Understanding Injection Moulding: A Comprehensive Guide
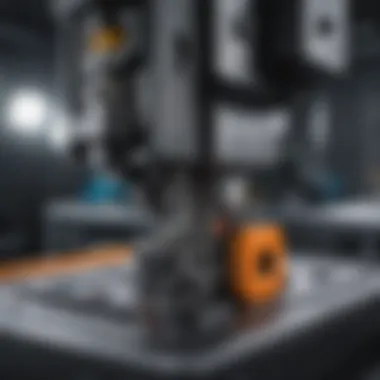
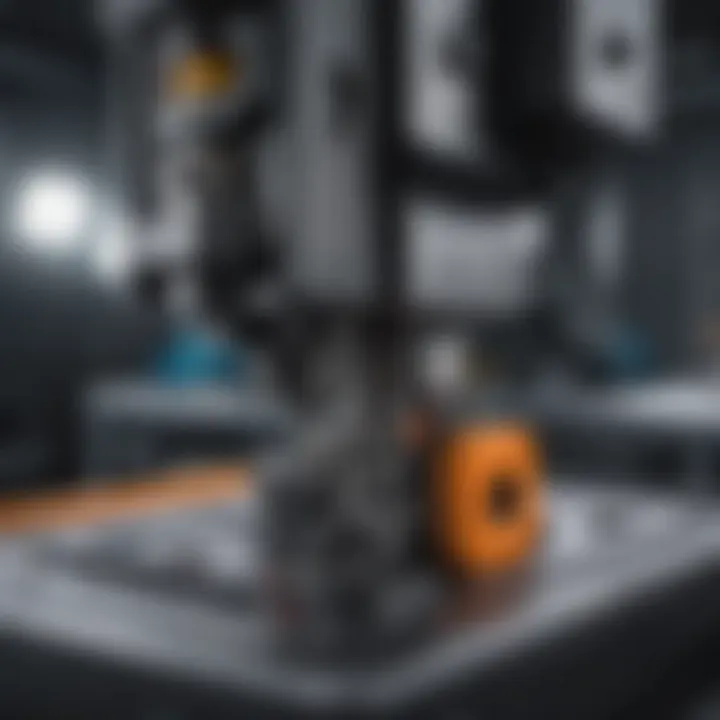
Intro
Injection moulding is a key process in modern manufacturing, predominantly for creating plastic products. Understanding this method entails not just its workflow but also the materials, designs, and the overall impact it holds on production and the industry. This document aims to breakdown the critical aspects of injection moulding to facilitate a comprehensive grasp for students, researchers, and professionals alike.
The injection moulding process involves heating thermoplastic substances until they are malleable, then injecting them into a mould where they solidify. This method enables mass production with precision. Its ability to create a variety of shapes efficiently has made it a popular choice in numerous industries including automotive, consumer goods, and healthcare.
The significance of this guide is rooted in its detailed exploration of the injection moulding process along with its benefits and limitations. Understanding these factors is crucial not only for those directly involved in engineering and manufacturing but also for stakeholders and decision-makers who rely on informed insights to drive production strategies.
A detailed look into the applications and advancements in technology will be provided, thus equipping readers with the knowledge needed to navigate the complexities of injection moulding.
Intro to Injection Moulding
Injection moulding plays a crucial role in modern manufacturing. It is a highly efficient method used to produce a wide range of plastic products, from everyday items to components for complex machinery. By understanding this process, clients can optimize production runs and enhance product quality.
Definition of Injection Moulding
Injection moulding is a manufacturing process where molten material, usually plastic, is injected into a mould. The heated plastic is forced into a tightly closed cavity, allowing it to take the shape of the mould. Once cooled, the mould is opened to release the solidified product. This process is highly versatile and can produce both simple and intricate shapes with precision and consistency.
History and Development
The history of injection moulding can be traced back to the early 19th century. Initially, it was done by hand using simple tools. However, significant advancements occurred in the 20th century with the invention of automatic machines. In the 1940s, the first fully automated injection moulding machine was developed. This innovation revolutionized the industry, allowing for mass production and significantly reducing costs. Today, injection moulding has evolved with technologies like computer-aided design, which enhances accuracy and efficiency.
Importance in Manufacturing
Injection moulding is fundamental in various industries, including automotive, healthcare, and consumer goods. Its importance cannot be understated:
- High Production Efficiency: It allows for rapid production, which is vital in meeting market demands.
- Material Usage: This process minimizes waste, making it environmentally friendly.
- Accuracy and Consistency: Parts produced are highly uniform, which is essential for large-scale production.
Understanding injection moulding opens doors to better product design and optimization in manufacturing.
A comprehensive look at injection moulding helps illustrate its significance in shaping modern industrial processes.
The Injection Moulding Process
The injection moulding process is crucial in modern manufacturing, especially for high-volume production of plastic products. Understanding this process helps clarify how different elements work together to create efficient and precise moulding. Various steps ensure that quality is maintained while meeting production demands. This section explains the detailed steps involved in the process along with the functions of critical machinery components.
Overview of the Process Steps
Clamping
Clamping is the first step in the injection moulding process. It involves securing the mould halves together to prevent any material leakage during injection. This step is essential because it sets the stage for the accuracy and quality of the finished product. A key characteristic of clamping is the ability to exert substantial force, which is vital for ensuring precision.
A hydraulic system is often used for clamping, and its robust capability makes it a popular choice. Its unique feature is the adjustable force, allowing it to accommodate different mould sizes and shapes. The advantages include consistent pressure and reliable operation, although its disadvantages can be higher energy consumption and maintenance costs.
Injection
Injection is where the actual moulding happens. Melted plastic is injected into the mould under high pressure. This step is significant as it defines the shape and characteristics of the final product. A notable characteristic of injection is its speed; it allows for rapid production cycles.
The injection unit typically employs a screw mechanism, which provides effective mixing and temperature control of the plastic. This unit is beneficial as it can handle various types of materials. A unique feature is its capability to adjust the injection speed and pressure, helping to minimize defects like air traps or sink marks. The challenges in this step include the need for precise temperature control and the potential for material degradation at high temperatures.
Cooling
Cooling is a vital phase where the injected plastic is allowed to solidify. This step directly influences the dimensional accuracy and surface quality of the final product. The cooling time must be optimized to balance efficiency and quality. A key characteristic is the use of temperature-controlled cooling channels, which help maintain uniform cooling across the mould.
Efficient cooling systems, like water or chillers, make this step beneficial by reducing cycle times. The unique feature is that enhanced cooling methods can lead to better surface finish and reduced warping. However, one disadvantage is the risk of thermal stresses if the temperature is not controlled carefully.
Ejection
Ejection is the final step, where the solidified part is removed from the mould. This step is crucial for ensuring that the production cycle can restart quickly. A main characteristic of ejection systems is the use of ejector pins that push the part out without damaging it.
Ejection systems are essential because they allow for quick and efficient removal of components. Their unique feature is the ability to operate automatically, which reduces manual labor. However, some disadvantages include the risk of damaging complex shapes, requiring careful design of the ejector mechanism.
Key Machinery Components
Understanding the machinery components in injection moulding helps to comprehend its efficiency and versatility in the production process. Each component plays a specific role that contributes to the overall functionality of the system.
Injection Unit
The injection unit is responsible for melting and injecting the plastic material into the mould. It comprises a hopper, screw, and barrel. This unit's importance lies in its ability to provide consistent melt quality and injection pressure. A key characteristic is its design, allowing for effective mixing and homogenous melt.
The injection unit's unique feature is its versatility; it can be adapted for various materials and applications. The advantages include high precision and control, while challenges can arise, such as wear and tear of screw components over time.
Clamping Unit
The clamping unit holds the mould in place during injection. It ensures the mould halves are securely closed to prevent any leakage. A crucial aspect of this unit is its clamping force, which must be calibrated according to the thickness of the moulding material.
The key characteristic of the clamping unit is its strength, with some models using servo motors for better efficiency. Its unique feature is the capability to handle large mould sizes. However, higher initial costs for advanced clamping systems can be a consideration.
Control Systems
Control systems manage all stages of the injection moulding process. They monitor parameters like temperature, pressure, and timing, ensuring that mold quality is consistently maintained. A crucial aspect is their ability to provide real-time feedback and automation.
These systems are especially beneficial as they enhance productivity and reduce human error. A unique feature is the integration of software that can track production data. However, one potential disadvantage is the complexity of maintenance and operation, requiring trained personnel.
Material Feeding Mechanism
The material feeding mechanism ensures a steady supply of plastic granules to the injection unit. The feeding system's importance is evident in its role in maintaining consistency during the injection phase. Various types of hoppers are used, such as gravity or volumetric feeders, depending on the desired process control.
A key characteristic of efficient feeding systems is their design to minimize material waste and ensure accurate dosing. The unique feature is the potential for automatic feeding systems, which enhance productivity. While the advantages include reduced manual labor, disadvantages can include the initial high cost of automated systems.
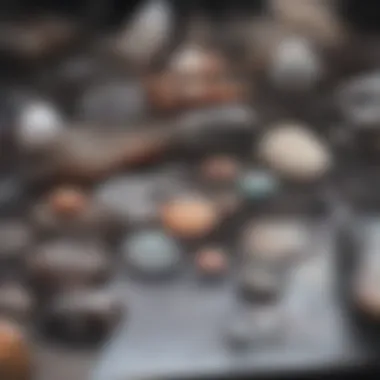
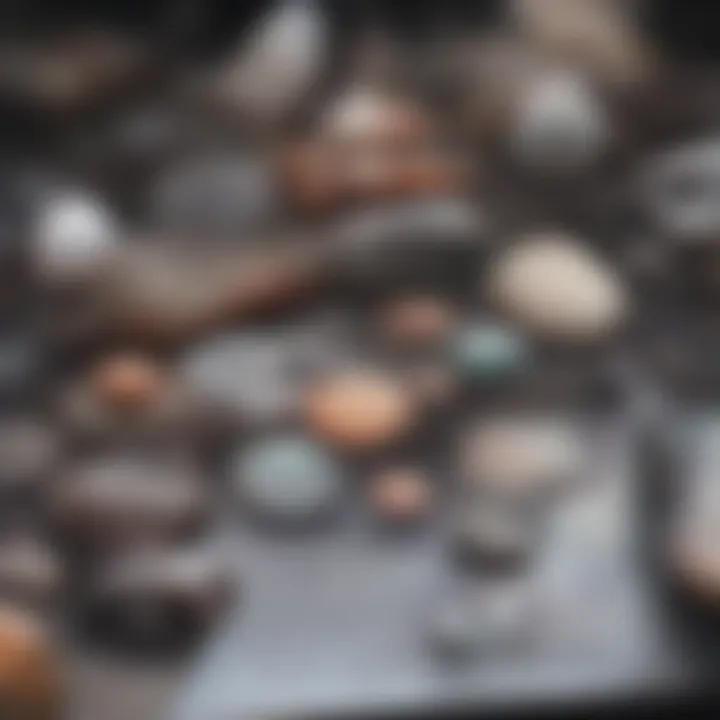
Materials Used in Injection Moulding
Injection moulding relies heavily on the choice of materials, as they significantly influence the final properties of the products. The materials used not only determine the functionality of the end products but also impact the production efficiency and costs. Understanding these materials is vital for selecting the right ones for specific applications.
Types of Plastics
Thermoplastics
Thermoplastics are a prominent category in injection moulding. Their defining characteristic is that they become soft when heated and harden upon cooling. This reversible nature allows for reshaping and reprocessing, making thermoplastics a popular choice for many applications. Their ease of processing contributes to the speed and cost-effectiveness of production.
One unique feature of thermoplastics is their ability to be remoulded without significant chemical change. This ensures less waste and greater resource efficiency. Common types include polyethylene, polypropylene, and polystyrene. These plastics are widely used in consumer goods and packaging due to their impact resistance and lightweight properties.
Advantages of thermoplastics include:
- Recyclability
- Ease of processing
- Wide range of applications
Disadvantages, however, can be:
- Limited thermal resistance compared to some thermosetting plastics
- Potential for warping at higher temperatures.
Thermosetting Plastics
Thermosetting plastics represent another critical category in the materials used for injection moulding. Unlike thermoplastics, these materials undergo a chemical change when heated. Once set, thermosetting plastics cannot be remoulded or reshaped. This robust characteristic makes them particularly suitable for applications requiring high dimensional stability and structural integrity.
Key examples include epoxy resin and phenolic plastics, often used in automotive and electrical applications. Their unique feature is the strong bonding achieved during the curing process, resulting in excellent thermal and chemical resistance.
Advantages of thermosetting plastics include:
- High strength and durability
- Excellent thermal stability
On the downside:
- Irreversible once set, limiting flexibility in manufacturing
- More complex processing requirements.
Additives and Fillers
The use of additives and fillers enhances the properties of base materials, allowing for tailored performance in specific applications. Additives can provide benefits such as UV resistance, flame retardancy, or improved flow characteristics. Fillers, like talc and calcium carbonate, increase strength and reduce costs without significantly affecting the product's properties. Understanding the implications of using these materials is essential for successful moulding.
Material Selection Criteria
Choosing the right material for injection moulding involves several critical factors. Considerations include:
- Mechanical properties: Strength, flexibility, and impact resistance required.
- Thermal properties: Resistance to heat and thermal expansion.
- Chemical compatibility: Resistance to various chemicals it may be exposed to.
- Cost-effectiveness: Balancing the desired properties with material costs.
- Environmental impact: Considering sustainability practices such as recyclability and carbon footprint.
Each of these criteria plays an integral role in achieving the desired functionality and longevity of the final product. The right choice can lead to significant advantages in production and use.
Design Considerations in Injection Moulding
Understanding design considerations is vital in the process of injection moulding. The design phase determines how effective and efficient the injection moulding will be. Proper design minimizes waste, ensures product quality, and reduces costs. Every component, from the mould itself to the parts being produced, requires careful thought to optimize performance and manufacturability.
In this section, we will discuss the fundamentals of mould design, part design guidelines, and factors promoting manufacturability. Each of these elements plays a pivotal role in ensuring that the final products meet specifications, are cost-effective, and function as intended.
Mould Design Fundamentals
The mould is the heart of the injection moulding process. The design of the mould needs to accommodate the desired shape and features of the part while also allowing for efficient production cycles. Key considerations include material selection, thermal characteristics, and ease of maintenance. Moulds are often constructed of steel or aluminum, each having its pros and cons in terms of durability and cost.
It is crucial for the mould to have the right balance between strength and heat resistance to withstand high-temperature processes. Understanding the thermal expansion and contraction of both the mould and the plastic will greatly affect the quality of the end product. Careful mould design will ultimately enhance productivity and reduce defects.
Part Design Guidelines
Good part design greatly influences the success of the moulding process. Specifically, designers need to consider the following:
Thickness
Thickness impacts many aspects of injection moulding. An optimal wall thickness allows for even cooling and reduces the risk of defects such as warping or sink marks. Generally, thinner walls favor quicker cycles but can compromise strength. A consistent thickness across a part minimizes stress concentrations, thus improving the mechanical integrity.
Key characteristics include:
- Even heat distribution
- Reduction of cooling time
- Overall strength balance
People often prefer consistent wall thickness for a good reason; it improves flow and decreases likelihood of defects like short shots, which occur when not enough material is injected into the mould.
Draft Angles
Draft angles are essential for easy ejection of parts from the mould. These angles are small slopes that facilitate the removal of parts without causing damage. Without adequate draft, parts may stick to the mould and lead to surface imperfections or even breakage.
Improvements from draft angles include:
- Reduced friction
- Lower cycle times
- Minimization of wear on moulds
Typically, a draft angle of at least 1-2 degrees is recommended to ensure effective ejection conditions. This angle should be consistent across the mould to maintain product uniformity.
Radii
Radii refer to the rounded corners featured in part designs. These help to transition between surfaces and enhance flow of the molten plastic during injection. A well-designed radius can contribute to both aesthetics and functionality of the final product.
Benefits of incorporating radii include:
- Decreased stress points
- Improved aesthetics
- Better material flow during injection
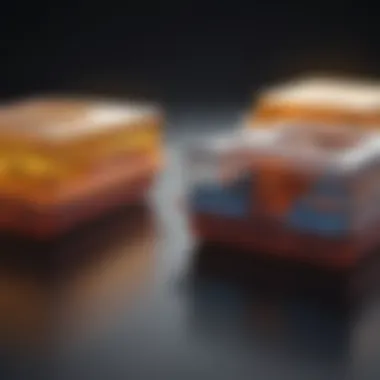
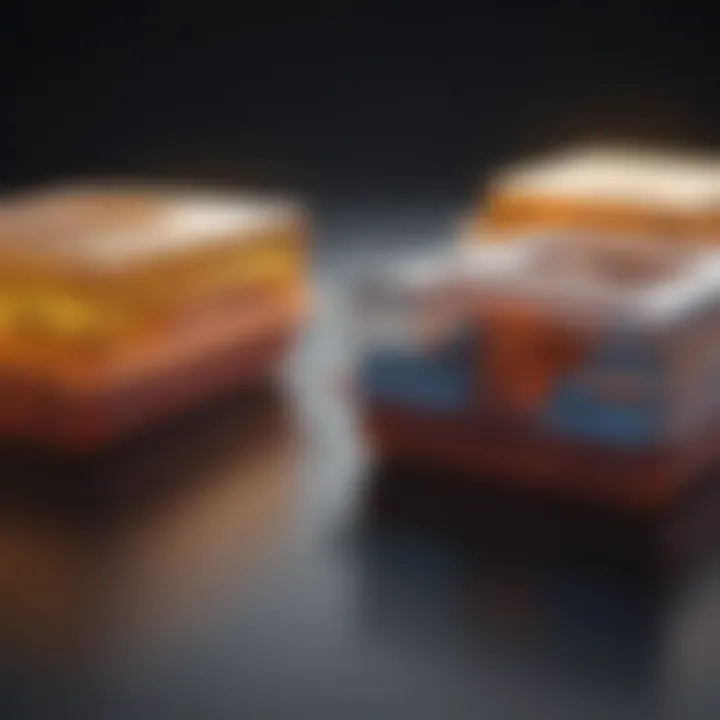
Radii also help avoid issues like stress concentration that can lead to part failure. Designers should choose radii carefully to balance manufacturing constraints and functional requirements.
Design for Manufacturability
Design for manufacturability (DFM) aligns product design with manufacturing processes. It encourages collaboration between design engineers and production teams to optimize designs for efficacy and efficiency. Key strategies include the reduction of component count, standardizing parts, and simplifying assembly. DFM principles significantly reduce production costs and improve time-to-market.
Ultimately, integrating design considerations during the early phases of injection moulding can lead to producing high-quality, cost-effective products that are easier to manufacture and assemble.
Applications of Injection Moulding
Injection moulding is a cornerstone of modern manufacturing. Its versatility allows it to be applied across various industries to produce a wide range of products. Understanding the applications of injection moulding is essential for grasping its significance in manufacturing processes. This section will explore different sectors where injection moulding excels, focusing on consumer products, automotive components, and medical devices.
Consumer Products
The consumer market benefits greatly from injection moulding. Everyday items, such as containers, toys, and household appliances, are predominantly made using this method. The advantages of injection moulding in producing user-friendly and aesthetically pleasing products are substantial. It provides:
- Cost-effectiveness: High-volume production reduces the per-unit cost significantly.
- Design Flexibility: Complex shapes can be produced with precision. This allows brands to innovate in design without heavy costs.
- Consistency: Each product is virtually identical, ensuring quality and reliability in consumer goods.
Due to these factors, many companies lean on injection moulding to fulfill mass production needs while maintaining brand standards.
Automotive Components
In the automotive industry, injection moulding has transformed how parts are manufactured. Key benefits include:
- Weight Reduction: Lightweight plastic parts contribute to fuel efficiency in vehicles. This is increasingly important amid growing environmental concerns.
- Durability: Modern plastics often outperform traditional materials in various applications, offering superior resistance to wear and tear.
- Complex Component Integration: Many automotive components are produced as single, integrated parts, rather than assembling multiple pieces. This streamlining aids in reducing the overall assembly time.
Common applications in this field include dashboards, exterior trim, and various interior components. With the rise of electric vehicles, the demand for complex and lightweight components made via injection moulding is only expected to grow.
Medical Devices
The medical field presents unique challenges that injection moulding is well-equipped to handle. The advantages include:
- Precision: Devices require tight tolerances for functionality and safety. Injection moulding can achieve these specifications.
- Biocompatibility: Specialized materials used in injection moulding can be tailored to meet biocompatibility standards, crucial for implants and surgical instruments.
- Mass Production: Devices like syringes, inhalers, and diagnostic equipment can be produced at scale, reducing costs and improving availability.
Quality control is paramount in this sector, as flaws could have serious consequences. Thus, rigorous testing methodologies are integral to the production process within the injection moulding domain for medical applications.
Injection moulding is not just a manufacturing technique; it shapes industries, impacting everything from consumer habits to automotive advancements and healthcare solutions.
Injection moulding demonstrates extensive application potential across various sectors, with consumer products, automotive parts, and medical devices illustrating its capacity to meet complex manufacturing demands.
Advantages and Disadvantages of Injection Moulding
Understanding the advantages and disadvantages of injection moulding is crucial for making informed decisions in manufacturing processes. This section outlines the various benefits and limitations of the injection moulding method, highlighting specific elements that impact its overall effectiveness and suitability for different applications.
Key Advantages
High Efficiency
High efficiency in injection moulding is one of the most significant features that appeal to manufacturers. This method can produce large quantities of parts quickly, which is critical for businesses aiming to scale production. The automated nature of the process means that once the mould is made, parts can be produced continuously. This minimizes downtime and contributes to higher output rates. Companies that rely on mass production often find injection moulding a beneficial choice due to this aspect of efficiency.
Versatility
Versatility is another key characteristic of injection moulding. This process can handle various materials, including different types of plastics and even some metals. It allows for complex shapes and designs, making it suitable for a range of industries such as consumer goods, automotive, and medical. The ability to customize mould designs adds to its appeal. However, the specific requirements for different materials can complicate some aspects of production.
Consistency
Consistency in quality is essential in manufacturing, and injection moulding excels in this area. The precision of the process ensures that parts produced are uniform, meeting exact specifications. This reliability is vital for products requiring tight tolerances. With each cycle producing nearly identical parts, businesses can decrease the likelihood of defects, which results in less waste and increased customer satisfaction.
Limitations and Challenges
While the advantages of injection moulding are substantial, it also presents limitations that manufacturers must consider. The initial cost of creating the moulds can be high, which may not be justifiable for small production runs. Additionally, complex designs can lengthen mould creation time, affecting turnaround.
Another limitation is the dependence on the material's properties. Some materials may not perform well under the injection moulding process, leading to issues like warping or insufficient strength. Therefore, careful selection of materials and thorough testing are critical.
Overall, weighing these advantages and disadvantages is essential for anyone considering injection moulding as a viable production method. By understanding its efficiency, versatility, and consistency alongside its limitations, manufacturers can make better choices that align with their specific needs.
Quality Control in Injection Moulding
Quality control is critical in injection moulding. It ensures that products meet specified standards. This section highlights specific elements and benefits of quality control in this manufacturing process. Effective quality control reduces defects, minimizes waste, and guarantees consistency in final products.
In injection moulding, maintaining high quality is vital. Different factors can influence product quality, such as machine calibration, material selection, and environmental conditions. Implementing robust quality assurance techniques can positively affect production efficiency and product integrity.
Quality Assurance Techniques
Quality assurance encompasses various techniques and practices to maintain product standards. Some of these techniques include:
- Process Monitoring: Regularly checking machine performance can prevent deviations which can lead to defects.
- Material Inspection: Quality of raw materials is crucial before they enter the moulding process. Inspecting materials ensures compliance with standards.
- Testing Samples: Conducting tests on randomly selected samples helps identify potential issues early.
- Training: Continuous training of operators on machinery and processes enhances overall product quality.
Common Defects and Their Solutions
Injection moulding is not without its challenges. Certain defects can arise during production. By understanding these defects, appropriate solutions can be implemented. Below are some common defects:
Short Shots
Short shots occur when the mould does not fill completely. This defect can weaken the product and affect its functionality. The main characteristic of short shots is the incomplete filling of the captured cavity in the mould. This is generally considered a significant issue.
To address short shots:
- Increase injection pressure.
- Reduce melt viscosity of the material.
- Ensure the material temperature is adequate.
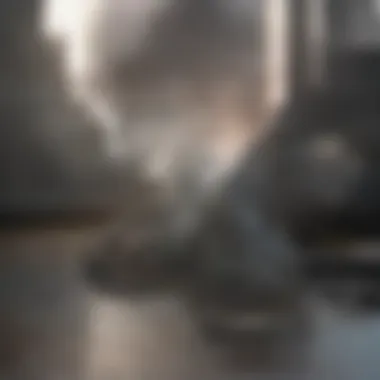
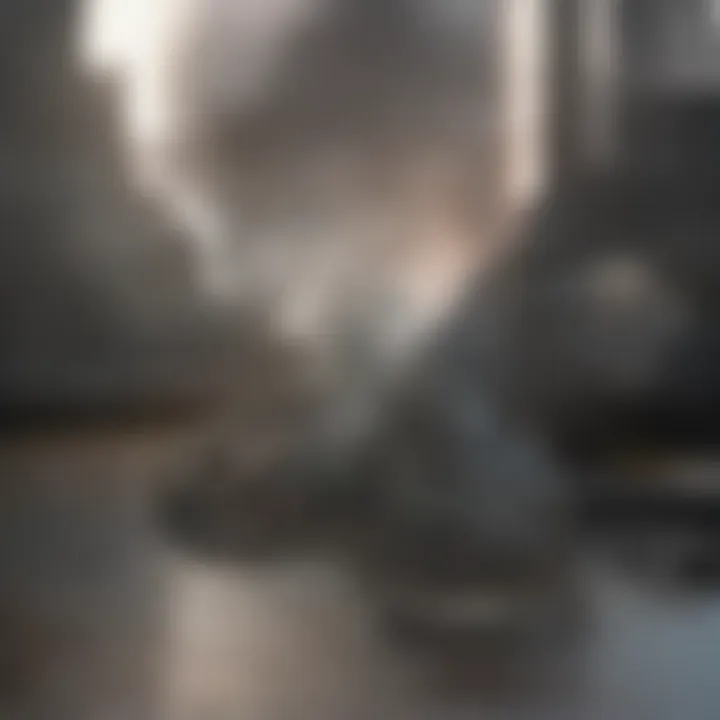
Warpage
Warpage refers to the distortion of finished parts. It can be caused by uneven cooling or improper mould design. Warpage often leads to functional problems and aesthetic defects. The key aspect of warpage is the change in shape from the original design.
Solutions for warpage include:
- Adjusting cooling rates.
- Modifying the design to minimize stress concentrations.
- Selecting appropriate materials that resist warping.
Sink Marks
Sink marks appear as depressions on the surface of a part. They are primarily a cosmetic defect but can indicate deeper quality issues. The main factor causing sink marks is the cooling of thicker sections quicker than thinner sections.
To resolve sink marks, manufacturers can:
- Adjust the cooling and injection parameters.
- Use materials with better flow characteristics.
- Improve gate design to ensure more uniform filling.
Environmental Considerations
The significance of environmental considerations in injection moulding cannot be overstated. As industries evolve, there is a growing awareness of the environmental impact of manufacturing processes. Injection moulding, while being efficient in producing high volumes of plastic products, raises questions about sustainability and eco-friendliness.
Sustainability in Injection Moulding
Sustainability in injection moulding involves adopting practices that minimize environmental harm while maximizing resource efficiency. Manufacturers are increasingly implementing strategies to reduce waste, energy consumption, and carbon emissions. This focus on sustainability is not only beneficial for the planet but also for businesses, as consumers are more inclined to support companies that prioritize environmental responsibility.
Several approaches can enhance sustainability in this process:
- Material Innovation: Using bioplastics or recycled materials can significantly reduce the environmental footprint associated with traditional plastic production.
- Energy-Efficient Machinery: Adopting advanced, energy-efficient machines reduces electricity consumption during the moulding process, leading to lower operational costs and less environmental impact.
- Waste Reduction Techniques: Implementing measures like regrinding scrap material for reuse ensures that less waste is generated. By recycling redundant products, companies can also decrease their resource dependency.
Improving sustainability is a holistic endeavor that takes into account the entire lifecycle of the product, from design to disposal.
Recyclability of Materials
Recyclability is a crucial factor in the environmental conversation surrounding injection moulding. The ability to recycle plastics not only decreases waste in landfills but also conserves resources. Understanding the types of materials used in injection moulding is key to this discussion.
Plastics are categorized by their recyclability, with some being more easily recyclable than others. Thermoplastics, for instance, can be remelted and shaped multiple times, making them ideal for recycling. Examples include:
- Polyethylene Terephthalate (PET): Commonly used in bottles, PET is widely accepted for recycling and can be transformed into a variety of products.
- Polypropylene (PP): This type of plastic is also recyclable, often used in packaging and automotive applications.
However, thermosetting plastics present a challenge in recycling. Once set, they cannot be remelted or reshaped, making them difficult to process after disposal.
To enhance recyclability, manufacturers should consider:
- Designing for Disassembly: Creating products that can be easily separated into recyclable components promotes efficient recycling efforts.
- Collaborating with Recycling Facilities: Establishing partnerships with local recycling centers ensures that waste from the injection moulding process is properly handled.
"The future of injection moulding relies not only on technological advancements but also on adopting eco-friendly practices that ensure the longevity of our planet."
Through these measures, injection moulding can evolve beyond its traditional role, becoming a more responsible player in the manufacturing landscape.
Future Trends in Injection Moulding
Understanding the future trends in injection moulding is crucial. This concept helps us anticipate changes and adapt to the evolving landscape of manufacturing. New technologies and applications can significantly enhance production efficiency. As industries face increasing demands for sustainability and performance, awareness of these trends becomes vital.
Advancements in Technology
Industry 4.
The concept of Industry 4.0 represents the new era of manufacturing. It integrates modern technologies with manufacturing processes. This integration leads to smarter factories that can optimize operations. The key characteristic of Industry 4.0 is its reliance on data. It uses Internet of Things (IoT) devices to collect and analyze real-time data. This capability allows manufacturers to make informed decisions quickly. It is a beneficial choice for injection moulding.
Moreover, the unique feature of Industry 4.0 is the connectivity it provides. Machines can communicate with each other, allowing for seamless adjustments. This connectivity can improve production efficiency. However, it also necessitates investments in smart technologies and training.
Automation
Automation plays an important role in injection moulding. It enhances production speed and consistency. The key characteristic of automation is its ability to reduce human intervention. While this approach can lead to higher output rates, it is essential to maintain quality standards. Automation is a popular choice for manufacturers aiming for efficiency.
A unique feature of automation is the use of robotics. Robots can handle intricate tasks with precision. This technology minimizes human errors and maximizes productivity. However, reliance on automation can lead to challenges, such as job displacement and high setup costs.
Emerging Applications
The emergence of new applications for injection moulding reflects the versatility of the technology. Several sectors, including medical, automotive, and consumer goods, increasingly rely on injection moulding. Innovations in material science have expanded the range of products that can be produced. Moreover, injection moulding is adapting to new demands, such as customization and rapid prototyping.
"As industries evolve, the possibilities for injection moulding grow exponentially, highlighting its staying power in modern manufacturing."
In summary, recognizing future trends in injection moulding is essential. Staying informed about advancements in technology and exploring emerging applications can help industry professionals remain competitive. Companies that embrace these trends are better prepared to meet future challenges.
Epilogue and Insights
In the realm of manufacturing, injection moulding stands as a pivotal technology. Its role is not only fundamental to the production of a myriad of plastic products but also integral to the advancement of manufacturing methodologies. The conclusion of this article synthesizes insights about the complexities and nuances of injection moulding, emphasizing how this process shapes the industry.
Key elements of injection moulding include the efficacy of production and adaptability in design. By capturing its importance, we also consider its implications for sustainability and innovation. As industries evolve, the capacity for injection moulding to adapt to new materials and technologies positions it as a continually relevant process.
"Injection moulding combines precision with efficiency, making it indispensable for modern manufacturing."
Understanding injection moulding allows stakeholders—engineers, designers, and business leaders—to make informed decisions. The insights gained throughout this article illustrate the need for rigorous design considerations and quality control mechanisms. These are not just best practices; they significantly enhance operational performance and product quality.
Summary of Key Points
- Definition and Process: Injection moulding involves injecting molten material into a mould, which cools to form a part. The steps include clamping, injection, cooling, and ejection.
- Materials: The choice of thermoplastics and thermosetting plastics directly impacts product performance and recyclability.
- Design Considerations: Mould and part design significantly influence manufacturability. Key factors like thickness, draft angles, and design for manufacturability play critical roles.
- Applications: Injection moulding finds usage in consumer products, automotive components, and medical devices, highlighting its versatility.
- Quality Control: Implementing quality assurance techniques is vital to mitigate common defects and ensure product integrity.
While this overview only scratches the surface, it points toward a comprehensive understanding required for successful injection moulding practices.
Final Thoughts on Injection Moulding
As we conclude our exploration of injection moulding, it is clear that this process is more than just a method of production; it is a dynamic and evolving field. The future will likely see increased automation and integration with Industry 4.0 principles, enhancing efficiency and reducing waste.
Professionals engaged in this domain must remain aware of these trends and the ongoing need for sustainable practices. The integration of newer materials and technologies, coupled with the existing ones, will define the future landscape of injection moulding.
The journey through injection moulding, as detailed in this guide, equips students, researchers, and industry professionals with the essential information needed to navigate its complexities and embrace its potential.