Thermoforming Process: In-Depth Analysis of Techniques
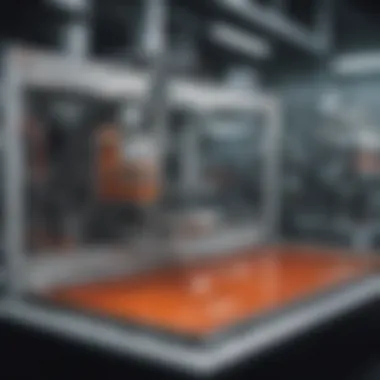
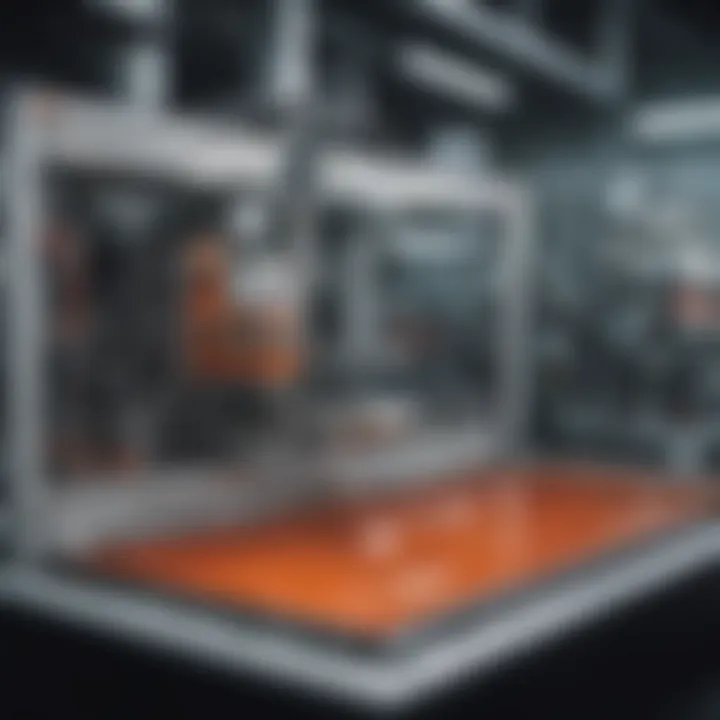
Intro
The realm of plastic manufacturing has witnessed notable progress over the years, yet few processes stand out like thermoforming. While it may not grab headlines daily, this method is crucial in producing countless items we use in everyday life. By utilizing heat and pressure, manufacturers can shape plastic sheets into numerous functional forms, catering to a broad range of industries. From packaging to automotive parts, the applications are as varied as they are fascinating.
Understanding how this process works and the materials involved is not just an academic inquiry; it has real-world implications for efficiency, sustainability, and innovation. With advancements in technology shaking up traditional methods, the landscape of thermoforming is evolving. Moreover, discussions around eco-friendly practices and materials further underscore its modern significance in addressing global challenges.
As we navigate through this comprehensive examination, we'll dissect the nuances of thermoforming, shedding light on both its historical context and cutting-edge developments. This knowledge isn't just for the specialists in the field, but is also valuable for students and educators keen on grasping how theory meets application in the manufacturing domain.
With this introduction, let’s delve deeper into the key findings.
Prelims to Thermoforming
Thermoforming stands at the crossroads of innovation and practicality, serving as a key technique for shaping plastic materials into diverse forms. This process isn’t just a manufacturing method; it’s a vital link in the chain of industrial production that influences everything from packaging to automotive components. By understanding thermoforming, stakeholders can appreciate its significance in modern manufacturing, including its efficiency, versatility, and adaptability. This section aims to dissect what thermoforming is all about and set the stage for a deeper exploration of its mechanics and applications.
Understanding Thermoforming
At its core, thermoforming involves heating plastic sheets until they become pliable enough to be shaped into specific designs through various mechanical methods. These sheets, typically made from thermoplastics, can be easily molded, cut, and formed into precise configurations needed for an array of applications.
The beauty of thermoforming lies in its ability to produce items with intricate designs and vast dimensions—all while maintaining a cost-effective approach. Whether creating simple containers or complex parts, manufacturers harness this technology to cater to consumer demands. Traditional methods, such as injection molding, often demand more upfront investment and longer lead times. In contrast, thermoforming offers a quicker turnaround, which can significantly benefit industries that need rapid prototyping and short-run production.
Historical Context
The roots of thermoforming trace back to the mid-20th century, when the plastic industry began expanding rapidly following World War II. In those days, materials like polystyrene and polyethylene revolutionized packaging and product production. Initially, the thermoforming techniques were rudimentary, primarily dealing with basic shapes and low production volumes, but as demand grew, so did the technology.
Advancements in heating techniques and material science played a pivotal role in smoothing the evolution of thermoforming. By the 1980s and 1990s, manufacturers employed more sophisticated methods, such as vacuum and pressure forming, which enhanced the precision and quality of the finished products. Moreover, as industries shifted towards sustainability, the development of biodegradable thermoplastics opened a new chapter in thermoforming's narrative, merging environmental responsibility with industrial application.
In summary, the history of thermoforming echoes the broader growth of the plastic industry, influenced by technological advances and market needs. Recognizing this context enriches our understanding of the current state of thermoforming and its future potential.
Mechanics of the Thermoforming Process
Understanding the mechanics of the thermoforming process is crucial for grasping how raw plastic or other materials transform into functional items. This section digs into the heart of thermoforming, unraveling both its heating techniques and molding methods. By fully comprehending these mechanics, one can appreciate not just the practicality, but the efficiency and adaptability of this process in various applications.
Heating Techniques
Heating is a pivotal step in the thermoforming process, where materials are softened enough to take shape. This can be accomplished through different methods, each presenting unique characteristics and advantages. Below are the three predominant heating techniques used in the thermoforming industry:
Convection Heating
Convection heating utilizes hot air to warm the thermoplastic sheets, making it a widely used method in the industry. The hot air circulates around the material, gradually increasing its temperature. A notable benefit of convection heating is that it provides even heat distribution, minimizing the risk of overheating or warping the material.
- Unique feature: The ability to heat multiple sheets simultaneously due to the nature of air circulation.
- Advantages: It is energy-efficient and offers a controllable heating environment.
- Disadvantages: This method might be slower compared to others, making it less suitable for high-speed production.
Radiant Heating
Radiant heating works by using infrared radiation to directly heat the surface of the plastic sheets. This method is quite efficient, as it warms the material without having to waste energy heating the surrounding air. Many manufacturers lean towards radiant heating because it can achieve quicker heating times and precise temperature control.
- Key characteristic: Direct heating that provides immediate effect on the surfaces.
- Advantages: Fast processing time and focused energy application.
- Disadvantages: There might be uneven heating if the material thickness varies, leading to challenges in consistent quality control.
Contact Heating
Contact heating, as the name suggests, involves direct contact between the heating elements and the plastic sheets. This method allows for rapid temperature increase and is particularly effective for thicker materials.
- Key characteristic: The immediate heat transfer due to direct contact.
- Advantages: It generally requires less time to heat the material thoroughly.
- Disadvantages: The risk of localized overheating is higher, which can compromise material integrity if not monitored carefully.
Molding Methods
Once the materials are adequately heated and malleable, they are shaped using various molding methods. Each method offers its own benefits, tailored to specific production requirements.
Vacuum Forming
Vacuum forming is a popular choice for creating detailed shapes with relatively lower costs. In this method, the softened material is draped over a mold, and a vacuum is applied to suck the material down onto the mold surface. This technique is particularly effective for shallow or moderately deep molds, providing excellent detail and surface fidelity.
- Key characteristic: Utilizes atmospheric pressure to draw the material into the mold.
- Advantages: Cost-effective tooling and quick setup times.
- Disadvantages: Limited to simpler shapes; complex geometries might require additional techniques.
Pressure Forming
Pressure forming pushes the material against the mold using air pressure, which allows for the creation of intricate designs. This method usually results in better detail and surface quality compared to vacuum forming, making it highly suitable for aesthetic components.
- Key characteristic: Use of positive pressure rather than vacuum.
- Advantages: Capable of forming complex shapes with tighter tolerances.
- Disadvantages: Higher tooling costs and longer cycle times compared to vacuum forming.
Mechanical Forming
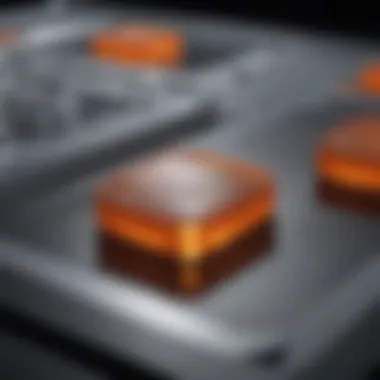
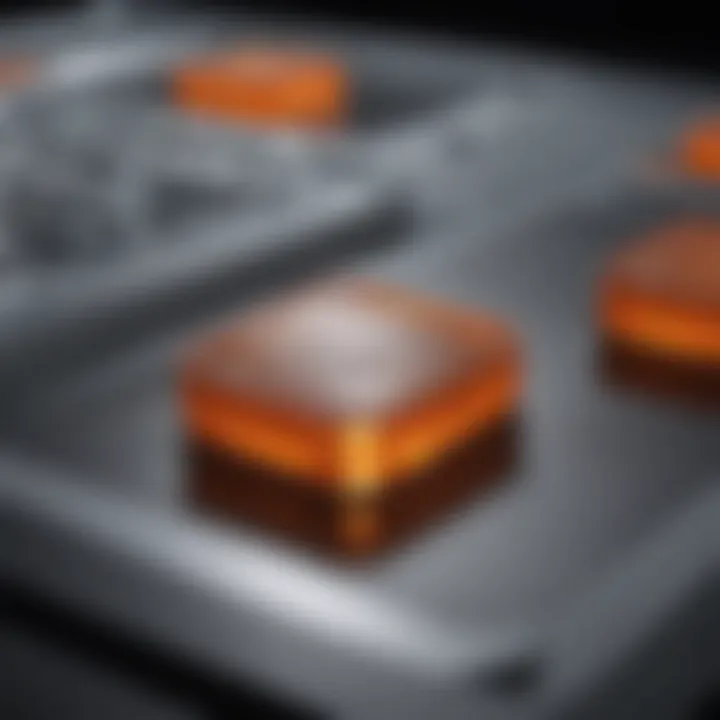
Mechanical forming involves physically manipulating the material into shape using mechanical devices or tools. This method is typically used for producing thicker materials or components that require strength and durability.
- Key characteristic: Uses physical force rather than pressure or vacuum.
- Advantages: Suitable for heavy-duty applications and strong parts.
- Disadvantages: More complex machinery and longer setup times may be necessary.
The mechanics of the thermoforming process provide a foundational understanding that is vital for success in plastic manufacturing. By choosing the appropriate heating and molding methods, professionals can optimize production efficiency while addressing specific product needs.
Materials Utilized in Thermoforming
Understanding the materials that go into the thermoforming process is critical, as they define not just the application but also the performance and efficiency of the products created. A wide array of materials can be utilized in this process, each offering unique properties that can influence shape, durability, and cost. This section discusses the importance of elastomers, thermoplastics, and advanced composite materials in thermoforming, spotlighting their characteristics, benefits, and practical implications.
Elastomers
Elastomers play a pivotal role in thermoforming applications, mainly due to their flexibility and resilience. These materials, often rubber-like, can stretch and compress, making them ideal for applications that require some give.
Some notable benefits of elastomers include:
- High elasticity: They can return to their original shape after being deformed.
- Resilience: Resistant to weather, chemicals, and UV light.
These advantages make elastomers useful in various products, such as seals and gaskets, where durability is essential.
Thermoplastics
When it comes to thermoforming, thermoplastics are the workhorses. They can be heated to form shapes and then cooled to solidify. Their versatility makes them particularly noteworthy, and three common varieties stand out: Polyethylene, Polystyrene, and Polyvinyl Chloride.
Polyethylene
Polyethylene is one of the most widely used thermoplastics in thermoforming. It is lightweight and resistant to chemicals, which makes it a popular choice for packaging and containers. One of the key characteristics of polyethylene is its exceptional tensile strength. This property allows it to withstand substantial stress without deformation.
The unique feature of polyethylene is its ability to be recycled without losing quality, which adds a significant advantage in today’s eco-conscious market. However, it may not perform well under intense heat, limiting its use in high-temperature applications.
Polystyrene
Polystyrene is another major player in the thermoforming landscape, known for its clarity and rigidity. It is particularly advantageous in creating detailed shapes with high visual appeal, often employed in products like food containers and display materials.
Its low cost makes it a beneficial choice for mass production, while its lightweight nature adds to its appeal. However, polystyrene can be brittle and may not handle impacts well compared to other materials, which is a limitation in certain applications.
Polyvinyl Chloride (PVC)
PVC is a versatile material praised for its contrast between rigidity and flexibility. It is popular in the production of both hard and soft packaging options. The key characteristic of PVC is its durability and resistance to moisture, making it suitable for outdoor applications and plumbing components.
One unique feature of PVC is its adaptability; it can be made flexible by adding plasticizers. This flexibility allows for a broader scope of applications, although it can have a higher cost than some alternatives. On the downside, concerns about its environmental impact have led to scrutiny regarding its recyclability.
Advanced Composite Materials
Advanced composite materials represent the cutting edge of thermoforming, combining two or more materials to create a final product with superior qualities. These composites often exhibit enhanced strength, lighter weight, and increased resistance to environmental factors compared to conventional materials.
By employing advanced composites, manufacturers can develop products that not only meet specific requirements but also open avenues for innovation across industries such as aerospace, automotive, and sports equipment. The integration of these materials showcases the impressive evolution of the thermoforming process, reflecting both technological advancements and the industry's adaptability to the ever-changing market demands.
Applications of Thermoforming
The thermoforming process plays a crucial role across various sectors, ranging from packaging to automotive and medical fields. Its significance cannot be overstated, as it not only meets product demands but also enhances manufacturing efficiency and design versatility. This section will explore how thermoforming transforms industries, focusing on three specific applications: packaging solutions, automotive components, and medical devices.
Packaging Solutions
Thermoforming is extensively used in the packaging sector. Its ability to create custom shapes tailored to the products ensures they are well-protected during transportation and storage. For instance, companies often use clear plastic blisters made through thermoforming to showcase consumer goods. This method offers several advantages:
- Cost efficiency: Producing lightweight packages reduces shipping costs while minimizing material waste.
- Durability: These packages can withstand impacts, ensuring product integrity.
- Aesthetic appeal: A well-formed package attracts customers, enhancing brand visibility.
Moreover, recyclable thermoformed materials help address environmental concerns, making it an attractive option for companies striving to implement sustainable practices. The ease of production and customization means that packaging can adapt quickly to changing consumer preferences without heavy investments.
Automotive Components
In the automotive industry, thermoforming has revolutionized how components are made, contributing to both performance and safety. Parts like dashboards, paneling, and interior fittings are often produced using this technique. Key benefits include:
- Weight reduction: Using thermoformed plastics, manufacturers can create lighter components that improve fuel efficiency.
- Design flexibility: The ability to form complex shapes allows for ergonomic designs that enhance driver and passenger comfort.
- Cost savings: Assembling multiple parts into a single thermoformed piece can streamline production, leading to lower labor costs and reduced assembly time.
Automakers increasingly rely on advanced thermoplastics that boast high strength and durability, making them ideal for critical applications. This trend shows no sign of slowing, as manufacturers continue to innovate and seek ways to enhance vehicle performance through efficient manufacturing techniques.
Medical Devices
Thermoforming has also carved a niche in the healthcare sector, where precision and reliability are non-negotiable. Products like trays for surgical instruments, custom packaging for medical devices, and breathing masks often use thermoformed materials. Consider the following aspects:
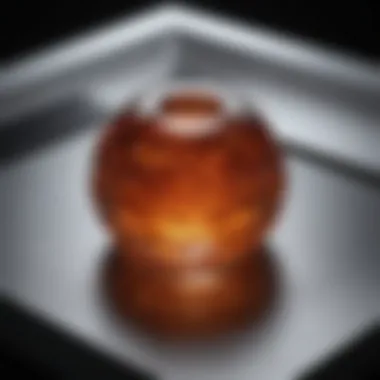
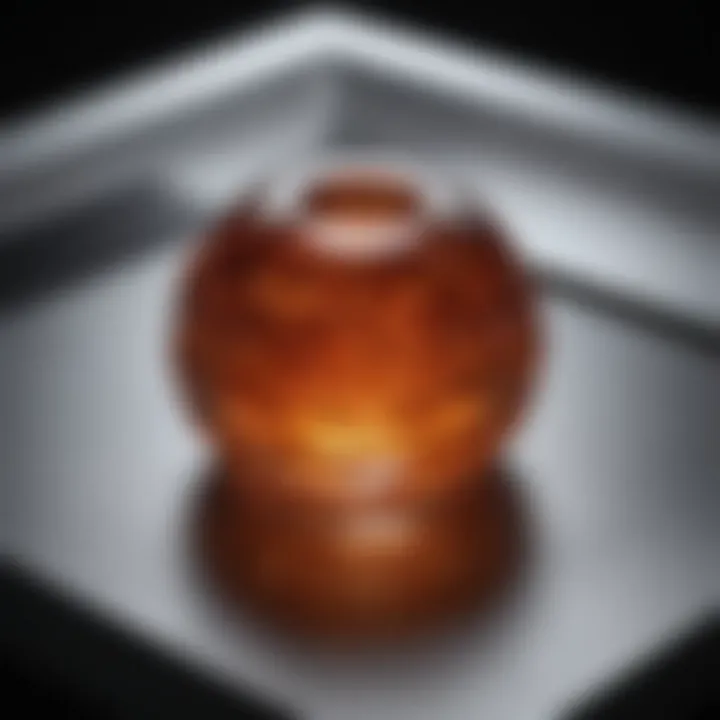
- Sterilization compatibility: Many thermoformed products can withstand sterilization processes without degrading, ensuring they remain safe for medical use.
- Customization: The ability to tailor shapes to fit specific medical devices aids in functionality and storage efficiency.
- Regulatory compliance: Industries facing strict regulations find that thermoforming provides a pathway to create compliant products efficiently.
Because the healthcare field constantly adapts to new challenges, thermoforming provides a flexible manufacturing approach helping to design and produce necessary medical equipment more swiftly and economically.
"The versatility of thermoforming allows industries to innovate and adapt quickly to changing demands, making it an indispensable manufacturing process."
As we can see, the applications of thermoforming are diverse and impactful. Each sector leverages the process to solve unique challenges, highlighting its importance in today's manufacturing landscape.
Advantages of Thermoforming
Thermoforming, while often seen as just one method among many in the plastic fabrication process, brings a host of distinct advantages that make it a preferred choice across various industries. Understanding these benefits can illuminate why thermoforming is such a vital topic in the discussions of plastic manufacturing today. The advantages fall primarily into two major categories: cost-effectiveness and design flexibility.
Cost-Effectiveness
One of the main strengths of thermoforming lies in its cost-effectiveness. The process typically requires less machinery and energy compared to injection molding, making it a financially attractive option, particularly for smaller production runs or custom applications. Here are some specific aspects to consider:
- Reduced Initial Investment: Setting up a thermoforming operation often requires a lower capital outlay than other techniques. This makes it appealing for startups and businesses that are experimenting with new product designs without a hefty financial commitment.
- Material Efficiency: The material waste during thermoforming is often significantly lower than other methods, primarily because it uses sheet materials that can be trimmed in ways that minimize off-cuts. Manufacturers can recycle those off-cuts or use them in other processes, further enhancing cost efficiency.
- Lower Labor Costs: The automation of thermoforming can greatly minimize the labor necessary for production. While some setups are manual, many modern systems are designed to optimize workflow, which reduces the need for extensive human oversight and can speed up production cycles.
Thus, companies can achieve more competitive pricing in the market while maintaining the quality of their products.
Design Flexibility
Another noteworthy advantage of thermoforming is its remarkable design flexibility. This property allows designers and engineers unprecedented freedom to innovate. This flexibility is evident in several areas:
- Wide Range of Shapes and Sizes: Thermoforming offers the ability to create complex shapes that might be difficult or impossible to achieve with other methods. The only limit is often the creativity of the designer.
- Variety of Materials: A diverse array of thermoplastics can be used in thermoforming, ranging from traditional options like polystyrene to more advanced composite materials. This allows for the tailoring of material properties for specific applications.
- Custom Solutions: Because the process can quickly adapt to new designs, companies can experiment with products without exorbitant time or material costs. This is particularly significant in industries like packaging and automotive, where customer preferences can change rapidly.
"Thermoforming is not just a process; it’s an avenue for creativity and innovation in design, providing tools to bring the imaginative to life."
In summary, the advantages of thermoforming, highlighted by its cost-effectiveness and design flexibility, make it a strategic choice in a competitive landscape. Businesses looking to optimize their production and product design would do well to consider the potential that thermoforming holds for their ventures. The exploration of this process reveals not just the mechanics behind it, but the substantial benefits that can be harnessed to meet varying market demands.
Challenges in Thermoforming
In the realm of plastic fabrication, the thermoforming process stands out for its versatility and efficiency. However, like any technique, it is accompanied by its share of challenges. Addressing these challenges is essential for optimizing production and ensuring high-quality outputs. This section will delve into two primary challenges: material limitations and production speed.
Material Limitations
The selection of materials in thermoforming is often a double-edged sword. While there is a wide variety of thermoplastic materials available, not all are suitable for thermoforming applications. Understanding the limitations associated with different materials is crucial for designers and engineers.
Some materials might not withstand the necessary heating temperatures without degrading, while others may exhibit poor flexibility or formability. For example, films made from polycarbonate could become brittle when subjected to the heating and forming process, limiting their usability in certain applications. Moreover, thickness variations can lead to incomplete forms or uneven cooling, causing weak points in the final product.
Furthermore, recycling can complicate material selection. Not all thermoplastics can be recycled effectively, which poses a dilemma for manufacturers seeking to implement sustainable practices. Choosing the right material not only affects production efficiency but also influences the product's overall performance and marketability.
Production Speed
At the heart of many production facilities lies the quest for speed without sacrificing quality. In thermoforming, production speed can be a significant bottleneck, stemming from various factors. One prominent issue is the heating phase. Depending on the material's thermal properties, the time it takes to reach the optimal temperature can vary widely.
A slower heating process prolongs the overall cycle time, delaying output and affecting profitability. Additionally, mold design intricacies can lead to extended cooling times. In cases where thick materials are utilized, the cooling time may need to be increased to ensure the final part retains its shape and structural integrity.
Moreover, multiple setups for different molds and configurations can contribute to inefficient production. Each changeover requires time and labor, detracting from overall productivity.
To mitigate these challenges, the industry is exploring various solutions, such as:
- Upgrading heating technology to more efficient methods like rapid infrared heating.
- Implementing automation for mold changes to minimize downtime.
- Investing in research to develop advanced materials with better thermoforming qualities.
"The key to overcoming the challenges in thermoforming lies in a thorough understanding of the materials and processes involved, ensuring that production teams are equipped to adapt and innovate."
Environmental Considerations
As industries worldwide grapple with the pressing need for environmental sustainability, the thermoforming process has emerged as a critical area of focus. This part of the article emphasizes the environmental considerations surrounding thermoforming, examining the ways in which this plastic fabrication technique can align with sustainable practices and contribute to the solution of ecological challenges. The choices made during the design, production, and disposal phases impact not only the economy but also the environment at large. Therefore, understanding these implications becomes essential for professionals in this field.
Sustainability Practices
When discussing sustainability in thermoforming, there are several practices worth highlighting:
- Material Selection: Choosing materials that have a lower environmental impact is paramount. Biodegradable thermoplastics and recycled plastics are increasingly popular choices. Employing these materials can minimize waste and lessen the carbon footprint of the production process.
- Energy Efficiency: Implementing energy-efficient equipment can significantly reduce the energy demands of the thermoforming process. Technologies designed for reduced energy consumption not only lower operational costs but also decrease greenhouse gas emissions.
- Water Usage: Although water consumption may be less obvious than energy use, it plays a role in thermoforming. Monitoring water usage and opting for closed-loop systems helps in conserving this vital resource, thus reinforcing an eco-friendly approach.
These practices underscore a proactive approach to minimizing environmental impact, indicating that thermoforming can evolve into a more sustainable process with specific strategies in place. Companies that embrace these sustainability practices often find themselves ahead of the curve, not just in terms of ecological responsibility but also in market competitiveness.
Recycling Potential
The recycling potential of thermoformed products is another critical aspect of environmental considerations. When evaluating the lifecycle of thermoformed materials, it's important to note:

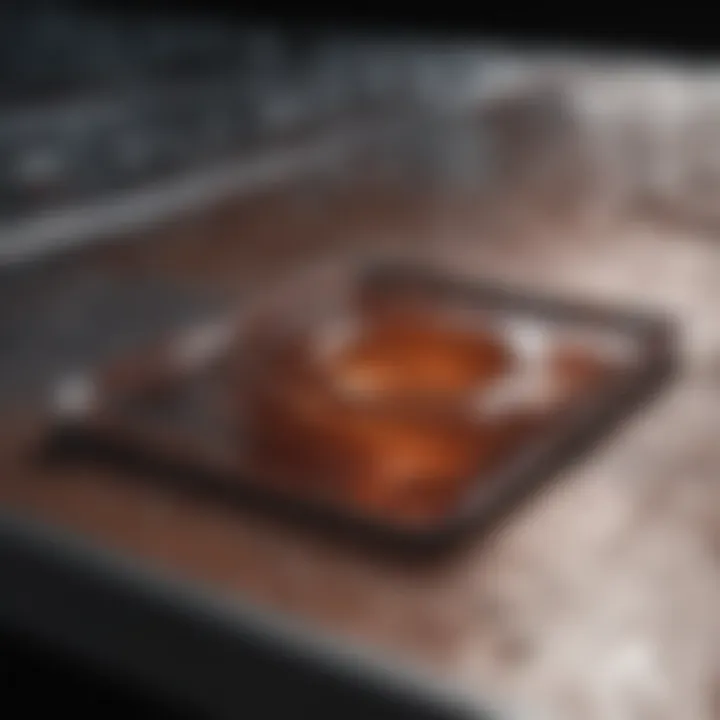
- Material Recovery: Many thermoplastics used in thermoforming, such as polyethylene and polystyrene, are recyclable. Establishing effective systems for collecting and processing these materials post-consumer use can greatly enhance circular economy initiatives.
- Design for Recycling: Designing products with their end of life in mind is increasingly becoming a best practice. This involves creating items that are easily disassembled or made from a single type of compatible material to facilitate recycling.
- Consumer Awareness: Encouraging consumers to participate in recycling programs can significantly impact the effective recovery of thermoformed products. Educational campaigns about how and where to recycle can enhance participation rates.
"Sustainability is not a niche but a necessity for the future of industry."
By acknowledging these environmental aspects, professionals in the thermoforming sector can help forge a path toward a greener and more responsible industry.
Technological Advancements in Thermoforming
In the landscape of manufacturing, technological advancements have sparked a revolution, particularly in the thermoforming sector. These innovations not only enhance efficiency but also bring forth improvements in product quality, precise design capabilities, and sustainable practices. As the industry moves forward, it's crucial to explore how these changes fundamentally reshape conventional methods. The primary focus lies in automation and the integration of cutting-edge software solutions like 3D modeling tools, which are pivotal in modernizing the thermoforming process.
Automation and Industry 4.
The term Industry 4.0 is becoming a buzzword, representing the fourth industrial revolution. This shift encompasses a smarter production line, where automation plays a crucial role. In thermoforming, automation streamlines operations, reducing human error and bolstering production rates. For instance, automatic machines can precisely control heating, molding, and cooling processes, achieving repeatable results that were previously unattainable through manual methods.
Here are several key benefits of automation in thermoforming:
- Increased Efficiency: Automated systems can operate continuously, ensuring that production runs faster and more consistently than human-operated machines.
- Reduced Costs: While the initial investment in automated systems may raise eyebrows, the long-term savings on labor costs and waste can pay off significantly.
- Enhanced Quality Control: Automation improves precision, leading to fewer defects and more uniform products, which is vital for applications like medical devices or automotive parts where integrity is critical.
Moreover, automation allows for real-time data collection, enabling manufacturers to monitor performance metrics and swiftly address any issues that arise. This capability fosters an environment of continual improvement, highlighting the growing importance of data-driven decision-making in manufacturing.
3D Modeling Software
Moving on to the software which backs up these advancements, 3D modeling software is revolutionizing how designers and engineers approach thermoforming projects. The incorporation of such technologies allows for advanced simulation and design verification. Instead of jumping into production with a prototype, designers can visualize how a product will behave under different conditions.
Key aspects of 3D modeling software include:
- Design Flexibility: Engineers can create complex geometries and customize designs without the need for physical prototypes, minimizing waste and costs.
- Testing and Simulation: Software can simulate various factors such as temperature, pressure, and material behavior, allowing designers to optimize parameters before actual production begins.
- Collaboration: These tools often facilitate better communication among team members, clients, and suppliers by providing a shared platform to visualize concepts, making it easier to address concerns early in the design phase.
Utilization of 3D modeling tools streamlines workflows and fosters innovation. By being able to iterate designs rapidly, manufacturers can respond to market demands with agility while ensuring that products are both efficient and durable.
"The fusion of automation and innovative software in thermoforming is not merely a trend; it's a defining characteristic of the future of manufacturing."
Future Trends in Thermoforming
The landscape of manufacturing is changing rapidly, and thermoforming is no exception. Future trends in thermoforming are crucial for understanding how this process can evolve to meet the growing demands of various industries. By recognizing the significance of these trends, stakeholders can strategically position themselves for success in a competitive market. Here, we'll discuss specific elements, benefits, and considerations influencing the future of thermoforming.
Innovative Materials
One of the standout trends is the development of innovative materials. New types of thermoplastics are entering the market, boasting enhanced properties such as increased durability and decreased weight. Biodegradable plastics are gaining traction, aligning with the global push for sustainability. Their application in thermoforming processes shows promise, allowing manufacturers to create functional designs without compromising on environmental responsibility.
Additionally, the incorporation of recycled materials into the thermoforming process not only bolsters sustainability efforts but also opens avenues for cost reduction. For instance, manufacturers are increasingly using recycled PET from plastic bottles, thereby minimizing waste and conserving natural resources. This not only taps into a rich material source but is also attractive to consumers looking for eco-friendly options.
- Customization options: New materials support complex designs and intricate shapes.
- Enhanced performance: Innovative materials often lead to better product performance, enhancing overall user experience.
- Regulatory advantages: Emerging regulations around plastics are forcing companies to innovate toward more sustainable practices.
Market Projections
Market projections indicate that the future of thermoforming is bright, buoyed by several factors. The global demand for plastic products continues to rise, spurred by their versatile applications. Analysts suggest that the thermoforming market will grow at a steady CAGR over the next several years, driven largely by the packaging, automotive, and medical device sectors.
"Industry experts predict that sustainability-driven innovations will redefine consumer preferences, which means prioritizing plastic products made from recycled or biodegradable materials."
Some key considerations influencing these market projections include:
- Technological advancements: The integration of automation and AI into production processes can enhance efficiency and reduce costs.
- Consumer awareness: As consumers grow more environmentally conscious, they push brands to adopt sustainable practices, making eco-friendly thermoformed products more appealing.
The balance of these trends will drive innovation and create new opportunities for companies looking to stay ahead in the thermoforming game. Understanding these dynamics is vital for professionals in the field, assisting them to navigate potential challenges and seize opportunities for growth.
The End
The conclusion serves as a vital aspect of understanding the thermoforming process, summing up its significance and the multifaceted elements that underpin it. By performing an analysis of the information presented throughout the article, we can gauge how the various components interlink to form a comprehensive knowledge base. The thermoforming process stands as a crossroads of innovation, technology, and environmental consciousness in the plastic manufacturing industry.
When we reflect on the key points discussed, several aspects arise as particularly noteworthy. The mechanics of thermoforming—such as heating techniques and molding methods—provide insight into how materials are shaped and formed efficiently. Not to forget the diverse range of materials used, which include elastomers and thermoplastics like polyethylene and polystyrene, each bringing unique advantages to the table.
"Understanding the entire scope of thermoforming is instrumental for students, researchers, and professionals alike, as it influences decision-making in product design and material selection."
Moreover, the benefits of thermoforming reveal its importance in various applications. Whether in packaging, automotive components, or medical devices, the versatility of the process cannot be overstated. As we navigate the challenges of production speed and material limitations, it becomes apparent that innovation is essential for the continued advancement of these methods.
Lastly, the considerations around sustainability add a contemporary layer to the conversation. As the industry moves toward green practices, recycling potential and sustainability remain focal points. Individuals armed with a thorough understanding of these trends can contribute meaningfully to both their professions and the environment.
Recap of Key Points
- Thermoforming is a transformative method in plastic fabrication that utilizes heat and pressure.
- Various heating techniques, like convection and radiant heating, play critical roles in the process.
- Molding methods including vacuum and pressure forming are essential in shaping materials.
- Common materials used are thermoplastics such as polyethylene and polystyrene, each with distinct benefits.
- This manufacturing process is prevalent in diverse sectors, notably packaging, automotive, and medical devices.
- Sustainability practices are increasingly relevant, focusing on eco-friendly material use and recycling.
Final Thoughts
The journey through the complexities of thermoforming paints a clear picture: this process is not merely about plastic shaping. It’s a dance of technology and creativity, aiming to meet changing market needs while embracing sustainability and design flexibility. As innovations continue to arise, it is crucial for those engaged in this field to embrace continuous learning. Staying abreast of technological advancements and eco-friendly practices will only enhance expertise and drive successful outcomes.
The future of thermoforming lies in its ability to adapt—whether through innovative materials or markets that evolve alongside them. Hence, understanding its core principles today will set the stage for advancements tomorrow.