Exploring the Art and Science of Slip Casting Ceramics
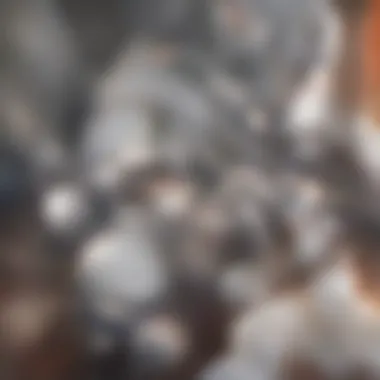
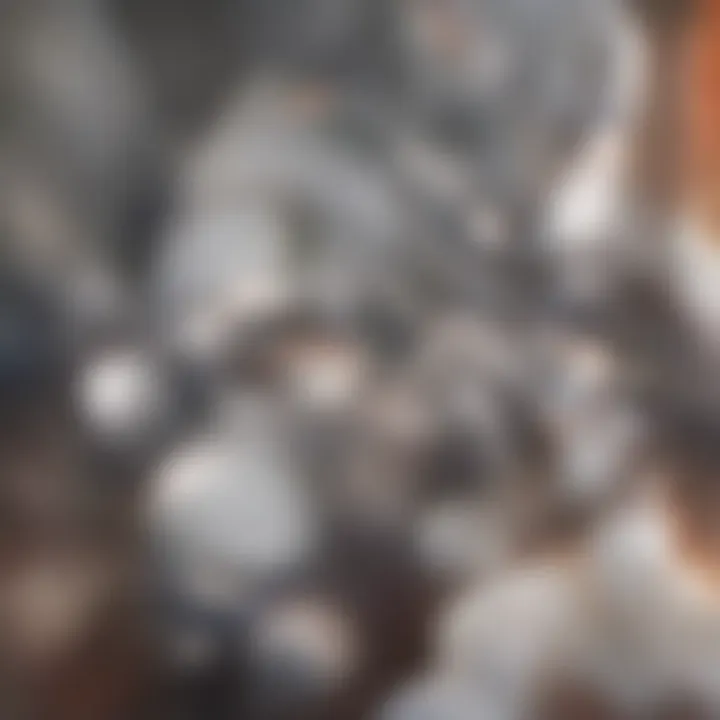
Intro
Slip casting is a revered technique in ceramics, known for its versatility and efficiency. It involves pouring a liquid clay mixture, or slip, into a mold, allowing intricate shapes to take form as the liquid settles and solidifies. This method dates back to ancient times, and its evolution reflects the growing sophistication of ceramics as an art and craft.
Importance of Slip Casting
Slip casting is not merely a production process; it is a gateway that connects art, technology, and science. This technique makes it possible to reproduce complex forms with accuracy and consistency. It is particularly significant in today's world where design precision and material innovation are highly sought after.
In essence, understanding slip casting can benefit a range of individuals from students pursuing material sciences to professionals in the ceramics industry. It provides a thorough grounding in both theory and practice, enriching comprehension of material properties and manufacturing processes.
Key Findings
The exploration of slip casting unveils several critical aspects:
- Historical Context: Slip casting has a rich history that dates back centuries. Its development correlates with advancements in material science and industrial capabilities.
- Techniques and Applications: The methods involved in slip casting are diverse, offering various advantages in manufacturing specific shapes and designs. Current applications span from tableware to intricate artistic objects.
- Advantages: Some of the main benefits include lower labor costs, reduced waste, and the ability to create highly detailed forms. This technique allows for mass production without sacrificing quality.
- Limitations: However, it is important to note the limitations, such as mold wear and the dependency on the quality of the slip used. This presents challenges that practitioners must navigate.
"The advancement of slip casting technologies provides an exceptional lens through which to examine the intersection of design and material innovation."
Major Results
The analysis reveals that while slip casting serves as an efficient production technique, its effectiveness hinges on the understanding of various factors. These include:
- The composition of the ceramic slip, which impacts the final product's durability and aesthetic.
- The design of the mold, which dictates the possibilities for intricacy and originality in the finished piece.
- The drying and firing processes, which are critical to achieving the desired physical properties of the ceramics.
Discussion of Findings
The findings create an intriguing narrative about how slip casting serves both artisanal interests and industrial applications. Discussions highlight the adaptability of this technique to contemporary material needs and artistic expressions. Enhanced precision in mold design and slip preparation has led to innovations that expand the realm of what is achievable in ceramic arts.
Methodology
Research Design
A qualitative approach was employed to analyze the multifaceted dimensions of slip casting. This included reviewing literature, interviewing industry experts, and studying contemporary practices.
Data Collection Methods
Data was collected from a variety of sources including:
- Academic journals focusing on ceramics materials and processes.
- Online forums and discussions, such as those found on Reddit and Facebook, where enthusiasts and professionals exchange experiences.
- Case studies from established ceramics studios, which provided practical insights into the application of slip casting.
Prologue to Slip Casting Ceramics
Slip casting is a pivotal method in the art of ceramics, allowing for the creation of intricate shapes and designs that would be very difficult to achieve through other techniques. This section serves as a foundation for understanding how slip casting operates, its historical significance, and its current relevance in the ceramics industry.
Definition of Slip Casting
Slip casting refers to a ceramic forming technique that involves pouring a liquid clay mixture, known as slip, into a mold. The mold is typically made of plaster, which absorbs water from the slip, gradually forming a layer of clay on the inside surface. Once the desired thickness is obtained, the excess slip is poured out, leaving the clay to dry and take the shape of the mold. This method is lauded for its versatility and efficiency in producing both simple items and complex forms, making it a favorite among ceramists.
Historical Context
The practice of slip casting dates back several centuries and has deep roots in various cultures. Originating in ancient civilizations, it evolved as artisans sought to produce pottery that was both functional and decorative. In the 19th century, with the advent of mass production, slip casting techniques expanded significantly. The industrial revolution played a key role in modernizing this traditional craft. Today, slip casting is well-established in both artistic and industrial ceramics, bridging a gap between heritage and contemporary art.
Importance in Ceramics
Slip casting is crucial for a variety of reasons. Firstly, it allows for remarkable precision in reproducing complex shapes, which is essential in modern ceramics. This technique supports the production of identical pieces at a large scale, making it economically sensible.
Secondly, the process facilitates elaborate designs that enhance the aesthetic value of ceramic products. From fine china to sculptural art pieces, the implications of slip casting are vast and varied. Furthermore, as sustainability becomes a focal point in production methods, slip casting offers waste reduction opportunities through efficient material use.
In summary, understanding the definition, historical context, and importance of slip casting is crucial for those interested in the ceramics field. This will set the stage for a deeper exploration of its components and processes.
Understanding the essence of slip casting can illuminate pathways for innovation in ceramics while respecting tradition.
The Composition of Ceramic Slip
The composition of ceramic slip is essential for understanding the slip casting process. This section delves into the various components that make up the slip. It includes the raw materials used, how they are combined, and the preparation techniques that determine the final product's quality. A proper understanding of these elements contributes significantly to producing durable and artistically valuable ceramics.
Raw Materials Used
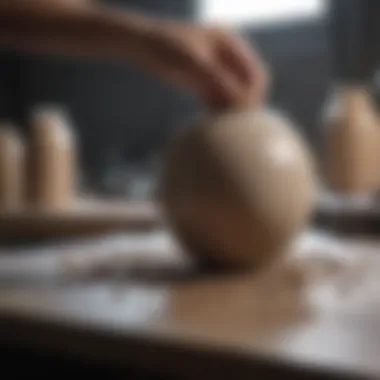
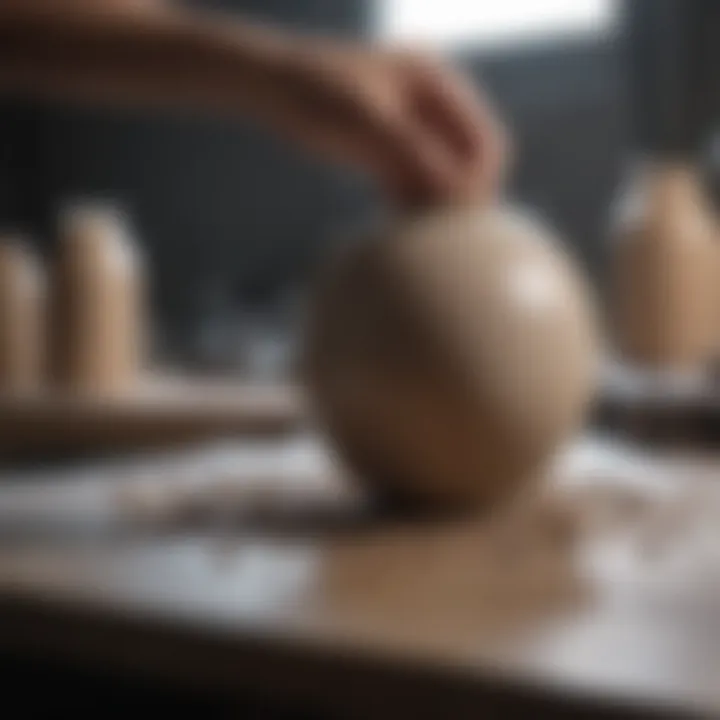
The raw materials in slip casting play a crucial role in determining the characteristics of the final product.
Clay Types
Clay types are a primary component in the slip. Different types of clay, such as earthenware, stoneware, and porcelain, each have unique properties that influence the finished piece. For example, porcelain clay is known for its whiteness and translucency, making it a popular choice for fine ceramics.
The key characteristic of clay types is their plasticity. High plasticity allows for ease in shaping and molding, which is essential during casting. However, some clays can shrink significantly during drying and firing. This fact is important when designing molds and anticipating how the piece will behave throughout the process.
Water Content
Water content in the slip determines its workability and flow characteristics. A certain amount of water is needed to achieve the desired viscosity, allowing the slip to fill molds effectively.
The key aspect of water content is its effect on the consistency of the slip. Too much water can weaken the final product, while too little can lead to poor mold filling. The right balance ensures a workable slip that maintains strength after drying and firing.
Additives
Additives are substances incorporated into the slip to enhance specific properties. These can include deflocculants to improve fluidity, binders for strength, and colorants for aesthetics.
The key characteristic of additives is their versatility. They can modify the slip to suit various applications and achieve particular design goals. However, using additives requires caution. Overusing them may lead to unwanted reactions during firing, affecting the quality of the ceramic.
Preparation Techniques
Proper preparation of the ceramic slip is vital to ensure consistent quality in the casting process.
Mixing Procedures
Mixing procedures in slip preparation involve combining all raw materials with the right proportions. This step is critical for achieving uniform consistency throughout the slip.
The primary aspect of mixing is ensuring that all ingredients are well integrated without introducing air bubbles. Poor mixing can lead to defects in the finished product. A thorough mix produces a smooth slip that pours easily into molds.
Consistency and Viscosity Control
Achieving the correct consistency and viscosity in the slip is essential. This control affects how well the slip will fill the mold and how it will behave during drying and firng.
A specific feature of consistency control techniques is their impact on the slip's flow characteristics. Measuring viscosity ensures that the slip maintains an optimal thickness that meets the requirements of the mold. Too viscous a slip may not fill the mold properly, while too runny may lead to uneven casting.
The Slip Casting Process
The slip casting process is a fundamental aspect of ceramic production. It enables manufacturers to create complex shapes with precision and efficiency. Understanding this process is crucial for those in ceramics, whether they are students, educators, or industry professionals. Each phase of slip casting contributes to the final quality and design of the ceramic product. Here, we detail the key components of the slip casting process.
Molds Used in Slip Casting
Molds are essential in slip casting. They define the shape of the final product and can be made from various materials, including plaster or metal. Plaster molds are popular because they absorb moisture from the slip, allowing for a quicker setting time. The design of the mold is often dictated by the desired geometry of the piece.
Using a well-crafted mold ensures consistent shapes and sizes in production. It also allows for more intricate designs that might be difficult to achieve with traditional forming methods. Careful cleaning and maintenance of these molds is necessary to prevent defects in future casts.
Pouring the Slip
Once the mold is prepared, the ceramic slip is poured into it. The slip needs to be the right consistency to flow easily into the mold without air bubbles. Achieving the right viscosity is critical. If the slip is too thick, it won’t fill the mold completely; if it is too thin, it may lead to weak products.
After pouring, the mold is typically left undisturbed for a specific period. This allows the slip to begin setting. During this stage, the mold absorbs moisture from the slip, creating a skin around the mold cavity. The thickness of this skin can be controlled by monitoring the pour time and the amount of slip retained in the mold.
Drying and Setting
The drying and setting phase is crucial in the slip casting process. After the desired thickness of the clay layer forms against the mold, the excess slip is poured out. At this point, the piece must dry further before being removed from the mold. This phase involves careful monitoring of temperature and humidity to prevent cracking.
Once adequately dried, the piece can be safely removed from the mold. Handling the unfired ceramic requires caution, as it can be fragile in this state. Drying also helps to strengthen the product as moisture levels decrease. The next steps usually involve trimming and cleaning the product to prepare it for glazing and final firing.
Finishing Techniques for Slip Casted Products
The finishing techniques applied to slip casted products are essential in defining the quality and aesthetics of the final piece. After the initial casting process, these techniques enhance the appearance and durability of ceramics. Proper finishing also contributes to the functionality of the product. A well-finished item meets both aesthetic and practical requirements, making these techniques fundamental in ceramic artistry and production.
Successful finishing begins with trimming and cleaning. This phase focuses on refining the shape and removing any imperfections that may have occurred during the casting process. Proper trimming can make a significant difference in the final output, ensuring pieces fit correctly during assembly and preventing defects in the glazing phase.
Trimming and Cleaning
Trimming and cleaning are critical steps that follow the drying of the slip casted product. During slip casting, the clay can retain excess moisture, which may cause it to warp or create uneven surfaces. Trimming involves carefully removing any excess material and smoothing the edges and surfaces for a polished appearance.
When cleaning, attention is paid to remove any residues or marks left by the mold. This includes handling surfaces to ensure they are free from dust or other foreign materials. A thorough cleaning subsequently prepares the item for glazing, which is crucial for achieving the desired finish.
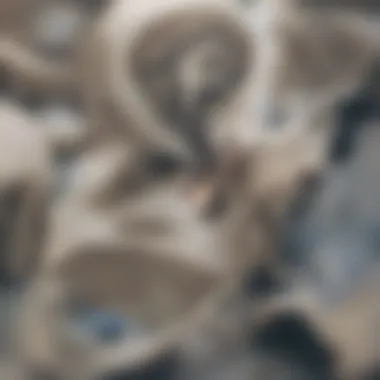
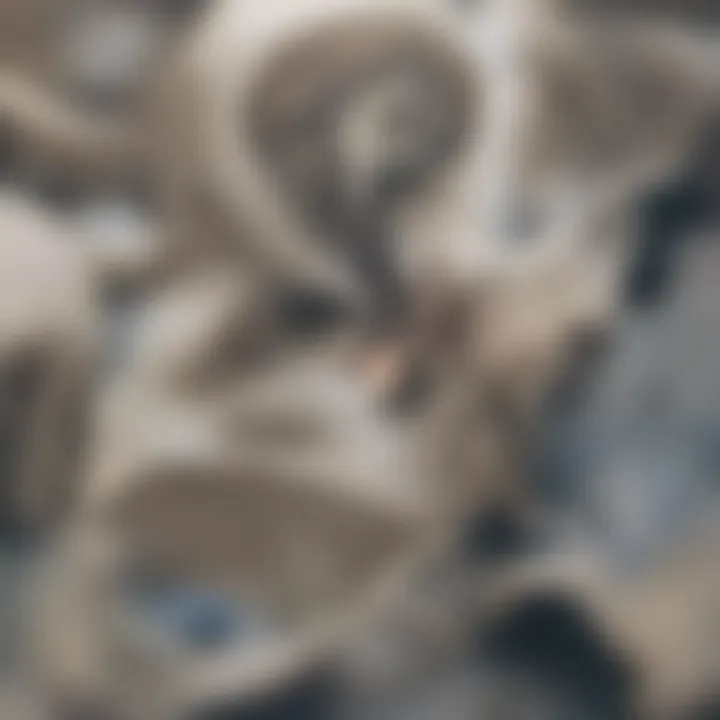
Glazing and Surface Treatments
Glazing involves the application of a glass-like coating on the surface of slip casted ceramics. This process serves not only cosmetic purposes but also adds functionality, like making the item waterproof or less porous. Surface treatments can vary widely, offering diverse textures and finishes depending on the intended use of the ceramic.
Types of Glazes
Different types of glazes offer unique characteristics that can dramatically affect the final product. Common glaze categories include transparent, opaque, matte, and glossy, each contributing differently to the visual appeal and functionality of ceramics.
- Transparent glazes provide clarity, showcasing the underlying clay body.
- Opaque glazes hide the clay body, allowing for bold color application.
- Matte glazes offer a soft, non-reflective surface that can create a warm, inviting feel.
- Glossy glazes create a shiny and vibrant look, reflecting light and colors beautifully.
The key characteristic of these glazes is their versatility and durability, making them popular choices among ceramics artisans. However, the unique feature of each glaze type comes with its own advantages and disadvantages, including the difficulty of achieving the desired finish or issues related to application consistency.
Application Methods
Applying glaze requires skill and experience. Various application methods exist, each affecting the texture and overall presentation of the final product. Common techniques include dipping, pouring, spraying, and brushing.
- Dipping is effective for uniform coverage and is commonly used for production items.
- Pouring can be efficient for larger pieces or when applying multiple glazes.
- Spraying allows for delicate and detailed glaze application.
- Brushing offers control in design and decoration, especially on smaller items.
The key characteristic of these methods lies in their ability to achieve different effects on the surface. Each method is a beneficial choice depending on the specific goals of the ceramic artist. However, misapplication can lead to drips, runs, or uneven coating, highlighting the importance of precision in this process.
Firing Process
Finally, the firing process solidifies all previous steps. Firing is crucial as it transforms both the clay and glaze chemically, resulting in a durable and functional product. During firing, the piece is subjected to high temperatures that cause the clay particles to fuse together and the glaze to vitrify, creating a hard, glassy finish that enhances both beauty and utility.
This phase is marked by careful scheduling. Adjusting temperature and duration can lead to varied results within the final appearance. Therefore, understanding the composition and the specific properties of materials used in slip casting becomes vital to achieving the ultimate desired outcome.
Benefits of Slip Casting in Ceramics
The slip casting process is a unique ceramic shaping method that presents several advantages, defining its significance within the ceramics industry. This section will explore two primary benefits: efficiency and production capacity, along with the ability to create complex shapes and designs. Together, these advantages illustrate the practicality and versatility of slip casting in enhancing ceramic production.
Efficiency and Production Capacity
Slip casting offers notable efficiency in the production process of ceramics. This method automates the shaping of items, significantly reducing the labor time involved compared to traditional hand-building techniques. When using plaster molds, the slip can be poured quickly, taking advantage of gravity and fluid dynamics to fill the mold uniformly. This low-energy requirement leads to higher throughput, making it an optimal strategy for large-scale production.
Furthermore, slip casting can facilitate the production of multiple identical pieces simultaneously. Each mold can be reused multiple times, allowing for a streamlined operation where numerous items are produced in parallel. The ability to multiply production without a proportional increase in labor or resource consumption enhances the viability of this manufacturing method within industrial contexts.
In addition, the waste generated through slip casting is generally lower than that of other methods. Excess slip can often be recycled back into the process, minimizing material use and supporting more sustainable practices in ceramics.
Complex Shapes and Designs
Another significant benefit of slip casting is its ability to create intricate shapes and detailed designs with relative ease. The fluid nature of the slip enables it to flow into every recess and contour of the mold. This characteristic makes it possible to manufacture items with complex geometry that might be challenging to achieve through other forming methods, such as hand building or wheel throwing.
The capacity to design molds allows artists and manufacturers to explore unique artistic visions. The intricate detail available in slip cast pieces can produce aesthetically appealing results along with functional items. For instance, items such as decorative porcelain figurines or finely crafted dinnerware benefit from the consistency and precision made possible by this method.
"Complexity in design is not just an artistic endeavor; it can also enhance functionality and user experience in ceramic products."
In summary, the benefits of slip casting in ceramics extend from efficiency and production capacity to the ability to create complex and beautiful forms. Understanding and leveraging these advantages is crucial for anyone involved in ceramic design or production, as it directly impacts both productivity and the potential for innovation in the field.
Challenges Associated with Slip Casting
The practice of slip casting ceramics is not without its difficulties. Understanding these challenges is crucial for both novice and seasoned practitioners in the field. The obstacles faced during this process can have significant implications on product quality, environmental sustainability, and overall efficiency. Addressing these challenges can lead to advancements in techniques and materials, improving outcomes in various applications.
Material Waste and Environmental Impact
One of the most pressing concerns in slip casting ceramics is material waste. The process inherently results in surplus slip that does not end up in the final products. This excess material accounts for a sizable portion of waste, leading to environmental issues. The question of sustainability becomes important when considering how raw materials are sourced and used.
To mitigate this waste, several strategies can be considered:
- Recycling Slip: Many manufacturers are adopting methods to reuse leftover slip. This involves collecting excess material and reintroducing it into the production cycle. Effective recycling can minimize waste and conserve resources.
- Raw Material Management: Careful selection and management of raw materials can reduce waste. Understanding the right proportions of clay, water, and additives is essential to optimize the slip for the desired outcome, reducing the likelihood of excess material.
- Environmental Regulations: Adhering to guidelines and regulations can help limit the environmental footprint of slip casting operations. This includes standards for waste disposal and emissions that impact the surrounding area.
Quality Control Issues
Quality control is another critical aspect that challenges many slip casting processes. Variability in slip formulation or inconsistencies during pouring can lead to defects in finished ceramics. This can be detrimental to both aesthetic appeal and functional performance. Therefore, implementing rigorous quality control measures is essential for success.
Some strategies for ensuring quality include:
- Monitoring Slip Consistency: Regular checks on the viscosity and density of the slip help guarantee uniformity. This is paramount because any variation can affect how the slip behaves in the mold.
- Standardized Molding Processes: Utilizing standardized molds and pouring techniques minimizes risks. If molds are not uniform, it can lead to discrepancies in the thickness and strength of the final product.
- Training Personnel: Operators need adequate training to understand the nuances of the slip casting process. Proper training programs can equip workers with the skills needed to identify potential issues and respond effectively.
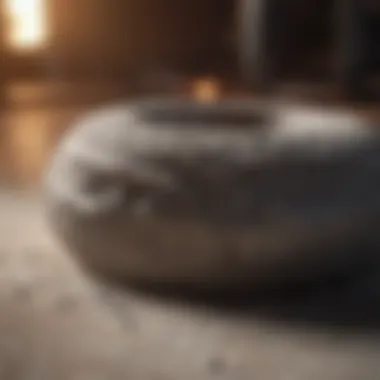
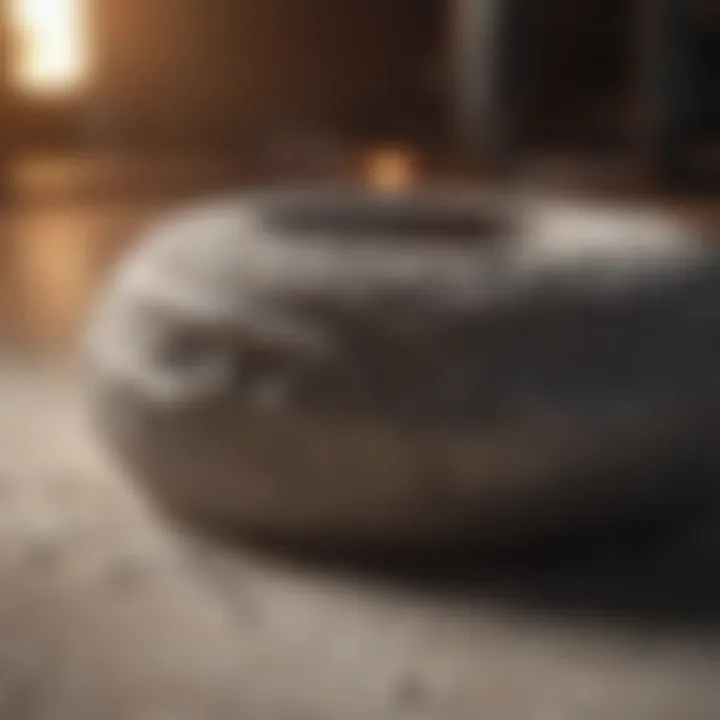
In summary, addressing the challenges of slip casting is vital for maintaining quality and reducing environmental impact. Solutions like recycling materials and implementing stringent quality controls can enhance the overall effectiveness of the slip casting process. Thus, for professionals in ceramics, learning how to navigate these challenges is essential.
Applications of Slip Casting in Various Industries
The versatility of slip casting in various industries cannot be overstated. This method not only enables the production of complex shapes but also ensures efficiency and consistency, which are crucial in a wide range of applications. Understanding the applications of slip casting provides insights into its value in both artistic and industrial contexts.
Art and Craft Ceramics
In the domain of art and craft ceramics, slip casting offers unique advantages. Artists can create intricate designs and forms that would be difficult to achieve through other methods. By using porous molds, the slip adequately fills all details, capturing every nuance of the design. This precision is especially important for decorative items, sculptures, and artisan pottery.
Furthermore, slip casting allows for the production of multiple identical pieces, fostering a balance between creativity and efficiency. Artists can replicate their work while keeping the unique charm that characterizes handmade ceramics. This has opened doors for artisans to exhibit their work in galleries and craft fairs, where beauty and functionality meet.
Industrial Ceramics
For industrial ceramics, slip casting plays a critical role. This sector requires durability and specific material properties that can be tailored through the casting process. Industries such as aerospace, automotive, and electronics utilize slip casting for components that need to withstand extreme conditions. The ability to create complex shapes with exact specifications makes it an effective method for producing ceramic insulators, structural components, and other essential parts.
Another significant aspect is the scalability of slip casting. Once a mold is created, thousands of identical pieces can be produced efficiently, significantly reducing production time and costs. This efficiency meets the demands of industries that require high-volume output without sacrificing quality.
Porcelain and Tableware Production
Porcelain and tableware production is perhaps one of the most recognized applications of slip casting. This process allows manufacturers to create fine china with intricate designs. Porcelain's delicate nature can be honored through slip casting, as the method ensures even thickness and minimizes defects.
The market for tableware is robust, reflecting consumer preferences for both aesthetic appeal and durability. Slip casting supports these demands by creating lightweight yet strong products that are suitable for daily use or special occasions. The wide variety of glazes available enhances the final product's appeal, allowing for artistic expression in functionality.
In summary, the applications of slip casting extend from artistic creations to critical industrial components and fine tableware.
"Slip casting bridges the gap between craft and industry, creating beautiful yet resilient products for diverse needs."
By understanding the importance of slip casting in these fields, we recognize its vital role in advancing both the arts and manufacturing sectors. This exploration serves students, researchers, and professionals seeking to comprehend the multifaceted nature of slip casting ceramics.
Future Trends in Slip Casting Ceramics
The landscape of slip casting ceramics is evolving rapidly, influenced by advancements in technology and materials science. Understanding these future trends is essential for students, researchers, and industry professionals who wish to remain relevant in this field. Innovations not only improve the efficiency and quality of ceramic products but also address sustainability concerns that are growing more significant in today’s manufacturing processes.
Advancements in Materials Science
Recent developments in materials science are reshaping slip casting ceramics. New types of clays and additives are being explored to enhance the properties of ceramic slips. For instance, using nanomaterials has shown promise in increasing the strength and durability of finished products. Researchers are also investigating alternative raw materials that can replace traditional components, making the process more sustainable.
Some benefits of these advancements include:
- Improved mechanical properties: Enhanced materials can produce ceramics with higher resistance to cracking.
- Sustainability: Utilizing alternative materials reduces the reliance on finite resources, decreasing environmental impact.
- Customization: New materials allow for a broader range of applications, catering to specific industry needs such as biomaterials for medical use.
Developments in ceramics might also lead to lighter, more functional designs, especially in industrial applications. The integration of performance materials can result in products that are not only aesthetically pleasing but also functional and efficient.
Automation and Technology Integration
Automation in slip casting is another critical trend. Digital fabrication techniques are becoming prevalent in ceramic production, leading to improved precision and consistency. Technologies such as 3D printing and computer-aided design (CAD) are allowing for the creation of complex molds and forms that were previously difficult to achieve. This shift toward more automated processes brings several merits:
- Increased efficiency: Automation can reduce production times, making large-scale manufacturing more feasible.
- Consistency in quality: Automated systems ensure uniformity in the casting process, reducing human error.
- Innovation in design: Technology facilitates the exploration of creative designs that push the boundaries of traditional ceramics.
The integration of machine learning and artificial intelligence into the casting process will enhance quality control. These technologies can analyze production data in real-time, enabling manufacturers to make quick adjustments and optimize processes.
"The future of slip casting ceramics is not merely about traditional practices; it is about innovation that combines tradition with modern technology to create something entirely new."
In summary, the future of slip casting ceramics is brighter and more dynamic than ever. Advancements in materials science alongside automation will significantly influence both the quality and sustainability of the products. It is crucial for professionals in the field to stay informed and adapt to these changes to harness the full potential of slip casting techniques.
Closure and Implications
The conclusion acts as a pivotal segment that encapsulates the essential themes discussed throughout the article. In the context of slip casting ceramics, it is paramount to comprehend both the technical and artistic merits of this craft. Slip casting not only enhances the production capabilities of ceramic artisans but also broadens the design possibilities. This method facilitates the replication of intricate forms, allowing artists to explore creativity without the constraints typically faced in traditional molding.
Moreover, there are vital considerations regarding the ecological impact of slip casting. Sustainable practices in material sourcing and waste management must become a focal point in the ongoing discourse about ceramics manufacturing. By emphasizing environmentally friendly techniques, the industry can mitigate some of the negative repercussions associated with large-scale production.
In summary, the implications of slip casting extend beyond mere production techniques; they encompass economic, environmental, and artistic dimensions. Understanding these layers provides invaluable insight for stakeholders involved in ceramic production, thereby fostering an industry that is both innovative and responsible.
Summarizing Key Points
- Historical Significance: Slip casting has evolved over centuries, originating in ancient practices and finding place in contemporary ceramics.
- Techniques: Detailed examination of materials, processes, and finishing touches reveals how important precision is in achieving quality outcomes.
- Advantages: This method supports mass-production in ways that allow for complex shapes and wider accessibility. Efficiency is a central strength of slip casting.
- Challenges: The industry must address issues concerning waste and quality assurance consistently while pushing boundaries in material science.
The Role of Slip Casting in Future Ceramics
Looking ahead, the role of slip casting will likely evolve significantly. As technology integrates with traditional methods, newer machines will streamline processes and reduce the labor intensity of slip casting. Automation is already beginning to influence various facets of production, enabling artists to achieve higher levels of precision.
Additionally, advancements in materials science indicate a future where new compositions of ceramic slip might offer improved properties, such as enhanced durability or lower environmental impact.
The crossover between artistic expression and technological innovation will lead to transformative developments. Slip casting may increasingly adopt practices aligned with sustainable production, responding to the growing demand for environmentally conscious manufacturing in various industries, from art to tableware.