Zirconia Machining: Challenges and Techniques
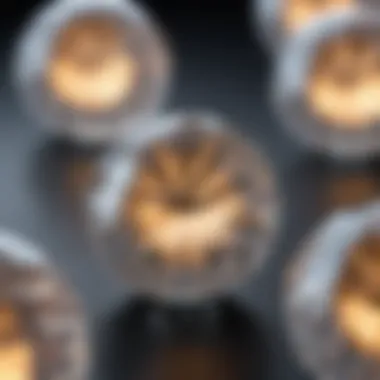
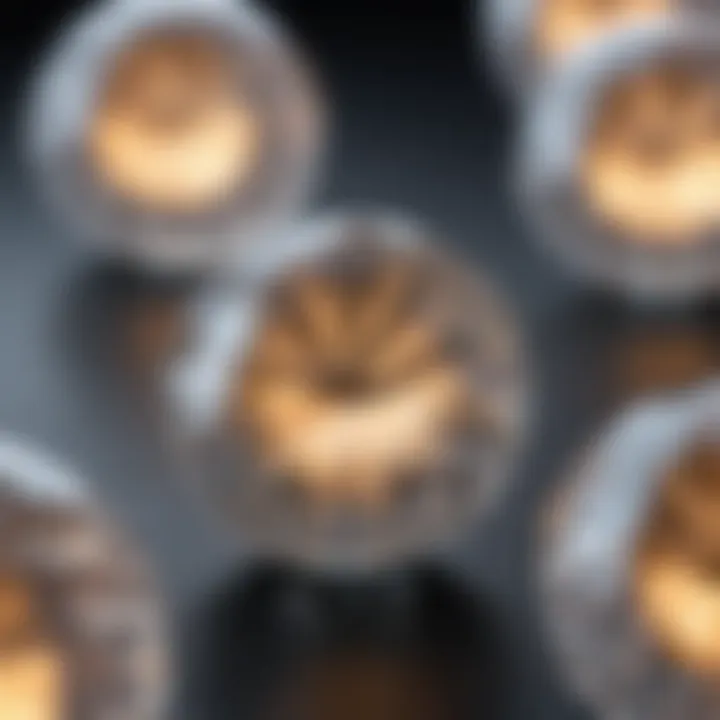
Intro
Zirconia machining presents a captivating field of study, characterized by a range of intricate properties and formidable challenges. Widely recognized in industries such as dentistry, aerospace, and electronics, zirconia’s unique characteristics make it both a favorite and a puzzle for machine operators and engineers alike. As we dive into the subject, this article aims to shed light on various facets of zirconia machining, including its mechanical properties, the obstacles faced during processing, new techniques emerging in the field, and its growing significance across diverse industries.
The journey will take us through understanding zirconia itself, exploring why it's such an attractive material for manufacturing. From hardness to resistance to corrosion, its attributes set the stage for its wide utilization. However, this comes with a catch: machining zirconia isn't as straightforward as it might seem. The difficulties often encountered, such as tool wear and thermal stability, can transform the process into a minefield if not navigated properly.
Key insights will be pulled together, examining methodologies being adopted in modern zirconia machining. We will also highlight how technological advancements are influencing these techniques and pushing the envelope of what's possible.
By the end of our exploration, we aim to provide a well-rounded understanding that is not just relevant but also indispensable for students, researchers, educators, and professionals engaging with this advanced material.
Foreword to Zirconia
Zirconia, or zirconium dioxide, has become a material of immense significance in various industries because of its unique properties. Understanding zirconia is not just about looking at its chemical composition; it encompasses exploring how it performs under different conditions and what makes it suitable for a range of applications. This introduction serves as the groundwork for deeper discussions later in the article, establishing the importance of zirconia in machining processes and the factors influencing its widespread use.
One of the key benefits of zirconia is its exceptional toughness and resistance to wear, which makes it a prime candidate in the dental and medical fields. These properties allow for highly durable prosthetics that stand the test of daily wear and tear. Unique thermal properties are also worth noting. Zirconia exhibits low thermal conductivity, a trait critically valued in sectors like aerospace, where component reliability is essential even under extreme temperatures. Thus, having a solid grounding in zirconia’s qualities will lead to a more comprehensive understanding of the subsequent sections.
Moreover, this section serves as a stepping stone for readers, facilitating a seamless transition into the material’s historical context. Knowing the material's evolution will enable readers to appreciate the challenges and advancements discussed later in the article.
Understanding Zirconia
Zirconia is a crystalline compound derived from zirconium, a metal that comes from ores like zircon. When discussing zirconia, one must consider its polymorphism: it can exist in several forms, notably cubic, tetragonal, and monoclinic phases. In engineering and manufacturing, the most commonly utilized form is the cubic phase, which exhibits remarkable strength and flexibility. This characteristic makes zirconia highly sought after in applications where stress resistance is paramount.
The significance of zirconia extends beyond mere functionality. Its aesthetic appeal comes into play especially in dental applications, where it can be crafted to mimic natural tooth color. This characteristic renders zirconia more than just a mechanical asset; it merges functionality with beauty, setting it apart from other materials.
In recent years, zirconia's role has expanded dramatically. The advancement in fabrication techniques has allowed for increasingly complex designs and immediate access to high-precision components. With 3D printing and other innovative manufacturing methods taking center stage, zirconia will undoubtedly play a pivotal role in the future of production.
Historical Context and Development
The history of zirconia is a fascinating tale of discovery and technological advancement. The use of zirconium dates back to the 18th century, when it was first isolated by the Swedish chemist Jöns Jacob Berzelius. However, the significant shift to zirconia as a usable industrial material began much later, in the late 20th century. Initially, it was regarded as a mere curiosity, but as industries began to prioritize strength and thermal stability, its value soared.
In the 1980s, the dental industry recognized zirconia for its commendable mechanical properties. Its application in dental ceramics signaled a significant breakthrough, ushering in a new era where aesthetics became as important as functionality in prosthetics. Such a shift marked zirconia's transformation from an obscure compound to an integral player in modern medicine and engineering.
With ongoing research, zirconia continues to evolve. Enhanced manufacturing processes have led to the development of advanced ceramics featuring Ce-TZP (cerium stabilized tetragonal zirconia polycrystals), further broadening its horizons in various fields including aerospace, where high performance is non-negotiable. As we stroll through the annals of its development, it’s clear that zirconia’s story is just beginning.
Material Properties of Zirconia
Understanding the material properties of zirconia is crucial when it comes to machining this advanced material. Its unique characteristics not only influence the machining process but also determine its applicability across various industries. Zirconia, or zirconium dioxide, is known for several essential properties, including outstanding mechanical strength, thermal stability, and biocompatibility. These traits make it a preferred choice in fields ranging from dentistry to aerospace.
Mechanical Characteristics
Zirconia is renowned for its mechanical strength, which sets it apart from many other materials. It exhibits high flexural strength and toughness that make it resistant to fracture, even under considerable stress. This characteristic is particularly significant in applications requiring durability and reliability.
- High Strength: Zirconia maintains its strength under varying conditions, which is essential in applications like dental crowns.
- Toughness: The ability to absorb energy without cracking enhances performance in structural components.
Though it is a brittle material, innovative machining methods can harness its strengths effectively. Utilizing tools made of diamond or cermet can minimize tool wear, which is a common issue encountered when machining zirconia.
Thermal and Chemical Stability
Another noteworthy feature of zirconia is its remarkable thermal and chemical stability. This property allows zirconia to withstand high temperatures without significant degradation of its physical properties. This stability is vital in applications like thermal barrier coatings and in areas exposed to extreme heat conditions.
- Thermal Resistance: Zirconia performs well at elevated temperatures, making it suitable for environments where other materials would fail.
- Chemical Stability: It resists corrosion and oxidation, ensuring a long service life even in harsh environments.
These thermal and chemical properties ensure that components made of zirconia can perform reliably over extended periods, enhancing their appeal in fields such as lighting or electronic devices.
Biocompatibility and Applications in Health Care
Zirconia is also highly regarded for its biocompatibility, making it a popular choice in health care applications. The ability of zirconia to interact safely with biological systems facilitates its use in various medical devices and implants.
- Dental Implants: The use of zirconia in dental applications stems from its aesthetic appeal, high strength, and resistance to plaque accumulation.
- Surgical Instruments: Its corrosion resistance contributes to the longevity and effectiveness of surgical tools.
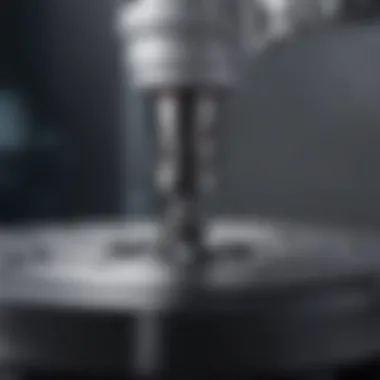
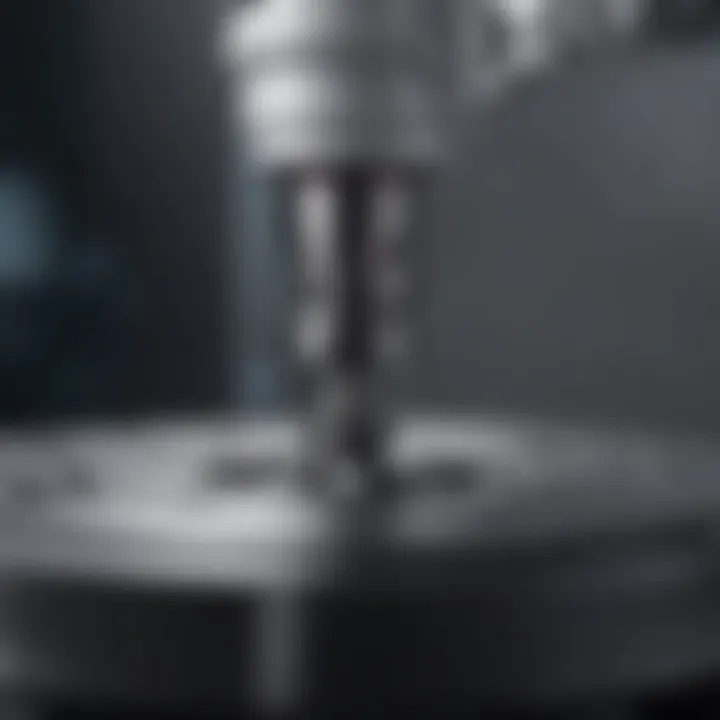
"Zirconia's compatibility with biological tissues, coupled with its mechanical properties, makes it a game-changing material in the health care field."
These factors collectively underline the significance of zirconia’s material properties in machining and application across diverse industries. Its unique characteristics not only bolster its performance but also pave the way for revolutionary advancements in technology and manufacturing.
Challenges in Zirconia Machining
When it comes to machining zirconia, one cannot overlook the notable hurdles that accompany this intricate process. Understanding these challenges is crucial for anyone involved in the field, from students learning the ropes to experts fine-tuning their techniques. Zirconia’s properties, while advantageous, also introduce complexities that can complicate its machining. Not only can these issues lead to inefficiencies, but they can also affect the overall quality of the final product.
Brittleness and Tool Wear
Zirconia is known for its impressive strength and durability, but this very brittleness presents a unique set of problems during machining. When subjected to stress, zirconia can chip or crack, causing significant waste and requiring costly rework. This brittleness means that traditional machining tools often struggle to keep up. Regular cutting tools, made from high-speed steel for instance, tend to wear down quickly when used on zirconia, resulting in reduced precision and increased time for tool replacements.
"The challenge of brittleness is like trying to cut through ice with a spoon; it requires specific tools and methods to get any work done efficiently."
To combat tool wear, it's imperative to use tooling materials designed for high hardness and toughness such as polycrystalline diamond (PCD) or cubic boron nitride (CBN). These materials not only hold up better against the abrasive nature of zirconia but also contribute to precision in machining. However, choosing the right tools often requires a deeper understanding of the machining parameters—something less experienced operators might overlook.
Moreover, as the cutting edge of a tool dulls, it can lead to further complications. Increased friction can generate excessive heat, which could potentially alter the structure of zirconia and undermine the integrity of the workpiece. Operators must constantly monitor tool conditions and be prepared to make timely adjustments to prevent catastrophic failures.
Surface Finish and Precision
The quality of the surface finish on zirconia machined parts is another significant concern. Given that zirconia is commonly utilized in applications where precision is paramount, such as dental implants or components in aerospace, any compromise in surface quality won’t be taken lightly. Poor surface finishes can lead to increased friction, wear, and ultimately failure in applications needing high reliability.
Achieving a flawless finish typically necessitates multiple machining operations which can complicate the workflow. For instance, manufacturers may need to employ techniques such as grinding after the primary machining. While effective, these methods are time-consuming and can add substantial costs to production processes.
An additional issue arises when trying to implement high-speed machining methods. High speed can indeed enhance productivity but can also introduce vibration, leading to an instability that damages the surface finish and compromises precision. Striking a fine balance between speed and stability becomes a critical task for machinists.
One possible solution to these challenges involves leveraging advancements in technology, such as the use of computer numerical control (CNC) machines which provide greater control over the machining process. By optimizing the parameters through which the machining occurs, one can improve both surface finish and overall precision.
In summary, tackling the challenges of brittleness and surface finish during zirconia machining is of utmost importance. With the right tools, techniques, and constant vigilance, machinists can significantly enhance their outcomes, paving the way for the material’s broader adoption across various industries. Understanding these challenges not only aids in improving machining processes but ultimately contributes to the pursuit of engineering excellence.
Techniques in Zirconia Machining
In the realm of zirconia machining, selecting the appropriate techniques can significantly influence both the efficiency of the production process and the quality of the finished product. Various methods exist, each offering its own benefits and considerations that can align with specific project requirements. Understanding these techniques is fundamental in maximizing the potential of zirconia as a material, enabling professionals to confront challenges head-on while pushing the boundaries of application.
Conventional Machining Methods
Conventional machining methods have been utilized for years across multiple industries, providing a solid foundation for working with zirconia. Techniques like grinding and milling make the most of the material's mechanical properties, though they do come with challenges related to wear and accuracy.
- Grinding involves the use of a rotating wheel coated with abrasive particles, effective in shaping and finishing zirconia. This method, while offering potential for precision, can wear down tools much faster due to zirconia's hardness.
- Milling employs rotating cutting tools to remove material, but again, wear can be a concern, especially when using traditional tooling materials.
One important consideration in conventional machining is ensuring the machinery is equipped with the right specifications to handle the intricate demands of zirconia. A misstep here could mean compromised quality, leading to increased costs and wasted materials.
Advanced Machining Techniques
As technology has advanced, machining techniques have evolved, introducing innovative methods that harness the unique characteristics of zirconia. These advanced techniques, particularly electrochemical machining and laser machining, are instrumental in addressing some of the limitations posed by traditional methods.
Electrochemical Machining
Electrochemical machining (ECM) leverages the principles of electrolysis to remove material, offering a non-contact method that minimizes mechanical stresses on zirconia components.
- Key characteristic: The ability of ECM to achieve complex shapes with high precision is a standout feature. This capability reduces the risk of workpiece cracking, particularly essential when dealing with brittle materials like zirconia.
- Unique feature: One significant advantage of ECM is its capability to machine intricate geometries without causing deformation. This is especially advantageous for delicate applications in fields such as aerospace and medical device manufacturing.
However, it is pertinent to mention that ECM may require specialized equipment and expertise, potentially elevating initial investment costs.
Laser Machining
Laser machining has garnered attention for its ability to achieve remarkably fine cuts and engravings on zirconia. This method utilizes focused laser beams to vaporize material, a technique that is both efficient and precise.
- Key characteristic: A prominent feature of laser machining is its speed; setups can often be completed in a shorter time frame compared to traditional methods. This efficiency, coupled with the ability to cut complex designs, makes it an attractive option.
- Unique feature: The adaptability of laser machining means it can be employed for various applications, from creating intricate patterns to larger structural components, with minimal thermal impact on the surrounding material.
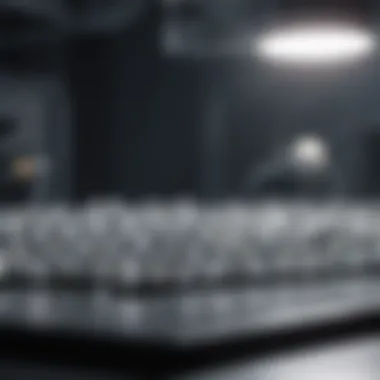

Despite its numerous advantages, laser machining can produce heat-affected zones, which may influence the material properties of zirconia. Hence, careful consideration is required to mitigate this effect during the machining process.
3D Printing of Zirconia
3D printing has opened new doors in zirconia machining by allowing for additive manufacturing techniques. This innovative approach enables the layer-by-layer construction of components, offering design flexibility that traditional machining methods cannot match.
3D printing facilitates rapid prototyping and can significantly reduce the time from concept to production. Additionally, it opens the door to customizations that are essential in applications like dental prosthetics and orthopedic implants.
However, challenges remain, such as achieving high-density parts and ensuring proper adhesion of layers, which are essential for maintaining the integrity of the final product. With continual advancements in technology, the capabilities and applications of 3D printed zirconia are expected to expand further, offering exciting possibilities for future developments in the field.
Machining Tools and Equipment
When it comes to zirconia machining, the choice of tools and equipment is nothing short of pivotal. This advanced material, known for its incredible hardness and thermal stability, requires specialized machinery to ensure precision and efficiency. The correct selection of tools not only affects the quality of the final product but also impacts the machining process itself, driving productivity and minimizing costs.
Cutting Tools Design
Designing cutting tools for zirconia machining is a nuanced endeavor. Unlike softer materials, zirconia can lead to rapid tool wear if traditional tool designs are used. Thus, cutting tools must be crafted with an understanding of the material's properties. High-performance ceramics or diamond-coated tools often come into play here.
- Tip Geometry: The sharpness and shape of the tool tip are essential for creating clean cuts and preventing chipping during the machining process. A well-designed tool tip can significantly enhance cutting efficiency, making the machining operation smoother.
- Tool Length: The length of the cutting tools must be considered in relation to the specific machining operation. Longer tools are sometimes necessary for deeper cuts but may introduce flex, which can compromise precision.
- Material Selection: Selecting the right base material for cutting tools is crucial. For instance, ceramic tools provide exceptional hardness, while carbide tools can offer greater toughness. Balancing these properties is key for optimizing performance.
In practice, engineers often conduct trials to assess the effectiveness of different tool designs. This iterative process can yield insights into which configurations produce the best results, allowing for continuous improvement.
Wear-Resistant Coatings
With zirconia's abrasive nature, wear-resistant coatings have emerged as a necessary aspect of machining tools. These coatings serve a dual purpose: enhancing tool lifespan while improving the machining accuracy. The interplay between the coating and the tool substrate is vital to achieving desired performance outcomes.
- Types of Coatings: Common wear-resistant coatings include titanium nitride (TiN), aluminum oxide, and titanium alumina. Each type offers different benefits in terms of hardness and friction reduction. For instance, TiN is often favored for its ability to resist oxidation and enhance surface smoothness during machining.
- Application Methods: The process of applying these coatings can vary, but physical vapor deposition (PVD) and chemical vapor deposition (CVD) are two widely used techniques. These methods create a thin layer of coating that adheres strongly to the tool, ensuring durability.
- Performance Impact: Research has shown that tools with wear-resistant coatings can significantly extend operational life, reducing the need for frequent tool changes. This not only saves costs but also reduces downtime in manufacturing operations.
"Choosing the right tools is like selecting the right key for a lock; it can make all the difference in achieving success in zirconia machining."
Applications of Zirconia Machining
The significance of zirconia machining cannot be overstated, especially when one considers its diverse applications across multiple industries. Zirconia, known for its resilience, exceptional mechanical properties, and compatibility with biological tissues, has found its niche in sectors that demand high performance, precision, and durability. This section delves into the specific applications of zirconia machining, detailing how these benefits translate into real-world uses.
Dental Applications
When one thinks of zirconia, dental applications often take the forefront. The use of zirconia in dental prosthetics has gained tremendous popularity owing to its aesthetic appeal and strength. Zirconia crowns and bridges not only mimic the translucency of natural teeth but also exhibit remarkable resistance to wear and fracture.
The benefits include:
- Aesthetics: With its tooth-like color, zirconia can be crafted to match natural dentition seamlessly.
- Durability: Zirconia’s high strength ensures that dental restorations withstand chewing forces without cracking.
- Biocompatibility: Patients experience fewer allergic reactions since zirconia is free from metals, making it suitable for restorative dentistry.
Moreover, the precision in machining zirconia allows for more customized solutions in dental implants, ensuring that patients receive prostheses tailored to their unique anatomical needs.
Aerospace and Automotive Industries
In sectors like aerospace and automotive, where safety and efficiency are paramount, zirconia machining stands out. Components made from zirconia are used in high-performance engines and turbine systems where extreme conditions prevail. The inherent qualities of zirconia allow parts to endure heat while remaining lightweight.
Key aspects include:
- Thermal Stability: Zirconia maintains its properties under extreme temperatures, critical in jet engines and exhaust systems.
- Corrosion Resistance: This material proves itself in environments that pose chemical threats, ensuring longevity despite harsh elements.
- Weight Reduction: Lighter components lead to improved fuel efficiency, a crucial factor in modern transport solutions.
By machining components from zirconia, manufacturers can produce parts that enhance overall vehicle performance while adhering to stringent regulatory standards, thereby contributing to the advancement of technology in transportation.
Electronics and Other Sectors
Zirconia’s applications extend into the electronics sector, where its insulating properties are critical. Components such as insulators, capacitors, and substrates benefit from zirconia’s ability to withstand electrical stress. Additionally, its thermal conductivity makes it suitable for heat dissipaters in electronic devices, preventing overheating.
Considerations for the electronics industry include:
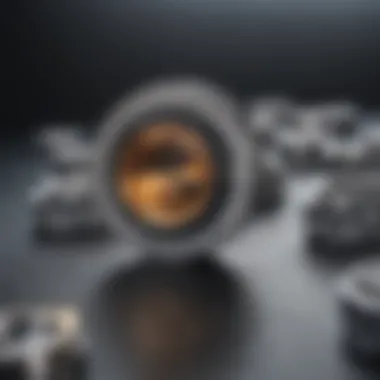
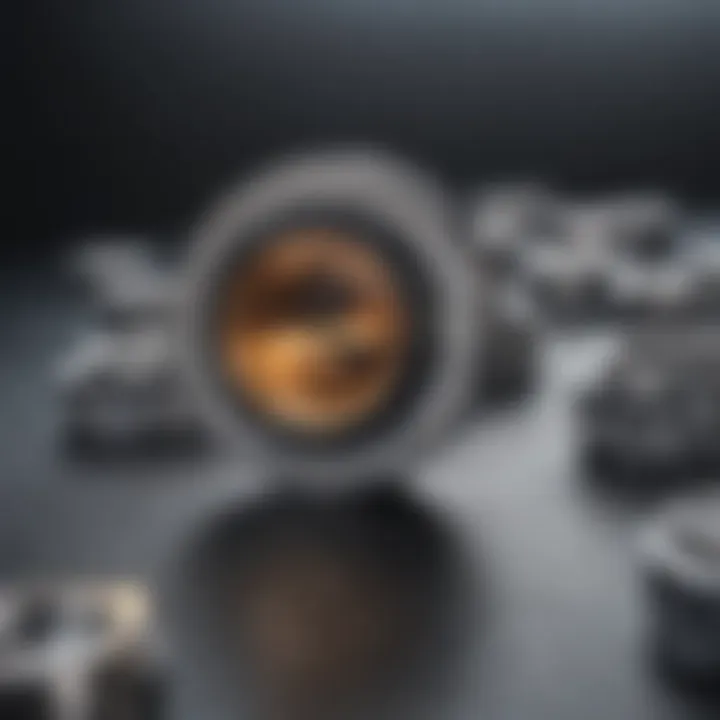
- Insulation: Zirconia provides excellent electrical insulation, essential for safety and efficiency in electrical applications.
- Miniaturization: As the industry pushes for smaller components, the intricate machining capabilities of zirconia allow for the design of compact electronic parts without compromising performance.
- Adaptability: Zirconia is being utilized in sensors and actuators, showcasing its capability in microelectromechanical systems (MEMS).
Furthermore, zirconia is also utilized in other sectors, such as textiles and chemical processing, underscoring its versatility in meeting the unique demands of various industries.
In summary, zirconia machining plays a vital role in enhancing the effectiveness and longevity of components across multiple fields. From dental applications ensuring patient satisfaction to aerospace engines optimizing performance, and electronics ensuring safety, the adaptability of zirconia is nothing short of remarkable.
Environmental Considerations
In an age where the conversation around sustainability and environmental stewardship is more relevant than ever, the machining of zirconia is no exception. Zirconia machining carries both challenges and opportunities as we consider its environmental impact. Understanding these elements is crucial for industries that utilize zirconia, as it affects everything from regulatory compliance to corporate responsibility.
The significance of integrating sustainable practices in zirconia machining cannot be overstated. As industries grow increasingly conscientious about their ecological footprint, focusing on sustainability not only enhances a company's public image but also can lead to cost savings in the long run. By adopting greener methods, one can reduce waste, lower energy consumption, and minimize the overall environmental impact. In fact, companies committed to sustainable practices often find that they can improve manufacturing efficiency while positioning themselves ahead of competitors.
Sustainability in Zirconia Machining
Sustainability in zirconia machining revolves around multiple key aspects:
- Energy Efficiency: The machining process can be energy-intensive. Switching to energy-efficient machinery or optimizing existing processes can greatly reduce power usage and greenhouse gas emissions.
- Material Utilization: Efficient material design and holders help ensure that less raw material is wasted during machining. This not only conserves resources but also cuts down on costs.
- Reducing Emissions: Employing advanced technologies such as dry machining instead of traditional methods can significantly reduce the emission of harmful volatile organic compounds (VOCs) associated with lubricants and coolants.
Each of these practices has the potential to contribute to a more sustainable zirconia machining process. The proactive approach towards sustainability also resonates well with consumers and stakeholders, drawing a direct connection to corporate ethics.
Recycling and Recovery Techniques
Recycling and recovery techniques serve as critical components of a sustainable zirconia machining process. The industry is increasingly looking to innovate ways to reclaim materials that would otherwise be discarded.
Common methods include:
- Milling Scrap Recovery: Zirconia machining creates significant amounts of scrap material. Innovations in recovery techniques can take this scrap and process it into usable raw material, effectively closing the loop on material consumption.
- Use of Reclaimed Zirconia: By sourcing reclaimed zirconia for new applications, not only is waste reduced but the lifecycle impact of zirconia is lessened as well.
As industries pivot to sustainable practices, the move toward recycling and recovery reflects a broader trend towards circular manufacturing, where waste is seen as a resource rather than a problem.
Future Directions in Zirconia Machining
Zirconia machining is at a critical juncture as industries increasingly seek materials that can enhance performance while being adaptable to new manufacturing techniques. The exploration of future directions offers insights into how the field can evolve, setting the stage for innovations that could redefine not just zirconia, but the foundations of machining as a whole. With changes in technology and market demands, it's important to consider both the potential benefits and the challenges businesses will need to address moving forward.
Innovations in Machining Technology
The advancements in machining technology promise to bring about significant improvements in the efficiency and effectiveness of zirconia processing. Notably, the integration of automation and artificial intelligence is making waves. For example, smart machines that utilize algorithms to predict tool wear and suggest maintenance schedules could drastically reduce downtime. This kind of proactive approach allows manufacturers to streamline their operations and mitigate unexpected failures, thus maintaining higher output levels.
Additionally, the rise of adaptive machining techniques is on the horizon. This method uses data feedback during the machining process, allowing for real-time adjustments. In practice, if a cutter begins to dull, the system can immediately adapt the cutting speed or feed rate to maintain the desired quality of the surface finish. Such innovations not only enhance precision but also save time and resources.
We are also seeing the development of new materials for cutting tools that could vastly improve their lifespan and performance when working with zirconia. For example, coatings like diamond or CBN (Cubic Boron Nitride) can withstand higher temperatures and resist wear better than traditional tools. This means fewer replacements and enhanced productivity over the long run.
"The quest for efficiency drives innovation in zirconia machining, pushing the boundaries of what's possible in manufacturing."
Potential New Applications
As innovations in technology unfold, so too do the potential applications of zirconia machining that transcend traditional boundaries. Industries are beginning to explore realms like aerospace, automotive, and even medical technology with increased fervor.
In aerospace, for instance, zirconia can be utilized in components that require both high strength and low weight. Its properties allow for stronger, lighter parts that can contribute significantly to fuel efficiency, leading to cost savings and reduced environmental impact.
In the field of medical devices, zirconia is exceptionally promising, especially in dental applications like crowns and bridges. However, ongoing research into its biocompatibility could lead to its use in more complex implants, potentially transforming how procedures are conducted. This opens the door not just for new product lines but also for groundbreaking medical treatments.
Moreover, the electronics sector is beginning to appreciate zirconia's potential for creating components that require high dielectric strength. As the push for smaller yet more efficient electronic devices continues, zirconia's unique attributes may position it as a prime candidate for various applications in consumer technology.
In summary, the future of zirconia machining is laden with prospects that could lead to remarkable strides across multiple industries. Innovation in technology paired with creative new applications will undoubtedly shape the landscape and redefine our understanding of what's feasible in manufacturing.
The End
The significance of concluding an examination of zirconia machining cannot be overstated. It represents not only a summation of the findings presented but also a crucial turning point for discerning its future directions and applications. A well-crafted conclusion in this context should highlight the key benefits and considerations regarding zirconia's unique properties and machining challenges, while also fervently expressing optimism for its potential growth in various sectors.
Summary of Insights
Through the exploration of zirconia machining, multiple insights rise to the surface. The material's impressive attributes—such as hardness, biocompatibility, and resistance to corrosion—make it invaluable across a range of industries. The discussion surrounding the challenges in machining, particularly concerning brittleness and the wear of tools, has illuminated areas where improvements can be made. Additionally, techniques like laser machining and 3D printing have demonstrated innovative ways to enhance efficiency and precision. Ultimately, the summarized insights strengthen the case for continued investment in research and development to optimize zirconia's machinability.
The Road Ahead for Zirconia Machining
Looking forward, the trajectory of zirconia machining appears hopeful. Innovations are on the horizon with advancements in technology, such as real-time monitoring systems and adaptive control methods, which can potentially streamline processes and improve outcomes. Moreover, as industries continue to seek eco-friendly alternatives, zirconia’s sustainability credentials put it in the spotlight. Future applications, particularly in aerospace and medical fields, may expand even further with the ongoing discoveries in material science and engineering techniques. In closing, the road ahead for zirconia machining is paved with potential, and the insights gleaned from this analysis are an essential part of navigating that path.