Wet Grain Mill: Functionality and Applications Explained
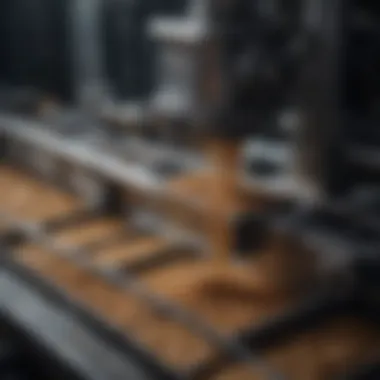
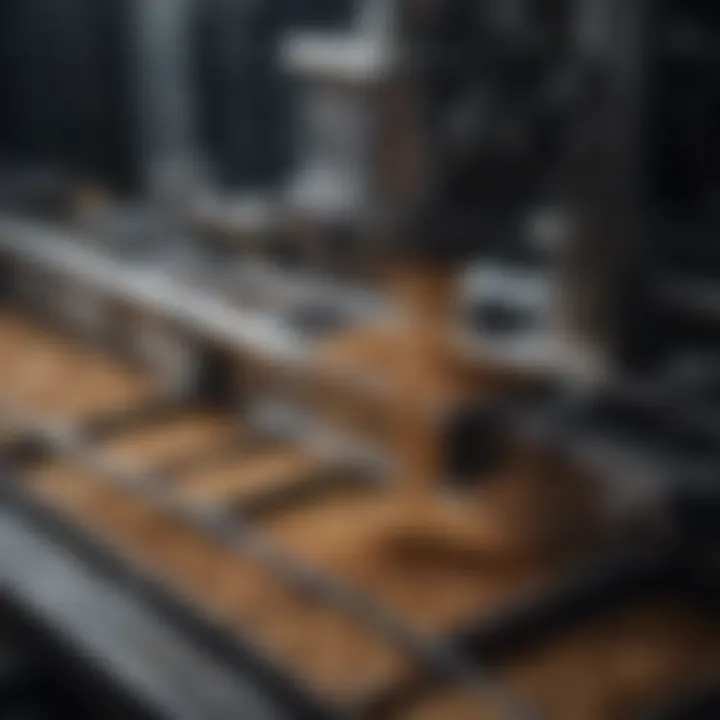
Intro
Wet grain milling is an essential process in agriculture and food production. This technique not only differentiates itself from dry milling but also provides unique benefits in terms of efficiency and product quality. Understanding the mechanics and applications of wet grain mills can be vital for students, researchers, educators, and professionals involved in food science and engineering.
Key Findings
Major Results
The research on wet grain mills reveals several important findings:
- Wet milling enhances the extraction efficiency of starches and proteins.
- The process reduces the energy requirements compared to dry milling.
- Wet grain mills produce products that have better texture and flavor.
- Specific types of grains, such as corn and rice, particularly benefit from this process.
These results indicate that wet milling is not just a method for grain processing, but a strategic approach that can significantly improve yield and quality.
Discussion of Findings
The efficiency of wet grain mills lies in their design. These mills utilize water to create a slurry, which helps to soften the grain. This allows for a more thorough and efficient extraction of components such as starch and oils. Furthermore, the moisture content in wet milling aids in reducing wear and tear on machinery, offering a more sustainable operational model.
"The advantages of wet milling are not limited to higher efficiency; they extend to improving the nutritional profile of the end products."
Wet grain milling is especially relevant in industries that demand high standards of ingredient quality. As demand for gluten-free and organic products increases, the role of wet mills could become even more prominent.
Methodology
Research Design
This study utilized a mixed-methods approach combining qualitative insights from industry practitioners and quantitative analysis of milling efficiencies.
Data Collection Methods
Data was collected through:
- Surveys from practitioners in the milling industry.
- Analysis of performance data from various wet grain mills.
- Review of relevant articles and papers on milling processes.
This comprehensive collection of data enabled a clearer understanding of the current state of wet milling technology and its applications in agriculture.
Prelims to Wet Grain Milling
Wet grain milling is a specialized processing technique critical in both agricultural practices and industrial operations. This method involves the crushing and grinding of grains in the presence of water or other liquids, leading to several distinct benefits compared to its dry milling counterpart.
The importance of wet grain milling lies in its ability to enhance the extraction of various components from the grain, such as starch, protein, and fiber. The inclusion of moisture during processing not only reduces the energy required for milling but also improves the overall yield of valuable end products. This factor is particularly crucial for sectors that depend on high-quality grain outputs, such as food and beverage industries.
Another significant consideration about wet grain milling is its role in influencing the texture and consistency of the final product. Foods produced through this process typically exhibit a smoother texture, which is particularly desirable in products like sauces, pastes, and certain alcoholic beverages.
"The efficiency of wet milling can significantly impact the cost and quality of grain-based products."
In addition, wet milling allows for enhanced flexibility in operational parameters, as the moisture level can be adjusted based on specific processing requirements. This adaptability is valuable for producers aiming to tailor their products to meet changing consumer preferences or market demands.
Furthermore, the operational setup for wet grain milling can be complex, involving several stages of processing that adjust the grain's physical and chemical properties. The comprehensive nature of this method warrants exploration, providing insights into its mechanics, applications, and potential innovations that can improve efficiencies in grain processing.
Through this examination, it becomes clear that understanding wet grain milling is integral for stakeholders in the agricultural and industrial sectors. The parallels drawn between performance outcomes and production quality reinforce the need for continuous research and development in this area.
The Mechanics of Wet Grain Mills
Understanding the mechanics of wet grain mills is essential for anyone involved in agricultural processing and food production. This section elucidates how these machines operate, outlining their key components, the operational processes involved, and the specific benefits they bring to milling operations.
Components of a Wet Grain Mill
Wet grain mills are composed of several critical components that work together to achieve efficient milling. These include:
- Feeding System: This is where raw grain enters the mill. It must ensure a consistent flow to maintain quality.
- Grinding Plates or Rollers: Typically made of high-quality materials, these are critical for crushing and grinding the grains. The design and spacing directly affect the end product.
- Water Management System: Since wet milling requires water, this system regulates the quantity and facilitates the mixing of water with the grain to achieve the desired consistency.
- Separation Mechanism: After grinding, there is a need for separating the milled product from the water. This can be accomplished using filters or centrifugation.
- Control Panel: It oversees the operation of the mill, allowing adjustments to speed, water input, or milling pressure based on the requirements of the processing phase.
The interplay of these components ensures that wet grain mills can handle different types of grains, producing a range of textures and flavors suited for various applications in food production.
Operational Process Overview
The operational process in wet grain milling combines mechanical and hydraulic actions to process the grain effectively. The key stages include:
- Preparation Phase: Grains are cleaned and soaked in water. This step is crucial as it enhances the milling process by reducing the hardness of the grains.
- Milling Phase: The soaked grains are fed into the mill where they are subjected to grinding. The design of the grinding components allows for precise control over particle size.
- Separation and Dehydration: Once milled, the product needs to be separated from water. This is often achieved through centrifugation or filtration, ensuring that excess moisture is removed.
- Packaging and Distribution: After the milling process is complete, the final product is packaged for transportation and sale.
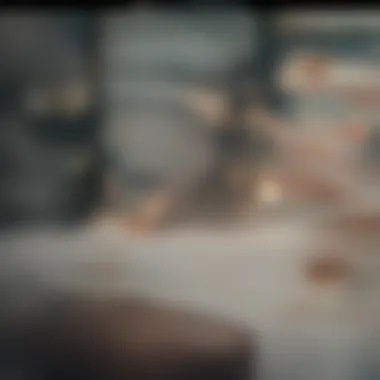
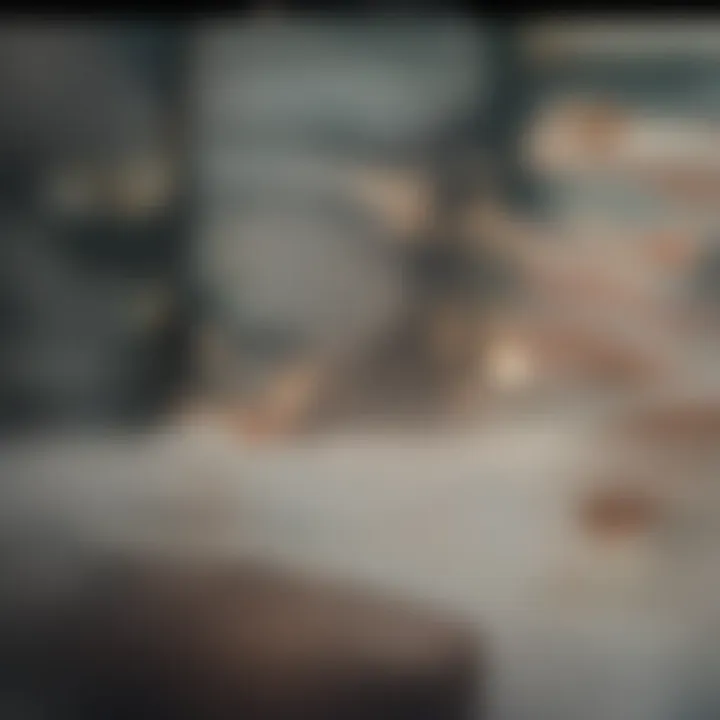
This systematic approach effectively converts raw grains into products suitable for consumer consumption and industrial use.
"Wet milling increases the extraction of starch and other essential components, potentially improving nutritional quality of food products."
Comparison with Dry Milling Techniques
Wet grain milling plays a crucial role in various industries, and understanding its distinction from dry milling techniques is essential. This comparison not only clarifies operational differences but also sheds light on the specific applications where each method excels. By examining the key differences and evaluating the advantages and disadvantages of both processes, stakeholders can make informed choices based on their needs.
Key Differences in Process
Wet milling and dry milling are fundamentally different in how they process grains. In wet milling, grains are soaked in water, which softens the structure and facilitates more efficient breakdown during milling. This hydration alters the physical and chemical properties of the grain, making it easier to extract starches and other valuable components.
In contrast, dry milling operates without moisture. Grains are ground into flour or meal without preliminary soaking. This method may maintain more of the original grain composition, but it could result in lower yields of extractable materials. Furthermore, in wet milling, the by-products like starch and protein are often isolated, providing additional commercial value, a benefit not typically seen in dry milling processes.
Advantages and Disadvantages of Each Method
Wet Milling
Advantages:
- Higher Yield: The soaking step often leads to greater extraction rates of starches, proteins and oils.
- Improved Quality: Products from wet milling often have superior texture and nutritional value, enhancing their appeal in food industries.
- Versatile Applications: Wet milling is essential for producing various products, including alcohol, starches, and syrups.
Disadvantages:
- Higher Operational Costs: Wet milling requires more water and energy, influencing overall costs.
- Complexity in Setup: The equipment and processes in wet milling are usually more intricate, requiring specialized knowledge.
Dry Milling
Advantages:
- Simplicity: Dry milling processes are generally easier to implement and operate, often requiring less specialized technology.
- Lower Water Usage: This method conserves water, making it more sustainable in water-scarce settings.
Disadvantages:
- Lower Yield: Dry milling often leads to less efficient recovery of raw materials, primarily due to grain losses during the process.
- Quality Limitations: The end products may lack the desired texture and flavors when compared to those produced via wet milling.
Each method has its unique strengths and weaknesses. Evaluating these aspects assists manufacturers and processors in selecting the most appropriate milling technique according to their goals and constraints.
Applications of Wet Grain Milling
Wet grain milling serves multiple essential functions in various industries, with pivotal applications particularly visible in food production and related sectors. Understanding these applications sheds light on the significance of wet grain mills. This method not only facilitates efficient processing but also enhances the quality of end products. As economies evolve, so does the demand for innovative solutions in grain processing, making this topic increasingly relevant.
Food Industry Uses
The food industry is one of the most prominent beneficiaries of wet grain milling. Different grains such as corn, rice, and wheat undergo this milling process to produce many staples. Wet milling processes allow for the extraction of valuable components such as proteins, oils, and starch. These components become crucial in producing various food products like corn syrup, tortillas, and beer.
- Wet milling aids in producing fine flours that have improved texture, thus enhancing the quality of bakery products.
- The process allows for better extraction of starches which are key in food thickening and binding agents.
- Wet milled grains can also be fermented more easily, making it a preferred choice in brewing and distillation processes.
Grab attention with the high-quality flour that results from wet milling. It supports not only bakeries and breweries but also snack companies producing items like tortillas and cereals.
Nutritional Outcomes of Wet Milling
Wet milling significantly influences the nutritional profile of grain-based products. When grains are milled wet, it allows for the retention and even concentration of essential nutrients. These include vitamins, minerals, and phytochemicals, which can sometimes be diminished in dry milling.
Key nutritional benefits include:
- Higher fiber content due to minimal processing of the bran layer.
- Enhanced availability of protein, which is crucial for diet.
- Better absorption of micronutrients, supporting overall health.
The milling process lends itself to producing whole grains that are richer in nutrients, making them a healthier option for consumers.
Impact on Grain Quality
The quality of grains after milling is a critical consideration for producers and consumers alike. Utilizing wet grain milling can improve several quality attributes in the final product. This includes:
- Grain consistency: The wet process allows for more uniform particle sizes.
- Texture: Products made from wet-milled grains exhibit smoother textures.
- Flavor: This process often enhances the natural flavors present in the grains.
The attention to grain quality can dictate consumer preferences and market success. Additionally, products produced through wet grain milling generally receive higher evaluations in sensory analyses compared to their dry-milled counterparts.
"The quality of the final product is paramount. Wet grain milling not only affects texture and flavor but also retains much more of the grain's nutritional value".
In summary, the applications of wet grain milling are diverse and impactful, highlighting the importance of this process in modern food production and processing industries.
Factors Influencing Efficiency in Wet Grain Milling
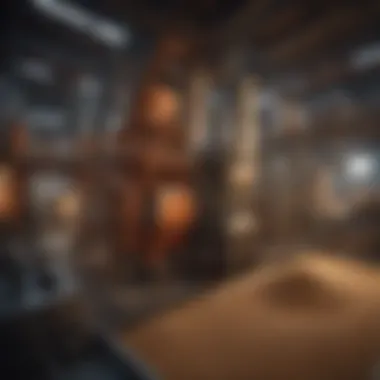
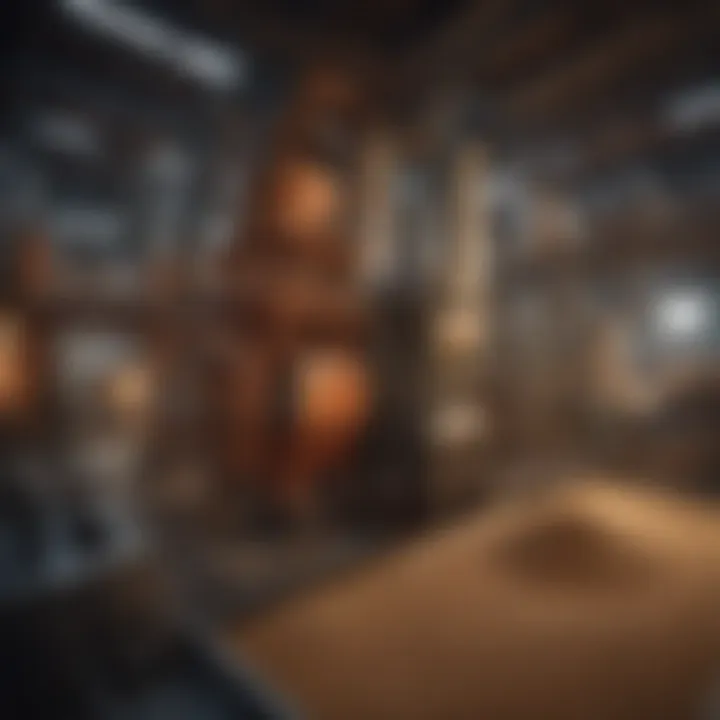
The efficiency of wet grain milling is crucial for optimizing processes in various industrial applications. Understanding the factors that impact this efficiency can lead to better performance, cost savings, and improved product quality. These factors can be broadly categorized into two main areas: moisture content of the grain and milling speed along with energy consumption. Both aspects are significant as they directly relate to how effectively a wet grain mill operates.
Moisture Content of Grain
Moisture content is one of the most critical factors influencing the efficiency of wet grain milling. The ideal moisture level varies depending on the type of grain and the specific milling process. Typically, the moisture content should range between 14-20%. If the moisture level is too high or too low, it can lead to several issues.
- High Moisture Content: Excessive moisture may cause clogging in the milling equipment. This results in increased wear on the mill components and can decrease overall throughput. The unground particles may form clusters, thereby affecting the quality of the final product.
- Low Moisture Content: Insufficient moisture can lead to inefficient milling. The lack of moisture can make the grain too brittle, resulting in excessive dust and fine particles rather than the desired coarse or product consistency. This can hinder the extraction of nutrients, particularly when the milling is related to food production.
Overall, optimal moisture management must be practiced to ensure maximum performance of wet grain mills. Consistency in moisture content can lead to more predictable milling outcomes, thereby enhancing the efficiency of the entire milling process.
Milling Speed and Energy Consumption
Milling speed plays a pivotal role in the efficiency of grinding operations. It is essential to carefully balance the speed with the type of grain being milled. Fast speeds can increase throughput but may not necessarily yield a better product. Conversely, slower speeds can ensure thorough milling but may sacrifice efficiency in terms of volume processed.
- Energy Consumption: The relationship between milling speed and energy consumption is critical. Higher speeds often lead to greater energy use. It is important to evaluate whether the increase in speed translates into better output quality and quantity. This necessitates careful monitoring of energy costs versus productivity gains.
- Impact on Product Quality: The quality of the milling process is not only determined by how fast the grains are ground but also by how uniform the resulting particles are. An imbalance in speed may lead to variations in particle size, which could affect subsequent processing steps, especially in food applications.
In summary, optimizing both moisture content and milling speed, accompanied by the consideration of energy consumption, is necessary for achieving efficient wet grain milling. Manufacturers and operators must continually assess these factors to enhance performance and reduce costs. By doing so, they can ensure that wet grain milling remains a viable option in various sectors, providing high-quality outputs while minimizing energy waste.
"Efficiency in wet grain milling is not about speed alone, but about harmonious balance of all influential factors."
The insights gained from understanding these operational parameters can significantly affect the economic viability of wet grain milling. As the industry evolves, ongoing research and adaptation to new technologies will continue to inform the best practices for maximizing efficiency.
Technological Advancements in Wet Grain Milling
Technological advancements in wet grain milling are reshaping the agricultural landscape. These innovations not only enhance processing efficiency but also ensure higher quality outputs. As the industry evolves, understanding these advances becomes critical for stakeholders aiming to optimize their milling processes.
Innovative Milling Techniques
Innovative milling techniques have emerged, driven by the need for more effective grain processing. One notable technique is the use of ultrasonic milling, which employs sound waves to improve particle size reduction. This method showcases how sound resonates through slurry to reduce energy consumption while achieving finer grinds.
Another advancement is high-pressure milling, which uses increased pressure to facilitate the breakdown of grains. This can enhance the extraction of starches, yielding a higher quality product for various applications in food production.
Furthermore, integrating traditional milling knowledge with modern engineering principles leads to hybrid milling systems. These systems optimize both wet and dry milling processes. Such techniques allow for flexibility in production, accommodating different grains and desired end products effectively.
Automation and Smart Technologies
Automation plays a pivotal role in transforming wet grain milling processes. With advancements in automation, grain mills can now operate with minimal human intervention. This reduces the likelihood of errors and increases throughput. For example, smart sensors can monitor moisture levels in real-time, automatically adjusting water addition during the milling process.
In addition to sensors, the incorporation of industrial Internet of Things (IoT) technologies allows mill operators to gather and analyze performance data comprehensively. This data-driven approach signals when maintenance is needed, thus preventing unscheduled downtimes and extending equipment life.
Moreover, the adoption of machine learning algorithms enables predictive analysis. These algorithms can optimize production schedules through a better understanding of market demand patterns. With this, mills can enhance their responsiveness to consumer needs while also managing inventory more effectively.
"As the boundaries of technology expand, so do the possibilities within the realm of wet grain milling. The blend of automation and innovation ensures that efficiency and quality remain at the forefront of production."
By embracing these technological advancements, wet grain milling operations can offer competitive edges in quality, efficiency, and adaptability in an ever-evolving market.
Economic Considerations
Understanding the economic implications of wet grain milling is essential in todayโs agricultural landscape. This section explores the financial aspects that impact farmers, millers, and the broader food industry. Evaluating costs associated with wet grain milling versus dry milling can greatly influence decisions on technology adoption and operational efficiency.
Cost-Benefit Analysis of Wet vs. Dry Milling
A thorough cost-benefit analysis serves as a crucial tool for stakeholders involved in grain processing. Wet milling typically involves higher initial setup costs and equipment expenses. However, it offers benefits like enhanced product quality and versatility in application. Specific elements to consider in this analysis include:
- Initial Investment: Wet mills often require higher capital investment compared to dry mills. This includes the cost of machinery designed for water integration, as well as maintenance expenses.
- Operational Costs: Energy consumption is usually higher in wet milling. The additional energy needed for water heating and processing can contribute significantly to ongoing expenses.
- Product Yield: Wet milling generally yields a higher amount of usable products. This increased yield can offset some of the higher operational costs and justifies the initial investment.
- Market Demand: Products derived from wet milling, such as starches and proteins, have distinct market advantages. Higher demand can lead to increased profitability for millers.
Market Trends and Consumer Demand
Market trends show an evolving landscape for grain processing methods. The demand for products resulting from wet milling processes is on the rise, driven by several factors:
- Health Trends: Consumers increasingly value health-focused food products. Wet milling can produce higher-quality nutritional components, thus attracting health-conscious buyers.
- Sustainability Concerns: Environmental awareness among consumers impacts purchasing choices. Wet milling can yield more efficient resource usage and waste reduction, aligning with sustainable practices.
- Innovation in Food Products: The food industry constantly seeks novel products. Wet milling opens avenues for creating diverse food products, from beverages to gluten-free options.
"As consumer preferences shift, understanding the market demand for wet-milled products can shape business strategies in the grain milling sector."
Market observation indicates that companies investing in wet milling technology are often better positioned to meet contemporary consumer demands. Monitoring industry trends helps millers adapt strategies to ensure they remain competitive in an evolving market.
Environmental Implications
Understanding the environmental implications of wet grain milling is crucial for industry stakeholders. This topic covers not only the ecological impact but also how wet milling processes can align with sustainability goals. As the world becomes increasingly aware of climate changes and resource depletion, optimizing milling practices presents an opportunity to reduce waste and improve efficiency.
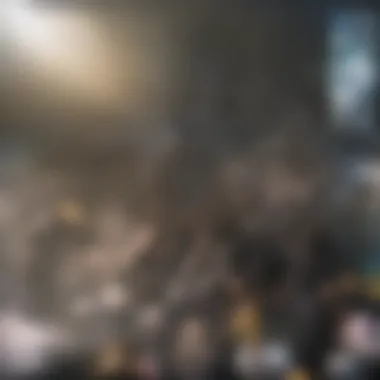
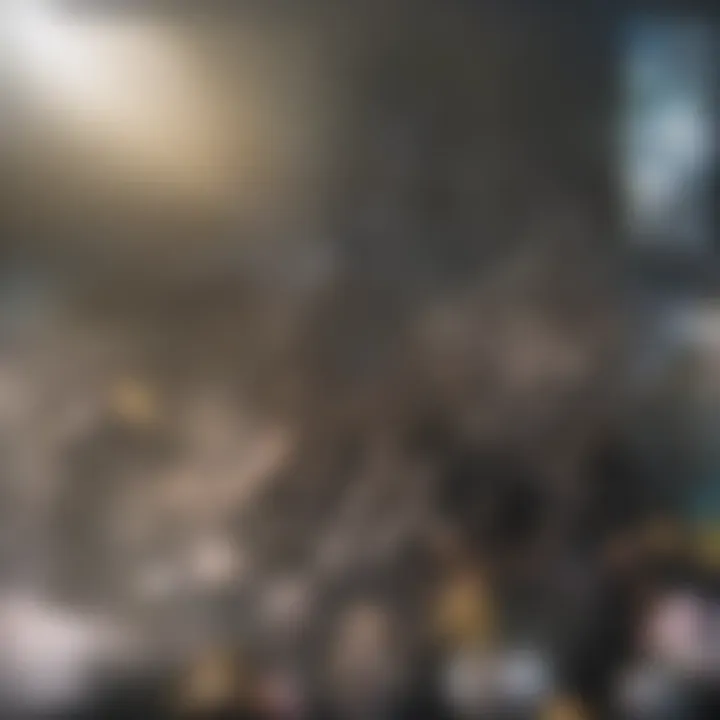
Sustainability Practices in Milling
Sustainability in wet grain milling involves a series of practices designed to minimize environmental footprints. This includes adopting energy-efficient technologies and processes. Measures such as using renewable energy sources for milling operations can significantly reduce greenhouse gas emissions. Additionally, the practice of sourcing grains locally reduces transportation emissions, making a positive impact.
Implementing water recirculation systems is another vital sustainability practice. These systems allow mills to reuse water within the process, thus conserving the water supply. Moreover, proper management of by-products, which often includes grain husks and germ, can enhance sustainability. Mills can explore options for converting these by-products into value-added products, such as animal feed or biofuel, thereby minimizing waste.
Waste Management and Resource Recovery
Waste management in wet grain milling plays a significant role in maintaining environmental integrity. Effective waste management strategies help to mitigate the negative impacts of milling activities. This includes not only the management of physical waste but also understanding how to effectively recover resources from the milling process.
Resource recovery can be achieved by repurposing waste by-products. For example, spent grains, which are produced in large quantities during milling, can serve as a protein source in animal feed or be used in brewing. This not only reduces disposal costs but also promotes a circular economy within the food and agriculture sector.
Furthermore, mills can benefit from implementing comprehensive waste audits. These audits help identify waste removal options that align with environmental regulations. Such proactive measures not only ensure compliance but also position the milling facility as a responsible and environmentally-conscious entity in the market.
"Sustainable practices in milling not only help the environment but can also improve the bottom line by reducing waste and optimizing resource use."
In summary, the environmental implications of wet grain milling reflect a balance between industrial needs and ecological responsibility. By adopting sustainability practices and enhancing waste management strategies, the industry can make strides towards a more responsible and efficient future.
Regulatory Landscape Affecting Wet Milling
In the realm of wet grain milling, understanding the regulatory landscape is crucial for manufacturers, operators, and consumers. Regulatory frameworks govern how milling processes operate, ensuring safety, quality, and sustainability of the products created. Compliance with these regulations is not only essential for maintaining a reputable business but also for achieving broader industry goals, such as consumer protection and environmental conservation.
The regulatory landscape is multifaceted, encompassing various aspects. Food safety regulations are implemented to prevent contamination and ensure that the end products are safe for consumption. Environmental regulations address the ecological impact of milling operations. Therefore, being aware of these standards is key for anyone involved in wet grain milling.
Food Safety Standards
Food safety standards play a prominent role in the wet milling process. These standards are designed to minimize risks associated with foodborne illnesses, which can arise from improper handling and processing of grains. For instance, various countries have established protocols, such as Hazard Analysis and Critical Control Point (HACCP), to identify critical points in production that could lead to contamination.
Specific guidelines often dictate the acceptable levels of moisture, temperature, and hygiene practices in wet milling facilities. Following these regulations protects consumers and enhances mills' operational reliability. Adhering to food safety standards can also engender trust among consumers. Therefore, companies that invest in compliance with food safety requirements can position themselves favorably in a competitive marketplace.
Environmental Regulations
Environmental regulations represent another critical component of the regulatory framework for wet grain milling. As sustainability becomes an increasingly important concern globally, milling operations must align with various environmental policies. These regulations focus on minimizing the ecological footprint of milling activities. They address aspects such as water usage, waste management, and energy consumption.
Wet grain milling can produce significant wastewater, which must be treated before being released into public systems. Additionally, proper waste management practices help reduce the environmental impact and promote resource recovery.
Companies are often required to comply with assessments that measure their environmental impact, often necessitating investments in sustainable technologies. By prioritizing these regulations, milling businesses can contribute to environmental sustainability while potentially reducing operational costs in the long run.
"Regulatory compliance is not just a legal obligation; it can be a strategic advantage that reinforces brand integrity and customer loyalty."
Future Directions in Wet Grain Milling Research
The research into wet grain milling continues to evolve, addressing both ongoing challenges and emerging opportunities within the agricultural sector. Understanding future directions is essential as it informs the development of improved techniques and tools, thereby enhancing efficiency and product quality across various applications.
Among the key elements of this area of study is the impact of technological advancements, which may revolutionize traditional methods. Future innovations could lead to enhancements in milling precision, energy consumption, and overall operational efficiency. As the industry increasingly leans towards sustainability, researchers are exploring ways to minimize waste and utilize by-products, aligning with modern environmental standards. Furthermore, there is growing interest in the nutritional profiles of products derived from wet grain milling and how these can be optimized through science and engineering processes.
Potential Areas for Innovation
Potential areas for innovation in wet grain milling can be categorized into various domains:
- Equipment Enhancements: The design of new milling machines with integrated smart technologies could improve user interaction and process monitoring.
- Sustainable Practices: Innovations centered around sustainability, such as water reuse systems or energy-efficient motors, could reduce the environmental footprint of milling operations.
- Advanced Materials: Research into durable, non-corrosive materials for the milling machinery could prolong the life and effectiveness of the equipment.
- Better Quality Control: The application of real-time monitoring technologies can enhance the control systems within milling processes, ensuring quality and consistency in the final products.
In contrast to traditional milling, these innovations not only aim to optimize the milling process but also target specific outcomes that align with market demand for higher quality and sustainability.
Importance of Interdisciplinary Research
The importance of interdisciplinary research in wet grain milling cannot be overstated. It brings together diverse fields including food science, engineering, and environmental studies to foster comprehensive solutions. Such collaborative efforts can lead to:
- Holistic Solutions: By merging principles from various disciplines, researchers can develop innovative approaches to problems that single disciplines might not address adequately.
- Enhanced Innovation: Interdisciplinary teams often generate more creative solutions, combining insights from biology, chemistry, engineering, and economics to address complex challenges.
- Practical Applications: Interdisciplinary research ensures that findings are applicable in real-world settings, promoting practicality and usability in the equipment and practices adopted by the industry.
- Broadened Perspectives: Engaging multiple disciplines helps broaden the understanding of the milling process, enabling practitioners to consider considerations from diverse angles, thereby improving decision-making processes.
"The crossroads of research are often where the most significant breakthroughs occur, particularly when diverse viewpoints and expertise combine."
Finale and Summary of Insights
In summarizing the impact and functionality of wet grain milling, it is clear that this process serves as a cornerstone in many agricultural and industrial applications. Wet grain milling not only enhances the quality of the final product but also delivers a variety of benefits that are crucial for both producers and consumers.
The mechanics of wet grain milling are intricately designed to achieve efficient particle reduction while maintaining the nutritional properties of the grain. This operational advantage positions wet milling favorably compared to dry milling techniques, particularly in applications requiring higher quality end products. Understanding these operational processes allows stakeholders to make informed decisions regarding their milling techniques based on specific goals.
The multitude of applications across different sectors, particularly in food production, highlights the importance of this milling method. From producing flour to beverages, the versatility of wet grain milling extends its relevance within food manufacturing, underscoring its necessity. Nutritional outcomes are another crucial consideration; wet milling often facilitates better retention of vital nutrients, contributing to healthier food products.
Moreover, the ongoing evolution of technology in wet grain milling signifies promise for future research and development. As new technologies emerge, they will likely lead to greater efficiency, sustainability, and product quality, aligning with environmental considerations. Those involved in agricultural practices should stay informed about these advancements to leverage them effectively.
From an economic perspective, understanding the cost-benefit dynamics between wet and dry milling is essential for businesses aiming to optimize their operations. Current market trends reflect heightened consumer demand for higher-quality food products produced through more innovative milling processes. Recognizing these trends enables producers to align their production methods with market expectations.
"Understanding the intricacies of wet grain milling is essential for ensuring quality and sustainability in food production."