaminations, and voids, which traditional methods may overlook. Shearography relies on laser technology to analyze minute changes in the surface structure when the object is subjected to stress or deformation.
The high-resolution data obtained from shearography provides a comprehensive view of the material's condition. Professionals can identify potential failures before they escalate, thus ensuring safety and reliability. Furthermore, advancements in shearography technology continuously improve detection capabilities, helping industries maintain high-performance standards.
Real-Time Result Analysis
Shearography testing also enables real-time result analysis, which is crucial for fast decision-making. As the process generates and analyzes data almost instantaneously, it facilitates prompt identification of issues. This aspect is particularly beneficial in high-stakes environments, such as manufacturing and inspection, where time is often of the essence.
Real-time analysis allows for immediate corrective actions if flaws are discovered. Such timely intervention can significantly reduce downtime and associated costs. It also contributes to better workflow efficiency, enabling companies to maintain productivity while ensuring quality.
Overall, the advantages of shearography testing—its non-destructive nature, sensitivity to flaws, and ability to provide real-time results—underscore its significance in various industries, leading to enhanced safety and quality assurance.
Limitations and Challenges
Shearography testing, despite its advantages, does come with certain limitations and challenges. Understanding these factors is crucial for professionals and researchers alike. Awareness of these limitations can guide their practical applications and improvement efforts.
Surface Preparation Requirements
The requirement for proper surface preparation is one of the most pronounced limitations of shearography testing. A clean and smooth surface is necessary for optimal results. Contaminants like dirt, oil, or paint can interfere with laser coherence and accuracy. These elements can generate misleading readings, leading to misinterpretation of test results. Therefore, time-consuming preparation measures are often needed before testing.
Professionals must take care that the work piece is adequately cleaned and, if required, treated. This ensures that the shearography testing is reliable and the data gathered is useful for analysis.
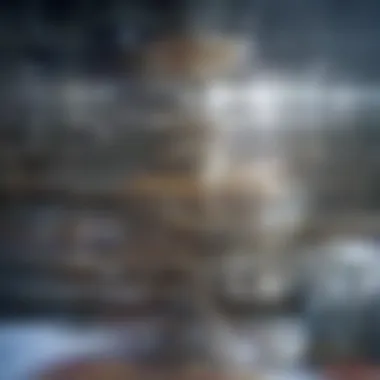
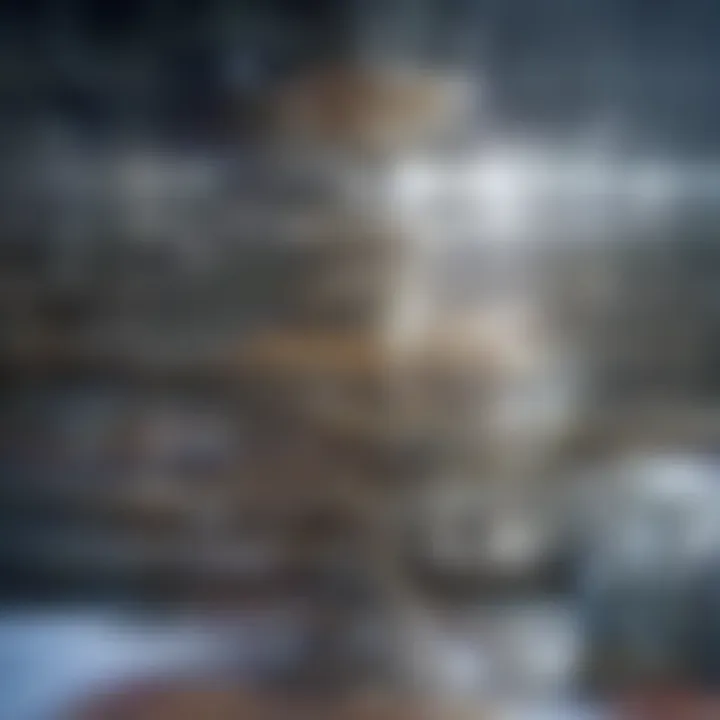
Material and Geometry Restrictions
Material and geometry restrictions also present significant challenges. Shearography testing is effective on certain materials but less reliable on others, especially when there are non-homogeneous materials or complex geometries. For instance, highly reflective surfaces can distort the laser image, while very absorbent materials can absorb too much laser energy. This can yield poor results. Furthermore, the part's geometry can affect how the stress is applied, and subsequently, how defects manifest. Therefore, choosing suitable materials and geometries is critical to achieving accurate defect detection.
Environmental Sensitivity
Another limiting factor involves environmental sensitivity. Shearography testing typically requires controlled conditions. Environmental factors such as temperature fluctuations, ambient light interferences, and vibrations can impact the reliability of test results. For example, minor temperature changes can induce strain on the materials, affecting the laser's performance. Professionals must, therefore, ensure that the testing environment is stable to maximize the accuracy of their readings.
"Understanding the limitations and challenges of shearography testing enhances its efficacy in various industrial contexts."
Recent Advancements in Shearography Technology
Recent advancements in shearography technology have significantly enhanced its capabilities and applications. As industries demand higher efficiency and precision, the evolution of shearographic methods has addressed these needs through improved techniques and integration with digital technologies. Understanding these advancements is crucial in maximizing the benefits they bring to various fields like aerospace, automotive, and civil engineering.
Integration with Digital Technologies
The integration of digital technologies has brought a new dimension to shearography testing. Modern systems utilize sophisticated software that enables real-time data analysis, making it easier to identify defects swiftly. This integration allows for the combination of shearography with computer-aided design (CAD) and simulation software, streamlining workflows and enhancing accuracy.
- Automation: Automation in data acquisition has become a reality. Advanced systems now allow for automated scanning of parts, reducing human error and improving repeatability.
- Data Management: The capacity to manage and store large volumes of data has improved. This enables more comprehensive analysis over time, making it feasible to compare different test results and track the health of components.
- Machine Learning: Machine learning algorithms are starting to be employed to interpret data more effectively. These technologies can predict failure points and identify patterns that were previously unnoticed.
Improved Imaging Techniques
The imaging techniques utilized in shearography testing have also seen considerable advancements. Enhanced imaging provides clearer and more detailed representations of defect structures.
- High-Speed Cameras: The use of high-speed cameras allows for capturing rapid changes in the material under stress, which is vital in dynamic shearography applications. This can provide insights into transient behaviors that are critical for understanding material stability.
- Multi-Wavelength Interferometry: This method has been developed to improve sensitivity by evaluating materials at different wavelengths. This enables better detection of both surface and subsurface irregularities.
- 3D Shearography: The evolution of three-dimensional shearographic techniques provides a more detailed view of the internal structures of components, allowing for more comprehensive assessments compared to traditional 2D methods.
The advancements in shearography technology have markedly improved the accuracy of flaw detection and assessment in various materials, promoting safety and reliability.
With these recent advancements, shearography continues to elevate its status as a vital non-destructive evaluation method. As industries embrace these technologies, the applications and effectiveness of shearography will likely expand, ensuring its relevance in an evolving technological landscape.
Future Perspectives
As technology evolves, the future of shearography testing appears promising. Understanding the future perspectives allows industry professionals and researchers to anticipate changes. This section examines research directions and potential industry trends that could shape the evolution of shearography methods.
Research Directions
Research in shearography testing is vital to its development. Novel methodologies and improvements in existing technologies can enhance detection capabilities. Some focus areas include:
- Advanced Algorithms: Developing algorithms that improve image processing can result in higher defect detection rates.
- Integration with Artificial Intelligence: Utilizing AI may help analyze patterns in data, making detection even more efficient.
- Material Science Advances: Studying new materials and composites can expand shearography’s applicability. Insights into how different materials respond to shearography testing will enhance its scope.
- Real-Time Monitoring Systems: Researching systems that enable real-time analysis will drastically improve operational efficiency in various sectors.
Each direction offers substantial potential. By concentrating on these areas, the reliability and effectiveness of shearography testing could see significant growth.
Potential Industry Trends
Industry trends directly influence how shearography testing is adopted across sectors. Several key trends are emerging:
- Automation and Robotics: Increased use of automated systems for shearography testing may streamline processes and enhance precision.
- Integration with 3D Printing: As additive manufacturing grows, shearography may play a crucial role in quality assurance, ensuring structural integrity of 3D-printed components.
- Environmental Awareness: There is a growing demand for non-destructive testing methods like shearography that align with sustainability goals. Its non-invasive nature makes it an appealing option.
- Government Regulations: Stricter regulations on safety and quality in industries like aerospace and automotive will drive the adoption of shearography for regular inspections.
In summary, the future of shearography testing is contingent on innovations within the field and the industries it serves. By understanding these trends and directions, professionals can prepare for shifts in methodology and application, ensuring continued resonance of shearography in critical assessment practices.
"Staying ahead in shearography testing means embracing innovation and adapting to industry demands."
Ending
In this section, we will explore the significance of conclusions drawn from the extensive study of shearography testing. A well-structured conclusion synthesizes the essential insights presented throughout the article, highlighting both the theoretical and practical aspects of the topic. Shearography testing plays a vital role in ensuring safety and reliability across various industries, demonstrating that non-destructive evaluation methods are indispensable.
Summary of Key Findings
The article has established several key findings about shearography testing:
- Non-destructive testing: Shearography's ability to inspect materials without causing damage is crucial for maintaining structural integrity, especially in fields like aerospace and automotive.
- High sensitivity: This testing technique is particularly sensitive to flaws, extending its use to complex composite materials that may not be easily assessed using traditional methods.
- Real-time results: Data is quickly analyzed, allowing for immediate decisions in manufacturing processes or structural integrity assessments.
- Broader applications: Industries have increasingly adopted this testing method for quality assurance and maintenance, demonstrating its versatility.
This summary encapsulates the fundamental insights into shearography testing, reinforcing the value of further research and application in various sectors.
Final Thoughts on Shearography Testing
This balanced understanding of strengths and challenges will ensure that shearography testing continues to be a trusted tool in identifying and mitigating risks in material integrity. As research directions unfold and industry trends evolve, the significance of shearography will likely expand, affirming its place as a trusted evaluation tool.