Understanding Vibration Absorbers: Insights and Uses
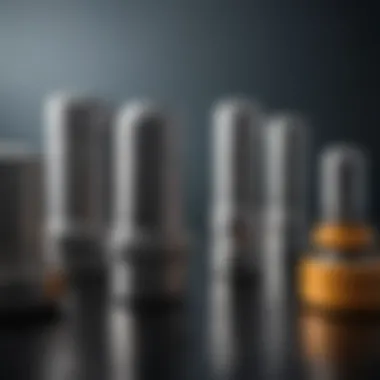
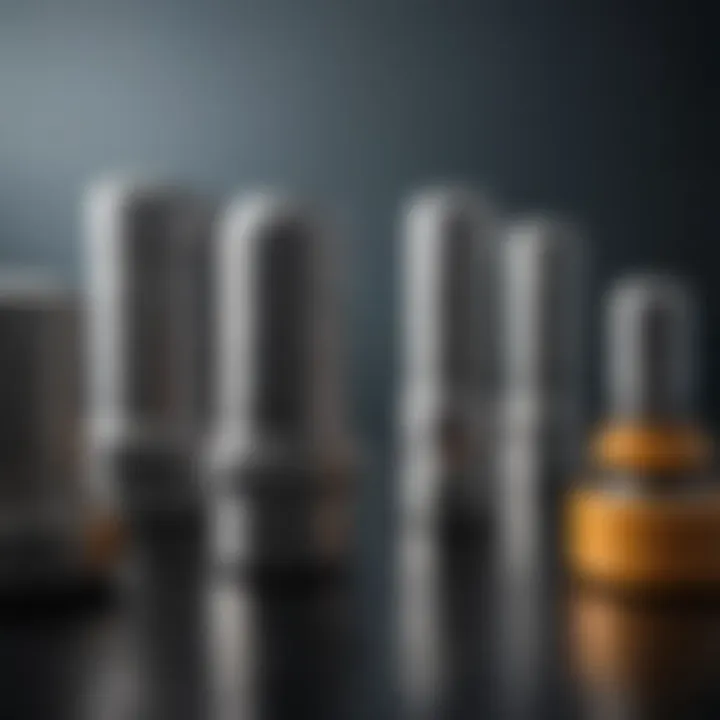
Intro
Vibrations, whether originating from machinery, vehicles, or even natural phenomena like earthquakes, can wreak havoc in various settings. They disrupt workflows, compromise structural integrity, and can even endanger safety. That's where vibration absorbers come into the picture. These ingenious devices are not just fancy gadgets; they play a crucial role in ensuring smooth operations across different industries. Understanding their functionality and applications is essential for students, researchers, and professionals aiming to tackle the challenges posed by unwanted vibrations.
Key Findings
In the realm of vibration management, several pivotal aspects emerge that provide a clearer understanding of how vibration absorbers operate and their significance across various fields. This section outlines the main findings to emphasize the effectiveness and application scope of these systems.
- Functionality of Vibration Absorbers: At their core, vibration absorbers are designed to target and reduce specific vibration frequencies. By using mechanical properties or passive elements, they dissipate energy, thus minimizing unwanted oscillations.
- Types of Absorbers: Various types of vibration absorbers exist. To name a few, there are tuned mass dampers, viscous dampers, and elastomeric isolators. Each type is suited for different applications, depending on the nature of vibrations to be mitigated.
- Applications Across Industries: Vibration absorbers find use in a myriad of industries—from aerospace, where they protect sensitive instruments, to automotive, where they enhance passenger comfort. Their adaptability marks their importance in practical settings.
"Vibration absorbers act like superheroes against the chaos of oscillations, each with its own unique powers to tackle specific challenges."
Discussion of Findings
The exploration of vibration absorbers reveals a rich tapestry of technology and design, reflecting how far we've come in the quest for vibration control. Diving deeper into specific applications underscores their effectiveness in real-world scenarios. For instance, in a skyscraper, a tuned mass damper counteracts sway caused by wind, maintaining comfort and safety for its occupants.
In manufacturing, heavy machinery often creates vibrations that can lead to premature wear and tear. Here, implementing vibration absorbers not only extends equipment life but also improves energy efficiency.
The ongoing research into advanced materials, such as smart polymers, suggests even greater potential for future applications. These innovative approaches enhance both absorption capability and responsiveness to varying vibration conditions.
The End
As we navigate through the fundamental aspects of vibration absorbers, it becomes clear that their role in mitigating vibrations cannot be overstated. They are not merely components but integral solutions to helping both industry and academia address common yet complex challenges. Understanding them enables us to appreciate the engineering behind safety and efficiency in various fields.
In high-speed trains, vibration absorbers ensure a smooth journey, while in the seismic design of buildings, they protect lives. Through thoughtful design and innovation, vibration control technologies continue to evolve, responding to the needs of an ever-changing world.
Preamble to Vibration Absorbers
The notion of vibration absorbers occupies a crucial niche within the larger framework of engineering and material sciences. As industries constantly grapple with the challenges presented by unwanted vibrations, understanding the role and functionality of these devices becomes increasingly paramount. Imagine a precision machine, finely tuned for performance—unwelcome vibrations can disrupt its operation, leading to decreased efficiency and potential failure.
Definition of Vibration Absorbers
Vibration absorbers are specialized devices or systems designed to mitigate the impact of unwanted vibrations in various settings. These can be found in an array of applications, ranging from heavy industrial machinery to delicate electronic gadgets. The primary goal of a vibration absorber is straightforward: to either reduce the amplitude of vibrations or shift the system’s resonance frequency away from that of the vibrating source. They come in different types, each suited to specific scenarios, whether it be a rubber mount in an engine or an advanced active system in an aerospace application. Essentially, they help maintain performance and prolong the lifespan of both machinery and structures by absorbing excess energy that would otherwise lead to degradation.
Historical Context and Development
The evolution of vibration absorbers traces back to the early days of mechanical engineering. Before the advent of modern techniques, craftsmen relied on basic principles of balance and mass distribution to minimize vibration effects. However, as technology advanced, the need for more sophisticated solutions became apparent.
In the mid-20th century, innovations began to emerge significantly. Engineers started to utilize materials with specific damping properties, like viscoelastic materials, which perform admirably under stress. The development of active vibration absorption systems, particularly in aerospace fields, showcased a significant leap forward. These systems employ sensors, actuators, and control algorithms to adapt to changing vibration conditions in real time, a feat that traditional passive systems simply could not accomplish.
Today, industries are more aware than ever about the detrimental effects of vibrations. Modern construction techniques and maintenance protocols often include vibration absorption as a fundamental component. From high-rise buildings swaying in the wind to quiet, reliable operation of consumer electronics, the advancements in this field continue to refine our ability to manage vibrations effectively.
Underlying Principles of Vibration Absorption
Understanding the underlying principles of vibration absorption is crucial as it lays the groundwork for effectively mitigating unwanted vibrations. At its core, vibration absorption involves the transfer of kinetic energy away from sensitive components or structures, thereby enhancing their performance and longevity. By grasping these principles, one can make informed decisions regarding the design and application of vibration absorbers in various fields.
Basic Mechanics of Vibration Transmission
To comprehend how vibration absorbers work, it is important to first explore the mechanics behind vibration transmission. Vibration occurs when an object oscillates, creating waves of energy that propagate through it or its surroundings. Various materials transmit vibrations differently, influenced by their density, elasticity, and structure.
In general, vibrations can be described as mechanical disturbances that travel through a medium—like air, metal, or rubber. Each medium has its own behavior: a rigid material like steel may transmit vibrations quickly and with high fidelity, while softer materials, such as rubber or foam, may dampen and absorb some of the energy instead. This is where the choice of material becomes essential in designing a vibration absorber.
When a machine operates, it tends to generate vibrations due to moving parts, imbalances, or external forces. If not addressed, these vibrations can lead to fatigue, wear, or even catastrophic failures. Understanding the transmission paths of vibrations through different structures allows engineers to position vibration absorbers effectively, steering the energy away from critical components.
"The key to effective vibration control lies in the meticulous selection of materials and the strategic placement of absorbers."
Resonance and Damping Effects
Resonance is a phenomenon that occurs when the frequency of external vibrations aligns with the natural frequency of a system. In such cases, even small oscillations can lead to excessive vibrations, often resulting in structural failure or machine malfunction. This is particularly relevant in the design of vibration absorbers; if a device can be tuned to operate at a specific frequency, it can counteract the resonant frequencies generated by machinery.
Damping effects play a crucial role in managing vibrations. Damping refers to the energy dissipation process, where some of the vibrational energy is converted into thermal energy, effectively reducing the amplitude of oscillations. Different damping materials offer varying degrees of energy absorption. For instance, viscoelastic materials can provide substantial damping through their ability to deform under stress and then return to their original shape.
Key Considerations for Damping:
- Material Selection: The choice between materials like rubber, foam, or metals can drastically affect the damping performance.
- Environmental Factors: Temperature and humidity can influence material behavior; thus engineers must account for these variables during design.
- Application Requirements: The specific needs of the equipment or structure determine whether passive, active, or semi-active vibration absorbers are employed for optimal damping performance.
In summary, grasping the basic mechanics of vibration transmission along with the dynamics of resonance and damping will inform better design and application of vibration absorbers in real-world scenarios. This knowledge ultimately leads to improved safety, efficiency, and longevity of machinery and structures.
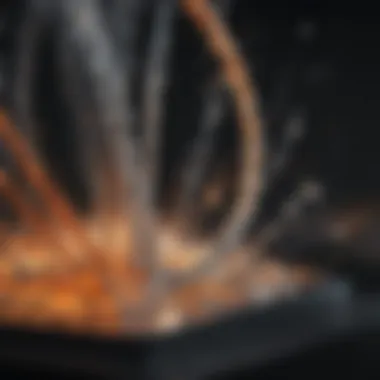
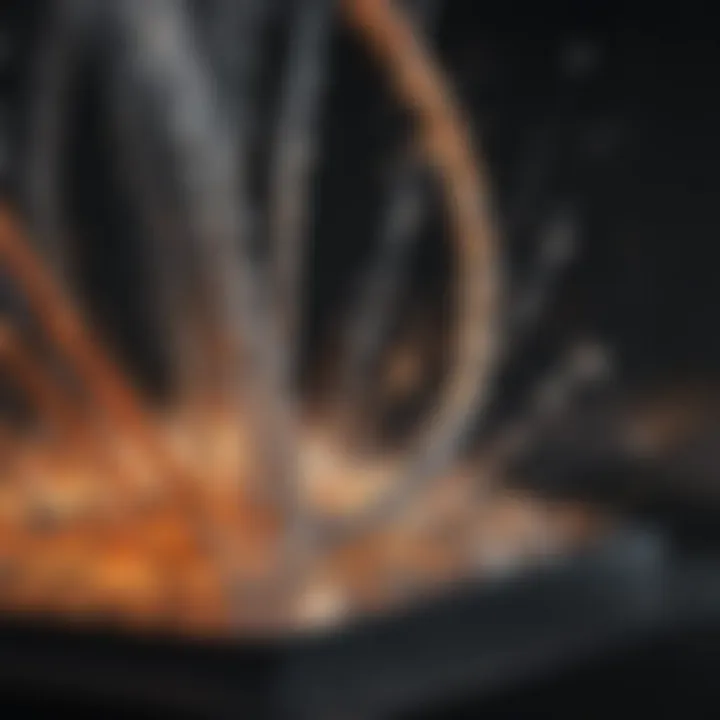
Types of Vibration Absorbers
Understanding the different types of vibration absorbers is crucial in grasping their functionality and applications across various sectors. Each type carries its own set of advantages, mechanisms, and specific use cases, tailoring vibration management techniques to various needs. Whether it’s passive, active, or semi-active solutions, the choice of vibration absorber can significantly impact performance, longevity, and cost-efficiency.
Passive Vibration Absorbers
Passive vibration absorbers work on the principle of resonance, exploiting natural frequencies to counteract unwanted vibrations. These devices do not require external power, making them robust and reliable under most conditions. Typical examples include tuned mass dampers and viscoelastic materials. A tuned mass damper can be found on skyscrapers, like the Taipei 101, where it absorbs sway caused by winds or earthquakes. They are elegant in their simplicity, with the main consideration being that they must be properly tuned to the system they serve.
The benefits of passive absorbers are significant:
- Simplicity: Less likelihood of mechanical failure.
- Cost-effectiveness: No additional energy sources required.
- Maintenance-free: Generally low upkeep once installed.
In design, careful attention must be paid to factors such as the mass, stiffness, and damping ratio to optimize performance. If not appropriately designed, these products may introduce additional vibrations instead of mitigating them.
Active Vibration Absorbers
On the flip side, active vibration absorbers utilize sensors and actuators to respond to dynamic conditions in real-time. These systems actively generate counter-vibrations to cancel out disturbances, making them adaptable and highly effective in volatile environments. A common application is in aerospace engineering, where the need for minimizing vibrations can enhance structural integrity and passenger comfort.
The main advantages of active absorbers include:
- Adaptability: They can adjust to changing conditions quickly.
- Effectiveness: Better at managing a wide frequency range.
- Precision: Capable of fine-tuning vibration control to specific needs.
However, the complexity of such systems means that they generally require a constant power supply and rigorous maintenance to ensure sensitivity and reliability, making them more suited for applications where performance is non-negotiable.
Semi-Active Vibration Absorbers
Semi-active vibration absorbers combine elements of both passive and active systems. These devices do not have their own actuation capability but can modify their characteristics based on the input from sensors. They often use smart materials, like magnetorheological fluids, which change viscosity in response to applied magnetic fields. A classic use of such technology is in modern automotive suspensions, where they can vary stiffness and damping based on road conditions.
Benefits include:
- Flexibility: Capable of modifying performance dynamically.
- Energy efficient: Requires less power compared to fully active systems.
- Enhanced performance: Offers a balance between energy use and vibration control.
Despite these merits, the design of semi-active absorbers still hinges primarily on the right integration of sensors, controllers, and the materials used, demanding meticulous engineering attention for optimal results.
Each type of vibration absorber presents unique advantages and can be selected based on specific applications, performance requirements, and economic factors.
Applications of Vibration Absorbers
Vibration absorbers play a crucial role in various sectors, serving to reduce or eliminate unwanted vibrations that may cause significant damage or discomfort. Their applications span across multiple industries, ensuring smoother operations and enhancing the durability of machinery as well as structures. Whether it’s a bustling factory floor, a high-speed train, or even your favorite gadget, the strategic implementation of vibration absorbers can lead to improved performance and safety. By understanding their specific uses, industry professionals can make informed decisions about their deployment and maintain efficiency.
Industrial Machinery
In industrial settings, machinery often runs at high speeds, generating vibrations that can result in premature wear and tear, increased maintenance costs, and potential safety hazards. Machines like turbines or compressors are particularly susceptible to vibration issues, which can impact their operational integrity.
Using vibration absorbers in this context helps isolate equipment from vibrations, providing a safeguard against both physical wear and operational disruptions. For instance, in a manufacturing plant, installing a tuned mass damper on a conveyor system can significantly reduce the transmission of vibrations, resulting in smoother material handling.
"Effective vibration control in industrial machinery not only increases lifespan but also enhances productivity."
This increased reliability ultimately leads to lower downtime and maintenance costs, translating to a more profitable bottom line. Moreover, by minimizing vibrations, workers experience a more comfortable environment, which can improve morale and productivity as well.
Transportation Systems
Transportation systems are another area where vibration absorbers shine. Vehicles, whether they are trains, cars, or aircraft, encounter various forces that generate vibrations. These can result from uneven road surfaces, high speeds, or changes in direction, leading to discomfort for passengers and potential structural issues for the vehicles.
In the case of trains, for instance, implementing active vibration control systems can enhance ride quality by actively counteracting vibrations in real time. Such systems adjust based on feedback from sensors that detect acceleration and response, ensuring a smoother ride. Similarly, in automotive engineering, specialized bushings and mounts reduce vibrations transmitted from the engine and road surfaces into the cabin.
This dual benefit of improved comfort and safety extends to cargo transportation as well, where vibration control can protect sensitive goods from damage during transit.
Building and Structural Engineering
The application of vibration absorbers in building and structural engineering cannot be overstated. Buildings designed in areas prone to seismic activity, for example, can greatly benefit from tuned mass dampers. These systems help to counter the oscillations caused by earthquakes, thus safeguarding the structural integrity of the building.
Additionally, in architectural design, vibration absorbers can minimize the impact of wind-induced vibrations on skyscrapers. The incorporation of sloshing dampers in water tanks on rooftops creates an effective counterbalance against sway from gusts, enhancing the overall stability of the structure.
In essence, vibration absorbers not only protect the physical assets but also uphold the safety of inhabitants and occupants in urban environments, making them indispensable in modern construction practices.
Consumer Electronics
The consumer electronics sector is where vibration control is often overlooked yet critical. Devices like smartphones and laptops can be susceptible to vibrations that may affect performance, particularly in components like hard drives and speakers.
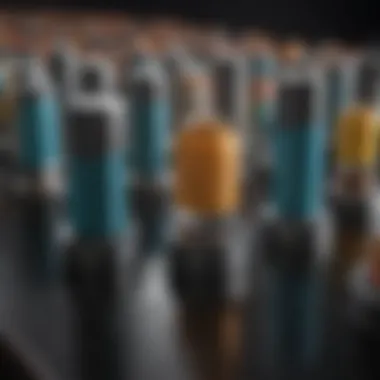
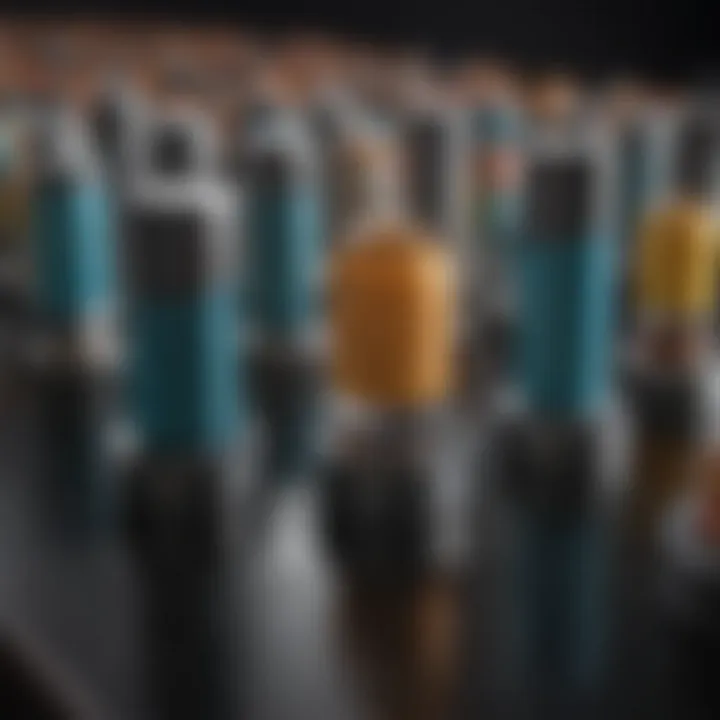
Implementing vibration dampening technologies in these devices can improve sound quality and increase the lifespan of sensitive components. For instance, in high-end audio equipment, adopting vibration isolation pads can enhance sound clarity by reducing the interference caused by vibrations during playback.
Furthermore, in the realm of wearables which are increasingly popular, integrating active vibration control enhances user experience by minimizing disruptions from movement or handling.
These applications highlight how vibration absorbers can lead to more reliable consumer products, ultimately better aligning with customer expectations of quality and performance.
Factors Affecting Vibration Absorption Efficiency
Importance of Vibration Absorption Efficiency
The efficiency of vibration absorbers plays a crucial role in determining their effectiveness across various applications. When we talk about vibration absorption, we’re referring to the ability of these systems to mitigate and dampen unwanted vibrations that can lead to detrimental impacts on machinery, structures, and even human comfort. Understanding the factors affecting vibration absorption efficiency is essential for anyone involved in the design and application of these systems, as it can lead to enhanced performance, longevity, and overall effectiveness of the absorbers.
Material Properties
The choice of materials in constructing vibration absorbers can significantly influence their performance. Different materials possess unique mechanical properties that affect how vibrations are transmitted, absorbed, and dissipated. Here are some key material considerations:
- Damping Characteristics: Materials that exhibit high internal damping can effectively absorb energy from vibrations. For instance, viscoelastic materials like rubber are notorious for their ability to dissipate vibrational energy effectively.
- Stiffness: The stiffness of a material impacts how much it can compress, deform, or bend under load. Softer materials may absorb more vibrations but lack the structural integrity required for certain applications, while stiffer materials may provide better support but absorb less energy.
- Fatigue Resistance: Since vibrational forces can cause wear and tear over time, selecting materials with high fatigue resistance extends the life of the absorbers and ensures consistent performance.
- Environmental Factors: Consideration of temperature, humidity, and exposure to chemical agents can alter the properties of the materials. Materials that perform well in controlled environments may fail in industrial or outdoor settings.
Design Parameters
Design parameters also critically influence the effectiveness of vibration absorbers. Here’s a look at several essential design factors that need to be taken into account:
- Size and Shape: The dimensions and overall design affect how well an absorber can fit into a given space. A well-designed absorber can operate efficiently in tighter areas, whereas an ill-fitted one may not function optimally due to restrictions in movement.
- Mounting Techniques: How an absorber is mounted can alter its vibration absorption capabilities. Using effective mounting techniques can help achieve better energy dissipation through proper alignment and isolation from the vibrating source.
- Tuning to Frequencies: For any vibration absorber, tuning to the specific frequencies it is designed to counteract is paramount. This requires a keen understanding of the vibration profile of the system to ensure that the absorber is designed effectively; otherwise, it may amplify vibrations instead of absorbing them.
"Understanding the interplay between material properties and design considerations is foundational in maximizing vibration absorber efficacy."
- Integration with Systems: Vibration absorbers should be designed to work seamlessly with the systems they are protecting. This comprehensive integration ensures that all elements function holistically to combat vibrations effectively.
In sum, from the intrinsic properties of the materials to the intricacies of design, numerous factors impact the efficiency of vibration absorption systems. Awareness of these variables provides essential insights for engineers and designers, leading to the development of more effective solutions for vibration mitigation.
Design Considerations for Vibration Absorbers
Design considerations play a crucial role in the efficiency and functionality of vibration absorbers. When engineers and designers set out to create effective vibration management solutions, they must keep a multitude of factors in mind to ensure their designs are not just theoretically sound but also practically applicable. These considerations may range from material selection to geometrical parameters, all of which can influence how well a vibration absorber performs in real-world scenarios.
Mechanical Design Challenges
The mechanical aspects of vibration absorbers come with their fair share of challenges. For instance, the physical constraints of space can severely limit the choices of vibrational management solutions. Here are some common challenges engineers might face:
- Limited Space: Often, there isn't enough room for conventional absorbers, particularly in compact machinery or consumer products, necessitating innovative solutions.
- Weight Limitations: In applications such as aviation, every gram counts. Extra weight from the absorber may shift aircraft performance metrics.
- Durability and Longevity: The absorbents must endure fatigue over time. Components that don’t wear down easily can reduce the need for frequent replacements, which is often a must in industrial settings.
These challenges underscore the importance of acute attention to detail in the design process. Engineers might need to utilize extra simulation tools to predict how materials will react under various conditions to mitigate these mechanical challenges effectively.
Innovative Design Approaches
With every challenge comes an opportunity for inventive solutions. As technology advances, so do the strategies used in designing vibration absorbers. Here are a few innovative approaches that have gained traction:
- Use of Smart Materials: These materials can change their properties in response to external stimuli. For example, piezoelectric materials generate an electric charge in response to applied mechanical stress, providing a two-fold benefit of absorption and energy harvesting.
- Topology Optimization: This is the process of optimizing material layout within a given design space, which can yield lighter and more effective vibration absorbers by eliminating unnecessary material without compromising integrity.
- Active Control Strategies: Employing sensors and actuators can allow for real-time adjustments to suppress unwanted vibrations. These dynamic systems can adapt to changing conditions, providing an elegant solution to variable vibration environments.
"Effective design serves as the foundation upon which functional vibration absorption is built. It’s not just about the materials or methods, but how they work together to solve a problem."
The integration of these factors not only ensures the absorbers’ effectiveness but also enhances their longevity and functionality across various applications. With the future of vibration management leaning heavily on these design considerations, ongoing research and development will undoubtedly yield even more promising solutions.
Advancements in Vibration Absorber Technology
The field of vibration absorbers is never stagnant; it constantly evolves as technology progresses and industries demand more efficient solutions. The advancements in vibration absorber technology not only tackle the existing challenges but also bring about innovative methods to enhance performance and reliability in diverse applications. These developments are vital for improving systems in sectors such as manufacturing, transportation, and consumer electronics. As companies aim to reduce wear and tear, increase safety, and protect sensitive components, understanding these advancements becomes crucial.
Smart Materials and Structures
Smart materials have revolutionized the way we think about vibration absorption. These materials can adapt their properties in response to external stimuli, making them not just useful, but highly efficient. For instance, piezoelectric materials can generate electrical energy from mechanical stress, thus allowing them to absorb vibrations while potentially providing power to other systems.
The integration of smart materials into vibration absorbers offers several advantages:
- Dynamic Adaptation: The ability to change properties based on vibration input enhances performance.
- Energy Harvesting: By converting vibrations into usable energy, these materials can provide self-sustaining systems, especially in remote monitoring applications.
Vibration control systems using smart materials can be used in automotive applications, where sensors detect road conditions and adjust the absorber characteristics accordingly. This capability results in a smoother ride and less wear on vehicle components. Moreover, incorporating shape-memory alloys into structures can provide active damping, granting engineers more control over the vibration response of the whole system.
"Smart materials offer a future where the boundaries of vibration control are in constant flux, leading to innovative solutions that were previously thought unattainable."
Recent Research Trends
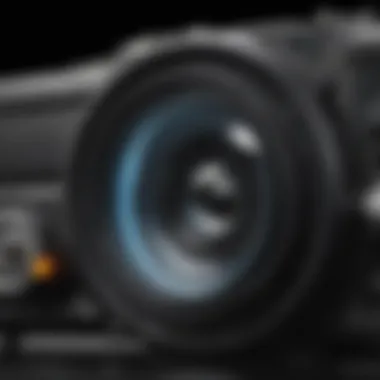
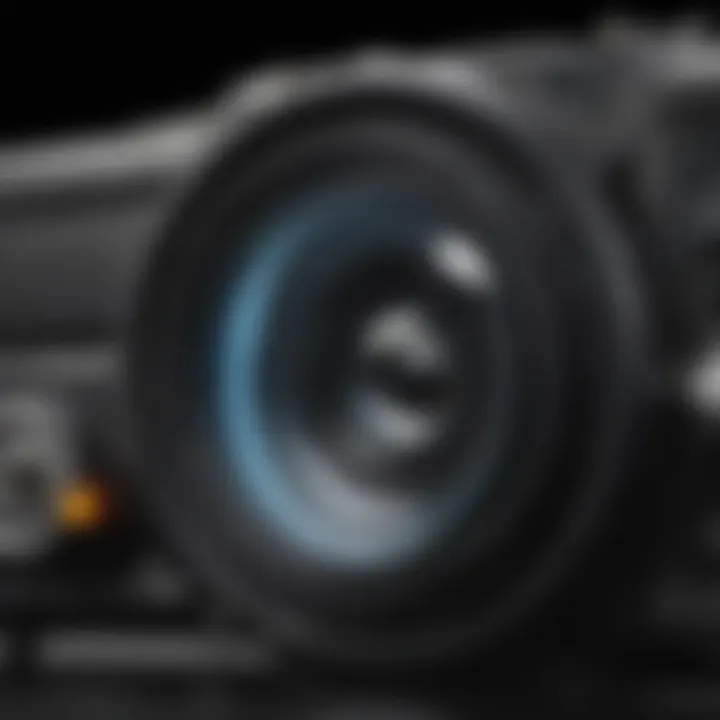
Recent research in vibration absorption technology is showing significant strides in areas like computational materials science, nanotechnology, and improved modeling techniques. Researchers are employing advanced simulation software to predict how various materials behave under specific vibration conditions. This predictive modeling allows for a more informed selection of materials and designs, ultimately leading to optimized absorbers.
Some noteworthy trends include:
- Nano-Enabled Absorbers: The incorporation of nanoparticles into traditional materials enhances their properties. This results in constructions that are lighter yet stronger, increasing the efficiency of vibration absorption.
- Multi-Functional Structures: Research is looking at how vibration absorbers can perform multiple roles, such as structural support and energy management, thus enhancing the overall functionality of a system.
- Integration with IoT: The Internet of Things is pushing forward the development of smart vibration absorbers capable of real-time monitoring and adjustments, enabling systems to respond on the fly to changes in their environment.
As these trends develop, looking at how fundamental research translates into practical applications is essential for staying ahead in the field. As noted in various studies, the collaborative work among institutions and industries leads to innovations previously unconsidered, paving the way for a new realm of possibilities in vibration management.
In summary, the advancements in vibration absorber technology showcase a promising future driven by smart materials and ongoing research. This evolution continuously shapes how industries approach vibration control, improving both performance and efficiency.
Case Studies of Vibration Absorber Implementation
The significance of case studies in the realm of vibration absorbers cannot be overstated. They provide real-world insights that theoretical discussions might miss. By focusing on specific instances of vibration absorber implementation, one can evaluate their effectiveness, the challenges faced during deployment, and the resulting benefits in various industries. This exploration serves a dual purpose: it not only illustrates the practical applications of vibration absorbance technology but also highlights the ongoing evolution of these systems through lessons learned from each case.
Manufacturing Sector
In the manufacturing industry, vibrations are omnipresent and can have detrimental effects on machinery and productivity. A case study from a prominent automobile assembly plant reveals the pivotal role vibration absorbers play. Here, the facility faced significant issues with high-frequency vibrations caused by stamping presses. These vibrations not only affected the equipment's operational efficiency but also led to excessive wear and tear, resulting in costly downtimes.
The installation of tuned mass dampers significantly mitigated these unwanted vibrations. These damping systems targeted the specific frequencies produced by the stamping operations, effectively reducing the amplitude of vibrations transmitted through the foundations. Post-implementation monitoring indicated a 60% reduction in vibrating energy, leading to increased machine lifespan and improved product quality. Furthermore, employees reported a noticeable drop in noise levels, enhancing the working environment.
Key Benefits in Manufacturing:
- Extended Equipment Lifespan: Reduced wear and tear lead to lower maintenance costs.
- Enhanced Quality of Output: Improved stability translates to higher product accuracy.
- Worker Safety and Comfort: Decreased noise and vibration levels create a better workplace environment.
Aerospace Applications
The aerospace sector presents unique challenges regarding vibration management due to the complex and high-stakes nature of flight. A notable case involved a leading aircraft manufacturer facing vibrations within their newly designed passenger jet during wind tunnel tests. These vibrations were not only a concern for structural integrity but also passenger comfort on the actual flight.
To address this, the team deployed advanced active vibration control systems integrated with smart materials capable of adjusting in real-time to the detected vibrations. Through rigorous testing and iterative design, these systems were fine-tuned to minimize the resonant frequencies generated by airflow and engine operation. The solution proved incredibly effective, achieving a 75% reduction in cabin vibrations. This case not only emphasizes the booming technological advancements in the aerospace industry but also showcases the importance of understanding vibration dynamics in critical applications.
Key Benefits in Aerospace:
- Improved Passenger Comfort: Reduced vibrations result in a more pleasant flight experience.
- Structural Integrity: Enhanced safety through improved design resilience.
- Efficiency in Design: Being able to iterate on models quickly supports faster innovation cycles.
By delving into these case studies, it becomes clear that vibration absorbers are not merely theoretical constructs but essential elements in various industries. Each successful implementation reinforces the notion that vibrational control is crucial for both efficiency and safety.
Future Directions in Vibration Absorption Research
In the rapidly advancing domain of engineering, the exploration of vibration absorbers is continuously evolving. This section delves into the future directions in vibration absorption research, shedding light on emerging opportunities and challenges that could reshape how we manage vibrations across various applications. Not only does this research play a pivotal role in enhancing existing technologies, but it also lays the groundwork for innovative approaches that can improve efficiency, safety, and sustainability in numerous industries.
Emerging Trends
Research efforts in vibration absorption are gravitating towards several key trends that promise to enhance the functionality and efficacy of absorbers. With increased integration of technology, we are witnessing a shift towards:
- Smart Materials: The use of materials that can respond dynamically to vibrations is gaining traction. Materials such as piezoelectric compounds or shape-memory alloys are becoming vital in the development of smarter absorbers capable of adjusting their properties in real time, enabling better performance in varying conditions.
- Sustainability: As environmental concerns rise, there's an increased emphasis on sustainable materials and processes in design. Researchers are actively looking into biodegradable or recyclable materials to create vibration absorbers, aligning with the broader trend of minimizing environmental impact.
- Sensor Integration: Utilizing sensors within vibration absorption systems can provide real-time data on performance and vibration metrics. This integration allows for proactive adjustments in systems, enhancing not just the effectiveness of absorbers but also the overall operational efficiency of machines and structures.
Potential New Applications
The horizons for vibration absorbers are expanding, with a spectrum of potential new applications becoming clear. These applications overlap with various fields, integrating vibration control into areas such as:
- Renewable Energy Systems: As turbines and other renewable technologies proliferate, vibration rotors in wind farms or wave energy converters face unique challenges. Advanced vibration absorbers can help mitigate wear and tear, extending the life of these systems significantly.
- Wearable Technology: With the emergence of wearable health devices, vibration absorbers can play a crucial role. They can not only enhance comfort but also improve the functionality of devices by minimizing external vibrational interference, leading to more accurate readings.
- Robotic Systems: In robotics, where precision is paramount, vibration absorbers could assist in maintaining the stability of robots during complex tasks. The ability to refine operations in industrial robots or even drones could lead to significant advancements in manufacturing and logistics.
"The future of vibration absorption is not just in treating symptoms but addressing root causes through innovation and materials science."
As these trends unfold and applications become more diverse, it’s essential for researchers, engineers, and stakeholders to stay abreast of developments in this field. Adaptation and innovation will be key to harnessing the full potential of vibration absorption technologies.
Closure
The conclusion of this article serves a pivotal role, encapsulating the essence of vibration absorbers and their multifaceted applications. It is not just a mere summary; rather, it underscores why understanding these devices is crucial for industries reliant on machinery and structures that experience dynamic loads.
Summary of Key Points
Throughout this text, we explored various elements intrinsic to vibration absorbers:
- Definition: Vibration absorbers are devices engineered to minimize unwanted oscillations, enhancing system stability and longevity.
- Types: We classified absorbers into passive, active, and semi-active categories, diving into their mechanisms and applications.
- Applications: They find utility in diverse settings—ranging from heavy industrial machinery to the delicate electronics in consumer gadgets.
- Design Considerations: Factors such as material selection and mechanical design challenges were discussed, shedding light on what engineers must consider during design phases.
- Technological Advancements: Innovations in smart materials have the potential to shape the future of vibration management significantly.
The article has painted a broad picture, illustrating how critical these absorbers have become across various sectors—not just from an engineering perspective but also for optimizing economic and functional aspects.
Implications for Future Research
Looking ahead, the realm of vibration absorbers demands ongoing investigation. The following areas merit particular attention:
- Smarter Absorbers: With the rise of smart materials, research should focus on harnessing these technologies to develop more efficient absorption systems that can adjust dynamically to varying conditions.
- Environmental Factors: Investigating how vibration absorbers can be optimized in relation to environmental dynamics like temperature fluctuations or humidity could broaden their competitive use.
- Sustainability and Eco-design: Future studies might explore the integration of eco-friendly materials and sustainable practices in the design process, aligning industrial needs with environmental stewardship.
In summary, the exploration of vibration absorbers intertwines innovative engineering with practical applications. For students, researchers, and professionals alike, understanding these devices will not only enhance their knowledge but also contribute to more effective designs and implementations that could potentially revolutionize industries dependent on vibration management.