Understanding Vacuum Gauges: Principles and Applications

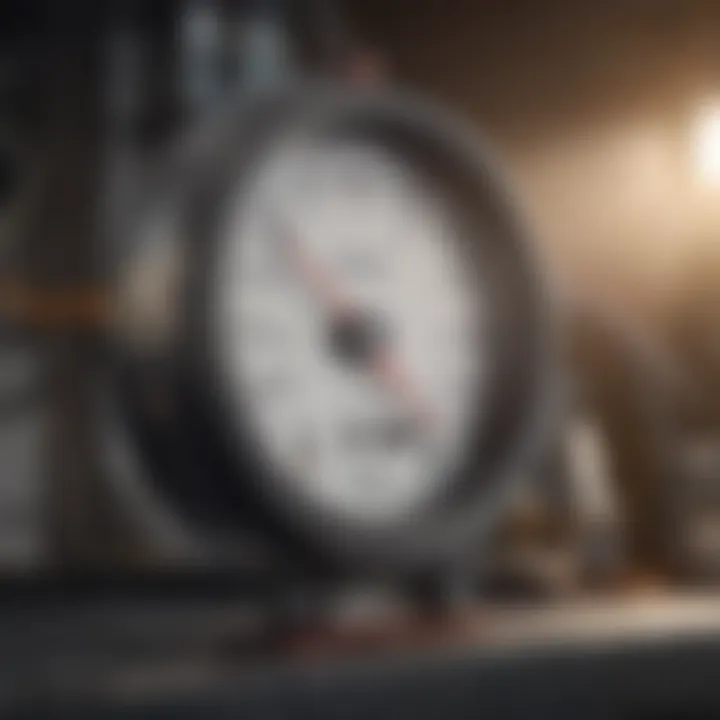
Intro
Vacuum gauges are instruments critical to measuring pressure in vacuum systems. Their significance spans many fields including scientific research, industrial operations, and more. In understanding these tools, one must explore how they function, the various types that exist, and how they are applied in real-world scenarios. This discussion seeks to provide a comprehensive overview of vacuum gauges, emphasizing their design, operation, and calibration.
Key Findings
Major Results
Through rigorous examination of vacuum gauges, it becomes clear that their operational principles are foundational to effective pressure measurement. Various types of vacuum gauges serve distinct purposes, from simple mechanical gauges to sophisticated electronic devices. The appropriate selection of a gauge directly influences not only measurement accuracy but also the efficiency of processes that rely on vacuum technology.
Discussion of Findings
The analysis reveals that calibration is a central aspect of employing vacuum gauges. Regular calibration ensures that measurements remain within specified tolerances, which is essential for both research and industrial applications. Furthermore, environmental factors such as temperature and humidity can significantly impact gauge performance and should be considered during assessments. The integration of modern technologies into gauge designs has also contributed to advancements in precision and reliability.
"Understanding the unique characteristics and limitations of each vacuum gauge variation is essential for optimal system performance."
In summary, choosing the right vacuum gauge demands a careful consideration of specific application requirements and an understanding of how these instruments operate in a range of environments.
Methodology
Research Design
The approach employed for this exploration includes a thorough literature review of existing scientific materials on vacuum gauges. This includes product specifications, academic studies, and expert interviews.
Data Collection Methods
Data was collected through various channels including academic journals, industry reports, and hands-on evaluations of different vacuum gauge types in operational settings. Observations from these contexts informed the conclusions drawn about measurement effectiveness and applicability in diverse situations.
By synthesizing key findings and methodologies, the article aims to illuminate the essential role vacuum gauges play in ensuring accurate and reliable pressure measurements across a multitude of fields.
Prelims to Vacuum Measurement
Understanding vacuum measurement is crucial in various fields, such as science, industry, and healthcare. Vacuum gauges are indispensable tools that help quantify the pressure within vacuum systems. Recognizing the significance of accurate pressure measurement relies on grasping the fundamental principles of vacuum gauges. This section will cover key definitions, applications, and the overall importance of vacuum gauges in the context of vacuum measurement.
Definition of a Vacuum Gauge
A vacuum gauge is an instrument designed to measure pressures below atmospheric pressure. Essentially, it indicates how far below this reference level the pressure exists. These gauges can employ various measurement techniques to deliver reliable readings, catering to different applications.
For instance, mechanical vacuum gauges use physical changes in a mechanism, like a Bourdon tube or a diaphragm, to reflect pressure changes. In contrast, electronic gauges leverage electronic signals to deliver precise measurements. Their function is vital for diverse applications ranging from laboratory experiments to large-scale industrial processes.
Importance of Vacuum Gauges
Vacuum gauges hold monumental significance for a variety of reasons. First, they ensure process control. In many industries, maintaining a specific vacuum level is essential for product quality. Failure to monitor vacuum pressure accurately can lead to defective products or safety hazards.
Moreover, vacuum gauges play a pivotal role in research. Scientists depend on precise measurements to conduct experiments that require controlled environments. The data provided influences results and conclusions drawn from the research. Furthermore, vacuum gauges aid in equipment maintenance by detecting issues such as leaks or failures in vacuum systems.
In summary, vacuum gauages are more than just tools. They underpin the operational integrity and efficiency across sectors, reinforcing their importance in vacuum measurement.
Types of Vacuum Gauges
Understanding the various types of vacuum gauges is crucial for accurately measuring and controlling pressure in vacuum systems. Each type has its unique characteristics, advantages, and limitations. This section dives into the main categories, offering insights into their construction, functionality, and applications.
Mechanical Vacuum Gauges
Mechanical vacuum gauges utilize physical mechanisms to measure pressure, their simplicity often being their greatest asset.
Bourdon Gauge
The Bourdon gauge is a widely recognized type of mechanical vacuum gauge. It functions based on the tendency of a curved tube to straighten when pressure is applied. As a result, the movement is transformed into a dial reading, providing a visual indication of vacuum levels.
A key characteristic of the Bourdon gauge is its ruggedness and ease of use. It is a beneficial choice for many applications including industrial settings where robustness is essential. The gauge can measure a wide range of pressures, which contributes to its versatility.
However, the Bourdon gauge does have limitations. Its accuracy can decline at very low pressures, making it less suitable for high-precision applications. Additionally, changes in temperature may affect its readings, leading to discrepancies.
Diaphragm Gauge
The diaphragm gauge operates using a flexible diaphragm that moves in response to pressure changes. This movement drives a corresponding output, typically seen on a dial or display.
Its key characteristic is sensitivity, enabling it to provide precise measurements at lower pressures. Diaphragm gauges are particularly useful in laboratory environments where exact measurements are needed, making it a popular choice in scientific research.
Nevertheless, diaphragm gauges can be impacted by changes in ambient temperature and mechanical vibrations, possibly introducing variability in readings. Thereβs also the risk of diaphragm rupture if excessive pressure is applied, leading to failure in measurement.
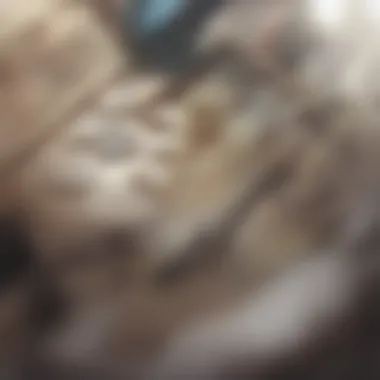
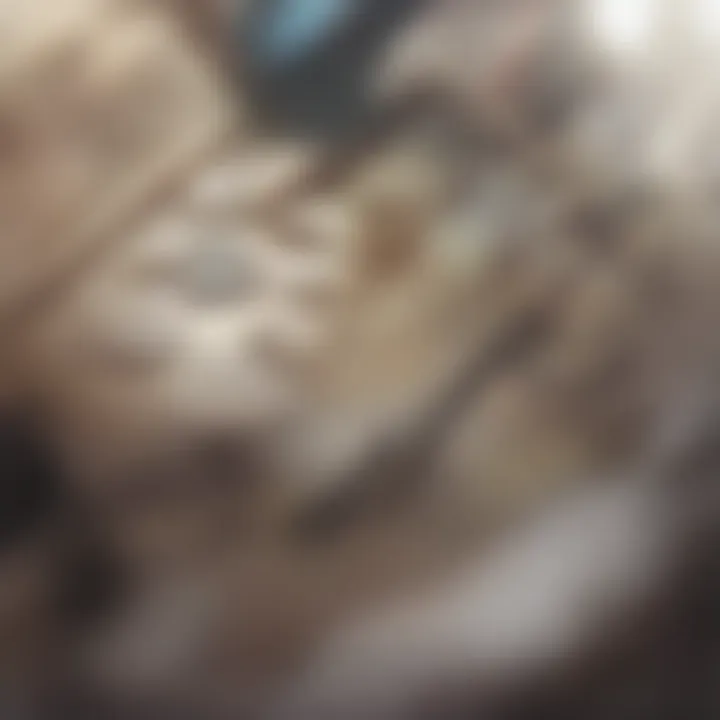
Electronic Vacuum Gauges
Electronic vacuum gauges have gained prominence due to their enhanced sensitivity and digital readouts. They offer a more modern approach to pressure measurement.
Capacitance Manometer
A capacitance manometer measures pressure through changes in capacitance caused by a deflection of a diaphragm between two conductive plates. One of its crucial attributes is high accuracy and stability across various pressure ranges.
This type of gauge is a beneficial choice in both industrial and high-tech research applications where precision is paramount. The unique feature is its capability to measure down to ultra-high vacuum levels, something traditional mechanical gauges struggle with.
On the downside, capacitance manometers can be costly and require careful handling due to the sensitive electronics involved. Furthermore, calibration is necessary for ensuring accuracy over time.
Piezoresistive Gauge
Piezoresistive gauges utilize piezoresistive materials that change electrical resistance when subjected to pressure. This principle allows for high precision in readings.
Their key characteristic lies in their ability to operate across different pressure ranges, making them versatile for various applications. They are also beneficial in situations where quick response times are required.
However, these gauges can be more complex to set up and might need specialized knowledge for maintenance and calibration. They are also susceptible to temperature effects, potentially influencing measurement accuracy.
Thermal Conductivity Gauges
Thermal conductivity gauges measure pressure based on the principle that the thermal conductivity of gases varies with pressure. Their unique design allows for rapid and real-time measurements.
Pirani Gauge
Pirani gauges feature a filament whose thermal properties change when it is in contact with gas at different pressures. They are valued for their simplicity and effectiveness in measuring low to medium vacuum levels.
The main advantage of Pirani gauges is their quick response time, which is critical in many dynamic vacuum processes. Nevertheless, they have limitations in measuring very low pressures accurately and can produce errors in non-ideal conditions due to the influence of gas species.
Thermocouple Gauge
Thermocouple gauges operate on the principle of heat transfer and are capable of providing accurate pressure measurements. With their high sensitivity, they can measure a wide range of pressures effectively.
The characteristic strength of thermocouple gauges is their broad application spectrum, reaching from laboratory to industrial settings. While they offer reliability, exposure to extremes of temperature might impact their readings over time.
Ionization Vacuum Gauges
Ionization vacuum gauges are sophisticated instruments that measure vacuum levels in environments where other types may fail. They use ionization of gas molecules to provide pressure readings.
Cold Cathode Gauge
Cold cathode gauges generate ions through electrical discharge in gas, allowing for very sensitive measurements at ultra-high vacuum levels. This gauge is a powerful tool for applications that require precision.
A unique feature of cold cathode gauges is their wide measuring range. However, they can be more intricate to operate and might require more maintenance compared to simpler gauges.
Hot Cathode Gauge
Hot cathode gauges utilize a heated filament to create ions; these are then detected to provide vacuum readings. This type allows for effective measurement in ultra-high vacuum conditions.
Their key characteristic is that they can measure extremely low pressures accurately and can provide faster response times. Despite their benefits, they are more sensitive to contamination and can require frequent calibrations, which might be a drawback in some applications.
Principles of Vacuum Measurement
Understanding the principles of vacuum measurement is crucial in various fields such as industry, research, and healthcare. Vacuum gauges measure pressure levels in environments that are less than atmospheric pressure. The insights gained from these measurements inform numerous applications, from creating high-quality products to conducting precise scientific experiments.
Pressure Measurement Basics
Pressure measurement is foundational to vacuum gauging. It refers to the force exerted by gas molecules per unit area, typically measured in pascals (Pa) or torr. The principle behind pressure measurement is the behavior of gases, which expands to fill their container. In a vacuum, the number of gas molecules is limited, resulting in reduced pressure levels.
For accurate measurements, it is essential to consider factors such as temperature and the nature of the gas involved. Different vacuum gauging techniques apply various means to determine pressure, including mechanical deformation, electrical signals, or thermal conductivity. Each method has strengths and weaknesses, affecting the needle of accuracy and responsiveness.
Understanding Absolute Pressure
Absolute pressure measurement indicates the pressure relative to a perfect vacuum. This concept is fundamental for calculating the true pressure of gases. The absolute pressure is the sum of atmospheric pressure and gauge pressure, aligning it with a reference point of zero pressure.
Knowing absolute pressure is vital when precise vacuum conditions are necessary. For example, in a laboratory setting, experiments often rely on maintaining specific absolute pressures to ensure reliable results. Failure to account for absolute pressure can lead to erroneous findings or compromised processes.
Gauge Pressure vs. Absolute Pressure
The distinction between gauge pressure and absolute pressure is critical for accurate pressure assessments.
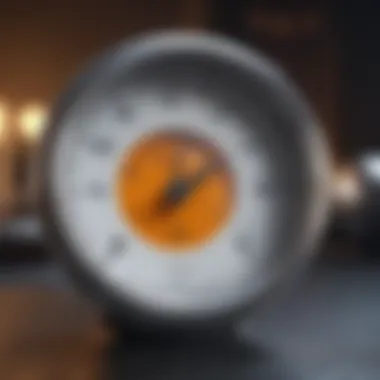
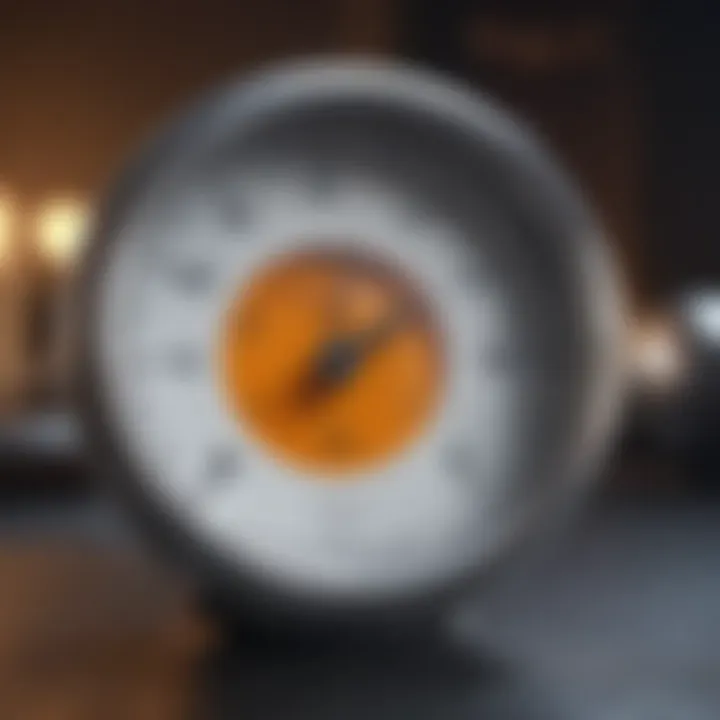
- Gauge Pressure refers to the pressure measured against atmospheric pressure. It is what most gauges display and is useful for applications where the specific atmospheric conditions do not significantly affect the measurement.
- Absolute Pressure, as noted, measures against a complete vacuum. This measurement is crucial in scientific applications where atmospheric influence cannot be overlooked.
Understanding the difference allows engineers and researchers to select appropriate measurement tools for their specific needs.
In summary, the principles of vacuum measurement inform the design and application of vacuum gauges. Knowledge of pressure basics, absolute pressure, and the differences between gauge and absolute pressure enhances both accuracy and performance in various sectors.
Calibration and Accuracy
Calibration and accuracy stand as pivotal cornerstones in the realm of vacuum measurement. Their significance cannot be overstated, particularly in the context of ensuring that vacuum gauges provide reliable and precise data. Accurate measurements are critical for systems requiring exact pressure readings, such as scientific research and industrial applications. Inaccurate readings can lead to faults in processes or skewed research data, which might have far-reaching consequences.
Calibration Techniques
Calibration is a systematic process that adjusts the readings of a gauge to align with a known standard. Different techniques exist to maintain the integrity of vacuum measurement.
Primary Standards
Primary standards refer to the most accurate means of pressure measurement. They are often used as references against which other measuring devices are calibrated. Their key characteristic is their high precision and traceability to national or international standards. This makes them a preferred choice for absolute accuracy in vacuum systems.
The unique feature of primary standards is their ability to provide fixed pressure points for calibration, minimizing chance of error. In contexts where exactitude is non-negotiable, primary standards are indispensable. However, they may be more expensive and less accessible for routine calibration.
Secondary Standards
In contrast, secondary standards are calibrated against primary standards. These devices hold a crucial role in day-to-day measurement needs, providing a balance between convenience and accuracy. The main characteristic of secondary standards is their affordability and practicality, making them prevalent in various applications.
Their unique feature lies in their ease of use; secondary standards can be employed directly in the field, avoiding the need for complex setups. However, while they offer good accuracy, they do not attain the level of precision found in primary standards. Therefore, a comprehensive calibration system typically involves both primary and secondary standards to ensure optimal accuracy across a range of applications.
Factors Affecting Accuracy
Several factors can significantly influence the accuracy of vacuum gauges. Environmental conditions such as temperature and humidity may alter readings. Additionally, gauge type plays a role; for example, electronic gauges may be susceptible to electrical noise, while mechanical gauges can be affected by physical wear and tear.
Furthermore, regular maintenance is a vital aspect; dirt or contamination on gauge sensors can lead to inaccurate readings. Users must be diligent about cleaning and servicing their equipment to maintain accuracy.
Finally, human error during the calibration and measurement processes introduces another layer of complexity. Understanding and mitigating these factors can refine the accuracy of vacuum measurements, underscoring the importance of a robust calibration strategy for effective vacuum gauge performance.
Applications of Vacuum Gauges
Vacuum gauges play a vital role in various fields. Understanding their applications enhances our grasp of their significance. Vacuum measurement is not limited to one industry; it permeates manufacturing, scientific research, and healthcare. Each sector leverages vacuum technology to achieve specific outcomes, improve efficiency, and ensure safety. The accuracy of vacuum gauges directly affects product quality, research data, and, in healthcare, patient safety. Therefore, knowing these applications is essential for professionals in research and industry alike.
Industrial Applications
Manufacturing
In manufacturing, vacuum gauges are critical. They ensure optimal conditions during processes like vacuum forming and coating. High precision is required to create components with tight tolerances. Such precision is only achievable with proper vacuum measurement. Thus, vacuum gauges become integral in equipment performance. They help in monitoring the vacuum levels, which makes sure that the processes are running smoothly.
One key characteristic of manufacturing applications is the variety of processes that require vacuum conditions. For example, semiconductor manufacturing relies heavily on vacuum to prevent contamination. Therefore, selecting the right gauge can significantly affect production quality. It promotes consistency and reduces wastage. However, the challenge is the potential for gauge drift over time, which requires regular calibration.
Food Processing
In food processing, vacuum gauges assist in numerous tasks. They regulate the atmosphere in packaging and cooking processes. Vacuum sealing helps to extend shelf life by reducing oxygen, which inhibits spoilage. The key characteristic here is the emphasis on hygiene and safety. Proper vacuum measurement helps maintain standards crucial for food safety.
The unique feature of vacuum packaging is its ability to preserve freshness. This technique allows food to stay consumable longer, which benefits both producers and consumers. However, a disadvantage can be the reliance on electric power, which can be a concern in remote areas. Overall, vacuum gauges enable better control in food processing.
Scientific Research
Physics Experiments
Physics experiments often require precision and control over environmental conditions. Vacuum gauges provide essential measurements for experiments in particle physics and quantum mechanics. Their core importance lies in creating low-pressure environments, which is necessary for studying particle behavior. The key characteristic is the precision with which measurements can be taken.
These gauges allow researchers to collect reliable data, leading to robust results. A specific feature is the ability to maintain constant vacuum levels for prolonged periods. This is crucial, as fluctuations can lead to erroneous results. However, the accuracy can be influenced by environmental factors, requiring careful monitoring and adjustment.
Material Science
Material science often intersects with vacuum technology. Conducting experiments at various vacuum levels can help understand material properties better. This contributes to advancements in electronics, nanotechnology, and other fields. The availability of high-resolution vacuum gauges means researchers can achieve needed precision in their experiments.
A significant benefit lies in the ability to manipulate material properties by changing vacuum conditions. Adjustments in pressure can lead to different atomic structures. However, the downside can be the complexity of measurements, as each material may respond differently. Thus, understanding how to interpret these measurements is key to success in research outcomes.
Healthcare Applications
Vacuum Packaging
In healthcare, vacuum packaging is crucial for maintaining sterility. It ensures that medical supplies are preserved without contamination. The controlled environment achieved through vacuum helps in the storage of sterile instruments and medications. One of the key characteristics of healthcare applications is regulatory compliance. Maintaining strict standards is mandatory.
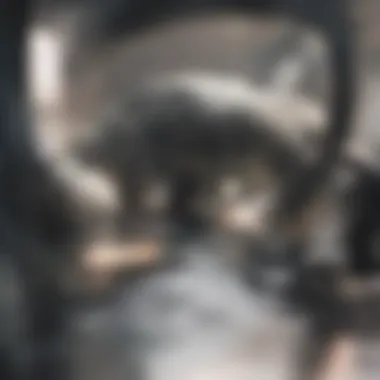
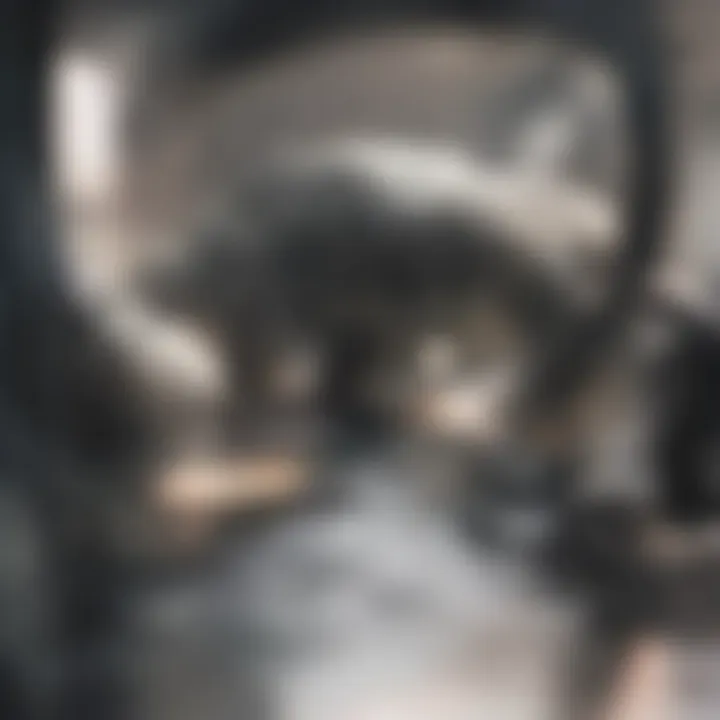
Vacuum packaging helps organizations comply with these regulations by extending the life of equipment and medicines. However, the disadvantage is the reliance on specific equipment, which can become costly. Organizations need to assess the budget against the benefits provided by vacuum technologies.
Blood Sample Preservation
Vacuum technologies are also vital in blood sample preservation. Blood samples require specific storage conditions to prevent degradation. Using vacuum storage minimizes exposure to contaminants, ensuring sample integrity. An essential characteristic is the ability to store samples longer without quality loss.
This feature is beneficial for diagnostic testing and research purposes. However, mishandling vacuum storage can lead to compromised samples, impacting test accuracy. It is crucial to follow protocols to prevent such issues. Proper vacuum gauge use can mitigate risks significantly.
The applications of vacuum gauges are not just technical; they directly influence quality and safety across numerous fields.
Challenges in Vacuum Measurement
Understanding the challenges in vacuum measurement is crucial for scientists and engineers who rely on accurate measurements for their experiments and industrial processes. The reliability of the readings from vacuum gauges has significant implications on the operation efficiency and safety of vacuum systems. Challenges can arise from several sources, which include limitations inherent to different types of vacuum gauges and the impact of contaminants in the measured environment.
Limitations of Different Gauge Types
Each type of vacuum gauge has distinct characteristics that can influence its effectiveness in various applications. For example, mechanical gauges, while cost-effective, often lack the accuracy required for high vacuum applications. On the other hand, electronic gauges provide better precision but may suffer from non-linearity at extremely low pressures. Specific limitations include:
- Mechanical Gauges: These often cannot measure very low pressures. They also may be affected by temperature changes, leading to erroneous readings.
- Capacitance Manometers: Although precise, they can be sensitive to temperature and require careful calibration to ensure accurate measurements.
- Thermal Conductivity Gauges: These gauges depend heavily on the type of gas being measured. Changes in gas composition can lead to measurement errors.
- Ionization Gauges: Their operating mechanism usually means they cannot function well at atmospheric levels. They are primarily suited for high vacuum measurements.
Understanding these limitations helps users choose the correct gauge for specific tasks, thus improving measurement accuracy.
Impact of Contamination
Contamination presents a significant challenge in vacuum measurements. It can arise from several sources, including outgassing from materials within the vacuum chamber and unwanted particles entering the system. Contaminants influence the behavior of gas molecules, consequently affecting the gauge performance and accuracy. Key considerations include:
- Outgassing: Materials in the vacuum system can release gas over time. This outgassing can change the vacuum levels, cause fluctuations in readings, and degrade measuring devices over time.
- Particulate Contamination: Dust or other particles entering the vacuum can disrupt measurements. Sensors may not register accurately if the particulate matter influences gas properties or the measuring environment.
- Chemical Contaminants: They can create reactions that change pressure readings and affect vacuum gauge calibration. Precise vacuum conditions are imperative in many applications, and contamination can hinder this.
Accurate vacuum measurement is essential in various fields, and understanding challenges such as gauge limitations and contamination is vital to ensure reliable readings and successful outcomes.
Ultimately, by recognizing these challenges, researchers, and engineers can adopt better practices to mitigate their effects. This has profound implications not only for individual projects but also for advancements in vacuum technology.
Future Trends in Vacuum Measurement Technology
The landscape of vacuum measurement technology is constantly evolving. Keeping pace with advancements is crucial for industries that rely on precision and accuracy. This section discusses future trends, emphasizing how they can transform the measurement landscape. The benefits of these emerging technologies, alongside important considerations, will help stakeholders understand what is at stake in vacuum measurement going forward.
Advancements in Sensor Technology
Recent strides in sensor technology have greatly enhanced the performance of vacuum gauges. Innovations in materials and design are helping manufacturers create sensors with improved sensitivity and lower power consumption. One notable advancement is the development of silicon-based pressure sensors, which offer superior accuracy. These sensors are capable of measuring extremely low pressures with high resolution.
Moreover, modern sensors are integrating features such as digital output, which allows for easier data interpretation. With real-time data monitoring being critical in various applications, these advanced sensors enable better control and feedback in vacuum systems. This technology is increasingly being adopted in cleanrooms, laboratories, and manufacturing processes
Benefits of Advancements:
- Enhanced accuracy and reliability of measurements.
- Faster response times for real-time applications.
- Reduced size and weight of equipment, facilitating easier installation.
With these improvements, the future of vacuum measurement looks poised for advancements that will support more complex and demanding applications than ever before.
Integration with IoT
As industries continue to immerse themselves in smart technology, the integration of vacuum measurement systems with the Internet of Things (IoT) is gaining momentum. This integration allows vacuum gauges to communicate with other devices and systems over the internet, opening new avenues for efficiency and data management.
The IoT connectivity enables remote monitoring and management of vacuum systems, which is especially valuable in sectors like pharmaceuticals and semiconductor manufacturing. For instance, operators can access real-time pressure data from multiple locations, leading to faster troubleshooting and reduced downtime. This capability not only streamlines processes but also enhances the decision-making processes for operators.
"The integration of IoT into vacuum measurement technology represents a significant paradigm shift for industries worldwide."
Considerations in Integration:
- Cybersecurity measures are essential to protect sensitive data.
- Training personnel to manage and interpret IoT data effectively is crucial.
Closure
The conclusion serves as a critical component of this article, synthesizing the previously discussed elements surrounding vacuum gauges. Effective vacuum measurement technologies are vital across various sectors, including industrial production, scientific research, and healthcare. These instruments not only ensure quality and safety but also enhance efficiency in processes where vacuum conditions are pivotal.
Recap of Importance and Applications
In summary, vacuum gauges are indispensable tools for maintaining optimal control over vacuum systems. Their applications are widespread and encompass:
- Manufacturing: They help ensure products meet strict quality standards by monitoring vacuum levels during processes such as metal forming and packaging.
- Scientific Research: Vacuum gauges are essential in experiments that require a controlled environment, including material science and physics studies.
- Healthcare: Their role in preserving biological samples and vacuum sealing food products highlights their importance in this sector.
Understanding the nuances of how these gauges function, their calibration, and the implications for accuracy can greatly benefit professionals in any field utilizing vacuum systems.
Final Thoughts on Vacuum Measurement
As technology continues to evolve, so too will the capabilities of vacuum measurement equipment. The integration of advanced sensor technologies and the Internet of Things (IoT) into vacuum gauging systems shows promise for the future. Innovations will likely enhance accuracy, data transmission, and usability, making vacuum gauges even more efficient and reliable in their respective applications.
Ultimately, a solid grasp of vacuum measurement principles not only aids in the effective use of these tools but also contributes to advancements in multiple fields. Armed with this knowledge, researchers, engineers, and students can better appreciate the complex role of vacuum gauges in shaping modern practices.