Understanding Degas Epoxy Resin: Composition and Uses
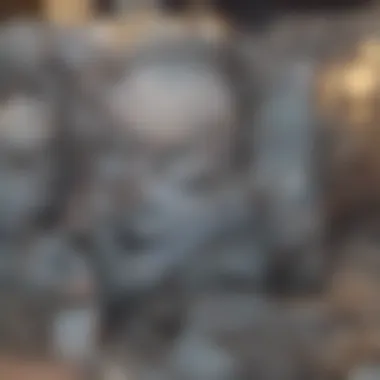
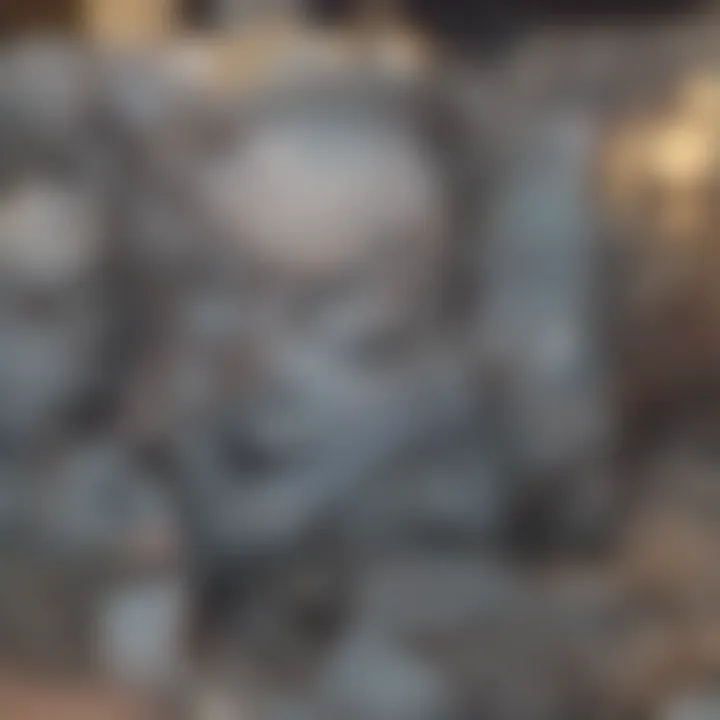
Intro
Degas epoxy resin has emerged as a significant material in various industrial applications. Its unique composition allows for versatility and superior performance compared to traditional materials. Understanding its properties, methods of application, and best practices is essential for researchers and practitioners who seek to maximize its advantages.
The composition of degas epoxy resin is typically composed of a hardener and base adhesive. This two-part system creates a strong bond once cured, resulting in a durable and resistant material. This article will delve into the details of its chemical makeup, processes for effective application, and practical guidance to ensure successful use.
In this exploration of degas epoxy resin, we will examine its advantages in strength and adhesion, where it can be applied, and safety considerations during its use. Professionals across fields, from artists to engineers, will find this information valuable for enhancing their projects with degas epoxy resin.
Foreword to Degas Epoxy Resin
Degas epoxy resin has gained significant attention in various fields due to its unique properties and adaptability. In this section, we will explore the fundamentals of degas epoxy resin, emphasizing its importance within the broader context of material science. Understanding the basics sets the foundation for a deeper discussion of its chemical composition, applications, and best practices.
Degas epoxy resin serves as a critical material in industries ranging from manufacturing to arts and crafts. Its capability to create strong and durable bonds is attributed to its specific composition and properties. Unlike traditional resins, degas epoxy offers enhanced mechanical performance and better resistance against environmental influences, making it preferable for intricate projects where precision is vital.
Moreover, the ability to remove air bubbles through degassing elevates the quality of finished products. This process minimizes imperfections and ensures a smooth and uniform surface, greatly impacting aesthetic and structural integrity.
Definition and Characteristics
Degas epoxy resin is a thermosetting polymer that consists of two primary components: the epoxy resin itself and the hardener or curing agent. When combined, these components undergo a chemical reaction that results in a solid, durable material.
Characteristics of degas epoxy resin include:
- High tensile strength: Offers resistance to deformation under stress.
- Low viscosity: Facilitates easier application and penetration into molds or surfaces.
- Excellent adhesion: Bonds well to various substrates, enhancing versatility.
- Chemical resistance: Maintains performance in hostile environments.
These characteristics contribute to its widespread use in applications requiring both strength and precision.
History and Development
The development of epoxy resins dates back to the early 20th century, with significant advancements made during the mid-century. Initially used in industrial applications, the technology has evolved to cater to a broader range of sectors, including construction, automotive, and electronics.
The introduction of degas epoxy resin represents a significant milestone in this evolution. Tailored formulations and improved curing processes have enabled the production of resins with reduced air entrapment. The ongoing research and development in this field focus on enhancing the material's performance further while considering environmental sustainability.
Through this exploration of its definition, characteristics, and historical context, one can appreciate the relevance and benefits of degas epoxy resin. This understanding lays the groundwork for further discussion on its chemical composition, applications, and best practices.
Chemical Composition of Degas Epoxy Resin
The chemical composition of degas epoxy resin is paramount in understanding its application and performance. The blend of materials within the resin determines its physical properties, such as strength, flexibility, and curing time. Knowing these components allows users to make informed choices for specific applications and ensures effective use of the resin. The emphasis on its composition helps illustrate why degas epoxy is favored in various industries, from manufacturing to artistry.
Resin Components
Degas epoxy resin consists primarily of epoxy resins and hardeners. The epoxy resins are oligomeric compounds that undergo polymerization. This process occurs when they react with hardeners, resulting in a thermosetting polymer that offers significant strength and durability. The main resin type used in degas epoxy is bisphenol-A epoxy, known for its chemical resistance and coating qualities.
Furthermore, various additives can enhance the performance of the basic resin. These include:
- Fillers: Materials like silica or talc can be added to reduce costs and improve specific attributes.
- Pigments: Additives for color and aesthetics, allowing customization for artistic projects.
- Flow modifiers: These improve the workability of the resin without compromising strength.
Each component plays a role in tailoring the final product to meet user requirements. Balancing these constituents is essential for achieving the desired properties while ensuring ease of application.
Curing Agents
Curing agents, often referred to as hardeners or catalysts, are crucial in the curing process of degas epoxy resin. They determine how quickly the resin sets and the ultimate properties of the solidified product. Common curing agents include amine-based, anhydride-based, and polyamide-based hardeners.
The choice of curing agent affects:
- Curing time: Faster curing agents lead to quicker project completion, essential for industrial applications.
- Thermal resistance: Some agents offer higher heat resistance than others, making them suitable for specialized uses like electronics.
- Mechanical strength: The interaction between the resin and curing agent influences the final structure, impacting durability and longevity.
In summary, the optimal selection of both resin components and curing agents is essential for the intended use. Understanding these aspects allows for better adjustments and the achievement of high-performance results when using degas epoxy resin.
Importance of Degassing in Epoxy Resin Use
Degassing is a critical process in the application of degas epoxy resin, influencing both the aesthetic and functional qualities of the final product. When air bubbles remain trapped in the resin, they can lead to a range of defects, undermining the integrity of the material and its performance. Understanding the importance of degassing helps practitioners produce more reliable and visually appealing results, reinforcing the value of this step in the overall resin application workflow.
Effects of Air Bubbles
Air bubbles introduce not just cosmetic flaws into the epoxy resin, but also can significantly compromise functionality. Bubbles create weak points within the cured material. If structural integrity is essential, the presence of air pockets can lead to cracks or breaks under pressure. Additionally, these bubbles can form surfaces that are unyielding to bonding during application with other materials.
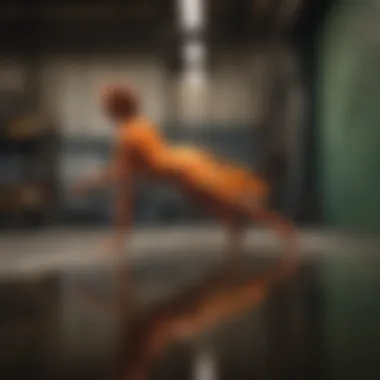
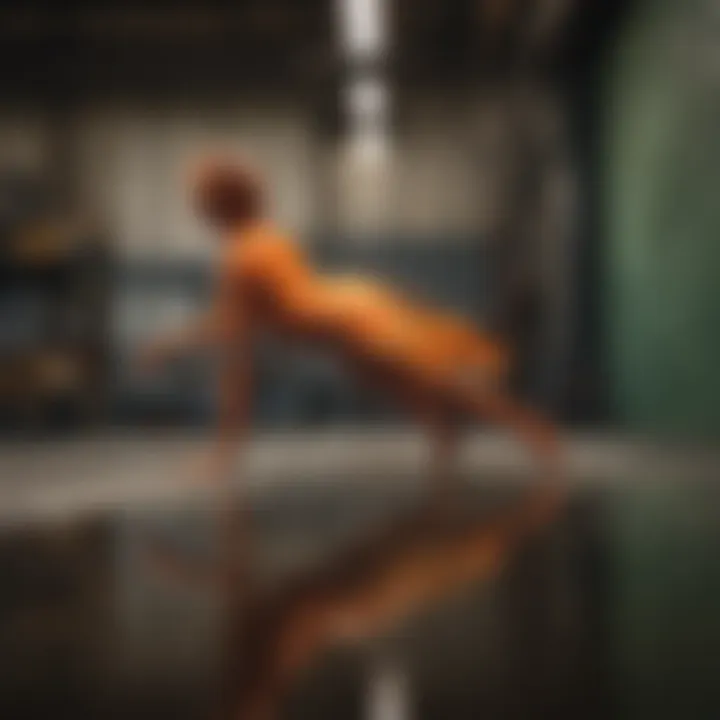
The detrimental impact of air bubbles can manifest in various ways:
- Visual Defects: Bubbles leave an unwanted impression in clear castings and coatings, diminishing the appearance of the finished product.
- Reduced Strength: The presence of air can lessen the tensile and compressive strength, weakening the final product.
- Inconsistent Finish: Air pockets can lead to uneven surfaces, which poses challenges for subsequent coatings or finishes.
It is essential to ensure a thorough degassing process to mitigate these risks and achieve consistent results in epoxy applications.
Benefits of Degassing
The benefits of degassing epoxy resin extend beyond merely preventing the presence of air bubbles. Here are some of the key advantages nuanced in the degassing process:
- Enhanced Clarity and Aesthetics: A degassed resin allows for a more transparent, crystal-clear finish, vital in artistic and decorative applications.
- Improved Surface Adhesion: By minimizing air pockets, the bonding properties of the resin with other materials are optimized, leading to better durability and longevity.
- Consistent Curing Behavior: Degassed resins typically cure more uniformly, leading to predictable mechanical properties, which is essential for applications needing precise specifications.
- Extended Workability: Degassing can extend the working time of the resin, allowing for more extensive layouts and adjustments before the curing begins.
"Degassing is not just an optional step; it is an integral part of achieving high-quality, reliable epoxy resin applications."
If you want to learn more about the significance of degassing, consider further reading on epoxy resin applications at Wikipedia.
Methods for Degassing Epoxy Resin
Degassing epoxy resin is a crucial process. It leads to a higher quality in the final product. Air bubbles trapped within the resin can lead to a variety of defects, such as weak points or visually unappealing surfaces. Employing effective methods for degassing can enhance the mechanical strength, minimize imperfections, and improve overall appearance. Therefore, understanding how to correctly apply these methods is essential for craftsmen and industrial users alike. The methods discussed here include vacuum degassing, pressure degassing, and heat application techniques. Each method has its own merits and challenges that should be considered based on the project requirements.
Vacuum Degassing
Vacuum degassing is a widely used technique for removing air bubbles from epoxy resin. This method involves placing the epoxy mixture in a vacuum chamber. When the chamber is evacuated, the reduction in pressure allows air bubbles to expand and eventually escape to the surface. The advantage of vacuum degassing is that it can remove a significant number of bubbles without introducing additional heat or pressure. However, it is important to ensure that the vacuum pump is efficient and that the chamber is properly sealed to avoid leaks. Failure to do so may result in insufficient degassing, which could compromise the quality of the resin.
- Setup Requirements: A vacuum chamber and pump are essential.
- Process Time: The process usually takes 15 to 30 minutes, depending on the resin's viscosity and the vacuum level.
- Considerations: Avoid letting the resin cure during the degassing process. Monitor the curing time closely to avoid drawbacks.
"Effective vacuum degassing is critical for producing castings with minimal air inclusions and enhanced structural integrity."
Pressure Degassing
Pressure degassing is another effective method. This technique involves pressurizing the epoxy resin to remove air bubbles. By pressurizing the mixture, the gas becomes soluble within the resin, thus reducing its volume. When the pressure returns to normal, the gas expands and is released. This method is particularly useful for high-viscosity resins that resist bubble formation. It also works well for larger pours where vacuum degassing may not be feasible. However, specialized equipment for pressure control is necessary, which can be a financial consideration.
- Required Equipment: A pressure vessel and appropriate gauges are needed.
- Process Insight: The time taken can vary but usually lasts under 10 minutes.
- Precautions: Care must be taken when returning to normal atmospheric pressure to prevent rapid expansion of dissolved gases, which can create new bubbles.
Heat Application Techniques
Heat application techniques involve gently warming the epoxy resin prior to or during the degassing process. Heat decreases the viscosity of the resin, promoting the rise of air bubbles to the surface. This method can be done in conjunction with vacuum or pressure degassing to enhance efficiency. It is particularly effective for thicker resins that trap bubbles more easily. Proper temperature control is key; excessive heat can lead to premature curing or degradation of the resin.
- Temperature Range: This may vary, but 60 to 80 degrees Fahrenheit is generally safe.
- Application Methods: Heat guns or controlled heating pads can be used, taking care to distribute heat evenly.
- Limitations: This technique may not be suitable for all resin types; always check the manufacturer's specifications.
Applications of Degas Epoxy Resin
Applications of degas epoxy resin are diverse and pivotal in various industries. This section elucidates how and why this material plays a crucial role in manufacturing, artistry, and electronics, highlighting its significance for professionals, craftsmen, and researchers alike. The knowledge of applications not only enhances the understanding of degas epoxy resin but also underscores its benefits over traditional materials. The reader can appreciate the versatility and practicality of using degas epoxy resin in different fields.
Manufacturing and Industrial Uses
Degas epoxy resin finds extensive application in manufacturing and industrial contexts. Its strong adhesive properties, durability, and resistance to environmental factors make it a preferred choice for many applications.
- Composite Materials: Degas epoxy is used in the production of composite materials, combining strength and lightweight features essential in industries like aerospace. These composites exhibit high mechanical properties, supporting the demands of modern engineering.
- Coatings and Adhesives: In manufacturing, degas epoxy is utilized as a coating for metal and other substrates. Its ability to form a robust bond ensures long-lasting protection against wear and corrosion. The adhesive characteristics allow it to bond different materials together effectively.
- Electrical Encasement: Various industries utilize degas epoxy resin for electrical components. Its insulating properties help in protecting sensitive parts from moisture and mechanical stress, ensuring the longevity of devices.
In essence, degas epoxy resin serves as an integral material in several manufacturing processes, with its unique properties leading to enhanced performance and reliability in products.
Artistic and Craft Applications
The artistic realm benefits significantly from degas epoxy resin, providing artists and crafters a medium to create intricate and beautiful designs. This resin allows for innovative expressions in various forms.
- Jewelry Making: In art, one notable application is in jewelry making. Artists infuse degas epoxy with colors and textures to craft unique pieces. The clarity of the resin allows embedded items to be displayed beautifully.
- Casting and Molding: Degas epoxy is popular for casting. Artists can create sculptures or decorative items, often incorporating pigments or inclusions to add visual depth.
- Furniture Design: Designers use degas epoxy in creating stunning tabletops and other furniture pieces. The resin can be poured over wood or other materials, offering both protection and a striking aesthetic.
Exploring the potential of degas epoxy in artistry fosters creativity, enabling artists to push the boundaries of their work by experimenting with this versatile material.
Electronics and Electrical Applications
In the electronics sector, degas epoxy resin is favored for its insulating and protective qualities, making it indispensable for several applications.
- Circuit Board Manufacturing: Degas epoxy resin is commonly used to encapsulate circuit boards, protecting components from environmental damage. Its dielectric strength ensures minimal electrical interference, which is vital in high-performance electronics.
- Potting and Encapsulation: The resin helps in potting electronic devices, sealing them against moisture and shock. This encapsulation extends the lifespan of valuable components, ensuring operational reliability in varying conditions.
- Heat Resistance: Degas epoxy can withstand considerable heat, making it suitable for applications in automotive electronics or high-temperature environments without compromising integrity.
In summary, the applications of degas epoxy resin are extensive. Its properties facilitate its use in manufacturing, artistry, and electronics. A significant point is that understanding these applications helps in optimizing the use of degas epoxy resin across different industries.
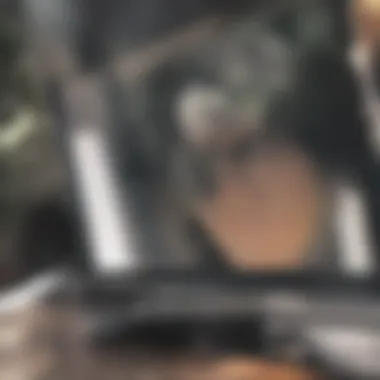
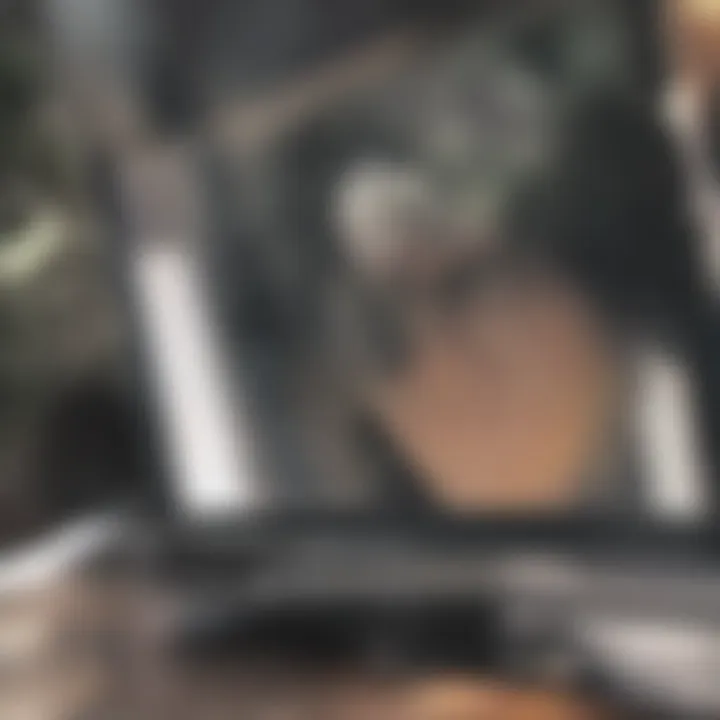
Best Practices for Using Degas Epoxy Resin
Understanding the best practices for using degas epoxy resin is crucial for achieving quality results. This section places emphasis on key areas such as surface preparation, mixing, and curing, each integral to the overall success of a project. By adhering to these guidelines, users can minimize common problems and maximize performance. It is essential to note that these best practices help ensure the desired properties of the resin, including durability, finish, and application effectiveness.
Surface Preparation Techniques
Surface preparation forms the foundation of any successful epoxy application. An inadequate surface can lead to poor adhesion and thus affect the overall outcome. First, the area to be treated must be clean and free of contaminants. Dust, grease, and other debris can interfere with the bond between the epoxy and the surface.
Common surface preparation methods include:
- Sanding: This method increases the surface area for bonding and roughens the surface, allowing for better adhesion.
- Wiping with solvent: Using isopropyl alcohol or acetone removes any oils or residues.
- Drying: Ensure the surface is completely dry as moisture can create complications during application.
These techniques will contribute to achieving a strong bond between the epoxy and the material, ensuring longevity and performance.
Mixing Guidelines
Proper mixing of the epoxy components is critical. An incorrect mix ratio can result in failure to cure or reduced physical properties. Typically, epoxy resin and hardening agent need to be mixed in specific proportions, often found on the product label.
Here are key mixing best practices:
- Use a clean container: Contamination from prior mixtures can negatively affect the current batch.
- Stir thoroughly: This ensures that the components are uniformly distributed. Mix for at least 3 to 5 minutes, scraping down the sides and bottom of the container.
- Avoid air introduction: Stir gently to prevent air bubbles from forming. Mixing in a vacuum can significantly reduce trapped air.
Following these guidelines leads to a consistent mixture, ensuring the desired chemical reaction takes place during the curing process.
Curing Process Optimization
The curing stage solidifies the advantages of using degas epoxy resin. Optimizing this process can elevate the performance of the end product. To achieve optimal curing conditions, consider the following tips:
- Maintain temperature: A stable, warm environment during curing enhances the speed and completeness of the reaction. Recommended temperatures are usually between 70°F and 85°F.
- Monitor humidity levels: Moisture can affect the curing process. Lower humidity is desirable to minimize complications.
- Allow adequate curing time: Each product has a recommended curing time. Be patient and do not rush this process to ensure full hardness and protection against environmental factors.
Overall, following these practices helps streamline the use of degas epoxy resin, fostering an effective application process with enduring results.
"Proper preparation and mixing are the cornerstones of effective epoxy resin application. Neglecting these steps can lead to costly mistakes and project failure."
By embracing these best practices, users equip themselves for success, leading to effective and efficient use of degas epoxy resin in any application.
Troubleshooting Common Issues
Understanding and resolving common issues associated with degas epoxy resin is critical for achieving successful results. Problems such as surface imperfections and incomplete curing can compromise the integrity of the final product. This section explores these issues in detail, providing insights that can help both novices and experienced users alike.
Surface Imperfections
Surface imperfections in cured epoxy can manifest in various forms—bubbles, pits, or uneven finishes. These defects can arise from multiple sources, including improper mixing or inadequate degassing. When air gets trapped in the resin, it leads to unsightly bubbles on the surface after curing.
To mitigate surface imperfections, it is essential to:
- Ensure thorough mixing: Mix the resin and hardener according to the manufacturer's instructions. Failure to do this can result in an uneven cure.
- Implement proper degassing techniques: Vacuum or pressure degassing can significantly reduce air bubble formation.
- Prepare the surface adequately: Clean any debris or dust from the substrate before applying the epoxy.
Additionally, examining curing conditions is necessary. High humidity or low temperatures can lead to surface issues as well. By maintaining optimal environmental conditions, one can minimize these problems.
Incomplete Curing Problems
Incomplete curing is another common issue when using degas epoxy resin. This problem can arise when the resin is not mixed correctly, or the proportion of resin to hardener is imbalanced. It can often lead to sticky or soft surfaces that do not attain the expected mechanical properties.
To address incomplete curing:
- Double-check mixing ratios: Always refer to the epoxy product's guidelines for correct ratios and follow them precisely.
- Allow adequate curing time: Each epoxy formulation has a specific pot life and cure time that should be respected to ensure proper hardening.
- Regularly inspect environmental conditions: Ensure that humidity and temperature levels meet the specified requirements for the chosen epoxy resin.
By adhering to the proper guidelines and practices, users can reduce the frequency of these issues, thus extending the lifespan and effectiveness of their projects.
"Preventing common problems through careful preparation and execution can save considerable time and resources in the long run."
Safety Considerations When Using Degas Epoxy Resin
Using degas epoxy resin can be a complex task, making safety considerations paramount. This section highlights various aspects of safe practices that must be observed to ensure a safe working environment. Proper attention to safety can help prevent accidents, injuries, and health issues.
Personal Protective Equipment (PPE)
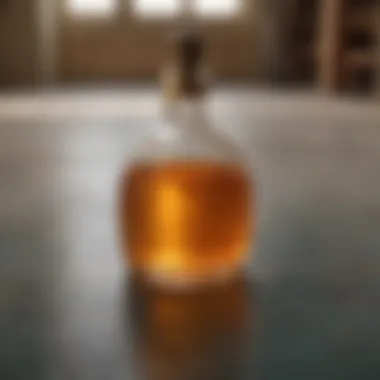
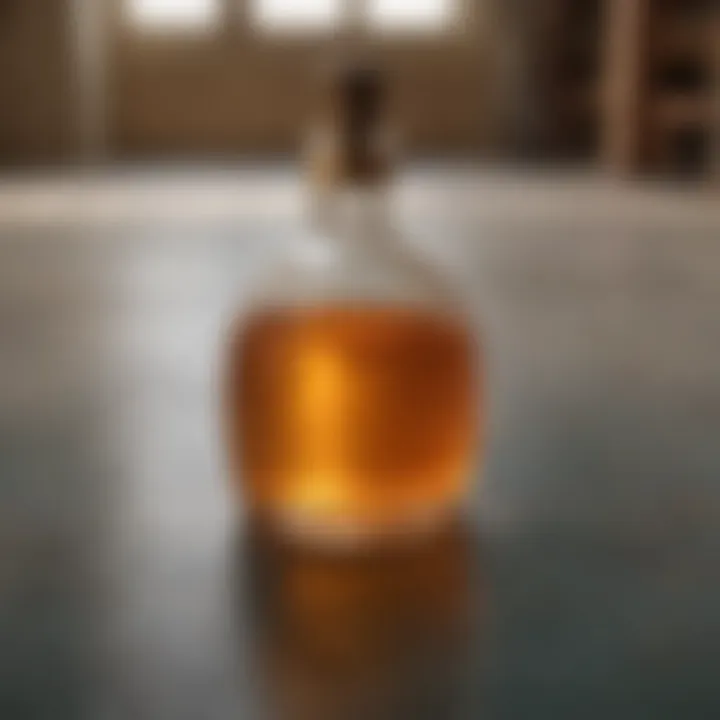
Personal Protective Equipment is essential when handling degas epoxy resin. PPE helps to shield the user from hazardous substances. It includes items such as gloves, goggles, and respirators.
- Gloves: Chemical-resistant gloves should be worn at all times. Nitrile gloves are typically recommended. They provide good protection against chemical exposure and should cover the wrist.
- Goggles: Safety goggles that fit snugly prevent resin from splashing into the eyes. This is vital as the chemicals can cause irritation or injury.
- Respirators: In situations where ventilation is inadequate, using a respirator ensures that inhalation of fumes is minimized. Selecting the right type based on the specific materials used is important.
Ventilation and Workspace Safety
Adequate ventilation is critical when working with degas epoxy resin. In such environments, the buildup of fumes can pose significant health risks. A well-ventilated space allows for the dissipation of harmful vapors.
- Natural Ventilation: Open doors and windows can be effective in allowing fresh air circulation. This method is often the simplest.
- Mechanical Ventilation: Utilizing exhaust fans can significantly improve airflow. They help to remove fumes quickly and are a good option for enclosed spaces.
- Workstation Organization: Keeping the workspace tidy is essential. Clutter can lead to accidents. Ensure tools and materials are organized; this reduces the chances of spills and injury.
It is essential to conduct risk assessments before starting any project involving degas epoxy resin. Planning for safety is an integral part of the process, which ultimately leads to a more efficient and hazard-free working environment.
Environmental Impacts of Degas Epoxy Resin
Understanding the environmental impacts of degas epoxy resin is crucial in today's world where sustainability is gaining attention. The resin’s composition, usage, and ultimate disposal have implications for ecosystems and human health. This section explores the specific elements of sustainability concerns associated with degas epoxy resin and examines recycling and disposal practices that impact the environment.
Sustainability Concerns
The production and application of degas epoxy resin raise various sustainability concerns. One significant aspect is the sourcing of raw materials. Commonly derived from petroleum-based substances, the manufacture of epoxy resins contributes to fossil fuel depletion and greenhouse gas emissions. This points to a necessary shift towards alternative, bio-based materials.
Next, the use of degas epoxy resin in industrial applications often involves chemicals that can have environmental effects. During its curing process, certain volatile organic compounds (VOCs) may be released. These compounds can contribute to air pollution and have harmful effects on human health. Thus, evaluating the chemical formulations used in producing degas epoxy resin is essential for mitigating negative impacts.
Furthermore, the use of degas epoxy resin in products that are not biodegradable presents another sustainability issue. End-of-life scenarios, where products are disposed of in landfills, lead to long-lasting environmental footprints.
Recycling and Disposal Practices
Recycling and disposal practices for degas epoxy resin products are vital components in addressing their environmental impact. As epoxy resins are thermosetting materials, they do not melt down upon reheating, complicating traditional recycling methods. However, advancements in technology are attempting to change this.
- Recycling Initiatives: Some companies are developing processes to break down epoxy resins into their original components, making them reusable. This helps reduce the need for virgin materials and limits landfill contributions.
- Disposal Guidelines: Proper disposal practices require that users follow specific guidelines to minimize environmental harm. Products made from degas epoxy resin should not be disposed of in regular waste facilities. Instead, it is advisable to check local regulations regarding hazardous waste to ensure safe disposal.
- Raising Awareness: Educating consumers and manufacturers about proper disposal and recycling methods can play a significant role in reducing negative impacts. This extends to advocating for responsible product design, focusing on ease of recycling and material recovery.
"Innovative practices and awareness can transform how we handle degas epoxy resin, leading to a more sustainable future."
Future Trends in Epoxy Resin Technology
The future of epoxy resin technology is crucial for various industries. As demand grows, so does the necessity for higher performance, versatility, and environmental sustainability. Current trends indicate that innovative formulations and advancements in application techniques are at the forefront of this evolution. These changes not only enhance the functional properties of epoxy resins but also make their use more efficient and eco-friendly.
Innovative Formulations
Innovative formulations in epoxy resins focus on improving their mechanical and thermal properties. The incorporation of nanomaterials is a significant development. Nanoparticles can enhance the strength and thermal stability of the resin, leading to better performance in demanding applications. For instance, carbon nanotubes or silica nanoparticles can be added to create composites that exhibit higher tensile strength and impact resistance.
Additionally, water-based epoxy systems are gaining popularity. They provide a lower VOC (volatile organic compound) alternative, improving safety for users and reducing environmental impact. These formulations not only meet regulatory standards but also cater to markets prioritizing sustainability. Improving curing agents is also a trend. New catalysts reduce curing times while maintaining the desirable properties of the final product.
Advancements in Application Techniques
Advancements in application techniques are equally vital in shaping the future of epoxy resins. One noteworthy method is automated dispensing technology. This technique increases precision and efficiency, allowing for a more controlled application. Automated systems minimize material waste and enhance consistency across production batches.
Moreover, 3D printing technology has begun to utilize epoxy resins. This application expands the potential for customized products and rapid prototyping. The ability to create complex shapes directly from digital designs represents a significant step forward in manufacturing and design flexibility.
"Innovative formulations and application techniques are the keys to driving the future of epoxy resin technology."
The continuous development in this field not only influences current usage but also opens pathways for entirely new applications.
The End
The conclusion serves as a pivotal part of this discussion on degas epoxy resin. It gathers the insights presented in previous sections and emphasizes the necessity of understanding this material for both practical and theoretical reasons. The conclusion encapsulates key elements such as the chemical composition, various applications, and best practices typically associated with degas epoxy resin.
One key benefit of summarizing the information is reinforcing the significance of the degassing process. By doing so, users can appreciate the advantages that degassed epoxy resin offers over conventional materials. It becomes clear that effective utilization of this resin lies not only in its application but also in the preparation process, highlighting the importance of proper techniques. A thorough grasp of the material's characteristics ensures better decision-making, whether in artistic projects or industrial applications.
Furthermore, considerations regarding safety and environmental impacts are confirmed here. A well-rounded understanding can instill confidence in users, equipping them to tackle various challenges in using degas epoxy resin. Recommendations made throughout the article can lead to improved outcomes and increased creativity in application.
"Understanding the properties and best practices associated with degas epoxy resin enhances the efficacy of its applications, paving the way for innovations in multiple industries."
This final section acts as a reminder of the overall message: to use degas epoxy resin effectively requires a solid grasp of its composition, application methods, and environmental factors. This knowledge ultimately fosters safer and more efficient practices among users in diverse fields.
Summary of Key Points
- Chemical Composition: The components of degas epoxy resin include various resins and curing agents that influence performance.
- Application Range: Widely utilized in manufacturing, art, and electronics, demonstrating its versatility.
- Best Practices: Surface preparation, accurate mixing, and optimal curing are critical to achieving desired results.
- Safety Considerations: Understanding personal protective equipment and workspace ventilation is essential for safe handling.
- Environmental Impact: Awareness of sustainability and disposal practices underscores responsible use of materials.
Final Thoughts on Degas Epoxy Resin
In summary, degas epoxy resin is more than just a material; it represents a transformative approach to bonding and artistic creation. Its unique properties and applications create opportunities for those in various fields, from industrial engineers to hobbyist crafters. As technology advances, the formulations and techniques associated with this resin are likely to evolve, opening new avenues for innovation.
Being well-informed about the resin’s characteristics and careful in its application will lead to improved performance and quality. Therefore, this comprehensive overview should serve as a valuable resource for anyone looking to delve deeper into the nuances of degas epoxy resin, ensuring both safe and effective use in future projects.