Innovations in Powder-Based Fusion for Material Science
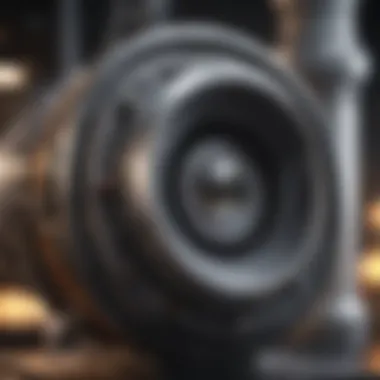
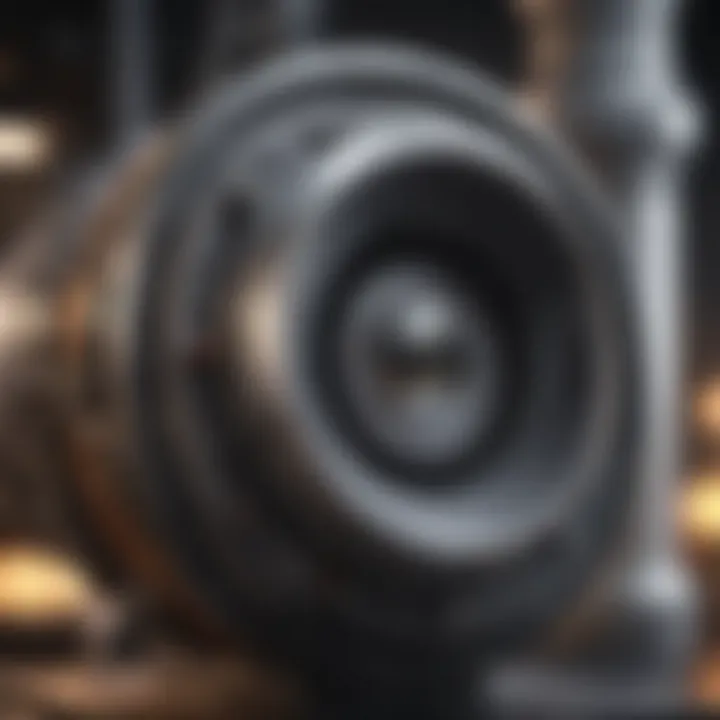
Intro
In the realm of material science, the innovative techniques that have emerged in recent years have shifted paradigms and opened new avenues for exploration. One such technique is powder-based fusion, which is not merely a method, but rather a catalyst pushing the boundaries of what can be created from powdered materials. It's a cornerstone of additive manufacturing that allows complex shapes to come to life in ways once thought impossible.
Through this article, we will traverse the intricate pathways of powder-based fusion, exploring the wealth of methodologies involved, the principles that underpin these processes, and the ever-evolving advancements that are shaping this cutting-edge field. Professionals, educators, and keen enthusiasts will find a rich tapestry woven from various applications that highlight the benefits and the challenges of this technology.
Buzzing with potential, the impact of powder-based fusion is palpable across industries, from healthcare to aerospace. The possibilities are expanding like the universe itself, and understanding this technology is more critical now than ever.
Key Findings
Major Results
This segment showcases the significant outcomes derived from research and application in powder-based fusion technologies. A few key observations include:
- Diverse Applications: Powder-based fusion has significantly expanded its reach across sectors, including automotive, aerospace, and biomedical fields.
- Material Versatility: Various materials, such as polymers, metals, and ceramic powders, can be fused effectively, underlining the technique’s adaptability.
- Enhanced Precision: Increased control over layer thickness and part design culminates in superior accuracy, leading to improved end-use functionality.
In summation, the landscape surrounding powder-based fusion is multifaceted, highlighting how its various methodologies not only serve specialized industries but also push the boundaries of material capabilities.
Discussion of Findings
The advantages highlighted paint a promising picture, yet they don't come without hurdles. Each benefit tends to counterbalance certain difficulties encountered, which might include:
- Cost Implications: The initial investment in equipment and materials can be high, posing a barrier for smaller companies engaging with the technology.
- Process Complexity: The methods involved demand a high level of expertise and precise control. Variability in environmental conditions can impact results negatively.
- Material Limitations: While adaptable, not all materials are compatible with all processes, necessitating ongoing research to advance material capabilities.
As we unravel these complexities, a clear understanding of the potential applications and limitations will become essential to harness the full scope of what powdered fusion can achieve.
Methodology
Research Design
The methodologies investigated here rely on a systematic review of existing literature, case studies, and emerging trends from numerous academic journals and industry reports. This design allows us to create a well-rounded picture of how powder-based fusion technology evolves.
Data Collection Methods
Data for this analysis has been amassed through various channels, such as:
- Peer-Reviewed Articles: In-depth reviews and original research articles provide a wealth of information from established experts in the field.
- Webinars and Conferences: Presentations and discussions held in forums foster knowledge sharing regarding practical applications and emerging trends.
- Industry Reports: Analysis from industry leaders offers insights on market demand, technological advancements, and investment trends.
By employing these methods, we can piece together an in-depth understanding of both past innovations and future trajectories in powder-based fusion.
Understanding Powder-Based Fusion
Understanding powder-based fusion is critical for comprehending modern material science. This technique plays a monumental role, acting as a bridge between traditional manufacturing methods and the innovative capabilities of additive manufacturing. With its ability to create intricate designs that standard processes cannot achieve, powder-based fusion allows for optimal customization and efficiency in production.
Definition and Importance
Powder-based fusion encompasses various additive manufacturing methods that utilize powdered materials as the primary substance. Essentially, it involves the process of fusing these powders using heat or binding agents to construct a solid object layer by layer.
The importance of this technique can be observed in many domains, particularly in aerospace, medical devices, and automotive industries. With demand for lighter, stronger, and more complex components, powder-based fusion meets these needs effectively. Traditional manufacturing often falls short due to limitations in design capabilities, whereas this technique empowers engineers and designers to explore previously inconceivable shapes and structures. Not to mention, it contributes significantly to waste reduction, as it only uses the material needed for production.
In addition, as sustainability becomes a focal point in industry practices, powder-based fusion tends to generate less scrap compared to conventional machining methods. This not only helps in conserving resources but also provides a cost-effective alternative, enhancing its appeal among manufacturers.
Historical Context
Historically, the roots of powder-based fusion can be traced back to the mid-20th century with sintering technology being developed to improve material properties. The introduction of Selective Laser Sintering by Carl Deckard in the 1980s revolutionized this domain, marking the advent of modern additive manufacturing. This breakthrough allowed for the first time the use of lasers to selectively fuse powdered materials, paving the path for a slew of other techniques designed to exploit the advantages of powder-based methods.
Over the years, the progression of technology has led to smoother and faster processes, transitioning from early-stage prototyping to full-scale production. Today, powder-based fusion is recognized as a pivotal element of Industry 4.0, integrating with digital manufacturing techniques. The milestones achieved over these decades reflect the importance of continual innovation, pushing boundaries forward even further with advancements like Binder Jetting and Electron Beam Melting.
"The journey of powder-based fusion is marked by innovation, embodying the creative spirit of material science and engineering."
In this context, understanding powder-based fusion is not just an academic exercise; it is vital for fostering advancements that will define the future of manufacturing.
Merging history with contemporary applications equips students, researchers, and professionals with a solid foundation to engage with this evolving field. Whether it’s fine-tuning production processes or pioneering new materials, the principles of powder-based fusion remain crucial to material science.
Key Techniques in Powder-Based Fusion
The realm of powder-based fusion encompasses a range of techniques pivotal for fabricating complex geometries in material science. These methodologies not only pave the way for innovative designs but also optimize material usage, making production more cost-effective and environmentally sustainable. The effectiveness and precision of these techniques can vary widely, depending on the specific application and the materials involved. Understanding the core techniques is essential for anyone engaged in the fields of additive manufacturing and material engineering. Let's delve into the three key methods that lead the charge in this dynamic area.
Selective Laser Sintering
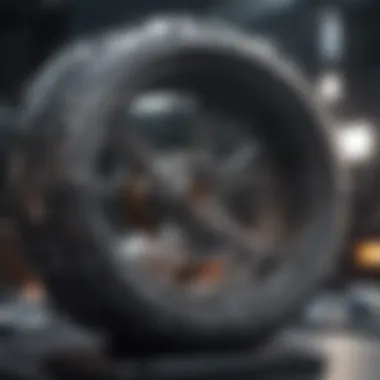
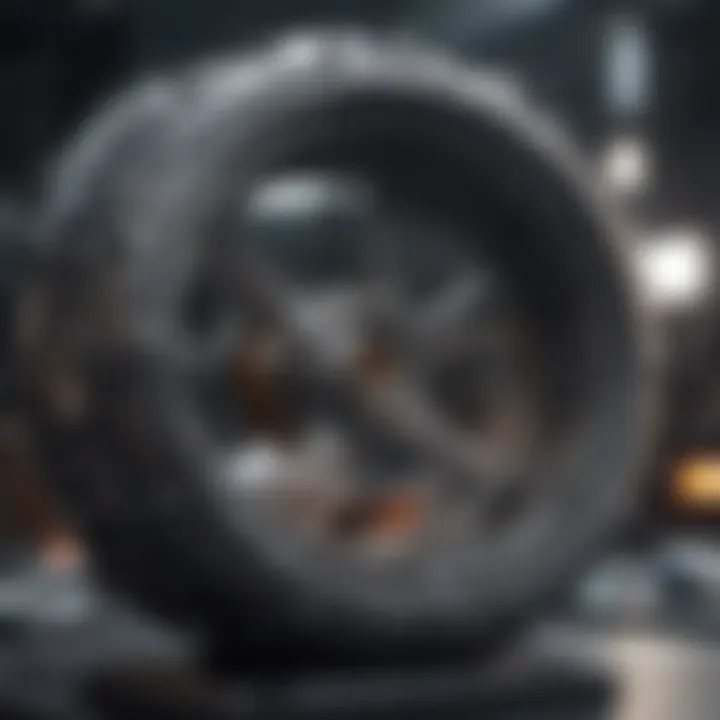
Selective Laser Sintering (SLS) stands out as one of the most widely-adopted techniques in powder-based fusion. In this method, a laser beam selectively fuses powdered material by scanning across the surface according to a digital design. Each layer gets melted and then cooled, solidifying into the desired form. The process allows for high precision and a wide range of materials including plastics and metals.
There are several advantages to using SLS:
- Versatility: It supports various materials and can create complex geometries that traditional manufacturing struggles with.
- Material Efficiency: The unused powder can be recycled for future builds, minimizing waste.
- Strong Parts: The resulting objects often exhibit superior strength characteristics due to the SLS process.
However, factors like precise calibration of the laser and the thermal dynamics of the materials must be monitored closely. Mismanagement can lead to defects, affecting the ultimate performance of the final product.
Electron Beam Melting
Electron Beam Melting (EBM) shares similarities with SLS but utilizes an electron beam instead of a laser. This variant is particularly adept at producing metal components, which are often required in industries like aerospace and medical devices. EBM operates in a vacuum, allowing for high melting temperatures, making it an excellent choice for hard materials that are notoriously difficult to process.
Why is EBM significant?
- High Density: It provides dense, high-quality parts with excellent mechanical properties.
- Industrial Applicability: Particularly valuable in the production of critical aerospace components that demand while maintaining integrity under extreme conditions.
- Speed: The technique tends to be faster than SLS for larger builds due to the energy density of the electron beam.
A key consideration in EBM, however, involves the elimination of residual stresses. Without proper management, it can lead to warping or cracks, which compromises structural integrity during the cooling process.
Binder Jetting
Binder Jetting takes a fundamentally different approach from both SLS and EBM. This technique involves depositing a liquid binding agent onto layers of powder, which helps to bond the particles together. After each layer is completed, an additional layer of powder is applied and the process continues until the object is fully built.
This method has several key benefits:
- Multiple Materials: It allows for the use of several different kinds of powders, including metals, sand, and ceramics.
- Cost-Effective: As it does not rely on thermal energy input to the same extent as laser or electron methodologies, it can be more affordable, especially for larger scale operations.
- Post-Processing Flexibility: The resulting green parts can undergo different post-processing treatments, such as sintering or infiltrating, to enhance their strength and durability.
Despite its advantages, Binder Jetting does have limitations, particularly regarding the strength of the uncured parts. Considerations must be made for subsequent sintering or other processes that will ultimately set the final structure’s properties.
"Understanding these core techniques gives insight into the potential and limitations of powder-based fusion processes. By choosing the right method, professionals in material science can push the boundaries of what’s possible in manufacturing."
In summary, these key techniques in powder-based fusion each offer unique advantages suited to different applications and materials. A solid grasp of how they function and their specific challenges is indispensable for both emerging and seasoned professionals in the rapidly evolving field of material science.
Materials Used in Powder-Based Fusion
The selection of materials in powder-based fusion is a pivotal aspect in the realm of material science. Understanding the specific materials that can be utilized not only broadens the capabilities of additive manufacturing but also impacts the mechanical, thermal, and aesthetic properties of the final products. The key to success in this technique lies in choosing materials that are compatible with the fusion processes, ensuring they can withstand the high temperatures and rapid cooling inherent in these methods.
Notably, every material has its own set of attributes that can influence the performance and application of the fabricated parts. For instance, some metals may yield parts with greater strength, while certain polymers can offer lightweight and flexible characteristics. In this voyage through materials used in powder-based fusion, we shall explore three primary categories: metals and alloys, ceramics, and polymers.
Metals and Alloys
Metals and alloys form the backbone of many applications in powder-based fusion. The most commonly used materials within this category include titanium alloys, stainless steels, and aluminum alloys. Not only do these materials provide exceptional mechanical properties, but they also exhibit good thermal conductivity.
The versatility of these metals makes them popular in industries ranging from aerospace to biomedical engineering. For instance, titanium alloys, renowned for their strength-to-weight ratio, are essential in aircraft components and medical implants. However, processing metals requires a keen understanding of parameters like particle size and distribution, which can greatly influence the final properties of the material.
- Strength: Metals often have high tensile and compressive strength.
- Durability: They tend to withstand extreme conditions better than other materials.
- Weldability: Many metallic powders can be fused, re-welded, or recycled.
"The selection of the right metal alloy forms the crucial crux of successful powder-based applications."
Ceramics
Ceramics are often overlooked in discussions about powder-based manufacturing, yet they hold their own in specialty applications. Their hardness, resistance to high temperatures, and chemical stability allow ceramic parts to perform exceptionally well in demanding environments such as electronic components or high-temperature applications.
The challenge with ceramics lies in their brittleness. When designing components, it's essential to consider how the specific fusion process affects their integrity. Advances in ceramic technologies, such as improved sintering methods, have made it possible to produce fine, intricate shapes that were once deemed impractical.
- Chemical Resistance: Excellent for corrosive environments.
- Thermal Stability: Very high melting points, making them ideal for high-heat applications.
- Insulation Properties: Great electrical insulators, which is vital in electronic parts.
Polymers
Polymers stand out due to their flexibility and lightweight nature. In recent years, material innovations have facilitated the advancement of polymer powders in powder-based fusion processes, such as selective laser sintering. Various polymers, including polyamide and polystyrene, demonstrate distinct properties that can be tailored for specific applications, from automotive components to consumer goods.
Moreover, polymers can be engineered to display a vivid range of colors and textures, offering unique aesthetics alongside functionality. As sustainability continues to take center stage, researchers are looking into biodegradable polymers and recycled materials as alternatives to traditional options.
- Customization: Different colors and textures can be achieved.
- Flexibility: Excellent for applications requiring resilience and bending.
- Lightweight: Reduces the overall weight of the product, enhancing its efficiency.
Principles of Powder-Based Fusion Processes
Understanding the principles behind powder-based fusion processes is crucial for decoding the complex interplay of factors that influence the production of materials in additive manufacturing. These principles govern how energy interacts with the powder, the way materials are shaped, and the quality of the final products. Emphasizing these foundations not only enhances our grasp of existing techniques but also paves the way for innovations that could transform material science.
Thermal Dynamics
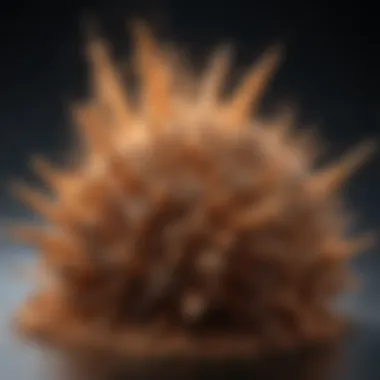
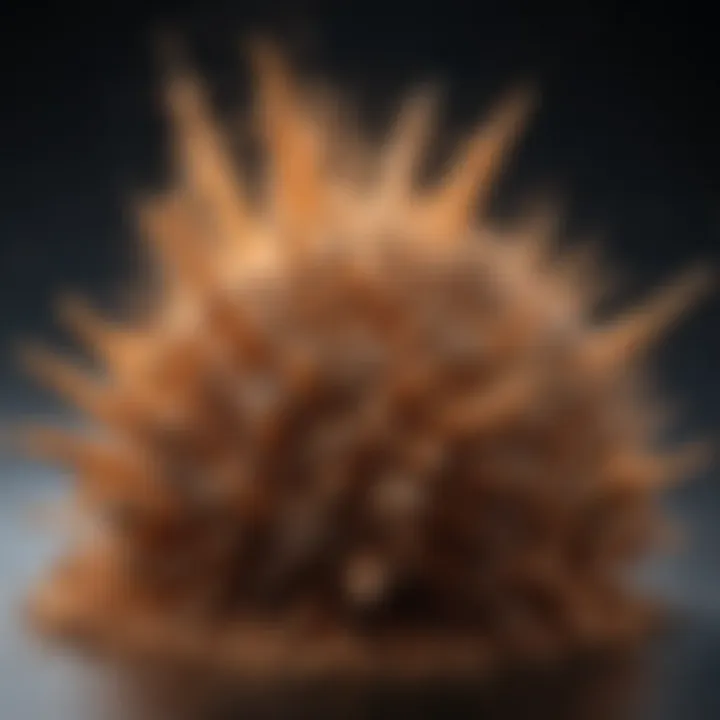
Thermal dynamics play a pivotal role in powder-based fusion, impacting both the efficiency of the manufacturing process and the properties of the final product. At its core, thermal dynamics focuses on the transfer of heat and how it influences the powder behavior during fusion. The heat source, whether a laser or electron beam, dictates how much energy is deposited into the powder bed.
A crucial aspect of this process is the temperature gradient created by the energy source. For instance, when the temperature rises rapidly in localized areas, rapid melting occurs, which is then followed by cooling as the energy source moves. This cycling affects grain structure, density, and mechanical properties of the produced object. Moreover, understanding how various materials respond to heat helps scientists tailor processes for specific applications. As an example, metals like titanium and nickel alloys exhibit distinct thermal behaviors compared to polymers, which can alter the effectiveness of the fusion process.
The interplay between heat and powder is further complicated by the need for controlled environments to prevent oxidization or other chemical reactions. Such considerations can determine long-term performance in applications like aerospace or medical devices, which demand precision engineering.
Powder Behavior and Flow
The behavior and flow characteristics of powders are vital to ensuring a smooth and effective fusion process. Unlike liquids or gases, powders behave uniquely due to their granular nature. Factors like particle size, shape, and distribution significantly influence how they flow and compact under applied stresses.
Key characteristics to consider include:
- Flowability: Refers to how easily powders move and pack together. Poor flow can lead to inconsistencies in layer thickness, compromising structural integrity.
- Cohesion: The tendency of particles to stick together affects the spreadability during the layer deposition phase. Too cohesive and they clump; too loose and they scatter, which is not desirable.
- Angle of Repose: This measures the maximum angle at which a pile of powder can remain stable. Understanding this can help optimize hopper designs for better feeding into the fusion system.
Powder properties also interact with thermal dynamics. For instance, a rougher surface might lead to increased friction during flow, which can affect the melting behavior as well. Furthermore, enhancements in processing techniques continuously reshape our comprehension of flow dynamics. For example, advances in powder treatments, such as spherical shaping and surface coating, have made significant differences in suitable applications, especially in intricate designs found in aerospace or automotive components.
Applications of Powder-Based Fusion
In the realm of material science, the applications of powder-based fusion occupy a significant space. This innovative technology substantially broadens the possibilities for creating complex components in numerous industries. When examining this field, it becomes evident that several sectors are reaping the benefits of these techniques, leading to enhancements in efficiency, performance, and design.
Aerospace Engineering
In aerospace engineering, the demand for lightweight yet robust materials is paramount. Powder-based fusion processes enable engineers to fabricate intricate designs that are not feasible with traditional methods. For example, the ability to generate lattice structures results in components that are both strong and lightweight. Parts such as fuel nozzles, brackets, and even integrated sensors can be designed without the constraints of conventional machining. This leads not only to a reduction in material waste but also improves the overall aerodynamic efficiency of aircraft.
Additionally, the rapid prototyping capabilities of these technologies facilitate faster testing and iteration of designs. As a result, aerospace companies can respond swiftly to evolving specifications and regulatory standards, crucial in a field frequently scrutinized for safety and performance. Striving for perfection in this sector pushes powder-based fusion techniques into continuous evolution to meet stringent requirements.
Medical Devices
The medical device sector is another area experiencing a paradigm shift thanks to powder-based fusion. The customization and complexity achievable with these methods allow for the production of tailored implants and surgical instruments. For instance, titanium implants can be crafted to match a patient’s anatomy precisely, enhancing comfort and functionality. This approach not only improves fit but can also foster better healing outcomes and integration with surrounding tissues. When it comes to prosthetics, the technology has been game-changing. Units that fit each patient perfectly can now be produced using additive manufacturing, improving the quality of life for many.
Moreover, the possibility of integrating multiple functionalities into a single device is an unparalleled advantage in this sector. Devices that combine sensing technologies with prosthetic functions can lead to advancements unheard of in the past. The ongoing development of biocompatible materials is paving the way for future innovations, which assures a bright horizon for medical practitioners and patients alike.
Automotive Industry
In the automotive arena, powder-based fusion proves itself essential in addressing the complexities of modern vehicle design. With the industry's shift toward electric and autonomous vehicles, weight reduction and performance efficiency are crucial. Manufacturers are tapping into these technologies to produce intricate geometries for components like heat exchangers, throttle bodies, and even advanced powertrain elements. This results in considerable improvements in fuel efficiency and reduced emissions, aligning with global sustainability goals.
The integration of advanced materials through powder-based techniques also opens avenues for experimenting with new alloys and composite materials that enhance performance while keeping costs manageable. Automotive firms are increasingly adopting these innovations as they strive to outpace competitors in a fast-evolving market. By utilizing powder-based fusion methods, they are not only optimizing production timelines but also elevating their design capabilities to new heights.
"The potential of powder-based fusion in various applications underscores its impact across numerous sectors, creating efficient, customizable solutions tailored to modern demands."
Overall, as we continue to witness advancements in powder-based fusion technologies, these applications will certainly expand further, reaffirming their significance in not just engineering sectors but also in daily life.
Advantages of Powder-Based Fusion
The advancements in powder-based fusion technology present several noteworthy advantages that distinguish it from traditional material processing methods. These benefits are not just theoretical; they impact real-world applications in a variety of fields, providing unique solutions to complex problems. Understanding these advantages is crucial for anyone involved in material science, engineering, or production technologies. Let’s break down the major perks of powder-based fusion.
Design Freedom
One of the most significant advantages of powder-based fusion is the design freedom it offers. This technology allows for the creation of intricate and customized geometries that traditional manufacturing methods cannot achieve.
For example, designers can implement features like complex lattice structures in aerospace components which provide high strength-to-weight ratios. This level of complexity isn't just for aesthetic purposes; it's a game changer in functional engineering. Moreover, designers can iterate rapidly, testing different configurations without the need to build new molds or tooling. This flexibility leads to innovation and design exploration that can surpass conventional constraints.
Material Efficiency
Another compelling benefit of powder-based fusion is its material efficiency. Conventional subtractive manufacturing processes tend to generate a significant amount of waste, as material is cut away from larger blocks. In contrast, powder-based fusion builds objects layer by layer, utilizing only the material needed for the part itself. This not only reduces waste but also lowers material costs over time.
Additionally, with advances in recycling technologies, unused or leftover powder can often be reclaimed and reused in subsequent builds. This sustainable aspect enhances the environmental profile of powder-based fusion, aligning with the growing emphasis on sustainability in manufacturing.
Rapid Prototyping
The rapid prototyping capability provided by powder-based fusion is another crucial advantage. This can significantly shorten time-to-market for new products. Instead of extensive and costly iterative processes, companies can quickly produce prototype parts for testing, thereby streamlining development cycles.
In industries like automotive and medical devices, where testing and validation are paramount, having the ability to produce a working prototype in a matter of hours or days can lead to substantial competitive advantage. The agility in product development not only enhances innovation but also enables businesses to respond swiftly to market demands and changing consumer preferences.
"The key to staying ahead in today's market is adaptability, and powder-based fusion leads the way in providing such flexibility."
Challenges in Powder-Based Fusion
The realm of powder-based fusion, while brimming with innovations and potential, is not without its hurdles. These challenges can influence everything from the reliability of the final product to the overall cost-effectiveness of the manufacturing process. Understanding the intricacies of these obstacles can not only help in navigating them but also point the way to future enhancements in the field.
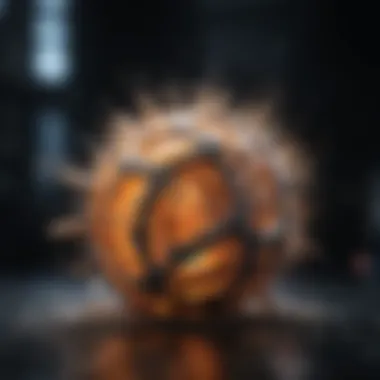
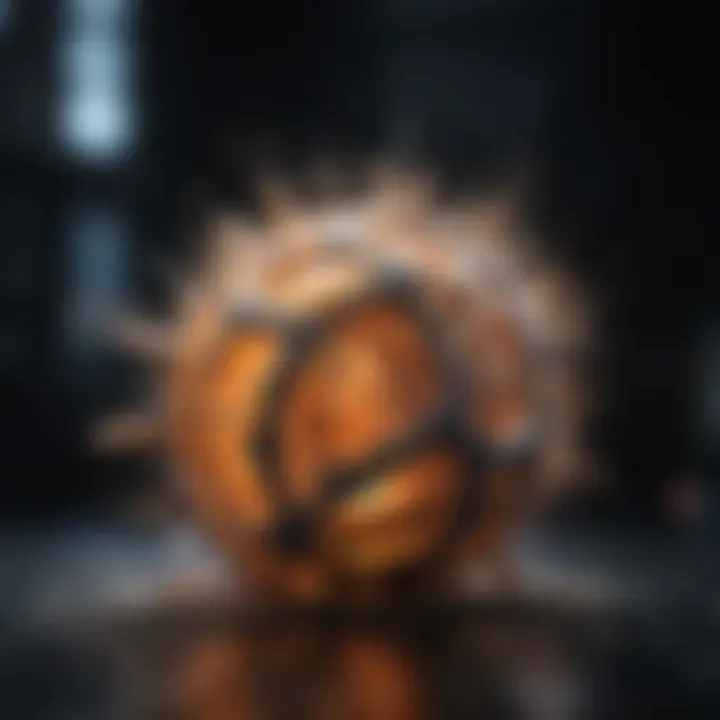
Cost Considerations
Cost remains a significant factor in the implementation of powder-based fusion techniques. The initial investment in machinery and materials can be daunting, especially for smaller firms or those just breaking into the market. Machinery such as selective laser sintering systems or electron beam melting devices comes with a hefty price tag. Additionally, the powders used in these processes, whether metal or polymer, often carry a high cost. This makes budgeting for production runs tricky since economic viability frequently hinges on achieving high volumes of output.
Another layer to this financial puzzle is the operational cost. Maintenance of high-tech equipment, necessary safety measures, and energy consumption can all add up quickly. Over time, the real challenge is to strike a balance between quality and cost. If an organization can master this balance, it can gain a competitive edge in a space that’s rapidly evolving.
Process Control and Quality Assurance
Ensuring quality in powder-based fusion is akin to walking a tightrope; it requires exceptional balance and precision. The fusion process involves multiple variables like temperature, time, and powder characteristics. Small deviations in any of these can lead to defects in the end product. For instance, temperature fluctuations during sintering can result in inconsistent mechanical properties, compromising the integrity of the final part.
To combat these challenges, many manufacturers are turning to advanced monitoring systems, using real-time data to adjust the process dynamically. However, deploying such systems also increases complexity and costs, leading many firms to grapple with the question: how much control is necessary to ensure quality without overstepping into excessive spending?
"Quality assurance in powder-based fusion is about maintaining the delicate equilibrium of various factors to yield reliable results."
Environmental Impact
As we advance into an era increasingly focused on sustainability, the environmental ramifications of powder-based fusion cannot be overlooked. While additive manufacturing techniques such as these can minimize waste compared to traditional manufacturing processes, they can still pose serious ecological concerns. For example, the extraction and production of metal powders involve energy-intensive methods that can contribute to a higher carbon footprint than one might initially expect.
Moreover, the use of certain materials can lead to hazardous waste, requiring responsible disposal methods that often add another layer to the cost considerations. As industries continue to push for greener solutions, finding materials and methods that lower the environmental toll is essential.
Employing recycling methods for discarded powders and utilizing more sustainable materials can mitigate some of these challenges, yet the industry is still figuring out the best approaches to implement these changes effectively.
In summary, while powder-based fusion offers an extraordinary toolkit for modern manufacturing, the obstacles of cost, quality control, and environmental impact loom large. A thoughtful exploration of these challenges reveals not just problems but also potential avenues for improvement in a dynamic field.
Future Trends in Powder-Based Fusion
The future of powder-based fusion is rich with potential, driven by the relentless quest for innovation in material science. This section takes a closer look at the trends not only transforming this technology but setting the stage for a new frontier in manufacturing and design.
Advancements in Material Science
Material science is experiencing a renaissance, particularly where powder-based fusion is involved. Researchers are now developing novel powder compositions tailored for specific applications—think metals that withstand extreme environments or polymers that can be molded into intricate shapes with high strength.
The trend suggests a move towards more sophisticated materials that are engineered at the molecular level. This includes:
- Functionally Graded Materials: These materials can exhibit varying properties over different sections, enabling designs that require different functionalities across a single component.
- Nanostructured Powders: These powders promise enhanced mechanical properties and can lead to lighter and stronger parts, meeting the demands of sectors such as aerospace and automotive.
As the materials available for powder-based fusion evolve, so does the capability to create complex, intricate designs that were previously unfathomable. This advancement is not just about adding to the arsenal of materials but fundamentally altering the way products can be conceived and produced.
Integration with AI Technologies
Integrating artificial intelligence into powder-based fusion practices opens a new chapter of possibilities. AI can drastically improve the design and production processes by:
- Predictive Analytics: AI can analyze large datasets to predict how certain powders will behave under different conditions, making for a more reliable and efficient production process.
- Design Optimization: Machine learning algorithms can create optimized designs faster than human counterparts by testing various configurations digitally and selecting the best fit for performance and material usage.
Such innovations offer not only savings in time and resources but also increase the probability of successful outcomes in the print cycle. Adopting AI technologies might provide a way for smaller enterprises to step up to the plate, creating more equal opportunities in the industry.
Sustainability Initiatives
With increasing global attention on sustainability, powder-based fusion technologies are being reevaluated through this lens. Future trends are likely to focus on eco-friendliness, pushing the development of sustainable practices in production.
Several avenues are emerging:
- Recyclable Powders: Innovations are underway to create powder materials that can be recovered and reused multiple times without loss of properties, which can significantly reduce waste.
- Energy Efficiency: Techniques and machinery are being developed to minimize energy consumption during the printing process, thereby slashing carbon footprints.
Organizations are making conscious efforts to adopt practices that don’t just support their bottom line but also contribute positively to the planet. The drive for sustainability isn't just a nice-to-have; it’s becoming a key condition for success in modern material science.
The future promises a powder-based fusion landscape that is smarter, stronger, and significantly more sustainable than ever before.
The End
The exploration of powder-based fusion technologies is becoming increasingly significant within material science. As industries seek innovative techniques for creating complex parts with enhanced performance, the role of these methods continues to evolve. This article underscores the importance of understanding the direct implications of powder fusion on not just manufacturing processes, but also on global sustainability efforts and economic viability.
Summary of Key Insights
In reviewing the advancements and principles of powder-based fusion, several key insights emerge:
- Diverse Techniques: Mastery of methods like Selective Laser Sintering and Electron Beam Melting has opened new avenues for creating precise components tailored to specific industry needs.
- Material Versatility: Various materials, namely metals, ceramics, and polymers, enhance the application scope across sectors including aerospace, medicine, and automotive.
- Benefits vs. Challenges: While the benefits of design freedom, material efficiency, and rapid prototyping are clear, challenges such as upfront costs and environmental considerations cannot be overlooked.
These insights form a rich tapestry of knowledge that is crucial for further development in this area, particularly among students and professionals who are shaping the future of material science.
The Future of Powder-Based Fusion
As we gaze into the horizon of powder-based fusion, a few trends are markedly pressing:
- Material Science Advancements: Ongoing research will likely unveil new powder strategies and materials which can further increase the efficiency and sustainability of productions.
- AI Integration: The fusion of artificial intelligence with traditional methods may yield smarter production lines, helping to streamline processes and reduce waste.
- Sustainability Initiatives: With increasing focus on ecological impacts, future innovations will need to address not only performance but also the environmental footprint of production methods.
In summary, the future of powder-based fusion appears bright but requires careful navigation through intricate challenges. Engaging with these dynamics prior to implementation will equip researchers, educators, and industry professionals to contribute effectively to this ever-evolving field.