Understanding Engine Test Cells: Key Insights
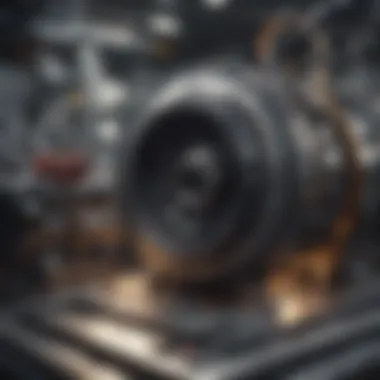
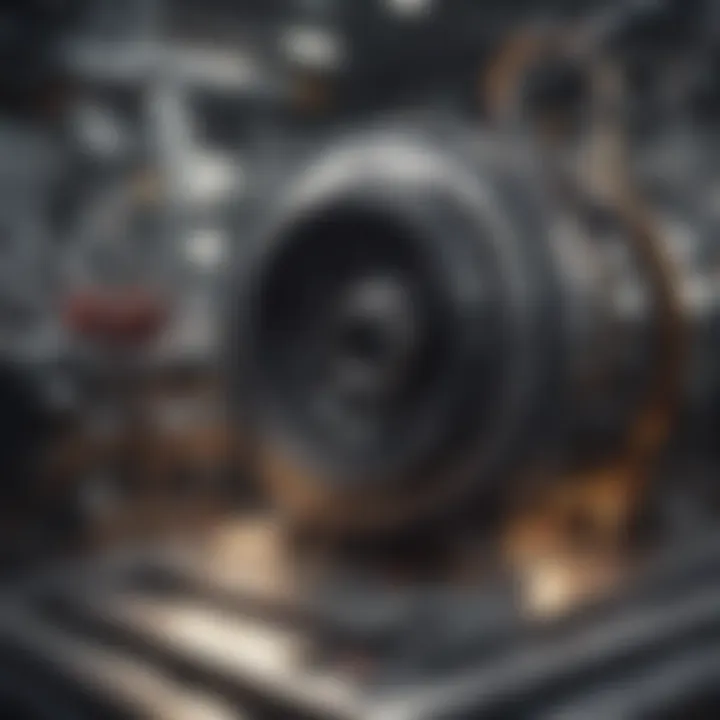
Intro
Engine test cells are essential facilities in the automotive, aerospace, and industrial sectors. Here, engines undergo rigorous testing to evaluate performance, durability, and overall reliability. These specialized environments transform real-world performance expectations into quantifiable data, aiding designers and engineers in refining their products. Whether examining how a turbocharged engine stands up to high-altitude flight or measuring fuel efficiency for an electric vehicle, test cells are at the heart of innovation.
The significance of engine test cells can’t be overlooked. Essentially, they offer a controlled setting where variables can be manipulated and outcomes meticulously measured. This is where theoretical designs are put to the test against rigorous standards.
In this article, we will journey through the intricacies of these advanced facilities. Our exploration will range from understanding the core principles behind their design to analyzing future trends that may shape the landscape of engine development further. By focusing on the engineering principles and methodologies prevalent in these testing environments, a clearer picture emerges, demonstrating just how pivotal these cells are in today's engineering practices.
From vehicle emissions standards to aviation demands, a deeper understanding of engine test cells allows for enhanced reliability and performance in our engines. This guide aims to illuminate these critical areas, providing valuable insights for students, researchers, and professionals alike.
Prologue to Engine Test Cells
Engine test cells serve a pivotal role in the broader scope of engine development and evaluation, acting as specialized environments where engines are put through their paces. The significance of these facilities extends beyond mere functionality; they are the bedrock upon which cutting-edge engineering practices are built. By offering controlled conditions for testing, these cells allow for precise measurement of performance metrics, ensuring that engines meet stringent industry standards and consumer expectations.
Being equipped with advanced instrumentation, test cells enable engineers to gather invaluable data across various parameters such as power output, fuel efficiency, and emissions. This data isn't just numbers on a screen; it forms the foundation of research that drives innovation in automotive, aerospace, and marine industries, among others. In an era where sustainability and efficiency are paramount, the careful testing performed in these cells can inform design choices that lead to more environmentally friendly engines.
The importance of engine test cells can be distilled into three core elements:
- Precision: They provide the necessary conditions to accurately test engine performance, free from external variables.
- Validation: Results from these tests validate engineering designs, reassuring manufacturers and consumers alike that the engines are reliable and safe.
- Innovation: With evolving technologies, test cells are at the forefront of applying new methodologies and tools to improve testing accuracy and efficiency.
Understanding the mechanisms and capabilities of engine test cells is crucial for anyone involved in engine research or development. This foundation enables stakeholders to appreciate the complexities of testing procedures and their implications for future trends and innovations.
Definition and Purpose
Engine test cells, at their core, are carefully designed and constructed spaces, fashioned specifically for evaluating the performance of various engines under controlled settings. They are equipped with sophisticated instrumentation to monitor a multitude of variables such as torque, RPM, and fuel consumption. The fundamental purpose of these facilities can be synthesized into two primary objectives:
- To ensure that engines operate reliably within the parameters of their design during different conditions.
- To facilitate research initiatives that advance engine technology and performance standards.
Engine test cells are collaborators in the engine development process, allowing engineers to explore the limits, performance potential, and failure modes of engines that may be utilized in diverse applications. Their role is nothing short of critical in bridging theoretical engineering principles with practical applications.
Historical Evolution
The journey of engine test cells stretches back to the early days of engine technology. In the beginning, testing was often rudimentary at best. Engineers relied heavily on trial and error, often subjecting engines to harsh operational conditions, primarily on the roads or in the air. However, as engines became more sophisticated, the need for controlled testing spaces became evident.
- Late 19th Century: The rudimentary form of testing environments emerged with simple dynamometers that provided a basic assessment of engine power output.
- Mid-20th Century: War brought about rapid advancements in aerospace and automotive engineering, and with it, the design and capabilities of test cells expanded, incorporating more complex measurements and comfortable operational environments.
- 21st Century: The current era is marked by high-tech facilities featuring computer-controlled test setups. This advancement has led to the integration of data analytics and simulation tools that enhance testing accuracy and efficiency.
Today, the evolution of these test cells is not only a testament to the progression of technology but also to the ever-increasing demands for performance, safety, and environmental consciousness in engine design. Looking back, it is clear that the historical evolution of engine test cells reflects a broader trend within engineering, where precision and reliability are constantly being prioritized.
Types of Engine Test Cells
Understanding the various types of engine test cells is fundamental for anyone involved in engine development and evaluation. These facilities are tailored to meet specific testing requirements and provide the necessary environments to ensure engines perform optimally under different conditions. The type of test cell directly influences the methodology and outcomes of engine testing, making their classification and characteristics essential knowledge for engineers, researchers, and students.
Static Test Cells
Static test cells are designed primarily for performance measurement in a controlled setup, where the engine operates under stationary conditions. In such cells, the engine is typically mounted securely, allowing engineers to focus on precise performance metrics without the influence of vehicle dynamics.
One of the significant advantages of static test cells is their ability to facilitate thorough diagnostics and calibration. Here, operators can manipulate various parameters, such as air-fuel ratios and ignition timing, while closely monitoring emissions and power output. The static nature of the test cell allows for detailed data collection and analysis, which is crucial for optimizing engine performance.
Technically, these cells often feature sophisticated instrumentation, such as:
- Dynamometers for measuring torque and power.
- Data acquisition systems to track numerous performance metrics in real-time.
This type of testing is particularly beneficial in the early stages of engine development, where understanding fundamental characteristics and behavior is critical. Furthermore, static test cells help identify issues related to thermal efficiency and emissions compliance.
Dynamic Test Cells
In contrast to static test cells, dynamic test cells allow for testing engines under moving conditions, which closely simulate real-world operating scenarios. These setups often resemble a vehicle’s operational environment, enabling more realistic assessments of engine behavior, performance, and durability.
Dynamic testing is vital for understanding how an engine interacts with various operational variables, such as:
- Load changes
- Speed variations
- Temperature fluctuations
The main benefit here is the ability to perform comprehensive performance assessments that include how well an engine responds to conditions it will face on the road or in flight. Technically advanced dynamic test cells are equipped with a full array of monitoring systems, which can evaluate not just power and efficiency but also noise, vibration, and harshness (NVH) characteristics. This is particularly important in sectors like automotive and aerospace, where these factors significantly impact user experience.
Another notable feature of dynamic test cells is their adaptability for continuous testing. This allows engineers to quickly adjust parameters and conditions, leading to rapid prototyping cycles and more efficient development timelines.
Engine Simulation Platforms
Engine simulation platforms represent a more recent innovation in testing technology. These platforms utilize computational models to replicate engine behavior before physical testing even begins. Simulations provide a virtual environment where engineers can evaluate performance under a diverse range of conditions and configurations.
This method reduces the need for extensive physical prototypes, thereby trimming down development costs and timelines. One of the standout elements of engine simulation is its ability to visualize outcomes based on theoretical parameters, allowing engineers to innovate more freely without the limitations imposed by physical testing rigs.
The integration of AI and machine learning into simulation platforms helps analyze complex performance data, providing insights that might remain unnoticed in traditional testing methods. This shift to virtual environments also creates opportunities for:
- Enhanced accuracy in prediction models.
- Better optimization of engine performance.
- Comprehensive scenario testing that includes potential real-world failures.
Overall, engine simulation platforms are propelling engine testing into a new era by creating efficient pathways for engineers to test, adapt, and ultimately improve engine designs.
"With each advancement in testing technology, we become a step closer to remarkable efficiencies and innovations in engine development."
Understanding the different types of engine test cells creates a foundation for optimizing engine performance and reliability. Each type offers unique advantages suitable for specific testing needs, and recognizing these distinctions is crucial for effective engine evaluation and development.
Design and Construction of Engine Test Cells
The design and construction of engine test cells are pivotal in ensuring that engines are evaluated under controlled conditions, accurately simulating real-world operating scenarios. In the realm of engine testing, several elements come into play—each with its own significance. An understanding of these elements not only facilitates rigorous testing methodologies but also enhances the reliability of the results garnered. Here, we delve into the structural considerations, acoustic treatment, and the intricate control systems that together make up a robust test cell design.
Structural Considerations
Structurally, an engine test cell must be built to handle the immense forces produced by the engine being tested. The strength and stability of the structure directly affect the safety and integrity of the testing process. The framework typically involves reinforced concrete or steel to ensure it withstands vibrations, heat, and other stresses that occur during operation.
Key aspects include:
- Load-Bearing Capacity: The materials selected must cater to the maximum load capacity of the testing engines.
- Vibration Isolation: Systems must be in place to prevent vibrations from interfering with sensitive testing equipment and data collection instruments. This is often accomplished using specialized mounts and dampeners.
- Space for Expanson: Consideration for future upgrades or modifications is crucial, as engine technology continues to evolve. A flexible design allows for the integration of new testing capabilities without the need for extensive reconstruction.
Ultimately, a well-thought-out structural design fosters both safety and efficiency—allowing engineers to focus on performance metrics without the anxiety of structural failures.
Acoustic Treatment
Incorporating acoustic treatment in engine test cells is not just an afterthought; it's a necessity. Engines generate significant noise, which poses several challenges, from compliance with environmental regulations to the potential detrimental effects on human operators.
Effective strategies for acoustic treatment involve:
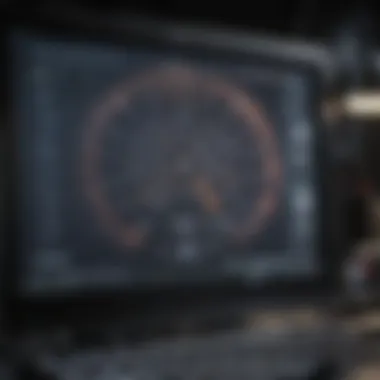
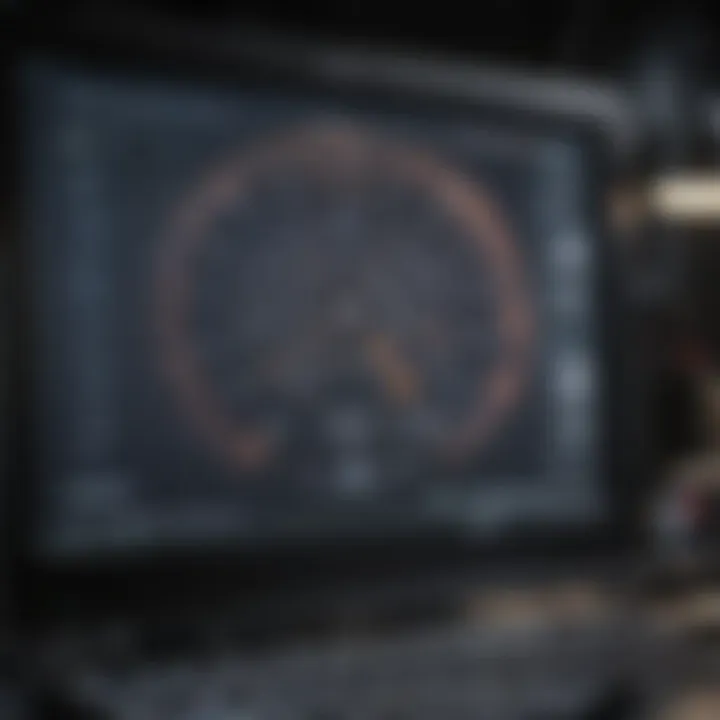
- Soundproofing Materials: The interior walls of the test cell are often lined with sound-absorbent materials, such as mineral wool or acoustic panels, to deaden the noise.
- Design Layout: The arrangement of equipment can also impact sound reflection and absorption. Angles and shapes that reduce echo and vibration transmission are carefully employed.
- Ventilation and Exhaust Systems: Beyond noise, the handling of exhaust gases is vital. Well-designed systems ensure that harmful emissions do not escape into the environment, while also minimizing sound leakage.
By prioritizing acoustic treatment in the design process, facilities not only meet regulatory compliance but also create a more conducive environment for testing.
Control Systems and Instrumentation
High-quality control systems and instrumentation are the backbone of effective engine testing. They enable precise monitoring, measuring, and controlling of engine parameters during tests. The integration of advanced technologies enhances both the accuracy and reliability of test results.
Some essential components include:
- Data Acquisition Systems: These systems collect data from various sensors that monitor real-time performance variables such as engine temperature, pressure, and RPM.
- Automated Control Interfaces: Modern test cells often utilize computerized interfaces to automate the manipulation of test parameters—this minimizes human errors and enhances repeatability in tests.
- Integration Capabilities: The ability to integrate with other systems, such as simulation software or remote monitoring, allows for more flexible and efficient testing protocols.
"The efficiency of engine tests is often dictated by the control systems in place; poor instrumentation can render even the most sophisticated tests useless."
Key Components of Engine Test Cells
Understanding the key components of engine test cells is crucial for grasping how these facilities function. These elements contribute significantly to the accuracy and efficiency of engine testing, impacting everything from data collection to operational performance. By dissecting each component, we gain insight into the importance of meticulous design and implementation.
Dynamometers
Dynamometers play a pivotal role in engine test cells by measuring the power output of an engine under various operating conditions. They effectively simulate the load that an engine experiences in real-world scenarios. This allows engineers to gather empirical data about engine performance, which can be critical for tuning and development.
When selecting a dynamometer, several factors need consideration, such as:
- Type: There are two main types, the eddy current dynamometer and the hydraulic dynamometer. Each serves different purposes depending on the application.
- Range: The dynamometer must be capable of handling the engine's expected power range accurately.
- Software integration: Modern dynamometers often come integrated with software systems that enhance data analysis, transforming raw data into understandable insights.
Investing in a quality dynamometer is not just about performance; it's about ensuring that the data collected is reliable and valid, which can ultimately lead to more efficient engine designs.
Fuel Management Systems
A well-functioning fuel management system is essential for managing how fuel is delivered to the engine during testing. These systems regulate fuel pressure, adjust fuel delivery rates, and monitor fuel quality. This aspect is particularly important since even subtle changes in fuel delivery can lead to significant variations in engine performance.
Key aspects of effective fuel management systems include:
- Precision control: Allows engineers to set specific parameters for testing, ensuring that conditions are as accurate as possible.
- Feedback loops: These systems often feature real-time sensing that adjusts fuel flow based on current engine performance data.
- Compatibility: The system must be compatible with multiple fuel types to accommodate various testing scenarios.
Without precise fuel management, test results could be skewed, leading to misguided conclusions about engine functionality.
Cooling and Lubrication Systems
Engine cooling and lubrication systems are the unsung heroes of any testing procedure. An engine generates significant heat while running, and without proper cooling mechanisms, engines can overheat, leading to inaccurate readings and potential damage. Likewise, lubrication is vital as it minimizes friction between moving parts, ensuring the engine operates smoothly during tests.
Factors to keep in mind when evaluating these systems include:
- Temperature control methods: Whether through liquid or air cooling, maintaining optimal temperature ensures reliability in performance tests.
- Oil types and delivery mechanisms: Using the right type of oil in specific quantities can drastically impact engine behavior during evaluations.
- Monitoring systems: Integrated sensors that provide real-time data on temperature and oil pressure can help engineers make informed adjustments as needed.
"Effective cooling and lubrication not only protect the engine but also maintain the integrity of test results."
Ultimately, these fundamental components of engine test cells are integral to achieving precise measurements and reliable performance assessments. Understanding their significance can greatly enhance the testing process and contribute to more innovative engine designs in the future.
The Testing Process
The testing process is critical in ensuring that engines perform optimally and meet the required standards across various industries. This phase is where theoretical knowledge translates into practical insights, validating designs and verifying performance under controlled conditions. Each step in this process, from preparation to analysis, provides essential feedback that influences subsequent design iterations and manufacturing decisions.
Preparation for Testing
Before an engine can grace the stage in a test cell, ample preparation is essential. Engineers and technicians must first ensure that all equipment is functioning correctly and that the testing parameters are well-defined. This includes:
- Calibration of Instruments: Accurate readings during tests hinge on calibrated devices. If instruments are not calibrated, the results may lead to incorrect conclusions.
- Setting Test Parameters: The specific conditions, such as temperature, pressure, and engine load, must be meticulously set based on the testing objectives.
- Preparing the Test Cell: The test environment itself needs attention. This may involve verifying that the engine mounting is secure and that any necessary cooling or fuel systems are primed and ready.
Attention to detail is paramount during this preparatory phase, as any oversight can skew results, leading to costly redesigns or delays.
Execution of Engine Tests
Once preparation is complete, the testing phase can commence. This stage is where everything comes together. Engineers monitor engine behavior under various conditions, collecting real-time data. For example, during a dynamic test on a turbocharged engine, the performance metrics related to boost pressure, exhaust temperature, and fuel consumption are closely tracked.
In a typical engine test, the following aspects are often monitored:
- Power Output: Measured in horsepower or kilowatts, this is a crucial metric that demonstrates the engine's capability.
- Efficiency Metrics: Including fuel economy and thermal efficiency, these help ascertain how effectively the engine converts fuel into work.
- Emissions Testing: With increasing regulatory scrutiny on emissions, it is vital to monitor pollutants like NOx and CO2 throughout the test.
Real-time data analysis during this phase allows engineers to make instant decisions. For instance, if an engine begins to overheat, adjustments can be made immediately rather than waiting until after the test.
Post-Test Analysis
The final step in the testing process is post-test analysis. This phase involves scrutinizing the data gathered during the execution of the tests. Engineers evaluate the performance against the predetermined benchmarks to assess how well the engine met expectations.
Key areas of focus include:
- Data Correlation: Comparing results against simulations and previous tests shows whether the engine performed as predicted.
- Failure Analysis: If any malfunctions occurred, such as a sudden drop in oil pressure, a thorough examination is necessary to identify root causes.
- Recommendations for Improvement: Insights gained from each test guide future designs. Engineers may suggest material changes or design alterations to enhance performance.
"The only real mistake is the one from which we learn nothing."
Throughout each of these steps, collaboration between various engineering teams becomes vital. Input from all professionals, whether it’s mechanical, electrical, or software engineers, can shine a light on different aspects of the engine's performance, paving the way for better products.
By meticulously following this structured testing process, organizations can significantly enhance their engine development practices, leading to better-performing engines and ultimately saving time and resources.
Data Collection and Analysis
In the world of engine testing, data collection and analysis emerge as paramount players. Essentially, they serve as the backbone of any testing program, enabling engineers and researchers to draw valid insights regarding engine performance, efficiency, and durability. Without a robust framework for collecting and interpreting this data, the often expensive and complex process of engine testing would lack the rigor it demands, turning potentially lucrative developments into mere shots in the dark.
Importance of Accurate Data
Accurate data is not just a luxury; it’s a necessity. Consider the intricate web of operations in an engine test cell. Every test generates substantial amounts of data ranging from thermal readings and pressure metrics to emissions outputs. Without careful analysis, these figures can quickly pseudoinformation rather than guiding decisions. When every horsepower counts, having precise measurements can be the difference between an engine that meets regulatory standards and one that falls short.
Moreover, accuracy in data collection underscores safety. When developing engines for aerospace or automotive applications, a minor miscalculation can lead to catastrophic failures. It's no coincidence that the adage "measure twice, cut once" holds weight in these intensive test environments. Research has shown that improvements in data accuracy can reduce error margins by up to 30%. Hence, prioritizing accurate data means protecting investments and ensuring higher reliability across applications.
Data Management Systems
As any seasoned engineer can tell you, collecting data is only half the battle. The real challenge lies in managing and analyzing that data efficiently. Enter data management systems, which revolutionize how information is organized, accessed, and interpreted. These systems serve as digital libraries, containing a vast array of data points from past tests, current analyses, and predictive models.
Implementing a well-designed data management system offers several benefits:
- Centralized Storage: Information is cataloged and easily retrievable.
- Data Security: Only authorized personnel can access sensitive data, reducing the risk of leaks.
- Real-time Analysis: Engineers can make on-the-spot decisions based on immediately accessible data sets.
- Collaboration: Multiple teams can access the same data for collaborative projects, streamlining workflow.
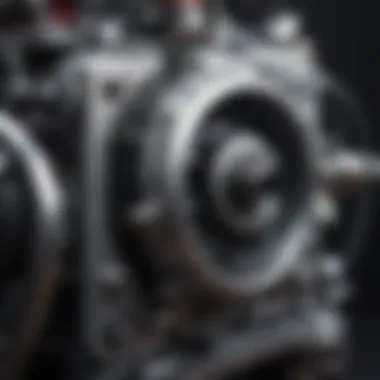
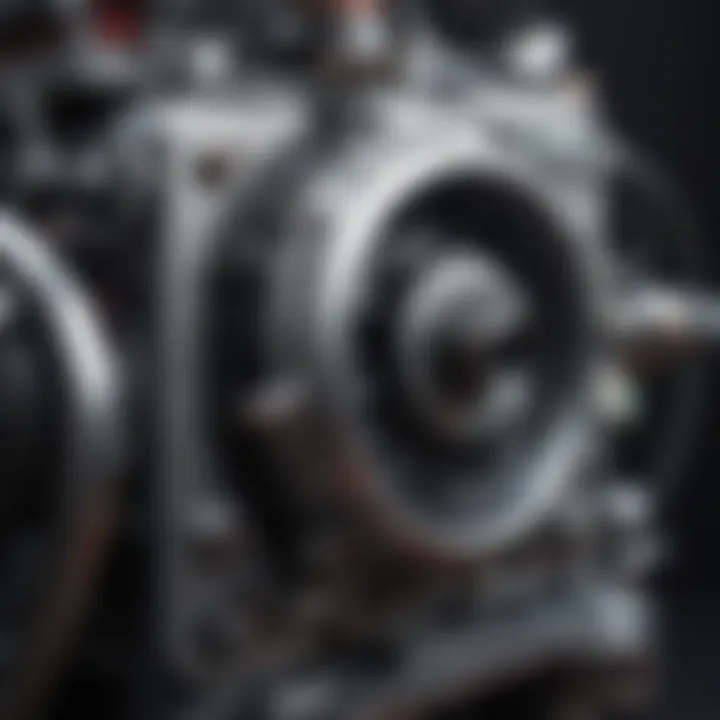
Furthermore, these systems often integrate with other technologies like artificial intelligence and machine learning, enabling predictive analytics. They can forecast potential engine performance issues before they even arise, providing a significant edge in proactive testing.
"In the realm of engineering, timely and accurate data analysis is akin to having a crystal ball. It allows you to foresee challenges before they materialize."
Employing advanced data management systems thus becomes not just a suggestion but a requisite for modern engine testing operations. The capacity for rich analysis and real-time data access becomes a game-changer, enhancing effectiveness and helping engineers fine-tune engines for optimal performance in their respective sectors.
Applications of Engine Test Cells
The application of engine test cells extends beyond mere experimentation; it’s a fundamental aspect of how industries ensure that their engines not only meet specifications but also exceed performance expectations. Every sector that relies on engines, whether for transportation or production, stands to gain dramatically from the fine-tuning facilitated by these sophisticated facilities. The ability to simulate real-world conditions allows engineers to glean insights that guide design improvements, enhancing both performance and reliability for end users.
Automotive Industry Testing
In the automotive sector, test cells play a pivotal role in quality assurance and innovation. Manufacturers leverage these specialized environments to rigorously evaluate engine performance under various scenarios. For instance, during the development phase of a new model, engineers can test the engine's response to different fuel types, temperature extremes, and load conditions, providing crucial data to fine-tune engine efficiency and reduce emissions.
- Benefits of Automotive Testing:
- Optimizes fuel economy.
- Ensures compliance with legislation on emissions.
- Reduces the risk of making costly errors post-production.
Automotive testing is particularly vital for hybrid and electric vehicles, given the rapid evolution in technologies and consumer expectations. As manufacturers seek to stay ahead of the curve, engine test cells serve as a vital arena for trialing cutting-edge technologies such as alternative fuels and advanced combustion methods.
Aerospace Engine Testing
Aerospace engineers often operate in an arena where precision and reliability are not merely desirable but absolutely critical. In this field, engine test cells help ensure that aircraft engines deliver the necessary power while maintaining safety during various flight conditions. Each engine undergoes rigorous testing to mimic the operational environment it will face at high altitudes and variable speeds.
"The reality of aerospace engine testing is that it’s not just about performance, it’s about safety – lives depend on it."
Consider the testing protocols for jet engines. These engines are subjected to extensive assessments, where aspects such as thrust performance, fuel consumption, and noise levels are meticulously monitored. The data acquired informs engineers on fuel efficiency and performance potential, ultimately impacting aircraft design and operational economics.
Marine and Industrial Applications
Marine engines, powering everything from yachts to commercial shipping vessels, also rely heavily on testing cells. The harsh conditions at sea demand engines that can stand the test of time and performance. Engine test cells provide the environment necessary for testing under simulated weather conditions, load factors, and fuel mixtures that are unique to marine operations.
For industrial applications, such as generators or machinery engines, testing is crucial in a different sense. Industrial engines need to perform consistently under demanding workloads. Through rigorous testing, manufacturers can better understand the wear and tear on engines, allowing for the development of maintenance schedules and longevity strategies.
In summary, the applications of engine test cells stretch across automotive, aerospace, and marine industries, underscoring their integral role in engine development and performance optimization. With advancements in technology and methodology, these facilities will continue to evolve, offering even greater insights into engine capabilities and efficiencies.
Technical Challenges in Engine Testing
Engine testing, a critical aspect of modern engineering, often runs into multiple hurdles that can complicate the process. Understanding these technical challenges is key to refining testing methodologies and improving engine performance across various applications. Whether in automotive, aerospace, or industrial sectors, the implications of these hurdles can be far-reaching.
Engineering Constraints
One of the most pressing challenges in engine testing arises from engineering constraints. These constraints can stem from several factors, including design specifications, resource availability, and technology limits. For instance, when designing an engine test cell, engineers must account for:
- Space Limitations: The physical dimensions of the testing facility can impose restrictions on how engines are arranged and tested. Limited space can affect the installation of necessary equipment.
- Material Strength: Components subjected to high stress must be constructed from materials that can withstand these loads without sustaining damage. Taking shortcuts in material selection can lead to catastrophic failures.
- Budget Constraints: Financial limitations can affect the scope of testing and the quality of materials and technologies used in engine test cells. A tight budget might mean fewer resources for advanced technologies that could provide better insights during testing.
These engineering constraints can hinder accurate data collection and compromise the reliability of test results. Therefore, careful planning and innovation are vital to navigate these challenges.
Environmental Considerations
Another major challenge in engine testing revolves around environmental considerations. Testing engines, particularly in dynamic conditions, generates significant noise and emissions that can impact both external environments and surrounding communities. Several factors are crucial here:
- Noise Control: Engine tests often produce sound levels that exceed regulatory limits. This can lead to community objections or even legal actions. Thus, implementing effective acoustic treatments and using sound-dampening technologies is imperative.
- Emissions Regulations: Compliance with environmental laws concerning emissions is increasingly stringent. Testing facilities must incorporate equipment that captures and manages exhaust emissions efficiently. Failure to do so can result in hefty fines and damage to the reputation of the organizations involved.
- Sustainability: The shift towards more sustainable practices prompts facilities to invest in technologies that minimize environmental impact. This may entail adopting cleaner fuels or exploring alternative energy sources for testing engines.
Both engineering constraints and environmental considerations play crucial roles in shaping the future of engine testing methodologies. The need for innovation in overcoming these challenges has never been greater.
Navigating these technical challenges requires a holistic approach, focusing on long-term solutions. Addressing these issues thoughtfully can lead to more effective testing processes, thereby enhancing the overall performance of engines across various applications.
Ultimately, identifying and overcoming these hurdles is not merely an operational necessity but is imperative for the advancement of engine technology.
Innovations in Engine Testing Technologies
The realm of engine testing is not static; it's always evolving. The significance of this progress can't be overstated, especially when considering the stakes involved in performance, safety, and environmental impact. As engines become more complex and the demands placed upon them increase, innovations in testing technologies are essential to ensure reliability and efficiency. It’s about pushing the limits of what engines can achieve and doing so in a manner that is sustainable and safe.
Emerging Testing Methodologies
Recent years have seen the advent of various methodologies that challenge the traditional approach to engine testing. One such methodology is the use of virtual prototyping. Rather than solely relying on physical models, engineers can utilize sophisticated software to simulate engine behavior under diverse conditions. This reduces the time and cost associated with producing physical prototypes.
Moreover, rapid prototyping techniques like 3D printing have enabled engineers to create intricate parts in a fraction of the time previously required. This flexibility allows for more frequent iterations and refinements based on test data, effectively accelerating the development cycle.
Some key points regarding emerging testing methodologies:
- Simulation Tools: Software like MATLAB and Simulink allows for complex simulations of engine dynamics.
- Dynamic Testing: This involves real-time evaluation under operational conditions, offering unprecedented insights into performance.
- Environmental Testing Solutions: These provide a better understanding of how engines perform under extreme conditions, such as high temperatures or varying humidity levels.
"Embracing innovative testing methodologies means not just keeping pace with the industry but setting the pace."
Integration with AI and Machine Learning
Artificial intelligence and machine learning (AI/ML) are reshaping the landscape of engine testing. These technologies add layers of sophistication to data analysis, transforming it from mere observation to predictive intelligence. By analyzing vast amounts of data, machine learning algorithms can detect patterns and make recommendations that human analysts might overlook.
This integration offers several benefits:
- Predictive Maintenance: By assessing wear and tear before it becomes critical, these systems enhance reliability.
- Optimized Testing Procedures: AI can assist in determining the most effective testing strategies, minimizing unnecessary tests and focusing resources where they are truly needed.
- Real-Time Feedback: If an anomaly occurs during a test, machine learning systems can adjust parameters on-the-fly, ensuring accurate representation of engine performance under diverse conditions.
The result is a streamlined process that enhances efficiency and diminishes the complexity typically associated with engine testing. This convergence of technology signifies a shift toward a more proactive approach, where potential issues are addressed before they escalate into problems.
Regulatory and Safety Standards
Regulatory and safety standards play an essential role in ensuring the reliability and integrity of engine test cells. The operation of these facilities isn't just about performance metrics; it also involves compliance with a host of regulations that protect the health and safety of personnel as well as the environment. For engineers, researchers, and decision-makers, understanding these standards can be critical in both operational planning and risk management.
Compliance Requirements
When it comes to compliance, engine test cells need to adhere to various national and international standards. These guidelines not only dictate the operational procedures but also the design and maintenance of the test cells themselves. Some critical aspects of compliance include:
- Environmental Regulations: These rules often govern emissions, ensuring that any pollutants are kept within specified limits.
- Health and Safety Codes: These rules establish safe working conditions for employees. This encompasses everything from the layout of the test cell to ensure safe access to equipment, to emergency protocols in case things go awry.
- Standards set by Organizations: Organizations like the Society of Automotive Engineers (SAE) or the Federal Aviation Administration (FAA) provide specific guidelines that must be followed for testing procedures and equipment certification.
"Compliance is not just about following the rules; it is about embodying a culture of safety and excellence in every aspect of engine testing."
These compliance requirements may vary depending on the location and purpose of the engine testing. For example, testing a military engine will require stricter protocols than testing a passenger vehicle engine. This already complex web of regulations can present additional challenges to engineers, making thorough understanding and stringent adherence vital.
Safety Protocols in Testing
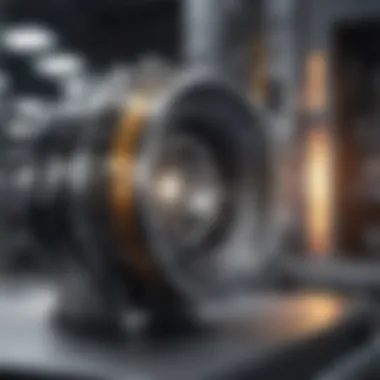
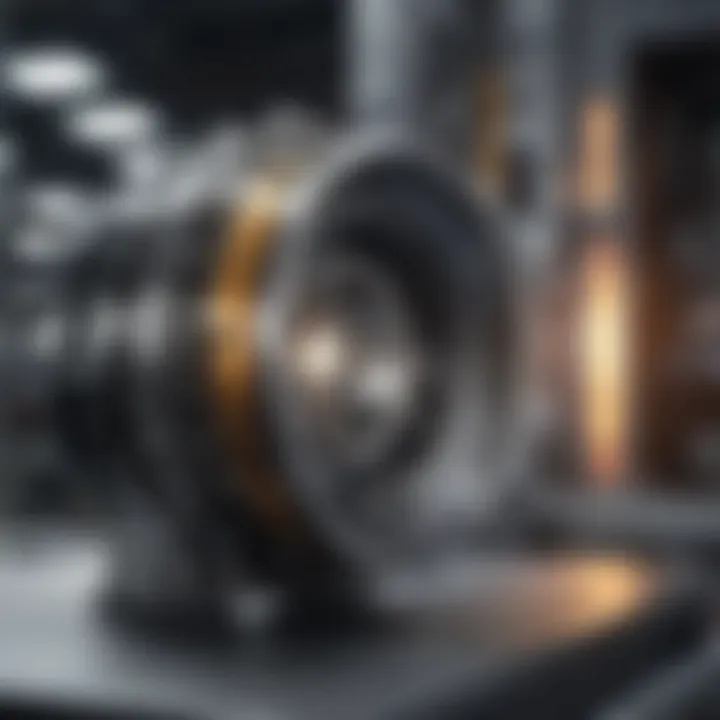
Safety protocols are the backbone of operation in engine test cells. They are designed to minimize risk during the testing phases and protect both the operators and the environment. Some key safety measures include:
- Personal Protective Equipment (PPE): All personnel must wear appropriate gear such as helmets, goggles, and gloves to shield against potential hazards.
- Operational Procedures: Detailed operational procedures dictate how tests are to be conducted, from engine installation to shutdown processes. All staff should be trained in these procedures.
- Emergency Response Plans: Each facility should have a comprehensive emergency plan that applies to various potential scenarios, such as fuel leaks or equipment failures. Regular drills must be scheduled to ensure everyone knows their role in an emergency.
In addition, regular audits and inspections are crucial. These not only help to verify compliance but also identify areas for improvement. Ensuring consistent adherence to safety protocols can significantly reduce accident rates, fostering a safer work environment.
Overall, the stringency of regulatory and safety standards in engine test cells should not be seen as a burden. Rather, they provide a framework that enhances the quality and reliability of testing, ensuring that innovations in engine design and performance can be pursued without compromising safety or compliance.
Future Trends in Engine Testing
The landscape of engine testing is evolving rapidly. With advancements in technology and a growing emphasis on sustainability, it’s crucial to stay abreast of the latest trends reshaping this field. Here’s what’s on the horizon for engine test cells.
Sustainability Initiatives
Environmental consciousness has taken center stage in recent years, pushing industries towards greener practices. Engine test cells are no exception. Key sustainability initiatives include the adoption of energy-efficient processes and renewable energy sources. This shift minimizes the carbon footprint linked to engine testing.
For instance, some facilities are now integrating solar panels and wind turbines as alternative energy sources. Not only does this reduce reliance on traditional energy, it also lowers operational costs in the long run.
Moreover, recycling water used in cooling systems is gaining traction. Instead of discharging water after one use, innovative systems recirculate it, significantly conserving water resources. Coupled with efforts to improve emissions controls, these moves position engine testing as a champion of sustainable practices within engineering.
Advancements in Testing Efficiency
As engines become more complex, testing methods must keep pace. Efficiency has emerged as a top priority in design and execution. Engine test facilities are utilizing automation and sophisticated software to streamline processes, enhancing both speed and accuracy.
One notable advancement is the use of real-time data analytics. By collecting data constantly during tests, engineers can make immediate adjustments rather than waiting for post-test analysis. This has shown to cut testing times dramatically while enhancing results.
Furthermore, digital twins—a virtual model of the physical engine—allow for simulations that predict performance before actual physical testing. This technological leap not only saves time but reduces the costs associated with extensive engine modifications.
"Real-time data analytics and automation are revolutionizing engine test cells, making them faster and more efficient than ever before."
Case Studies of Engine Test Cells
In the realm of engine testing, case studies serve as invaluable resources that shed light on real-world applications and outcomes of various testing methodologies. These examples illustrate not just successes, but also the pitfalls that engineers and researchers have encountered. By dissecting specific instances of engine test cell implementations, we are able to draw lessons that inform future projects and refine practices in the field.
Successful Testing Campaigns
Successful testing campaigns highlight what can be achieved when proper planning and execution align. One prime example can be found in the automotive sector, where Ford Motor Company utilized its test cells to achieve breakthroughs in engine performance. Their campaign was characterized by a multi-faceted approach to testing, featuring rigorous data collection and analysis.
Key elements of this success include:
- Comprehensive Data Gathering: Throughout the campaign, engineers collected data on various metrics, such as horsepower, torque, and emissions. This allowed them to make informed adjustments during the tuning phase.
- Iterative Testing: Ford embraced an iterative approach, enabling quick modifications based on real-time data. Each round of tests provided insights that guided the next set of adjustments, ultimately resulting in a more efficient engine.
- Cross-Disciplinary Collaboration: The integration of input from multiple engineering disciplines ensured that all aspects, from thermodynamics to materials science, were considered.
In summary, the successful testing campaigns not only validate the capabilities of engine test cells but also underscore the importance of a well-organized and collaborative approach.
Lessons Learned from Failures
Failure in testing environments can often be as insightful as successes. Drawing insights from failed ventures can yield crucial information that prevents similar mistakes in the future.
Take the case of a well-known aerospace company that encountered unforeseen issues during an engine test. The initial failure was linked to inadequate cooling systems, which resulted in overheating and damaging the engine. The aftermath of this incident illustrated several key lessons:
- Importance of Thorough System Checks: Before commencing tests, a comprehensive review of all systems—including cooling and lubrication—should be performed to ensure reliability.
- Backup Protocols: Establishing robust backup systems is critical. If one component fails, alternatives should immediately be available to prevent catastrophic outcomes.
- Realistic Testing Scenarios: Testing conditions must mirror real-world situations as closely as possible. By simulating the stress that engines might face in actual use, engineers can better prepare for potential failure modes.
"Every failure teaches us something vital. Embracing failure is essential for innovation; it leads us to improvements we never thought possible."
By diving deeply into these case studies, whether they celebrate triumphs or analyze setbacks, we acknowledge that both success and failure play pivotal roles in shaping the landscape of engine testing. These narratives enrich our understanding and guide future development, making each engine test cell not just a facility, but a cornerstone of engineering advancement.
Comparative Analysis of Testing Facilities
The overarching landscape of engine testing facilities is varied and intricate. Comparing these facilities is not merely an academic exercise; it’s essential for understanding how different environments and technologies influence the outcome of engine tests. The variation in designs, technologies used, and operational methodologies can substantially impact both performance metrics and overall efficiencies. This comparative analysis reveals the strengths and weaknesses inherent in each facility type, providing valuable insight for engineers and decision-makers.
Global Perspectives on Engine Testing
Engine testing is a global endeavor. Different regions bring unique philosophies and practices to engine test cell design and usage. For instance, in the automotive industry in Germany, a pronounced emphasis is placed on emissions and efficiency. Consequently, facilities are often equipped with advanced dynamometers and sophisticated data collection systems to meet stringent regulatory standards. Conversely, aerospace testing, predominantly occurring in the United States and parts of the UK, prioritizes thrust measurement and operational safety. This regional variation often translates to different investment levels, technological advancements, and research outcomes.
"The engines of the future won't just be tested under the hood, but also in the context of the global environment they must operate in."
Moreover, the incorporation of regional standards adds another dimension. For instance, testing facilities in Asia are increasingly aligned with sustainable practices, looking to reduce carbon footprints while maintaining robust performance metrics. Understanding these global perspectives allows engineers to adopt best practices and innovations gleaned from various locales, thereby fostering a more integrated approach to testing and engine development.
Cost-Benefit Analysis of Facilities
In any industry, costly investments must demonstrate tangible returns. Engine test cells are no exception. A detailed cost-benefit analysis can unearth the underlying value propositions tied to these facilities. This analysis doesn't only look at the initial setup costs, which can be exorbitant, but also the operational costs associated with maintenance, staffing, and technology upgrades.
- Initial Costs
- Operational Costs
- Long-Term Savings
- Construction and equipping of the test cell
- Installation of specialized monitoring and analysis equipment
- Regular maintenance schedules
- Staff training and development
- Increased efficiency leading to quicker test cycles
- Enhanced reliability resulting in reduced failure rates during production
A comprehensive cost-benefit analysis thus reveals that while the upfront costs of state-of-the-art testing facilities might be daunting, the long-term advantages often outweigh these initial outlays. As newer technologies surface, such as those integrating AI for data analysis, the potential for optimizing testing processes expands, making these facilities not only valuable but also essential in the competitive landscape of engine production.
In summary, engaging in a comparative analysis of testing facilities unveils valuable insights that contribute to more informed decision-making in engine testing. By examining global perspectives and conducting detailed cost-benefit analyses, stakeholders can strategically position themselves to harness innovations and efficiencies, ultimately driving advancements in engine technology.
Culmination
The conclusion of this article is pivotal because it encapsulates the comprehensive understanding developed over the previous sections regarding engine test cells. As we’ve explored, these specialized facilities are not merely a backdrop for testing; they form the core foundation upon which modern engine development is built. They serve a dual purpose: optimizing performance and ensuring compliance with safety standards across various industries.
One important aspect covered herein is the necessity of accurate data collection. Engine test cells provide precise measurements that inform engineers about various performance metrics—fuel efficiency, power output, and emissions, to name a few. This accuracy is essential not only for the debugging and improvement of engines but also for regulatory compliance.
Additionally, the exploration of technological innovations signifies the ongoing evolution within this field. As new tools and methodologies emerge, they promise enhanced capabilities in testing, which in turn leads to advancements in engine design. The integration of tools like AI and machine learning is not just a novelty but a becoming standard that magnifies outcomes and expectation management for future projects.
The takeaway here is crystal clear: the significance of engine test cells transcends the traditional view of testing. They are vital in steering the course of research and development, providing insights that redefine engine performance while contributing to sustainability efforts and regulatory adherence.
"Testing facilities are not just buildings—they are the crucible in which the future of engine performance is forged."
Summary of Key Insights
Summarizing key insights from our exploration, it is critical to recognize:
- Engine test cells are essential for accurate performance evaluation, offering real-time analysis that informs design iterations.
- The evolution of testing methodologies, including the adoption of AI, has streamlined processes and heightened precision in diagnostics.
- A holistic perspective on regulatory standards highlights the necessity for adherence, ensuring that engines are not only high-performing but also environmentally compliant.
- Through various applications in automotive, aerospace, and industrial sectors, it is evident that engine test cells play diverse yet unified roles in engine development.
Future Directions
Looking ahead, the future of engine testing appears to be intertwined with several key areas:
- Sustainability Initiatives: The automotive industry is increasingly leaning toward environmentally sustainable practices. Expect innovations that not only enhance performance but prioritize ecological responsibility.
- Integration of Advanced Technologies: The incorporation of big data and machine learning algorithms will likely reshape how engineers approach testing. As more data becomes available, systems can learn and predict engine performance under various conditions.
- Remote Testing Scenarios: With advancements in communication technology, remote operation of test cells could become feasible, allowing engineers to analyze and manipulate tests from afar—a particularly useful scenario in global collaborations.
- Customization of Testing Protocols: As engine designs diversify—from electric to hydrogen-powered—testing facilities will need to adapt to unique requirements, necessitating tailored protocols for effective assessment.
In essence, the future of engine test cells will likely reflect the broader trends in engineering and environmental stewardship. Engaging with these advancements will not only benefit manufacturers but the planet as well, driving forward a more sustainable era in engine technology.