Understanding Thermal Expansion in Stainless Steel
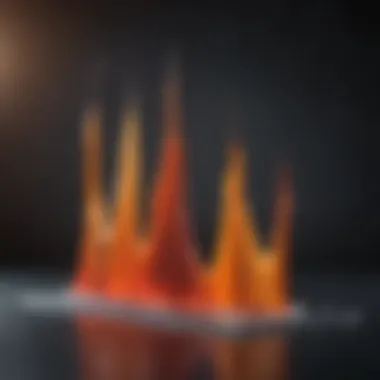
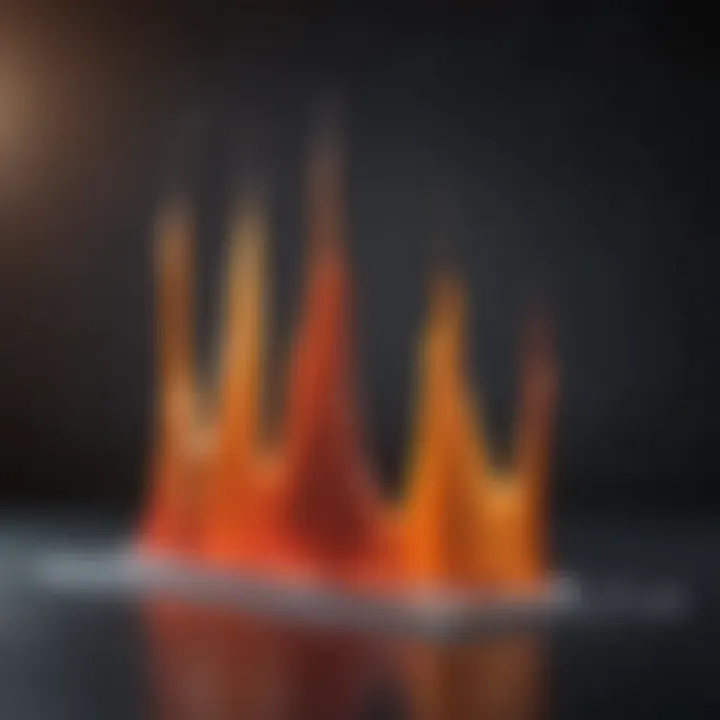
Intro
The coefficient of thermal expansion (CTE) is a critical property for materials, particularly stainless steel. This property quantifies how much a material expands or contracts when exposed to changes in temperature. For engineers, understanding CTE is essential, as it influences the integrity and performance of structures and components under varying thermal conditions.
In this article, we will explore the CTE of stainless steel in great detail, discussing its scientific basis, measuring methods, variations across different alloys, and the practical implications for engineering and manufacturing.
Key Findings
Major Results
The coefficient of thermal expansion for stainless steel varies among the different grades of the material. Generally, CTE values range from 15 to 20 x 10^-6 /°C (understandably, these values depend greatly on the specific alloy). For example, austenitic stainless steels like 304 and 316 exhibit a CTE closer to 16.5 x 10^-6 /°C, while ferritic grades tend to show slightly lower values.
Understanding this variation is significant in scenarios where stainless steel is used in environments with wide temperature fluctuations. If not considered, such thermal expansion can lead to material failure, stress, or distortion.
Discussion of Findings
The practical implications of CTE extend to several industries, including construction, automotive, and aerospace. In construction, for example, the expansion of steel frameworks can cause issues if joints do not accommodate movement. In engineering, maintaining the integrity of components critical to safety and performance requires precise calculations regarding thermal response.
"The ability to predict material behavior under changing temperatures is vital for ensuring structural integrity and reliability in engineering designs."
Methodology
Research Design
This article reviews existing literature on the coefficient of thermal expansion in stainless steel. It synthesizes findings from various studies in order to present a cohesive understanding of the subject.
Data Collection Methods
Data on CTE values were collected from peer-reviewed journals and reputable engineering resources. Laboratory experiments and standardized tests provide a significant amount of this information, allowing for a reliable depiction of CTE behavior across different conditions.
Preface to Thermal Expansion
Understanding thermal expansion is crucial in engineering and material science. It involves how materials change in size as a response to temperature variations. This behavior has significant implications for material selection, design processes, and operational efficiency. For stainless steel, knowing the coefficient of thermal expansion (CTE) helps engineers predict how components will react under changing temperatures. This understanding is key to ensuring structural integrity, reducing risks, and optimizing performance across various applications.
Definition of Thermal Expansion
Thermal expansion refers to the tendency of materials to expand when heated. When the temperature of an object increases, its atoms vibrate more vigorously, pushing each other apart. This results in an increase in the material's volume. There are two primary types of thermal expansion: linear and volumetric. Linear thermal expansion considers the changes in one dimension, whereas volumetric thermal expansion accounts for changes in all three dimensions.
The coefficient of thermal expansion is a quantitative measure of this expansion. It is defined as the change in length per unit length per degree change in temperature. In mathematical form, it is expressed as:
[ CTE = \frac\Delta L/L_0\Delta T ]
where ( \Delta L ) is the change in length, ( L_0 ) is the original length, and ( \Delta T ) is the change in temperature. The units are typically expressed in parts per million per degree Celsius (ppm/°C).
Importance in Material Science
The significance of thermal expansion in material science cannot be overstated. It influences how materials are used in various applications. For instance:
- Thermal Stress: When a material expands unevenly, it can cause stress, leading to cracks or structural failures.
- Design Considerations: Understanding CTE allows engineers to design joints and connections that are less likely to fail under temperature changes.
- Material Combination: Different materials expand at different rates. Joining materials with dissimilar thermal expansion properties can cause issues unless properly accounted.
In the context of stainless steel, knowing its CTE is essential. Stainless steel exhibits a relatively low CTE compared to other metals, making it suitable for applications where temperature fluctuations are common. Engineers and designers must consider this property to ensure longevity and reliability in their projects.
Fundamentals of Coefficient of Thermal Expansion
The coefficient of thermal expansion (CTE) is fundamental in understanding how materials, including stainless steel, react to changes in temperature. This property governs how objects expand when heated and contract when cooled. In engineering and manufacturing, knowledge of CTE is indispensable for predicting the behavior of components under thermal stress.
Understanding the fundamentals of CTE aids in effective material selection for various applications. Materials that exhibit high stability in their CTE are often preferred in critical components. For example, in constructions where temperature variation is significant, such as bridges or high-heat applications, recognizing these thermal properties is vital to ensure structural integrity and longevity.
The benefits of grasping CTE fundamentals also extend into everyday applications, including HVAC systems, pipelines, and electronic devices. A solid knowledge of how stainless steel reacts to heat can lead to better designs that minimize thermal stress and enhance performance.
The considerations are numerous. For engineers, the impact of temperature changes on a project can sometimes be overlooked; this neglect can cause catastrophic failures. Thus, focusing on the fundamental aspects of CTE is key to preventing such outcomes.
Overview of Coefficient of Thermal Expansion
The coefficient of thermal expansion is a material property defined as the rate at which a material expands when subjected to an increase in temperature. It is usually expressed in parts per million per degree Celsius (ppm/°C). For stainless steel, this value typically ranges around 16 to 20 ppm/°C, depending on the specific alloy and conditions.
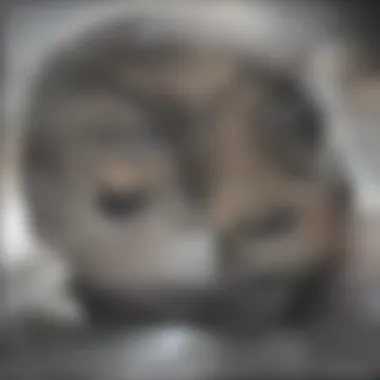
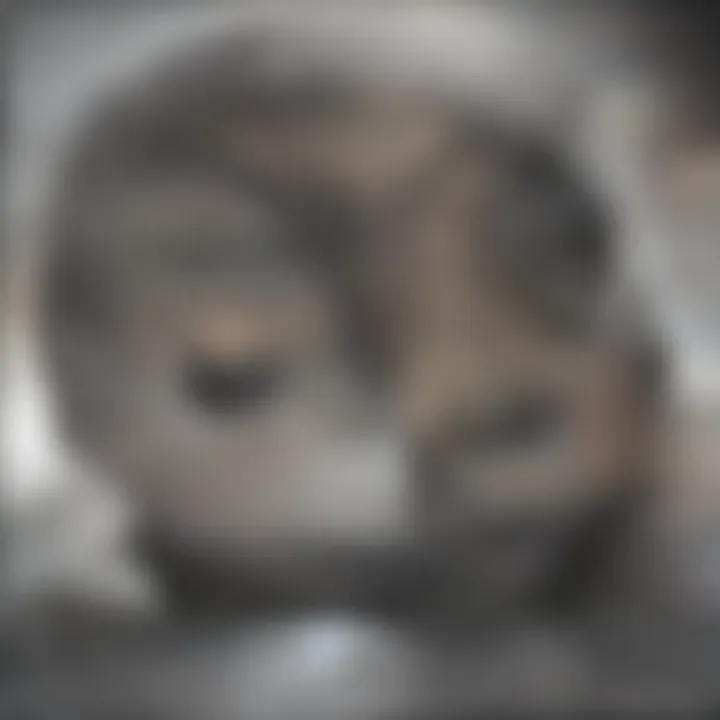
CTE can be categorized into two types: linear and volumetric expansion. Linear expansion refers to the change in length of a material as it heats. Volumetric expansion describes how an entire material's volume changes with temperature. For most engineering purposes, linear expansion is the primary focus.
This property affects various industrial processes, from production to end-use applications. Engineers and designers must consider how expansion can influence assembly tolerances, connections, and the overall lifespan of products.
Units of Measurement
When discussing the coefficient of thermal expansion, the standard unit is parts per million (ppm) per degree Celsius. This unit expresses how much a material will expand for a given temperature increase. While discussing CTE, it is important to ensure clarity in measurement units.
In some cases, CTE can also be reported in inches per inch per degree Fahrenheit (in/in/°F). This measurement is commonly used in industries where Fahrenheit is the standard temperature scale. Here are some key points about the units of measurement:
- Expression of Change: CTE indicates the number of parts per million that a material expands per degree of temperature change.
- Standardization: CTE must be measured under controlled environments. It is crucial to maintain consistent ambient conditions for accurate results.
- Relevance in Design: Different industries may use different units, but understanding the conversion between these units is essential for engineers.
In summary, a robust understanding of the fundamentals of the coefficient of thermal expansion in stainless steel is critical for effective engineering practices and material applications.
"Understanding the Coefficient of Thermal Expansion helps predict material behaviors under thermal stress, ensuring better designs and applications."
This knowledge can prevent failures and improve the efficiency of systems within various industries.
Stainless Steel as a Material
Stainless steel is widely recognized for its versatility and durability. Its significance in the discussion of the coefficient of thermal expansion (CTE) cannot be overstated. The material’s unique properties make it an essential choice in various applications, especially in environments subject to fluctuating temperatures. Understanding the CTE in stainless steel allows engineers and scientists to predict material behavior under thermal stress, ensuring reliability and performance in real-world applications.
Key Benefits of Stainless Steel:
- Corrosion Resistance: Stainless steel maintains its integrity in diverse environmental conditions. This property is crucial in applications ranging from construction to manufacturing, where exposure to moisture and chemicals may occur.
- Strength and Ductility: The strength of stainless steel, combined with its ability to deform without breaking, makes it ideal for structural applications. This balance ensures safety and longevity in engineered products.
- Thermal Stability: As a material, stainless steel exhibits relatively low thermal expansion, which is beneficial in applications requiring precise dimensional stability. This stability is vital in fields like aerospace and automotive engineering, where even minor dimensional changes can lead to catastrophic failures.
Understanding the CTE associated with stainless steel not only aids in material selection but also informs design strategies that mitigate the risks associated with thermal expansion.
Properties of Stainless Steel
The properties of stainless steel vary depending on its alloy composition, which significantly influences its performance in different environments. Here are some fundamental properties:
- Melting Point: Generally, stainless steel has a melting point between 1400°C to 1450°C. This high melting point is critical for applications in extreme temperatures.
- Thermal Conductivity: Stainless steel has relatively low thermal conductivity, which affects how heat is transferred through the material. This property can lead to temperature gradients that must be considered in design.
- Elastic Modulus: The elastic modulus of stainless steel is generally high, indicating greater stiffness compared to other materials. This property can impact how structures respond to applied loads over time.
- Hardness: Based on the alloying elements and processing, stainless steel can achieve high hardness levels, leading to enhanced wear resistance.
These properties significantly influence how engineers approach the design of components and structures made from stainless steel.
Common Alloys and Their Characteristics
Stainless steel comes in various alloys, each tailored for specific applications. Commanding specific characteristics, these alloys play a crucial role in determining the CTE and overall performance of the material.
- 304 Stainless Steel: Known for its good corrosion resistance and formability, this alloy is among the most commonly used. Its CTE value typically ranges from 16 to 17 x 10⁻⁶/°C.
- 316 Stainless Steel: This alloy is similar to 304 but with the addition of molybdenum, enhancing its resistance to corrosion in chloride environments. Its CTE is slightly higher than that of 304.
- 410 Stainless Steel: This alloy is a martensitic type, known for its high strength and wear resistance but offers lower corrosion resistance. Its CTE can differ significantly due to the different composition.
- Duplex Stainless Steels: Combining austenitic and ferritic properties, these alloys exhibit high strength and resistance to stress corrosion cracking. The CTE of duplex stainless steels is generally lower than that of standard austenitic grades.
Understanding the unique characteristics of these alloys is essential for making informed decisions in material selection and application. Each alloy's specific traits influence its behavior under varying thermal conditions, thereby affecting its suitability for different engineering contexts.
Coefficient of Thermal Expansion in Stainless Steel
The coefficient of thermal expansion (CTE) is an essential characteristic of stainless steel that influences its behavior under varying temperatures. Understanding the CTE helps engineers and material scientists predict how stainless steel will react in different thermal environments. This knowledge is crucial for ensuring the structural integrity of components in various applications.
Typical CTE Values for Stainless Steel
The typical CTE values for stainless steel vary among different types of alloys. Generally, the standard CTE for austenitic stainless steels ranges from approximately 15 to 20 x 10^-6 /°C. Ferritic steels tend to have a slightly lower coefficient, usually around 10 to 15 x 10^-6 /°C.
These values indicate how much a material will expand with an increase in temperature. For example, AISI 304, one of the most common austenitic stainless steels, has a CTE of about 16.5 x 10^-6 /°C. By contrast, AISI 430, a ferritic stainless steel, typically displays a CTE of 10.3 x 10^-6 /°C. The variation in these values has implications for design and manufacturing processes, particularly where temperature fluctuations are common.
Variation Among Different Alloys
Different stainless steel alloys exhibit distinct CTE values due to their unique compositions. For example, the addition of molybdenum, which is prevalent in higher-performance stainless steels, can affect the thermal expansion characteristics.
- Austenitic Alloys: Alloys such as AISI 316 contain nickel and molybdenum, leading to higher CTE values. The more alloyed elements contribute to increased thermal expansion as compared to simpler compositions.
- Ferritic Alloys: These tend to have lower CTE values because they have a more stable crystal structure. However, they are less ductile compared to austenitic alloys, which is essential during thermal cycling.
In specific engineering situations, selecting a stainless steel alloy with the right CTE can prevent thermal stresses, reduce fatigue, and avoid failure over time. Recognizing the variations among different alloys is crucial for applications such as:
- Heat exchangers: Where different materials might interface with stainless steel, CTE mismatches can lead to failure.
- Turbine blades: Where thermal conditions change rapidly and designs must accommodate expansion.
In summary, understanding the CTE in stainless steel and its variations among different alloys leads to better engineering decisions and enhances the performance of products across numerous industries.
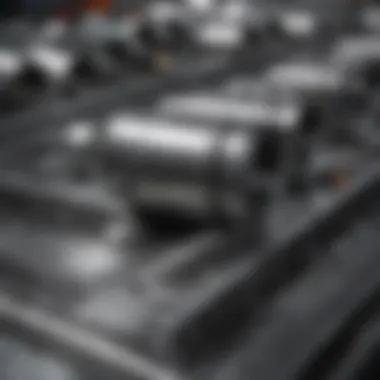
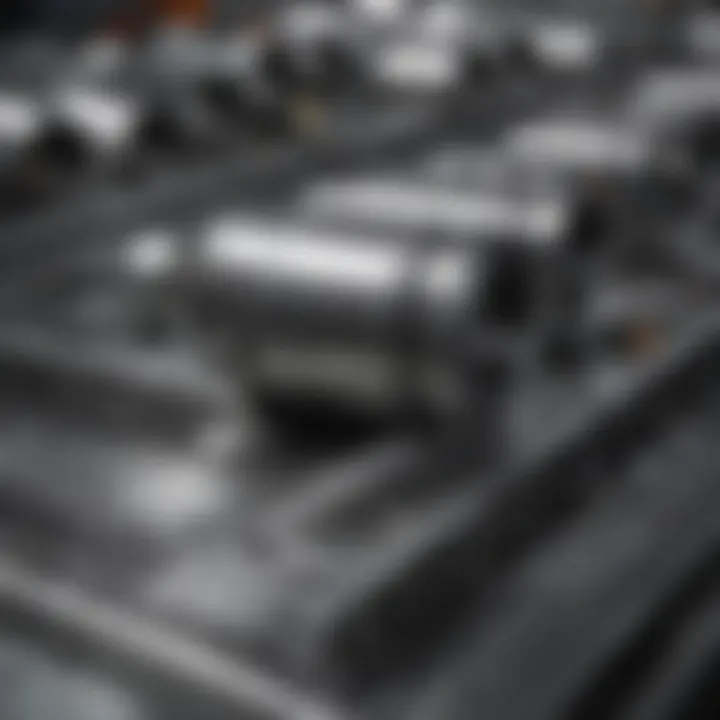
Factors Influencing Coefficient of Thermal Expansion
The coefficient of thermal expansion (CTE) in stainless steel is not static; it is influenced by various elements that warrant thorough examination. Understanding these factors is crucial for engineers, researchers, and designers. They can directly affect material performance in real-world applications, leading to important considerations during design and manufacturing processes.
Alloy Composition
The specific composition of stainless steel alloys plays a significant role in determining their CTE. Stainless steel is primarily composed of iron, but the inclusion of elements such as chromium, nickel, and molybdenum can alter its thermal expansion characteristics. For example, alloys like 304 and 316 stainless steel exhibit different CTE values due to their varying nickel content.
Some key points about how composition influences CTE include:
- Nickel Levels: Increasing nickel generally leads to increased ductility, which may correlate with a higher CTE.
- Chromium Content: Higher chromium may enhance corrosion resistance but could reduce the rate of thermal expansion.
- Other Elements: The presence of elements such as titanium or copper can introduce further variability in thermal expansion behavior.
Additionally, the forms in which these alloys are produced (such as sheets, bars, or tubes) may introduce anomalies in thermal expansion due to residual stresses formed during manufacturing. A comprehensive understanding of alloy composition therefore elucidates the subtleties of how CTE is affected and aids in selecting the right material for specific uses.
Temperature and Environmental Impact
Temperature has a profound impact on the coefficient of thermal expansion. As the temperature increases, most materials expand, including stainless steels. However, the degree of expansion can vary based on temperature ranges and the specific environmental conditions the materials are exposed to.
Factors to consider include:
- Operating Temperatures: Different applications may expose the material to varying temperatures. The thermal expansion behavior of stainless steel can change at elevated temperatures due to phase transformations.
- Environmental Conditions: Corrosive environments can lead to surface changes that may affect thermal expansion. For example, exposure to seawater can alter the surface characteristics of alloys like 316 stainless steel, affecting its CTE.
"Temperature variations can lead to significant stresses in structural applications, necessitating careful engineering to accommodate these changes."
In summary, both alloy composition and environmental conditions play a critical role in influencing the coefficient of thermal expansion in stainless steel. Understanding these factors allows for more informed decisions in material selection and application, ultimately ensuring better performance in engineering applications.
Measurement Techniques for Coefficient of Thermal Expansion
Understanding the coefficient of thermal expansion (CTE) requires precise measurement techniques. These techniques are critical as they directly influence how accurately the CTE of a material can be determined. Accurate measurements ensure that the properties of materials, like stainless steel, can be effectively applied in various engineering domains.
The importance of measurement techniques lies in their ability to provide quantifiable data that guides engineers and designers in their projects. A good understanding of how to measure CTE can prevent failures in structural integrity and enhance material performance under thermal stress. Two widely used methods for measuring CTE are dilatometers and thermal mechanical analysis (TMA). Each technique has unique benefits and considerations that make it suitable for different applications.
Dilatometers
Dilatometers are devices specifically designed to measure dimensional changes in materials as they undergo temperature variations. The principle behind a dilatometer is straightforward: as a material heats up, it expands, and this change in length can be quantified.
Key aspects of dilatometers include:
- High precision: Dilatometers offer excellent sensitivity, allowing for small changes in length to be detected, which is essential for materials with low CTE values.
- Controlled environment: Many dilatometers can operate under controlled conditions, such as a vacuum or inert atmosphere, to minimize external factors that could influence measurements.
- Variety of designs: Different types of dilatometers are available, catering to various experimental needs, including optical and mechanical designs.
One notable advantage of dilatometers is their ability to present continuous data across a range of temperatures. This continuous measurement provides a clear profile of how a material's dimensional properties change with temperature, which is valuable in research and material characterization. However, it's important to note that dilatometers may require careful calibration and setup to ensure accuracy.
Thermal Mechanical Analysis (TMA)
Thermal mechanical analysis is another prominent technique used for measuring CTE. TMA assesses the mechanical properties of materials as they are subjected to heat, recording changes in length and other mechanical parameters. This method can analyze bulk samples as well as films, making it suitable for a wide range of materials.
Features of TMA include:
- Multi-functional analysis: In addition to CTE, TMA can provide data on other thermal properties, including softening points and phase transitions.
- Automated data collection: Modern TMA systems often feature automated data collection and analysis capabilities, which streamline the measurement process, reducing human error.
- Temperature range versatility: TMA can be used over a wider range of temperatures compared to many other techniques, allowing for comprehensive material analysis.
TMA is particularly beneficial when evaluating materials that experience complex thermal behaviors. This complexity makes it crucial for sectors that require precision, such as aerospace and automotive industries.
Accurate measurement of CTE is essential for ensuring the reliability and safety of engineered structures, especially when dealing with materials exposed to varying thermal conditions.
Applications of CTE in Engineering
The coefficient of thermal expansion (CTE) in stainless steel is a critical factor in numerous engineering applications. Its importance cannot be overstated, as it directly impacts structural integrity and device performance in a variety of contexts. Engineering fields ranging from construction to manufacturing are heavily influenced by the behavior of materials when subjected to temperature changes. Understanding how CTE affects these areas is vital for the development of safe and efficient designs.
In practical terms, engineers must consider CTE during the design process. When materials expand or contract due to temperature fluctuations, they can induce stress in structures or components. This stress can lead to material failure, misalignment, or other deterioration. Thus, failing to account for CTE could result in costly repairs or catastrophic failures. Engineers can employ several strategies to mitigate associated risks effectively.
Structural Integrity in Construction
In the realm of construction, the structural integrity of buildings and infrastructure depends significantly on the CTE of materials used. Stainless steel is often favored for its durability and strength, but its response to heat can lead to challenges.
- Seismic Design: In earthquake-prone areas, the expansion of steel can influence how a building behaves under seismic loads. Appropriate CTE considerations in the design phase help distribute stresses evenly, enhancing the structure’s resilience.
- Thermal Bridging: In multi-material assemblies, the differences in CTE between materials can create thermal bridges, leading to energy losses and potential failure points. Engineers must select compatible materials or incorporate design features that minimize these interactions.
- Expansion Joints: To accommodate movement, expansion joints are often designed into structures. Understanding the CTE allows engineers to calculate the required size and placement of these joints, ensuring that they function effectively without compromising the integrity of the structure.
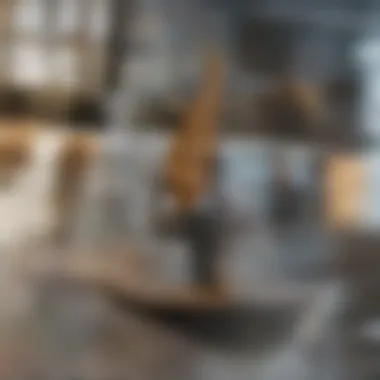
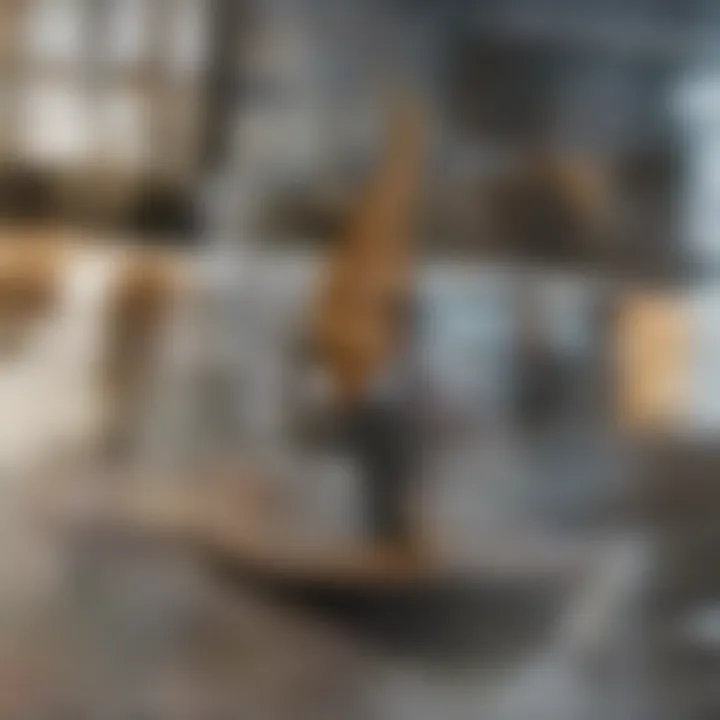
The relationship between CTE and the material's characteristics plays a pivotal role in the safety and longevity of buildings. By understanding these implications, engineers can design more reliable structures that withstand environmental variations.
Machinery and Equipment Design
In the machinery and equipment sector, the CTE of stainless steel is equally crucial. Components that must perform reliably under varying temperatures require careful analysis of the thermal properties.
- Fit and Tolerance: Precision machinery often involves tight tolerances. Variations in temperature can lead to dimensional changes, affecting how parts fit together. Engineers need to design components considering these potential changes to maintain operational efficiency.
- Thermal Cycling: Equipment that undergoes frequent heating and cooling cycles—such as engines or reactors—must have materials that can withstand repeated thermal fluctuations without degrading. The CTE helps engineers predict lifespan and performance stability under such conditions.
- Heat Exchangers: In systems where heat transfer is critical, such as in heat exchangers, understanding the thermal properties of stainless steel aids in optimizing design for maximum efficiency. Proper CTE management allows for better temperature control and energy savings.
Challenges Related to Thermal Expansion
Understanding the challenges related to thermal expansion in stainless steel is crucial for various engineering applications. Thermal expansion can lead to significant variations in dimensions when temperature changes occur. This is especially important in structures and machinery where precision is critical. The behavior of stainless steel under thermal stress can influence not only the lifespan of components but also their performance under operating conditions.
Thermal Stress and Its Consequences
Thermal stress arises when materials are restricted from expanding freely due to temperature changes. In the context of stainless steel, this stress can result in deformation or even fracture in extreme cases. When stainless steel components heat up, they expand. If they are constrained, this leads to internal stresses as the material attempts to accommodate its thermal expansion.
Some consequences of thermal stress include:
- Cracking: This is a serious risk, especially in welds and joint areas where stress concentration is higher.
- Fatigue: Repeated heating and cooling cycles can lead to fatigue failure, which seriously impacts material integrity over time.
- Joint Behavior: When components are assembled, differential expansion can warp connections, which in turn can lead to functional failures.
In many applications, such as in aerospace and automotive industries, where equipment operates in varying thermal environments, addressing thermal stress is vital.
Design Mitigation Strategies
To mitigate the risks associated with thermal expansion and the subsequent thermal stress in stainless steel, several design strategies can be implemented. These strategies are essential in engineering practices to ensure safety and performance stability.
Some effective design mitigation strategies include:
- Expansion Joints: Incorporating expansion joints allows components to move without restraint. This helps absorb movements caused by temperature variations.
- Material Selection: Using alloys with lower coefficients of thermal expansion can reduce thermal stress. Choosing the appropriate stainless steel grade for specific applications is crucial.
- Thermal Insulation: Insulating heated surfaces or components can minimize temperature variations, thus reducing the overall thermal expansion effect.
- Regular Maintenance: Frequent inspections can identify signs of thermal stress early, allowing preventative actions to be taken before failures occur.
Adequate planning for thermal expansion challenges is essential in designing safe and reliable systems, especially in sectors where precision and material behavior are paramount.
Addressing these challenges proactively can preserve structural integrity and enhance the performance of stainless steel components in various applications.
Future Trends in Research on Thermal Expansion
The exploration of thermal expansion extends beyond the classical studies of materials. As industries require more efficient and durable materials, the focus on understanding the coefficient of thermal expansion (CTE) in stainless steel is paramount. This area of research can lead to significant improvements in various applications ranging from construction to manufacturing. The study of future trends in thermal expansion is critical for designing components that withstand temperature fluctuations while retaining structural integrity. Emerging materials and advanced testing methods will shape how engineers approach thermal management.
Nanostructured Materials
Recent advances have introduced nanostructured materials as a potential game-changer in thermal expansion research. These materials, characterized by their unique configurations at the nanoscale, exhibit distinct thermal behaviors compared to traditional materials. The manipulation of their structure allows for tailored thermal expansion properties, which can enhance performance in specific applications. For instance, researchers are investigating how nanoparticles can effectively change the thermal expansion of stainless steel alloys. Such innovations could lead to lighter, stronger, and more thermally stable materials that resist deformation under thermal stress.
The implications of these developments include:
- Greater flexibility in design, allowing for the creation of more complex structures.
- Improved energy efficiency in thermal management systems.
- Enhanced longevity of components subject to thermal cycling.
Advancements in Measurement Techniques
The accuracy of measuring the coefficient of thermal expansion is vital for both research and application purposes. Recent advancements in measurement techniques are facilitating more precise evaluations of thermal expansion. Techniques such as laser interferometry and digital image correlation are proving essential. These methods offer improved resolution, enabling researchers to capture the minute changes in dimensions that occur during thermal exposure. Combining multiple methods could lead to a comprehensive understanding of CTE across various conditions.
Considerations regarding advanced measurement techniques include:
- Enhanced data collection methods that provide real-time insights.
- Integration of artificial intelligence in analyzing measurement data.
- Development of portable technologies for on-site evaluations.
The ongoing evolution of measurement techniques not only enhances research capabilities but also influences industrial standards, ensuring materials can meet increasingly rigorous demands.
As these trends develop, the connection between research and practical application continues to expand. Keeping pace with these advancements is crucial for students, researchers, educators, and professionals keen on optimizing material performance and longevity in engineering.
End
The conclusion of this article summarizes the essential aspects of the coefficient of thermal expansion (CTE) in stainless steel, emphasizing its critical role in engineering and material science. The CTE is a fundamental property that dictates how stainless steel expands or contracts in response to temperature changes. This knowledge is invaluable for applications where temperature fluctuations are common, ensuring structural integrity and reducing the risk of failure in components.
Moreover, understanding the CTE facilitates better design strategies. Engineers can use this information to select appropriate materials, predict performance under operational conditions, and safeguard against thermal stress. The discussion also highlights the variations among different stainless steel alloys, making it clear that a one-size-fits-all approach is inadequate. This calls for careful material selection based on specific application needs and environmental conditions.
As we turn our attention to future research, considerations around advancements in measurement techniques and nanostructured materials are paramount. The impact of ongoing studies will likely lead to more refined engineering practices and innovative applications. Overall, comprehending the thermal expansion of stainless steel is not just about scientific theory; it has real implications in industrial settings, contributing to improved safety, performance, and durability of engineered products.
Summary of Key Points
- The coefficient of thermal expansion is vital for evaluating how materials behave under changing temperatures.
- Stainless steel exhibits a range of CTE values depending on its alloy composition, thus impacting its performance.
- Factors such as alloy composition and temperature significantly influence CTE.
- Measurement techniques like dilatometers and thermal mechanical analysis are crucial for accurately determining CTE values.
- A thorough understanding of CTE is necessary for the design and application of stainless steel in engineering projects.
Implications for Future Research and Application
Further research in the field of thermal expansion can open new avenues. Here are several potential implications:
- Refinement of Measurement Techniques: Improved methods may lead to more precise data on CTE, which is crucial for high-performance applications.
- Exploration of New Materials: The investigation into nanostructured materials could yield even better properties than traditional stainless steel alloys, leading to more efficient designs.
- Application in Emerging Technologies: As new industries emerge, a deeper comprehension of thermal expansion behaviors will assist in the development of innovative solutions.
- Optimization of Existing Processes: Understanding the nuances of CTE allows for the fine-tuning of manufacturing processes and materials selection, enhancing overall product reliability.
In summary, attention to the coefficient of thermal expansion in stainless steel not only helps in achieving immediate engineering goals but also lays the foundation for future technological advancements. This understanding serves as a bridge between current practices and innovative possibilities.