Exploring Nickel Plating Mechanisms and Applications
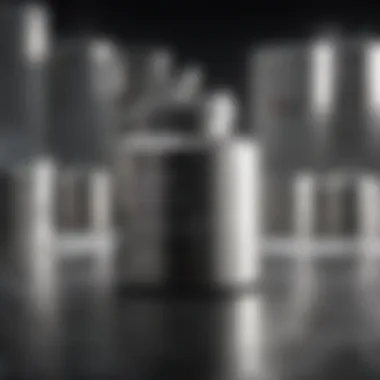
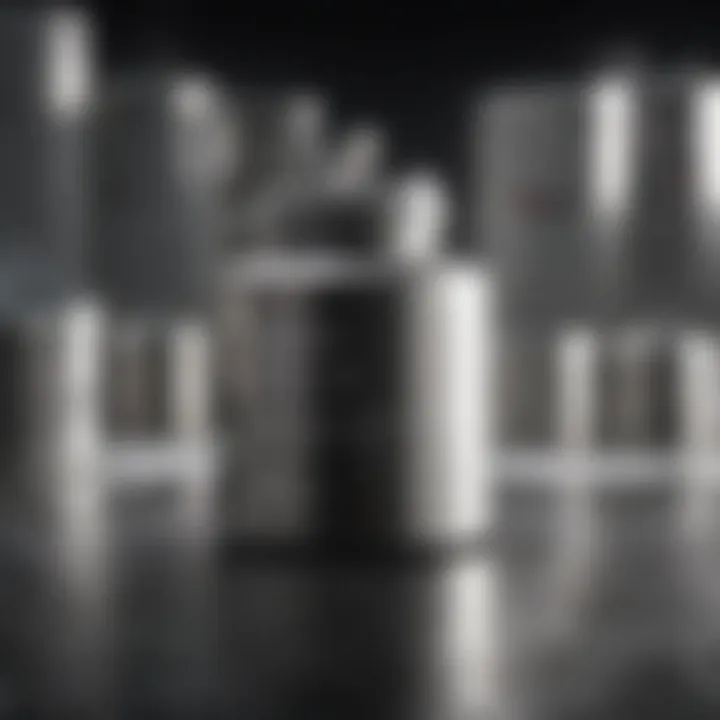
Intro
Nickel plating serves as a functional enhancement to metal components across diverse industries. This process is not merely aesthetic; it improves durability, resistance to corrosion, and wearability of surfaces. Grasping its mechanisms and applications is crucial, especially for students, researchers, educators, and professionals engaged in material sciences and engineering.
Nickel, as a metal, boasts several properties that make it a preferred choice for plating. It can withstand extreme environments, resist oxidation, and provide a smooth finish. The application of this technique has transformed sectors ranging from aerospace to consumer electronics. As we delve deeper, we will examine the technical aspects of nickel plating, its different application methods, and the myriad benefits it offers.
Key Findings
Major Results
Throughout this exploration, several key insights emerge regarding nickel plating:
- Versatility: Nickel plating can be applied to a wide variety of metals and is used in many industries.
- Protection: It effectively shields against corrosion and enhances the surface hardness.
- Conductivity: The process can improve electrical conductivity in specific applications.
"Nickel plating not only protects but also extends the lifetime of metal substrates."
Discussion of Findings
The findings suggest that nickel plating is more than a simple coating process. The chemistry behind the plating solution plays a significant role in determining the quality of the final product. Various formulations and concentrations can yield different physical properties. Additionally, the process parameters, including temperature and current density, significantly affect the plating's microstructure and performance.
Understanding these factors allows for optimized applications tailored to meet specific performance criteria in challenging environments. The implications for industry standards and practices become evident as we consider the performance requirements for components in critical applications.
This article will further emphasize these points, guiding readers through experimental data, case studies, and industry applications.
Prolusion to Nickel Plating
Nickel plating is an essential process in many industries. It improves the properties of metal surfaces, enhancing durability, corrosion resistance, and aesthetic appeal. This process involves the deposition of a thin layer of nickel on a substrate material. The significance of nickel plating cannot be underestimated in today’s manufacturing environment, where performance and reliability are paramount. It finds applications across sectors, from aerospace to electronics, ensuring that products meet stringent industry standards.
Definition of Nickel Plating
Nickel plating is defined as the process of depositing a layer of nickel on a surface. This is typically done using two main methods: electrolytic and electroless plating. In electrolytic plating, an electric current is used to reduce nickel ions. In electroless plating, a chemical reaction causes nickel to deposit onto the surface without external electricity. The outcome is a coating that enhances the base material's characteristics, providing a hard and protective layer. Nickel plating also serves decorative purposes, giving metals a shiny appearance. This quality makes it suitable for consumer goods, such as jewelry and automotive parts.
Historical Context
The practice of nickel plating dates back to the late 19th century when it was first introduced as a means to improve the appearance and durability of metal objects. In the early years, the process was refined, and nickel plating became a common industrial solution. Notably, during the World Wars, the demand for durable components surged. Nickel became crucial in military applications, where protection against corrosion was essential. Over the decades, advancements in technology and chemistry have led to more efficient and environmentally friendly methods of nickel plating. Today, it continues to evolve with growing awareness regarding sustainability and performance standards in various industries.
The Chemistry of Nickel Plating
Nickel plating is not just a surface treatment; it is a sophisticated chemical process that enhances the performance characteristics of metals. Understanding the chemistry behind nickel plating is essential. This knowledge informs professionals about the different methods and materials used in the plating process. Moreover, it allows for the optimization of the plating process, ensuring that the desired outcomes are consistently achieved.
Electrolytic Nickel Plating
Electrolytic nickel plating involves the use of an electrical current to deposit nickel onto a substrate. The process takes place in an electrolytic solution containing nickel salts. A direct current is passed through the solution, leading to the accumulation of nickel ions at the cathode, where the substrate is located.
In this method, several factors influence the quality of the plating. Current density is particularly important; a higher current density can lead to a quicker deposition but may result in a less uniform surface. Additionally, contaminants in the plating bath can affect the adherence and quality of the deposited nickel. The electrolytic method allows for relatively thick layers of nickel to be deposited, which is beneficial for various applications, including those in the automotive and aerospace sectors.
Electroless Nickel Plating
Electroless nickel plating differs fundamentally from its electrolytic counterpart. This approach does not require an external current; instead, it relies on a chemical reaction to deposit nickel onto surfaces. The process involves immersing the metal in a solution containing nickel salts, reducing agents, and stabilizers.
One advantage of electroless nickel plating is its ability to provide uniform coverage even on complex geometries that may be difficult to coat using electrolytic methods. Moreover, it can adhere to non-conductive surfaces, which expands its application range. Common industries utilizing electroless nickel include electronics and those in need of corrosion resistance. However, the chemical composition of the plating solution must be carefully controlled to ensure effective plating and desirable qualities.
Plating Solutions and Additives
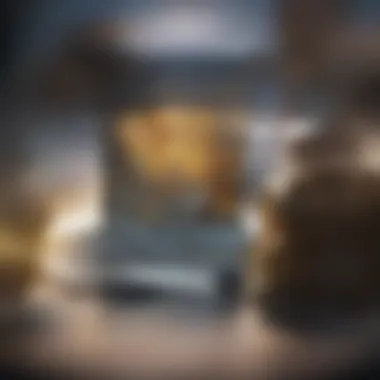
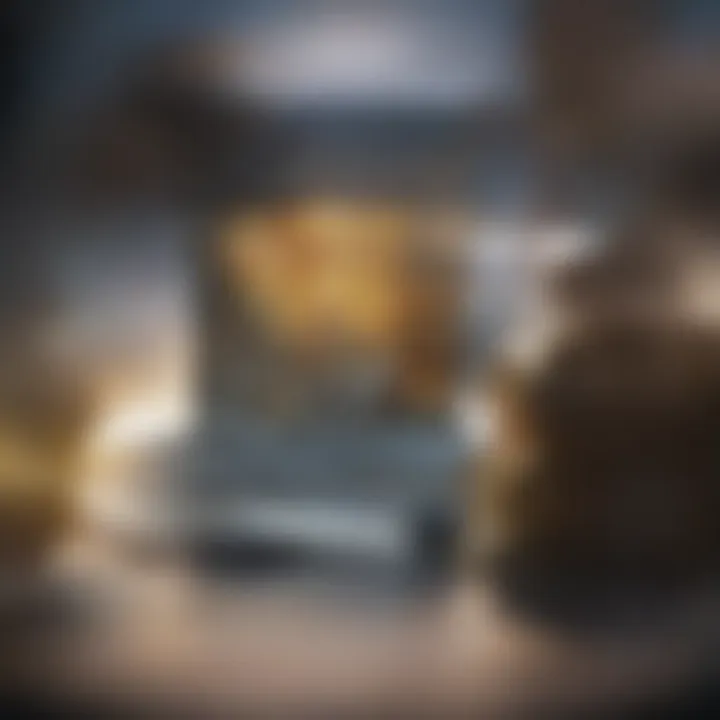
The formulation of plating solutions is critical to achieving desired plating outcomes. Nickel plating solutions consist of nickel salts, such as nickel sulfate, along with various additives to enhance properties. These additives can include brighteners, which help to improve the appearance of the plated surface, and complexing agents to stabilize the nickel ions in the solution.
Key components of plating solutions include:
- Nickel sulfate
- Nickel chloride
- Boric acid
- Brighteners
- pH buffers
The right concentration and combination of these components can significantly influence the plating's overall performance, including adhesion, brightness, and resistance to corrosion. Parameters like temperature and pH levels are also monitored closely during the process, as these can alter the plating efficiency and quality.
"The chemistry behind the plating process is essential for achieving desirable qualities and performance in nickel-plated components."
How Nickel Plating Works
Nickel plating is a critical process that enhances the value and performance of metal substrates. Understanding how nickel plating works offers insights into its numerous advantages in various applications. The mechanisms involved in nickel plating include several steps, each crucial for ensuring the quality and durability of the finished product. Additionally, there are factors that can impact the success of the plating process.
Preparation of the Surface
Before any nickel plating can occur, the surface of the metal must be meticulously prepared. This step is vital, as it ensures proper adhesion and effectiveness of the nickel layer. Surface preparation often involves cleaning, which can be done through several methods including alkaline cleaning or acid pickling. Removing any grease, dirt, or oxidation is critical to avoid flaws in the nickel deposit. A rough surface profile may also be created to enhance bond strength. This careful preparation guarantees that the nickel plating adheres properly, resulting in a stronger, more reliable finish.
Application Process
The application process for nickel plating can be carried out using various methods. The two primary techniques are the Electrolysis Method and the Autocatalytic Method, each having distinct features and advantages.
Electrolysis Method
This method involves the use of an electrolytic cell. In this technique, an electric current is passed through a nickel-containing solution, directing nickel ions to the metallic surface being plated. The current density is a crucial factor; higher densities can lead to thicker deposits, but may also introduce stress in the nickel layer.
One key characteristic of the Electrolysis Method is its control over layer thickness. This allows for uniform coverage, essential in industries where precise specifications are mandatory. However, this technique requires careful monitoring of several variables, including temperature and pH levels, which can complicate the process.
Advantages of the Electrolysis Method:
- Uniform layer thickness
- Effective adhesion to the surface
- Wide application in various industrial sectors
Disadvantages include the need for electrical equipment and the potential for uneven plating if not properly controlled.
Autocatalytic Method
The Autocatalytic Method, also known as electroless plating, does not require an external electric current. Instead, the chemical reaction proceeds in a solution containing nickel salts and reducing agents. The nickel is deposited uniformly on the base material as long as it is clean and properly prepared.
A significant feature of this method is its ability to coat complex geometries that might be challenging for the Electrolysis Method. Furthermore, the layer can develop over time, allowing for more extensive coverage in intricate areas. The Autocatalytic Method is especially beneficial when dealing with parts that have complex shapes.
Advantages of the Autocatalytic Method include:
- Ability to coat complex shapes
- No need for electrical setup, leading to cost savings
- Uniform coverage regardless of surface geometry
However, limitations exist, such as slower deposition rates compared to electrolytic processes.
Post-Plating Treatment
After the plating process, post-plating treatments are essential to optimize the nickel layer properties. These treatments can involve processes such as heat treatment for stress relief, which enhances the mechanical properties of the plating. Additionally, the finished item may undergo surface finishing operations to improve appearance and corrosion resistance. The post-treatment phase is a significant step that cannot be overlooked as it effects both the aesthetic and functional qualities of the plated surface.
Key Factors Influencing Nickel Plating Quality
Nickel plating quality is essential for the durability and functionality of coated objects. Several critical elements impact this quality. Understanding these factors allows for better control over the plating process, resulting in enhanced performance and longevity.
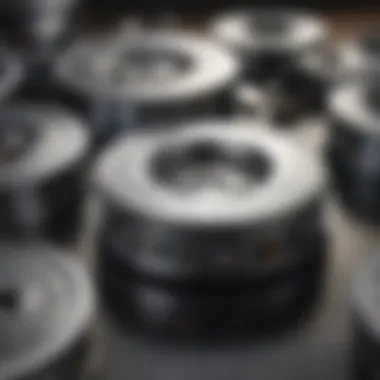
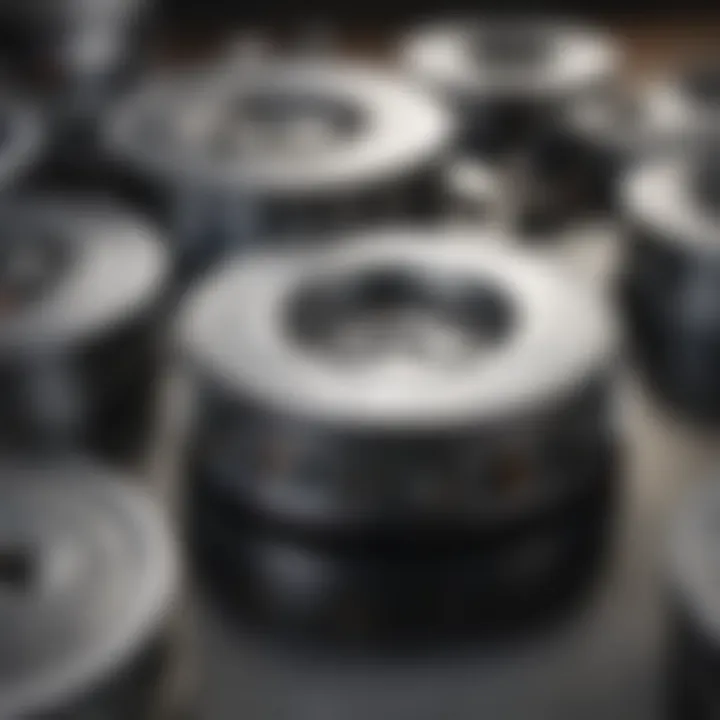
Current Density
Current density refers to the amount of current applied per unit area of the surface being plated. It plays a vital role in nickel plating. A higher current density can lead to faster plating but may also result in poor adhesion and lower quality. Conversely, a lower current density can enhance the uniformity and thickness of the nickel layer.
Optimizing current density is crucial. Too high can lead to rough surfaces, while too low can prolong the process unnecessarily. The desired current density varies depending on the thickness and type of coating required.
- Ideal Range: It is important to find a balance that meets the specific needs of the component being plated.
- Testing: Regular monitoring during the application can help in maintaining the desired current density.
"Achieving the correct current density is crucial for ensuring a quality nickel plating finish."
Temperature Control
Temperature has a profound effect on plating quality. The chemical reactions involved in the nickel plating process are temperature-sensitive.
- Optimal Range: The recommended temperature for most nickel plating processes is between 45 to 60 degrees Celsius. In this range, the plating solution remains effective and provides optimal coverage.
- Effects of Temperature: Higher temperatures can accelerate the reaction but may also increase the risk of defects such as pits or cracks. Lower temperatures, meanwhile, can slow down the process, leading to less efficient plating.
It is vital to maintain the temperature consistently throughout the plating process to achieve uniform results. Temperature fluctuations can impact the appearance and properties of the nickel layer.
pH Levels in Plating Solutions
The pH level of the plating solution influences the quality of the nickel deposit. Each nickel plating bath requires a specific pH for optimal performance.
- pH Range: Typically, the pH levels for nickel plating solutions should be maintained between 4.0 and 5.5. This range allows for the best plating results and oxidation control.
- Consequences of Imbalance: If pH levels are too high or too low, it can lead to various issues, such as poor adhesion, increased porosity, or inconsistent layer thickness.
Monitoring and adjusting pH levels is a routine task during the plating process. Regular testing ensures the plating solution remains effective, ultimately enhancing the quality of the nickel coating.
Each of these factors—current density, temperature control, and pH levels—must be carefully monitored and optimized to achieve high-quality nickel plating. By paying attention to these components, industries can improve the reliability and performance of coated products.
Applications of Nickel Plating
Nickel plating holds substantial significance across multiple industries due to its exceptional properties and performance enhancements. As an electroplating technique, it provides a protective layer that can withstand various conditions, thus extending the lifespan of metal parts and components. There are four primary applications of nickel plating that demonstrate its diverse utility: the aerospace industry, automotive components, electronic components, and decorative uses. Addressing specific needs within these fields has led to the advancement of the techniques and understandings surrounding nickel plating.
Aerospace Industry
In the aerospace sector, nickel plating plays a vital role in ensuring the reliability and durability of components exposed to extreme conditions. Aircraft parts, such as landing gear and turbine blades, require materials that resist wear, corrosion, and excessive heat. The application of nickel plating enhances the performance of these components significantly. For instance, the electrolytic nickel plating method is often utilized because it creates a dense and uniform coating that stands up to harsh environments. The result is not only a longer lifespan for parts but also improved safety, which is paramount in aerospace applications.
Automotive Components
The automotive industry also benefits greatly from nickel plating. Components such as engine parts, fasteners, and decorative trim often undergo nickel plating to improve resistance against wear and corrosion. This is crucial as cars are subject to various harsh conditions, including moisture, road debris, and chemicals. Additionally, nickel plating provides an attractive finish that enhances the aesthetic appeal of vehicles. Using a combination of both electrolytic and electroless nickel plating methods allows for tailored solutions, bringing together functionality and design seamlessly in automotive applications.
Electronic Components
In electronics, nickel plating serves as an integral part of the manufacturing process. It provides critical properties such as improved conductivity and corrosion protection for connectors and circuit boards. Often, a nickel layer is applied followed by a layer of gold to create a superior finish known for its protective capabilities. This is essential in maintaining the performance and reliability of electronic devices over time. Given the increasing demand for smaller yet more powerful electronic gadgets, the importance of nickel plating continues to grow as manufacturers seek efficient and effective ways to meet these demands.
Decorative Uses
Beyond industrial applications, nickel plating is also employed for decorative purposes. Items such as jewelry, door hardware, and kitchen fittings are often plated with nickel to enhance their visual appeal while simultaneously providing corrosion resistance. The shiny finish of nickel is highly valued in the decorative arts sector, as it offers an elegant appearance that can mimic the look of silver at a fraction of the cost. However, it is worth noting that there are some health considerations regarding nickel for certain individuals, which has led to ongoing discussions about its use in decorative contexts.
Nickel plating is clearly a versatile and essential process in a wide range of applications. Its unique properties extend the functional life of components and enhance their overall performance. As industries continue to evolve, the significance of nickel plating will undoubtedly persist, adapting to meet the emerging challenges and needs.
"The integration of nickel plating into manufacturing processes not only enhances existing products but also paves the way for innovative applications in various fields."
Environmental Considerations
In recent years, the environmental impact of industrial processes, including nickel plating, has gained significant attention. The importance of focusing on environmental considerations in nickel plating cannot be overstated, as the methods used in application can greatly affect both local ecosystems and broader environmental health. Thus, the examination of waste management practices and compliance with regulations becomes essential to mitigate negative effects.

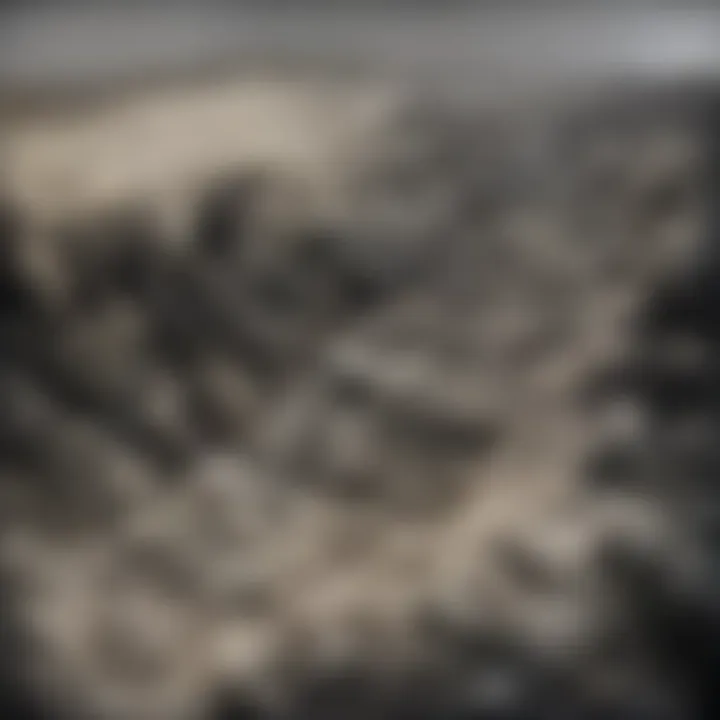
Waste Management in Plating Processes
Effective waste management is a critical element in the nickel plating process. During nickel plating, various chemicals and materials are used. These substances, if not handled properly, can lead to hazardous waste. It is essential to implement rigorous waste management strategies to minimize waste generation and ensure safe disposal.
- Types of waste commonly generated can include spent plating solutions, metal hydroxide sludge, and rinse water.
- These substances may contain nickel and other chemicals that pose environmental risks if released into ecosystems without treatment.
To deal with this, industries should focus on:
- Recycling Processes: Nickel can be recovered from spent solutions through methods such as ion exchange or precipitation. This reduces the amount of new nickel required and minimizes waste.
- Treatment Systems: Onsite treatment of wastewater before release ensures that pollutants are removed, complying with local environmental regulations.
- Minimization Techniques: Implementing technology to reduce the amount of solution used or enhancing the efficiency of the plating process contributes to less waste output.
By adhering to these waste management practices, industries can significantly lower their environmental footprint, fostering a more sustainable approach to nickel plating.
Regulations and Compliance
Compliance with environmental regulations is crucial for industries engaged in nickel plating. Regulatory frameworks are designed to safeguard public health and the environment by controlling the discharge of harmful substances. The regulations may vary by region but typically include limits on:
- Heavy Metals: This includes monitoring and maintaining proper levels of nickel and other metals in effluents, as these substances can contaminate soil and waterways.
- Chemical Usage: Restrictions on certain chemicals used in plating solutions encourage the adoption of eco-friendlier alternatives.
Organizations often conduct regular audits to ensure compliance with local, national, and international standards. In addition, failure to comply can result in legal repercussions and financial penalties, as well as reputational damage.
Future Trends in Nickel Plating
Nickel plating technology continuously evolves to meet various industrial demands and environmental standards. Recognizing the importance of this evolution not only helps in maintaining competitive advantage but also ensures compliance with stringent regulations worldwide. This section explores the specific advancements that are reshaping the nickel plating industry, alongside sustainability initiatives that are becoming increasingly critical.
Advancements in Plating Technologies
Recent innovations in nickel plating technologies show great promise for improved efficiency and quality. These advancements include:
- Pulse Plating: This technique involves fluctuating the current in electrolytic processes, which can enhance the uniformity and adhesion of the nickel layer. It helps in achieving finer microstructures which can improve surface hardness and wear resistance.
- Nanotechnology: The integration of nanomaterials into plating solutions can lead to enhanced properties such as better corrosion resistance and lower friction coefficients. Manipulating materials at the nanoscale opens doors to new applications and superior performance in various environments.
- High-Throughput Techniques: Industries are utilizing automated systems to increase the volume and speed of nickel plating processes. These systems can efficiently manage solutions and monitor quality in real time, contributing to the successful scaling of production.
"The future of nickel plating is not just about improving existing methods; it's about innovating processes that redefine industry standards."
As these technologies continue to advance, they will likely drive the industry toward greater customization and efficiency, addressing the varying needs of different sectors.
Sustainability Initiatives
With growing concerns about environmental impacts, the nickel plating industry is taking significant steps toward sustainability. Important initiatives include:
- Waste Reduction: Modern nickel plating facilities are increasingly aiming for zero waste. Techniques such as recovery and reusing plating solutions reduce the environmental footprint by minimizing waste production and conserving resources.
- Green Chemistry: Moving towards eco-friendly chemicals in plating solutions is a key focus. Manufacturers are researching safer alternatives that do not compromise performance while being less harmful to the environment.
- Energy Efficiency: Plating operations are adopting energy-efficient machinery and practices. This can reduce energy costs significantly while lowering carbon emissions associated with nickel plating processes.
As industries push for more sustainable practices, it is imperative for nickel plating to align with these trends. Sustainability not only reflects corporate responsibility but is rapidly becoming a market requirement.
In summary, the future trends in nickel plating point towards significant advancements in technology and a strong commitment to sustainability. Understanding these developments is essential for professionals seeking to stay informed and competitive in this evolving field.
Culmination
Summary of Key Points
In this article, we explored several key areas concerning nickel plating:
- Definition and Historical Context: Nickel plating is defined as a method of depositing a layer of nickel onto a substrate. Historically, this technique has evolved to meet the demands of diverse applications across various sectors.
- Chemistry and Methods: We discussed both electrolytic and electroless nickel plating, detailing how each method functions, alongside their respective plating solutions and additives.
- Process Steps: The article highlighted the preparation of surfaces, application processes, and crucial post-plating treatments that determine the quality of the finished product.
- Factors Influencing Quality: Critical variables such as current density, temperature, and pH levels were examined, showcasing their impact on achieving optimal plating results.
- Applications: The diverse use of nickel plating in industries like aerospace, automotive, and electronics demonstrates its wide-ranging applicability, alongside decorative uses.
- Environmental Considerations: We addressed waste management and regulatory compliance, recognizing the importance of sustainable practices within nickel plating processes.
- Future Trends: Technological advancements and sustainability initiatives are reshaping the landscape of nickel plating.
The amalgamation of these discussions reinforces the relevance of nickel plating in modern applications, driving both performance and innovation.
Implications for Industry
The implications of understanding nickel plating extend significantly into the industrial realm. Industries can benefit from adopting nickel plating techniques to enhance the durability and longevity of their products. The aerospace and automotive sectors, for instance, rely heavily on the corrosion-resistant properties of nickel in components that face harsh environments.
Furthermore, as industries lean toward sustainable practices, integrating more eco-friendly plating options can facilitate compliance with regulations while minimizing ecological impact. Professionals in manufacturing and engineering sectors should stay informed on emerging trends and advancements in plating technologies to maintain a competitive edge.