Defining Process Safety Management: A Comprehensive Overview
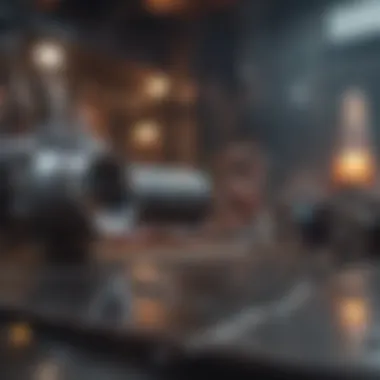
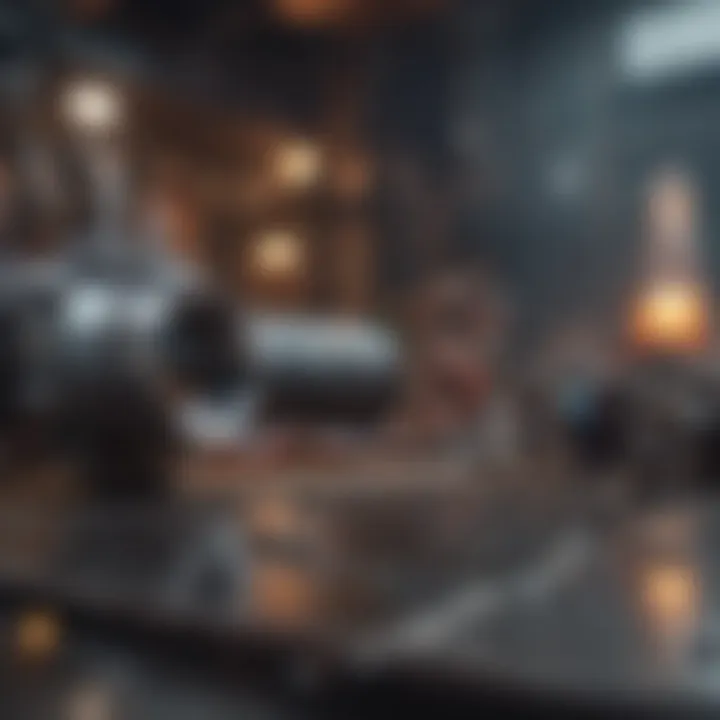
Intro
Process safety management (PSM) is a critical component of safety practices across industries that handle hazardous materials. It goes beyond just adhering to regulatory demands; it embodies a holistic and proactive approach to minimizing risks associated with industrial processes. Defining what process safety management entails involves not only understanding the definitions but also grasping the underlying principles that guide effective implementation. In this overview, we'll dive into its significance, methodologies, and the evolving landscape as we adapt to new technologies.
Key Findings
Major Results
In recent years, thorough evaluations of process safety management systems have yielded several insights:
- Increased Compliance Rates: Organizations with robust PSM programs demonstrated higher compliance with safety regulations, which ultimately improved their operational reputation.
- Reduced Incidents: Evidence suggests that companies prioritizing PSM have experienced a decline in hazardous incidents, resulting in both financial savings and enhanced employee morale.
- Enhanced Training Programs: Effective training regimes tied to PSM principles have improved workers' understanding of hazards and emergency response—paving the way for a more safety-conscious workforce.
Discussion of Findings
The data underscores one fundamental truth: PSM is not merely a checklist compliance tool; it is a culture of safety that echoes throughout an organization. Employees are more engaged when they understand the "why" behind their safety protocols. Take, for example, a chemical plant where workers are trained not just on operational procedures, but on hazard recognition as well. The result is a workforce that is informed and vigilant.
"Investing in PSM means investing in the safety of your people and the integrity of your company."
Methodology
Research Design
This article employs a qualitative research design to capture the comprehensive nature of process safety management. By examining case studies, industry reports, and expert testimonials, we map out the essential components and functions of PSM.
Data Collection Methods
Data was collected through multiple avenues including:
- Interviews with Industry Professionals: Conversations with safety managers and engineers provided real-world insights into PSM practices.
- Review of Regulatory Documents: Analyzing safety regulations from different agencies helped identify the legal framework that shapes PSM.
- Case Studies: Detailed examination of organizations that exemplify best practices in PSM highlighted successes and areas for improvement.
In this exploration, we aim not just to inform but to inspire a shift in mindset regarding safety management—creating environments that prioritize well-being for all stakeholders involved.
Understanding Process Safety Management
Understanding Process Safety Management (PSM) stands as the cornerstone in ensuring safety and efficiency across various industries where hazardous materials are involved. The gravity of this concept is not merely academic; it echoes in the everyday practices of professionals committed to protecting lives and the environment. By grasping what PSM entails, stakeholders can mitigate risks and prevent catastrophic incidents, which, in turn, fosters a safer workplace and enhances operational integrity. The essence of PSM revolves around systematic protocols that identify, evaluate, and control the hazards associated with processes involving chemicals.
Process Safety Management Defined
At its core, Process Safety Management is a disciplined framework that encompasses the management of hazards associated with processes involving hazardous substances. According to the U.S. Occupational Safety and Health Administration (OSHA), PSM is defined by its focus on preventing the release of any substance defined as a "highly hazardous chemical" in a process. This isn't just about compliance; it's about cultivating a culture where safety isn't an afterthought but a primary focus.
PSM incorporates several critical elements, designed to work cohesively:
- Safety Information: Detailed knowledge about the chemicals and processes in use.
- Hazard Analysis: Systematic approaches to identify and analyze potential hazards.
- Operating Procedures: Clearly defined protocols for operating safely.
- Training and Competence: Ensuring workforce is skilled and knowledgeable.
In today's fast-paced work environments, the significance of PSM can't be overstated. It's about proactively managing risks rather than reactively dealing with incidents. PSM provides an organized method to oversee these risks, leading to improved safety performance and operational reliability.
Historical Context of PSM
The roots of Process Safety Management stretch back to several catastrophic events in industrial history, notably the 1984 Bhopal disaster in India, which remains a stark reminder of the potential consequences of poor safety management. This disaster was pivotal, resulting in the loss of thousands of lives and prompting worldwide scrutiny of chemical safety regulations.
In the aftermath, regulatory bodies like OSHA took significant heed, leading to the establishment of the Process Safety Management Standard in 1992. This was a groundbreaking moment that integrated various elements of process safety, enhancing both national and global standards for safety management. Over the years, as industries evolved with new technologies and methodologies, so did PSM. It adapted to include emerging threats and tailored its approaches accordingly.
"Not learning from history not only leaves us repeating mistakes, but also stunts our ability to progress in our safety measures."
Today, PSM is global. Countries and regions have adopted their protocols, often interlacing international frameworks with localized needs. As such, understanding the historical context of PSM provides crucial insights into its current frameworks and practices.
In summary, Process Safety Management is not just a regulatory requirement; it is a vital aspect of operational success and employee safety within industries dealing with hazardous materials. Understanding its principles and historical backdrop equips professionals with the tools necessary to foster a culture of safety that prioritizes prevention over confrontation. This foundation will set the stage for exploring the core elements and regulatory frameworks guiding PSM, as well as the cultural changes and technological advancements shaping its future.
Core Elements of Process Safety Management
When companies operate complex processes, there’s no underestimating the role of Process Safety Management (PSM). It’s really not just a checkbox operation or another safety program thrown into the mix; the core elements of PSM form a framework that ensures operations can run smoothly while also safeguarding people, environment, and property. Here’s a deeper look into what makes these core elements vital and how they contribute to overall safety and operational excellence.
Safety Information
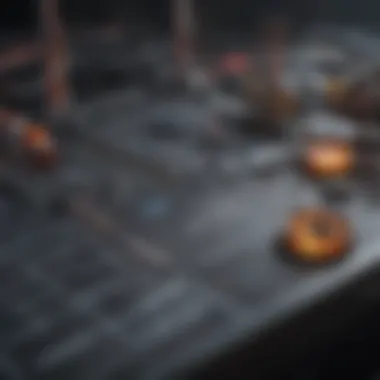
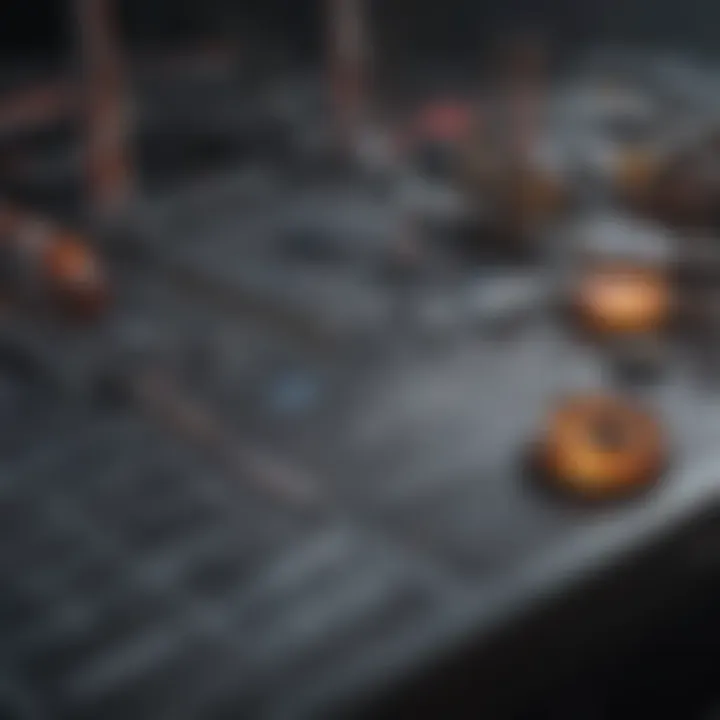
The foundation of any strong PSM program is safety information. This element entails gathering and maintaining comprehensive data about the processes and equipment in use. It covers everything from chemical properties to equipment specifications to safety-related operating conditions.
Why does it matter? Well, think of it this way: without accurate information, a ship may as well set sail without a map. Companies must ensure this information is not only accurate but also accessible to those who need it most.
Inventory data, process flow diagrams, and operating manuals all play a critical role in helping employees understand the hazards associated with their work. Regular updates and reviews ensure that the information remains relevant against evolving risks.
Hazard Analysis
Every safety program recognizes the necessity of understanding risks. Hazard analysis goes beyond just listing potential issues - it's about deeply analyzing risks and addressing them.
Types of Hazard Analysis
There are several types of hazard analysis that companies can implement.
- What-If Analysis: A brainstorming technique where teams consider all possible scenarios and their consequences. It keeps discussions flowing and often reveals overlooked risks.
- HAZOP (Hazard and Operability Study): A structured method aimed at uncovering how deviations from the design intent could lead to hazards. This is a thorough process that's especially powerful due to its collaborative nature.
- FMECA (Failure Mode, Effects, and Criticality Analysis): Focuses on potential failure modes in a system and their impact on the overall operation. This method stands out due to its meticulous attention to detail, ensuring nothing slips through the cracks.
Each type brings its unique characteristics and value to a PSM program, helping firms pinpoint vulnerabilities effectively.
Methods for Conducting Analyses
Once the types of analysis are chosen, the next step is to delve into the methods for conducting these analyses.
- Qualitative Risk Assessment: This method assesses risks based on qualitative criteria rather than numerical data. It's quick and often less resource-intensive, but it may skip over nuances in complex environments.
- Quantitative Risk Assessment: This rigorous approach utilizes numerical data to compute probabilities and potential impacts. While it provides detailed insight, it also demands significant resources and expertise.
Choosing the right method rests on various factors including resources, the complexity of the processes involved, and the regulatory expectations.
Operating Procedures
Strong operating procedures are like the blueprint to a safe operation. They dictate how work should be carried out and help ensure everyone’s on the same page. Each set of procedures should be clear, well-documented, and accessible to all workers. Regular reviews of these procedures are necessary to keep them relevant and effective as conditions evolve.
Training and Competence
A robust training program is paramount. Employees must be equipped not only with the knowledge of how to perform their tasks but also with an understanding of the associated hazards. This isn’t simply a once-a-year training session but ongoing education that engages employees at all levels. It’s about building a knowledgeable workforce that can recognize hazards and act accordingly.
Mechanical Integrity
Mechanical integrity assuredly plays a crucial role in ensuring that all equipment functions as intended. Regular inspections, maintenance checks, and repairs help avert unforeseen malfunctions that could escalate into hazardous situations. Establishing consistent protocols for monitoring mechanical integrity can safeguard against equipment failure.
Management of Change
In the ever-evolving landscape of industries, changes are inevitable; however, how a company approaches those changes makes all the difference. Effective management of change procedures ensures that any alterations to processes or equipment are evaluated for potential risks beforehand. This proactive measure helps keep unforeseen hazards at bay.
Incident Investigation
Understanding what went wrong after an incident is pivotal for preventing future occurrences. A thorough incident investigation digs into the root causes rather than just scratching the surface. Lessons learned from these investigations should be integrated back into the PSM framework, continuously refining processes and enhancing safety.
Emergency Planning and Response
Preparedness is critical in the event of an incident. A solid emergency response plan must be in place, covering everything from evacuation procedures to communication strategies. Regular drills can help prepare employees, ensuring they're ready to respond quickly and effectively.
Auditing and Performance Measurement
Lastly, regular auditing and performance measurement are essential to ensure that PSM practices are effective and being followed correctly. By benchmarking performance against regulatory requirements or organizational goals, businesses can identify areas for improvement and ensure that they meet established safety standards.
Regulatory Framework for Process Safety Management
A robust regulatory framework is crucial for effective Process Safety Management (PSM). It lays the groundwork for safety practices and provides a specific structure through which organizations can implement safety measures. Complying with regulations is more than just a legal requirement; it ensures that organizations prioritize the safety of their operations and employees. In an environment rife with potential hazards, a clear regulatory framework helps in mitigating risks and safeguarding against accidents.
The framework comprises various standards, guidelines, and regulations tailored to different industries. As such, having a comprehensive understanding of these regulations enables organizations to streamline their safety management processes. The benefits derived from a thorough PSM regulatory framework include:
- Enhanced accountability: Regulations define roles and responsibilities, ensuring that key personnel are held accountable for safety practices.
- Consistency in practices: A clear framework promotes uniform safety standards across an organization, reducing discrepancies that could lead to incidents.
- Improved risk management: By aligning with regulatory guidelines, organizations can identify, assess, and control risks more effectively.
Here is a look at the two major components constituting the regulatory framework for PSM: international standards and compliance mechanisms.
International and National Standards
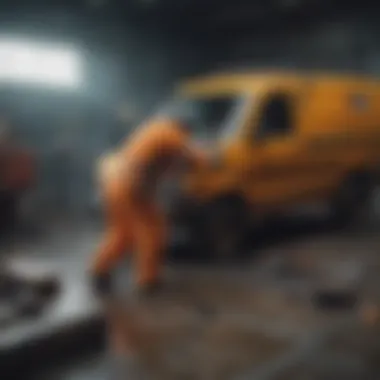
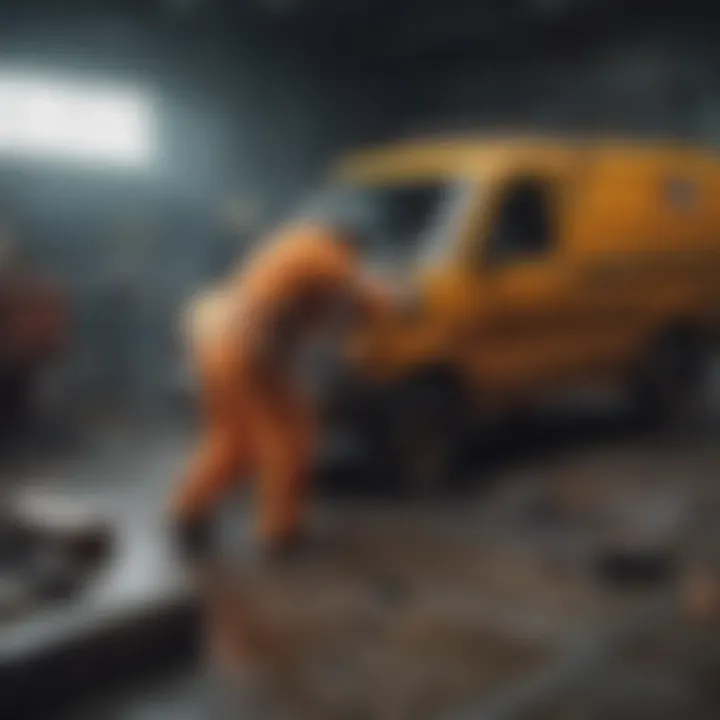
The foundation of any regulatory framework rests upon established standards, both at the international and national levels. Various organizations have developed guidelines that inform best practices for process safety across different sectors.
For instance, the International Organization for Standardization (ISO) published ISO 45001, which focuses on occupational health and safety management systems. This standard pushes companies to exceed minimum requirements and remain proactive about workplace safety. Similarly, the Occupational Safety and Health Administration (OSHA) in the United States has developed several regulations directly impacting PSM, such as the Process Safety Management Standard (29 CFR 1910.119).
These standards emphasize the need for:
- Hazard identification and risk assessment processes.
- Effective communications regarding safety practices and training programs.
- Continuous monitoring of safety measures to ensure compliance with the laid-down regulations.
However, simply complying with these standards is not enough. Organizations need to adopt a mindset that values safety as an integral part of their operations. Doing so can promote a culture of safety that not only reinforces compliance but also fosters innovation and continuous improvement.
Compliance and Enforcement Mechanisms
Once established, the effectiveness of PSM regulatory frameworks hinges on compliance and enforcement mechanisms. Such mechanisms serve as safeguards, ensuring that organizations adhere to safety standards and follow through on their commitments to risk management.
Regulatory agencies and organizations often utilize a combination of inspections, audits, and monitoring systems to ensure compliance. This could include:
- Regular audits: To assess whether the PSM processes are in line with the required regulations.
- Enforcement actions: Legal consequences imposed on organizations that neglect their safety responsibilities, such as fines or penalties.
- Incentive programs: Many regulatory bodies offer programs to reward organizations with exemplary safety records, fostering a competitive atmosphere where safety is prioritized.
Moreover, the role of employees is paramount in ensuring compliance. Encouraging a culture where every worker feels responsible for safety can lead to remarkable improvements in adherence to regulations. Employees should be equipped with adequate training and knowledge about the regulatory requirements to help bring about a safer work environment.
In summary, a solid regulatory framework for Process Safety Management drives accountability and enhances safety practices across organizations. Adhering to international and national standards, coupled with efficient compliance mechanisms, creates a resilient culture that prioritizes safety above all.
Cultural Aspects of Process Safety Management
Cultural aspects of Process Safety Management (PSM) play a critical role in ensuring safety standards and practices are adhered to within an organization. It is not merely the procedures and regulations that dictate the success of a PSM program, but the underlying culture that supports these practices. A positive safety culture encourages employees to prioritize safety, communicate openly about risks, and engage in proactive behaviors that enhance overall risk management.
Organizations can leverage cultural aspects to create a supportive environment where safety is everyone's responsibility. This is vital because, when employees feel their contributions toward safety are valued, they are more likely to engage fully in safety initiatives. The importance of cultivating a strong safety culture cannot be overstated, as it directly influences the effectiveness of PSM.
The Role of Leadership in PSM
Leadership plays a pivotal role in steering the safety culture of an organization. Leaders set the tone for how safety is perceived and prioritized. When they demonstrate commitment to safety—through their actions, communications, and decisions—it inspires employees to do the same. For example, a manager who actively participates in safety drills sends a clear message about the importance of safety protocols. On the other hand, if leaders overlook safety issues, employees might perceive safety as an afterthought, leading to potential hazards.
"Effective leadership is not just about following rules, it’s about embodying the spirit of safety in every action and decision made."
A safety-oriented leadership style is characterized by transparency, open communication, and accountability. This not only fosters trust but also builds a resilient safety culture. Engaging with employees through safety committees or regular meetings reinforces the message that their input is valued.
Building a Safety Culture
A safety culture doesn’t emerge overnight; it requires continuous effort and the active involvement of all employees. To build this culture, organizations should focus on two significant aspects—Employee Engagement and Continuous Improvement Strategies.
Employee Engagement
Employee engagement is the cornerstone of a vibrant safety culture. When employees are engaged, they are more inclined to recognize and report hazards, suggest improvements, and participate in safety-related training programs. Key characteristics of effective employee engagement include:
- Active Participation: Employees need to feel that their voices matter. Encouraging them to contribute to safety discussions makes them part of the solution.
- Training Opportunities: Providing ongoing training helps employees feel equipped to handle potential safety issues. This builds confidence in their roles and fosters a sense of ownership.
- Recognition Programs: Recognizing employees who actively engage in safety practices can motivate others to follow suit.
However, employee engagement also has its challenges. Maintaining sustained interest can be tough, especially in larger organizations where the disconnect between management and staff can occur. Organizations must ensure that engagement is part of daily operations, not just a once-in-a-while initiative.
Continuous Improvement Strategies
Adopting continuous improvement strategies contributes significantly to the evolution of a safety culture. This means organizations should always be on the lookout for ways to enhance safety practices. Aspects to consider include:
- Feedback Mechanisms: Implementing systems where employees can provide feedback about safety practices can lead to valuable insights and improvements.
- Regular Training Updates: Safety protocols should not be static. Regularly updating and adapting training materials based on new findings or technologies ensures employees remain informed.
- Incident Review: Analyzing past incidents for lessons learned fosters a culture of openness instead of fear, which can otherwise stifle reporting and discussion of safety concerns.
In summary, while building a safety culture is a multifaceted endeavor that requires ongoing commitment from leadership and involvement from all employees, the long-term benefits offer both improved safety outcomes and enhanced productivity. By prioritizing roles within culture and focusing on employee engagement along with consistent improvement strategies, organizations can achieve a more robust and effective Process Safety Management program.
Best Practices in Process Safety Management
Best practices in Process Safety Management (PSM) play a crucial role in ensuring the safety and health of workers while enhancing operational efficiency. These practices provide a structured approach to risk management, enabling organizations to foster a culture of safety within their operations. Adopting these proven strategies isn’t merely an option; it’s a necessity for any industry that involves hazardous materials or complex processes.
Implementing Effective PSM Programs
An effective PSM program serves as the backbone of safeguarding both personnel and the environment. The journey to implement such a program begins with a detailed assessment of existing processes, current safety measures, and organizational culture.
Key Components to Consider:
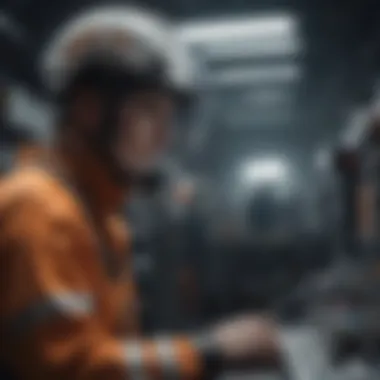
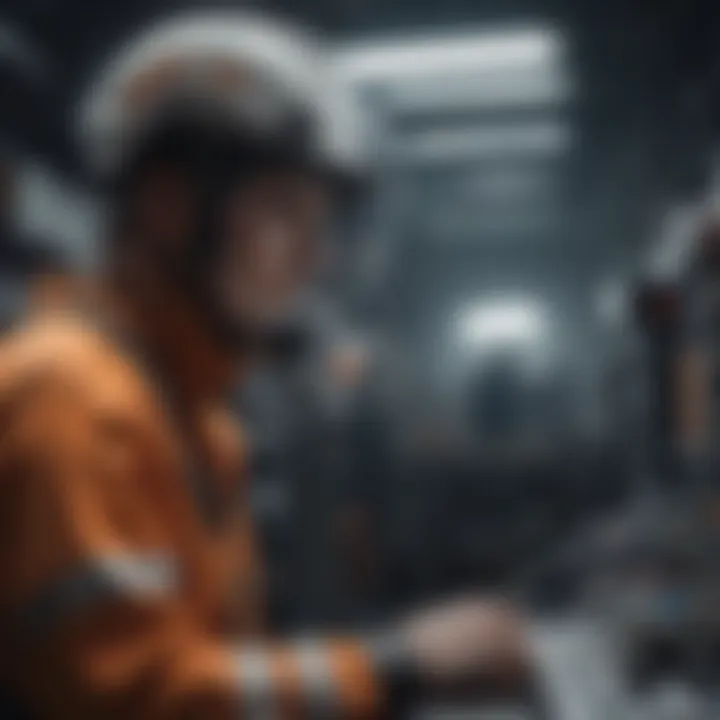
- Risk Assessment: Start by identifying potential hazards associated with processes and evaluate their likelihood and consequences. Prioritize these risks to channel resources effectively.
- Leadership Commitment: Management must show commitment by providing adequate resources, training, and support for the PSM program. Their involvement sets the tone for a safety-first culture.
- Employee Involvement: Encourage feedback and participation from all levels within the organization. Engaging employees not only enhances their understanding of safety protocols, but it also fosters a sense of responsibility.
- Continual Training: Incorporate routine training to keep employees up-to-date on safety procedures and emergency response plans. Using realistic simulations can also sharpen their readiness to handle unexpected situations.
The successful implementation of these components effectively minimizes the chances of accidents, injuries, or environmental damage, making it possible to operate with confidence amidst inherent risks.
Case Studies and Lessons Learned
Learning through real-world scenarios is vital for honing PSM practices. Case studies provide a wealth of insights, revealing what works, what doesn’t, and how continuous improvement can reshape safety standards.
1. The Texas City Refinery Explosion
In 2005, a catastrophic incident at BP’s Texas City refinery underscored the importance of rigorous PSM practices. Following the tragedy, investigations revealed critical lapses in hazard analysis and risk management. The fallout prompted the industry to reevaluate protocols, spotlighting that every step in PSM is interlinked and must be treated with utmost seriousness.
2. The Bhopal Disaster
The 1984 gas leak in Bhopal, India, remains one of the world's worst industrial disasters. It exposed flaws in safety systems and the dire consequences of inadequate PSM practices. This event led to the establishment of stricter regulations and processes to prevent similar incidents globally.
These examples illustrate the necessity of a proactive approach to PSM. They highlight that the cost of neglecting safety can be unfathomable. Incorporating lessons learned from past incidents into current practices strengthens the resolve across the board for safer operations.
"Those who fail to learn from history are condemned to repeat it." - Winston Churchill
Ultimately, the commitment to best practices in PSM cultivates a sustainable strategy that not only protects human life but also preserves the integrity of the organizations involved. Continuous monitoring, learning, and revising practices accordingly serve as building blocks for long-term safety success.
Challenges in Process Safety Management
In the realm of Process Safety Management (PSM), few topics hold as much weight as the challenges that organizations encounter. These obstacles can range from identifying risks to adopting integrated systems. Acknowledging and addressing these challenges is crucial—it’s where safety meets operational effectiveness. This section delves into two main hurdles: the identification and mitigation of risks, as well as the integration of PSM with other management systems. Each aspect plays a pivotal role in upholding safety standards and fostering a proactive safety culture.
Identifying and Mitigating Risks
Effective risk identification forms the backbone of any PSM initiative. Organizations need to grasp the full extent of hazards within their operations. It's not just about ticking off a box on a compliance checklist; it's about understanding the nuances of risk in a deep and detailed manner. This involves a systematic approach that includes both qualitative and quantitative assessments.
There are several methods and techniques commonly used in this process:
- Job Safety Analysis (JSA): Breaks down tasks to identify potential hazards before they can affect productivity or safety.
- Failure Mode and Effects Analysis (FMEA): Analyzes possible failure points within processes to help prioritize which risks need addressing first.
- What-If Analysis: Encourages a brainstorming culture, allowing teams to speculate what could go awry and devising strategies accordingly.
Mitigating these identified risks isn’t simply a theoretical exercise. Practical strategies such as engineering controls, administrative adjustments, and personal protective equipment are paramount. Through properly understanding and addressing risks, organizations reduce the chances of incidents that could otherwise lead to catastrophic consequences. As the old saying goes, "an ounce of prevention is worth a pound of cure."
Integration with Other Management Systems
The integration of Process Safety Management with other management systems is like trying to fit a square peg into a round hole. It requires ingenuity and a thoughtful approach to make sure that safety syncs nicely with other operational spheres, such as Quality Management (QM) and Environmental Management Systems (EMS). Failing to incorporate these systems could lead to a siloed approach—safety measures become disconnected from overall operational goals, which ultimately compromises safety.
When done correctly, the integration can yield numerous benefits:
- Streamlined Processes: Reducing redundancies and improving communication fosters a more efficient workflow.
- Holistic Risk Management: This creates a robust framework where all facets of safety—including environmental and operational practices—are covered.
- Enhanced Compliance Tracking: A unified approach simplifies regulatory compliance, as organizations can implement checks that consider all areas of risk simultaneously.
To facilitate this integration, it’s essential to adopt a risk-based approach and cultivate a culture where safety is seen as a collective responsibility. Leaders should encourage collaboration across departments, showing that safety isn’t just a compliance issue; it is integral to achieving success across all levels of the organization.
"Effective planning and execution within the boundaries of integrated systems could be the defining characteristic of a safe workplace."
Navigating these challenges can be complex, but it is achievable. Organizations must stay vigilant and proactive, continuously refining their strategies to meet an ever-evolving landscape of safety management. Through a committed approach to risk management and integration, they can take significant strides toward ensuring safer, more productive environments.
The Future of Process Safety Management
As industries evolve, so too must their approaches to Process Safety Management (PSM). The landscape of workplace safety is shifting, driven by technological advancements, changes in regulatory environments, and the need for continuous improvement in safety practices. The future of PSM holds significant importance in enhancing operational efficiencies while safeguarding the well-being of employees.
Emerging technologies, data analytics, and artificial intelligence are paving new paths in PSM by providing tools that allow for predictive safety measures. These technologies not only enhance risk identification and assessment processes but also effectively streamline incident investigations. Incorporating advances like the Internet of Things (IoT) allows real-time monitoring of safety parameters, which can alert management to potential hazards before they escalate into serious incidents. Thus, an organization can pivot towards a more proactive safety culture rather than a reactive one.
Moreover, with heightened scrutiny from regulatory bodies regarding safety compliance, maintaining alignment with changing regulations will be crucial for many organizations. Stakeholders must recognize and adapt to these evolving regulations, ensuring continuous compliance not only to mitigate legal risks, but also to build a robust safety framework that champions employees' health and safety.
As the workplace becomes more globalized, collaboration among diverse industries and organizations is becoming increasingly invaluable. Sharing insights, experiences, and best practices can cultivate a collective intelligence that empowers all parties involved. In this interconnected environment, failure in one sector can lead to repercussions across many others. Therefore, a broader understanding of process safety and collaboration across sectors can pave the way for establishing uniform standards that benefit everyone.
Emerging Technologies in PSM
The role of emerging technologies in PSM cannot be overlooked. As organizations seek to innovate, the integration of new technologies into safety management systems becomes essential. Here are some significant technological trends shaping the future of PSM:
- Predictive Analytics: Utilizing historical data to forecast potential incidents and enhance preparedness. An organization can become agile in its response to potential hazards when it can predict them.
- Artificial Intelligence: AI algorithms can identify patterns and anomalies in operations that may have previously gone undetected, fostering a culture of preventative safety measures.
- Virtual and Augmented Reality: Training programs leveraging VR and AR can create realistic emergency scenarios, allowing employees to practice their responses without actual risks. This immersive experience can lead to better training outcomes and readiness during real incidents.
- Remote Monitoring: Digital devices can now continuously monitor physical conditions and parameters in real-time, offering insights that ensure a safer work environment.
As these technologies continue to develop, they will contribute significantly to the evolution of PSM.
Trends in Safety Regulation and Compliance
The regulatory environment surrounding PSM is dynamic and continually evolving. Staying ahead of trends in safety regulation and compliance is vital for organizations looking to maintain high safety standards. Here are some trends to keep an eye on:
- Stricter Regulations: Governments are increasingly considering stringent regulations that demand compliance across various sectors. Organizations will need to adapt their PSM strategies accordingly to anticipate regulatory changes.
- Focus on Human Factors: Recognizing the role of human error in incidents leads to regulations that emphasize employee behavior, training, and awareness, making it imperative for workplaces to foster a safety-first mindset.
- Increased Penalties for Non-compliance: With regulators cracking down on non-compliance, organizations that fail to meet safety standards may face hefty penalties, potentially impacting their reputation significantly.
- Industry Collaboration: Regulatory bodies are encouraging sectors to collaborate and share insights. This collaboration can lead to standardized regulations across industries, easing the compliance burden and enhancing overall safety management strategies.
Staying informed about evolving safety regulations is not just a legal necessity; it is a fundamental aspect of promoting a resilient safety culture.