Exploring the Aseptic Packaging Process for Food Safety
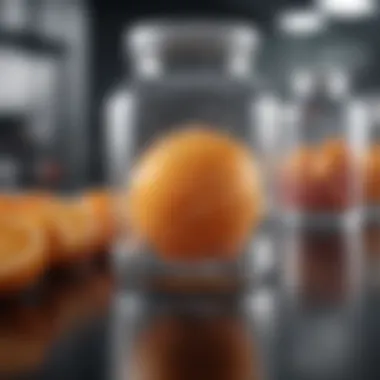
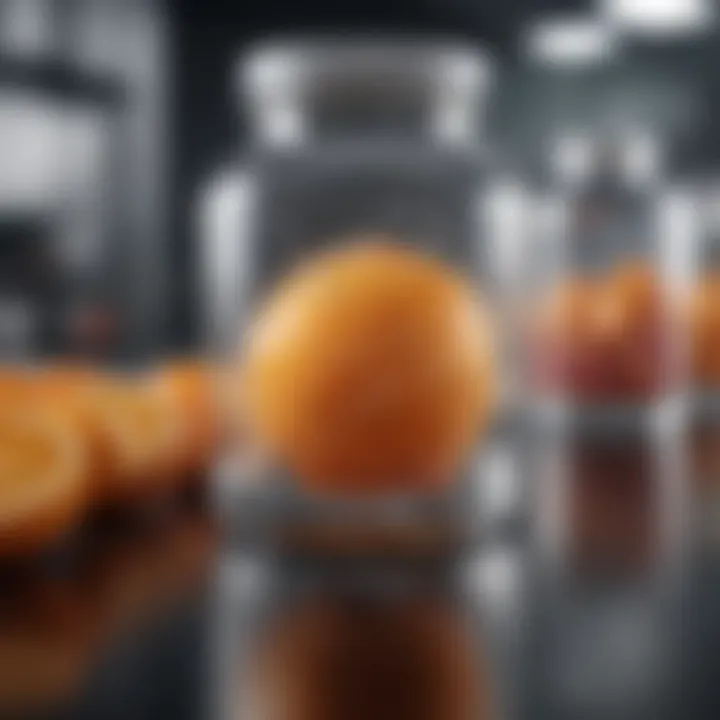
Intro
With the rise of sustainability concerns and preference for minimal preservatives, the relevance of this packaging technique cannot be understated. The aseptic method has roots that stretch back to the early 20th century, yet it has evolved tremendously, adapting to advancements in technology and changes in consumer expectations. In this piece, we will dissect its history, the technologies employed, and the relevance it holds in meeting modern food safety standards. By diving into the operational intricacies, environmental considerations, and future trends, the reader will garner a rich understanding of aseptic packaging and its impact on food preservation and safety.
Prelims to Aseptic Packaging
Aseptic packaging has become increasingly vital in the modern food and beverage industry, playing a critical role in ensuring that products remain safe and effective for consumption long after their production. The process revolves around sterilizing both the product and the packaging independently before they are combined in a manner that maintains sterility. The importance of this technique cannot be overstated, especially in a world where food safety is paramount. Aseptic packaging not only extends the shelf life of perishables but also maintains their nutritional quality, flavor, and overall integrity.
Definition and Importance
To grasp the significance of aseptic packaging, it's essential to define it clearly. Aseptic packaging is, in its simplest terms, a method of packaging that involves sterilizing a food product and its container separately, then bringing them together in a sterile environment. This process effectively prevents any microbial contamination, making it an attractive option for items that would otherwise spoil quickly.
The advantages of this method are manifold:
- Extended Shelf Life: Products can last months or even years without refrigeration.
- Reduction of Food Waste: Longer shelf lives contribute to less spoilage and waste in the supply chain.
- Convenience: Aseptic packaging allows consumers to store products at room temperature, enhancing usability and accessibility.
- Nutritional Preservation: With careful processing, the nutrition and taste profile of the food remains intact.
- Safety Assurance: Customers can feel confident consuming products, knowing rigorous procedures are in place to ensure quality.
Historical Background
The journey of aseptic packaging is rich and rooted in innovation. The origins can be traced back to the early 20th century when food preservation began to gain traction in both household and industrial settings.
- In the late 1800s, canning revolutionized how food was stored, but it wasn't until after World War II that serious advancements in aseptic methods began. The development of the first commercial aseptic filling machines took place in the 1960s, where producers sought alternatives to traditional canning which was often energy-intensive and limiting.
- The launch of Tetra Pak in the 1960s marked a significant milestone with its pioneering designs for packaging liquids, which emphasized both convenience and sterility. This innovation allowed milk and juice producers to distribute their products without refrigeration, subsequently changing consumer habits.
- As the demand for safe and stable products surged, especially amid rising concerns regarding foodborne illness, the aseptic packaging process evolved rapidly through the years. It began incorporating high-temperature processing and advanced materials for packaging, keeping pace with the growing needs for longer shelf life and safety in food products.
Today, aseptic packaging is a cornerstone of food safety strategy across the globe, serving various industries from dairy to pharmaceuticals, and it continues to adapt and innovate in response to modern agricultural and consumer challenges.
"The development of aseptic packaging has not just changed how we store food; it's reshaping the way we think about food production and safety."
The rich historical context combined with a robust understanding of its definition sets the stage for a deeper exploration into the fundamentals and methodologies of the aseptic packaging process.
Fundamentals of the Aseptic Process
In the realm of food preservation, understanding the fundamentals of the aseptic packaging process is paramount. This is no mere technicality; it’s a critical foundation that ensures safety and quality in consumables. Aseptic packaging stands as a bridge between the production environment and the end-user, safeguarding against contamination while maintaining the freshness and nutritional value of products. By grasping the core elements of this process, stakeholders can navigate the complexities of modern food systems more effectively.
Overview of the Packaging Process
At its heart, the aseptic packaging process involves several congruent stages that work together to combat spoilage and microbial growth. The outline of the process is akin to a well-choreographed dance, where each step must be executed flawlessly for the end result to be effective. Initially, the food or beverage is sterilized, often through methods such as heat, steam, or chemicals. Following this, the sterilized product is transferred into pre-sterilized containers within an environment that prevents any exposure to airborne contaminants. This crucial stage happens inside a sterile chamber that minimizes the risk of microbial intrusion.
Next comes the sealing, where the integrity of the package is tested to ensure no gaps exist that might allow bacteria or mold to sneak in. Proper sealing is not merely a finishing touch; it plays a pivotal role in sustaining shelf life and preserving the product’s quality over time. Think of it as a lock on a door; if the door isn’t sealed tight, it opens the way for unwanted guests. On average, products in aseptic packaging can last six months or longer without refrigeration, making this process a lifeline for food security in many regions.
Key Components Involved
The aseptic packaging process hinges on a few essential components, each playing a unique role in the overall efficacy of packaging. Understanding these components not only brings clarity to the process but also highlights the interconnectedness of technology and food safety. Here are the key players:
- Sterilizers: These machines ensure that any product ready for packaging is free from harmful microorganisms. Various forms of sterilization include steam injection, chemical sterilization, or hot water methods.
- Filling Machines: After sterilization, the filling machines take charge, deftly transferring the liquid or solid product into prepared containers without compromising sterility.
- Sealers: These are pivotal in keeping the environment intact and protecting the product from external elements.
- Control Systems: Modern aseptic processes rely heavily on automation. Control systems monitor temperature, pressure, and other key parameters, ensuring that the process remains within safe limits.
- Containers: The materials used for packaging can significantly affect product quality. Common options include polyethylene, aluminum, and glass, each with their distinct advantages.
To put it plainly, without these components working in concert, the whole operation can go awry. Each piece of equipment and technology must function harmoniously, like the gears in a finely-tuned watch, to ensure the food or beverage not only remains fit for consumption but also retains its desired qualities.
Aseptic packaging is an ingenious response to the challenges of modern food distribution and conservation making it a vital piece in today's food handling puzzle.
Technological Innovations in Aseptic Packaging
In the world of food preservation, technological innovation is like the wind at your back, propelling the aseptic packaging process into a realm of efficiency and reliability. These advancements are transforming how we think about food safety, extending shelf life, and maintaining the quality of products without the need for refrigeration. This section focuses on the key elements of these innovations, their benefits, and critical considerations that shape the future of aseptic packaging.
Emerging Technologies
The landscape of aseptic packaging is continually evolving, shaped by various emerging technologies that enhance its efficiency. Several groundbreaking methods have surfaced, each offering unique benefits to producers and consumers alike. Here are a few notable examples:
- High-Pressure Processing (HPP): This technique involves applying intense pressure to food products, eliminating pathogens and enhancing shelf life while preserving flavor and nutritional value.
- Nutritional Ultra-Pasteurization: This method allows for the use of heat treatment at lower temperatures, effectively killing harmful bacteria without compromising the nutrient integrity of the food.
- Smart Packaging Technologies: Innovations in smart packaging provide opportunities for real-time monitoring of the product's condition, including freshness and temperature. This technology helps consumers and suppliers ensure optimal quality and safety throughout the supply chain.

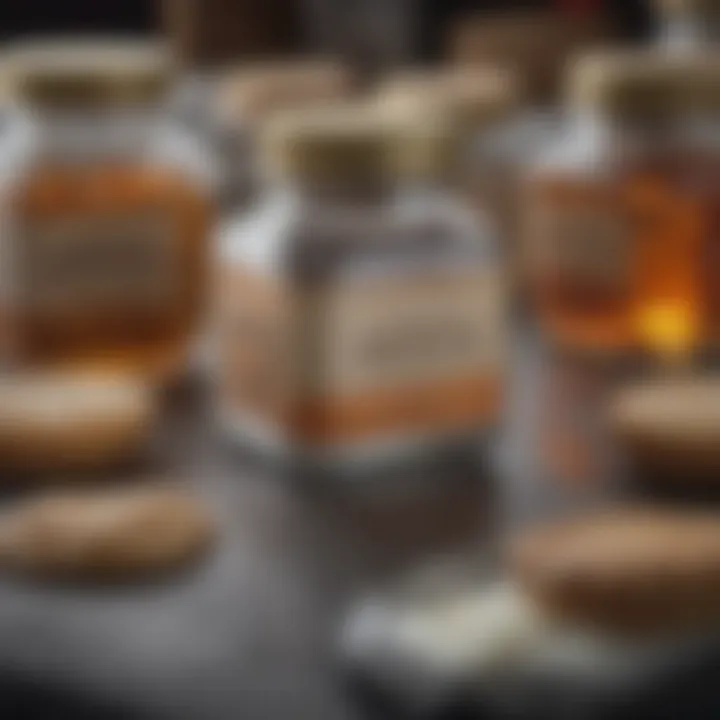
These technological advancements not only facilitate better preservation methods but also resonate with consumer preferences towards healthier choices. Adapting these technologies can lead to improved customer satisfaction and brand loyalty – aspects crucial in today's competitive markets.
Automation in Aseptic Systems
Automation plays a fundamental role in modernizing aseptic packaging processes. By investing in automated systems, companies can streamline operations, enhance productivity, and minimize human error. There are several key elements to consider:
- Increased Efficiency: Automating tasks such as filling, sealing, and packaging significantly reduces the time taken for each cycle, resulting in more products being processed within shorter timeframes.
- Enhanced Consistency: Automated processes offer a level of precision that manual operations can't match. Consistency in fill volumes and sealing integrity leads to uniform quality across all batches, which is paramount in the food and pharmaceutical sectors.
- Data-Driven Decision Making: Automation enables the collection of valuable data during the packaging process. This data can be analyzed for making informed decisions that enhance operational strategies and improve product outcomes.
Adoption of automation technologies also reflects a commitment to sustainability. For example, optimizing the use of materials through automated processes reduces waste, contributing positively to environmental goals.
The integration of these automated solutions showcases how the industry is adapting to meet consumer demands while optimizing operational capabilities.
"Technological advancements in aseptic packaging highlight the industry's evolution, balancing efficiency with safety mandates to meet today’s market needs."
As we investigate the intertwining paths of emerging technologies and automation in aseptic systems, it becomes clear that these innovations are not merely enhancements; they are essential ingredients for advancing food safety protocols and shaping future sustainability initiatives.
Methodologies of Aseptic Packaging
The methodologies employed in aseptic packaging are crucial for its effectiveness in maintaining product integrity and safety. The primary goal is to eliminate microbial contamination while ensuring the quality of food and pharmaceuticals is preserved through various techniques. Understanding these methodologies helps us appreciate the intricate balance between technology, human oversight, and rigorous standards that define the industry today. In this section, we will explore three significant methodologies: Standard Aseptic Techniques, Modified Atmosphere Packaging, and Retort Packaging. Each method has its own unique characteristics and advantages.
Standard Aseptic Techniques
Standard aseptic techniques involve the use of heat, chemicals, or filtration to sterilize packaging materials and the contents to be packaged. The process begins with the sterilization of both the product and the container, followed by filling and sealing in a controlled environment to prevent contamination.
- Key Elements:
- Material Selection: Choosing suitable materials that could withstand the sterilization process; often, glass or specific polymers are favored.
- Sterilization Methods: Heat (such as steam or dry heat) most commonly, but sometimes chemicals are also employed.
- Controlled Environment: Sterile conditions must be maintained throughout the entire filling process.
The beauty of standard aseptic techniques lies in their ability to ensure a long shelf life without the need for preservatives. This not only preserves the taste and nutrition of food products but also enhances consumer safety, making it a vital method in food preservation.
Modified Atmosphere Packaging
Modified Atmosphere Packaging (MAP) is a technique that alters the composition of gases within the packaging to delay spoilage. By adjusting the levels of oxygen, carbon dioxide, and nitrogen, the growth of spoilage organisms can be inhibited. This method is especially beneficial for products that are sensitive to atmospheric conditions, such as fresh produce and certain meats.
- Considerations:
- Optimal Gas Composition: Understanding the specific requirements of each type of food product is key to effective MAP.
- Packaging Materials: The materials used need to be barrier-protective, providing a tight seal to maintain the modified atmosphere.
This approach not only prolongs the shelf life of perishable goods but also retains their flavor and texture. It’s common to find MAP utilized in supermarkets today, where fresh produce can stay viable much longer than traditional packaging techniques.
Retort Packaging
Retort packaging combines the advantages of canned goods and flexible packaging. It involves sealing food within pouches and then heating them at high temperatures to achieve a shelf-stable product. This process effectively destroys bacteria and enzymes that cause spoilage, while also maintaining the taste and nutritional value of the food.
- Main Benefits:
- Convenience: Lightweight and easy to use, retort pouches are increasingly popular in ready-to-eat meals and field rations.
- Safety and Shelf Stability: Provides a longer shelf life without refrigeration; ideal for emergency supplies or military use.
Retort packaging exemplifies the effectiveness of aseptic methodologies, combining modern technology with practicality. Its role in providing safe and long-lasting food options cannot be overstated.
"The methodologies of aseptic packaging not only protect food but also respond to modern demands for convenience and safety, shaping the future of food distribution."
In summary, the methodologies of aseptic packaging are all about maintaining product quality and safety. Whether through traditional sterilization, modifying atmospheric conditions, or employing retort techniques, each method plays a pivotal role in the broader narrative of food safety and preservation.
Quality Assurance and Food Safety Standards
Quality assurance and food safety standards are integral to the aseptic packaging process. They ensure that products delivered to consumers are safe, high-quality, and compliant with regulations put forth by governing bodies. Understanding these standards not only helps manufacturers adhere to the law but also aids in instilling consumer confidence in products.
In the context of aseptic packaging, quality assurance entails rigorous processes and protocols designed to maintain the integrity of food and beverages throughout their shelf life. This is particularly important as the target is to prevent microbial contamination while preserving nutritional quality.
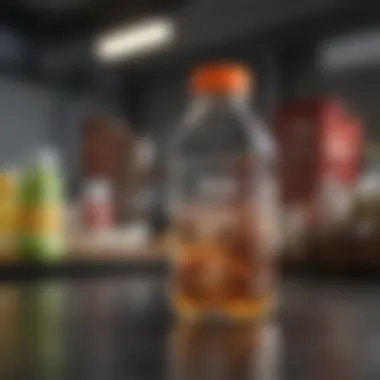
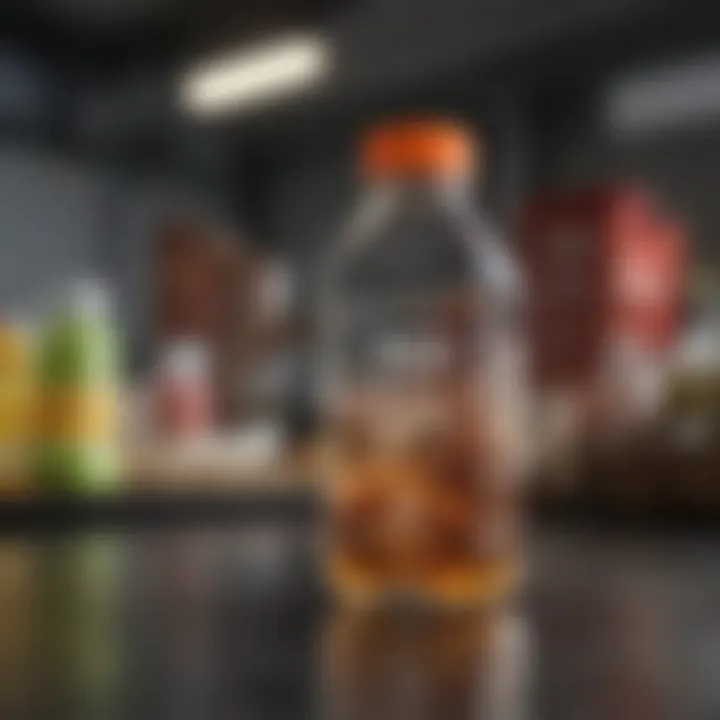
Regulatory Frameworks
Various regulatory frameworks guide the aseptic packaging industry. Agencies like the U.S. Food and Drug Administration (FDA) and the European Food Safety Authority (EFSA) set stringet standards that manufacturers must adhere to. These regulations outline acceptable practices and procedures for each stage of the packaging process, including sterilization methods and material safety.
The global nature of food supply chains means that compliance with local and international standards is critical. Having a solid grasp of these regulations helps companies avoid costly recalls and ensures that their products are ready for the global market. Keeping up with amendments and updates in regulations is also important, as this field is continually evolving due to advances in technology and changes in consumer preferences.
"Compliance is not just a cost; it's an opportunity to stand out in a crowded market by demonstrating your commitment to quality and safety."
Testing and Validation Procedures
Testing and validation procedures form the backbone of quality assurance strategies in aseptic packaging. These methods are designed to verify that each step in the process effectively controls contamination risks.
Common procedures include:
- Microbial testing: Regularly testing products for microbial presence is essential. This helps identify any contamination issues before products reach consumers.
- Sterilization efficacy studies: These studies confirm that the sterilization process effectively eliminates pathogens that could compromise product safety.
- Shelf-life testing: Assessing how long a product can maintain its quality without spoilage is crucial for both safety and marketing.
By performing these validations, companies can fine-tune their processes to enhance food safety and optimize their production efficiency. The documentation generated from these tests not only helps in building a quality assurance narrative but also serves as critical evidence of compliance during audits.
Environmental Impacts of Aseptic Packaging
Aseptic packaging not only plays a crucial role in food safety and longevity but also has significant environmental consequences. As the globalization of food systems and the demand for convenience grow, understanding the environmental impacts of aseptic packaging becomes imperative. This section covers various elements, benefits, and considerations linked to aseptic packaging and its environmental footprint.
Sustainability Considerations
The aseptic packaging process can be viewed through the lens of sustainability, which is becoming paramount in today’s eco-conscious society. One key aspect is the reduction of food waste. By extending the shelf life of products without the need for refrigeration or preservatives, aseptic packaging helps combat food wastage significantly. Studies indicate that nearly one-third of food produced globally is wasted, and effective packaging solutions can contribute to reducing this alarming statistic.
Furthermore, the materials used in aseptic packaging are often designed to be lightweight compared to traditional packaging, thus minimizing transportation emissions. Consider the following points:
- Reduced Carbon Footprint: The lightweight nature of aseptic packages means that less energy is expended during both production and transportation.
- Recyclable or Compostable Materials: Innovations in materials, such as those derived from renewable resources, offer opportunities for recycling or composting after use, leading to a lower overall environmental impact.
- Reduced Use of Preservatives: Aseptic packaging’s ability to keep products safe without chemical preservatives aligns with sustainability goals, promoting cleaner ingredient lists which are increasingly demanded by consumers.
Waste Management Strategies
With the rise in popularity of aseptic packaging, addressing waste management becomes crucial in mitigating its environmental impact. Here's a closer look at some effective strategies:
- Recycling Programs: Implementing and promoting recycling initiatives specifically for aseptic packaging materials can divert waste from landfills. Manufacturers and retailers can collaborate to develop programs that facilitate the collection and recycling of used packages.
- Education and Awareness: Educating consumers regarding proper disposal methods is essential. Many individuals may not realize that certain aseptic containers can be recycled, leading to higher rates of food and package waste left unmanaged.
- Innovative Collection Points: Establishing dedicated collection boxes for these items at supermarkets or community centers can encourage proper disposal and recycling of aseptic packages.
"Aseptic packaging can play an instrumental role in promoting a more sustainable future, provided that effective waste management strategies are cornerstones of its implementation."
- Lifecycle Assessment: Carrying out lifecycle assessments of aseptic packages helps to identify the environmental footprint from production to disposal, informing better practices and reducing negative impacts.
In summary, while aseptic packaging presents many advantages regarding food safety, its environmental implications cannot be overlooked. With responsible practices in recycling and waste management, the aseptic packaging industry can contribute to a more sustainable future.
Applications of Aseptic Packaging
Aseptic packaging plays a pivotal role in various sectors, particularly in food and pharmaceuticals. Its importance lies in ensuring the longevity and safety of products while also meeting the increasing demand for convenience and quality. In an era where consumers are ever more health-conscious, understanding the applications of aseptic packaging is crucial.
One significant aspect of aseptic packaging is its ability to extend shelf life without preservatives. This technique allows for the preservation of taste, texture, and nutrient content, which are vital for consumer satisfaction. Furthermore, as globalization continues to grow, aseptic methods facilitate the transport of food items over long distances without compromising quality.
"The true value of aseptic packaging is at the intersection of quality preservation and safety, allowing food and medicines to travel far and wide without diminishing their integrity."
Use in Food Products
Aseptic packaging is revolutionizing the food industry by allowing perishable products to be stored for extended periods, often years, without refrigeration. One of the most common applications is in juice packaging. For instance, brands like Tropicana and Minute Maid utilize this technique to keep natural flavors intact while avoiding any added sugars or preservatives. Similar processes are used for dairy products, soups, and sauces, ensuring they remain safe to consume and do not require cooling before opening.
Aside from beverages and dairy, ready-to-eat meals packaged aseptically offer convenience without a trade-off in quality. The process involves heating the food to kill bacteria before sealing it in a sterile container, which effectively minimizes spoilage and enables it to be shelf-stable.
- Key Benefits in Food Applications:
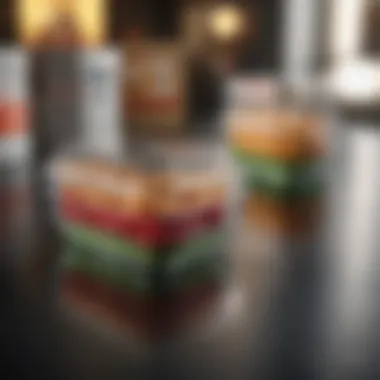
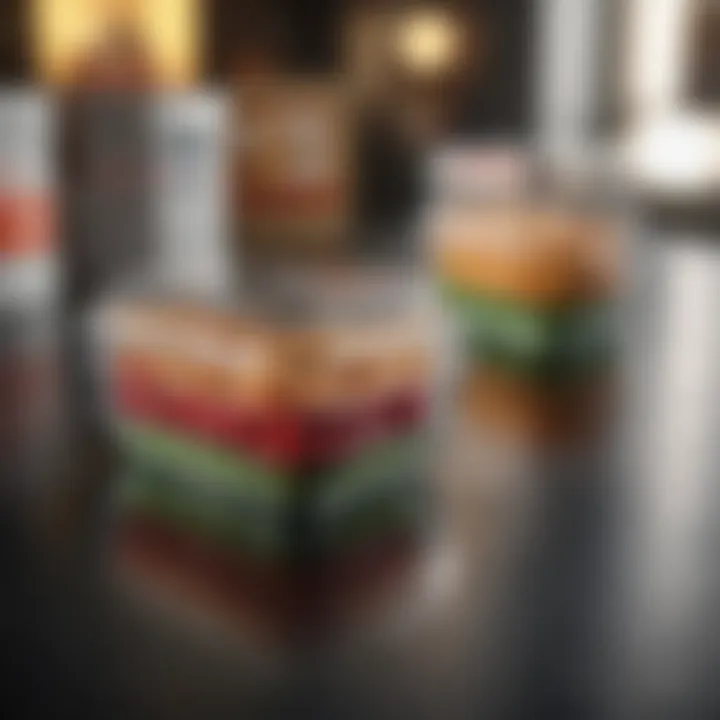
- Extended shelf life
- Reduced need for preservatives
- Enhanced flavor and nutritional retention
Pharmaceutical Applications
In the pharmaceutical realm, aseptic packaging is critical to ensuring that medications, particularly sterile injectables and other sensitive formulations, maintain their efficacy and are free from contaminants. Pharmaceutical companies, like Pfizer, often employ this method for a range of products, including tablets and vials, ensuring that they remain safe over time.
Aseptic techniques in pharma not only protect the medications from microbial contamination but also allow for easier handling and storage. Products can be distributed globally, ensuring that patients receive high-quality medications regardless of their location.
The technologies behind these systems must be finely tuned; any lapse in aseptic conditions can lead to recall and significant economic loss. Modern automated filling lines, for example, incorporate advanced robotics to reduce human contact, further minimizing contamination risks.
- Key Considerations for Pharmaceutical Applications:
- Stringent regulatory oversight
- Comprehensive validation processes
- Minimization of human contact in the packaging process
Challenges in the Aseptic Packaging Industry
The aseptic packaging industry plays a crucial role in food preservation and safety. Yet, like any sector, it faces several challenges that can impact its growth and efficiency. Understanding these challenges is key for professionals and academics alike, offering insights into potential areas for improvement and innovation. This section will explore operational hurdles and market competition, both significant elements that can affect not just the industry players but also the consumers who rely on these products.
Operational Hurdles
Operational hurdles are often the bedrock of complications within the aseptic packaging field. These challenges can stem from various factors, ranging from technological limitations to workforce training. Below are several key operational hurdles:
- Technological Infrastructure: Not every facility has access to the latest aseptic packaging technology, which can lead to inefficiencies. Older equipment may not function optimally, potentially compromising product safety. This is especially significant considering that the cost for upgrades can be substantial.
- Training and Skill Gaps: A knowledgeable workforce is essential for smooth operations. However, there may be a lack of trained personnel capable of navigating complex packaging systems. Constant advancements in technology mean that ongoing training is not just an option but a necessity.
- Supply Chain Disruptions: Aseptic packaging relies on a finely-tuned supply chain. Disruptions—whether due to natural disasters, political instability, or logistical challenges—can wreak havoc on production schedules. Moreover, as many components come from various suppliers, consistency in quality can be a concern that needs close attention.
"Operational issues can deter innovation, but addressing them head-on can lead to breakthroughs in efficiency and safety."
- Regulatory Compliance: Meeting the stringent regulations set by food safety authorities is no small feat. Constant changes in these regulations require companies to adapt quickly, often straining their operational capabilities. Companies need to maintain high standards to avoid costly penalties.
These operational hurdles not only affect the bottom line but also have broader implications on the reliability of food products. Addressing these challenges requires a comprehensive approach that marries technology, training, and meticulous regulatory adherence.
Market Competition
Market competition in the aseptic packaging industry is fierce and ever-evolving. New entrants often disrupt established players, creating a dynamic environment that forces adaptation and innovation. Below are some considerations regarding market competition:
- Cost Pressure: Many companies are facing pressure to reduce costs without compromising quality. This is challenging, as lowering operating expenses often leads to tough decisions—like cutting corners on safety or quality. The delicate balance of maintaining low prices while ensuring high standards can be a tightrope walk.
- Innovation Race: Companies are constantly on the lookout for the next big thing in aseptic technology. This creates a race where those who don’t keep pace might find themselves left behind. The development of smart packaging solutions, for example, is a rapidly growing area that requires significant investment and research.
- Brand Loyalty and Consumer Trends: The modern consumer has a heightened awareness of food safety and sustainability. Shifts in consumer preferences can influence market competition. Companies must stay attuned to these trends, ready to innovate their packaging solutions to meet customer demands. If a brand fails to match these expectations, consumers aren’t afraid to switch loyalty.
- Globalization: With the ability to source products from around the globe, competition is not just local. Companies must be aware of international competitors who may be able to provide lower prices or innovative solutions. This may force companies to adopt global standards, which can be both an opportunity and a challenge.
Future Directions and Trends
The landscape of the aseptic packaging industry is undergoing a transformation, driven by various factors that demand innovation and adaptation. The importance of understanding future directions and trends cannot be understated. As consumer preferences shift and regulatory demands tighten, stakeholders must stay abreast of emerging developments. This section will explore the significance of innovative packaging solutions and the integration of smart technologies, underscoring their potential benefits and considerations for the future.
Innovative Packaging Solutions
In a world where consumers are increasingly becoming environmentally conscious, innovative aseptic packaging solutions are rising to the occasion. Manufacturers are experimenting with biodegradable materials, reducing waste while maintaining the integrity of food and pharmaceuticals. Examples include using advanced polymers or natural fibers that break down much easier than traditional plastic materials.
- Benefits of Innovative Solutions:
- Enhanced sustainability
- Increased consumer appeal
- Reduction in costs through efficiency
Moreover, companies are embracing multifunctional packaging, which not only acts as a barrier to external elements but also incorporates features like moisture control or oxygen scavenging. This trend marks a significant leap as it allows products to have longer shelf lives while preserving quality.
Furthermore, the development of edible packaging is also gaining traction. Imagine packaging that, instead of ending up in a landfill, can be consumed along with the product! This approach raises a few eyebrows but certainly opens up discussions on how we view packaging material today.
"Innovative ideas in packaging aren’t just about protecting the product—they're crucial for protecting the planet too."
Integration with Smart Technologies
As technology continues to evolve, the integration of smart tech into the aseptic packaging process is becoming more apparent. Smart packaging is not merely a buzzword; it provides real-time data and insights into the condition of the product. Labels with embedded sensors or QR codes enable tracking and monitoring of storage temperature and shelf life.
- Key Considerations for Smart Tech in Packaging:
- Cost vs. Benefit Analysis: Implementing smart technology might require significant investment, thus requiring justification through enhanced efficiency or quality checks.
- Consumer Engagement: Augmented reality features can connect consumers with the product's journey, increasing trust and transparency.
- Data Security: As with any tech integration, safeguarding the data collected must remain a priority to maintain consumer trust.
Linking these advancements with IoT (Internet of Things) opens avenues for real-time alerts for supply chain disruptions. Such connectivity can bolster efficiency by informing stakeholders instantly about potential quality issues, thereby minimizing loss.
In summary, the future of aseptic packaging rests heavily upon innovative solutions and technological integration. Understanding and embracing these trends enables industry stakeholders to stay competitive while supporting broader sustainability goals.