Understanding Low Melting Point Solder in Electronics
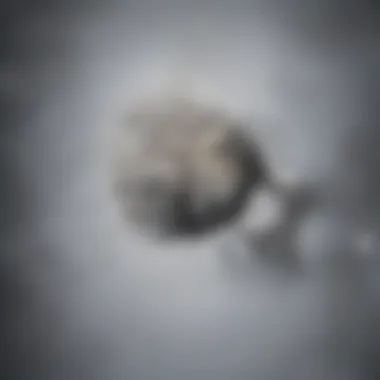
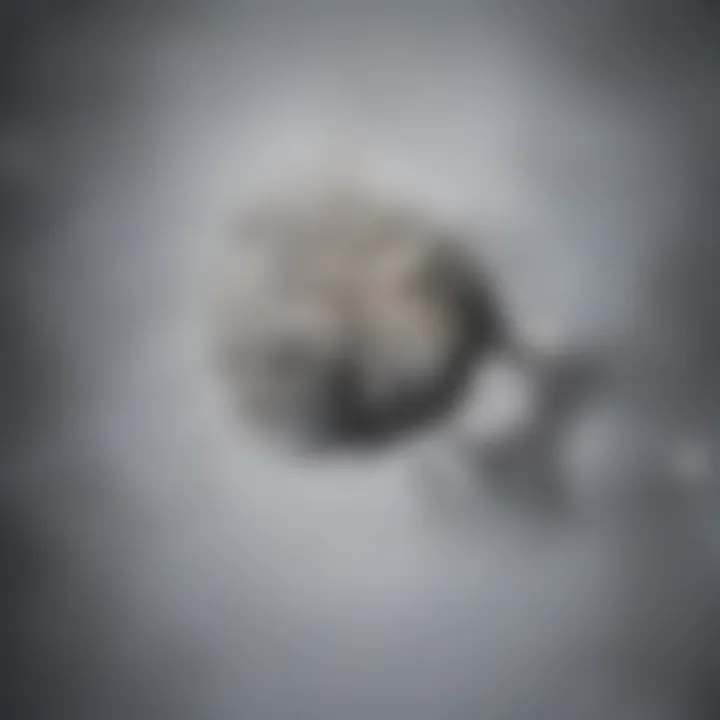
Intro
Low melting point solder plays a crucial role in various industries, particularly in electronics. These solders are specifically designed to melt at lower temperatures, facilitating their usability in sensitive components that may otherwise be damaged by traditional high-temperature soldering methods. This aspect makes them vital for modern manufacturing processes, particularly in the production of compact and intricate electronic devices.
Understanding the properties, manufacturing techniques, and applications of low melting point solder is essential for professionals and researchers in electronics. This article offers a comprehensive breakdown of what makes these solders unique, along with their benefits and drawbacks, thereby providing valuable insights for informed decision-making.
Key Findings
- Chemical Composition: Low melting point solders typically contain tin, lead, bismuth, and indium. Each alloy blends these metals to achieve specific melting points and characteristics.
- Applications: Primarily used in electronics, low melting point solder also finds use in medical devices and automotive components.
- Environmental Concerns: The presence of lead in some low melting point solders raises significant environmental and health issues, leading to the exploration of lead-free alternatives.
- Advantages and Disadvantages: While these solders offer ease of use and lower temperatures during application, their mechanical strength is often lower compared to traditional solders.
Major Results
Low melting point solders exhibit several unique physical properties that make them suitable for various applications. For instance, they provide excellent wetting characteristics on metal surfaces, which is vital for strong mechanical bonds. Furthermore, the ability to melt and solidify at lower temperatures helps prevent damage to sensitive electronic components during assembly.
Discussion of Findings
The findings reveal that while low melting point solders are advantageous, certain limitations must be taken into account. The lower mechanical strength can lead to concerns over long-term reliability, especially in high-stress environments. Moreover, as industries move towards more sustainable practices, the emphasis on finding safer alternatives is becoming increasingly apparent. Understanding these factors is critical for anyone involved in manufacturing or using low melting point solders.
Methodology
Research Design
This article employs a qualitative research design, focusing on literature review and expert interviews to gather pertinent information regarding low melting point solder. This approach allows for a nuanced understanding of the topic, combining theoretical knowledge with practical insights from industry professionals.
Data Collection Methods
Data were collected from diverse sources, including academic journals, industry reports, and reputable online resources. Discussions with professionals in the field offer firsthand accounts of their experiences with low melting point solder, revealing practical considerations that might not be evident in purely theoretical texts.
The integration of varied sources ensures a comprehensive portrayal of low melting point solder, making this article a reliable resource for students, researchers, and professionals seeking in-depth knowledge.
Prelude to Low Melting Point Solder
Low melting point solder has emerged as a crucial material in numerous fields, yet its nuances often require deeper exploration. In the realm of electronics, where the assembly of components demands precision and care, the choice of solder can significantly impact the quality of the final product. Low melting point solder allows for effective joining of parts without exposing sensitive components to excessive temperatures. This characteristic not only preserves the integrity of the components but also enhances overall reliability in applications.
Furthermore, low melting point solder plays a key role in specialized industries such as medical device manufacturing and jewelry making. Understanding its distinctive properties and applications enables professionals to make informed choices during the production process. By optimizing solder selection, one can achieve both improved functionality and adherence to regulatory standards. This article will delve deeper into the elements defining low melting point solder, outlining its chemical composition, manufacturing processes, and critical properties.
Definition and Overview
Low melting point solder refers to an alloy used to create permanent joints between various materials. Typically, these solders have melting points below 300°C. They are mainly composed of a mixture of metals, such as tin and lead, though modern alternatives often replace lead due to health concerns. The primary feature of low melting point solder is its ability to flow smoothly into the joint, ensuring a robust electrical and mechanical bond.
Key terms related to low melting point solder include:
- Alloying: The process of combining different metals to achieve desired properties.
- Fusion Temperature: The specific temperature at which the solder transitions from solid to liquid.
- Wetting: The ability of the molten solder to spread and adhere to surfaces, an important factor for effective bonding.
Historical Context
The development of low melting point solder has evolved significantly over time. In ancient times, artisans primarily used gold and silver for soldering, but these materials were costly and not as effective for everyday uses. By the 19th century, the introduction of tin-lead solder marked a critical turning point. This alloy provided a balance of melting temperature and strength while being more economical.
Over the years, innovation led to the exploration of various other formulations, especially in response to the need for safer alternatives. With the advent of regulations surrounding lead use, solder materials have been reformulated to include lead-free options such as tin-copper and tin-silver. This shift has not only influenced manufacturing techniques but has also sparked ongoing research into performance enhancements for these solders. Understanding this historical context is important for anyone engaged in solder technology today, as it reflects the ongoing challenges and advancements in material science.
Chemical Composition of Low Melting Point Solder
Understanding the chemical composition of low melting point solder is crucial, as it significantly influences the performance, applicability, and reliability of solder joints in various applications. The combination of different alloys determines their melting behavior, thermal properties, and mechanical strength. By analyzing the effectiveness and characteristics of specific alloys, we can design solder materials that cater to specific needs across different industries, particularly electronics.
Common Alloys Used
Low melting point solders often consist of blends of tin, lead, bismuth, and other metals. Each alloy brings specific advantages:
- Tin-Lead (Sn-Pb): This traditional alloy has a melting point typically ranging from 183 to 190 °C. It is well-known for its excellent wetting and mechanical properties, making it a preferred choice for many electronic applications. However, its use is decreasing due to environmental regulations.
- Tin-Bismuth (Sn-Bi): This alternative has a melting point around 138 °C. It is increasingly favored because it is lead-free, providing an environmentally friendly option with decent mechanical strength.
- Tin-Silver-Copper (SAC): This alloy is popular in lead-free applications. Its melting point ranges from 217 to 221 °C, which is higher than some other low melting point solders. Nonetheless, its robust nature makes it suitable in demanding environments.
- Lead-Free Solders: Regulations have shifted many sectors away from lead-based solders, leading to innovations in lead-free options. Alloys such as Tin-Copper (Sn-Cu), are emerging for their beneficial properties in manufacturing processes without harmful lead content.
Elemental Analysis
Elemental analysis of low melting point solders reveals insights about their composition and potential risks associated with certain metals. Common elements in these solders include:
- Tin (Sn): It is the primary component, contributing significantly to the solder's mechanical strength. Tin also aids in excellent electrical conductivity.
- Lead (Pb): Though effective, lead is toxic and poses health risks. As a result, its use is facing regulatory scrutiny globally, necessitating a shift to safer materials.
- Bismuth (Bi): This element is key in creating low melting point alloys. It is less toxic than lead and performs well in lower temperature applications, balancing performance and safety.
- Silver (Ag) and Copper (Cu): These metals are often added to enhance the strength and corrosion resistance of the solder joints. Their presence assures a better mechanical integrity in soldered connections.
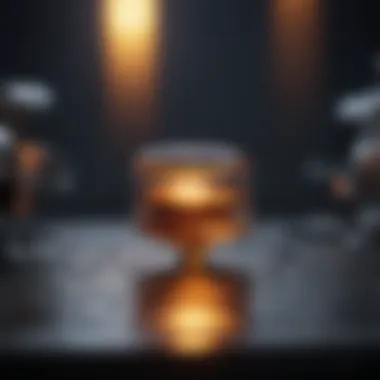
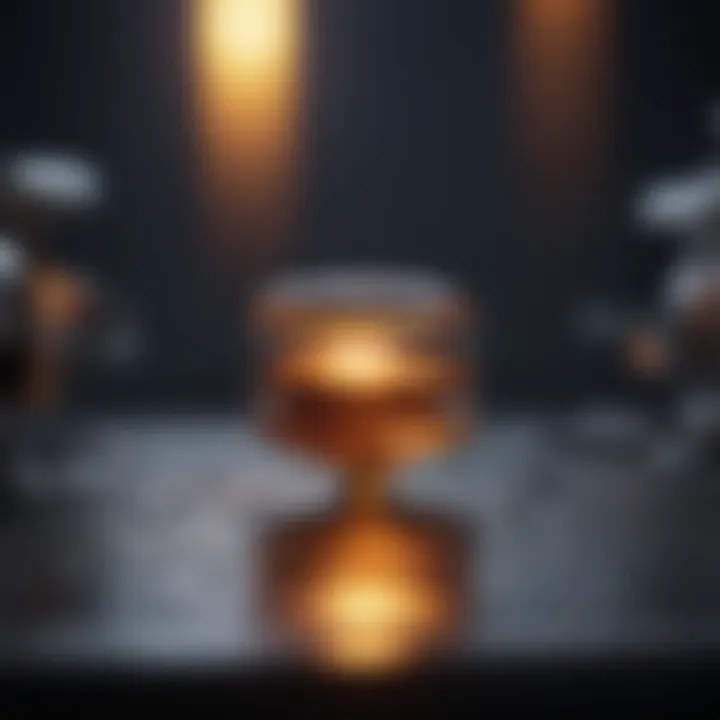
In summary, analyzing the chemical composition of low melting point solder presents essential considerations for addressing quality, environmental impact, and performance across varied applications.
Manufacturing Processes
The manufacturing processes involved in producing low melting point solder are crucial to its performance and application. Proper techniques ensure that the solder meets industry standards and customer requirements, particularly in sensitive fields like electronics and medicine. High-quality production not only guarantees the integrity of the solder but also its effectiveness in various applications.
Production Techniques
The production of low melting point solder mainly involves the careful selection and combination of its constituent materials. The common alloys used, such as those based on bismuth or indium, require precise methodologies to achieve the desired melting points and mechanical properties.
- Melting and Alloying: The process typically begins with melting the base metals. The alloys are heated to a specific temperature where they become liquid. Once melted, different metals are combined to form the targeted solder composition. Control over temperature and time is essential for achieving a uniform mixture.
- Casting and Solidification: After achieving the desired alloy, it is then cast into molds to create solder bars or wires. Rapid cooling techniques may be employed to ensure that the solidification occurs uniformly, affecting the microstructure of the solder. This contributes to its overall performance in applications.
- Forming and Finishing: Once solidified, the solder may need to be processed into various forms such as pellets, wires, or preforms. This can involve drawing, rolling, or cutting. The final product is subjected to surface treatment to enhance its properties, ensuring there are no defects that could affect solderability or corrosion resistance.
- Environmental Considerations: Manufacturers are increasingly considering environmental implications during the production process. Reducing waste, recycling materials, and adhering to regulatory standards are becoming more important. Companies often aim to minimize the use of hazardous substances in their solder, aligning with industry trends toward sustainability.
Quality Control Measures
Quality control measures play a significant role in the manufacturing processes of low melting point solder. Implementing rigorous standards ensures the reliability of the solder, particularly in critical applications.
- Inspection Methods: Various inspection techniques are utilized throughout the production stages. This can range from visual inspections to using advanced technologies such as X-ray to identify internal flaws.
- Testing Properties: The mechanical properties, like tensile strength and ductility, are routinely tested against specified benchmarks. The solder must perform adequately under the conditions it is meant for, especially in electronics where failure can mean significant economic loss and safety concerns.
- Batch Consistency: It's vital to maintain consistency across batches to ensure that the solder performs the same way every time. Monitoring parameters during production helps in identifying any variations that might compromise this consistency.
- Documentation and Traceability: Keeping thorough documentation of production processes, material sourcing, and quality tests is essential. This traceability ensures accountability and aids in addressing any issues that arise after solder is deployed in real-world applications.
Key Consideration: Effective manufacturing processes in producing low melting point solder not only enhance its performance but also influence the sustainability and safety of the end products.
Physical Properties of Low Melting Point Solder
The physical properties of low melting point solder are essential to understand not only for technical applications but also for design considerations in manufacturing processes. Knowledge of these properties helps engineers and manufacturers choose the right solder for specific applications, ensuring that their final products perform well and meet industry standards. In this section, we will delve into the melting point range, thermal conductivity, and mechanical properties of low melting point solder, highlighting their significance.
Melting Point Range
The melting point range is one of the most defining characteristics of low melting point solder. This property determines the temperature at which the solder transitions from solid to liquid, influencing its application in various fields. Typical low melting point solders include those based on lead, tin, bismuth, and indium.
For example, solders made from tin-bismuth alloys generally melt between 138-180°C, while indium-based solders can melt at even lower temperatures. The lower the melting point, the less heat is needed for soldering, which is particularly advantageous when working with temperature-sensitive components. This can prevent damage to delicate electronics and other materials that could be adversely affected by high temperatures.
"The melting point of solder plays a critical role in ensuring product integrity and functionality."
Thermal Conductivity
Thermal conductivity is another important aspect of low melting point solders. This property dictates how heat is transferred through the material during the soldering process. High thermal conductivity allows for efficient heat distribution, which can significantly enhance the quality of solder joints. The ideal low melting point solder will not only melt quickly but will also facilitate rapid heat transfer to the surrounding components.
Typically, lead-based solders exhibit superior thermal conductivity compared to other alloys. However, lead-free solders have made considerable advancements, and some can provide comparable performance. It is vital to choose a solder with appropriate thermal conductivity to avoid cold solder joints, which can lead to electrical failures.
Mechanical Properties
The mechanical properties of low melting point solder relate to its strength, ductility, and reliability after soldering. These properties are crucial because they affect how well the solder performs under stress or thermal cycling. Low melting point solders tend to have lower mechanical strength compared to standard solders like those based on lead-tin alloys. This can lead to challenges in applications subject to significant mechanical stress.
Moreover, flexibility is an important factor. A ductile solder can absorb stress without cracking, making it suitable for dynamic applications. Designers must consider these properties to ensure longevity and reliability in various conditions.
In summary, understanding the physical properties of low melting point solder—specifically the melting point range, thermal conductivity, and mechanical properties—enables better decision-making for applications. This knowledge assists in selecting suitable solders for specific tasks while optimizing performance and ensuring product longevity.
Applications of Low Melting Point Solder
Low melting point solder plays a crucial role in various industries, especially in applications where precision and sensitivity are paramount. Its unique properties make it suitable for tasks that involve delicate components, thereby helping to improve efficiency and reduce energy consumption. Understanding its applications provides key insights into why low melting point solder is favored in electronics manufacturing, medical device assembly, and crafts like jewelry making.
Electronics Manufacturing
The electronics industry heavily relies on low melting point solder due to its ability to minimize the risk of thermal damage to sensitive electronic components. The use of solders like indium-based alloys allows for solid connections while exposing items to lower temperatures during the soldering process. This is essential when assembling intricate devices like smartphones and tablets, where components are densely packed and heat sensitivity is a significant concern.
Additionally, the low energy requirements of these solders contribute to more environmentally friendly manufacturing processes. The integration of low melting point solder can enhance workflow by reducing the time needed for soldering operations, which is essential in high-volume production environments.
"Low melting point solder is vital for constructing compact electronic devices without compromising integrity."
Key Benefits:
- Reduces thermal stress on components.
- Increases manufacturing efficiency.
- Offers a range of compatible materials.
Medical Device Assembly
In the medical sector, low melting point solder is particularly valuable. Medical devices often incorporate delicate sensors and circuits that require reliable connections without the risk of overheating. For example, surgical tools or diagnostic equipment often utilize these solders to ensure longevity and functionality.
A significant advantage in this area is the compatibility of low melting point solder with biocompatible materials. This ensures that devices can meet strict safety standards and do not introduce harmful substances into the body. Moreover, the precise nature of these solders allows for miniaturization in medical technology, enabling the development of smaller, more effective devices.
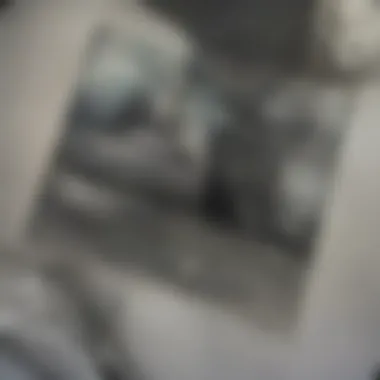
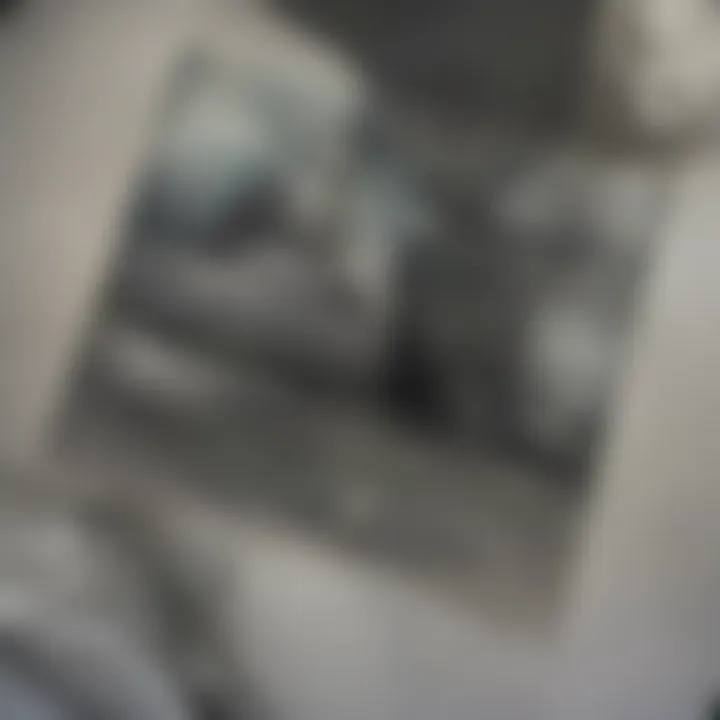
Main Considerations:
- Adherence to strict medical standards.
- Need for biocompatibility for patient safety.
Jewelry and Crafts
Low melting point solder is also popular in the realm of jewelry making and crafts. Artisans value it because it allows them to join metals with precision and minimal heating. This is particularly important for intricate designs where overheating can distort metal shapes and affect the final product.
Using solders with lower melting points enables jewelers to work with a variety of materials, creating compositions that highlight custom artistry. The ease of use and versatility offered by these solders allows for more creative applications and helps to achieve refined details in handmade jewelry.
Advantages:
- Facilitates detailed work without damaging materials.
- Expands creative possibilities for artisans.
Advantages of Low Melting Point Solder
Low melting point solders offer various advantages that cater to the needs of modern manufacturing and assembly processes. Understanding these benefits is crucial, especially in industries where precision and care are paramount.
One of the primary advantages is the lower energy requirements during soldering. This effect not only reduces operational costs but also minimizes thermal stress on sensitive components.
Lower Energy Requirements
The use of low melting point solder significantly mitigates the energy required to melt solder. Typical solders have higher melting points, which necessitate stronger heating equipment and larger energy consumption. With low melting point solders, the process requires much less thermal output. For instance, solders containing bismuth can melt at temperatures as low as 138 degrees Celsius, compared to traditional lead-based solders that may require over 200 degrees Celsius.
This reduction in energy directly translates to:
- Cost savings on electricity
- Less wear and tear on equipment
- Lower cooling times after soldering, which enhances overall efficiency
Furthermore, the reduced heating is beneficial in applications involving heat-sensitive components, preventing possible damage during assembly.
Compatibility with Sensitive Components
Low melting point solder is particularly valuable in sensitive electronic applications. Many modern devices incorporate components that are easily susceptible to heat. The delicate nature of these assemblies requires a careful approach to soldering. By using low melting point solder, manufacturers can avoid the risk of damaging components like integrated circuits and surface mount devices.
Key points regarding compatibility include:
- Minimized Risk of Damage: Lower processing temperatures reduce the chances of heat-induced failures.
- Preservation of Material Integrity: Components such as capacitors and sensors maintain their functional properties without the adverse effects of excessive heat.
- Enhanced Reliability: Solder joints are formed under conditions that do not compromise the mechanical or electrical specifications of the parts being joined.
Using low melting point solder, especially in sectors like electronics manufacturing, aerospace, and medical device assembly, ensures that the integrity of the components remains intact.
"Low melting point solders serve not just as a functional medium for joining materials, but also as a protective barrier against heat damage during soldering operations."
Disadvantages and Limitations
Understanding the disadvantages and limitations of low melting point solder is crucial for making informed decisions in its applications. These challenges can impact the performance and longevity of products that utilize this type of solder. While low melting point solder has its advantages, such as lower energy requirements and compatibility with sensitive components, it is also important to consider aspects that may hinder its effectiveness in certain scenarios.
Mechanical Strength Issues
One of the primary drawbacks of low melting point solder is its mechanical strength. Unlike higher melting point solders, which can offer robust joints, low melting point solders tend to be weaker. This reduced strength makes them more susceptible to mechanical stress, impacts, and fatigue over time. Products assembled with low melting point solder may face issues during regular use, especially in environments where vibrations or thermal cycles are common.
When engineers or manufacturers choose low melting point solder, they must account for the potential for joint failures, especially in critical applications such as aerospace or automotive industries. The reduced mechanical strength of these solders can lead to costly failures and safety risks.
Temperature Sensitivity
Another significant limitation concerns the temperature sensitivity of low melting point solder. These solders have a lower melting point, which is advantageous during the soldering process. However, it also means that they can reflow at relatively low temperatures. This sensitivity poses risks when the assembled components are exposed to elevated temperatures during operation or in environments where heat is a factor.
For instance, in electronics, a low melting point solder joint might weaken due to heat generated from nearby components or environmental conditions. This can compromise the integrity of the circuitry, leading to malfunctions. Therefore, careful consideration is necessary in applications where exposure to heat is likely.
"Understanding the mechanical strength and temperature sensitivity of low melting point solders is essential for ensuring reliability in applications."
Environmental Concerns and Regulations
Understanding the environmental concerns and regulations surrounding low melting point solder is crucial, especially given the increased focus on sustainability within industries. This section aims to outline the potential environmental impact of such solders, and the relevant regulations designed to mitigate these risks.
Toxicity of Components
Low melting point solders often contain several toxic elements, particularly lead. Lead exposure can have serious health effects, especially regarding the nervous system, and it can be harmful even in small quantities. The potential for leaching of lead into the environment during use or disposal highlights the significant risks associated with these materials.
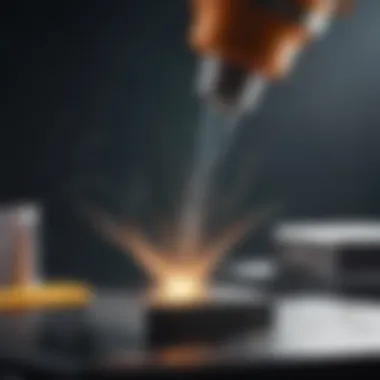
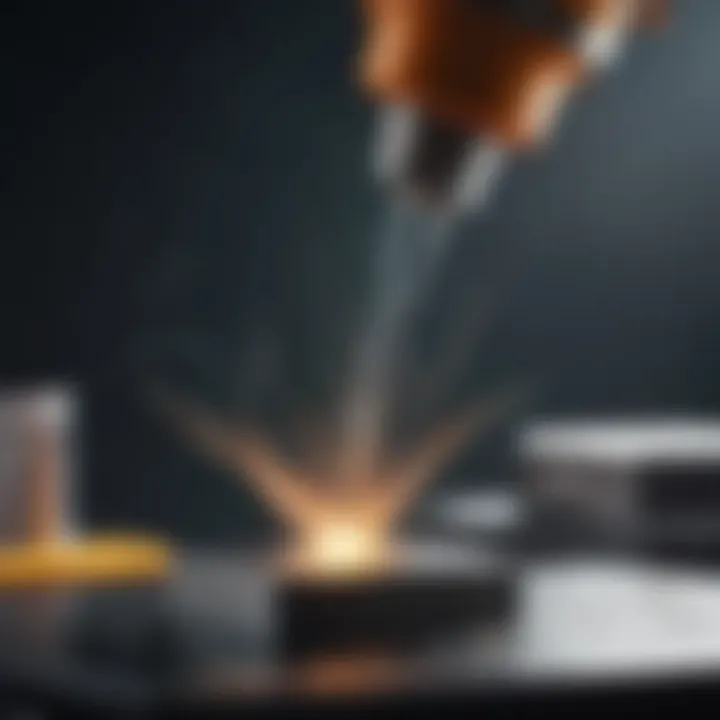
In addition to lead, other materials used in low melting point solders, such as cadmium or certain flux agents, may also present hazards. Cadmium is known for its toxicity and can cause damage to the kidneys and fragile bones. When selecting soldering materials, it is essential to understand the toxicity of each component. The risks of exposure must be minimized to protect both workers and consumers.
Compliance with Environmental Standards
As awareness of environmental issues rises, so do the regulations dictating the use of hazardous materials in manufacturing. Various international and national standards guide how electronic and other sectors can use low melting point solder.
In the European Union, for instance, the Restriction of Hazardous Substances Directive (RoHS) prohibits the use of lead in electrical and electronic equipment. Compliance with such regulations is not merely a legal requirement; it reflects a commitment to corporate responsibility and environmental stewardship.
Therefore, industries must evaluate their solder choices seriously, opting for alternatives when possible. The implementation of these environmental standards ensures that hazardous substances are phased out, promoting safer practices. It is also noteworthy that adhering to these standards can enhance the overall marketability of products, as consumers increasingly prefer eco-friendly options.
"Solder selection should not just prioritize performance but also consider environmental footprint."
Alternatives to Low Melting Point Solder
As the demand for high-quality soldering solutions grows, the exploration of alternatives to low melting point solder becomes vital. Understanding these alternatives involves assessing their properties, applications, and the considerations that guide their use in various industries. This section will outline the primary options available, providing insights into their suitability for different tasks.
Lead-based Solders
Lead-based solders have been widely adopted due to their favorable properties. This type of solder typically contains a mixture of lead and tin, with the addition of small amounts of other metals to enhance performance.
The main advantages of lead-based solders include:
- Melting Point: Lead-based solders have a higher melting point compared to low melting point solders, which can offer better mechanical integrity in some applications.
- Workability: They are often easier to work with when obtain high-quality joints and minimize the risk of defects.
- Cost-Effectiveness: These solders tend to be less expensive than alternatives, making them an attractive option for large-scale production.
However, there are significant health and environmental concerns associated with lead-based solders. Lead is a toxic substance. Exposure during manufacturing or disposal can cause serious health issues. As a result, many regulations have been established, limiting or banning the use of lead-based solders in specific applications.
Lead-free Solders
Lead-free solders have emerged as a prominent alternative, primarily driven by regulatory pressures and growing environmental awareness. These solders typically utilize a variety of elements such as tin, silver, and copper, which work together to provide desirable soldering characteristics.
Advantages of lead-free solders include:
- Regulatory Compliance: They meet the stringent requirements set forth by directives such as the European Union’s RoHS. This helps manufacturers comply with global standards aimed at reducing hazardous materials.
- Enhanced Safety: Lead-free solders eliminate the risk of lead toxicity, making them safer for workers and consumers alike.
- Improved Thermal Resistance: Many lead-free options exhibit superior thermal characteristics, which can be beneficial in high-temperature applications.
Despite these benefits, the switch to lead-free soldering is not without challenges. Lead-free solders generally have a higher melting point than traditional lead-based options. This can lead to issues when soldering sensitive electronic components. Additionally, some lead-free alloys can be more brittle, which might affect the mechanical strength of the joints.
"As industries evolve, the transition to lead-free solder is not just a requirement; it represents a commitment to innovation and safety in manufacturing."
Future Trends in Solder Technology
The area of solder technology is evolving. As industries demand higher performance and better sustainability, solder materials and techniques are being refined. This section looks at advancements that shape the future of low melting point solder.
Advancements in Material Science
Material science plays a pivotal role in the development of new solder formulations. Researchers are focused on creating solders that not only perform well but also minimize environmental impact. New alloys are emerging, designed to withstand demanding conditions while offering lower melting points. These advanced materials are key for improving manufacturing processes, reducing energy consumption, and enhancing product reliability.
A trend in material science is the integration of metallic and non-metallic components. For instance, biocompatible materials are becoming more relevant in medical devices. These new solder compositions ensure safety while maintaining effective bonding strength. Furthermore, ongoing studies are exploring the use of nanoparticles in solder, which can provide enhanced thermal and mechanical properties.
Innovations in Soldering Techniques
Techniques in soldering are also advancing. New approaches, like selective soldering and laser soldering, have gained traction. Selective soldering provides efficiency by targeting only specific components, thus conserving materials and reducing waste. Laser soldering offers precision; it uses energy tightly focused on a small area. This method is particularly useful in delicate assemblies where traditional methods might cause damage.
Moreover, automation is transforming soldering processes. Robotic systems are being deployed to ensure consistent quality and reduce human error. Automation also allows for greater scalability, making it easier to adapt to varying production needs.
"The future of solder technology lies in the intersection of innovative materials and advanced application techniques."
By combining these approaches, industries can expect to see significant improvements in the performance and longevity of solder joints. As challenges like miniaturization and thermal management persist, these advancements will become essential in maintaining reliability in various applications.
The End
In this article, we have examined low melting point solder in depth, which is crucial for various industrial applications, especially in electronics. The conclusion synthesizes the knowledge covered and emphasizes the significance of understanding its properties and usages. Low melting point solder serves as a reliable solution for joining components without the risk of damaging heat-sensitive parts. It allows for cost-effective manufacturing processes, reducing energy consumption and increasing efficiency.
Summary of Key Points
- Definition: Low melting point solder is a specialized alloy designed to melt at lower temperatures.
- Chemical Composition: Common alloys included tin, bismuth, and lead-free variants.
- Applications: This solder is widely used in electronics, medical devices, and jewelry production.
- Advantages: It offers lower energy requirements and is compatible with sensitive components.
- Disadvantages: Challenges include potential mechanical strength issues and temperature sensitivity.
- Environmental Concerns: Certain components carry toxicity risks, prompting regulatory compliance.
- Alternatives: Options include both lead-based and lead-free solders.
- Future Trends: Innovations in material science continue to shape soldering technology.
These points illustrate the evolving landscape of low melting point solder and its essential role in modern manufacturing.
Final Thoughts
As technology progresses, understanding low melting point solder becomes increasingly important. Its unique properties and applications make it indispensable in fields where precision and care are paramount. The ongoing research into materials and methodologies suggests that low melting point solder will remain integral in electronics and other industries. Continuous advancements will likely lead to better performance and environmental safety.
This knowledge does not just serve academic purposes. It equips professionals and researchers with the insights needed to make informed decisions on soldering materials. To sum up, a thorough grasp of low melting point solder and its implications can lead to improved practices and innovations in the industry, ensuring progress without compromising safety or efficiency.