Understanding the EDM Process: A Detailed Guide
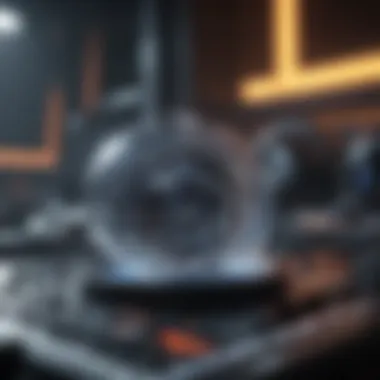
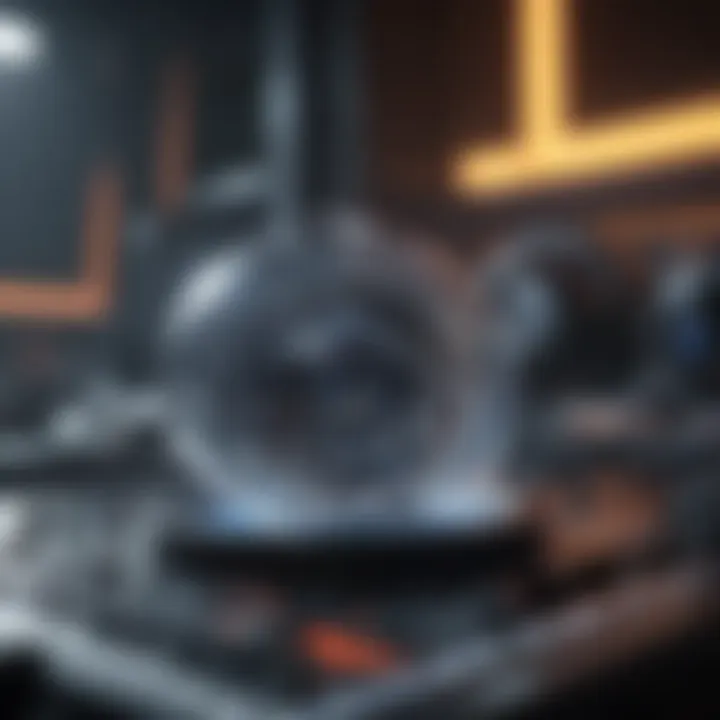
Intro
Electrical Discharge Machining, commonly known as EDM, is a fascinating technique in the world of manufacturing. It’s not just another method; it’s a game-changer, especially in the realm of precision metalworking. In this overview, we’ll peel back the layers of the EDM process, exploring its fundamental principles, operational mechanisms, and widespread applications across various industries.
At the heart of adherence to tight tolerances, this method employs a series of electrical discharges to shape materials. In a nutshell, EDM is almost like sculpting, using electricity instead of a chisel. This allows for the creation of intricate shapes and fine details in hard metals that regular machining couldn’t touch. It's a sophisticated method that opens doors to possibilities in engineering, aerospace, and even medical device manufacturing.
Understanding the nuances of EDM is essential not only for professionals in industry but also for academic researchers diving into material science. The discussion will further explore the advantages, such as its precision and ability to machine complex geometries, while also addressing some limitations inherent in the process. As we journey through this overview, we aim to provide insights rich enough for seasoned experts, yet accessible to those new to the technque.
Let’s delve into the key findings.
Key Findings
Major Results
The primary result of EDM ingrains itself in its ability to manipulate metals and other conductive materials with unmatched accuracy. Unlike traditional cutting methods, which can impose physical constraints due to tool wear and mechanical limitations, EDM’s non-contact nature allows it to handle intricate designs without the risk of distortion or damage to the tool itself. This quality not only enhances the precision of the machined parts but also significantly prolongs the life of the electrodes used in the process.
Some notable key findings include:
- Precision Engineering: EDM can achieve tolerances as tight as ±0.001 mm in many cases.
- Material Versatility: It is effective on a variety of conductive materials, including exotic alloys and hardened steels.
- Complex Geometries: It enables the production of complex shapes, such as undercuts, that would be difficult to achieve through other methods.
Discussion of Findings
With the benefits of EDM clear, the discussion naturally pivots to its relevance in contemporary manufacturing landscape. The evolution of technology plays a significant role here, allowing modern EDM machines equipped with advanced software to optimize cutting paths and electrode wear intelligently.
Moreover, the process does have its challenges. For instance, the requirement for conductivity limits material options, making certain composites unusable. Additionally, electrode wear can lead to inefficiencies, albeit advancements in materials are continually addressing these issues.
The intricate balance of advantages and limitations of EDM cements its position as a highly valuable process in the toolkit of manufacturers worldwide.
Methodology
Research Design
Diving deeper into understanding EDM also requires a look at its methodological framework. The research design often encapsulates both experimental and analytical approaches, ensuring a robust examination of its efficiency and outcomes. The integration of real-time data monitoring and feedback loops can refine the accuracy and productivity of the machining process.
Data Collection Methods
Data collection for EDM involves multiple techniques, including:
- Control Systems: Utilizing sensors to track parameters like spark frequency, voltage, and current.
- Material Tests: Assessing the metallurgical properties post-machining to gauge effectiveness.
- Performance Metrics: Evaluating cycle times and cost-effectiveness in real manufacturing scenarios.
Through these methodologies, researchers and professionals alike can appreciate the critical variables that influence EDM outcomes, thus informing future developments and applications.
As we proceed further into this comprehensive overview, expect a robust exploration of the advantages and limitations that shape EDM, along with cutting-edge technological advancements that push the boundaries of what's possible in manufacturing.
Prologue to EDM Process
The EDM process, or Electrical Discharge Machining, has become an indispensable technique in the modern manufacturing landscape. This precision machining method allows for intricate metal shaping that traditional methods often cannot achieve. Understanding the EDM process is not merely an academic exercise; it's a gateway into the precise world of advanced manufacturing. The intricacies of EDM facilitate the production of complex geometries and components critical in industries ranging from aerospace to medical devices.
Definition of EDM
Electrical Discharge Machining works by using a series of electric discharges between an electrode and the workpiece. This process results in the erosion of the metal, allowing for fine details and smooth finishes. One can liken it to the way water erodes rock over time, which, in essence, symbolizes how electrical energy is harnessed to shape materials.
EDM is particularly advantageous because of its ability to work with hard materials, including stainless steel and titanium, which are difficult to machine through conventional methods. Simply put, it allows manufacturers to create precise shapes swiftly without subjecting materials to mechanical stress.
Historical Development
The roots of Electrical Discharge Machining can be traced back to the 1940s. Initially, it emerged from experiments conducted on the concept of spark erosion. Researchers discovered that sparks generated between two electrodes could gradually erode materials. This paved the way for the first practical applications during the 1950s, when CNC (Computer Numerical Control) technology began to be integrated with EDM systems.
Over the decades, EDM has evolved rapidly. The development of dielectric fluids—substances that support the machining process—enhanced efficiency and precision significantly. Today, contemporary electrodes made from various materials, including copper and graphite, further fine-tune the EDM process. Manufacturers continuously strive to refine this technology, fostering innovations that push the boundaries of what is possible with EDM. This history not only highlights the significance of the EDM process in modern engineering but also represents the persistent drive for improvement and efficiency in manufacturing practices.
"The journey of EDM from concept to crucial manufacturing technology demonstrates the profound interplay of science and industry."
Fundamental Principles of EDM
Understanding the basic tenets of Electrical Discharge Machining (EDM) is crucial for grasping its role in manufacturing. These principles serve as the foundation upon which the entire process operates, influencing both efficiency and output quality. By delving into the core mechanics and system components, one can appreciate how EDM achieves its signature precision and versatility.
Basic Working Mechanism
EDM is based on a simple yet effective principle: material removal occurs through electrical discharges between an electrode and the workpiece. This process involves creating a spark that vaporizes material, thereby shaping the workpiece. The space between the electrode and the workpiece is filled with a dielectric fluid which plays a pivotal role. When sufficient voltage is applied, the fluid breaks down, allowing a spark to form. This microscopic explosion erodes the material in a controlled manner.
One of the key aspects of the working mechanism is that the electrode and the workpiece do not touch, minimizing the risk of damage or wear to either component. The process is inherently adaptable, allowing for adjustments in power levels, pulse durations, and other parameters, making it suitable for a variety of materials and geometries.
Key Components of EDM Systems
- Electrode Selection
Selecting the right electrode is a crucial choice that can significantly impact the EDM process. Electrodes can be made from various materials such as copper, graphite, or tungsten, each offering unique characteristics.
Electrode material, for instance, affects both the speed of machining and the surface finish. Copper electrodes are often popular for their excellent conductivity and heat dissipation properties, while graphite is chosen for its ability to withstand higher temperatures. However, graphite can produce a rougher surface finish compared to copper. In making this decision, factors such as the type of workpiece material and desired finish should be integrated into the selection criteria.
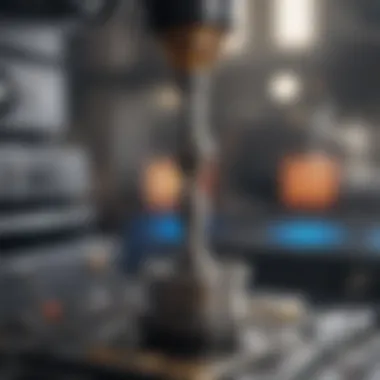
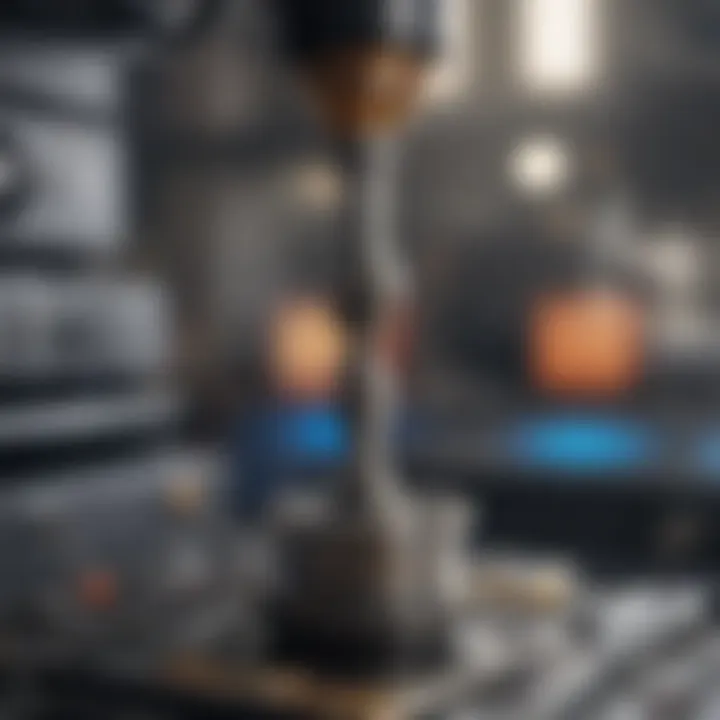
- Dielectric Fluid
The dielectric fluid serves multiple purposes—it cools the machining area, washes away debris, and facilitates the spark formation necessary for material removal. Common options include water-based fluids and oil-based options, with each having its advantages and drawbacks.
Water-based fluids tend to provide better cooling properties and lower costs, but they can also create rust issues on metal components if not managed carefully. Oil-based fluids, while more expensive, often increase the machining lifespan since they provide better lubrication, albeit at the cost of less efficient cooling.
- Power Supply
The power supply unit in an EDM system is vital for controlling the discharge cycles, affecting how effectively the machining process occurs. Typical units allow for settings such as voltage, current, and pulse frequency, which influence not only the machining speed but also precision.
For instance, high power levels increase the machining rate, but they may negatively impact the quality of the finish. Conversely, lower power can lead to a finer surface but at the expense of longer machining times. Thus, aligning power supply settings with the desired outcome is essential for an optimal EDM process.
"The interplay between these components can dictate the success of an EDM operation, thus understanding them is non-negotiable for anyone serious about adopting this technology."
In summary, the fundamental principles of EDM revolve around its basic working mechanism and its key components. Each element is interconnected and plays a significant role in achieving the precision and versatility that EDM is well-known for. By mastering these principles, users can enhance their effectiveness in applying EDM techniques in various industrial contexts.
Types of EDM Techniques
Electrical Discharge Machining is not a one-trick pony; it presents several techniques tailored for different machining needs. The significance of examining various EDM methods lies primarily in their capacities to adapt to diverse manufacturing requirements. This section delves into three prominent EDM techniques: Wire EDM, Sinker EDM, and Blow EDM. Each method comes with its own set of advantages, applications, and considerations that make it valuable within specialized industries.
Wire EDM
Wire EDM is a widely used technique predominantly in the aerospace and automotive domains. The core idea here is simple yet effective: a thin brass or copper wire, functioning as an electrode, moves through the workpiece, strategically removing material in a controlled manner. This method's precision cannot be overstated; it can achieve tolerances anywhere from ±0.0001 inches up to ±0.00005 inches, depending on the machine's capability and operational settings.
The advantages of Wire EDM include its ability to produce intricate details and fine features that traditional machining might struggle with. For instance, if you happen to work with complex parts such as turbine blades or intricate molds, Wire EDM becomes indispensable.
Advantages of Wire EDM:
- High accuracy for complex geometries
- Minimal tool wear
- Capability to cut hard materials without deforming them
- Environmentally friendly, as it uses less energy compared to other methods
On the other hand, Wire EDM does have its drawbacks, such as relatively lower processing speeds and the necessity for continuous electrode replacement. Nonetheless, its importance in creating complex shapes cannot be disregarded.
Sinker EDM
Also known as Plunge EDM, Sinker EDM employs a pre-shaped electrode that is plunged into the material. It's particularly useful for creating cavities and holes, and it excels in applications where a defined shape or contour needs to be created, such as in molds and dies. Unlike Wire EDM, which relies on a continuous wire, Sinker EDM utilizes a solid electrode, often made from carbon or copper, and this electrode mirrors the negative shape of the desired cavity.
One of the primary benefits of Sinker EDM is its effectiveness in machining harder materials, including titanium and various alloys. Additionally, it allows for complex cavitation, making it indispensable in industries focused on precision tooling.
However, Sinker EDM can have longer machining times and might not be suitable for thin-walled components due to the greater risk of thermal distortion. This calls for a careful consideration of the workpiece material and desired outcomes.
Blow EDM
Blow EDM, while not as common as the previous two techniques, is worth mentioning due to its unique approach. Instead of using a continuous electrode or a shaped one, Blow EDM employs a stream of dielectric fluid along with a conductive electrode, resulting in a dynamic machining process. This technique is particularly useful in applications requiring multiple small holes or channels.
One of the highlights of Blow EDM is its ability to facilitate efficient cooling, reducing the risk of thermal damage to the workpiece. It's often chosen when intricate geometry combined with efficient material removal is necessary.
In comparison to Wire and Sinker EDM, Blow EDM might fall short in terms of precision, but its unique cooling characteristics can provide significant benefits in specific applications.
The End
In summary, the EDM process has a range of techniques that cater to different manufacturing demands. Understanding these distinct methods allows professionals and researchers alike to choose the right technique for their specific needs, optimizing the benefits while also considering the limitations of each method. From the extraordinary precision of Wire EDM to the robust adaptability of Sinker EDM, and the innovative approach of Blow EDM, each presents unique advantages suited for various industrial challenges.
Industries Utilizing EDM
The Electrical Discharge Machining process stands out as a robust solution across various industries, transforming the manufacturing landscape significantly. The ability to execute precise manufacturing tasks where traditional methods fall short has made EDM a valuable asset in sectors requiring high accuracy and efficiency. Whether it's crafting intricate components or fine-tuning large parts, the significance of this process is underscored in several key industries. Understanding how EDM fits into these sectors offers a clearer picture of its relevance and advancements.
Aerospace Applications
In the aerospace industry, precision is not just desired; it's critical. Components used in aircraft engines and structural elements must adhere to extremely stringent tolerances, reflecting a premium on accuracy. EDM is often employed to create complex geometries, for instance, turbine blades with intricate cooling channels that enhance performance while withstanding high-stress conditions.
When dealing with heat-resistant alloys, traditional machining techniques can quickly become less effective, often leading to defects or material loss. EDM side-steps these issues, permitting high-quality finishes without compromising the integrity of the workpiece. Moreover, reduce machinery wear and extend tool life is indispensable in maintaining efficiency amid the rigorous production demands of aerospace engineering.
Automotive Manufacturing
The automotive sector thrives on innovation and precision, where performance and safety collide. Complex components such as gear systems, connectors, and dies require the exactness that EDM provides. As the industry leans more towards electric and hybrid vehicles, the demand for higher precision in manufacturing increases.
For manufacturers, EDM is particularly advantageous for producing tool inserts that fit into existing molds, facilitating easier, lighter, and more efficient casts. The ability to maintain exact specifications is vital in a field where even the smallest deviation can lead to operational headaches. Furthermore, the variability in electrode materials means manufacturers can select those most suited for their specific applications, thereby optimizing cost-effectiveness without sacrificing quality.
Medical Device Production
The medical device manufacturing field, considered one of the most regulated industries, highly values precision. Components used in devices like surgical instruments and implants must meet stringent regulatory standards. EDM enables detailed work that might be impossible with conventional methods. For instance, creating intricate connectors for electronic devices or precise surgical tools can be achieved with remarkable accuracy.
The advantages become even more apparent when discussing biocompatible materials where surface integrity is paramount. EDM’s ability to create smooth finishes means that devices are not only functional but also safe for patient use. As this sector evolves towards more innovative solutions enhanced by technology, the role of EDM in medical device production becomes essential to unlocking new possibilities for design and functionality.
The incorporation of Electrical Discharge Machining within these industries underscores its pivotal role in driving advancements and efficiencies in modern manufacturing.
By understanding the unique applications of EDM across these fields, one can appreciate why it has garnered such importance. The future of manufacturing is shaped not just by efficiency but by the symbiosis of complexity and precision—qualities where EDM excels.
Advantages of EDM
The EDM process carries considerable weight in the modern manufacturing landscape, and understanding its advantages is essential for those engaged in the field. This technique offers several standout benefits that ahould not go unnoticed. From achieving meticulous precision to negotiating complex geometries, its value crosses many boundaries. The conversation around EDM isn’t merely about efficiency; it encompasses the ability to create parts that wouldn’t be feasible with traditional machining methods. Let’s take a closer look at the factors making EDM a powerhouse.
Precision and Accuracy
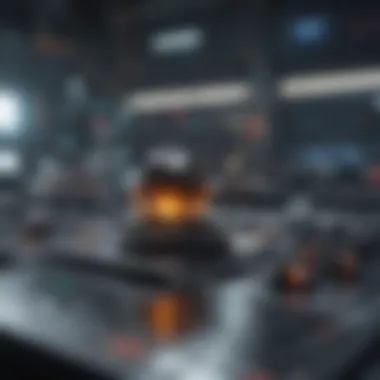
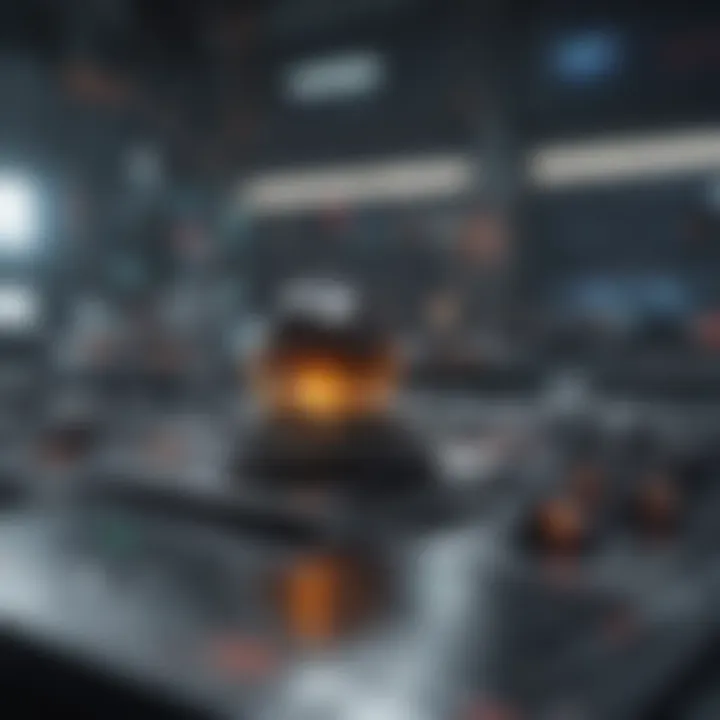
One of the crown jewels of EDM is its capability for precision and accuracy. This isn't just about hitting close to the mark; with Electrical Discharge Machining, the level of accuracy achieved can reach the micron scale. In fields like aerospace and medical manufacturing, where every fraction of a millimeter counts, this fine-tuning ability proves indispensable.
Another factor enhancing precision in EDM is the nature of the energy used. The process relies on controlled electrical discharges to erode material, minimizing the risk of thermal distortion or mechanical errors typically seen in conventional machining. Due to this, components possessing tight tolerances can be manufactured consistently, making EDM an ideal choice for applications requiring high precision.
Complex Geometries
EDM shines brightly when it comes to handling intricate and complex geometries. Traditional machining techniques often struggle to create detailed shapes like sharp corners, intricate curves, and deep holes. EDM, however, can navigate these obstacles with ease, eroding material in ways that seem almost effortless.
In scenarios where intricate design features are not just a preference but a necessity, the ability of EDM to work with customized electrode shapes allows for this complexity to be brought to life. Whether it’s a part for a high-performance engine or custom tooling, the degree to which EDM can accommodate unique designs cannot be overstated.
"The beauty of EDM lies in its flexibility to adapt to unique specifications without compromising quality."
Material Versatility
The EDM process isn’t just a one-trick pony; it thrives on versatility in material handling. A significant advantage is its ability to operate effectively with various materials—conductors like steel, copper, and tungsten can be manipulated deftly. The electrical discharge method isn't bound by the same limitations faced by mechanical cutting tools, which often degrade when working with hard materials.
Thus, industries like aerospace or medical, often dealing with exotic materials, find EDM crucial in their processes. The capability to manipulate diverse materials without significant wear on tools makes EDM a cost-effective solution, ultimately reducing operational downtime and maintaining production schedules.
In summation, whether it’s through precision, the handling of complex shapes, or the versatility with varied materials, the advantages of EDM are abundant. This process serves as a linchpin in advanced manufacturing technologies, showing just how essential it is for today’s demanding industries.
Challenges and Limitations of EDM
The Electrical Discharge Machining (EDM) process, while being highly effective for intricate metal shaping, is not without its setbacks. Understanding these challenges and limitations is crucial for industries relying on precision manufacturing. Each of the elements discussed below highlights concerns that can significantly influence production costs, lead times, and the overall effectiveness of EDM.
Surface Finish Concerns
Achieving a desirable surface finish is paramount in many applications, especially in industries such as aerospace and medical device manufacturing. The nature of the EDM process introduces certain inherent roughness due to the way material is removed through electrical discharges.
In some cases, parts may require extensive post-processing to reach the smoothness required for operational integrity. The surface finish can be influenced by several factors, including:
- The type of electrode material used
- The settings of the EDM machine
- The dielectric fluid characteristics
For example, a copper electrode may produce a smoother finish compared to a graphite one under identical processing settings. As such, manufacturers must carefully consider their electrode choices and machine settings to optimize surface quality. A lot can hinge on these choices, especially when the end application demands meticulous precision.
Processing Speed
One of the prominent challenges faced in EDM is the processing speed. While it excels in precision, EDM is often slower compared to traditional machining methods. The time it takes to erode material depends on various variables, including power settings and the size of the workpiece.
Manufacturers looking to optimize production often find themselves balancing speed and precision. The slower processing can lead to:
- Increased lead times in manufacturing cycles
- Higher overall operational costs due to longer machine run times
- Bottlenecks in production lines when EDM is used for critical parts
To address these concerns, operators may employ techniques such as optimizing the power settings or the use of higher conducting materials for electrodes. However, even with optimizations, EDM maintains a reputation for being a leisurely process relative to other methods.
Operational Costs
The costs associated with EDM can be a double-edged sword. On one hand, it's an invaluable process for achieving complex shapes and fine details; on the other hand, it can rack up significant expenses in several areas. Some key cost considerations include:
- Electrode wear: The constant need for electrode replacements can add up over time. Different materials wear differently, and while some may last longer than others, they often don’t come cheap.
- Dielectric fluid usage: Maintaining the appropriate level and quality of dielectric fluid is essential for efficient operation, and sourcing this fluid incurs regular costs.
- Maintenance of equipment: Like any machinery, EDM machines require regular upkeep to ensure they operate at peak efficiency. Neglecting maintenance can lead to costly repairs and operational inefficiencies.
"Investing in an efficient EDM machine is not just about the purchase cost, but also about understanding the entire ecosystem of operational expenses."
The combination of these factors contributes to the complex landscape of EDM operational costs. It is vital for businesses to conduct a cost-benefit analysis and to consider long-term implications before fully committing to EDM as their primary manufacturing method.
Through examining these challenges and limitations, a comprehensive picture of EDM emerges—one that acknowledges its strengths while also shedding light on the areas where improvement and careful consideration are necessary.
Critical Variables Impacting EDM Performance
The effectiveness of Electrical Discharge Machining (EDM) hinges on several pivotal variables that shape its performance. Understanding these variables is essential for constructing efficient machining processes. These factors can greatly influence not only the quality of the finished workpiece but also the operational efficiency of the EDM system itself. Key variables such as power settings, electrode material properties, and dielectric fluid characteristics must be finely tuned to achieve desired outcomes, reflecting the nuances of EDM technology.
Power Settings
Power settings are the heartbeat of the EDM process. They dictate how much energy the machine will use during operation. An appropriate power setting can help in achieving optimal machining conditions, balancing between efficiency and precision. Too high a power level can lead to excessive wear on the electrode—wasting both material and time, while too low can result in weakened machining performance. The ability to adjust power settings dynamically allows operators to adapt to varying workpiece materials and geometries. As a general guideline, a lower power setting can be beneficial for fine, intricate work, while higher settings are suited for broader cuts or tougher materials.
Electrode Material Properties
Electrode material is another crucial factor impacting the EDM process. The selection of electrode material directly impacts both the wear rate and the machining efficiency. Common materials include copper, graphite, and tungsten, each offering unique benefits. Copper, for instance, provides excellent electrical conductivity and is often favored for its durability. On the other hand, graphite is appreciated for its light weight and ability to withstand high temperatures, which can help maintain the machining precision over long production runs. When advising students or professionals about electrode selection, it’s vital to consider the application specifics—the material should match the demands of the workpiece to ensure optimal performance.
Dielectric Fluid Characteristics
Dielectric fluids serve as the unsung heroes in the EDM process. They facilitate the electrical discharge while also cooling the system during machining. The choice of dielectric fluid can significantly impact the surface finish, material removal rate, and overall efficiency of the process. Common fluids include deionized water and various oils. Each has its characteristics, with oils providing better lubrication properties but at the expense of cooling efficiency compared to water. It’s crucial to understand how fluid characteristics such as viscosity, conductivity, and flash point can influence the EDM process.
"Optimal cooling and flushing are paramount not just for maintaining temperature, but also for ensuring that the process remains free of debris that might hinder performance."
Thus, grasping the intricacies of dielectrics is key for anyone operating EDM equipment effectively.
In summary, the interplay of power settings, electrode materials, and dielectric fluid characteristics forms a delicate balance that can lead to successful EDM operations. Professionals and students alike should prioritize these critical variables to maximize performance and maintain high standards in their EDM applications.
Technological Advancements in EDM
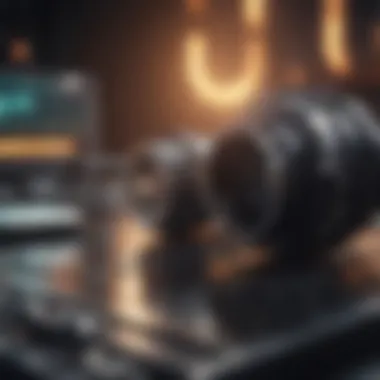
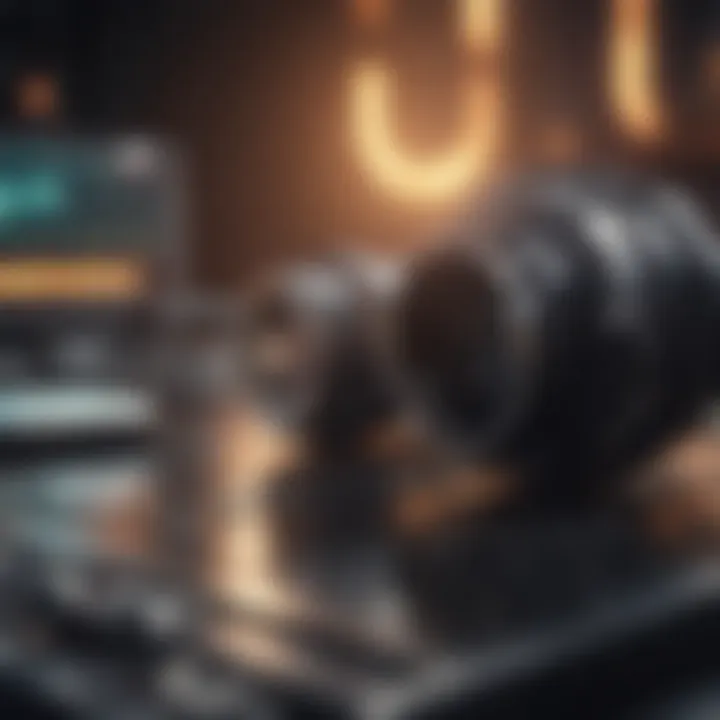
The landscape of Electrical Discharge Machining (EDM) is constantly evolving, shaped by rapid technological advancements. These developments not only enhance the efficiency of the EDM process but also expand its range of applications. Modern machines are becoming more sophisticated, integrating state-of-the-art features that improve overall performance, user-friendliness, and precision. Technology's role in EDM is not merely a trend; it is a necessity for staying relevant in today's competitive manufacturing environments.
Automation and CNC Integration
Automation in EDM has drastically transformed how machining tasks are approached. Computer Numerical Control (CNC) integration allows for greater precision and repeatability. Machines equipped with CNC essentially follow a pre-programmed set of instructions, which translates computer-generated designs into physical products. This programmer-driven approach minimizes human error, a factor that can have major consequences in precision engineering.
- Benefits of Automation:
- Increased Efficiency: Automated systems run consistently, 24/7, maximizing throughput.
- Improved Accuracy: Programs established through CNC reduce discrepancies.
With setups becoming more user-friendly, operators can focus on design aspects, leaving the repetitive tasks to the machines. An example can be seen in the aerospace sector; companies like Boeing employ CNC-integrated EDM systems to produce lightweight components with intricate designs, ensuring high levels of performance without compromising on safety.
Advances in Electrode Manufacturing
Electrode materials are crucial in optimizing the EDM process. Innovations in electrode manufacturing have led to new materials that offer enhanced conductivity and durability. Graphite, copper, and tungsten are commonly used, but advancements now enable the use of composite materials that combine the benefits of various components.
- Considerations in Electrode Technology:
- Material Composition: New composites offer tailored characteristics for specific applications.
- Cost-Effectiveness: Innovations in production techniques can lower the overall costs of electrodes without sacrificing performance.
The development of high-performance electrodes allows for better material removal rates, which is crucial in industries where time is of the essence. A case study involving the production of intricate molds for injection molding demonstrates how advanced electrodes can improve the process by increasing the lifespan and performance of the electrodes, fundamentally changing how businesses manage their resources.
Emerging Research Trends
Research in EDM is a hotbed of new ideas and technologies. Key areas of focus include hybrid machining processes where EDM is combined with other techniques, such as laser machining, to leverage their respective strengths. The emphasis is increasingly on improving sustainability and reducing operational waste. Strides in understanding the science behind the machining process are enabling scientists and engineers to craft new methodologies that optimize parameters much better than before.
Some emerging trends in this field include:
- Smart Data Utilization: Applying IoT (Internet of Things) for real-time monitoring to gather performance data.
- Sustainable Practices: Research into biodegradable dielectric fluids that minimize environmental impact.
- Advanced Simulation Techniques: Enhanced simulation tools are now available to predict and improve the EDM process before physical machining.
Each of these trends underscores the movement towards not just improving the technological aspect of EDM, but also towards aligning with broader industry-wide goals of efficiency and sustainability. As these innovations unfold, the insights gathered transform traditional machining landscapes, providing both opportunities and solutions for manufacturers facing modern-day challenges.
"Innovation in EDM technology is not just about complexity; it’s about simplicity, sustainability, and delivering precision at unprecedented levels."
In summary, the breathtaking pace of technological advancements in EDM highlights an exciting frontier in manufacturing. From automation and innovations in electrode materials to cutting-edge research trends, each facet plays a vital role in refining and enhancing the EDM process.
Future Perspectives on the EDM Process
The ongoing evolution of Electrical Discharge Machining (EDM) continues to ignite discussions about its future. As demand for precision in manufacturing rises, EDM is positioned to keep pace with technological advancements. This section lays out the upcoming trends and considerations in the EDM process that professionals, academics, and industry leaders must pay attention to. The embrace of innovative technologies is paramount in ensuring that EDM remains relevant and efficient.
Sustainability Considerations
One pressing issue in modern manufacturing, including EDM, is sustainability. The industry faces increasing scrutiny on its environmental impact. For EDM, sustainability can materialize in several ways:
- Reducing Waste: The EDM process inherently involves material removal; however, finding ways to minimize scrap and optimize material usage is vital.
- Eco-Friendly Dielectric Fluids: Traditional dielectric fluids often pose environmental risks. Research into biodegradable and less harmful alternatives could significantly alter the EDM landscape.
- Energy Efficiency: Enhancing the energy efficiency of EDM machines can contribute to reducing overall carbon footprints.
A commitment to sustainable practices could pave the way for EDM to align better with modern industrial standards.
By focusing on sustainability, companies can address market demands while also contributing positively to the planet.
Integration with Industry Four
The rise of Industry 4.0 introduces a paradigm shift in how manufacturing processes are integrated and optimized. EDM is not precluded from these advancements:
- Smart Factories: EDM processes enhanced by smart technologies can lead to more streamlined operations and real-time monitoring, allowing for quicker adjustments during production.
- Data Analytics: Utilizing big data analytics within EDM processes enables the identification of patterns and insights that can refine performance—leading to improved precision and reduced downtime.
- Collaborative Robots (Cobots): Coupling EDM machines with cobots can enhance workflow, allowing machines to focus on intricate tasks while robots handle repetitive or menial work.
This integration isn't merely an option; it’s becoming a necessity to remain competitive in a fast-evolving market.
Potential Innovations
Innovation in EDM technology remains a hotbed for exploration. Several promising areas could lead to significant advancements:
- Advanced Electrode Technologies: The development of new electrode materials with superior conductive properties could lead to finer precision and longer tool life.
- Hybrid Manufacturing Approaches: Combining EDM with other machining processes—like additive manufacturing—could provide unique solutions to manufacturing challenges.
- AI and Machine Learning: Implementing AI to predict tool wear and enhance the decision-making process during EDM production could revolutionize how the technique is utilized.
Each innovation could open up avenues for improved efficiency, better product quality, and further applications across diverse sectors.
The End
In wrapping up this exploration of the Electrical Discharge Machining (EDM) process, it’s crucial to understand its overarching significance in manufacturing. Each aspect discussed provides not just a glimpse into the operational mechanics but also reflects its relevance in today’s production landscape. The importance of EDM lies in its ability to achieve high precision with complex geometries that other methods simply can’t replicate.
Summary of Key Points
To encapsulate the main points:
- The understanding of EDM's fundamental principles sheds light on its unique ability to efficiently shape metals under varied conditions.
- Different types of EDM techniques, including wire and sinker EDM, have progressively addressed diverse industrial needs, showcasing versatility.
- EDM's applications across industries like aerospace and automotive highlight its critical role in producing parts that require extreme precision and durability.
- The advantages, such as material versatility and the capacity for intricate designs, outweigh many operational challenges, though awareness of issues like surface finish and processing speed remains vital.
- Ultimately, the blend of technology advancements and future innovations predicts an exciting horizon for EDM, cementing its place as a foundational technique in modern manufacturing.
Final Thoughts on EDM
Considering the insights gathered, it's clear that the EDM process is more than just a machining technique; it stands as a testament to precision engineering. As industries increasingly demand tighter tolerances and more complex shapes, the role of EDM won’t just persist but will likely expand within the complex tapestry of advanced manufacturing frameworks.
In sum, understanding EDM enhances knowledge for students, researchers, and professionals alike, equipping them with the critical insight needed to navigate a field that continues to evolve rapidly. The future of EDM, with its integration into automation and sustainable practices, promises to be as dynamic as the technologies it shapes.
"EDM is not just about eliminating material—it's about redefining possibilities in manufacturing."
As this landscape unfolds, staying informed about developments will be crucial, reinforcing the notion that EDM is a vital pillar of modern machining techniques.