Comprehensive Insights on System Integration in Industry 4.0
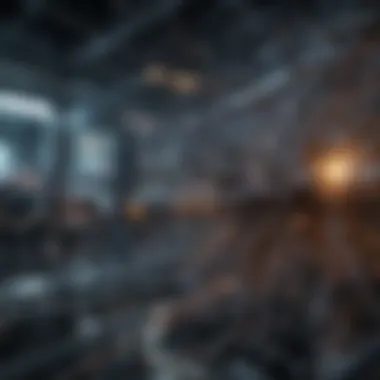
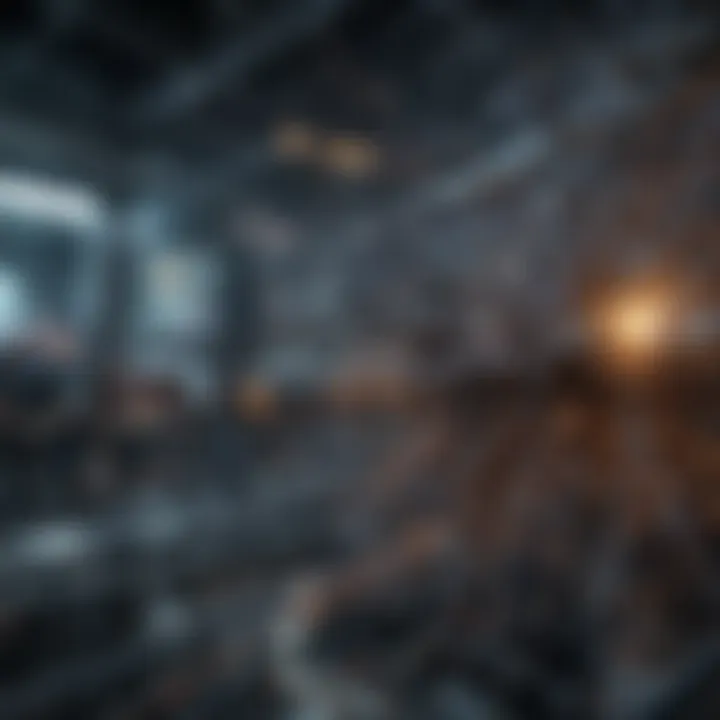
Intro
In todayâs rapidly evolving landscape, where digital convergence is not just a buzzword but an everyday reality, the importance of system integration cannot be overstated. Industry 4.0 heralds a new phase in manufacturing, characterized by smart technologies, the Internet of Things (IoT), and data-driven decision-making. Moreover, it is crucial to understand how these components interlink and function harmoniously within various organizational settings. System integration emerges as an essential process that ensures seamless communication and synergy among disparate systems, leading to more efficient operations and enhanced competitiveness.
With that in mind, this section aims to provide an overview of the critical findings related to system integration in Industry 4.0. It will present an insightful analysis of the key components, associated challenges, and the strategic approaches necessary to navigate this complex landscape successfully.
Integrating system components often means threading together various technologies and processes to create a cohesive unit. This endeavor is akin to assembling a jigsaw puzzle where each piece, representing a different technology or system, must fit perfectly for the whole picture to emerge. As we delve deeper into our exploration, we will break down each of these individual pieces and their roles within the broader framework of Industry 4.0.
This text will provide valuable perspectives for students, researchers, educators, and professionals seeking to grasp the nuances of system integration in modern industry. Through this lens, we encourage you to contemplate the implications of these findings and consider how they might influence future development within your areas of expertise.
Defining Industry 4.
The advent of Industry 4.0 represents a watershed moment for the manufacturing and production sectors, fundamentally altering their landscape through the infusion of advanced technologies. Understanding this paradigm is crucial for any organization looking to harness its potential. Industry 4.0 entails the convergence of digital and physical systems, driven by a web of interconnected devices, software, and human inputs. Here, organizations not only enhance their efficiency but also reposition themselves in a rapidly evolving market.
Historical Context
Historically, the industrial revolutions have evolved from steam power to electric energy, and finally to automated processes. Each stage has seen dramatic shifts in how goods are produced and delivered. The term "Industry 4.0" was first popularized in Germany around 2011 in a government initiative aimed at promoting the digitization of manufacturing. It's a natural progression from its predecessors, with an emphasis on connectivity and data exchange in manufacturing technologies. More than just a buzzword, it's grounded in a historical framework that highlights the technology-driven transformations over the centuries.
Core Technologies Involved
Grasping the essence of Industry 4.0 means diving into the core technologies that drive it. These include the Internet of Things (IoT), Artificial Intelligence (AI), Big Data Analytics, and Robotics and Automationâeach playing a pivotal role in shaping this new industrial landscape.
Internet of Things
The Internet of Things stands as a cornerstone of Industry 4.0, allowing devices, machines, and systems to connect, share data, and make autonomous decisions. Its ability to enable real-time communication creates a digital thread throughout the manufacturing process. One significant characteristic of IoT is its scalability; systems can grow as needed, integrating additional sensors or devices without a complete overhaul. However, a notable issue arises in data privacy and security, which necessitates robust measures to mitigate risk.
Artificial Intelligence
Artificial Intelligence provides a level of cognitive functionality that elevates Industry 4.0 systems beyond mere automation. AI can analyze patterns and predict outcomes, aiding in everything from maintenance scheduling to supply chain optimization. The core appeal of AI is its adaptability; it's not confined to repetitive tasks but can learn and evolve with new data. Nevertheless, its reliance on substantial datasets calls into question ethical considerations and biases that can influence AI decision-making.
Big Data Analytics
Big Data Analytics empowers organizations by transforming overwhelming sets of data into actionable insights. It plays a crucial role in decision-making processes, allowing for more informed choices and strategies based on trends extracted from data analysis. The fundamental characteristic here is its ability to process vast amounts of information quickly. However, the challenge is in ensuring data integrity and applying the correct analytics techniques, as poor quality data can lead to misleading conclusions.
Robotics and Automation
The field of Robotics and Automation revolutionizes traditional manufacturing practices by enabling high levels of precision and efficiency. Robots can work tirelessly, often leading to a reduction in human error and operational costs. A defining feature of this technology is its capacity for customization; robots can be programmed for various tasks without needing extensive downtime for reconfiguration. However, on the flip side, there are concerns over job displacement, warranting a discussion on how workforce policies must adapt alongside technological advancements.
Understanding System Integration
In today's rapidly evolving technological landscape, comprehending the essence of system integration within Industry 4.0 is crucial. As firms strive to leverage advanced technologies, integrating various systems emerges as a vital component for operational success. Effective system integration aligns different technological components seamlessly, ensuring that processes function harmoniously, enhancing productivity and facilitating informed decision-making. The implications of this integration resonate through every layer of an organization, from the shop floor to the executive suite, making it a cornerstone of the Industry 4.0 movement.
Concept and Importance
At its core, system integration refers to the unification of various subsystems into a single, cohesive system. This efforts allow disparate technologies to communicate and collaborate efficiently. In the context of Industry 4.0, the concept takes on heightened significance, promoting interconnectedness and enabling organizations to harness data from multiple sources. Thus, the importance of grasping system integration lies not only in understanding how systems interrelate but also in recognizing the potential for enhanced efficiency, innovation, and competitive edge.
A thoughtful integration process involves several stakeholdersâthe IT department, operational teams, and strategic plannersâall working together towards common goals. This collaboration leads to synergies that help improve workflows and reduce delays, ultimately boosting overall effectiveness. Particularly in the face of unforeseen disruptions or shifts in market demand, having a robust system integration strategy allows organizations to respond with agility and resilience.
Types of System Integration
Understanding system integration's various forms is essential for organizations aiming to adopt Industry 4.0 effectively. The three primary types are horizontal integration, vertical integration, and end-to-end integration, each providing distinct advantages and addressing specific integration needs.
Horizontal Integration
Horizontal integration involves connecting various systems across similar levels in the organization, often across different departments or functional areas. This type of integration facilitates information sharing and resource allocation, enabling a streamlined flow of data. One of its key characteristics is the ability to create a unified platform for access. This is especially beneficial as it can boost collaboration between departments, leading to improved communication and a better understanding of processes across the board.
A unique feature of horizontal integration is its capability to foster innovation through shared insights. For instance, when marketing teams leverage data from sales departments, they can craft targeted campaigns that resonate more effectively with customers, enhancing overall performance. However, this approach can also introduce challenges, such as silos forming if integration isn't adequately managed.
Vertical Integration
Vertical integration stands in contrast by emphasizing the interlinking of processes within the same business domainâthink of it like the supply chain. It involves connecting different levels of data and workflows from suppliers up through production to customers. This seamless connection allows for better control over the production process, significantly reducing delays and miscommunications.
A prominent characteristic of vertical integration is its ability to provide a holistic view of the operations, which can streamline decision-making. Companies adopting this method often discover that they can achieve a considerable reduction in costs and inefficiencies. One possible downside, however, is the potential for increased complexity as more layers are integrated, requiring careful management and oversight.
End-to-End Integration
End-to-end integration takes a comprehensive approach by uniting all aspects of a process from start to finish. This means connecting every step, including planning, sourcing, production, and distribution. The primary benefit here is significantly enhanced workflow efficiencies, allowing firms to respond swiftly to market demands or disruptions with precision.
Key in this type of integration is the transparency it offers, as all stakeholders can monitor progress and identify bottlenecks in real time. Organizations that implement end-to-end integration often find themselves at an advantage, as they can track everything from inventory levels to customer satisfaction. However, achieving this high level of integration requires commitment and robust IT infrastructureâwithout which the potential benefits may remain unfulfilled.
Efficient system integration is not simply a technical undertaking; it also demands a cultural shift, necessitating collaboration and openness throughout the organization.
In summary, understanding the different types of system integration enables organizations to adopt tailored strategies that best fit their operational needs. By embracing these approaches, firms can harness the power of their data and drive transformation within the realm of Industry 4.0.
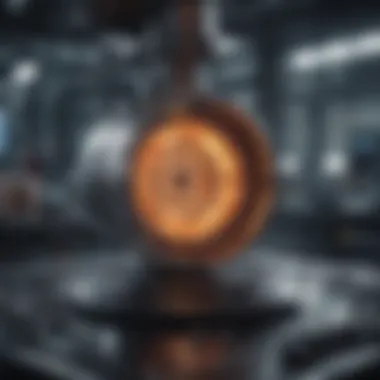
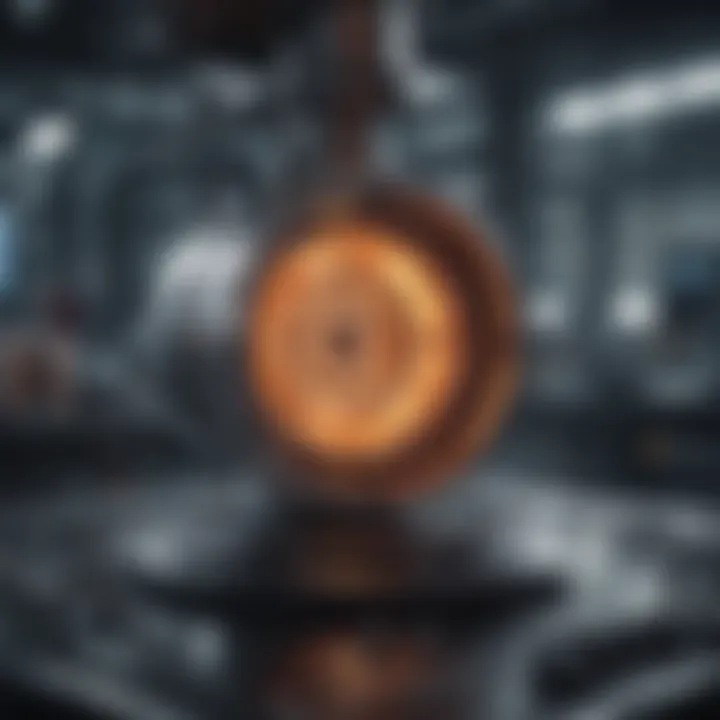
Architectural Components of Industry 4. Systems
Understanding the architectural components of Industry 4.0 systems is pivotal in grasping how modern industrial environments are constructed. At the heart of this transformation lies a blend of technologies that collectively enhance productivity, flexibility, and efficiency. Know that these components are the backbone that support seamless connectivity between devices, data, and networks.
Cyber-Physical Systems
Cyber-Physical Systems (CPS) represent a significant advancement in integrating the physical and digital worlds. They combine computation, networking, and physical processes. Think of CPS as the quintessential bridge between hardware and software.
Imagine a smart factory where machinery is equipped with sensors, gathering data and communicating in real-time. For instance, consider a car manufacturing unit where robotic arms, equipped with CPS, can adapt their tasks based on real-time feedback. This ability not only optimizes production lines but also minimizes downtime and enhances safety. The interplay between physical machinery and software allows for real-time monitoring and adjustments, making processes more efficient.
"CPS exemplify how concrete systems can be diversified through digital integration, leading to unprecedented scalability and customization."
However, the implementation of CPS brings challenges, such as ensuring reliability and maintaining security against potential cyber threats. Hence, industries must approach the deployment of cyber-physical systems with a strategic mindset, focusing on robust frameworks that prioritize these crucial aspects.
Cloud Computing
Cloud computing emerges as an essential element in Industry 4.0's architecture. It provides the infrastructure needed for scalability and flexibility, crucial for handling the vast amounts of generated data. By shifting operations to the cloud, organizations can leverage computing power on demand, reducing the need for extensive on-premise resources.
For instance, a company can analyze production data from a remote location, streamlining performance evaluations and decision-making processes. This accessibility allows teams to collaborate anywhere, reinforcing the idea that geographical boundaries are becoming irrelevant in industrial operations. Companies like Amazon Web Services and Microsoft Azure have revolutionized how industries approach data management, offering services that include storage, analytics, and application hostingâall in one package.
In addition, cloud computing enhances data security protocols via centralized management systems. Organizations can enforce stringent security measures across all their digital platforms, shielding sensitive information from potential breaches. However, cloud integration isnât without its hurdles. Businesses must grapple with data sovereignty regulations, compliance issues, and the risks of vendor lock-in, making it essential to craft well-informed cloud strategies.
Data Management and Analytics
Data management and analytics are the lifeblood of Industry 4.0. As production processes become more interconnected, the volume of data being generated skyrockets. Hence, effective management and analysis of this data become non-negotiable for companies aiming to stay competitive.
Data management involves organizing, storing, and maintaining data integrity. It assures that businesses can access reliable data when they need it. Subsequently, analytics takes it a step further by employing various techniques to extract meaningful insights from this data. For instance, predictive analytics can foresee equipment failures before they occur, leading to proactive maintenance and reduced operational costs.
Moreover, companies can harness machine learning algorithms to personalize products and services based on consumer behavior analysis. This kind of tailored approach fosters customer loyalty and satisfaction, distinguishing one organization from another in the vast industrial landscape.
In summary, the architectural components of Industry 4.0 systemsâCPS, cloud computing, and data management and analyticsâwork synergistically to propel industries into an era defined by efficiency and innovation. By understanding these components, stakeholders can navigate the transition towards more integrated and intelligent manufacturing environments.
Challenges of System Integration
Navigating the rough waters of system integration in Industry 4.0 isn't a walk in the park. The progress brought on by Industry 4.0 hinges not just on technologies but also on how seamlessly these systems can work together. Grasping the hurdles of system integration is crucial for organizations aiming to thrive in this competitive landscape. These challenges, if left unaddressed, can become stumbling blocks to harnessing the full power of digital transformation. From issues with interoperability to the complexities surrounding data security, itâs essential to tackle these concerns in order to optimize operations and ensure a smooth transition.
Interoperability Issues
Interoperability stands out as a core challenge in system integration. At its heart, interoperability is about ensuring different systems, machines, and software can communicate with one another effectively. In diverse manufacturing ecosystems, where equipment often comes from various vendors, the lack of standardized protocols can lead to a fragmented environment. This fragmentation can result in data silos, where information is trapped within isolated systems, restricting data flow and minimizing the potential of data-driven decision-making.
Furthermore, consider the implications of real-time data processing. To optimize operations, timely insights from various machines and sensors are vital. A situation arising from poor interoperability can lead to delayed response times and reduced production efficiency. Investing in common standards and protocols can mitigate these issues. Importantly, effective communication among all devices can create a unified platform that enhances operational visibility and analytical capabilities.
Data Security and Privacy Concerns
In an era dominated by data, ensuring its security has never been more critical. As organizations embrace system integration, they may unwittingly expose themselves to new vulnerabilities. The risk of data breaches can loom large when numerous systems are interconnected. Improperly configured interfaces or outdated security measures can serve as gateways for unauthorized access and cyber-attacks.
Moreover, privacy concerns associated with data collection and processing cannot be understated. Organizations must handle sensitive data with utmost care. For instance, in the healthcare sector, patient data privacy regulations impose strict limits on how data can be shared or accessed. Developing a robust cybersecurity strategy is paramount, which may include encryption techniques, regular vulnerability assessments, and compliance with regulations such as GDPR or HIPAA. Addressing these concerns upfront will create a more resilient integration framework that prioritizes the safety of crucial data assets.
Legacy Systems Compatibility
Most organizations donât just wake up one day and decide to integrate new technologies; they often grapple with existing legacy systems. These older systems, usually deeply embedded in operations, can be resistant to change. Often, they are not designed to interact with modern applications, presenting a substantial hurdle in the path of integration.
The compatibility issue can lead to significant resource allocationâboth time and moneyâmaking it a burden for companies trying to modernize their processes. It often requires extensive customization or even a complete overhaul of existing infrastructure, tasks that may seem intimidating. However, there are strategies to mitigate these challenges. For instance, adopting an incremental approach, where components are updated progressively, can lessen risks and ease transitions without disrupting business continuity. Additionally, leveraging modern middleware solutions can facilitate connections between legacy systems and new technology, ensuring organizations can preserve their investments while moving forward into the future.
"Successful integration relies on addressing the challenges proactively, ensuring no stone is left unturned in the quest for efficiency and effectiveness in Industry 4.0."
Benefits of Effective System Integration
System integration is often overlooked until a crisis strikes. In the age of Industry 4.0, where complexity can befuddle even the most seasoned practitioners, effective integration is paramount. It is not just about connecting devices; itâs about cultivating a seamless workflow that enhances every aspect of production, from efficiency to decision-making. Understanding the specific benefits can illuminate the importance of embracing this intricate process in todayâs digital landscape.
Enhanced Operational Efficiency
One of the most tangible benefits of effective system integration lies in improved operational efficiency. Companies that manage to integrate their systems successfully can experience a notable reduction in time wasted on repetitive tasks and errors. This efficiency manifests itself in various ways:
- Streamlined Processes: Automating mundane tasks reduces the need for manual interventions. For instance, a factory that uses automated inventory management systems can swiftly track parts and resources without human inputs.
- Reduced Downtime: Interconnected systems can alert operators about potential issues before they escalate into full-blown equipment failures, allowing for timely maintenance.
- Optimized Resource Allocation: When systems share data seamlessly, businesses can more accurately allocate resources where they're needed most. This means less waste and, ultimately, a better bottom line.
Furthermore, as tasks are completed quicker and with greater accuracy, the manufacturing output improves significantly. A factory not integrated properly may find its output littered with delays and errors, resulting in a frustrated workforce and unsatisfied customers.
Improved Decision-Making Processes
Data integrity and availability are the bedrock of effective decision-making. System integration empowers companies to make better decisions by providing real-time data across different departments. A few key aspects include:
- Holistic View of Operations: When various systems communicate, executives can gain insights that previously required time-consuming gathering of information. For example, a unified dashboard that tracks production, sales, and supply chain metrics allows for swift adjustments based on market needs.
- Data-Driven Culture: With integrated systems, teams are encouraged to utilize data analytics to inform decisions. This culture ensures decisions are not left to gut feelings but are instead grounded in concrete figures and trends.
- Risk Management: Rapid access to comprehensive data helps in identifying risks faster. Should a trend of delayed shipments arise, a company can proactively adjust operations before it snowballs into a bigger issue.
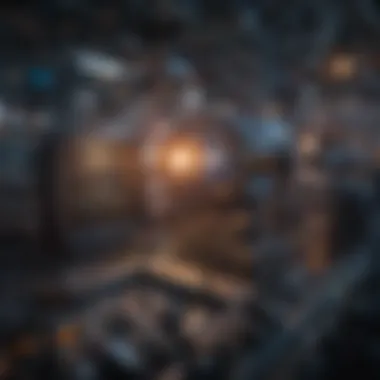
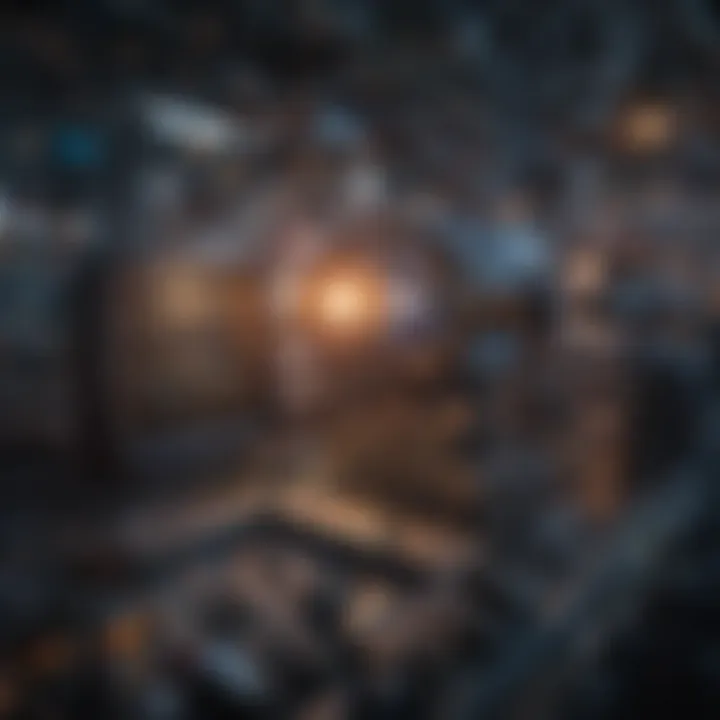
As a consequence, organizations that prioritize system integration see more accurate forecasts and informed strategies, greatly enhancing their competitive edge.
Increased Flexibility and Agility
In the fast-paced world of Industry 4.0, flexibility and agility are not mere buzzwords; they are essential for survival. Effective system integration provides that adaptability. Hereâs how:
- Rapid Response to Market Changes: Companies that can quickly pivot based on consumer demands or shifts in supply chains stand to gain a considerable advantage. Integrated systems facilitate changes without a full system overhaul.
- Scalability: Businesses that experience growth can seamlessly scale operations. For instance, a cloud-based system can effortlessly handle increased data loads as a company expands, unlike a traditional one that may struggle under pressure.
- Collaboration Across Departments: Integrated systems foster an environment where departments work closely together. For example, marketing, production, and sales can align their strategies based on shared performance metrics, driving growth and efficiency.
Ultimately, an organizationâs ability to adapt to change can mean the difference between thriving and merely surviving.
Effective integration is not just about technology; itâs about fostering a culture that embraces data and collaboration.
In this highly competitive industrial environment, embracing the notion of integration is no longer an option; it is a necessity.
Strategies for Successful System Integration
In the throes of Industry 4.0, the spotlight on system integration shines brighter than ever. Companies are challenged to seamlessly connect their processes, technologies, and people to thrive in an increasingly digital world. This integration isnât just a technical requirementâitâs an essential strategy that can determine an organizationâs survival and growth. By adopting effective strategies for successful system integration, businesses can harness advanced technologies, improve operational efficiency, and enhance competitiveness.
Establishing Clear Objectives
Setting the stage begins with establishing clear objectives. Without a roadmap, organizations can lose their direction amidst the rapid changes that Industry 4.0 brings. Clear objectives provide a focus that guides all integration efforts. These objectives should be Specific, Measurable, Achievable, Relevant, and Time-bound (SMART), allowing teams to formulate actionable plans and assess progress effectively.
- Identify Goals: Consider what the true aim of integration is. Is it to enhance productivity, improve data accuracy, or reduce operational costs?
- Set Performance Indicators: Define metrics that will be used to measure success. This could be reduced downtime, improved response times, or customer satisfaction ratings.
- Communicate Vision: Share these goals with stakeholders at all levels, ensuring that everyone understands the âwhyâ behind the integration process.
By having clear objectives, an organization can keep everyone on the same page and minimize misunderstandings that could derail progress.
Utilizing Standardized Protocols
When it comes to system integration, standardization is your friend. Utilizing standardized protocols streamlines communication between disparate systems and devices. Standardized protocols create a common language for machines, allowing them to work together more efficiently. Hereâs why theyâre crucial:
- Interoperability: Standards ensure that new systems can easily work with existing systems, thus reducing compatibility issues.
- Cost Efficiency: Less customization is needed when standards are adhered to, which can lower costs associated with integration efforts.
- Speedier Integration: With clear guidelines to follow, teams can implement integration solutions more rapidly.
Utilizing standards like OPC UA or MQTT helps organizations avoid the pitfalls of proprietary solutions that can restrict adaptation and flexibility. They lay the groundwork for robust, scalable integration workflows that can evolve along with the technology landscape.
Fostering Cross-Functional Collaboration
Last but not least is fostering a culture of cross-functional collaboration. In a world where silos often inhibit efficiency, encouraging diverse teams to work together is absolute key.
Cross-functional collaboration empowers various departments, such as operations, IT, and logistics, to share insights and expertise, enhancing overall integration efforts.
- Create Multi-disciplinary Teams: Bring together individuals from different functions to collaborate on integration projects.
- Encourage Open Communication: Tools and platforms that facilitate real-time sharing of information can break down barriers and foster an environment of collaboration.
- Share Responsibilities: When team members from various departments contribute to the integration strategy, it enhances ownership and accountability.
This approach creates an ecosystem where insights are shared and innovation flourishes, ultimately paving the way for smoother transitions and successful integration.
"Successful integration is as much about the technology as it is about peopleâcultivating teamwork can unlock the true potential of Industry 4.0."
In summary, successful system integration in the age of Industry 4.0 requires strategic foresight. Establishing clear objectives aligns efforts; utilizing standardized protocols simplifies processes; and fostering cross-functional collaboration builds a culture of unity and innovation. By embracing these strategies, organizations can truly leverage the full power of integrated systems, positioning themselves as key players in the evolving industrial landscape.
Emerging Trends in System Integration
In the vast landscape of Industry 4.0, staying on top of emerging trends in system integration is crucial for businesses striving for efficiency and competitiveness. These trends not only showcase technological advancements but also offer opportunities for organizations to reimagine traditional processes. Understanding these elements helps in navigating the complexities of integration, ensuring that companies remain agile and responsive to market demands. Here, we explore three significant trends: the role of artificial intelligence and machine learning, blockchain for enhanced security, and edge computing's influence.
Artificial Intelligence and Machine Learning
The integration of artificial intelligence (AI) and machine learning (ML) into systems is not just a passing fad; itâs a seismic shift that redefines operational capabilities. These technologies enable systems to adapt and optimize processes without human intervention. For instance, imagine a manufacturing plant where machines learn from each production cycle to predict maintenance needs, reducing downtime significantly.
AI and ML foster greater automation and data analysis in real-time, creating an environment where decisions can be data-driven and proactive. Moreover, companies can utilize predictive analytics for demand forecasts, helping them adjust their supply chain strategies more effectively.
Some benefits of incorporating AI and ML include:
- Enhanced predictive maintenance
- Improved resource allocation
- Streamlined workflows
In essence, industries leveraging these technologies are more resilient and can pivot quickly in response to changes in the market.
Blockchain for Enhanced Security
When it comes to safety and transparency in data sharing, blockchain is a frontrunner. Its decentralized nature guarantees that data cannot be easily tampered with, which is vital in system integration. In industries like supply chain, where multiple stakeholders are involved, blockchain provides a shared, immutable ledger that improves trust and accountability.
Consider a logistics company that uses blockchain to track shipments in real-time. Each transactionâwhether itâs the movement of goods or changes in custodyâis recorded, offering all parties visibility and reducing the chance of fraud.
Key advantages include:
- Enhanced data integrity
- Reduced operational costs due to fewer intermediaries
- Increased trust among partners and stakeholders
With greater security, companies can assure customers that their data is safe, paving the way for smoother transactions and relationships.
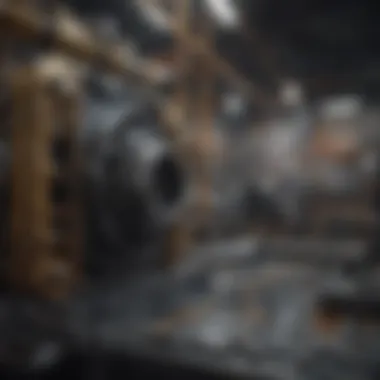
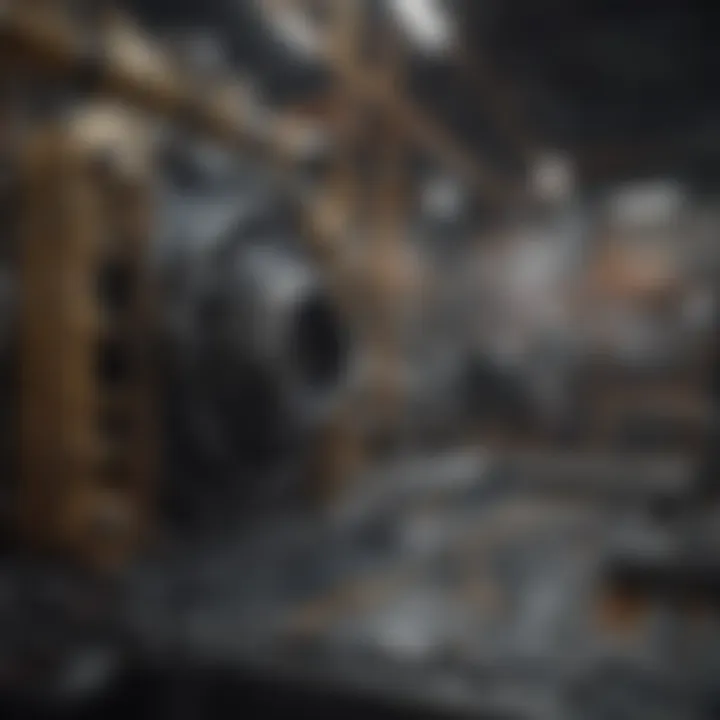
Edge Computing's Role
As the demand for real-time processing grows, edge computing is becoming an essential partner in system integration. Instead of sending all data back to a central server, edge computing processes information closer to its source. This reduces latency for critical applications, a vital factor in environments that rely on rapid decision-making, like autonomous vehicles or smart factories.
Imagine sensors placed on heavy machinery that can analyze their operational data instantly to detect inefficiencies. The data processed at the edge allows immediate responses, potentially preventing costly breakdowns or safety issues.
The merits of edge computing include:
- Reduced bandwidth consumption by processing locally
- Faster response times, leading to improved performance
- Enhanced ability to operate during network outages
Edge computing thus supports the real-time interactivity that modern systems need, further reinforcing the value of system integration in Industry 4.0.
Case Studies of Successful Integration
Case studies are more than just narratives; they serve as vital exemplars of how system integration manifests within different sectors. When we study successful integrations, we glean key insights that can inform future efforts and strategies. They showcase real-life applications of integration practices that have enabled organizations to overcome hurdles and achieve tangible benefits. Such case studies emphasize the versatility of integration across various industries while also highlighting common challenges that can arise.
Understanding these cases allows stakeholdersâfrom students to seasoned professionalsâto grasp the dynamic environment of Industry 4.0 and draw practical lessons applicable to their own contexts.
"The only real mistake is the one from which we learn nothing." - Henry Ford
Manufacturing Sector Examples
The manufacturing sector has dramatically changed, fueled by system integration that enhances efficiency. Take Siemens, for instance. They've embraced a smart manufacturing approach, known as the Digital Factory, which integrates design, production planning, and manufacturing processes into one seamless workflow. By utilizing IoT devices, they can monitor machine performance in real-time, thus allowing for predictive maintenance.
Another noteworthy example is General Electric's (GE) use of Digital Wind Farm technology. Here, multiple wind turbines are integrated into a virtual space, creating a cohesive network that optimizes power production. They use data analytics and machine learning for better wind energy forecasting.
Key Benefits from these examples include:
- Enhanced operational efficiency through data-driven decision-making
- Reduction of downtime with predictive maintenance features
- Improved quality control through integrated processes
Logistics and Supply Chain Integration
In logistics, the integration of systems is paramount for maintaining a competitive edge. Amazon stands out as a giant in this field. Their sophisticated integration of warehousing and delivery systems creates a coherent experience for customers, allowing real-time tracking and rapid fulfillment.
Moreover, logistics companies like DHL are leveraging cloud-based applications to integrate their supply chain operations. Through robust connection across platforms, they can analyze shipping routes, monitor vehicle health, and even use machine learning algorithms for inventory management.
The benefits of such integration are notable:
- Improved visibility of the supply chain, leading to better customer service
- Data-driven analysis to enhance route efficiency and reduce costs
- Increased flexibility in operations to adapt to market changes
Healthcare Systems Integration
Healthcare systems integration is critical as well, as it ultimately impacts patient care. The application of integration is vividly illustrated in how systems like Epic employ an integrated electronic health record (EHR). By combining patient data from various departmentsâsuch as labs, radiology, and physician officesâhealth providers gain comprehensive insights into patients' histories.
Another exemplary case is the integration used by CVS Health, combining pharmacy records with patient health data to provide streamlined care management. This integration lets healthcare professionals coordinate better and improve treatment plans based on real-time data.
Some of the advantages observed from these healthcare integrations are:
- Better patient outcomes driven by comprehensive data access
- Enhanced communication between healthcare professionals
- Reduction in errors and improved safety protocols for patient care
Integrating systems across various sectors illustrates not just the potentials of Industry 4.0, but also reinforces the notion that these innovations can drive efficiency. As we move toward a more interconnected industrial landscape, these case studies offer a roadmap for organizations eager to harness the power of system integration.
The Future of System Integration in Industry 4.
The future of system integration holds immense significance in the tapestry of Industry 4.0. As industries pivot towards more interconnected environments, the ability to integrate diverse systems seamlessly will define competitive advantage. Organizations that embrace this integration stand to not only enhance their operational efficiency but also foster innovation and adaptability in a rapidly changing market landscape. The integration journey will intersect with various technological trends, regulatory frameworks, and workforce dynamics, making it crucial for stakeholders to stay ahead of the curve.
Predicted Technological Advances
Anticipating the technological landscape of system integration offers intriguing possibilities. One can expect advancements in several key areas:
- IoT and Smart Devices: The proliferation of Internet of Things devices will dramatically streamline integration processes. These devices will collect and share data in real-time, allowing systems to work together cohesively.
- AI and Automation: Artificial Intelligence technologies are likely to become increasingly sophisticated. Predictive analytics, driven by AI, can foresee operational bottlenecks, recommending proactive solutions before issues escalate.
- Advanced Analytics: Big Data tools will become more integrated, capable of processing massive datasets to understand trends and operational efficiencies in real-time.
"In the next decade, the fusion of these technologies will create a more responsive, agile industrial landscape, paving the way for unforeseen innovation across sectors."
This milieu of continuous technological evolution compels organizations to adopt adaptive strategies to sustain competitive advantages.
The Role of Policy and Regulation
Policies and regulations will play an essential role in steering the future of system integration. As industries adopt more advanced technologies, the regulatory landscape must evolve to address the accompanying challenges. Here are some considerations:
- Data Privacy and Security: As integration increases connectivity, so do vulnerabilities. Regulations like GDPR in Europe serve as prototypes for how new frameworks must be designed to protect personal and corporate data.
- Standards for Interoperability: Governments and organizations must work together to establish common standards that facilitate the seamless exchange of information across systems, ensuring compatibility in an increasingly diverse technological ecosystem.
- Support for Innovation: Regulatory bodies should also promote innovation through favorable policies that encourage research and development in integration technologies, potentially even providing tax incentives for early adopters.
These policies aim to create an environment where integration serves as a catalyst for growth and sustainability across industries.
Skills and Workforce Development Needs
Equally important is the development of skills and resources within the workforce as we approach the future of system integration. The landscape of job requirements will shift significantly as integration technologies evolve. Key aspects to consider include:
- Upskilling Existing Employees: Organizations must invest in training their current workforce to adapt to new integration tools and methodologies. Specialized training in system architecture, cybersecurity, and data analytics will become paramount.
- Attracting New Talent: The demand for professionals well-versed in emerging technologies will increase. Hence, businesses need to create enticing career paths and educational partnerships with universities to attract young talent.
- Fostering a Culture of Continuous Learning: In a world where technology advances rapidly, fostering a culture of lifelong learning is essential. Encouraging employees to pursue continuous educationâwhether thatâs through formal programs or self-directed learningâwill be particularly beneficial.
In summary, the future of system integration in Industry 4.0 presents several challenges and opportunities. By considering technological advances, regulatory environments, and workforce development, organizations can position themselves to thrive in this digital era.