Understanding HVOF: Principles and Applications
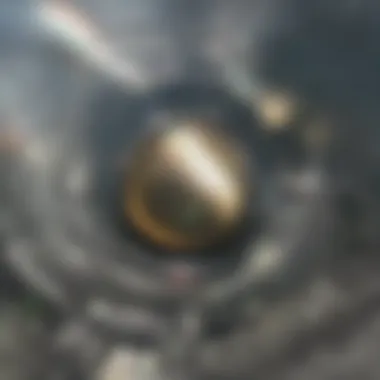
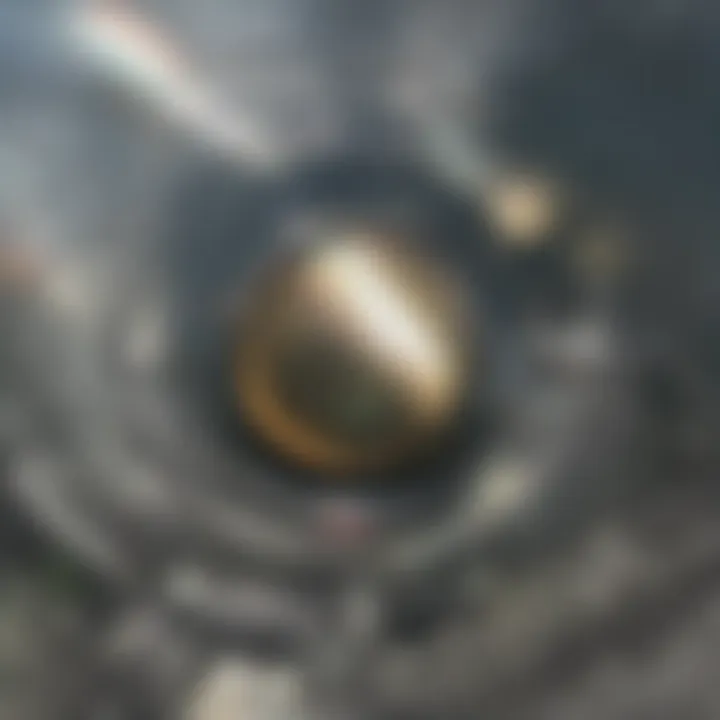
Intro
The High Velocity Oxy-Fuel (HVOF) system is a notable advancement in the realm of thermal spray technology. Its capacity to enhance surface properties makes it an essential process across various industries. From aerospace to automotive and manufacturing, the applications of HVOF are broad and varied. Understanding the principles behind this technology is crucial for professionals involved in materials engineering, ensuring they can leverage its capabilities effectively.
The HVOF system operates on core principles that govern the spray process. It utilizes a high-velocity gas to propel powdered materials onto a substrate, resulting in a strong and durable coating. This method not only improves wear resistance but also provides excellent corrosion protection. Therefore, knowing the fundamental mechanics of HVOF helps in better application and material selection.
In this article, the discussion will unfold by addressing key findings, methodologies, and future directions of the HVOF system. We will explore the procedural nuances, delve into various applications, and consider the future prospects of this technology in modern material solutions.
Preface to HVOF System
The High Velocity Oxy-Fuel (HVOF) system represents a critical advancement in thermal spray technology, significant for its role in enhancing the durability and performance of various surfaces. Understanding the fundamentals of HVOF is paramount for students, researchers, and professionals in material engineering and coatings technology. This section aims to lay the groundwork for better comprehension of the HVOF system's definition, overview, and historical context.
Definition and Overview
The HVOF system utilizes a combustion process that propels metallic or non-metallic powders onto a substrate at high velocities. The main principle is to achieve a dense coating with superior bonding strength. This method is particularly favored for its ability to produce coatings that exceed the limitations of traditional thermal spray techniques. Key aspects include:
- High velocity of particle impacts, ensuring reduced porosity.
- Capable of utilizing a variety of powder materials, enhancing versatility in applications.
- Efficient process leading to lower material waste and better safety standards.
Understanding these elements gives insight into why HVOF is chosen across different industries, from aerospace to medical device manufacturing.
Historical Development
The journey of HVOF began in the mid-20th century, emerging as a response to the limitations seen in earlier coating techniques like plasma spraying. Initial research focused on improving the thermal efficiency of combustion processes for spraying applications. By the late 1980s, HVOF systems gained popularity as equipment designs evolved, enabling finer control over temperature and velocity. Several milestones include:
- Development of new fuel mixtures which enhanced thermal efficiency.
- Introduction of automated systems that improved repeatability and quality consistency.
The historical context of HVOF is essential to appreciate its current advancements and applications in modern material engineering.
Operating Principles of HVOF
The operating principles of High Velocity Oxy-Fuel (HVOF) are fundamental to understanding the system's functionality and performance in various applications. This technology employs high-velocity particles created through combustion processes, which is critical for achieving effective surface coatings. The operational aspects of HVOF play a key role in its advantages, including enhanced coating adhesion, reduced oxidation, and overall performance in surface engineering.
Mechanics of High Velocity Spraying
In HVOF, the mechanics involve spraying powdered materials at high speeds onto a substrate surface. The system utilizes oxygen and fuel to create a high-velocity gas jet that melts and accelerates the powder particles. These particles can achieve velocities over 600 meters per second. This speed is crucial as it ensures that the coating adheres strongly to the substrate, thereby increasing its durability and lifespan.
The method can be operated in various forms, including liquid fuels or gaseous combinations, each affecting the particle velocity and heat. The mechanics also consider nozzles’ design, which directly impacts the velocity of the particles. For example, a converging-diverging nozzle is typically used to achieve supersonic speeds, thus optimizing the overall spraying efficiency.
Temperature and Pressure Dynamics
Temperature and pressure dynamics are vital components of the HVOF process. The combustion of gases generates extremely high temperatures, reaching approximately 3,000 degrees Celsius. This heat is essential for melting the powder materials so they can adhere effectively to the surface.
Pressure also plays a significant part in the mechanics of HVOF. The operational pressure within the combustion chamber needs to be controlled accurately to maintain the required flow rates of gases. Higher pressures will generally lead to increased particle velocity, enhancing the impact energy when the particles collide with the substrate. Understanding and managing these dynamics is crucial for optimizing coating performance and consistency.
Role of Gases in HVOF Process
The choice of gases in the HVOF process is another critical factor influencing the quality of the coatings. Typically, a mix of hydrogen, propane, or acetylene is used as the fuel gas alongside oxygen. The specific combination affects the flame temperature and the characteristics of the spray jet. For instance, hydrogen provides a higher flame temperature than propane, which can lead to improved melting of the powder and better adhesion.
Furthermore, the gases have a direct influence on the oxidation of the powder particles during spraying. It is necessary to minimize the oxidation to preserve the properties of the coatings. The correct management of gas mixtures and flow rates can reduce emissions and enhance the environmental friendliness of the HVOF process.
High Velocity Oxy-Fuel technology provides a superior coating experience, ensuring a well-bonded and robust surface capable of withstanding harsh environments.

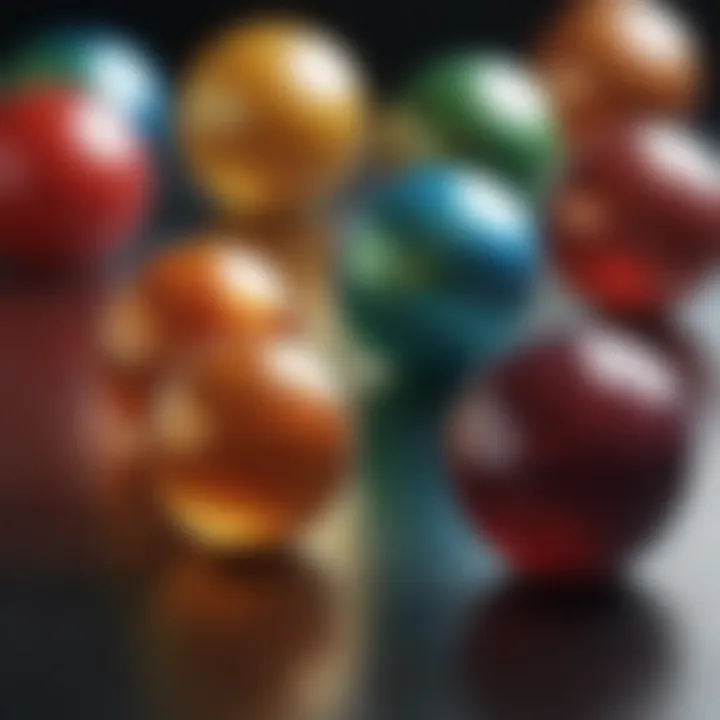
Materials Used in HVOF Applications
The choice of materials used in High Velocity Oxy-Fuel (HVOF) applications is crucial. The materials directly affect the quality and durability of the coatings produced. Understanding these materials helps to optimize the HVOF process, ensuring effective surface treatment for various applications.
Common Powder Materials
In HVOF, the powder materials utilized are primarily metal-based, ceramic, or composite powders. Each type has unique attributes suitable for specific applications. Here are some widely used materials:
- Nickel-based alloys: Often selected for their excellent corrosion resistance and ability to withstand high temperatures. They are common in aerospace and turbine components.
- Cobalt-based alloys: Used for their strong wear resistance properties. They are effective in various applications from mining to manufacturing.
- Tungsten carbide: Known for its hardness and wear resistance, making it ideal for applications where high abrasion occurs. Commonly used in cutting tools and wear parts.
- Ceramic powders: Such as alumina and zirconia. They offer high-temperature resistance but are more brittle than metal powders, thus best for specific scenarios.
Choosing the right powder is essential for achieving desired properties in coatings, reinforcing the performance of the final product.
Selection Criteria for HVOF Materials
When selecting materials for HVOF applications, several criteria must be considered:
- Compatibility with substrate: The selected material should bond efficiently with the substrate to create a durable coating.
- Thermal properties: Coefficients of thermal expansion and conductivity can impact the integrity of the final coating under temperature variations.
- Mechanical properties: Hardness, wear resistance, and toughness are essential properties to evaluate based on the application demands.
- Corrosion resistance: For applications exposed to harsh environments, selecting materials that can withstand chemical reactions is critical.
- Cost-effectiveness: The economic aspect cannot be sidelined. Balancing performance needs with budget constraints is essential for practical implementation.
Effective material selection can extend the life of components while enhancing performance in demanding environments.
"Material choice exists between performance expectations and economic realities. Understanding both leads to more informed decisions in the HVOF process."
In summary, the choice and selection of materials in HVOF applications play a significant role in achieving optimized surface treatments that not only meet but exceed industry expectations.
Applications of HVOF Technology
The application of High Velocity Oxy-Fuel (HVOF) technology is crucial for industries looking to improve durability and performance through advanced surface treatments. HVOF is not just a method; it is a solution that provides significant benefits across various sectors. This section will delve into specific applications in industrial coatings, aerospace components, and medical devices.
Industrial Coatings
In the realm of industrial coatings, HVOF technology stands out for its ability to deposit thick, dense coatings that provide superior protection against wear, corrosion, and thermal stress. Industries that require robust surface solutions, such as oil and gas, automotive, and manufacturing, utilize HVOF to apply materials like tungsten carbide and chrome oxide.
One major benefit of HVOF in coatings is the reduction of porosity. This feature is critical as it enhances the coating's overall integrity and lifespan. For instance, in the oil and gas sector, equipment is often exposed to harsh environments, requiring coatings that can withstand extreme conditions. HVOF’s precision allows for these needs to be met without compromising the substrate material.
Aerospace Components
The aerospace industry demands high standards for materials used in components due to the need for safety, performance, and efficiency. HVOF technology is employed for coating turbine blades, landing gear, and other critical components. The thorough spray process ensures that flight-safe features are rigorously maintained.
HVOF coatings can lead to weight reduction in parts while enhancing performance. For example, by applying a lower density but highly durable coating, manufacturers can optimize fuel efficiency without sacrificing strength. Such advancements have the potential to revolutionize component longevity and reliability, which are paramount in commercial and military aviation.
Medical Devices and Biocompatibility
In the medical field, HVOF technology finds applications in surface treatment of medical devices. Coatings need to exhibit biocompatibility, ensuring that they do not provoke adverse reactions in the human body. HVOF allows for the deposition of biocompatible materials such as titanium coatings on implants. These coatings improve osseointegration, where the bone bonds with the implant, significantly contributing to the success of surgical procedures.
Moreover, HVOF techniques facilitate improved mechanical properties like wear resistance on orthopedic implants. This attribute is fundamental for extending the lifespan of devices and reducing the chances of failure in patients.
HVOF technology addresses diverse needs across industries by enhancing material properties, ensuring safety, and promoting sustainability.
In summary, the applications of HVOF technology illustrate its integral role in pushing the boundaries of material performance in various critical fields. By offering enhanced surface solutions, HVOF technology represents a vital resource in modern industry.
Advantages of HVOF Over Other Thermal Spray Techniques
The High Velocity Oxy-Fuel (HVOF) system presents several advantages that set it apart from traditional thermal spray methods. These benefits are crucial, especially for industries where surface properties significantly impact product performance and longevity. Understanding these advantages helps in making informed choices about coating technologies.
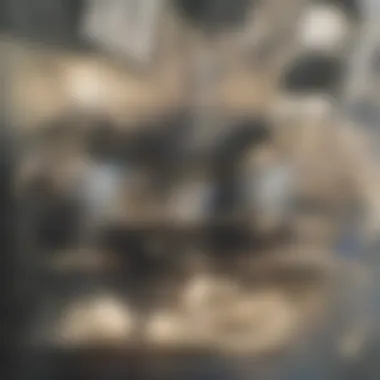
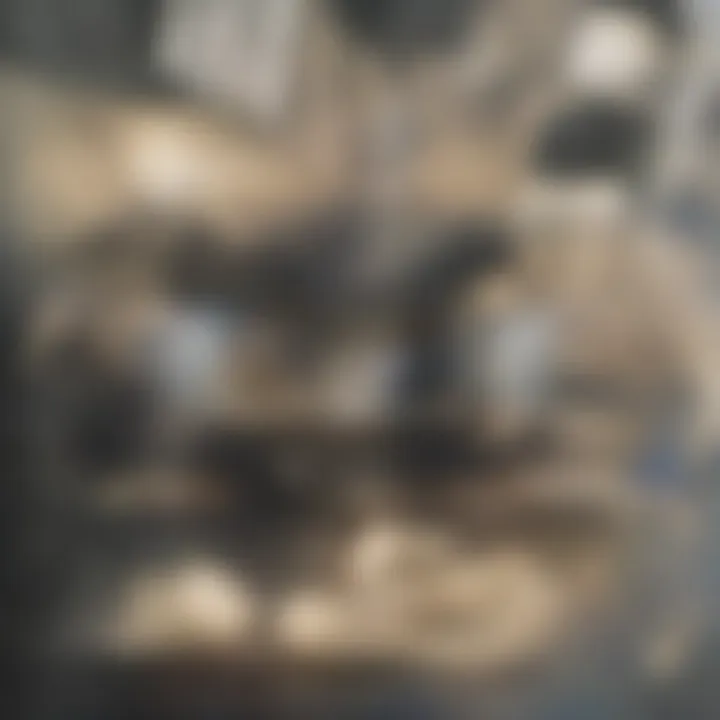
Superior Coating Adhesion
One significant advantage of HVOF is the superior coating adhesion it provides. This is largely due to the high kinetic energy involved in the HVOF process. When powders are sprayed at high velocities, they experience intense mechanical interlocking with the substrate. This results in a stronger bond that can withstand various stresses.
Factors influencing adhesion include the surface preparation methods used, the type of substrate, and the powder characteristics. Surface treatments such as grit blasting or chemical cleaning enhance the bonding capability. Additionally, the deposition temperature is relatively low compared to other techniques, such as plasma spraying, which helps minimize thermal distortion or damage to the underlying material.
Enhanced Wear Resistance
HVOF technology delivers exceptional wear resistance, making it suitable for applications in harsh environments. This is largely attributed to the denser coatings produced through this method. The high velocity and thermal energy result in a compact microstructure with fewer porosities, thus improving mechanical properties.
In industries such as mining, oil and gas, and manufacturing, wear resistance is critical. Coatings applied using HVOF can significantly extend the lifespan of components. This advantage reduces operational costs associated with maintenance and replacement of parts, adding value to the technology.
Reduced Oxidation in Coatings
HVOF systems are known for their efficiency in minimizing oxidation of the deposited materials. The controlled environment during the application, along with the low temperatures involved, contribute to this benefit. Oxidation can weaken coatings, leading to failure in service. HVOF effectively mitigates these risks, promoting durability.
Choosing HVOF not only improves performance but also enhances the reliability of products exposed to corrosive elements. This is particularly relevant in sectors such as aerospace and marine, where materials must endure dynamic and corrosive conditions.
"The advantages of HVOF technology enhance its appeal in sectors that demand high-performance materials."
Challenges in the HVOF Process
The HVOF system, while robust and efficient, also faces several challenges that can affect its implementation and efficacy. Understanding these challenges is crucial for practitioners, researchers, and anyone involved in surface engineering. By identifying these difficulties, solutions can be better formulated. This section discusses the equipment and operational costs of HVOF, as well as the challenges of process control and repeatability.
Equipment and Operational Costs
The costs associated with HVOF technology can be significant. The initial investment for HVOF equipment is often higher than that required for other thermal spray systems. Equipment needs to be precise and durable to withstand the high temperatures and pressures associated with the process. Specific brands like Sulzer Metco and Praxair offer advanced systems, but their prices reflect the technology's sophistication.
Purchasing specialized components, such as nozzles and powder feed systems, further increases expenses.
Operational costs also play a vital role. They include:
- Material Costs: High-quality powders required for optimal coatings come at a premium.
- Energy Consumption: The energy necessary to heat and propel the materials adds to the total operational costs.
- Maintenance: Regular maintenance of equipment is crucial to prevent breakdowns, which can lead to costly downtimes.
It is essential for companies to perform a cost-benefit analysis before investing in HVOF technology, ensuring that the potential returns justify the initial and ongoing expenditures.
Process Control and Repeatability
Achieving consistent results with the HVOF process is a core challenge. Variations in parameters such as temperature, pressure, and powder feed rate can lead to non-uniform coatings. Factors that contribute to difficulties include environmental conditions and equipment calibration variations.
The importance of process control cannot be overstated. Having precise control over each aspect of the HVOF operation is crucial for ensuring coating quality. This requires:
- High-Quality Sensors: Using advanced sensors that provide real-time data helps in monitoring and adjusting parameters promptly.
- Automated Control Systems: Employing automated systems can lead to better consistency and reduced human error, promoting uniformity in coatings.
"Achieving repeatability often demands rigorous testing and validation of processes to ensure that coatings meet industry standards."
In summary, while HVOF technology presents various advantages, managing equipment and operational costs alongside ensuring process control and repeatability remains essential. Companies utilizing this technology must carefully navigate these challenges to harness the full potential of HVOF.
Innovations in HVOF Technology
Innovations in High Velocity Oxy-Fuel (HVOF) technology have significantly advanced the field of thermal spray coatings. These innovations are vital for a number of reasons, primarily focusing on enhancing the performance, efficiency, and versatility of HVOF applications. As industries strive for improved materials and processes, advancements in HVOF can offer both immediate and long-term benefits.
Advancements in Coating Materials
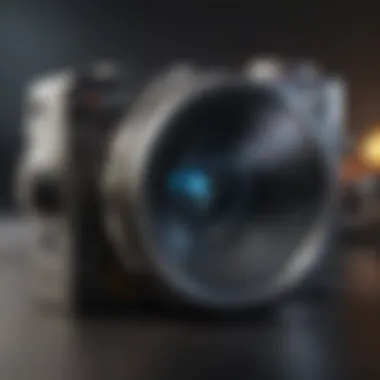
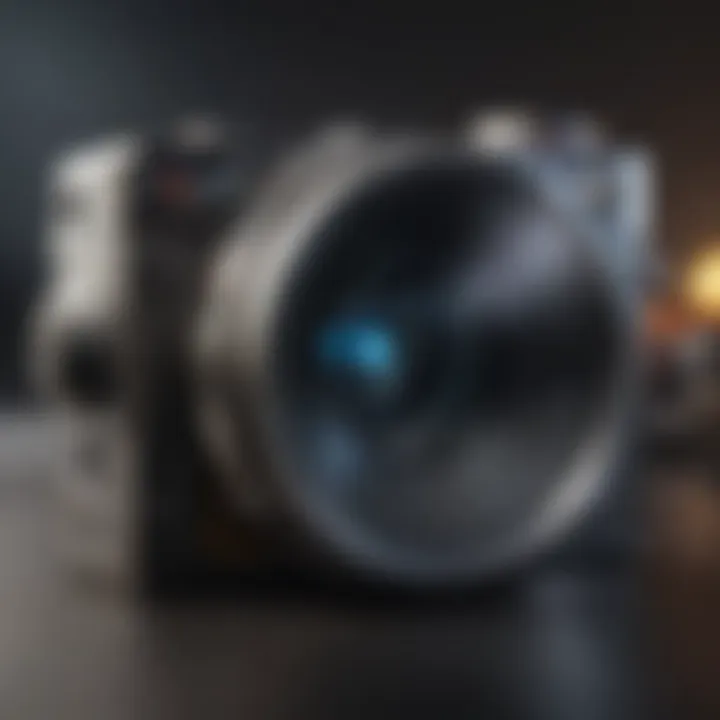
The realm of coating materials used in HVOF systems has seen remarkable progress. New powder materials are being developed with superior properties. Some of these include high hardness, improved wear resistance, and better corrosion resistance. Such advancements in materials enable coatings to withstand more extreme environments and prolonged use.
In terms of composition, many new alloy formulations have emerged. For example, ceramic-based materials, metal matrix composites, and functionally graded materials are becoming more common. This diversity allows for customization according to specific application requirements.
Furthermore, nano-coatings are attracting attention. These materials can significantly increase the surface area, resulting in improved interaction with the substrate and enhanced adhesion. This aspect is crucial as superior adhesion translates to better performance in service environments.
Integration with Additive Manufacturing
Another notable innovation is the integration of HVOF technology with additive manufacturing processes. This collaboration creates a robust synergy that addresses the challenges of traditional fabrication methods. In additive manufacturing, material is often deposited layer by layer. The use of HVOF for post-treatment can enhance the material properties of the added layers.
By applying HVOF coatings to parts manufactured through additive processes, one can achieve improved wear and corrosion resistance. These enhancements are important in sectors like aerospace and automotive, where component reliability is paramount.
Additionally, this integration permits the design of more complex geometries. HVOF can coat additive-manufactured components uniformly, which ensures that these intricate shapes maintain their mechanical integrity without compromising on surface performance.
"The fusion of HVOF technology with additive manufacturing is setting the stage for next-generation components with remarkable performance characteristics."
Overall, these innovations significantly contribute to the ongoing evolution of HVOF systems. They underline the potential for tailored solutions to specific operational challenges faced by various industries.
Environmental Considerations in HVOF Operations
Environmental considerations in High Velocity Oxy-Fuel (HVOF) operations are increasingly becoming a critical focus in modern industry. As the need for sustainable practices escalates across all sectors, understanding the environmental impact of HVOF processes is vital. This section explores the significance of waste management, recycling practices, and emission reduction strategies associated with HVOF technology.
Waste Management and Recycling
In HVOF operations, waste material can be generated through several processes. This includes leftover powder materials, maskings, and other by-products. Proper waste management strategies help mitigate the ecological footprint of HVOF applications. Efficient recycling practices not only reduce waste but also minimize the costs associated with material procurement.
Key points include:
- Recycling Powder Materials: Reusing unspent powder helps in significantly reducing material costs while promoting sustainability.
- Waste Disposal Practices: Following regulatory guidelines for waste disposal ensures that harmful substances are properly managed.
- Process Optimization: Refining process parameters reduces the volume of waste generated.
The implementation of structured waste management systems can lead to a decrease in environmental hazards, making operations more compliant with environmental standards.
Reducing Emissions in HVOF
Emissions during the HVOF process are a central environmental consideration. The combustion of gases used in the HVOF system can produce particulate matter and other harmful emissions. Addressing these concerns is essential for both compliance and overall ecological responsibility.
Within the context of emission reduction, focus is placed on the following aspects:
- Use of Low-Emission Fuels: Transitioning to fuels that lower greenhouse gas emissions can make the HVOF applications more environmentally friendly.
- Improved Combustion Efficiency: Optimizing the combustion process reduces excess emissions by ensuring that fuel is fully utilized.
- Ventilation Systems: Implementing advanced filtration and ventilation systems can capture and condition exhaust emissions before they are released into the atmosphere.
Emission reduction strategies are not merely regulatory compliance but are fundamental for advancing the sustainability of HVOF technology.
End
The conclusion is a crucial part of this article as it encapsulates the key insights gained from our examination of the HVOF system. Understanding the significance of HVOF technology is essential for students, researchers, and professionals alike. This process not only enhances material properties but also expands the potential applications across various industries, such as aerospace, manufacturing, and medical sectors.
Summary of Key Findings
In reviewing the critical elements of the HVOF system, several key findings emerge:
- Advanced Surface Coatings: HVOF produces superior coatings that exhibit excellent adhesion and durability. These coatings are pivotal for enhancing wear resistance and reducing oxidation-related issues.
- Diverse Material Applications: The versatility in material selection makes HVOF adaptable for many contexts. Commonly used powder materials include tungsten carbide and ceramic composites.
- Innovative Technology Integration: Advances in this field, particularly in coating materials and their integration with additive manufacturing, highlight the dynamic nature of HVOF technology and its capacity for future growth.
- Environmental Responsibility: Addressing emissions and effective waste management represent ongoing challenges but also provide pathways for sustainability in industrial settings.
Future Perspectives on HVOF Technology
Looking ahead, the HVOF system is positioned for further evolution. Researchers are focusing on improving process efficiency and expanding the range of materials that can be utilized.
- Development of Eco-Friendly Materials: Future innovations may include the exploration and implementation of environmentally friendly powder materials, aligning with global sustainability goals.
- Enhanced Process Automation: Increasing automation in HVOF systems can improve reliability and reduce human error, thus streamlining production processes.
- Cross-Disciplinary Research: Collaborations between disciplines, such as textiles and bioengineering, may lead to novel applications of HVOF, opening new avenues for technology exploitation.
Overall, the conclusion illustrates the transformative impact of HVOF technology on materials engineering while emphasizing its ongoing developments and potential for future advancements. Understanding these elements not only informs best practices in industry but also guides ongoing research efforts.