Transforming Utility Maintenance with Inspection Robots
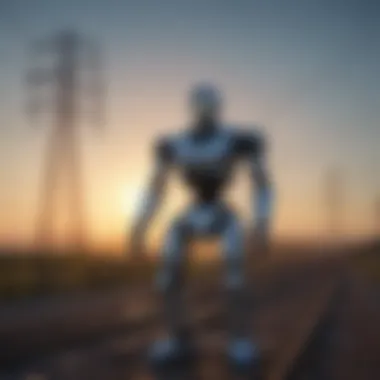
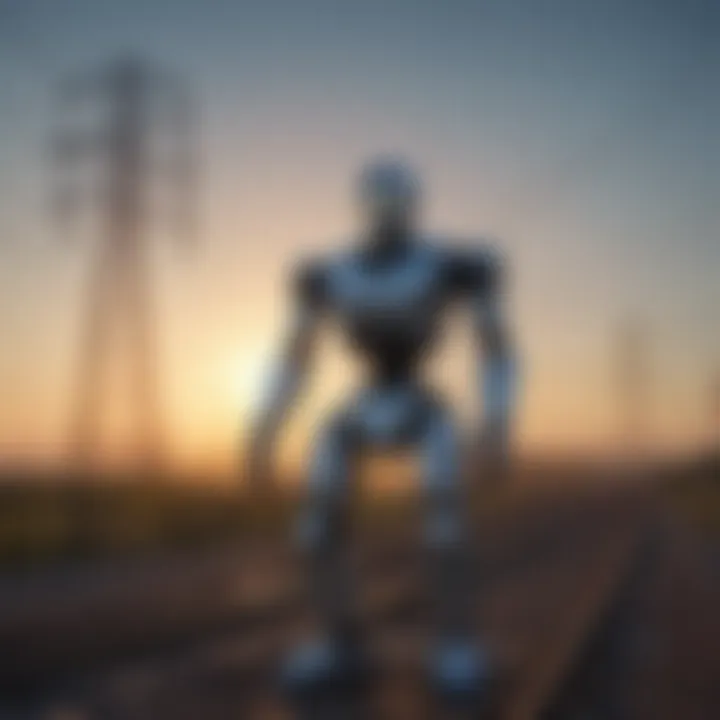
Intro
The evolving landscape of utility maintenance has seen remarkable advancements, and one of the most significant developments is the integration of transmission line inspection robots. These robots play a vital role in ensuring that power transmission networks operate efficiently and safely. As infrastructure ages, the need for constant monitoring intensifies. Traditional inspection methods, which often involve extensive manual labor and heighten safety risks, are giving way to robotic solutions that enhance both precision and safety.
This discussion aims to highlight key findings related to the use of these robotic systems, delve into methodological approaches employed in the field, and explore the broader implications of their adoption for utility maintenance. By shifting focus to technology-driven solutions, we examine the innovative frameworks that underpin robotic inspections and their contributions to the industry.
Key Findings
As the utility sector increasingly relies on technology, numerous key findings emerge regarding the effectiveness of transmission line inspection robots.
Major Results
- Efficiency Gains: Robots can conduct inspections significantly faster than humans. They reduce the time required to assess infrastructure conditions, allowing for quicker responses to potential issues.
- Safety Improvements: The risks associated with climbing poles or traversing hazardous weather conditions are considerably diminished. Robots perform inspections in environments that may be dangerous for human workers.
- Cost-Effectiveness: Although the initial investment in robotic technology may be high, long-term savings are evident. Reduced labor costs, fewer downtimes, and proactive maintenance lead to improved budget management.
Discussion of Findings
The findings suggest that the implementation of these robots not only enhances the effectiveness of inspections but also reassures stakeholders about the integrity of infrastructure. Analyzing data from various deployments reveals a trend toward increasing adoption among utilities worldwide. The convergence of artificial intelligence and machine learning within these robots allows for predictive maintenance, meaning potential issues can be resolved before they lead to significant failures.
"The implementation of robotics in utility maintenance not only transforms operational capabilities but also presents a crucial advantage in minimizing risks associated with manual inspections."
Methodology
To better understand the impact of transmission line inspection robots, it is essential to consider the methodologies involved in their deployment and effectiveness evaluation.
Research Design
This report draws on qualitative and quantitative research methods. The combination allows for a comprehensive understanding of the robots’ impacts on maintenance routines.
Data Collection Methods
Data was collected through direct observations, interviews with utility personnel, and analysis of operational data from utility companies utilizing these robots. Surveys distributed to engineers and operators offer additional insight into the robots' performance and acceptance within the workplace.
For further reading, visit sources such as Wikipedia, Britannica, or community discussions on Reddit and Facebook.
Intro to Transmission Line Inspection Robots
Transmission line inspection robots are increasingly recognized as crucial tools in the field of utility maintenance. They provide a new dimension of efficiency and safety in infrastructure management, particularly in the energy sector. This article delves into how these robots not only streamline the inspection process but also enhance the reliability of power transmission systems.
Definition and Purpose
Transmission line inspection robots are specialized machines designed to assess the condition of overhead power lines and related infrastructure. These robots operate using various technologies, including drones and ground-based systems. Their primary purpose is to identify potential issues such as corrosion, wear, and other structural weaknesses. By automating the inspection process, these robots significantly reduce the need for human labor in dangerous environments, thus improving safety.
The deployment of these robots is driven by the need to maintain a consistent power supply while minimizing operational risks. They can cover extensive distances quickly, gathering data that can be analyzed to determine when maintenance tasks should be performed. As technology continues to evolve, these robots are becoming more sophisticated, combining advanced sensors and imaging technologies to provide detailed insights.
Importance in Modern Engineering
The significance of transmission line inspection robots in modern engineering cannot be overstated. They enhance operational efficiency and maintain high safety standards in utility maintenance. Traditional inspection methods, which often involved manual checks performed by workers, generally carry higher risk and are more time-consuming. In contrast, robots are capable of executing inspections in adverse weather conditions or during non-peak hours, thus ensuring minimal disruption to power services.
Moreover, the use of these robots contributes to cost-effectiveness by reducing the frequency of outages and maintenance-related emergencies. By catching potential problems early, utility companies can prevent costly repairs and service interruptions. The integration of robotic inspection systems into maintenance protocols marks a significant advancement in engineering practices, showing that embracing technology can lead to better outcomes for both service providers and consumers.
"Incorporating transmission line inspection robots is no longer just an option; it’s a necessity in maintaining the integrity of our power infrastructure."
The ongoing development in this field indicates that as inspection robots become more advanced, their roles will expand beyond mere inspections. They will likely evolve to include predictive maintenance and real-time monitoring capabilities, indicating a shift towards more intelligent and responsive systems in power line management.
Historical Development of Inspection Technologies
The advancement of inspection technologies for transmission lines has a substantial impact on how utility maintenance operates today. Understanding the historical evolution of these technologies reveals the driving forces behind the development of present-day robotic systems. This section highlights the progression from early inspection methods to the sophisticated robotics employed today. By analyzing these developments, we can appreciate the efficiency, safety, and accuracy offered by modern inspection technologies.
Early Inspection Methods
In the early days of utility maintenance, inspection methods relied on manual labor. Teams of engineers and technicians conducted visual inspections, often requiring unsafe physical access to high-altitude transmission lines. These methods were not only labor intensive but also prone to human error.
- Visual Inspections: Utility workers used binoculars and handheld equipment to check for visible wear and tear. They looked for corrosion, broken components, or vegetation encroachment. Although important, this method lacked precision and could not detect underlying issues.
- Climbing Techniques: Inspectors often climbed poles to execute thorough examinations, placing their safety at significant risk. This hands-on approach had drawbacks, including a slow pace of inspection and higher likelihood of accidents.
- Mobile Platforms: Some utilities started employing bucket trucks to reach high lines, adding some level of safety and efficiency compared to traditional climbing. However, these vehicles still presented logistical challenges, including limited maneuverability in certain terrains and the costs associated with their operation.
The limitations from these early methods highlighted the necessity for more efficient and safer inspection techniques, setting the stage for later advancements.
Evolution to Robotics
As technology progressed, a shift towards automation began to take shape. The entrance of robotics into transmission line inspection marked a key turning point in utility maintenance.
- Introduction of Drones: The advent of drones revolutionized the industry. These aerial devices enabled remote inspections, equipped with cameras and sensors capable of capturing high-resolution images. Drones reduced inspection times significantly, allowing for quicker assessments while minimizing worker risks.
- Autonomous Ground Robots: Following drone innovations, ground-based robots emerged. These robots can traverse difficult terrains and perform inspections autonomously. Utilizing advanced sensors and imaging technology, ground robots can identify structural issues and relay data to decision-makers in real-time.
- Hybrid Systems: The most recent development involves hybrid systems that integrate both aerial and ground capabilities. By employing both types of inspection technologies, utilities can achieve a comprehensive evaluation of their infrastructure. Moreover, these systems can operate in different environments seamlessly, increasing overall inspection efficiency.
In summary, the evolution from manual inspections to robotics illustrates a compelling journey toward safety, accuracy, and efficiency in utility maintenance. Innovations in technology not only enhanced the quality of inspections but also reduced the risks associated with them. Understanding this historical context is crucial for appreciating the current capabilities of transmission line inspection robots, which play a pivotal role in modern utility maintenance.
Types of Transmission Line Inspection Robots
Understanding the various types of transmission line inspection robots is essential for gaining insights into how these machines enhance utility maintenance. Each category serves distinct functions and comes with its own set of advantages. This diversity enables utility companies to address specific inspection needs effectively.
Aerial Inspection Drones
Aerial inspection drones have emerged as a preferred choice for many operators due to their flexibility and widespread usability. These flying machines are equipped with high-resolution cameras, infrared sensors, and other advanced imaging technologies.
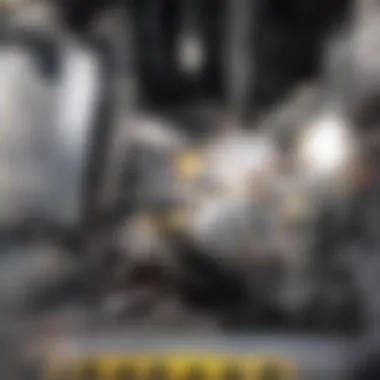
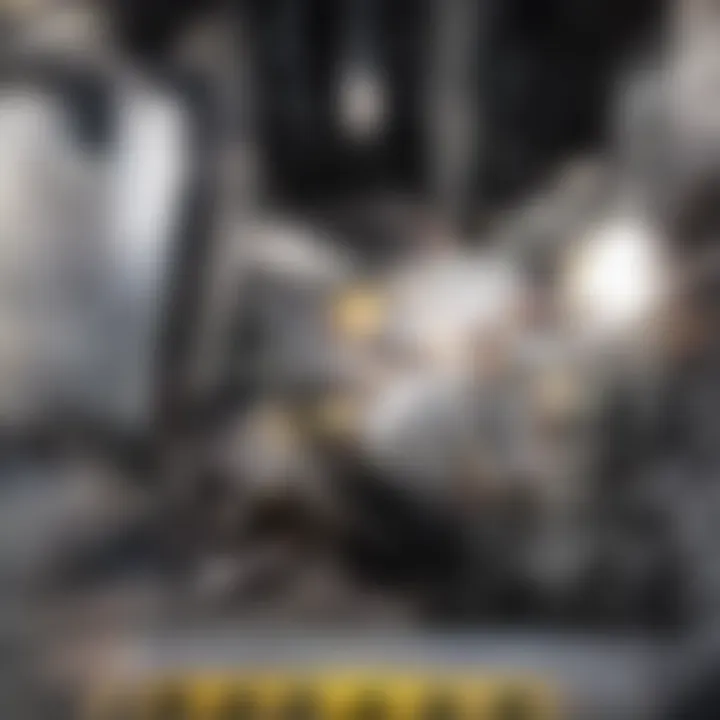
- Advantages: Their ability to cover large areas quickly reduces downtime and enhances the speed of inspections. This is particularly beneficial in areas that are difficult to access by ground means.
- Considerations: While drones can operate autonomously, they still require careful management in terms of flight paths and regulatory compliance.
Aerial drones not only inspect physical infrastructure but also provide real-time data, which can be analyzed to measure the health of the transmission lines. Their versatility in weather conditions adds to their appeal for utility maintenance organizations.
Ground-Based Robots
Ground-based robots offer a different approach to inspection. These robotic systems are designed to traverse the terrain beneath the transmission lines, inspecting components up close. They utilize a range of technologies, including cameras and ground-penetrating radar, to assess line health comprehensively.
- Benefits: One of the integral benefits is their ability to detect physical damages that may be overlooked from the air. This includes inspecting foundations and other structural components.
- Limitations: However, their operational speed is generally slower compared to aerial drones. They also may require support vehicles for mobility, particularly in rugged terrains.
In summary, ground-based robots add a layer of detailed analysis to inspections, ensuring that no critical aspect of the infrastructure is ignored.
Hybrid Inspection Systems
Hybrid inspection systems combine the best features of both aerial and ground-based technologies. They utilize drones for aerial surveillance while deploying ground robots for detailed inspections where necessary. This integrated approach allows for a comprehensive examination of the entire line structure.
- Key Features: These systems can adapt to changing conditions, switching between aerial and ground inspections to gather the most pivotal data.
- Operational Efficiency: Utilizing both forms means that data can be cross-referenced, leading to more accurate assessments and efficient allocation of resources.
With the capability to optimize inspection routines, hybrid systems showcase the evolution of robotic technology in utility maintenance, ultimately leading to improved safety and cost reductions.
Hybrid inspection systems exemplify the potential for advanced technology to redefine operational limits.
Core Technologies Behind Inspection Robots
The development of transmission line inspection robots hinges on various core technologies. These technologies are vital not only for the operational capacity of inspection robots but also for enhancing their effectiveness, accuracy, and reliability. Understanding these elements allows stakeholders to appreciate how inspection robots provide critical insights and timely maintenance solutions. This section highlights three key technological components: sensors and imaging technologies, autonomous navigation systems, and data processing and analysis software.
Sensors and Imaging Technologies
Sensors and imaging technologies form the backbone of inspection robots. These technologies enable the robots to gather crucial data regarding the condition of transmission lines. Various types of sensors, including thermal cameras, LiDAR, and ultrasonic sensors, play distinct roles in assessing infrastructure integrity.
- Thermal cameras detect temperature variations, which can signal electrical faults or overheating, helping to prevent outages.
- LiDAR uses laser light to measure distances accurately, generating detailed three-dimensional maps of transmission lines and nearby structures.
- Ultrasonic sensors detect cracks or material degradation that may not be visible to the naked eye.
These sensor technologies equip robots to conduct thorough inspections efficiently, especially in challenging environments. The ability to conduct detailed visual inspections reduces the need for human intervention, minimizing risk and optimizing resource allocation.
Autonomous Navigation Systems
Autonomous navigation systems enable inspection robots to move independently across expansive areas without direct human control. This capability is crucial for accessing remote or hazardous locations where traditional inspection methods would be unsafe or impractical. Technologies such as GPS, inertial measurement units, and obstacle detection sensors collaborate to facilitate effective navigation.
- GPS allows robots to track their location accurately, which is essential for mapping and data collection.
- Inertial measurement units help maintain stability and orientation as the robots traverse uneven terrain.
- Obstacle detection sensors ensure safe navigation by identifying and avoiding obstacles in real-time.
The integration of these systems enhances the efficiency of inspection processes. Robots can cover large distances quickly while performing detailed assessments, thereby significantly reducing downtime for maintenance.
Data Processing and Analysis Software
Once data is collected through sensors, it must be processed and analyzed to extract actionable insights. Data processing and analysis software is designed to convert raw data into understandable and usable information. Advanced algorithms and machine learning techniques analyze the data, detecting patterns and anomalies that may indicate issues.
- Real-time data analysis allows for immediate feedback, where potential failures can be identified and addressed promptly.
- Machine learning models improve over time, becoming more accurate in predicting faults based on historical data patterns.
By leveraging these software capabilities, utility companies can make informed decisions regarding maintenance schedules, ultimately leading to increased reliability and safety of the power transmission networks. It also contributes to reducing operational costs by identifying necessary repairs before they escalate into larger problems.
"Core technologies drive the efficiency and reliability of inspection robots, shaping the future of utility maintenance."
In summary, the integration of sophisticated sensors, autonomous navigation, and advanced data processing frameworks redefine how transmission line inspections are conducted. These core technologies minimize human intervention and enhance the precision of inspections, paving the way for a more efficient and cost-effective approach to infrastructure maintenance.
Operational Efficiency of Inspection Robots
The operational efficiency of transmission line inspection robots plays a crucial role in the modern framework of utility maintenance. Their deployment not only transforms the way inspections are conducted, but also significantly impacts the overall reliability and safety of power transmission networks. With the mandate of ensuring uninterrupted service to consumers, utility companies are increasingly turning to robotics as a solution to enhance operational protocols.
Efficient robots reduce manual labor and allow for to scale inspections that would otherwise require extensive human resources and time. This efficiency is essential, especially when it comes to managing the vast distances of transmission lines. The advantages span across multiple areas, including improved scheduling, enhanced time management, and overall cost effectiveness.
Scheduling and Time Management
Effective scheduling and time management are fundamental for any maintenance operation. In the context of transmission line inspections, these robots provide precise scheduling capabilities that traditional methods cannot match. They operate autonomously and can be programmed to conduct inspections according to the utility’s operational timeline.
By utilizing real-time data, inspection robots can prioritize tasks based on current conditions and performance indicators. This not only streamlines the workflow but also allows companies to allocate resources more effectively.
Additionally, the ability to conduct inspections during off-peak hours can help minimize disruptions to power supply and maintenance activities.
- Autonomy: Robots can operate independently, saving time spent on planning.
- Real-time Analysis: Immediate data collection allows for rapid decision-making.
- Flexible Scheduling: Inspections can occur at times optimized for the utility’s operations.
Cost-Effectiveness Evaluations
Cost-effectiveness is a pivotal factor in any utility maintenance strategy. The integration of transmission line inspection robots presents a notable reduction in operational costs over time. Initial investment in these robots may seem significant but is quickly offset by the reduction in labor, increased inspection speed, and fewer equipment failures.
When evaluating cost-effectiveness, several aspects come into play:
- Labor Savings: Fewer human resources are required for inspections.
- Reduced Downtime: Prompt inspections result in quicker response to repair needs.
- Long-Term Reliability: Enhanced maintenance leads to fewer outages.
"Robotic systems, through their efficiency and cost savings, are not just beneficial but essential for future utility management."
Applications in Different Sectors
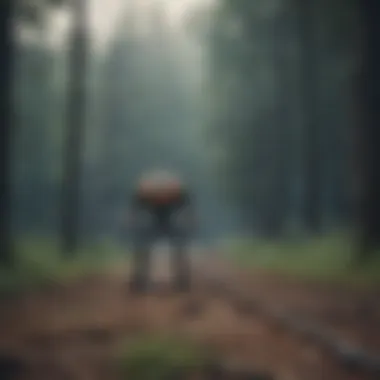
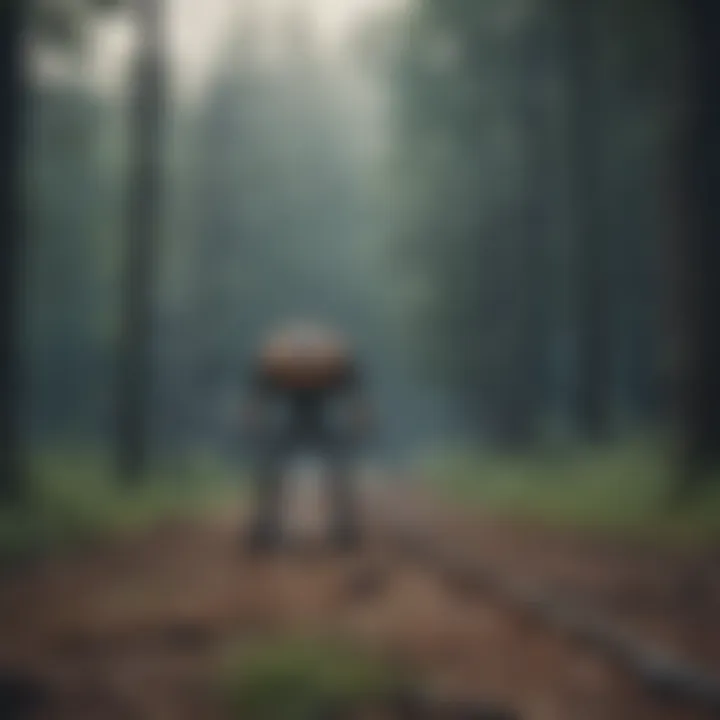
Transmission line inspection robots significantly impact various industries. Their deployment goes beyond efficiency; it embodies safety and reliability. This section explores how these robots serve essential roles in the utilities, energy, and telecommunications sectors. Understanding these applications highlights the multifaceted benefits and innovations in robotic inspection technologies.
Utilities and Energy Sector
In the utilities and energy sector, transmission line inspection robots are essential for maintaining grid integrity. They streamline assessment procedures, ensuring quick detection of line defects. These machines can cover vast areas quickly, identifying potential hazards such as loose connections or damaged insulators. This speed enhances operational reliability in power delivery.
Inspection robots provide detailed data through advanced imaging and sensor technologies. This data helps engineers make informed decisions about maintenance schedules and required repairs. By adopting these technologies, utility companies can optimize their resources, reducing manpower required for inspections. This automation minimizes human error and improves the quality of assessments.
Additionally, safety is a prime concern in this sector. Robots significantly reduce risks to human inspectors who might otherwise work in hazardous environments. By enabling remote operation and analysis, the risk of accidents diminishes. This operational shift marks a crucial advancement in how utilities approach line inspections.
Telecommunications
In the telecommunications field, the reliability of networks hinges on well-maintained transmission towers and lines. Inspection robots play a pivotal role in this ecosystem. They assess the conditions of communication infrastructure, ensuring that connections remain uninterrupted. This is especially critical in upscale areas where communication outages can lead to significant financial losses.
These robots facilitate routine checks of antennae, cables, and other communication equipment. Regular inspections help in predicting failures, thus allowing pre-emptive maintenance. By identifying issues early on, companies can mitigate downtime and maintain service quality for their clients.
Moreover, inspection robots in telecommunications can reach areas that might be challenging for human technicians. This flexibility further broadens the scope of inspections, ensuring comprehensive coverage. Like in the utilities sector, adopting these technologies reduces the risk involved in inspections, promoting a safer working environment for human operators.
"The application of robotic inspection methods revolutionizes the way we maintain critical infrastructure, enhancing both safety and efficiency in the process."
In summary, transmission line inspection robots are integral to modernizing maintenance in utilities and telecommunications. Their ability to boost operational efficiency while upholding safety standards makes them invaluable across sectors.
Challenges and Limitations
The rise of transmission line inspection robots marks a significant shift in utility maintenance practices. However, this evolution is not without its challenges and limitations. Understanding these obstacles is crucial for stakeholders who wish to leverage robotic technology effectively. This section discusses technical challenges faced in the operation of these robots, as well as regulatory and safety concerns that need to be addressed for safe implementation.
Technical Challenges
One of the major technical challenges is the development of advanced sensors capable of accurately assessing the condition of transmission lines. Transmission systems are often located in diverse environments, which can vary drastically in terms of terrain and weather. This variability can affect sensor performance. For example, rain or excessive dust might obscure vision systems required for inspections. Moreover, ensuring that robots can operate autonomously in these conditions remains a significant hurdle.
The integration of various technologies also poses complexities. Data derived from sensors must be reliably processed in real-time to provide actionable insights. Achieving effective data fusion from multiple sources, including visual and thermal imaging, can be tricky. Ensuring high levels of reliability and efficiency in data processing is essential for the robot to offer consistent performance.
"The complexity of integrating new technologies into existing infrastructures may slow down the rapid adoption of inspection robots."
Another prominent issue is maintaining the communication link between the robots and control centers. Interference from other electronic devices and geographical obstacles can disrupt the signal, leading to inefficiencies in operations. To tackle these issues, robustness against signal loss and adaption to changing conditions is vital.
Regulatory and Safety Concerns
Regulatory frameworks surrounding the deployment of inspection robots are still developing. As with any emerging technology, there is a growing need to establish clear guidelines to govern their use. These regulations should consider the technical capabilities and limitations of the robots, ensuring they are safe for both the infrastructure being inspected and the personal operating them.
Safety is a paramount concern, particularly when robots interact with high-voltage environments. Operators need to ensure that both robots and personnel are shielded from potential hazards. Comprehensive risk assessments must be conducted before deploying robots in sensitive areas.
Stakeholder engagement, especially with regulatory bodies, will help shape the legislation. Open dialogues are essential to addressing concerns regarding public safety and privacy. Developing protocols for responsible data collection and ensuring compliance with data protection laws is fundamental to mitigate risks associated with robotic inspections.
In summary, while transmission line inspection robots promise enhanced efficiency and safety in utility maintenance, it is crucial to address the technical challenges and regulatory concerns that accompany their integration into existing infrastructures.
Case Studies of Successful Implementations
Case studies on transmission line inspection robots serve a critical purpose in understanding the practical implications of these technologies in real-world scenarios. They showcase how innovative designs and advanced technologies contribute to the improvement of utility maintenance. Furthermore, they emphasize the various successes achieved through robotic integration and illustrate the tangible benefits provided both to utility companies and to the environment.
One of the primary benefits of these case studies is that they provide tangible examples of efficiency, reliability, and cost-effectiveness. By analyzing different implementations, stakeholders can grasp the nuances of various robot designs and the specific challenges they overcame. This knowledge can drive further research, development, and investment in the field, enhancing future innovations.
Notable Industry Leaders
Several organizations have led the way in adopting transmission line inspection robots, proving their value through successful implementations.
- Pacific Gas and Electric (PG&E): Known for its expansive overhead power line network, PG&E has integrated drone technology for timely inspection of transmission lines. Their use of aerial drones has significantly reduced downtime during inspections, enabling prompt data collection and analysis.
- Florida Power & Light (FPL): FPL has embraced robotic systems to monitor wear and corrosion on high-voltage infrastructure. Their deployment of ground-based robots has increased inspection frequency while minimizing manual labor, reinforcing safety protocols.
- TenneT: This European transmission system operator has implemented hybrid inspection systems that combine drones and ground robots. Such systems allow for versatile inspections, adapting to various terrains and weather conditions effectively.
Innovative Robot Designs
The evolution of transmission line inspection robots has led to innovative designs tailored to meet specific operational needs. These designs range from agile, lightweight drones to heavy-duty ground robots. Each offers unique advantages in terms of functionality and design philosophy.
- Aerial Drones: Equipped with high-resolution cameras and thermal imaging sensors, these drones allow for real-time monitoring of transmission lines. They are capable of navigating complex environments with speed, providing actionable insights quickly and efficiently.
- Ground-Based Robots: These are designed for more rugged terrains and can handle the physical challenges presented by natural obstacles. Their robustness enables them to perform visual inspections and data collection from close range, ensuring no detail is overlooked, even in difficult situations.
- Hybrid Models: The use of hybrid inspection systems represents a convergence of technologies. These designs leverage the strengths of both aerial and ground inspection methods, allowing for comprehensive coverage and efficient resource use.
Ultimately, the transition to robotic inspection in utility maintenance not only promotes operational efficiency but also enhances safety and effectiveness. The case studies highlight how various leaders in the industry have adopted these technologies and the innovative designs that support inspection processes.
Future Trends in Inspection Robotics
The future of inspection robotics, especially within the framework of transmission lines, is a subject that carries considerable importance in this article. It encompasses various technological evolutions that promise to alter the efficiency and safety of utility maintenance. The integration of robotics in this space not only advances traditional methods of inspection but also addresses critical issues including quick response times, predictive maintenance, and improved safety protocols for personnel. As we navigate forward, certain trends emerge as pivotal for both current and future implementations.
Advancements in AI and Machine Learning
Advancements in artificial intelligence (AI) and machine learning stand at the forefront of transforming inspection robotics. These technologies enable robots to process vast amounts of data in real-time, allowing for enhanced decision-making capabilities. AI algorithms can be employed to recognize patterns in the data collected from inspections. This could, for example, help identify potential weaknesses in electrical lines before they lead to outages. Furthermore, predictive analytics powered by machine learning can facilitate proactive maintenance actions. The benefits here are manifold:
- Increased Reliability: AI can minimize false positives in inspections, ensuring that maintenance is only performed when necessary.
- Enhanced Operational Efficiency: Automated analysis cuts down on time spent by human operators reviewing data.
- Adaptability: Machine learning models evolve and improve over time, allowing robots to adjust to different conditions and requirements in the field.
With the rapid advancements in AI, we are likely to see a more intelligent and autonomous approach to inspecting transmission lines that will significantly reduce human error and increase accuracy.
Integration with Smart Grids
The integration of inspection robots with smart grids represents a critical trend in the evolution of utility infrastructure. Smart grids use digital communication technology to detect and react to local changes in usage. By incorporating inspection robots into this framework, the functionality of these grids is greatly enhanced. Here are key elements regarding this integration:
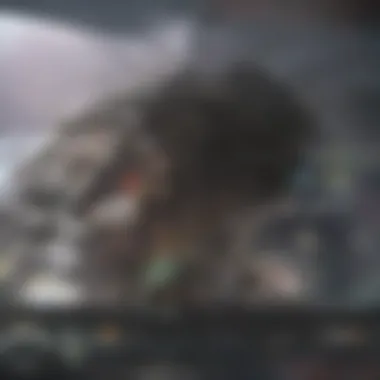
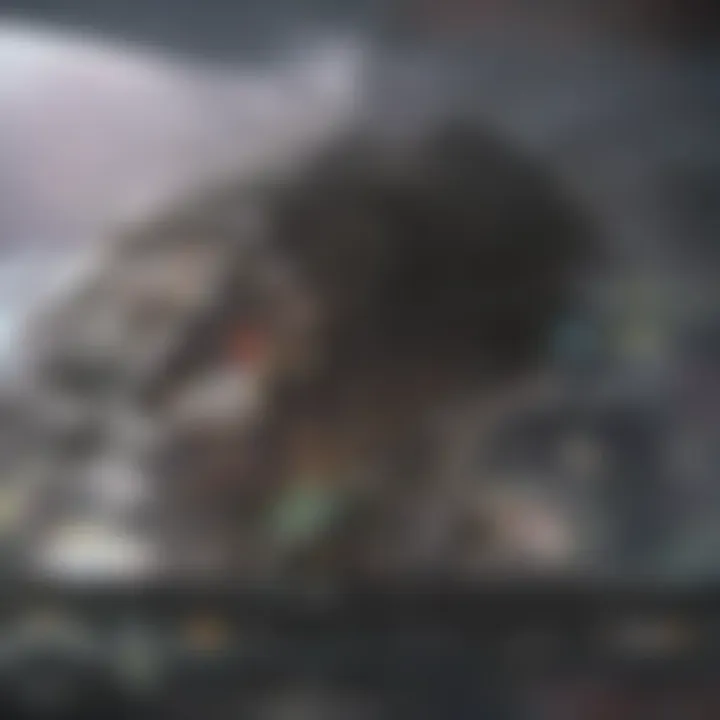
- Real-Time Monitoring: Robots can feed real-time data to the grid, facilitating immediate awareness of any irregularities that may affect service delivery.
- Automated Maintenance Scheduling: With insights gathered from robotics inspections, smart grids can dictate when and where maintenance is required, optimizing downtime and resource allocation.
- Improved Risk Management: Integrating robots allows for timely identification of potential failures, which supports better risk evaluation and mitigation strategies.
"The symbiosis between advanced robotics and smart grid technology is establishing new benchmarks for operational excellence in utility industries."
Environmental Impact of Inspection Robots
The deployment of transmission line inspection robots embodies a significant progression in utility maintenance with profound environmental implications. This topic elucidates how these robotic systems contribute to sustainability while offering a more effective means of managing infrastructure. Important elements include minimizing human presence in sensitive areas, improving energy efficiency, and reducing the carbon footprint associated with traditional inspection methods.
Minimizing Human Footprint
Inspection robots are designed to operate in environments where human access can be restricted or hazardous. This capability translates to reduced human intervention in delicate ecosystems. For instance, when inspection is required in remote terrains or areas with heavy vegetation, traditional methods often necessitate extensive human presence, leading to potential disruption of the local flora and fauna.
Robotic systems can traverse these areas quietly, without the need for vehicles or large inspection crews. This minimizes disturbance to wildlife and reduces the need for land clearing. The result is a gentler approach to infrastructure maintenance that respects the surrounding environment.
Energy Efficiency Considerations
The energy consumption of transmission line inspection robots is an essential factor in their environmental impact. Many modern inspection robots are powered by efficient batteries and optimized for low energy usage. They utilize advanced navigation and imaging technologies that allow them to assess line conditions effectively without excessive energy expenditure.
Moreover, these robots can often complete inspections faster than human crews, resulting in a lower overall energy expenditure per project. The integration of solar power into some models further enhances this benefit, ensuring a ready energy supply that decreases reliance on fossil fuels.
In summary, the deployment of transmission line inspection robots not only facilitates efficient utility maintenance but also provides a pathway towards more sustainable practices in the energy sector. They promote environmental stewardship through reduced human intrusion and improved energy use, solidifying their role as crucial instruments in modern utility management.
Ethical Considerations in Robotic Use
The integration of transmission line inspection robots in utility maintenance has brought forward pivotal ethical dilemmas that must be addressed. The use of robots offers significant advantages but also raises questions about data privacy, job displacement, and operational responsibility. Understanding these ethical considerations is crucial not only for fostering public trust but also for guiding future developments in the field.
Responsible Data Collection
With the deployment of inspection robots comes the vast potential for data collection. These machines often rely on advanced sensors and imaging technologies to gather information about the condition of power infrastructure. It is essential to outline clear protocols regarding data management and storage. Collecting enormous amounts of data raises privacy concerns, especially regarding how data is used and who has access to it.
Inspection robots should implement stringent measures to protect sensitive information. For instance, encryption techniques can safeguard data against unauthorized access. Furthermore, transparency in data collection practices is critical. Stakeholders need to know what data the robots are gathering, how it will be utilized, and the duration for which it will be stored.
"Ethical frameworks should be set in place to ensure responsible handling of data collected by robotic systems in utility contexts."
Impact on Workforce Dynamics
The adoption of robotic technologies can have profound implications for workforce dynamics within the utility sector. The introduction of these robots often leads to concerns about job security for workers whose tasks may be automated. However, it is important to understand that while some positions may become obsolete, other roles could evolve or emerge as a result of this technological advancement.
A careful balance must be struck between technological efficiency and the human element of utility maintenance. Companies should prioritize reskilling and upskilling their workforce to adapt to new roles centered around managing and operating robotic systems. Encouraging a collaborative approach between humans and robots can enhance productivity and innovation.
In addition, discussions involving labor representatives, policymakers, and industry leaders are vital to developing best practices that support a smooth transition. By addressing these workforce concerns early on, companies can alleviate fears and foster a culture that embraces technological advancement as a partner rather than a replacement.
Stakeholder Perspectives
The influence of transmission line inspection robots extends not just to the immediate operational benefits, but also to various stakeholders involved in the utility maintenance ecosystem. Each group, from utility companies to regulatory bodies, and finally to the general public, has their own unique perspectives and concerns regarding the deployment and implications of these robotic systems.
Utility Companies
Utility companies, as primary users of inspection robots, benefit significantly from their implementation. These companies face the constant challenge of maintaining extensive networks of transmission lines while ensuring reliability and safety. The integration of robotic technologies provides several advantages:
- Enhanced Efficiency: Robots can cover vast areas in less time than human teams, leading to quicker inspections. This allows utility companies to respond faster to potential issues.
- Cost Reduction: By reducing the need for manual inspections, companies can lower labor costs and decrease the overall expenditure associated with maintenance.
- Safety Improvement: Inspecting transmission lines often comes with inherent risks. Robots minimize human exposure to hazardous environments, allowing for safer operations.
Overall, utility companies must weigh the initial investment against long-term savings, considering both the financial and operational aspects of adopting these technologies.
Regulatory Bodies
Regulatory bodies play a pivotal role in oversight and compliance when it comes to introducing new technology in utility maintenance. They must ensure that the deployment of inspection robots meets safety standards while also promoting innovation. Considerations include:
- Safety Regulations: Ensuring that robotic systems adhere to established safety protocols is critical. This involves constant reassessment of both the technology and the environments in which it operates.
- Data Security: As inspection robots collect various data, there is a need to address privacy and security concerns for that information. Regulatory frameworks need to be updated to ensure protection against potential breaches.
- Standards Development: There is a need for developing industry standards for robotic performance and data reporting. This helps ensure reliability and consistency across different utility companies.
Thus, regulatory bodies must find a balance between encouraging technological advancements and safeguarding public interests.
Public Sentiment
Public perception of transmission line inspection robots significantly influences their acceptance and future development. Community concerns primarily revolve around:
- Environmental Impact: Members of the public are increasingly aware of the ecological footprint associated with utility maintenance. They are interested in how robots can minimize disturbances to the environment compared to traditional methods.
- Job Security: While robots improve efficiency, there is concern regarding the impact on employment for maintenance workers. Communicating the potential for upskilling and job creation in new areas is essential to allay these fears.
- Transparency and Trust: Public trust can be bolstered through transparent communication about how inspection robots function and their benefits. Engaging the community can lead to positive sentiment about these advancements.
In summary, stakeholder perspectives shape the narrative around transmission line inspection robots. These views highlight the multifaceted implications of integrating robotic technologies in utility maintenance, and they stress the need for careful consideration as this field continues to evolve.
Finale and Future Research Directions
The conclusion serves as a crucial part of the exploration into transmission line inspection robots. This section synthesizes the key findings from the article while setting the stage for future research and advances in the field. It is essential to emphasize how these robots are not merely tools but pivotal innovations that have reshaped utility maintenance, ensuring both operational efficiency and safety.
As the demand for reliable electrical infrastructure increases, the evolution of inspection technologies must also advance. The current landscape of robotic systems demonstrates how these machines improve not only in function but also in intelligence. They analyze vast amounts of data, enabling utility companies to make informed decisions and minimize accidents. Future research can focus on refining these systems further, integrating advancements in artificial intelligence and machine learning to enhance predictive maintenance capabilities.
Moreover, ethical considerations regarding the use of these technologies cannot be overlooked. Continuous oversight into how data is handled and the implications for the workforce must guide future innovations in this space. The balance between automation and human resource management will be a focal point for organizations aiming to integrate inspection robotics effectively while maintaining a skilled workforce.
Summary of Key Points
- Transformative Role: Transmission line inspection robots represent a significant leap in the maintenance of utility infrastructure. They provide precision and real-time analysis that traditional methods cannot achieve.
- Technological Innovations: Key technologies include advanced sensors, autonomous navigation systems, and sophisticated data processing software. These elements contribute to the robots' ability to navigate complex environments and perform detailed inspections efficiently.
- Operational Efficiency: By utilizing these robots, utility companies can reduce downtime, lower maintenance costs, and improve safety for their workers, demonstrating a clear return on investment.
- Future Prospects: The ongoing integration of AI and machine learning promises to further enhance the capabilities of inspection robots, allowing for smarter decision-making in maintenance operations.
Areas for Further Exploration
Looking ahead, several crucial areas warrant further investigation:
- AI Integration: Research should delve deeper into how artificial intelligence can improve the predictive capabilities of inspection robots, potentially reducing the frequency of outages.
- Regulatory Frameworks: The development of comprehensive regulations governing the deployment of these robots is vital. Identifying safety standards and operational guidelines will help streamline their use in various sectors.
- Public Perception: Understanding public sentiment regarding the use of robotic technologies in essential services could inform better communication strategies from utility companies.
- Environmental Impacts: Investigating the environmental footprint of these robots will provide insights into their sustainability and long-term viability.