Understanding Epoxy Outgassing: Causes and Effects
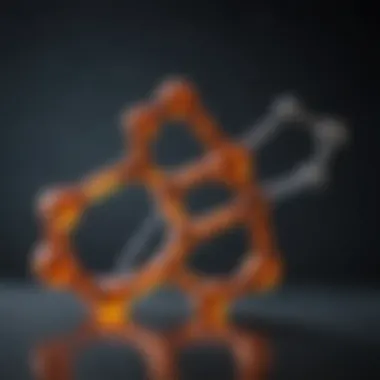

Intro
In various industries, the choice of materials is crucial, especially when it comes to performance and durability. One such material, epoxy, is widely recognized for its excellent adhesive properties and mechanical strength. However, there is a significant aspect often overlooked: epoxy outgassing. When epoxy is cured, it can release gases trapped within its structure. This phenomenon, known as outgassing, is especially critical in fields such as aerospace, electronics, and fine arts.
Understanding outgassing is not just academic; it has tangible implications for product functionality and appearance. In aerospace, for instance, the integrity of composite materials may be compromised if outgassing occurs during critical phases of flight. Similarly, in electronics, microchips and components can suffer from performance issues if gas release disrupts their assembly or operation. In the fine arts, the preservation of artworks is at risk when outgassing affects materials used in restoration or display.
This article will explore the mechanisms behind epoxy outgassing, its causes, and its impact across multiple applications. By delving into the chemistry of epoxy formulations and the external factors influencing outgassing, we can develop a well-rounded understanding of this significant issue. Furthermore, the article will present best practices for mitigating outgassing effects, which is essential for professionals and researchers in the field.
With this background in mind, it is evident that a thorough comprehension of epoxy outgassing is vital not only for material scientists but also for practitioners in various industries. Let's delve deeper into the key findings regarding this phenomenon.
Intro to Outgassing
Outgassing is a critical phenomenon that affects various applications, particularly in fields like aerospace, electronics, and fine arts. Understanding this process is crucial for improving material performance and ensuring durability. This section will provide foundational knowledge about outgassing, explaining its significance and the broader implications it carries.
Defining outgassing is the first step to recognizing its importance. This phenomenon occurs when volatile compounds, previously trapped within a material, are released as gas. Such gases can originate from multiple sources, including the curing agents in epoxies. The implications of outgassing are significant across several industries. It may affect adhesion, material integrity, and overall performance in practical applications.
An overarching consideration in this area is how outgassing can lead to undesirable outcomes. In aerospace, outgassing can cause issues with equipment performance, while in electronics, it may lead to failures and reduced lifespan of components. The fine arts are equally affected, with outgassing undermining the restoration efforts of valuable artifacts. Recognizing these challenges encourages stakeholders and professionals to develop better strategies to mitigate the risks associated with outgassing.
Each application has unique implications, but they share a common thread: the need for a comprehensive understanding of outgassing. The more we know about its causes and effects, the better we can manage it.
"In understanding outgassing, we unlock the potential for improving quality across various fields."
To lay the groundwork for this exploration, the next section will delve into the specific definition of outgassing, shedding light on this multifaceted process.
Understanding Epoxy Resins
Epoxy resins represent a vital substrate in numerous industrial applications. Understanding their composition and types is essential for grasping how outgassing can affect performance. These resins are unique due to their impressive adhesive properties and mechanical strength. They form a durable bond when cured, making them valuable in sectors such as aerospace, electronics, and art. The exploration of epoxy resins sheds light on their predisposition to outgassing, which can lead to adverse effects depending on their application.
Chemical stability and thermal resistance are also significant attributes of epoxy resins. However, the inherent solvents or residual components can outgas and create defects in the final product. This technical nuance underlines the importance of comprehending the components and systems of epoxy resins.
Composition of Epoxy Resins
Epoxy resins are predominantly composed of epoxide groups, which are three-membered cyclic ethers. These groups undergo a curing process when combined with suitable hardeners, leading to a thermosetting polymer. The primary constituents are:
- Epoxy Monomers: These are raw materials which contain epoxide functional groups. Bisphenol A and diglycidyl ether are common examples.
- Hardening Agents: Also known as curing agents, these compounds react with epoxy monomers. Common hardeners include amines and anhydrides. The selection of hardeners can drastically influence flexibility, heat resistance, and curing time.
- Additives: These may enhance certain properties such as UV resistance, flame retardance, or anti-corrosion effects. Incorporating these additives can introduce more variables to consider in outgassing behavior.
The correct formulation of these elements is crucial for the performance and stability of epoxy. Any variations in composition can affect both the degree of outgassing and the resultant material properties. Safe and effective production requires a detailed understanding of these chemical interactions.
Types of Epoxy Systems
Understanding the diverse types of epoxy systems is important for selecting the right formulation for specific applications. Each system comes with distinct characteristics and potential for outgassing.
- Liquid Epoxy Systems: Typically involve higher viscosity and are suitable for processes requiring precision, such as electronics. They tend to have a higher solvent content, which can increase outgassing risks.
- Solid Epoxy Systems: More compact formulations that generally exhibit lower levels of outgassing. These systems are often used in structural applications where strength is paramount.
- Modified Epoxy Systems: These are engineered with additional materials, like rubber or other polymers, to enhance toughness and minimize brittleness. While beneficial, these modifications can also introduce new components that may outgas.
- High-Temperature Epoxy Systems: Formulated to withstand elevated temperatures, these resins aim to retain performance under stress. However, the curing agents used in these systems may contribute to outgassing.
By considering the characteristics and implications of each type, manufacturers can better manage issues related to epoxy outgassing. Choosing the right system affects not only performance but also the longevity and integrity of the product.
Mechanisms of Outgassing in Epoxy
The mechanisms of outgassing in epoxy are crucial for understanding its implications across various industries. The release of gas from epoxy materials can compromise integrity and performance in applications where precision is paramount. This section will explore the chemical processes that lead to outgassing, as well as the environmental factors that affect the rate and extent of gas release. Insights into these mechanisms not only enhance the understanding of material behavior but also inform strategies for developing more effective epoxy systems.
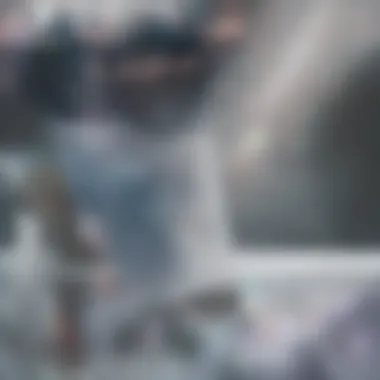

Chemical Processes Involved
Outgassing in epoxy is primarily a result of chemical reactions that occur during the curing process. When epoxy resins undergo polymerization, several volatile substances can be produced, including solvents, low-molecular-weight by-products, and moisture trapped in the material.
The curing agents, such as amines or anhydrides, often play a significant role in determining the extent of outgassing. Their chemical structure influences the volatility of the by-products.
In addition, temperature can dramatically alter the reaction kinetics, potentially increasing gas production. Understanding these chemical processes is critical for anticipating how an epoxy formulation will perform in real-world scenarios.
Factors Influencing Outgassing
Several factors significantly impact the outgassing behavior of epoxy resins. These include temperature, humidity, and pressure. Each of these factors introduces unique conditions that can exacerbate or mitigate the release of gases.
Temperature
Temperature plays a pivotal role in the outgassing process. Higher temperatures typically accelerate the curing process, leading to increased volatility of chemical by-products. This heat can enhance the kinetic energy of molecules, causing them to escape from the polymer matrix more readily.
A key characteristic of temperature influence is its dual nature. While elevated temperatures can expedite curing times, they can also lead to excessive outgassing if not controlled properly. The unique feature of temperature is that it can be a double-edged sword—it produces faster curing, yet risks compromising the performance of the epoxy.
Humidity
Humidity is another essential factor affecting outgassing in epoxy systems. The presence of moisture in the environment can correlate directly with the amount of volatile substances released from the material. High humidity conditions can lead to water vapor being trapped within the epoxy during the curing phase.
This retention of moisture can result in greater outgassing once the material is subjected to drying conditions. Importantly, the interaction between humidity and temperature can compound these effects, making it vital to monitor both environmental factors when working with epoxy.
Pressure
Finally, pressure influences outgassing behavior significantly. Lower atmospheric pressures allow gases to escape more easily from the material, increasing the likelihood of outgassing. This effect is particularly critical in applications like aerospace, where components experience varying pressures during flight.
The unique aspect of pressure in this context is that it directly affects material integrity. On the other hand, maintaining higher pressures during the curing process can help trap gases within the matrix, reducing the overall risk of outgassing. Understanding these pressure dynamics is fundamental for engineers and researchers focused on preventing outgassing in sensitive applications.
These factors—temperature, humidity, and pressure—combined with an awareness of the chemical processes involved, contribute to a holistic understanding of outgassing mechanisms in epoxy materials. Recognizing their implications assists in developing better strategies for mitigating the risks presented by outgassing.
Implications of Outgassing
The implications of outgassing in epoxy materials span across various industries, impacting not only the material’s performance but also the longevity and reliability of products. Understanding these implications is crucial for developers, engineers, and researchers involved in the design and application of epoxy resins. Outgassing can lead to deteriorated performance, affecting the structural integrity and operational functionality of devices and components in critical applications. Therefore, a thorough grasp of this phenomenon enables stakeholders to make informed decisions in material selection and processing techniques.
Impact on Material Performance
The performance of epoxy resins can vary significantly due to outgassing. When volatiles escape during the curing process, they create voids or bubbles in the final product. This porosity compromises mechanical strength, adhesion, and thermal stability. Specifically, the impact on tensile strength and flexural modulus can be notable, leading to premature failure under stress. For instance, in structural applications, this might result in safety hazards or structural inadequacies, as excessive outgassing can reduce load-bearing capabilities.
To mitigate these risks, selection of high-quality raw materials is essential. Manufacturers often conduct rigorous testing to determine the outgassing potential of specific epoxy formulations, ensuring that the final products meet performance standards.
Consequences in Electronics
In the electronics sector, outgassing poses unique challenges, particularly regarding the reliability and lifespan of sensitive components. For example, in semiconductors and circuit boards, the escape of gases can lead to contamination of surfaces or create areas where electrical shorts can occur. This outgassing in enclosed spaces, like circuit enclosures or multilayer boards, can degrade insulating properties over time.
Moreover, issues can arise during the soldering process. If outgassing occurs, the released gases can cause defects such as solder voids, affecting the electrical connections and overall performance of the circuit. Industry standards often necessitate stringent control measures and testing to minimize these outgassing effects, underscoring the importance of understanding this problem in electronics manufacturing.
Effects in Aerospace Applications
Aerospace applications are particularly sensitive to outgassing due to the high-performance standards mandated in this field. Epoxy resins are frequently used in composite materials for airframes and components. The implications of outgassing here can be severe, as volatile release may lead to reduced composite strength, increased weight, and potential failure under operational stresses.
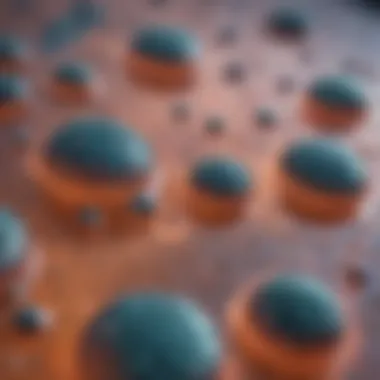

Furthermore, the vacuum environment experienced during flights can exacerbate these effects. Gas trapped within the epoxy matrix can form bubbles at high altitudes, which can compromise both the safety and efficiency of aircraft. As a result, engineers must meticulously select and evaluate epoxy formulations for aerospace projects, focusing on minimizing outgassing to maintain structural integrity.
Influence on Art and Historical Preservation
Outgassing is not restricted to industrial applications; it also significantly affects the fine arts and historical preservation. In the realm of art conservation, epoxy resins are used for repairing and restoring artifacts. However, these materials must be chosen carefully to avoid any chemical interactions that might arise from outgassing.
The release of volatiles can lead to discoloration, deterioration, or even irreversible damage to sensitive artworks. Conservators must balance the benefits of using epoxy for structural integrity with the potential risks associated with outgassing. Important considerations include using low-outgassing materials and maintaining controlled environments during the application to protect cultural heritage.
Understanding the implications of outgassing is vital across various fields because it systematically informs material selection, processing, and ultimately the success of applications in critical environments.
Mitigation Strategies for Outgassing
Addressing the challenge of outgassing in epoxy materials is vital for enhancing product reliability and performance across various industries. As epoxy applications grow, understanding and implementing mitigation strategies will prevent unwanted gas release, which could adversely affect mechanical properties, electrical performance, and aesthetic qualities.
Selecting Appropriate Epoxy Formulations
The initial step in reducing outgassing is the careful selection of appropriate epoxy formulations. Different epoxy resins have distinct chemical compositions, which influence their propensity to outgas. For instance, some formulations utilize lower viscosity resins that can trap fewer gases. Always consult the technical data sheets provided by manufacturers to find formulations specifically designed to minimize outgassing.
A few factors to consider in this context include:
- Viscosity: Lower viscosity resins may allow for better air release during curing.
- Filler Materials: Certain fillers can change gas permeability properties.
- Curing Agents: Selecting agents that promote complete curing can reduce the potential for gas formation.
Controlled Curing Processes
A well-managed curing process plays a crucial role in mitigating epoxy outgassing. The curing temperature and duration must be closely monitored. Too fast or uneven curing rates can trap gases within the epoxy. An ideal curing process should include gradual temperature increases and sufficient time for the epoxy to cure completely.
Some critical steps involve:
- Temperature Ramp-Up: Implement a slow increase in temperature to avoid rapid gas expansion.
- Extended Cure Times: Allow sufficient time for all chemical reactions to complete, minimizing the risk of trapped gases.
- Vacuum Curing: Using a vacuum chamber during the curing process can help to remove any residual air or dissolved gases, leading to improved epoxy quality.
Environmental Considerations
Environmental factors significantly influence outgassing behavior in epoxy systems. Humidity and atmospheric pressure can both affect the rate of gas release and the overall performance of the material. High humidity levels can introduce moisture into the mix, leading to unwanted reactions during the curing process.
Key considerations may include:
- Humidity Control: Maintaining a controlled environment with low humidity is essential during application and curing phases.
- Pressure Conditions: Applying vacuum or controlled pressure can help in reducing gas formation during curing.
- Storage Conditions: Proper storage of epoxy materials away from moisture and fluctuations in temperature can also mitigate potential outgassing issues.
"Mitigation strategies must address both formulation and environmental factors to effectively control outgassing in epoxy systems."
Implementing these mitigation strategies necessitates attention to detail and consistency throughout the curing process. By focusing on the selection of formulations, refining curing practices, and carefully monitoring environmental conditions, practitioners can significantly enhance the performance and integrity of their epoxy applications.
Research and Development in Epoxy Outgassing
Research and development play a critical role in addressing the complexities associated with epoxy outgassing. The phenomenon can severely impact material integrity and performance across various industries, making it essential to explore innovative solutions. By focusing on the mechanisms of outgassing, researchers aim to enhance the properties of epoxy formulations. This research contributes to improved reliability and performance in applications such as aerospace and electronics, where outgassing can lead to significant failures.
Additionally, the exploration of new materials and additives can provide insights into reducing or even eliminating outgassing. The findings from ongoing studies inspire the development of advanced manufacturing processes and technologies, ensuring better management of gas emissions in cured epoxy.
Current Studies on Outgassing
Numerous studies are currently being conducted to investigate the nature of outgassing in epoxy and its implications. Researchers are examining the relationship between the chemical composition of epoxies and their tendency to outgas. This involves analyzing how different curing agents and fillers influence the retention and release of gases.
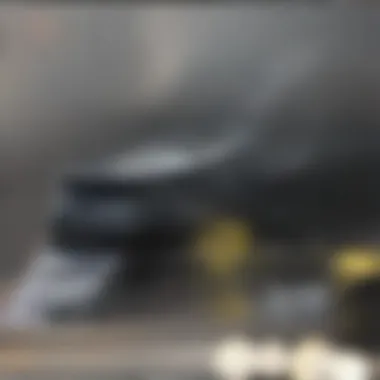

One important focus area is the use of thermal analysis techniques, such as thermogravimetric analysis (TGA), to detect outgassing behavior under various conditions. These studies help in identifying critical parameters—like the temperature and duration of the curing process—that affect the outgassing velocity.
"Understanding the chemistry behind epoxy formulations is key for improving material performance and reducing outgassing rates."
Moreover, interdisciplinary approaches are being undertaken, combining insights from chemistry, engineering, and material science. For example, research into nanomaterials and their applications in epoxy systems is gaining traction. The goal is to create more stable formulations that minimize gas release. Field studies in real-world applications, such as aerospace missions, are providing valuable empirical data.
Future Directions in Research
As the understanding of epoxy outgassing expands, future research is likely to focus on several key areas. First, the development of bio-based or environmentally sustainable epoxy resins presents a promising path. These materials not only reduce environmental impact but may also exhibit different outgassing characteristics.
Second, improved modeling techniques that predict outgassing behavior will become increasingly important. These can aid in the formulation of epoxies tailored to specific applications, aligning with industry needs. Implementing predictive analytics in manufacturing processes could lead to more refined control over outgassing phenomena.
Third, the integration of smart materials that respond to environmental changes may be explored. Such innovations could adjust the thickness of epoxy layers or seal off potentially harmful gas release in critical applications.
Lastly, collaboration between academic institutions and industry leaders will be paramount. Joint efforts can accelerate the transfer of knowledge from research environments to practical applications, ultimately enhancing the performance of epoxy materials in various sectors.
Case Studies on Outgassing
Case studies on outgassing provide critical insights into its real-world impact across various sectors. Understanding how outgassing manifests in practical applications allows for informed decisions in material selection, design processes, and best practices across industries. Analyzing specific instances of outgassing helps identify patterns and potential solutions and also illustrates the significance of addressing outgassing issues for long-term durability and performance.
Outgassing in Aerospace Components
Aerospace components demand the highest performance standards, where even minor defects can have dire consequences. Here, outgassing can severely compromise structural integrity and reliability. A notable example is the use of epoxy resins in composite materials for aircraft structures.
In one documented case, a specific epoxy formulation used in a satellite structure experienced significant outgassing during its launch into space. The outgassed materials contributed to contamination of sensitive equipment onboard, leading to operational failures. Evaluations of this event prompted a reassessment of epoxy choices and application methodologies in aerospace manufacturing. This case emphasizes the necessity of rigorous testing for outgassing properties in epoxy systems intended for use in aerospace applications.
Electronics Manufacturing Experience
In the electronics industry, outgassing can result in malfunctioning devices and reduced product lifespan. One significant study highlighted outgassing in a batch of printed circuit boards (PCBs) manufactured with a certain standard epoxy. During reliability testing, it was noted that emitted gases caused delamination of circuit layers, leading to failures.
The incident led researchers and manufacturers to explore alternative epoxy formulations with lower outgassing tendencies. Furthermore, the findings encouraged tighter control on the manufacturing environment, particularly regarding temperature and humidity, to minimize the potential for outgassing. By learning from these challenges, the electronics industry aims to produce more reliable and sustainable products.
Art Restoration Techniques
Art restoration presents another unique context for understanding epoxy outgassing. Many art pieces, especially those requiring bonding or fill for repairs, utilize epoxy resins. A case in point involved a famous painting that underwent restoration with epoxy adhesives.
The restorers initially overlooked the potential for outgassing, leading to the yellowing of the artwork due to volatile compounds being released. This incident drove home the importance of considering the long-term effects of material choice in art conservation. Contemporary practices now emphasize the selection of epoxy systems tested for low outgassing properties, along with careful monitoring of environmental factors during and after application. This shift highlights the intersection of science and art, revealing how material science can impact cultural heritage preservation.
"Case studies reveal not just problems but also pathways to innovation and better practices in material usage."
In summary, the examination of these case studies underlines the diverse implications of outgassing across different sectors. By scrutinizing these findings, professionals can enhance their practices, ensuring safety, performance, and preservations in aerospace, electronics, and fine arts.
Culmination
In assessing the phenomenon of epoxy outgassing, it is crucial to understand its implications in various fields. Outgassing can significantly impact material performance, particularly in industries like aerospace and electronics. These sectors often rely on the reliability of materials, and any release of gas during curing or application can cause defects, leading to catastrophic failures. Evaluating the conditions that lead to outgassing and understanding how to mitigate them is not just a preference but a necessity for maintaining integrity and functionality in critical applications.
Summarizing Key Insights
Throughout the article, several key points have emerged that underscore the importance of understanding epoxy outgassing:
- Definition and Relevance: Outgassing is defined as the release of gases from a material, which can compromise the performance of epoxy resins. It is vital to grasp this definition to approach mitigation effectively.
- Chemical Mechanisms: The chemical processes involved highlight how various factors during the curing process influence outgassing. Knowledge of these mechanisms can guide the formulation of epoxy systems.
- Environmental Factors: Temperature, humidity, and pressure play significant roles in the extent of outgassing. This knowledge can inform choices in material selection and application.
- Case Studies: Real-world examples from aerospace, electronics, and art restoration illustrate the consequences of outgassing and the importance of managing it.
Final Thoughts on Future Research
For future research, several directions merit attention:
- Innovative Formulations: Continued innovation in epoxy formulation that minimizes outgassing will be critical. Researchers should explore new materials that provide better performance under various environmental conditions.
- Longitudinal Studies: Long-term studies on the effects of outgassing in specific applications can provide deeper insights. This can help shape guidelines and best practices across industries.
- Collaborative Research: Interdisciplinary approaches that draw from chemistry, materials science, and engineering can lead to advancements in outgassing mitigation strategies.