Understanding Carbon Fibre: Properties and Future Trends
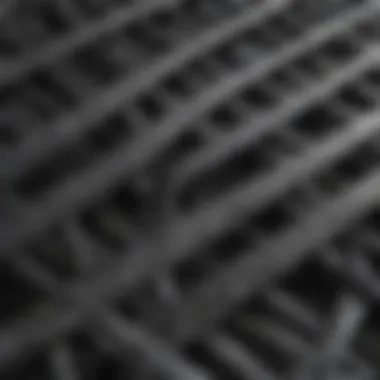
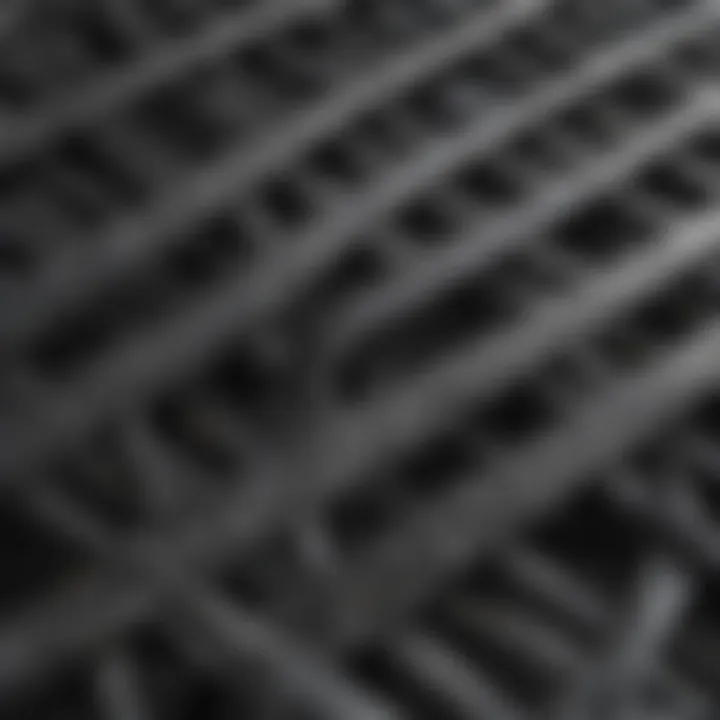
Intro
Carbon fibre has emerged as a material of significant interest in various domains, from aerospace to sports equipment. Its strength-to-weight ratio is unrivaled, making it an appealing choice for industries that prioritize both durability and lightness. Understanding carbon fibre involves examining its properties, applications, and future trends.
This article aims to provide a thorough analysis of the unique characteristics that make carbon fibre a standout material. Additionally, it will explore how it is manufactured, its applications across different sectors, and the probable advancements and environmental impacts.
Key Findings
Major Results
Through analysis, several key findings emerge regarding carbon fibre:
- Carbon fibre offers exceptional tensile strength, surpassing many traditional materials such as steel and aluminum.
- It is lightweight, which leads to improved fuel efficiency in aerospace and automotive applications.
- The versatility of carbon fibre allows for custom applications in sectors like construction, sports, and medical devices.
- Environmental concerns regarding the production and disposal of carbon fibre are becoming increasingly significant.
"The unique properties of carbon fibre, coupled with advancements in technology, allow for new innovations in design and functionality across multiple industries."
Discussion of Findings
The findings indicate that carbon fibre not only provides structural advantages but also opens new avenues for research and development. In industries such as aerospace, the reduction of weight can lead to greater efficiency and performance. Furthermore, the exploration of sustainable manufacturing practices is crucial as the demand for carbon fibre continues to rise. The ongoing discussion of its properties highlights the balance between innovation and environmental stewardship.
Methodology
Research Design
The research design of this article consists of a comprehensive literature review. This includes peer-reviewed journals, industry reports, and case studies to yield a wide range of insights regarding carbon fibre.
Data Collection Methods
Data was collected through:
- Reviewing scientific literature.
- Analyzing market trends and forecasts.
- Engaging with relevant industry experts through interviews and surveys.
These methods provide a robust understanding of carbon fibre and its impact on society today and in the future.
Preface to Carbon Fibre
The significance of carbon fibre in contemporary materials science cannot be overstated. Its unique blend of properties makes it an ideal choice for a variety of applications. Understanding carbon fibre is crucial for students, researchers, and professionals alike, particularly as industries seek innovative solutions to replace traditional materials.
Carbon fibre is renowned for its impressive strength-to-weight ratio. This characteristic allows for lighter designs without compromising structural integrity. As industries aim for efficiency and sustainability, carbon fibre presents a viable option that aligns with these goals.
Moreover, the growing demand for advanced materials in sectors like aerospace, automotive, and healthcare highlights the relevance of carbon fibre. Its versatility opens doors to applications that require materials capable of withstanding high stress and extreme conditions, contributing to advancements in technology and engineering.
As we explore the fundamental aspects of carbon fibre, understanding its definition and composition is essential. This lays the groundwork for appreciating its historical context and how it has evolved over time.
Definition and Composition
Carbon fibre consists of long, thin strands of carbon atoms bonded together in a crystal structure. These strands, typically less than 0.005 mm in diameter, are woven together to form fabrics or used in composite materials.
The primary composition of carbon fibre is derived from precursor materials. Common precursors used in the industry include polyacrylonitrile (PAN), pitch, and rayon. Each precursor impacts the final properties of the carbon fibre, influencing its performance in various applications.
The composition is not merely a science; it dictates the efficacy of carbon fibre in real-world usage. The combination of these elements determines its strength, weight, and thermal properties, making it customizable for specific industry requirements.
History and Development
The journey of carbon fibre began in the late 1950s when advancements in materials science made its production feasible. Initially, it was used for aerospace applications, where its strength and lightweight nature offered significant benefits.
In the 1970s, carbon fibre gained traction in the sporting goods market. The introduction of tennis rackets and bicycles made from this material showcased its potential in consumer products. As technology advanced, production processes were refined, leading to more widespread use.
The 21st century saw a dramatic increase in its applications. Industries such as automotive and medical devices started to incorporate carbon fibre, driven by trends towards lighter, stronger, and more durable materials.
Today, research is ongoing to enhance the properties of carbon fibre and its manufacturing processes. As we delve deeper into its properties, applications, and future trends, the historical context will serve as a foundation for understanding its current significance and potential.
Properties of Carbon Fibre
The study of carbon fibre properties is essential for various applications in engineering and materials science. Its unique characteristics make it a sought-after material across different industries. In this section, we will focus on key properties such as mechanical properties, thermal and electrical conductivity, and chemical resistance. Understanding these properties helps to evaluate the effectiveness of carbon fibre in comparative situations and also informs future innovations in material science.
Mechanical Properties
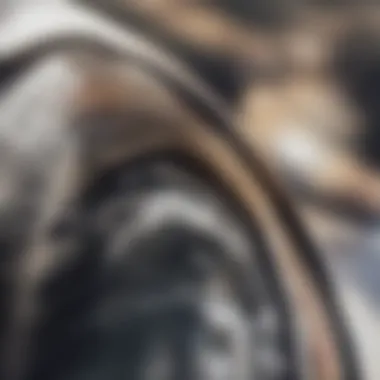
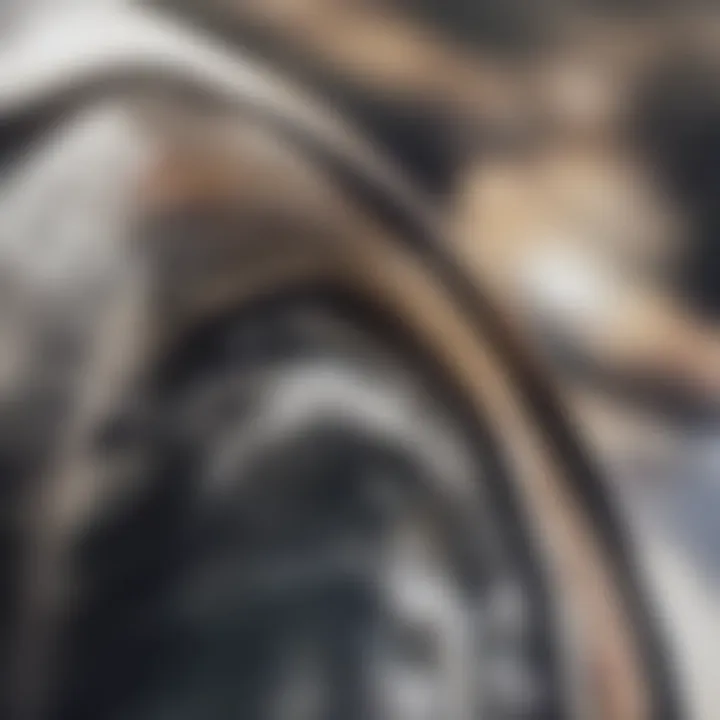
Mechanical properties include tensile strength, elastic modulus, and fatigue resistance. These factors are crucial because they determine how the material behaves under force, pressure, and other kinds of stress.
Tensile Strength
Tensile strength refers to a material's capacity to withstand stretching forces. Carbon fibre boasts impressive tensile strength, often surpassing that of steel. This is significant in applications where high strength-to-weight ratio is required, such as in aerospace and automotive sectors. The key characteristic of tensile strength is its ability to allow structures to remain light while supporting heavy loads.
The unique feature of tensile strength in carbon fibre lies in its lightweight nature and high efficiency. It provides advantages in fuel efficiency and performance. However, one must consider the challenges in achieving high tensile strength consistently during production.
Elastic Modulus
Elastic modulus is defined as the material's response to stress. It measures stiffness and indicates how much deformation occurs under loading. Carbon fibre has a high elastic modulus, making it very resistant to deformation. This property is beneficial for applications requiring precision and stability.
The critical aspect of elastic modulus is its relationship to stiffness. A higher elastic modulus implies better resistance to bending or stretching. This makes carbon fibre desirable in construction, but one drawback is that it can be less forgiving compared to more ductile materials, necessitating careful design choices.
Fatigue Resistance
Fatigue resistance is the ability of a material to withstand repeated loading and unloading without failing. Over time, materials can develop defects that lead to failure, but carbon fibre exhibits excellent fatigue resistance. This means it is suitable for high-stress environments and applications.
The unique aspect of fatigue resistance in carbon fibre makes it a wise choice for structures that undergo cyclical loads, such as aircraft components. While this property provides considerable longevity and reliability, it requires thorough testing and validation through quality control measures across batches.
Thermal and Electrical Conductivity
Carbon fibre demonstrates varying degrees of thermal and electrical conductivity. Its structure allows it to manage heat dissipation effectively, making it practical in high-temperature applications. That characteristic is particularly relevant in automotive and aerospace sectors, where excessive heat can lead to material failure.
On the electrical front, carbon fibre can conduct electricity, serving as a beneficial feature in certain technologies. Applications can range from sensors to composite materials that require electrical properties. However, its level of conductivity often varies with specific manufacturing processes, leading to inconsistencies that need addressing for reliable use.
Chemical Resistance
Carbon fibre also possesses notable chemical resistance. It can resist corrosion from many chemicals, making it suitable for use in harsh environments. This property enhances the longevity of products made from carbon fibre, promoting sustainability by minimizing replacement needs.
Nevertheless, it is essential to consider that while carbon fibre is resistant to numerous chemicals, it can react with strong acids and bases. Thus, its application must be carefully evaluated based on the environment where it will be utilized.
Manufacturing Processes
The manufacturing processes of carbon fibre play a crucial role in determining its quality, performance, and applicability. These processes not only dictate the characteristics of the final product but also address economic and environmental concerns associated with production. Understanding these processes provides insights into efficiency, material properties, and scalability. As industries increasingly shift towards lighter and stronger materials, an awareness of manufacturing methodologies becomes essential.
Precursor Materials
Polyacrylonitrile
Polyacrylonitrile, commonly known as PAN, is the most widely used precursor material for carbon fibre production. Its key characteristic is its high tensile strength, which facilitates the creation of strong fibres during the conversion process. PAN’s availability and its favorable mechanical properties make it a beneficial choice for carbon fibre synthesis.
One unique feature of polyacrylonitrile is its thermal stability, which enables it to withstand high processing temperatures. However, there are some disadvantages, particularly regarding its production cost and the environmental impact of its synthesis. Despite these concerns, its properties ensure that PAN remains a favored precursor in the carbon fibre industry.
Pitch
Pitch is another important precursor material used in carbon fibre manufacturing. Known for its high carbon yield, pitch has unique characteristics that allow it to produce fibres with excellent elastic modulus. This property is crucial in high-performance applications, where stiffness and strength are paramount.
A significant advantage of pitch is its relative low cost compared to PAN. However, its higher viscosity can make processing more challenging, which may limit its use in certain applications. Overall, pitch provides an alternative to PAN, especially where economic factors are considered.
Rayon
Rayon, a regenerated cellulose fibre, serves as a third precursor material in the production of carbon fibres. Rayon is notable for its ability to produce fibres with high tensile strength. Its key advantage lies in its sustainability; as a cellulose-based material, it sources from renewable resources.
However, compared to PAN and pitch, rayon offers lower carbon yields and can result in a less consistent fibre quality. These factors can influence its adoption in the industry. Nonetheless, rayon’s sustainable profile presents an attractive option for environmentally conscious production processes.
Production Techniques
Filament Winding
Filament winding is a vital production technique in carbon fibre manufacturing. This method involves winding continuous strands of carbon fibre over a mold to create composite structures. The key advantage of filament winding is its ability to produce complex shapes with high fiber volume fractions, enhancing the overall strength of the composite.
One unique feature is the preciseness with which the fibre can be laid down, optimizing the alignment in the desired direction, thus significantly improving mechanical properties. However, the challenge lies in the initial setup costs and the need for specialized equipment, which can deter some manufacturers.
Pultrusion
Pultrusion is another manufacturing method where resin-impregnated fibres are pulled through a heated die to form continuous lengths of composite material. This process creates products with uniform cross-sections, crucial for structural applications. Pultrusion’s key characteristic is its efficiency; it can produce long lengths of carbon fibre profiles with consistent quality.
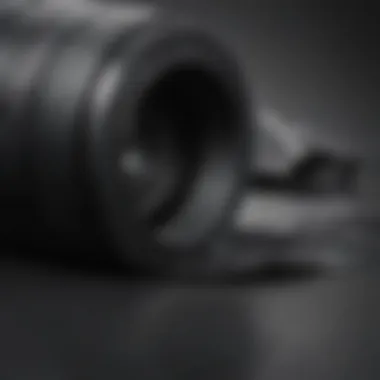
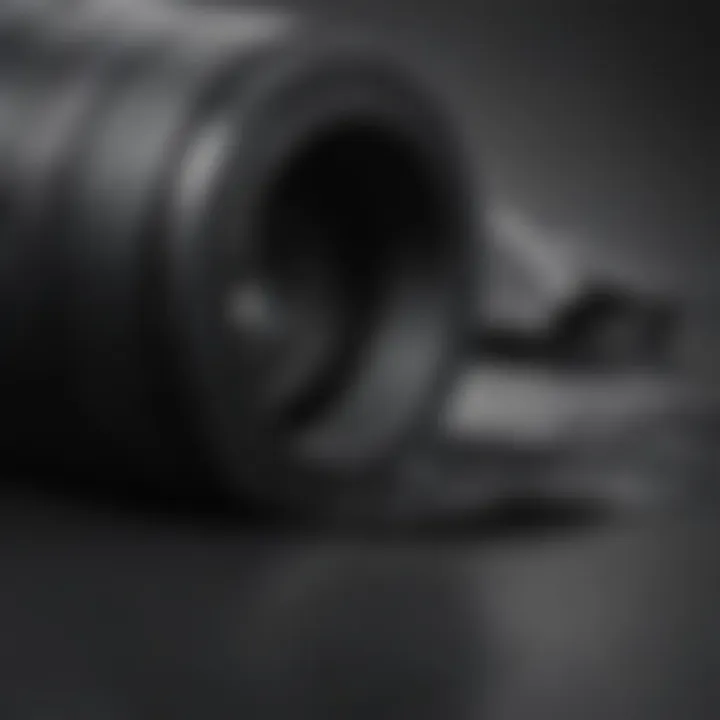
However, a limitation is that it is best suited for shapes that do not require extensive intricate detail. Additionally, it may not be as versatile for varied applications compared to other methods.
Prepreg Layup
Prepreg layup involves the use of pre-impregnated carbon fibre materials that have a resin system already applied. This technique allows for precise control over fibre placement and resin content. A key advantage of prepreg layup is its ability to produce lightweight composites with excellent mechanical performance.
One unique feature is the extended working time prior to curing, providing manufacturers with flexibility during the assembly process. However, the need for refrigeration to maintain the prepreg’s integrity can add complexity and cost to the storage and logistics of materials.
Quality Control and Testing
Quality control and testing methods are critical in ensuring that carbon fibre products meet performance standards. These processes include various destructive and non-destructive testing methods to assess properties such as tensile strength, fatigue resistance, and thermal stability. Regular quality assessments not only guarantee product reliability but also help in maintaining consistent manufacturing practices, ensuring the material's longevity in applications across aerospace, automotive, and other sectors.
"Quality control in carbon fibre production is not just a process, but an assurance of performance and safety across its applications."
Applications of Carbon Fibre
The application of carbon fibre is a pivotal topic in this article, as it showcases the material's versatility and significance across various industries. Understanding these applications allows for a deeper appreciation of carbon fibre's role in modern engineering and technology. Moreover, it elaborates on the specific elements, benefits, and considerations surrounding its usage.
Aerospace and Aviation
In the aerospace and aviation sectors, carbon fibre is crucial due to its lightweight and strength properties. The reduction in weight contributes significantly to fuel efficiency, which is vital for both commercial and military aircraft. Components made from carbon fibre, such as fuselage sections and wing structures, provide durability while reducing the overall mass of the aircraft. This composite material enables engineers to design better-performing aircraft that can carry more payload over longer distances, enhancing both commercial viability and operational effectiveness.
Automotive Industry
Performance Cars
Performance cars benefit immensely from carbon fibre. The lightweight nature of carbon fibre contributes to speed and agility, making it a preferred choice for high-performance vehicles. These cars utilize carbon fibre in various components, such as body panels and interior parts, providing both strength and aesthetics. The reduction in weight from using carbon fibre means enhanced acceleration and braking, a vital aspect that performance car enthusiasts value highly. Thus, carbon fibre is not just a functional choice; it is also a statement of engineering excellence.
Electric Vehicles
Electric vehicles (EVs) are another area where carbon fibre plays a significant role. The unique characteristic of carbon fibre, being much lighter than traditional materials like steel, directly impacts the efficiency and range of electric cars. By using carbon fibre, manufacturers can minimize the weight of EVs, leading to improved battery life and overall performance. However, integrating carbon fibre into EVs also comes with its challenges, such as higher production costs. This makes the choice of materials a balancing act between performance and affordability, crucial for the growing EV market.
Sporting Goods
The sporting goods industry has seen an increasing integration of carbon fibre. From bicycles to tennis rackets, carbon fibre enhances performance through weight reduction and increased stiffness. Athletes benefit from the superior properties of carbon fibre, which can yield better results in competitions. However, the premium price point can limit accessibility for some consumers.
Medical Devices
In medical technology, carbon fibre is applied in devices like prosthetics and surgical instruments. Its combination of lightweight and strength is essential to developing cutting-edge devices that improve patient outcomes. For instance, carbon fibre allows for prosthetics that are both comfortable and durable. The precision offered by carbon fibre in surgical tools can lead to better results in operations. Still, the high cost of carbon fibre may present challenges for widespread adoption in certain medical applications.
Advantages of Carbon Fibre Over Traditional Materials
Carbon fibre has emerged as a viable alternative to traditional materials such as steel and aluminum. Its distinct characteristics bring about notable benefits to many industries, particularly aerospace, automotive, and construction. In this section, we will explore the two main advantages: weight reduction and enhanced durability. Understanding these advantages is crucial for making informed decisions about material selection in various applications.
Weight Reduction
One of the most significant advantages of carbon fibre is its exceptional strength-to-weight ratio. This parameter refers to how much strength a material provides relative to its weight. Carbon fibre is lightweight yet remarkably strong. For instance, carbon fibre can have a strength that is five times greater than that of steel at roughly one-fifth the weight.
- The reduction in weight directly translates to improved fuel efficiency in vehicles, especially in the aerospace and automotive industries. Lighter structures require less energy for propulsion, leading to reduced operational costs.
- In automotive design, lighter components can significantly enhance performance. Acceleration speeds can improve, and handling can become more responsive. This attribute is increasingly important in the era of electric vehicles, where maximizing range is a primary concern.
- Weight reduction also allows for more design flexibility. Engineers can incorporate advanced designs and shapes without worrying about adding excessive weight.
The benefits become evident when investigating how vehicles are engineered. For instance, some manufacturers use carbon fibre in chassis design, resulting in quicker and more efficient vehicles. Brands like BMW in their M series and Boeing in their 787 Dreamliner, utilize carbon fibre extensively to achieve superior performance.
Enhanced Durability
Durability is another prominent advantage of carbon fibre that cannot be overlooked. It showcases excellent resistance to fatigue and impact, which prolongs the lifespan of products made from it. Traditional materials may corrode or deform under stress. In contrast, carbon fibre maintains its integrity over time.
- Fatigue Resistance: Carbon fibre's structure allows it to withstand repeated stress better than metals. This feature is essential in applications where parts experience repetitive loads, such as in aircraft wings or automotive components.
- Corrosion Resistance: Carbon fibre does not corrode like steel. It is inherently resistant to environmental factors, including moisture and chemicals. This property ensures a greater lifespan with lower maintenance needs.
- Impact Resistance: While carbon fibre can be brittle, advancements in composite technology have improved its performance in impact situations. In contexts like sports equipment, where sudden force is common, the material can absorb energy without failing.
Challenges and Limitations of Carbon Fibre
Carbon fibre represents a significant advancement in materials science. However, it is crucial to recognize the challenges and limitations inherent in its production and application. Understanding these issues is essential for researchers, industry professionals, and end-users alike. Without addressing these limitations, the potential of carbon fibre may be hampered, affecting its integration into various sectors.
Cost of Production
The production of carbon fibre is currently associated with high costs. Various factors contribute to the elevated price. Firstly, the precursor materials like polyacrylonitrile require extensive processing. This involves several stages, including spinning, stabilization, and carbonization, each demanding considerable energy and specialized equipment. For instance, the energy required during these processes can significantly inflate production costs, making carbon fibre less accessible to a wider market.
Moreover, small-scale manufacturers struggle to compete due to the economies of scale enjoyed by larger companies. Bulk production often leads to lower costs per unit, leaving small enterprises at a disadvantage. As a result, many manufacturers hesitate to invest in carbon fibre technologies, limiting innovation in applications where it could be beneficial.
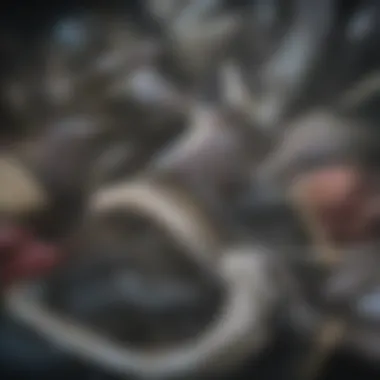
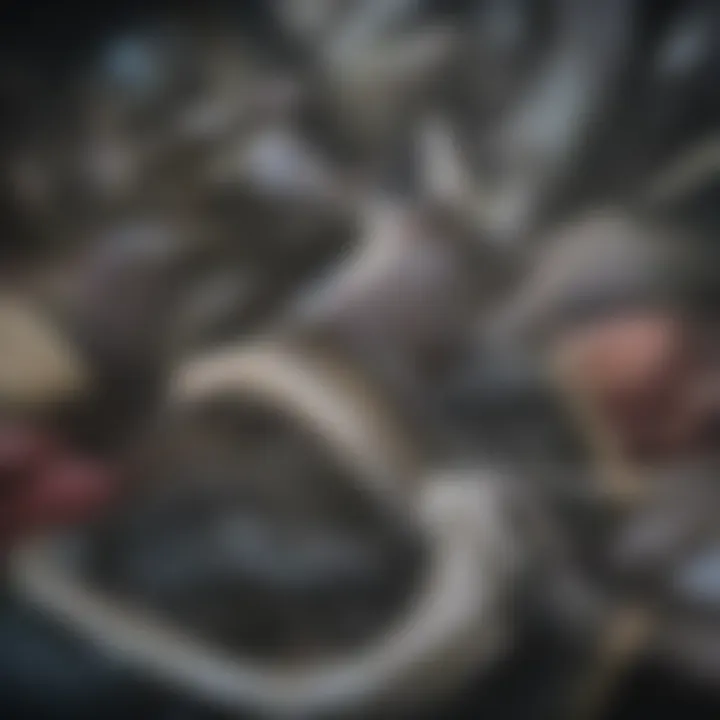
Recycling Issues
Another prominent limitation of carbon fibre lies in its recycling potential. Unlike traditional materials such as metals or plastics, carbon fibres present unique challenges during the recycling process. Once used, the current methods of recycling carbon composite materials are often inefficient and costly. Separating the fibres from the resin matrix is complex and often leads to quality degradation in the recycled material.
Furthermore, many carbon fibre products are not designed with end-of-life recycling in mind. This lack of foresight results in a significant amount of wasted material. In a world where sustainability is increasingly prioritized, the inability to recycle carbon fibre effectively brings into question its environmental viability.
"Addressing cost and recycling challenges is essential for the sustainable future of carbon fibre materials."
Future Trends and Innovations
The landscape of carbon fibre technology is evolving. Understanding future trends and innovations in this field is crucial for several reasons. First, it helps highlight the ongoing research and development aimed at enhancing the utility and efficiency of carbon fibre materials. Furthermore, these developments can significantly influence industries such as aerospace, automotive, and even renewable energy. Keeping abreast of these trends also aids professionals in making informed decisions about material selection and application.
Biocomposite Carbon Fibres
Biocomposite carbon fibres represent a significant shift in material science. These fibres integrate natural materials with traditional carbon fibre production techniques. The goal is to create a product that offers the robustness of carbon fibre while being eco-friendly. The incorporation of renewable resources helps reduce the carbon footprint associated with carbon fibre manufacturing.
Benefits of biocomposite carbon fibres include:
- Lighter weight than traditional fibres, which can enhance performance in various applications.
- Reduced environmental impact by utilizing renewable sources and minimizing waste.
- Sustainability in product life cycles through better recycling options.
The production of biocomposite carbon fibres still faces challenges, particularly in maintaining the mechanical properties that are characteristic of conventional carbon fibre. However, ongoing research aims to find a balance that maximizes both sustainability and performance of the fibres.
Integration with Smart Technology
The integration of smart technology into carbon fibre materials is another promising direction. Smart technology involves embedding sensors and electronic components into carbon fibre structures. This allows for real-time monitoring of conditions such as temperature, stress, and physical integrity. The potential applications are vast, from aerospace structures to protective gear in sports.
Some benefits of integrating smart technology include:
- Enhanced safety through continuous monitoring of structural health.
- Increased efficiency by providing data that can optimize performance.
- Adaptability to various conditions, enhancing the usability of carbon fibre components.
Overall, the blend of carbon fibre technology and smart integrations showcases the potential for future innovations that can transform industries. This area is under active research, paving the way for more advanced and intelligent materials.
"The next decade is expected to witness unprecedented advances in carbon fibre technology, revolutionizing its applications across numerous fields."
As we observe these trends, it's clear that carbon fibre's future is intertwined with environmental considerations and technological advancements, emphasizing the importance of ongoing innovation.
Environmental Impact of Carbon Fibre Production
The topic of environmental impact in carbon fibre production is critical in discussing its overall lifecycle. As industries increasingly turn to this advanced material for its superior properties, understanding its ecological footprint becomes essential. The production of carbon fibre entails various processes that contribute to its carbon footprint, raising concerns regarding sustainability. By examining these aspects, we can identify the necessary steps to mitigate negative outcomes and promote environmentally-friendly practices.
Carbon Footprint
The carbon footprint of carbon fibre production is a significant concern due to its energy-intensive nature. Typically, most carbon fibres are produced from polyacrylonitrile (PAN), which itself undergoes complex chemical processes. Each stage of production—spinning, stabilization, carbonization, and surface treatment—consumes large amounts of energy, primarily derived from fossil fuels. This heavy reliance results in substantial greenhouse gas emissions.
- Key contributors to the carbon footprint:
- High energy consumption during manufacturing
- Use of non-renewable energy sources
- Emission of volatile organic compounds during processing
Research suggests that the carbon footprint for producing one kilogram of carbon fibre can be around 20 to 30 kilograms of CO2 equivalent emissions. This data highlights the critical need for alternative methods or materials that can either reduce these emissions or utilize renewable energy sources to achieve a balance in ecological impact.
Sustainability Measures
In light of the significant environmental costs associated with carbon fibre production, there are effective sustainability measures that can be adopted. These measures aim to reduce the carbon footprint and promote more sustainable practices within the industry.
- Utilization of Renewable Energy:
Industries can shift towards renewable energy sources such as solar, wind, or hydroelectric power. This change can significantly lower emissions associated with production processes. - Development of Biocomposite Carbon Fibres:
Innovations in biocomposites can lead to the incorporation of natural fibers that are renewable and biodegradable, thus reducing reliance on synthetic precursors. - Improved Recycling Techniques:
Advancing recycling technologies for carbon fibre can facilitate the reuse of materials, minimizing waste and decreasing the demand for new raw materials.
Overall, by implementing these sustainability measures, the carbon fibre industry can transition towards a more environmentally responsible future, balancing the benefits of this high-performance material with essential ecological considerations.
Ending
In this article, we have delved into the complex world of carbon fibre, illuminating its various properties and applications. The importance of understanding carbon fibre lies not only in its remarkable characteristics but also in how it shapes modern industry and innovation.
Summation of Key Points
Carbon fibre is a high-performance material that offers several advantages over traditional materials. Its lightweight yet strong nature makes it invaluable in industries like aerospace and automotive. Key points to take away include:
- Mechanical Properties: Carbon fibre’s tensile strength and fatigue resistance ensure longevity and reliability in products.
- Applications: From performance cars to medical devices, its versatility is evident across numerous sectors.
- Environmental Considerations: While production can be resource-intensive, ongoing research into sustainable practices is essential.
- Future Trends: Innovations like biocomposite carbon fibres and smart technology integrations promise to enhance its utility.
"Carbon fibre is transforming industries by offering solutions that were previously unachievable with conventional materials."
Looking Ahead
The journey of carbon fibre is far from complete. As the emphasis on sustainability increases, the development of more eco-friendly carbon fibre production methods will likely be a significant focus. Researchers and industry leaders are exploring how to make carbon fibre recycling feasible and efficient. Furthermore, we can anticipate the integration of smart technologies that connect carbon fibre components to digital ecosystems. The future holds much promise, granting expansive opportunities for both research and application in the ever-evolving landscape of material science.