Understanding Fuel Injectors in Diesel Engines
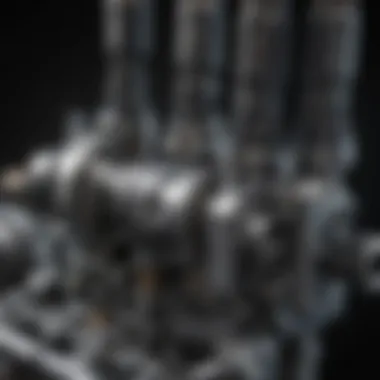
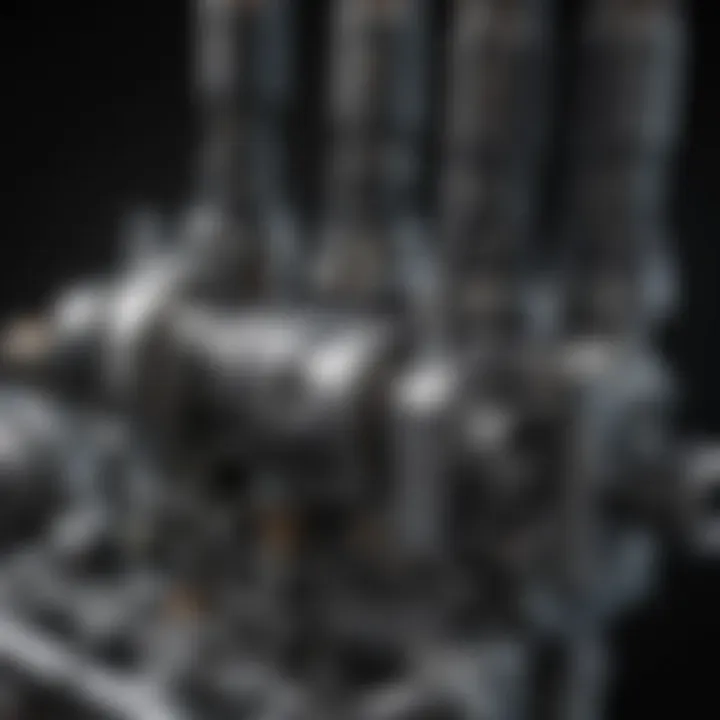
Intro
Fuel injectors play a crucial role in the operation and efficiency of diesel engines. Their primary function is to deliver the right amount of fuel directly into the combustion chamber at the optimal time. Understanding this mechanism is essential for those involved in automotive engineering, maintenance, and performance enhancement.
In diesel engines, fuel injection is more than just a delivery system; it significantly impacts fuel economy, emissions, and overall engine performance. As technology advances, so do the designs and functionalities of fuel injectors. This article aims to dissect these components in detail, ensuring that students, researchers, educators, and professionals have a robust understanding of diesel fuel injectors.
Key Findings
Major Results
Recent studies highlight the following key findings regarding fuel injectors in diesel engines:
- Types of Fuel Injectors: Various types of injectors, such as mechanical and electronic, serve different purposes and are suited for various engine designs.
- Impact on Performance: Efficient fuel injectors contribute to improved combustion, which directly enhances engine power and reduces emissions.
- Maintenance: Regular maintenance and cleaning of fuel injectors are essential to ensure that they function correctly and maintain optimal engine performance.
- Technological Advancements: Innovations in fuel injector technology, including common rail systems, have revolutionized the efficiency of diesel engines.
Discussion of Findings
These findings underline the significance of fuel injectors in modern diesel engines. Understanding the differences between types of injectors allows engineers to choose the appropriate system for specific applications. Moreover, acknowledging the importance of maintenance helps in reducing long-term operational costs by preventing repairs that arise from neglected systems. The advent of cutting-edge technologies also indicates a shift toward more environmentally friendly engines, aligning with global endeavors to reduce carbon footprints.
Methodology
Research Design
This article utilized a qualitative research design, incorporating a review of existing literature, technical documents, and expert testimonials to gather comprehensive insights into the role of fuel injectors.
Data Collection Methods
Data was collected from various sources:
- Academic Journals: Studies in mechanical and automotive engineering provided background information on injector technology.
- Industry Reports: Insights from fuel injector manufacturers and industry experts contributed to understanding current trends and technologies.
- Online Forums: Discussions on platforms like Reddit and Facebook provided real-world experiences and opinions that enriched the research.
Through a thorough examination of these aspects, the aim is to present a detailed narrative that informs the reader about the critical role of fuel injectors in enhancing the performance of diesel engines.
Prelude to Diesel Engine Mechanics
Understanding diesel engine mechanics is crucial because it lays the foundation for comprehending the role of each component within the system, including the extremely important fuel injectors. Diesel engines operate on a different principle compared to gasoline engines, utilizing compression ignition rather than spark ignition. This fundamental difference affects how fuel is injected, combusted, and managed within the engine. By exploring diesel engine mechanics, one can appreciate the precise nature of fuel injection and its impact on overall engine performance.
Overview of Diesel Engines
Diesel engines are widely used in various applications, from automobiles to industrial machinery. They operate on the diesel cycle, which involves compressing air to high pressures and temperatures before injecting fuel directly into the combustion chamber. This results in a more efficient fuel combustion process compared to traditional gasoline engines, often delivering higher torque and fuel efficiency. Diesel engines are favored for their durability and power, making them ideal for heavy-duty applications.
Key Characteristics of Diesel Engines:
- Compression Ratio: Diesel engines typically have a higher compression ratio, leading to improved thermal efficiency.
- Fuel Type: They use diesel fuel, which is thicker and has a higher energy density than gasoline.
- Torque Output: Diesel engines generate more torque at lower RPMs, which is beneficial for transporting heavy loads.
- Fuel Efficiency: Generally, they offer better fuel economy compared to gasoline engines.
Key Components of Diesel Engines
The functionality of diesel engines relies on several critical components that work in harmony. Each part plays a specific role, contributing to the engine's overall efficiency and performance.
- Cylinder Block: This is the main structure where the cylinders are housed. It provides the necessary strength and support for other components.
- Pistons: These move up and down inside the cylinders, compressing the air and the fuel mixture for combustion.
- Fuel Injector: This component is responsible for delivering diesel fuel into the combustion chamber at the right time and pressure. Its efficiency directly influences engine performance and emissions.
- Crankshaft: It converts the linear motion of the pistons into rotational motion, which ultimately drives the vehicle.
- Turbocharger: This component increases the air intake into the engine, improving combustion efficiency and power output.
Understanding these key components highlights the intricate design of diesel engines and emphasizes the significance of maintaining these parts effectively.
Role of Fuel Injection in Diesel Engines
Fuel injection plays a central role in diesel engines. It is a process that precisely delivers fuel into the combustion chamber. This delivery ensures efficient operation and optimal engine performance. Fuel injection directly affects fuel economy, emissions, and overall power output. Understanding its importance provides insight into how diesel engines function.
Importance of Fuel Injectors
Fuel injectors are the linchpins of the fuel injection system in diesel engines. Their primary function is to atomize the fuel. This atomization allows for better mixing of fuel and air, which leads to more efficient combustion. Inadequate atomization can result in incomplete combustion, which not only wastes fuel but also increases harmful emissions. Therefore, the design and functionality of fuel injectors is crucial.
Efficient injectors contribute to improved power output. They can increase horsepower while optimizing fuel consumption. For a diesel engine, this translates into lower operational costs.
"Properly functioning fuel injectors are vital for maximizing engine performance and minimizing emissions."
Moreover, fuel injectors need to deliver the correct amount of fuel at precisely the right moment. This timing significantly influences the combustion process. If fuel is injected too early or too late, it can lead to knocking or stalling. Hence, the role of injectors extends beyond mere fuel delivery; they also manage combustion timing, which is essential for engine longevity.
Fuel Injection vs. Carburetion
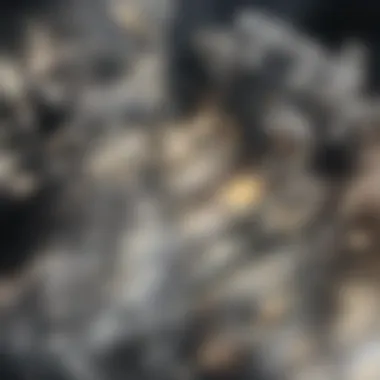
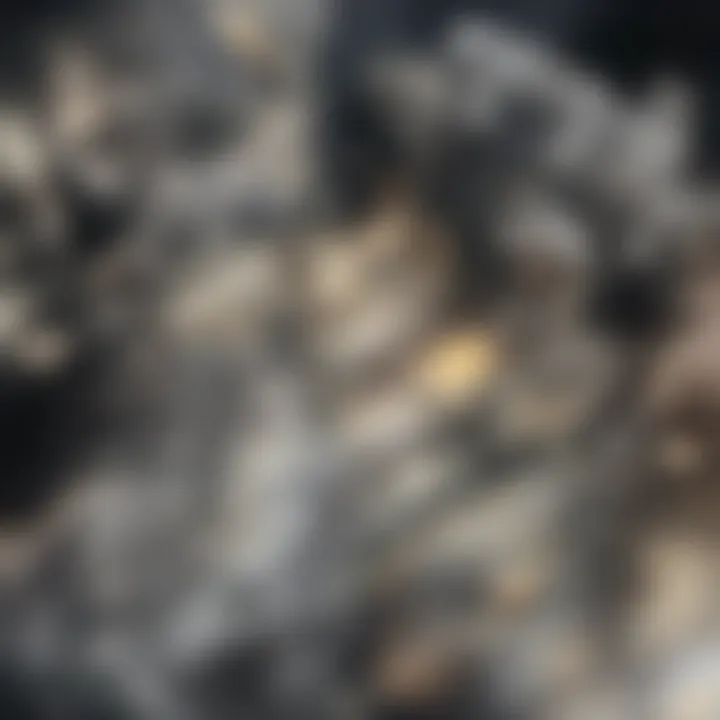
Fuel injection and carburetion are two methods for mixing fuel and air prior to combustion. Carburetors were the standard in older internal combustion engines, but fuel injection has become predominant in diesel engines for various reasons.
- Efficiency: Fuel injection systems are generally more efficient than carburetors. They deliver fuel directly to the combustion chamber, allowing for a more precise air-fuel mixture.
- Control: Injectors provide better control over fuel delivery, adjusting based on engine demand. Carburetors, in contrast, rely on a more passive method of fuel delivery that cannot react as quickly to changes in engine load.
- Emissions: Fuel injection systems offer improved emissions control. By optimizing the air-fuel mixture, they contribute to cleaner combustion and lower emissions of particulates and greenhouse gases.
- Cold Starts: Modern fuel injectors also perform better during cold starts compared to carburetors, which can struggle to provide the right mixture.
In summary, the transition from carburetion to fuel injection in diesel engines reflects advancements in technology aimed at enhancing performance, efficiency, and environmental sustainability.
Types of Fuel Injectors Used in Diesel Engines
Fuel injectors are critical components in diesel engine technology. They play an essential role in determining engine efficiency, performance, and emissions. Understanding the different types of fuel injectors is crucial for anyone studying or working in automotive technology. Each type of injector has unique characteristics. These differences impact both the functioning of the diesel engine and the overall driving experience.
Mechanical Fuel Injectors
Mechanical fuel injectors have been used in diesel engines for many years. They operate through basic mechanical principles. The injector is controlled by the engine's fuel pump, which supplies the pressurized fuel. When the injector opens, it sprays the fuel directly into the combustion chamber. This method is simpler and typically more robust. Mechanical designs tend to be less complex and less susceptible to electronic failure.
However, they do have limitations. Mechanical injectors usually do not allow for precise fuel metering. This can lead to less efficient combustion. They also tend to be less responsive to changes in engine conditions. Because of these limitations, they are becoming less common in newer diesel engines.
Electronic Fuel Injectors
Electronic fuel injectors represent a significant advancement in diesel technology. These injectors use electronic control units to regulate fuel delivery. The injector opens by receiving signals from the engine's computer. This allows for highly accurate fuel metering. Electronic injectors lead to better fuel economy and reduced emissions.
Additionally, they can adapt to various engine conditions. They adjust the amount of fuel injected based on factors like temperature or load. This flexibility allows for improved performance under a variety of circumstances. The complexity of electronic systems, however, can lead to more potential failure points.
Common Rail Fuel Injection Systems
Common rail fuel injection systems are among the most efficient types used in modern diesel engines. In this system, a single, high-pressure fuel rail supplies multiple injectors. Each injector can operate independently, allowing for precise control over fuel delivery.
This flexibility enables multiple injections per combustion cycle. This results in better atomization of fuel. As a result, it enhances combustion efficiency and reduces harmful emissions. Common rail systems also allow for a range of operating pressures, improving overall performance across different RPM ranges.
Components of Fuel Injectors
In diesel engines, the components of fuel injectors serve as a crucial link in the chain of fuel delivery and combustion. Understanding these components is essential for appreciating how they contribute to the engine's efficiency and performance. Each element has its specific function, and their interaction ensures optimal fuel atomization and precise combustion timing.
Nozzle Designs
The nozzle design of fuel injectors plays a central role in delivering fuel into the combustion chamber. Different designs influence how fuel is atomized, which affects combustion efficiency. Common designs include single-hole and multi-hole nozzles, each having distinct advantages based on the engine's requirements. For instance, a multi-hole nozzle can produce finer fuel spray patterns, improving mixing with air and thus enhancing combustion.
Factors like the angle of injection and the shape of the nozzle significantly impact the spray characteristics. These aspects are crucial for minimizing emissions and maximizing power output. Furthermore, advancements in nozzle technology continue to evolve. Newer designs aim to optimize performance while reducing environmental impact.
Fuel Injection Pump
The fuel injection pump is another critical component that ensures the fuel is delivered at the required pressure. This pump pressurizes the fuel before it reaches the injectors, making it possible for the fuel to be atomized appropriately upon injection. The pressure is vital as it affects the spray pattern and particle size of the fuel.
There are various types of fuel injection pumps, including inline and rotary pumps, each suited to different engine types. For example, inline pumps tend to be more efficient for high-output engines, while rotary pumps provide better control for smaller engines. Understanding the functionalities of these pumps helps in diagnosing performance issues in diesel engines.
Control Mechanisms
Control mechanisms regulate the timing and amount of fuel injected into the combustion chamber. These can be mechanical or electronic, with electronic systems becoming increasingly prevalent in modern diesel engines. The precision of these mechanisms directly affects fuel economy and emissions.
Electronic control units (ECUs) monitor various engine parameters and adjust the fuel injection timing accordingly. This responsiveness is especially important for meeting stringent emissions standards. In older models, mechanical adjustments were often made through springs and levers, which, although effective, lacked the precision of modern systems.
"The integration of advanced control mechanisms in fuel injectors marks a significant shift towards efficiency and reduced emissions in diesel engines."
Operational Mechanics of Fuel Injectors
Understanding the operational mechanics of fuel injectors is crucial for examining their efficiency and influence on diesel engines. The fuel injector's role is not merely about delivering fuel; it involves a complex interplay of timing, pressure, and design, all of which contribute to optimal engine performance. Misunderstandings about these operations can lead to reduced performance and increased emissions.
Fuel Delivery Process
The fuel delivery process begins at the fuel tank, where diesel fuel is stored. The fuel is pumped into the injection system, where it is pressurized before being injected into the combustion chamber. This pressure is essential; without it, the fuel would not atomize properly, leading to inefficient combustion. Fuel injectors utilize various designs to optimize this delivery.
- Types of delivery:
- Continuous injection: Common in older systems, it maintains a steady flow of fuel.
- Pulse-width modulation: Used in modern systems for more precise control, adjusting the length of injection depending on engine demands.
The injector opens at the moment predetermined by the engine control unit (ECU), allowing the precise amount of fuel to enter the chamber. This timing is critical; too early or too late can lead to poor combustion. Moreover, achieving the right droplet size during atomization ensures uniform mixing with air, which maximizes efficiency and power output.
Injection Timing and Pressure
Injection timing and pressure must be carefully coordinated to achieve optimal engine performance. The injection timing refers to the exact moment when the fuel is injected into the cylinder relative to the position of the piston. If the injector fires too soon, it can lead to engine knocking. If it fires too late, the mixture may not burn entirely, resulting in wasted fuel and increased emissions.
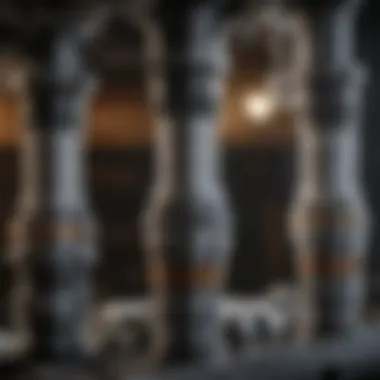
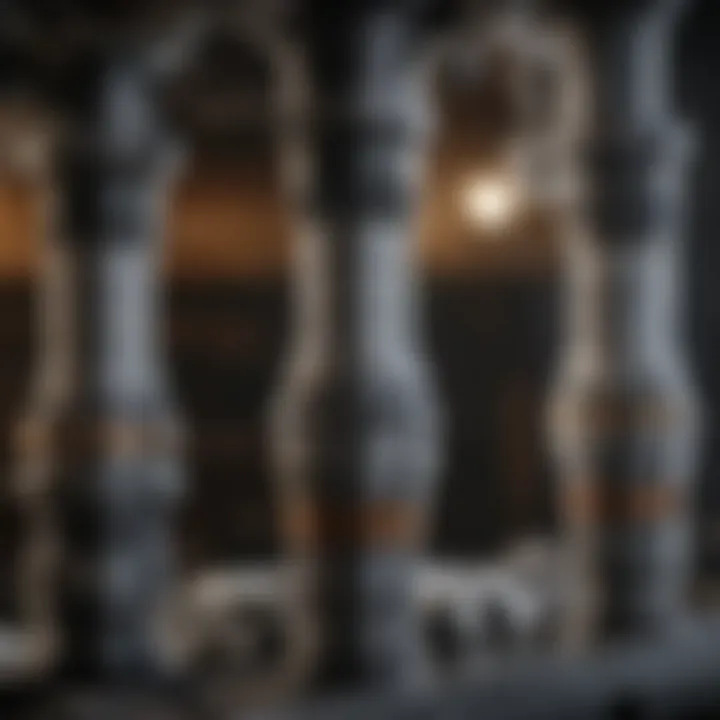
- Factors affecting timing:
- Engine speed
- Load conditions
- Ambient temperature
Similarly, injection pressure is another critical aspect. Higher pressure allows for better atomization of the fuel, enabling it to mix thoroughly with air for more complete combustion. Modern common rail systems can maintain pressures up to 2000 bar or more, significantly improving performance when compared to traditional systems. In comparison:
- Older systems often operated around 300 to 500 bar.
- Present-day systems provide flexibility and control, allowing adjustments based on demand.
Effects on Engine Performance
Fuel injectors play a significant role in the overall performance of diesel engines. Their function goes beyond merely introducing fuel into the combustion chamber. An efficient fuel injector can greatly influence numerous aspects of engine performance, including efficiency, fuel economy, and emissions.
Efficiency and Fuel Economy
The efficiency of a diesel engine is largely contingent on the optimal operation of its fuel injectors. When injectors deliver the right amount of fuel at the correct pressure and timing, it leads to a more complete combustion process. Incomplete combustion can result in wasted fuel and energy.
This is crucial for maximizing fuel economy. A high-performing injector ensures that the engine operates smoothly, generating more power while consuming less fuel. Modern high-pressure common rail systems exemplify this, allowing for precise fuel delivery. By utilizing multiple injections during a cycle, these systems optimize the combustion process, enhancing torque and overall performance. Compared to older injection technologies, they can improve fuel efficiency by a noticeable margin.
Factors affecting injector efficiency include:
- Injector design: Various designs influence atomization and fuel distribution.
- Injection timing: Precise timing can enhance performance and efficiency.
- Fuel quality: Higher quality fuels can improve injector performance.
Emissions Control
A further crucial element of fuel injectors is their influence on emissions control. As environmental regulations tighten worldwide, the role of fuel injectors becomes even more prominent in reducing harmful emissions. Injectors that operate effectively can help achieve the required air-to-fuel ratio, thereby minimizing unburnt hydrocarbons and particulate matter in the exhaust.
Innovative injector technologies, such as those equipped with piezoelectric actuators, have shown great promise in controlling injection patterns and timing. Such advancements allow for multiple injection events during a single cycle, ultimately leading to a cleaner burn. Less residual fuel contributes to reduced emissions, making it easier for diesel engines to comply with stringent regulations.
Key points regarding emissions and injectors include:
- Proper atomization: Better fuel atomization results in more complete combustion.
- Adaptive injection strategies: Systems that adapt to different driving conditions can manage emissions effectively.
- Maintenance: Regular maintenance ensures that injectors function properly, thereby reducing emission levels.
Maintenance and Troubleshooting
Maintenance and troubleshooting of fuel injectors is vital for the optimal operation of diesel engines. Ensuring that injectors function properly can significantly impact engine performance, efficiency, and longevity. Poor maintenance can lead to various issues, such as increased fuel consumption, emissions problems, and eventually engine damage. Thus, implementing effective maintenance practices is essential.
Common Issues with Fuel Injectors
Fuel injectors can face several issues that affect their performance. Some prevalent problems include:
- Clogging: Over time, fuel injectors can become clogged due to impurities in diesel fuel. This restricts the flow of fuel, leading to poor combustion and reduced engine power.
- Leakage: Damaged fuel injectors may leak fuel, which can cause a decrease in performance and increase emissions. Fuel leakage can also lead to fuel dilution in the oil, harming engine components.
- Electrical Failures: Electronic fuel injectors rely on electrical signals. Faulty wiring or poor connections can prevent them from operating correctly, leading to inconsistent fuel delivery.
- Wear and Tear: Continuous operation can lead to wear in injector components, affecting spray patterns and injection timing. This can result in inefficient fuel use and increased emissions.
Monitoring these issues can help in early detection, preventing major problems before they occur.
Routine Maintenance Practices
Routine maintenance of fuel injectors encompasses several essential practices to ensure their longevity and efficiency. Following are some standard procedures:
- Regular Fuel Filter Replacement: Keeping the fuel filter clean is crucial. It prevents contaminants from reaching the injectors, minimizing the risk of clogging.
- Injector Cleaning: Periodic cleaning can remove built-up deposits. This can be done using specialized cleaning solutions or ultrasonic cleaning processes.
- Fuel Quality Checks: Monitoring fuel quality is important. Using high-quality fuel with the right specifications can prevent injector issues stemming from impurities.
- Injector Testing: Routine testing of injectors can provide insights into their performance. This might involve measuring injection pressure, spray pattern, and total fuel delivery.
- Monitoring Engine Performance: Observing changes in engine performance, such as increased fuel consumption or rough idling, can indicate injector issues. Regular diagnostics can help identify and address problems quickly.
Proper maintenance practices lead to improved injector function, enhanced fuel efficiency, and decreased emissions. This ultimately sustains engine life and performance.
"Effective maintenance strategies can decrease costs associated with engine repair and improve overall engine performance."
Ensuring a consistent maintenance schedule allows for early detection of problems and contributes to the overall efficiency of the diesel engine.
Recent Technological Advancements
Technological advancements in fuel injector systems have transformed diesel engine performance and efficiency. The trend towards innovation is not only a response to environmental regulations but also driven by the demand for improved fuel economy and reduction in emissions. With the ongoing research and development in this field, the significance of these advancements can not be overstated. They enhance the precision of fuel delivery, refine combustion processes, and ultimately lead to better engine performance.
Injector Technology Innovations
Recent developments in injector technology have significantly impacted how diesel engines operate. One of the main innovations is the adoption of multi-hole nozzle designs. This design allows for a finer fuel atomization, promoting more complete combustion. Enhanced fuel atomization results in improved thermal efficiency and lower emissions.
The integration of piezoelectric actuators with fuel injectors represents another critical advancement. These actuators offer rapid response times and precise control over injection timing. This precision leads to better performance, particularly in terms of engine power and torque. The ability to control the injection pattern has become increasingly important, especially in high-performance diesel engines.
"Innovative injector technologies can lead to significant reductions in NOx and particulate emissions, enhancing compliance with stringent regulatory standards."
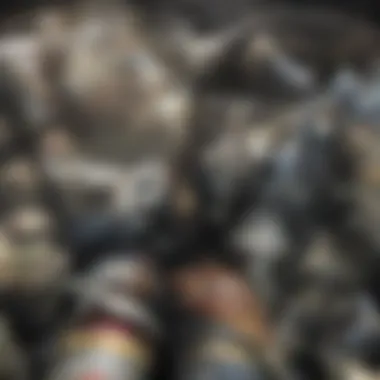
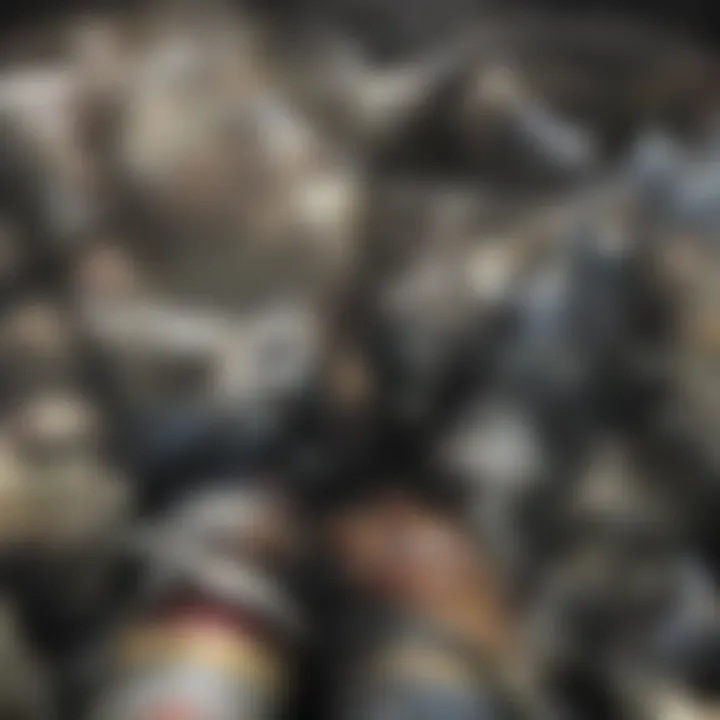
Smart Fuel Injection Systems
Smart fuel injection systems leverage modern sensors and electronic control units to optimize fuel delivery in real-time. These systems can adjust the fuel injection quantity and timing based on various parameters, including engine temperature, load, and speed.
Key features of smart systems include:
- Adaptive Strategies: They adapt injection strategies for different driving conditions, enhancing efficiency and responsiveness.
- Diagnostics: The systems can also provide diagnostic capabilities, allowing for on-the-fly adjustments and maintenance alerts.
- Integration with Hybrid Systems: They are often designed to work seamlessly with hybrid technologies, making diesel engines more versatile.
The ability to maintain optimal performance while meeting environmental standards makes smart fuel injection systems a fundamental component of future diesel engine designs, balancing performance and sustainability.
Impact of Fuel Quality
Fuel quality has a significant role in the performance and efficiency of diesel engines. It affects how well the engine operates and the longevity of its components. High-quality fuel ensures better combustion, which leads to improved engine performance, while low-quality fuel can cause a range of problems.
Fuel Specifications
Fuel specifications refer to the standards and requirements that diesel fuel must meet to ensure optimal use in engines. These specifications include parameters like cetane number, sulfur content, and density.
- Cetane number is crucial as it measures how easily the fuel ignites. Higher cetane numbers mean better combustion efficiency.
- Sulfur content is important because lower sulfur levels lead to reduced emissions and better environmental performance. Different regions have specific regulations regarding allowable sulfur content in diesel fuel.
- Density can influence the fuelโs energy content and how it interacts with other engine components.
Understanding these specifications helps users select the right fuel for their engines, contributing to efficiency and longevity.
Effects on Injector Performance
The quality of the fuel used directly impacts injector performance. When high-quality fuel is used, injectors can operate efficiently, ensuring proper atomization and spray pattern. This leads to more complete combustion and lower smoke emissions.
Conversely, low-quality fuel can lead to problems such as:
- Clogging of injectors due to impurities
- Poor performance from incomplete combustion, which raises emissions
- Increased wear on engine components, leading to higher maintenance costs
In summary, maintaining high fuel quality is essential not only for injector performance but also for the whole diesel engine system. It reduces the risk of damage and promotes a cleaner engine operation, ultimately benefitting performance, economy, and environmental compliance.
Future Trends in Diesel Engine Technology
Future trends in diesel engine technology are shaping the landscape of the automotive industry. These developments are prompted by a range of factors, including environmental regulations, the demand for fuel efficiency, and advances in engineering. Understanding these trends is crucial in the context of fuel injectors and their role in maximizing the potential of diesel engines. This section delves into two significant trends: the rise of alternative fuels and emerging injection technologies.
The Rise of Alternative Fuels
The shift towards alternative fuels is increasingly important due to environmental considerations. Diesel fuel, while efficient, contributes to greenhouse gas emissions. Alternative fuels such as biodiesel, compressed natural gas, and hydrogen are being explored as viable options. Here are some key points regarding these fuels:
- Biodiesel: Made from renewable resources, it can reduce emissions significantly while maintaining comparable performance to standard diesel.
- Natural Gas: Offers a cleaner combustion process, leading to lower emissions, though infrastructure for refueling is a limitation.
- Hydrogen: Has potential for zero emissions but faces challenges with storage and distribution.
Adopting these alternative fuels can help achieve stricter regulatory measures. Fuel injectors play a critical role in optimizing the performance of engines running on these fuels. They need to be adaptable to various fuel properties to ensure efficient combustion.
Emerging Injection Technologies
Advancements in injection technologies lead to improved performance in diesel engines. Technologies such as Multiple Injection Strategies and Piezoelectric Injectors are becoming more prevalent. Key developments include:
- Multiple Injection Strategies: Allowing for precise control over fuel delivery improves combustion efficiency and reduces emissions.
- Piezoelectric Injectors: Offer faster response times, enabling multiple injections within a single cycle, thus enhancing fuel atomization and overall engine performance.
"The evolution of fuel injection technologies is crucial for meeting regulatory requirements and enhancing fuel efficiency in diesel engines."
These technologies address the necessity for increased efficiency and decreased emissions in modern diesel engines. The ability to adapt fuel injector systems to work with emerging fuels and changing regulations will significantly influence the future of diesel engines.
With the continuation of innovation in fuel injectors, the diesel engine can remain competitive against other powertrains. Diesel engines must evolve alongside fuel injector technologies to embrace sustainable practices and meet consumer demands for efficiency.
The End
In this article, we have examined the vital role of fuel injectors in diesel engines. This section summarises important aspects while highlighting the necessity of understanding fuel injectors within the wider context of diesel engine performance and efficiency. Fuel injectors are key components that directly affect engine functionality, impacting everything from fuel consumption to emissions output. Their performance dictates the overall operation of the engine, influencing efficiency and overall power generation.
Summation of Key Insights
Understanding fuel injectors leads to several benefits:
- Enhanced Performance: Precise fuel delivery improves combustion efficiency, resulting in better engine performance.
- Cost Savings: Well-maintained fuel injectors can reduce fuel costs through increased efficiency.
- Reduced Emissions: Properly functioning injectors help minimize harmful emissions, aligning with environmental regulations.
It is clear that the role of fuel injectors extends beyond mere mechanics; they contribute to the reliability and performance of diesel engines. Knowledge in this area is essential for students, researchers, and professionals aiming to optimize engine performance or engage in diesel technology advancements.
Future Directions for Research
As the automotive industry evolves, future research could focus on:
- Advanced Injector Technologies: Exploring more efficient designs and materials that enhance performance while remaining cost-effective.
- Alternative Fuels Impact: Examining how different fuel types affect the operation and longevity of fuel injectors in diesel engines.
- Smart Systems Integration: Investigating how digital control systems can improve injector performance through adaptive strategies.
Researchers should aim to deepen the understanding of how fuel injectors interact with modern diesel engine technologies. This exploration will help align injector performance with future sustainability goals in the automotive sector.