Examining the Thermal Efficiency of Combined Cycle Power Plants
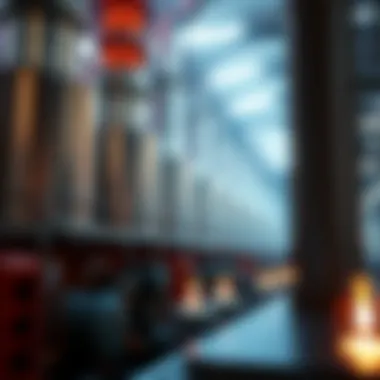
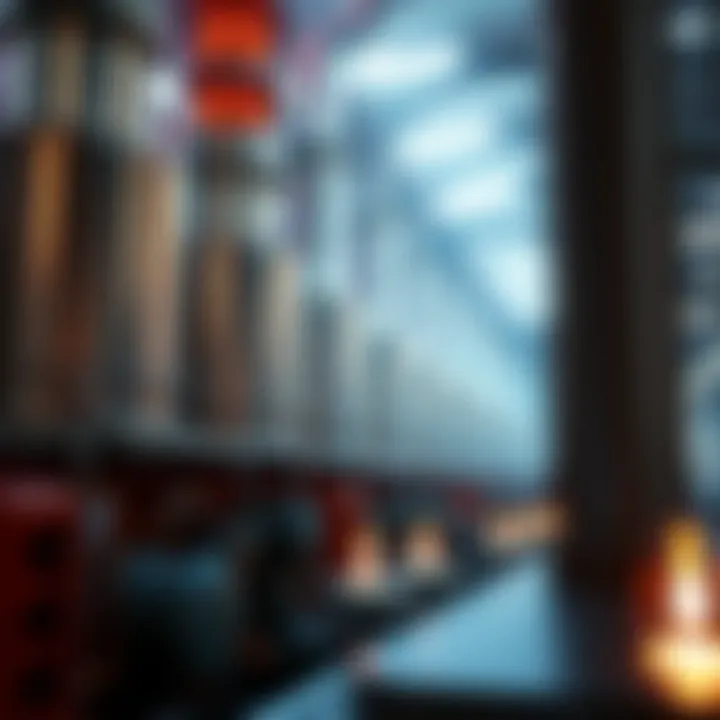
Intro
The thermal efficiency of power plants, especially those utilizing combined cycle technology, is a pivotal aspect of modern energy discourse. The world is constantly searching for ways to produce electricity that is both efficient and sustainable. Combined cycle power plants have garnered attention for their innovative ability to enhance thermal efficiency by integrating gas and steam turbines. This fusion of technologies allows for greater energy extraction from the same fuel source, ultimately resulting in less waste and reduced emissions.
In understanding thermal efficiency, it is essential to grasp how these plants operate. They employ a sequential process where gas turbines generate power, and the waste heat from this process is then used to produce steam for a steam turbine. This two-pronged approach significantly ups the ante on energy output compared to traditional single-cycle plants.
This article aims to delve into the rich framework of combined cycle power plants, exploring critical elements such as:
- Operational Mechanisms: How the integration of gas and steam turbines works in tandem.
- Key Factors Influencing Efficiency: Various elements that affect overall performance, from plant design to fuel quality.
- Technological Advancements: Innovations that fuel improvements in power generation.
- Sustainability Implications: The environmental impact and how high thermal efficiency plays a role.
Understanding these dimensions will not only enlighten researchers and industry professionals about the current state of power generation but also guide policymakers who shape energy initiatives. The goal is to offer a comprehensive narrative that aids in optimizing energy production while addressing environmental concerns effectively.
As we embark on this discussion, we will highlight the significant findings, methodologies, and implications connected with thermal efficiency, ultimately weaving a detailed tapestry of knowledge around the operation and impact of combined cycle power plants.
Prologue to Combined Cycle Power Plants
Combined cycle power plants represent a significant advancement in energy production, merging the principles of gas and steam technologies to achieve impressive thermal efficiency. As we grapple with the growing demand for energy amidst concerns around climate change and sustainability, the relevance of these facilities has never been more pronounced. By understanding how they function and their historical context, we can appreciate the fuller picture of energy generation that informs our current practices.
Definition and Functionality
At its core, a combined cycle power plant is designed to use two distinct processes to generate electricity: a gas turbine cycle and a steam turbine cycle. This approach allows the plant to harness waste heat from the gas turbine, which would otherwise be lost, by using it to create steam in a heat recovery steam generator (HRSG). This steam then drives the steam turbine, producing additional electricity. Hence, the combined cycle plants can achieve thermal efficiencies often exceeding 60%, significantly outpacing conventional single-cycle plants that usually rally around 33% to 45%.
This impressive efficiency not only minimizes fuel consumption but also reduces emissions per unit of electricity generated, making these plants a more attractive option in the quest for cleaner energy.
Historical Development
The journey of combined cycle technology began in the mid-20th century, as energy demands surged in tandem with industrial growth. The initial concept can be traced back to the 1940s with early experiments utilizing gas turbine engines. By the 1970s, the realization of the potential synergies between gas and steam cycles prompted engineers to develop integrated designs. These innovative designs transitioned from pilot projects to full-scale implementations, with significant operational plants coming into the limelight.
The 1990s saw a boom in the construction of combined cycle power plants, enabled by advancements in gas turbine technology, allowing for more efficient and robust operation at higher temperatures. The 21st century has continued this trend, as companies and governments increasingly prioritize cleaner energy strategies. Today, combined cycle plants are not only prominent in the United States but also gaining traction in various countries across Europe, Asia, and beyond. Their ability to adapt to fluctuating demands while maintaining efficiency marks them as a cornerstone of modern energy solutions.
"Harnessing the power of waste heat not only boosts efficiency, it represents a crucial step towards a sustainable energy future."
Understanding Thermal Efficiency
Thermal efficiency stands as a crucial pillar in the study and operation of combined cycle power plants. By diving into this topic, one can unearth the intricate details that define how these plants convert fuel into useful energy. Comprehending thermal efficiency allows stakeholders to assess the performance of power plants, guiding decisions on upgrades, technology implementations, or operational strategies. Essentially, it reveals the effectiveness of energy conversion processes and highlights areas ripe for optimization.
Definition of Thermal Efficiency
Thermal efficiency refers to the ratio of useful energy output to the total energy input, expressed as a percentage. For combined cycle power plants, this involves examining the energy produced by both gas and steam turbines relative to the fuel consumed. Mathematically, it can be defined as:
This definition underscores the essential function of heat engines and power plants. In layman's terms, it tells us how much of the fuel's energy is successfully transformed into electrical power. The better the thermal efficiency, the less fuel is wasted, translating into lower operational costs and reduced emissions.
Importance in Energy Generation
Understanding thermal efficiency goes beyond simple math; it carries significant implications for energy generation.
- Cost Savings: Higher thermal efficiency directly correlates to lower fuel consumption. In today’s economic landscape, where energy costs are a hot-button issue, reducing operational expenditure becomes paramount for plant operators.
- Environmental Impact: Improving thermal efficiency translates into decreased greenhouse gas emissions. Since combined cycle power plants produce electricity by harnessing the waste heat from gas turbines, capturing and utilizing that heat effectively is essential for minimizing the carbon footprint.
- Grid Reliability: Efficient power plants contribute to a more stable energy grid. By optimizing energy output, these plants can better meet demand fluctuations, enhancing reliability and reducing risks of blackouts.
- Policy Compliance: As global standards for emissions tighten, understanding and improving thermal efficiency enables plants to comply with regulatory frameworks, ultimately ensuring ongoing operation without costly penalties.
"Optimizing thermal efficiency not only supports economic factors but also underpins sustainability efforts, weaving a path toward cleaner energy production."
Components of Combined Cycle Power Plants
The efficiency and effectiveness of combined cycle power plants largely hinge on their three critical components: gas turbines, steam turbines, and heat recovery steam generators. Each of these plays a distinct role in optimizing power generation while minimizing waste. Understanding these components not only enhances comprehension of the operational framework but also illuminates the potential for improvements in thermal efficiency.
Gas Turbines
Gas turbines lie at the forefront of combined cycle power generation. These machines convert fuel energy directly into mechanical energy with remarkable speed and efficiency. Using a mixture of air and natural gas, these turbines ignite the fuel, generating high-temperature gases that expand through a turbine, thus producing energy to spin the generator.
There are several characteristics that underscore the importance of gas turbines:
- High Efficiency: Gas turbines can achieve efficiencies of over 60% when utilized in a combined cycle setting, where the waste heat is repurposed.
- Operational Flexibility: They can respond rapidly to changes in electricity demand, which is invaluable for balancing grid stability.
- Lower Emissions: Compared to traditional fossil fuel-based plants, gas turbines produce fewer greenhouse gases, making them a more environmentally friendly option.
Despite their advantages, one should consider factors like maintenance costs, where wear and tear from high operational temperatures can manifest as significant expenses over time. The right management strategies can mitigate these risks and enhance the longevity of the equipment.
Steam Turbines
Once the gas turbine expels hot gases, the heat recovery steam generator harnesses that energy, converting it into steam to drive the steam turbine. This dual cycle taps into the waste energy that would otherwise be lost.
Steam turbines are pivotal for several reasons:
- Utilizing Waste Heat: They take advantage of exhaust heat, improving the cycle's overall efficiency, which can help reach efficiencies around 80% across the entire plant.
- Robust Performance: Steam turbines are capable of handling high-pressure steam and can operate efficiently over long periods without significant degradation.
- Scalability: Their design and configuration can be adjusted to suit various power generation requirements, enhancing flexibility in plant design.
However, they do have drawbacks, such as higher initial capital costs and longer start-up times when compared with gas turbines. Addressing these concerns during the planning stage can ensure a smooth operational flow.
Heat Recovery Steam Generators
Heat recovery steam generators (HRSG) are integral parts of combined cycle power plants, serving as the bridge between gas and steam turbines. Their role focuses on capturing the waste heat from the gas turbine exhaust and converting it into steam.
Several benefits spotlight why HRSGs are indispensable:
- Energy Efficiency: By recuperating energy that would otherwise dissipate, HRSGs significantly boost the overall thermal efficiency of the power cycle.
- Sustainability: The increased efficiency translates to lower fuel consumption and reduced emissions due to the enhanced utilization of thermal energy.
- Flexibility in Design: HRSGs can be tailored to operate with different types of fuel and incorporate supplementary systems, such as duct burners, which provide additional heating when necessary.
Despite their advantages, HRSGs also come with challenges. Issues such as fouling and corrosion from high temperatures must be regularly monitored. Implementing protective measures can help ensure that HRSGs maintain high performance and efficiency levels.
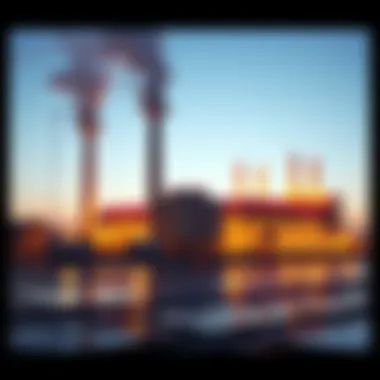
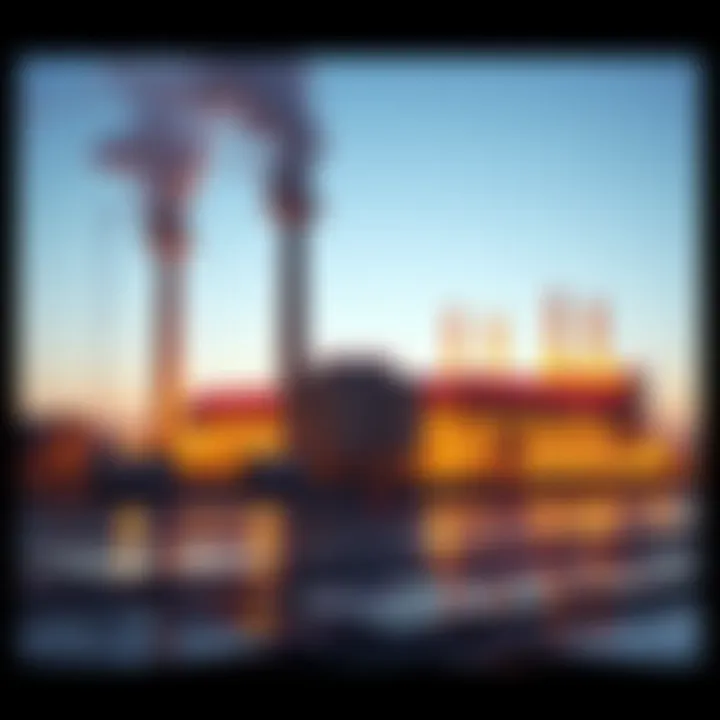
In summary, the components of combined cycle power plants are not merely parts of a machine; they represent a cohesive functional system that, when optimized, can lead to substantial gains in thermal efficiency, a critical goal for sustainable energy generation.
Thermodynamic Principles at Play
Understanding the thermodynamic principles at play in combined cycle power plants is crucial in realizing their efficiency. At the heart of these principles are the thermodynamic cycles that define how energy is converted and utilized. This section will delve into two significant cycles—the Carnot Cycle and the combined Rankine and Brayton cycles—which mark the foundation of thermal efficiency in these plants.
Carnot Efficiency
The concept of Carnot efficiency is often viewed as the gold standard in thermal efficiency analysis. It sets an upper limit on the efficiency any heat engine can achieve when operating between two temperature reservoirs. In simpler terms, the Carnot efficiency formula states that no engine can be more efficient than a Carnot engine, which operates ideally without any irreversibilities. The efficiency can be expressed as:
where (T_h) is the temperature of the hot reservoir and (T_c) is the temperature of the cold reservoir, both expressed in Kelvin.
This principle becomes vital for combined cycle power plants, as these plants effectively utilize the remaining heat energy from the gas turbines in their steam turbines. That essentially means they can yield a thermal efficiency that approaches the theoretical limit, which is primarily dictated by the temperatures of the steam and exhaust gases. In practical terms, the higher the temperatures involved, the greater the potential for efficiency improvements.
However, it’s crucial to recognize that real-life deviations due to mechanical inefficiencies, heat losses, and other operational constraints hinder achieving Carnot efficiency fully. Understanding these limitations invites engineers to find ways to optimize the operational parameters of combined cycle plants.
Rankine and Brayton Cycles
Now, moving onto the meat of the operation in combined cycle power plants: the Rankine and Brayton cycles. These two cycles work hand in glove. The Brayton cycle, also known as the gas turbine cycle, is the first to be employed in the sequence. It operates by drawing in ambient air, compressing it, mixing it with fuel, and igniting it to produce high-temperature, high-pressure exhaust gases that drive the gas turbine.
The Brayton cycle is characterized by its consistent pressure and temperature changes, which allow for quick energy conversion. The energy produced during this phase is then partially used to drive the compressor, making it quite efficient.
Simultaneously, the Rankine cycle takes the exhaust heat from the gas turbine and uses it to generate steam via the heat recovery steam generator (HRSG). This steam is then used to drive another set of turbines, producing additional electricity. This synergy effectively recycles waste heat, significantly enhancing overall thermal efficiency:
- Brayton Cycle:
- Rankine Cycle:
- Air Intake: Draws in and compresses air.
- Combustion: Mixes with fuel, igniting to produce exhaust gas.
- Expansion: Drives the gas turbine for electricity generation.
- Heat Recovery: Utilizes exhaust heat to create steam.
- Turbine Drive: Steam expands in a turbine generating more electricity.
- Condensation: Steam is cooled, and cycle repeats.
The combination of these two cycles in a single power generation system leads to greater overall efficiency, typically seen in combined cycle setups. The integration of the two cycles is what distinguishes combined cycle plants from conventional power plants, allowing them to convert more of the fuel's energy into usable electrical energy.
By comprehending these thermodynamic fundamentals, it becomes evident how they shape operational strategies, influence design choices, and ultimately determine the energy output of combined cycle power plants. This knowledge facilitates better decision-making for practitioners and engineers in the pursuit of optimal energy generation.
Factors Influencing Thermal Efficiency
Thermal efficiency in combined cycle power plants is not a one-size-fits-all number; it’s a dynamic metric influenced by various interrelated elements. Understanding these factors is not just essential—it is absolutely vital for enhancing the performance of energy generation systems. A thorough grasp of what influences efficiency can help engineers and policymakers craft better strategies for maximizing output while keeping environmental impacts at bay.
Ambient Conditions
The weather outside can play a surprising role in how well a combined cycle power plant performs. Ambient conditions, such as temperature, humidity, and altitude, directly affect both the gas and steam turbine efficiencies. For instance, at higher temperatures—let's say on muggy summer days—the air becomes less dense. This decrease in air density means gas turbines draw in less oxygen for combustion, ultimately leading to reduced efficiency. Similarly, low humidity can support better combustion but high altitude can cause lower air pressure, also impacting oxygen intake.
"Every degree counts, and the consequences of ambient variations can snowball quickly."
- Temperature: A cooler climate often enhances the performance of gas turbines as they draw in denser air.
- Humidity: High humidity may necessitate a balance, as it can dampen the combustion process in gas turbines but improve the cooling effect on steam cycles.
- Altitude: Power plants located at elevations are adversely affected due to the reduced atmospheric pressure, which hampers overall efficiency.
Evaluating these conditions enables plant operators to anticipate fluctuations and adapt their processes accordingly, like adjusting for optimal combustion ratios.
Operational Strategies
The way a power plant is managed has significant implications on its thermal efficiency. Operational strategies are the cornerstone where theory meets practicality, ensuring that all components work in harmony. Consideration is given to dynamic factors like load management, startup and shutdown procedures, and grid demand fluctuations.
- Load Management: By adjusting operational output based on real-time electricity demand, plants can minimize waste in fuel consumption, aligning operation with market needs.
- Startup Procedures: A slow and well-regulated startup might lead to quicker attainment of optimal operational conditions than a rapid approach, which can be more fuel-intensive.
- Shutdown Procedures: Just like starting up, revisiting how plants are shut down can affect their thermal efficiency. An efficient turbine cooling method post-operation can avoid thermal stress on components, prolonging their lifespan and improving future efficiency.
Successful execution of these operational strategies requires continuous monitoring and adjustment. Incorporating machine learning and predictive analytics can elevate the efficiency of these processes, which not only enhances performance but may also lead to lower operational costs over time.
Technology Advancements
As we move forward, technology will play a pivotal role in determining the thermal efficiency of combined cycle power plants. From innovative materials to cutting-edge software, advancements in technology offer a smorgasbord of possibilities to improve performance.
- Advanced Turbines: Today’s state-of-the-art turbines are designed with intricate cooling techniques and materials that can withstand higher temperatures, leading to better efficiency.
- Hybrid Systems: Developing hybrid systems that integrate renewable sources can mean less reliance on traditional fuel sources, benefitting both thermal performance and environmental concerns.
- Real-time Analytics: Deploying IoT solutions allows for constant tracking of plant parameters, predicting when maintenance is needed, and enhancing operational performance with data-backed decisions.
These technology advancements are making it possible to not only push the limits of thermal efficiency but also align energy production methods with broader environmental and economic goals. Realizing these efficiencies isn’t merely about numbers—it's about crafting a sustainable energy future.
Each of these factors interacts in complex ways, demonstrating that a deep and nuanced understanding of thermal efficiency can lead to not just improvements in energy production, but also a pivotal shift in how we view sustainability in energy generation.
Performance Metrics
Performance metrics are essential in understanding how well combined cycle power plants (CCPPs) function. These measurements provide a quantifiable assessment of the effectiveness of energy conversion processes. When evaluating the thermal efficiency of CCPPs, one cannot overlook the fundamental metrics that define their operational performance. Furthermore, effective metric analysis can lead to improvements in plant operation and decision-making for future investments.
One of the primary benefits of performance metrics is that they allow for a direct comparison between different CCPPs, thereby enabling industry professionals to identify best practices. Through benchmarking, stakeholders can assess the competitiveness of a plant in relation to others in this increasingly pertinent field, while also gaining insights into how to optimize performance.
Moreover, these metrics can signal areas for improvement and guide investments into technologies or processes that could enhance efficiency. Therefore, understanding performance metrics plays a pivotal role in ensuring not only operational excellence but also sustainability in energy generation.
Net Electrical Efficiency
Net electrical efficiency captures the ratio of electrical output to the total thermal energy input into the combined cycle power plant. This metric is critical as it encompasses all forms of energy loss within the system, offering a complete picture of how effectively a plant converts fuel into electricity.
A higher net electrical efficiency indicates a more effective facility, thus reducing operational costs and lowering emissions per unit of energy produced. A practical illustration is that if a plant has a net electrical efficiency of 60%, it indicates that 60% of the thermal energy from the fuel is converted into electrical output, with the remainder lost to waste heat and other inefficiencies.
The factors influencing net electrical efficiency include:
- Design of the plant: The configuration and arrangement of turbines and heat recovery systems play a significant role.
- Fuel type: The energy content and combustion characteristics of the fuel used can vastly affect efficiency.
- Ambient conditions: Weather factors, like temperature and humidity, can impact turbine performance.
- Operational practices: Regular maintenance and operational decisions can lead to incremental improvements in efficiency.
Heat Rate Analysis
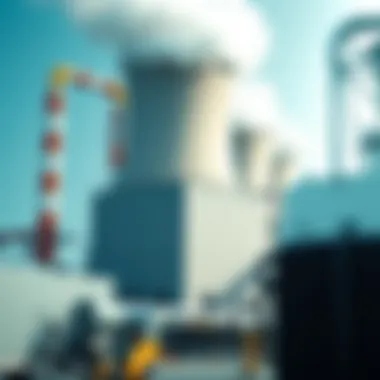
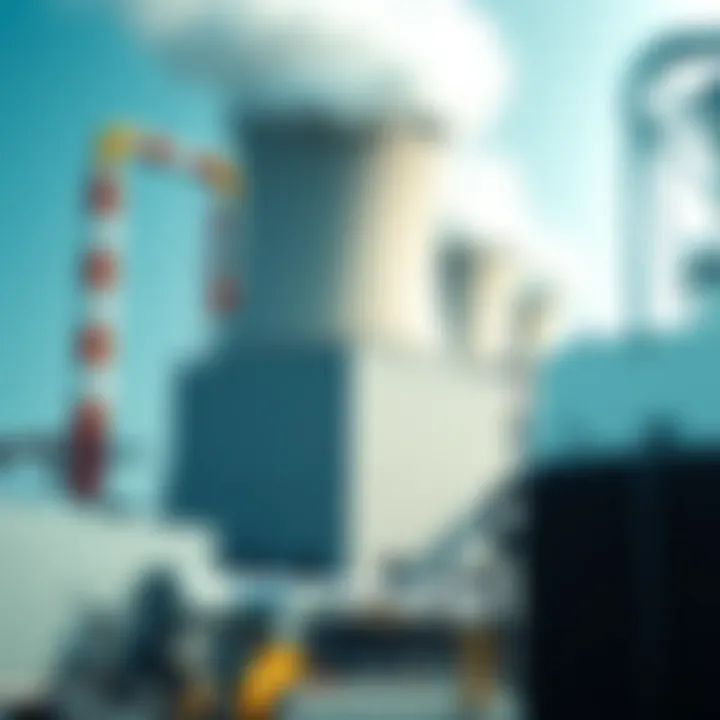
Heat rate analysis is a vital performance metric that indicates how much fuel energy is required to produce a unit of electricity, usually expressed in BTUs per kilowatt-hour (kWh). A lower heat rate essentially signifies a more efficient power plant, meaning it can generate electricity with less fuel input.
Understanding heat rate can unveil several important insights:
- Operational Cost: An efficient heat rate can significantly reduce the operational costs associated with fuel purchase.
- Competitiveness: Plants with superior heat rates can offer electricity at lower prices, making them more attractive in energy markets.
- Environmental Impact: A better heat rate indicates lower emissions per unit of electricity generated, aiding environmental sustainability goals.
As power generation evolves, leveraging heat rate analysis assists stakeholders in making informed decisions about investments in technology and selecting operational strategies that enhance efficiency.
"Monitoring performance metrics such as net electrical efficiency and heat rate analysis leads to enhanced operational strategies and ultimately, sustainable energy production."
Comparative Analysis
Comparative analysis serves as a critical lens through which we can assess the relative performance and efficiency of different energy generation methods. In the context of combined cycle power plants versus conventional power plants, this analysis reveals not just operational efficiencies but also broader implications for energy policy and environmental impact. Through this detailed examination, we can appreciate the nuances that define each power generation approach and understand their potential for a sustainable energy future.
Combined Cycle vs. Conventional Power Plants
When we pit combined cycle plants against their conventional counterparts, a stark contrast appears. Combined cycle power plants utilize both gas and steam turbines to harness energy more effectively than conventional power plants, which typically rely on a single cycle of energy conversion. The key benefits of this arrangement include:
- Higher Thermal Efficiency: Combined cycle plants often achieve thermal efficiencies above 60%, thanks to their ability to convert the waste heat from gas turbines into additional electrical power via steam turbines. In contrast, conventional plants may max out around 35-40% efficiency.
- Less Fuel Consumption: With their higher efficiency, combined cycle units require less fuel to produce the same amount of electricity. This directly correlates with lower fuel expenses over time, making them economically favorable.
- Reduced Emissions: The combustion process in combined cycle plants is cleaner because they are designed to optimize fuel use. When we tally emissions of carbon dioxide and other pollutants, combined cycle systems exhibit a significantly lower footprint than traditional fossil fuel plants.
It's not all sunshine and rainbows, though. The initial capital cost of setting up combined cycle power facilities tends to be higher due to their complexity and technology requirements. Operational considerations and maintenance also operate differently, affecting lifecycle cost assessments.
"Understanding these differences isn’t merely academic; it shapes how industries can respond to energy demands in a more sustainable way."
Impact of Fuel Type on Efficiency
The fuel type—natural gas, coal, or renewables—plays an influential role in thermal efficiency. In combined cycle power plants, natural gas reigns supreme, mainly for its cleaner burning characteristics and higher efficiency rates. Here’s a breakdown of the various fuel types and their respective impacts:
- Natural Gas: As the primary fuel for combined cycle plants, natural gas fuels combine high efficiency with comparatively lower emissions. The consistent advancements in extraction methods, such as fracking, have also made this fuel type more accessible and affordable.
- Coal: For conventional plants, coal remains a prevalent choice. However, when it comes to thermal efficiency, coal plants are often less competitive due to the high carbon footprint and other environmental concerns. They typically face stricter regulations that further reduce their feasibility.
- Renewables: Incorporating renewable energy sources alongside combined cycle systems is gaining attention. While renewables like wind and solar cannot replace fossil fuels directly in a combined cycle framework, they can complement operations—especially in hybrid configurations, enhancing overall thermal performance.
As fuel types continue to evolve, so too will the technologies and strategies employed in combined cycle and conventional plants. The adaptability and responsiveness of energy systems to different fuels can not only affect efficiency but also sustainability goals across the globe.
In summary, the comparative analysis of these elements not only highlights efficiency but also emphasizes the larger narrative of energy transition and climate stewardship. By drawing these comparisons, we foster a deeper understanding of how innovation in power generation can lead to a better and more efficient energy landscape.
Environmental Considerations
Environmental considerations play a pivotal role in the discussion of thermal efficiency in combined cycle power plants. As global energy demands continue to escalate, the impact of energy generation on the environment cannot be brushed aside. A careful examination of emissions and resource utilization sheds light on how these plants can contribute to a more sustainable energy future.
Emissions Profile
The emissions profile of combined cycle power plants is fundamentally different from that of conventional power plants. These plants are designed to operate with enhanced efficiency, which generally leads to lower emissions per unit of electricity produced.
- Reduced Greenhouse Gases: On average, combined cycle systems emit about 50% less carbon dioxide compared to traditional coal-fired plants. The utilization of natural gas as a primary fuel source significantly cuts down on harmful emissions, a crucial aspect amid the pressing battle against climate change.
- Nitrous Oxide and Particulate Matter: While natural gas combustion does emit nitrous oxide, the amount is substantially lower than that from fossil-fuel-powered alternatives. Technologies such as selective catalytic reduction help minimize these outputs further. Although combined cycle plants still produce some particulate matter, the levels are typically within acceptable regulatory limits.
Understanding these emission profiles is vital, as it helps policymakers establish better regulations and standards aimed at reducing environmental impact in energy production.
"Less pollution equates to a cleaner future; combined cycle plants are doing their part in mitigating climate change."
Resource Utilization
Resource utilization remains a core consideration in evaluating the sustainability of combined cycle power plants. Efficient use of resources can lead to reduced waste and better environmental outcomes.
- Water Usage: Unlike coal fired plants, which often depend heavily on water for cooling, combined cycle systems utilize cooling technologies that greatly diminish water consumption. Using closed-loop cooling can save vital water resources, especially in arid regions where water scarcity is an issue.
- Waste Heat Recovery: One significant advantage of combined cycle technology is its ability to capture waste heat that would otherwise be lost. This recovered heat is then used to generate steam for additional electricity production through steam turbines. This process not only increases overall efficiency but also optimizes the use of available resources, promoting a more sustainable operation.
- Sourcing Materials: The materials used in constructing combined cycle plants are essential to consider as well. Utilizing recycled materials or optimizing the selection of new materials can greatly enhance the resource efficiency of these power plants.
Future Trends in Power Plant Design
As the global energy landscape evolves, the design of power plants, particularly combined cycle power plants, is changing coming along with it. This shift is crucial as we strive for sustainability while maintaining high thermal efficiency. The conversation surrounding future trends in power plant design is not just about enhancing energy production; it's also about minimizing environmental impacts and integrating innovative technologies. This section will discuss two significant areas:
- Integration of Renewable Energy
- Emerging Technologies
Integration of Renewable Energy
One of the most pressing trends is the integration of renewable energy sources. As the demand for cleaner energy options gains momentum, power plants are increasingly looking to incorporate solar, wind, and other renewables into their operations. Doing so not only reduces greenhouse gas emissions but also stabilizes energy supplies.
Benefits of Renewable Integration:
- Reduced Carbon Footprint: By concocting natural gas with renewables like solar and wind, plants can cut down on harmful emissions significantly.
- Enhanced Reliability: Renewable energy can act as a backup during peak demand times, ensuring a steady flow of energy.
- Financial Savings: The long-term viability and decreasing costs of renewable technologies allow for reduced operational costs.
However, integrating these sources isn’t without its challenges. Issues such as intermittency and the need for advanced energy storage systems must be solved to ensure reliability and efficiency. Current advancements in battery technologies and hybrid systems aim to address these limitations, presenting a promising future for energy generation.
Emerging Technologies
The technological landscape surrounding power plants is vibrant and ever-changing. Innovations are making it possible to produce energy more efficiently and sustainably. Two key areas of focus include:
- Advanced Turbine Technologies: smarter and more efficient turbine designs are emerging, which can capture more energy from gas flows, leading to enhanced output.
- Carbon Capture and Storage (CCS): as discussions about climate change intensify, capturing carbon emissions before they enter the atmosphere is becoming vital. CCS technologies are being implemented more widely in power plants, allowing them to operate with minimal impact on the environment.
Benefits of Emerging Tech:
- Increased Efficiency: New materials and design innovations in turbines can bolster overall plant efficiencies.
- Lower Emissions: With technologies like CCS, power plants can reduce their environmental impact even when fossil fuels are used.
- Adaptability: Incorporating smart grid technologies allows facilities to respond to energy demand in real-time, optimizing performance.
"Future power plants must be adaptable and resilient, combining technologies across fuels and innovations to meet the energy demands of tomorrow."
In summary, the future trends in power plant design are steering the industry toward a landscape where sustainability, efficiency, and advanced technology intersect. By integrating renewable energy and adopting emerging technologies, combined cycle power plants can pave the way for a greener energy future, aligning with global energy goals. This journey not only ensures energy reliability but also promotes environmental stewardship, ultimately shaping a sustainable energy future.
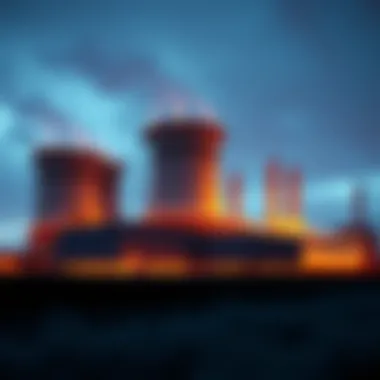
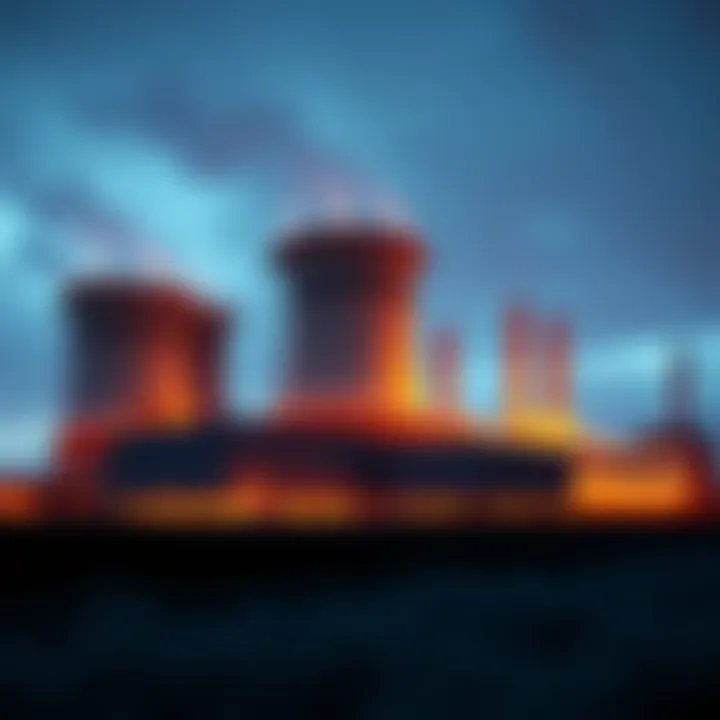
Case Studies
Case studies are invaluable in understanding the practical implications of thermal efficiency in combined cycle power plants. They provide real-world examples of how theoretical concepts translate into tangible results. These case studies offer insights that can guide future projects and inform policy decisions. By drawing on successes and failures, stakeholders can better comprehend operational efficiencies, costs, and environmental impacts.
Successful Implementations
One of the most notable examples of a successful implementation of a combined cycle power plant is the Bouchain Power Plant in France. This plant, operated by ENGIE, boasts a thermal efficiency exceeding 62%. Utilizing state-of-the-art gas and steam turbine technology, it demonstrates the effectiveness of integrating advanced components to maximize energy output from fuel.
The design choice to incorporate a heat recovery steam generator allows for efficient recovery of waste heat, leading to a significant reduction in fuel consumption. Such successful case studies underscore the critical elements that contribute to high thermal efficiency:
- Innovative Technology: The adoption of newer turbine technology has proven essential in increasing thermal efficiency.
- Optimized Operational Strategies: Implementations that include meticulous operational planning have achieved marked improvements in efficiency.
- Regulatory Support: Strong governmental policies incentivizing clean energy practices have played a crucial role in the success of such power plants.
Another prominent example is the Kawasaki Gas Turbine Combined Cycle Power Plant in Japan. It is equipped with an innovative air-cooled condenser that enhances overall efficiency by minimizing water usage, thus addressing environmental concerns while optimizing performance.
Lessons Learned
The analysis of these case studies reveals several lessons beneficial for future endeavors in combined cycle power plants:
- Importance of Adaptability: Plants must remain adaptable to advances in technology, ensuring they can incorporate upgrades as they become available.
- Holistic Approach: Success hinges on a systems-thinking perspective, where every component—from gas turbines to environmental systems—works in harmony.
- Operational Monitoring: Continuous performance monitoring is essential for early identification of inefficiencies, allowing for timely interventions that can drastically improve thermal performance.
- Community Engagement: Gaining community support through transparent communication regarding environmental impact and job creation has proven beneficial for project viability.
- Investment in Human Capital: Training personnel on new technologies and operational strategies enhances the effectiveness and reliability of combined cycle power plants.
"Successful applications in the field demonstrate that while technology is crucial, the human element cannot be overlooked; skilled operators are fundamental to achieving peak efficiency."
By dissecting these case studies, stakeholders in the energy sector can draw parallels to their own projects and set benchmarks for future success. Harnessing knowledge gained from past experiences can facilitate advancements in thermal efficiency, directly impacting sustainability efforts across the globe.
For more information on energy efficiency and power plants, consider visiting resources like Wikipedia or Britannica.
Economic Implications
When discussing combined cycle power plants, one cannot overlook the economic implications tied to their operation and efficiency. This dimension extends beyond mere profitability; it encompasses operational costs, investment requirements, and the broader impact on energy markets. In today's landscape, where financial viability becomes increasingly intertwined with sustainable energy practices, understanding the economic aspects of thermal efficiency can provide valuable insights to stakeholders across various fields.
Cost-Benefit Analysis
A thorough cost-benefit analysis presents a compelling narrative around the financial viability of combined cycle power plants. This approach evaluates the initial capital needed for plant infrastructure against the operational savings gained through enhanced thermal efficiency. Here are a few key points to consider in this analysis:
- Initial Investment Costs: Building a combined cycle power plant often demands substantial upfront investments, which can discourage potential stakeholders. These costs can include advanced turbine technologies, heat recovery steam generators, and other requisite equipment.
- Operational Expenses: Once operational, these plants typically enjoy lower fuel costs compared to conventional plants due to their higher thermal efficiency. For instance, a facility designed with a greater thermal efficiency can convert a more significant portion of fuel energy into usable power, effectively reducing the cost per megawatt-hour.
- Lifecycle Considerations: Over time, the initial costs can become less critical compared to the ongoing savings from fuel efficiency, maintenance costs, and potential revenue from electricity sales. A well-designed cost-benefit analysis can help illuminate this transition in perception from initial expenditure to long-term gains.
As highlighted by many industry reports, the importance of conducting a rigorous cost-benefit analysis cannot be overstated. The balance between investment costs and operational savings ultimately influences decision-making at both governmental and private levels.
"Understanding the financial dynamics of combined cycle power plants can shift perceptions and push stakeholders to recognize their viability in modern energy production."
Investment Outlook
The investment outlook for combined cycle power plants is ever-evolving. With the global push for cleaner energy solutions and improved efficiency, investor interest is honing in on these plants as viable options. Here’s what shapes the current landscape:
- Sustainable Energy Trends: As nations reinforce their commitments to reduce greenhouse gases, financial incentives are becoming more attractive for power generation facilities employing combined cycle technologies. Investors often find comfort in investments accompanied by government backing or favorable policies, which can enhance return potential.
- Technological Innovations: Advancements in turbine design and heat recovery systems continue to improve efficiency metrics. As these technologies become more commercially viable, the financial risk of investments decreases. Companies like Siemens and GE are at the forefront of innovation, driving changes that appeal to investors.
- Market Dynamics: The fluctuations in energy markets are key to understanding where investments can yield dividends. As natural gas prices remain relatively stable, combined cycle plants can offer a hedge against volatility, solidifying their attractiveness for investors.
To summarize, the investment outlook for combined cycle power plants appears robust. Financial analyses and market trends suggest that for those looking at the long game, these facilities represent not just environmental responsibility but also a promising financial venture.
Ultimately, economic implications tied to combined cycle power plants offer a rich tapestry of insights that can inform various stakeholders, from policymakers to corporate investors. By carefully weighing these considerations, one can better navigate the complexities of energy production in an increasingly competitive and environmentally conscious landscape.
Policy Recommendations
Regulatory Frameworks
A robust regulatory framework lays the foundation for promoting thermal efficiency within power plants. These frameworks typically define standards and performance metrics, ensuring that plants adhere to best practices in design and operation. Here are some notable elements of effective regulatory frameworks:
- Emissions Standards: By setting limits on greenhouse gases and other pollutants, regulations urge plants to adopt cleaner technologies. This indirectly promotes thermal efficiency by encouraging innovations that minimize waste and enhance operational performance.
- Performance Benchmarking: Providing benchmarks for thermal efficiency creates a competitive landscape, pushing plants to optimize their operations. Instead of working in isolation, companies can measure their performance against industry leaders, fostering a culture of continuous improvement.
Furthermore, regulations can be flexible enough to incorporate new technologies as they arise. Ensuring that these regulations are adaptable helps maintain relevance in a rapidly evolving energy sector.
Incentives for Efficiency Improvements
To drive the necessary changes in energy production practices, incentives play a significant role. Here are some common incentives that can be introduced:
- Financial Grants and Subsidies: Offering grants for technology upgrades can ease financial burdens on operators. For example, a government might subsidize the cost of implementing advanced heat recovery systems that enhance the overall thermal efficiency.
- Tax Breaks: Tax incentives for power plants that achieve specific efficiency metrics serve as a powerful motivator. When plants see a direct correlation between their operational efficiency and taxable income, there’s a greater incentive to invest in innovative solutions.
It's also essential to promote awareness and knowledge-sharing across the industry. Workshops, seminars, and online resources can facilitate education about efficiency practices and technologies, thus fueling a more informed approach to energy generation.
"A proactive policy approach can transform the landscape of thermal efficiency in combined cycle power plants, leading to a sustainable future."
For further reading on policy frameworks and incentives pertaining to energy efficiency, you may visit U.S. Department of Energy or refer to detailed analyses on Energy Policy on Wikipedia.
Culmination
A thorough understanding of thermal efficiency does more than enhance academic conversations; it informs decision-making for engineers, policymakers, and industry stakeholders. This article highlighted how combined cycle power plants utilize both gas and steam turbines effectively. This dual approach maximizes energy extraction from fossil fuels, enabling a higher efficiency rate than traditional plants. Moreover, addressing emissions and the environmental impacts is crucial. It's clear efficiency isn’t just a number; it’s intertwined with environmental policy and resource management.
Furthermore, the integration of advanced technologies—like artificial intelligence in operational analytics—has been discussed in various sections. These advancements serve to refine operational strategies, ultimately leading to better performance metrics. It’s time we recognize that improving thermal efficiency is not just beneficial but essential for future energy endeavors, paving the way for innovations in renewable technologies and beyond.
"Energy efficiency is doing more with less; it’s about doing the right things well."
Summary of Key Insights
- Operational Mechanisms: The mechanics of turbine operation demonstrate how combined cycle plants exploit dual energy sources, maximizing output.
- Factors Influencing Efficiency: This includes everything from ambient conditions to the latest technology advancements which can change the game entirely.
- Environmental Considerations: An emphasis on carbon footprint reduction indicates that higher thermal efficiency contributes to lower emissions.
- Future Implications: Acknowledgement of trends in integration with renewable energy confirms the role of combined cycles in future energy frameworks.
Future Outlook
As we look ahead, it’s evident that the future of combined cycle power plants will be defined by continued innovation and sustainability. Upgrading existing infrastructure with cutting-edge technologies and practices can lead to significant enhancements in thermal efficiency. Perspectives from various projects indicate trends that favor hybrid systems, where traditional processes are complemented by renewable sources.
Further research into energy recovery systems is expected to yield fruitful results. The merging of artificial intelligence and Internet of Things technology with power plant operations promises to optimize functions dynamically, responding in real-time to varying energy demands. Collaboration across sectors will be pivotal in not only meeting energy needs but doing so responsibly and intelligently.
In summary, the effectiveness and importance of combined cycle power plants will grow as global energy requirements change. By adopting a forward-thinking approach, the industry can better align itself with environmental standards, securing a sustainable future for energy production.