Exploring the Varieties of Nickel Plating Techniques
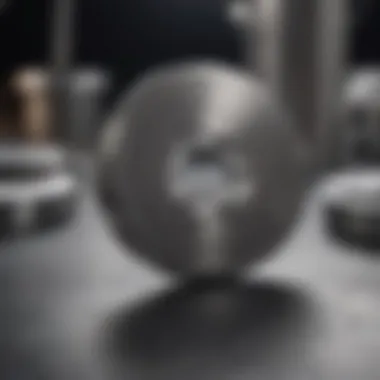
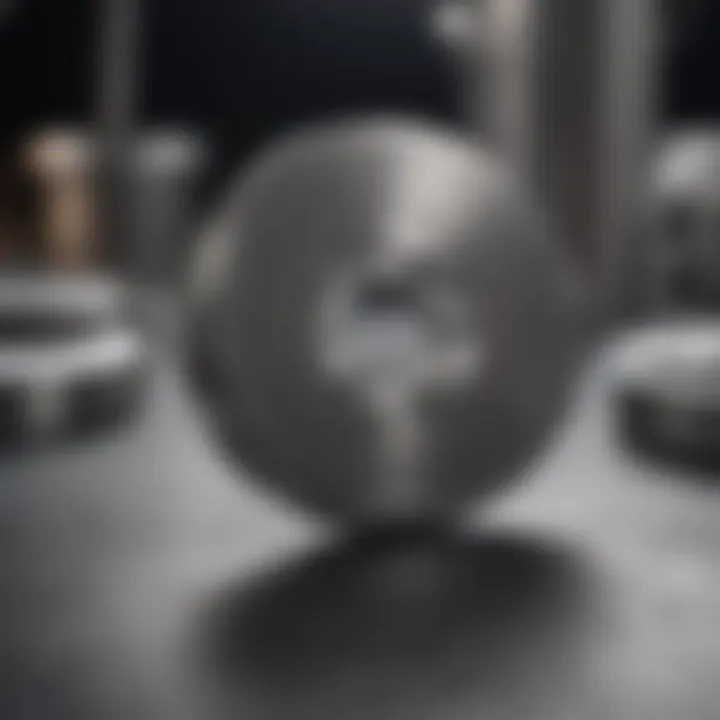
Intro
Nickel plating has become a critical procedure in various industries, providing substantial benefits for both functionality and aesthetics. The process not only enhances wear and corrosion resistance but also lends a decorative finish to products, making it popular in fields such as automotive, electronics, and aerospace. From the delicate intricacies involved in the application to the broader effects it holds within each sector, nickel plating deserves a thorough exploration.
Key Findings
Nickel plating can be categorized into several types, each serving different purposes and benefiting from unique properties. Some notable findings from recent studies and industry practices include:
- Electroless Nickel Plating: This method differs from traditional electroplating as it does not require an external electrical current. It is valued for its uniformity and ability to coat complex shapes.
- Electrolytic Nickel Plating: Commonly used in industries where thickness and adherence are paramount, this method uses an electric current to deposit nickel ions onto a surface, resulting in strong adhesion and hardness.
- Nickel-Palladium Plating: This advanced process combines nickel with palladium for enhanced corrosion resistance, making it ideal for high-end electronics.
"In the evolving landscape of surface treatment technologies, nickel plating stands out due its versatility and reliability."
Discussion of Findings
The examination of these various nickel plating types reveals not just their individual advantages but also their limitations. For instance, while electroless nickel plating ensures even coverage, it might not deliver the same electrical conductivity as electrolytic plating. Additionally, advancements in materials science often push the boundaries of these processes, leading to hybrid methods that enhance the physical and chemical properties of nickel coatings.
Methodology
A comprehensive analysis of nickel plating practices involves a multifaceted approach, combining literature reviews, case studies, and hands-on testing in laboratory settings. The aim is to craft an informed overview that caters to both industry professionals and academic researchers.
Research Design
The research employs a qualitative design, allowing for in-depth exploration of nickel plating techniques across various industries. Interviews from industry experts provide further insight into practical applications and emerging trends.
Data Collection Methods
Data is gathered through:
- Literature Review: Academic journals and technical papers, including resources from Wikipedia and Britannica.
- Surveys and Interviews: Feedback from professionals working with nickel plating, which helps identify common practices and challenges.
- Direct Observations: Engaging with plating operations gives real-world perspective.
By synthesizing these elements, the article aims to deliver an instructive and accessible narrative on nickel plating's multifaceted nature, providing readers with valuable insights and knowledge.
Intro to Nickel Plating
Nickel plating is a pivotal process in many industries, serving as a trusted method of enhancing the surface qualities of numerous materials. By applying a layer of nickel, products benefit from improved corrosion resistance, enhanced wear properties, and, in some instances, aesthetic appeal. These advantages make nickel plating not just a mere option, but in many cases, a necessity in manufacturing and craftsmanship. This section will take a closer look at what nickel plating entails, its historical journey, and why understanding this process is crucial for professionals and enthusiasts alike.
Definition of Nickel Plating
At its core, nickel plating is the deposition of a thin layer of nickel onto a substrate, which can be made of various metals or non-metals. This process can be performed through different methods, namely electrolytic techniques or electroless processes. The most commonly used method involves immersing the substrate in a nickel-rich solution where electric current facilitates the deposition. When done successfully, the result is a robust finish that can significantly prolong the lifespan of the underlying material. This finish may serve various purposes, such as protecting against rust, improving electrical conductivity, or creating an appealing appearance in consumer products.
Historical Context
Nickel plating has a history that goes back to the late 19th century, driven by industrial growth and the increasing need for durable materials. Some might say it was born out of necessity, as industries started looking for ways to improve their products in a rapidly changing marketplace. In 1805, the first metallic nickel was discovered, but it wasn’t until the industrial revolution that plating practices began to evolve.
During that time, the application of nickel plating began to gain traction, particularly in the automotive and aerospace sectors. Early applications primarily focused on improving aesthetic qualities and corrosion resistance of metal parts in cars and machinery. However, as technology advanced, so too did the methods and understanding of plating processes. The present day has witnessed remarkable innovations that allow for tailored nickel plating solutions, catering to specific industry needs. Understanding this evolution helps in appreciating not only the technical details but the larger relevance of nickel plating in sustaining industrial advancements.
The Science Behind Nickel Plating
Nickel plating is not merely a functional surface treatment; it intertwines the realms of chemistry and engineering. The deliciously complex dance between metal ions and the electric current results in coatings that are durable, corrosion-resistant, and attractive. This section aims to unpack the foundational components that make nickel plating a preferred choice among various industries. Therefore, understanding the science behind nickel plating is crucial, not just for those in the field, but also for anyone who wishes to grasp how such surfaces can enhance performance and extend the lifespan of different materials.
Electrolytic Process Overview
At the heart of nickel plating lies the electrolytic process. This technique involves submerging an object, often referred to as the substrate, in a solution rich in nickel salts, alongside an anode. When an electric current is passed through this solution, nickel ions are reduced at the cathode (the substrate’s surface) and deposited as a layer of metallic nickel.
The steps can be boiled down as follows:
- Preparation of the Substrate: Proper surface treatment is crucial. Cleaning, usually involving degreasing and sometimes etching, ensures that the surface will firmly hold onto the nickel layer.
- Electrolytic Bath Composition: The bath itself varies in composition depending on the desired outcome. A typical solution consists of nickel sulfate, nickel chloride, along with other additives that control the layer's texture and characteristics.
- Electric Current Application: The application of current requires precision. Too weak and the deposit won't form properly; too strong and you can end up with a poor finish.
- Post-Processing: Once the plating is done, usually rinsing and drying follow, often with further processes like passivating to improve corrosion resistance.
This electrochemical foundation lends all types of nickel plating their unique attributes, ensuring each application can be tailored to specific needs. The stability and strength of the created layer are the bedrock upon which industries rely in environments ranging from automotive to aerospace.
Chemical Composition
Understanding the chemical composition involved in nickel plating isn't just nerdy trivia. It's essential. Nickel plating solutions are not one-size-fits-all. Different additives can produce divers effects. For example:
- Nickel Sulfate: This is the primary source of nickel ions, contributing to the thickness and durability of the coating.
- Nickel Chloride: This helps in improving the uniformity of the deposit and enhances the conductivity of the bath.
- Brightening Agents: Such as sodium lauryl sulfate, these chemicals help impart a shiny finish to the plated surface.
- pH Buffering Agents: Maintaining the correct pH in the bath can significantly influence the quality of plating.
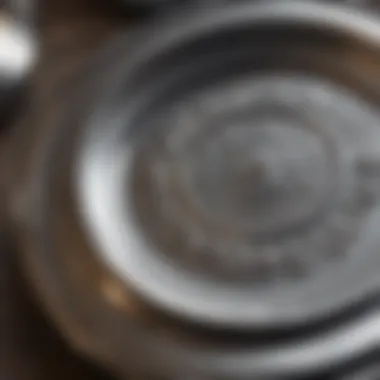
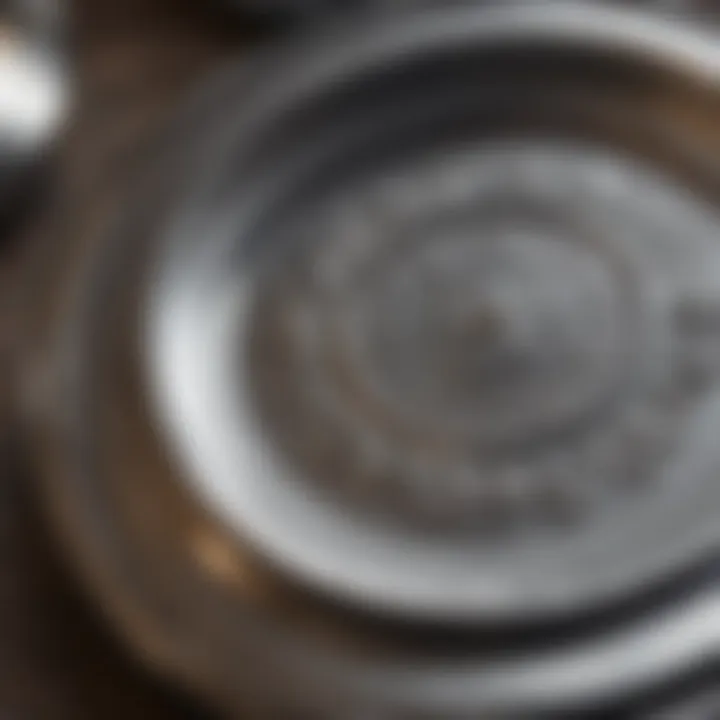
Understanding these components allows for focused adjustments. Changing one element might lead to a game-changing improvement in how the nickel layer adheres.
"The right mix makes all the difference; it’s like a chef knowing when to add that pinch of salt to elevate a dish to new heights."
In summary, both the electrolytic process and the composition of materials in nickel plating illustrate the intersection of science and practicality. This background enables industries to harness the full potential of nickel plating, leading to more robust products that endure the test of time and environmental challenges. Thus, anyone serious about nickel plating should delve deeper into these scientific principles.
Types of Nickel Plating
Nickel plating serves as a critical process in many industries due to its protective, decorative, and functional properties. Understanding the various types of nickel plating is essential for professionals and enthusiasts who aim to make informed decisions about surface treatments. This section dives into four main types: Electroless Nickel Plating, Electrolytic Nickel Plating, Hard Nickel Plating, and Bright Nickel Plating. Each type offers distinct benefits and considerations, which can significantly affect the choice depending on specific applications and performance requirements.
Electroless Nickel Plating
Process Description
Electroless nickel plating, often referred to as autocatalytic plating, is notable for its ability to produce a uniform coating without the need for an electric current. This process involves a chemical reaction in a bath that consists of nickel salts, reducing agents, and stabilizers. With this method, a higher degree of control over the thickness and consistency of coatings makes it particularly attractive for intricate shapes and components.
The key characteristic of electroless nickel plating is its ability to cover complex geometries evenly. This means that even when dealing with deeply recessed areas, the nickel can coat evenly, providing excellent corrosion resistance.
Uniformity and consistency are paramount in applications where precision matters.
However, the costs associated with the chemicals and potential disposal issues can not be overlooked.
Applications
The applications for electroless nickel plating are widespread, spanning automotive components, electronics, and valve manufacturing. It is frequently used in situations requiring corrosion resistance coupled with a lower wear rate, such as in hydraulic systems and marine environments.
A key characteristic of this process is its versatility; it can be applied to metals, plastics, and even ceramics. Since the coating is non-porous and dense, it is often the go-to choice when dealing with high-stress applications.
Advantages and Disadvantages
Electroless nickel plating presents several advantages, like excellent corrosion resistance and even coating thickness. However, it can be more costly than other methods, primarily due to the intricate control needed in the chemical process.
A unique feature of this process is its lack of need for rectifiers or complex equipment, which can sometimes simplify overall operational costs despite the chemical expenditure. Its drawbacks also include susceptibility to wear in high-friction environments, making careful selection critical.
Electrolytic Nickel Plating
Process Description
Electrolytic nickel plating utilizes an electric current to deposit nickel onto a substrate. The process involves immersing the base material in a nickel salt solution and applying a direct current, resulting in the deposition of nickel ions onto the surface. One of its key advantages is the feasibility of thick plating, which can be fine-tuned to various thickness requirements.
This method’s distinct feature is that it leads to higher penetration into the substrate, leading to better adhesion. It’s often favored for parts that need enhanced durability.
Applications
Electrolytic nickel plating is particularly popular in the automotive and aerospace industries due to its exceptional hardness and corrosion resistance. It’s also widely used in manufacturing tools and molds that undergo extreme wear.
The characteristic of this type is the ability to create a thicker coating compared to its electroless counterpart. It is a beneficial choice for components in harsh environments; however, the uniformity of the coating can vary depending on the shape of the parts being plated.
Advantages and Disadvantages
The main advantages of electrolytic nickel plating include better control over layer thickness and an ability to provide a functional finish for high-wear components. However, some disadvantages are the potential for uneven coating on complex geometries and the need for elaborate setups for large-scale operations.
Electrolytic nickel plating offers high productivity but can require more oversight and maintenance to ensure quality results.
Hard Nickel Plating
Characteristics
Hard nickel plating is distinguished by its unique ability to produce a tough, durable coating. Unlike other types, it utilizes a particular formulation that results in a denser and harder deposit. This characteristic is particularly valuable in applications where abrasion and corrosion resistance are paramount.
The high hardness of these coatings can provide significant wear resistance, making it a favored choice for operational components. However, there are specific limitations regarding ductility if high hardness is pursued too aggressively.
Typical Uses
Industries such as mining, oil and gas, and manufacturing increasingly rely on hard nickel plating. Its typical applications include gears, hydraulic cylinders, and various tooling. The wear resistance it provides extends the lifespan of tools and machinery while enhancing operational efficiency.
A great advantage of hard nickel plating is its effectiveness in reducing the coefficient of friction in certain applications, thereby improving overall performance.
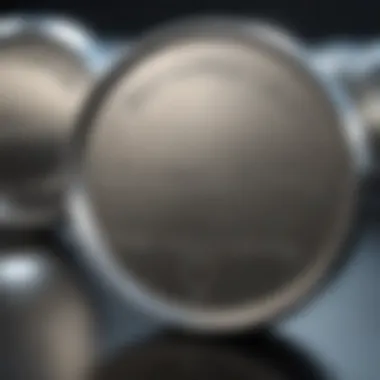
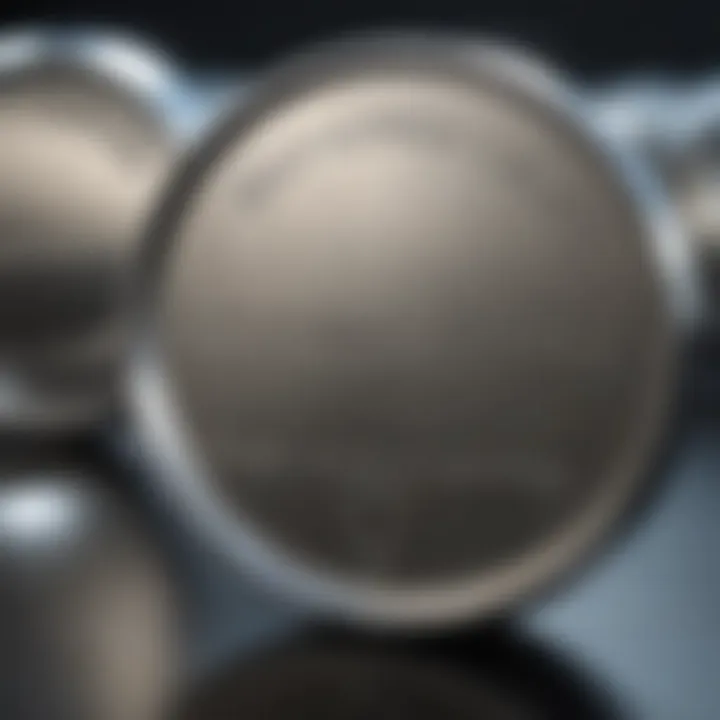
Pros and Cons
When it comes to the pros, hard nickel plating’s toughness is unparalleled, providing durability under extreme conditions. However, the cons include challenges with coatings, such as the risk of cracking in delicate applications due to inherent brittleness at high thicknesses.
Ultimately, the balance between hardness and flexibility must be carefully navigated to achieve satisfactory results.
Bright Nickel Plating
Process Description
Bright nickel plating creates a visually appealing finish while providing a protective layer. This process often involves a dual-layer system, starting with a matte finish followed by an electroplated bright nickel layer. The bright finish particularly caters to aesthetic needs while retaining the substrate's integrity.
The key characteristic of this method is its ability to produce a shiny, reflective surface that enhances product appearance. Its application extends beyond purely decorative when combined with functional elements like corrosion resistance.
Applications
Bright nickel plating finds its way into consumer products like jewelry, light fixtures, and decorative hardware, where appearance is crucial. Additionally, its protective properties make it suitable for automotive parts and other components exposed to the elements.
This type’s unique feature lies in the balance of appearance and function. While it presents a visually striking finish, it also enhances wear and corrosion resistance.
Advantages and Disadvantages
The advantages of bright nickel plating include its attractive finish, increased corrosion resistance, and the ability to make parts more aesthetically pleasing to consumers. However, potential downsides involve a tendency to form a less dense coating compared to hard plating, making it less ideal for high-wear applications.
One must weigh the importance of appearance against performance to ensure the chosen finish meets the requirements of the specific application.
Applications of Nickel Plating
Nickel plating serves as an integral part in various sectors, providing benefits that extend beyond mere aesthetics. This surface treatment is not just a shiny layer added for looks; it plays a vital role in enhancing material properties, extending the life of products, and improving performance in multiple applications. Nickel plating offers superior corrosion resistance, hardness, and wear resistance, making it a popular choice in both industrial and consumer products. Understanding these applications not only highlights the versatility of nickel plating but also underscores its significance in everyday items and high-tech machinery alike.
Industrial Uses
Automotive Industry
In the automotive world, nickel plating is paramount. It’s commonly applied to parts such as engine components, gears, and cylinder heads. The key characteristic of nickel plating in this sector is its ability to prevent corrosion, which is vital in keeping vehicles safe and operational under various weather conditions. The unique feature lies in the combination of both decorative and functional properties – it provides visual appeal while prolonging durability.
With the advantage of reducing friction, nickel-plated surfaces can enhance engine performance and fuel efficiency. Yet reliance on this process comes with a consideration; if not applied correctly, the finish can fail, leading to corrosion.
Aerospace Applications
The aerospace industry demands materials that meet stringent standards for performance and safety. Nickel plating is favored here primarily because of its high strength and excellent electrical conductivity. It’s often used on components like landing gear, fuel systems, and other critical parts where a failure could have catastrophic results.
Another key characteristic is its ability to withstand extreme temperatures and pressures, making it a trustworthy option in aviation. However, the unique feature of aerospace applications is their rigorous testing and certification processes. Disadvantages primarily come from the costs associated with these high standards and the specific equipment needed for plating.
Electronics Sector
In electronics, nickel plating serves a distinctive role, especially in connectors and circuit boards. Here, the process not only provides a surface that is resistant to corrosion but also increases solderability. The key attribute is the conductive property of nickel, which aids in reliable electrical connections.
The unique feature here involves performance under various environmental conditions – from humidity to temperature changes. Nonetheless, while its advantages are clear, one of the disadvantages is that the nickel itself can sometimes create galvanic corrosion if paired with certain metals, which requires careful consideration during component selection.
Consumer Products
Appliances
When it comes to household appliances, nickel plating brings a blend of functionality and style. Commonly found in kitchen gadgets and fixtures, nickel-plated appliances showcasing a shiny surface not only look good but are protected from wear and tarnishing. This is particularly beneficial in environments where items are frequently used or cleaned.
The addition of nickel improves surface durability and can make cleaning easier. Yet, consumers should be aware of potential downsides; excessive exposure to stronger cleaning chemicals can wear down even nickel finishes, so care instructions are a must.
Jewelry
Nickel plays a significant role in the jewelry sector, often used to enhance the quality of base metals or to create hypoallergenic options. The process allows for a shiny, attractive finish that is both affordable and durable. The characteristic shine of nickel-plated jewelry often appeals to those looking for something that looks expensive without breaking the bank.
A unique feature of nickel in this context is its possibility to cause allergic reactions in some individuals. Therefore, while beneficial for its aesthetics and cost, it also raises significate health considerations for sensitive individuals.
Home Fixtures
When it comes to home fixtures like faucets, doorknobs, or lighting, nickel plating offers a practical solution that merges style and substance. Its corrosion resistance is a valuable characteristic in damp environments, and its reflective quality enhances the aesthetics of any space.

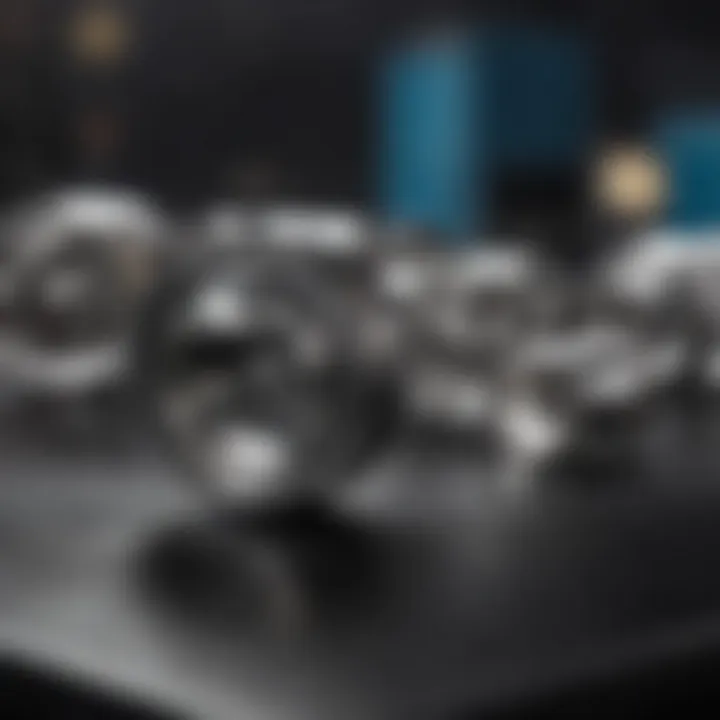
The unique selling point here is the longevity and easy maintenance that nickel plating provides, saving homeowners time and money in the long run. However, potential drawbacks include the challenge of matching finishes with other metals, leading to compatibility issues in design layouts.
"Nickel plating is not just about looks; it’s about increasing functionality and lifespan across various sectors."
Environmental Considerations in Nickel Plating
Nickel plating is a widely used process that offers various benefits, yet it also raises specific environmental concerns. Understanding these aspects is crucial for any industry relying on this technique. By paying attention to environmental practices, we can not only ensure compliance with regulations but also contribute to a more sustainable future.
Waste Management
Waste management in nickel plating is a pressing issue due to the chemicals involved. Proper disposal of waste materials is essential to minimize the environmental impact. Nickel, cadmium, and other hazardous substances released during the plating process necessitate careful handling.
One strategy companies can implement is to recycle the waste by using advanced filtration systems. These systems can significantly reduce the pollutants that go into landfills or waterways. On a larger scale, adhering to regulations set by institutions, like the Environmental Protection Agency (EPA), ensures facilities manage their waste adequately. Here are several waste management strategies worth considering:
- Closed-loop recycling systems: These systems allow for the recovery of valuable metals to be reused in the plating process.
- Chemical treatment methods: Applying chemical treatments to convert hazardous waste into non-toxic substrates can be effective.
- Waste minimization programs: Regular reviews of processes can uncover opportunities to reduce waste generation.
Efficient waste management serves a dual purpose: enhancing sustainability and reducing costs associated with waste disposal. Keeping the environment in good shape should be a top priority for every nickel plating operator.
Health and Safety Regulations
Health and safety regulations play an indispensable role in nickel plating operations. The use of nickel and other associated chemicals poses risks not just to the environment but also to the health of workers. Proper guidelines, established at both national and international levels, should be strictly followed for the safety of all personnel involved in the plating processes.
The key regulations typically encompass:
- Personal protective equipment (PPE): Workers should be equipped with gloves, goggles, and masks to reduce exposure to harmful substances
- Ventilation systems: Adequate airflow in plating areas is essential to prevent inhalation of toxic fumes.
- Regular training programs: Workers must understand risks and protocols related to handling chemicals in nickel plating.
"Ensuring the health and safety of workers not only complies with laws but also fosters a productive work environment."
Failure to comply with these regulations not only risks the health of individuals but can also lead to severe legal repercussions. Companies that prioritize the health and safety of their workforce tend to foster a culture of responsibility, resulting in lower accident rates and improved overall efficiency.
Future Trends in Nickel Plating
The landscape of nickel plating is ever-evolving. Keeping abreast of the future trends is essential for industry professionals and enthusiasts alike. These trends are not merely passing fads; they signify a transformative wave of innovations that influence efficiency, sustainability, and performance in nickel plating processes.
Innovative Technologies
Innovative technologies are reshaping how nickel plating is perceived and implemented. One noteworthy advancement is the development of high-throughput electroplating systems. These systems increase production speed without compromising quality, making it viable for mass production in industries such as automotive and aerospace.
Another significant innovation is the integration of automation and IoT (Internet of Things). With smart plating, operators can monitor plating parameters in real-time, leading to precise control over the plating process. This not only enhances consistency but also minimizes waste, as adjustments can be made instantly rather than after the fact.
"The integration of IoT technologies transforms the traditional plating shop into a smart factory, setting new industry standards for efficiency and quality."
Additionally, nanotechnology is making strides within the realm of nickel plating. By manipulating materials on a molecular level, manufacturers can create superior coatings with improved properties, such as increased corrosion resistance and reduced friction. This could lead to new applications in a variety of fields, pushing the boundaries of what nickel plating can achieve.
Sustainability Initiatives
The push for greater sustainability is another pivotal future trend in nickel plating. Environmental concerns are at the forefront of many industries today, and nickel plating is no exception. Manufacturers are adopting sustainable practices to minimize environmental impacts associated with traditional plating methods.
- Closed-loop systems are gaining traction. These systems recycle the plating solutions, essentially allowing them to be used multiple times, thus reducing waste.
- The shift towards green chemistry is also notable. Companies are exploring alternatives to harsh chemicals traditionally used in plating processes, leading to less toxic waste and safer working environments.
Moreover, sustainability extends to the sourcing of raw materials. There’s a notable trend toward using recycled nickel, which not only conserves resources but also significantly lowers the carbon footprint associated with mining virgin materials.
As the industry continues to adapt, it remains clear that the incorporation of innovative technologies coupled with sustainable practices can vastly improve both the efficacy and the environmental profile of nickel plating. Staying tuned to these trends will enable professionals to navigate the complexities of the future landscape of nickel plating, ensuring they remain competitive in an ever-changing market.
Closure
In wrapping up the discussion on nickel plating, it's clear that this surface treatment process plays a crucial role across a variety of industries. Not only does it offer a way to enhance the durability of metal parts, but it also significantly improves aesthetic appeal. The examination of the various techniques—be it electroless, electrolytic, hard, or bright nickel plating—reveals distinct properties that cater to different needs.
Summarizing Key Points
Throughout this article, several key aspects of nickel plating have been highlighted:
- Types of Nickel Plating: We explored various plating techniques, emphasizing their unique properties, processes, and applications. Each type serves a specific purpose based on physical and chemical properties.
- Environmental Considerations: Important discussions around waste management and safety regulations remind us that nickel plating, while beneficial, must be managed responsibly. The balance between industrial productivity and environmental health cannot be overstated.
- Future Trends: The section on innovative technologies pointed to emerging techniques and sustainability initiatives that aim to reduce waste and improve efficiency. Progress in these areas is essential for the ongoing relevance of nickel plating in modern manufacturing.
Despite the challenges that the industry faces, the future of nickel plating looks promising. The integration of cutting-edge technologies and a focus on sustainable practices are paving the way for more efficient methods and better outcomes.
Looking Ahead
Considering the rapid advancements in technology and increasing awareness of environmental impact, the direction of nickel plating is set for transformation. Key points to ponder include:
- Technological Advancements: With the rise of nanotechnology and advanced materials science, expect the emergence of more resilient and efficient nickel plating processes. Innovations could lead to faster application methods and reduced costs, making it accessible for smaller businesses.
- Sustainable Practices: The push for sustainability in manufacturing will likely shape the future of nickel plating. Companies will need to seek alternatives that minimize waste and energy consumption. Potential developments in eco-friendly plating solutions could complement traditional methods, leading to broader acceptance and implementation.
Ultimately, staying tuned into these trends can offer stakeholders invaluable insights, shaping strategies that align with the evolving needs of the market and the environment. As industries refine their approaches towards nickel plating, professionals in the field must adapt and innovate, ensuring their practices not only meet today’s demands but are also aligned with the vision for a sustainable tomorrow.