Understanding Oil-Lubricated Systems: Mechanisms & Benefits
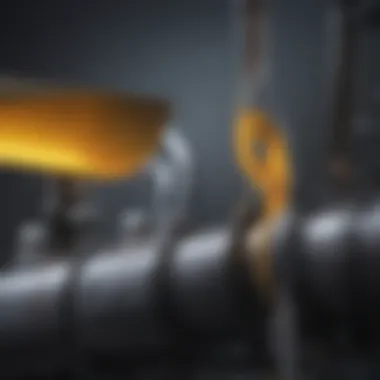
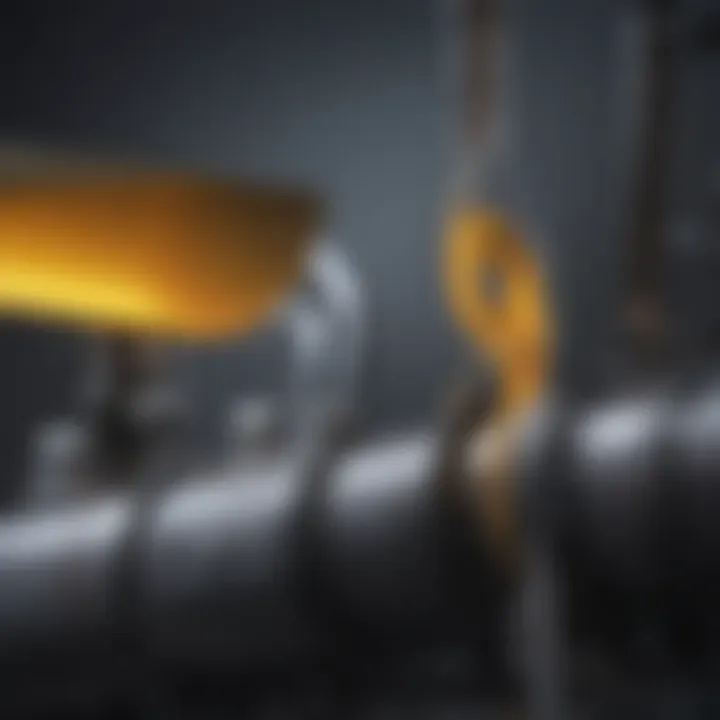
Intro
Oil-lubricated systems play a crucial role in several industries, ranging from automotive to manufacturing. This article explores their operational framework, advantages, maintenance techniques, and environmental considerations. Understanding these systems is not only essential for engineers and technicians but also for researchers who seek to innovate and improve efficiency. The increasing complexity of machinery demands an in-depth knowledge of lubrication systems to ensure longevity and reliability.
Key Findings
Major Results
- Enhanced Performance: Oil-lubricated systems significantly enhance the performance of mechanical components by reducing friction. This leads to improved efficiency and lower energy consumption.
- Longevity of Equipment: Regular use of suitable lubricants can extend the lifespan of machinery. This is particularly important in heavy industries where downtime results in substantial financial losses.
- Temperature Regulation: Oil helps in dissipation of heat generated by moving parts. This temperature control is vital for maintaining optimal functioning.
- Diverse Applications: These systems are versatile, finding applications in various fields like automotive, aerospace, and heavy machinery. Each sector leverages the benefits of oil lubrication differently.
Discussion of Findings
The exploration of oil-lubricated systems reveals a multifaceted approach towards maintaining machinery. The interplay of lubrication type, application method, and maintenance routine requires careful consideration. For instance, synthetic oils tend to offer better heat resistance and longevity compared to traditional oils. Furthermore, different industries may prefer specific formulations depending on factors like operating temperature and load conditions. Cost analysis also plays a significant role in the selection process.
Methodology
Research Design
This overview employs a systematic approach to gather information on oil-lubricated systems. This involves reviewing existing literature, industry reports, and case studies. Primary research is conducted through interviews with professionals in the field, providing firsthand insights on current practices.
Data Collection Methods
Data was collected via various methods, including:
- Literature Review: Academic papers and technical documents provided foundational knowledge of lubrication systems.
- Surveys: Feedback from industry professionals on their lubrication practices and challenges faced.
- Interviews: Direct discussions with engineers and maintenance experts yielded practical insights into the workings and issues of oil-lubricated systems.
Understanding the specific requirements and limitations of oil-lubricated systems is essential for optimizing their performance and minimizing negative impacts.
The End
Oil-lubricated systems are integral to many mechanical applications. A detailed examination reveals their benefits, challenges, and practical implications. The ongoing research in this field seeks to optimize lubrication types, improve maintenance practices, and address environmental concerns. A well-informed approach is essential to leverage the advantages while mitigating potential drawbacks.
Understanding Oil Lubrication
Oil lubrication is a cornerstone of modern engineering and maintenance practices across many industries. Its significance cannot be overstated, as proper lubrication is vital for optimizing the performance and longevity of machines and mechanical systems. At its core, oil lubrication reduces friction between moving parts, minimizing wear and tear, which in turn contributes to increased reliability and efficiency.
The Science of Lubrication
To grasp the concept of oil lubrication, it's important to understand the underlying science. Lubrication involves the application of a substance—oil, in most cases, to create a film between surfaces that are in relative motion. This film acts as a barrier that decreases direct contact, effectively reducing friction. When friction is reduced, heat generation decreases, resulting in cooler operating temperatures.
A good lubricant must have specific properties: viscosity, thermal stability, and compatibility with materials. Viscosity is the measure of a fluid's resistance to flow. Higher viscosity oils are better for applications with high temperatures and pressures, while lower viscosity oils are suitable for less demanding scenarios.
Furthermore, the thermal stability of an oil ensures that it maintains its properties even under extreme conditions. This stability is crucial in preventing oil breakdown, which can lead to harmful deposits and ineffective lubrication over time. Understanding these principles allows engineers and technicians to select appropriate lubricants tailored to specific applications.
Mechanisms of Oil Lubrication
The mechanisms of oil lubrication are multifaceted, involving various processes that work together to provide optimal performance. The two primary mechanisms are hydrodynamic lubrication and boundary lubrication.
In hydrodynamic lubrication, a full fluid film separates the moving surfaces. This occurs when the load on the lubricant is exceeded by the pressure generated by the motion of the surfaces. As the viscosity and flow characteristics of the oil create a stable layer, wear and friction are significantly reduced.
In contrast, boundary lubrication occurs when the lubricant film is insufficient to prevent contact. In this state, additives present in the oil form a protective layer on the surface, reducing wear. This situation is more common during startup or shutdown conditions, where surfaces may come into direct contact before sufficient oil film is established.
"Understanding the right type of lubrication is essential for machine efficiency and reliability."
Knowledge of these lubrication mechanisms informs not only the selection of lubricants but also maintenance practices. For instance, using the right oil viscosity can prevent premature machine failures attributable to inadequate lubrication. This understanding ultimately leads to better decision-making in maintenance protocols, enhancing the life cycle of equipment.
Types of Oil Lubricants
Understanding the various types of oil lubricants is essential in the context of oil-lubricated systems. Each type offers unique properties and advantages that can impact performance, efficiency, and environmental considerations. The selection of the right lubricant is crucial for the long-term operation of machinery across industries. The major categories include mineral oils, synthetic oils, and biodegradable oils, each with distinct characteristics and applications.

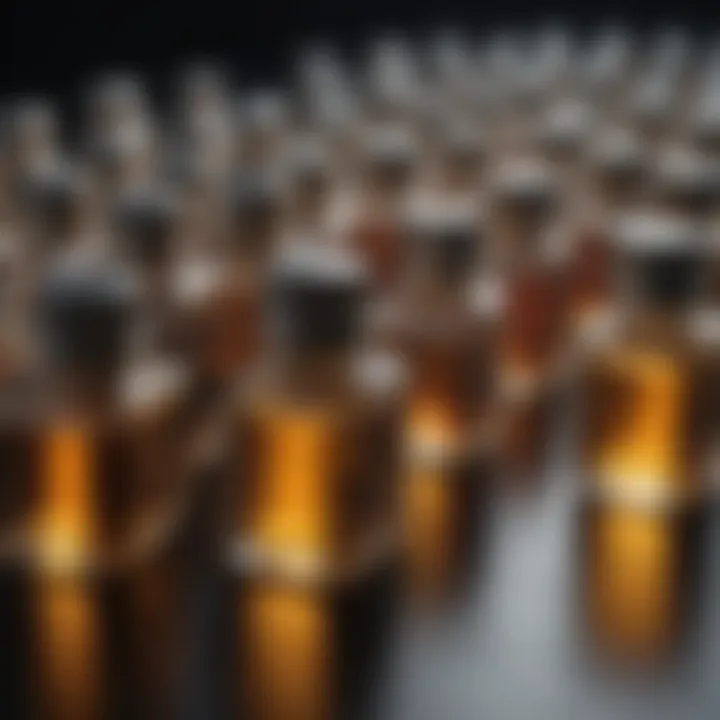
Mineral Oils
Mineral oils are derived from the refining of crude oil. They have been in use for a long time and are a common choice for many lubrication applications. These oils generally consist of a blend of paraffinic and naphthenic hydrocarbons, which give them favorable properties such as good lubricating ability and cost-effectiveness.
Key Benefits of Mineral Oils:
- Accessibility: Mineral oils are widely available and cost-effective compared to other types of lubricants.
- Versatile Applications: Suitable for various applications, including automotive engines and industrial machinery.
- Good Lubrication: Provides effective lubrication, which reduces friction and wear in mechanical systems.
One consideration when using mineral oils is their environmental impact. They are derived from non-renewable resources, and their degradation over time can lead to pollution. Additionally, while mineral oils often perform well under standard conditions, they may not offer the same performance under extreme temperatures compared to synthetic oils.
Synthetic Oils
Synthetic oils are engineered products made from chemically modified petroleum components or entirely from synthetic compounds. They exhibit superior performance characteristics, particularly in extreme conditions.
Advantages of Synthetic Oils:
- Enhanced Stability: Synthetic oils resist breakdown at high temperatures and provide better performance in cold climates.
- Improved Lubrication: They often have a lower viscosity, enhancing the lubricant's ability to flow and coat moving parts.
- Longer Service Life: Due to their stability, synthetic oils typically require less frequent changes and perform well over extended periods.
These oils can be more expensive than mineral oils, but their operational efficiency and longevity can justify the higher initial investment. They are commonly used in high-stress environments, such as aerospace and high-performance automotive applications.
Biodegradable Oils
Biodegradable oils are designed to minimize environmental impact. These lubricants are usually derived from renewable sources and can break down naturally, reducing pollution risks associated with conventional oils.
Benefits of Biodegradable Oils:
- Eco-Friendly: Their natural decomposition helps lower the risk of environmental contamination, making them suitable for applications in sensitive ecosystems.
- Renewable Resources: Often produced from vegetable oils or other renewable materials, contributing to sustainable practices.
- Effective Lubrication: Despite being environmentally friendly, they still provide effective lubrication and protect against wear.
However, biodegradable oils may not always match the performance of synthetic oils in extreme conditions. Therefore, it is essential to evaluate the specific application environment when choosing this lubricant type.
In summary, the selection of the appropriate oil lubricant is critical. Each type of oil varies in composition, performance under different conditions, and impact on the environment.
Understanding these differences allows professionals to make informed choices that align with operational needs and sustainability goals.
Applications of Oil Lubrication
Oil lubrication is a fundamental aspect of various industries, providing vital benefits and addressing specific needs across multiple applications. The reliance on oil-lubricated systems is not only a matter of performance but also significantly influences operational efficiency, safety, and longevity of equipment. Each sector employs tailored approaches to leverage oil lubricant characteristics, ensuring optimal functionality. Understanding the diverse applications of oil lubrication is crucial for professionals aiming to enhance productivity and reduce operational costs.
Automotive Industry
In the automotive sector, oil lubrication plays a key role in maintaining engine performance and reliability. Engine oil reduces friction between moving parts, which helps to increase fuel efficiency and reduce wear. Moreover, modern vehicles use specialized oils that are engineered to meet specific requirements, such as high-temperature stability and improved oxidation resistance.
Regular oil changes are essential in this industry. They prevent the buildup of contaminants that can lead to engine damage. Different types of oil are used based on vehicle design, climate conditions, and manufacturer specifications. This attention to lubrication directly affects vehicle lifespan and resale value.
Industrial Machinery
Industrial machinery relies heavily on oil lubrication to function effectively. In factories and manufacturing plants, machines operate under high stress and load. An appropriate oil lubricant minimizes friction and prevents overheating, which is vital in preventing costly breakdowns. Oil also serves to carry away heat generated from the operation, contributing to component longevity.
Regular monitoring of oil conditions, using techniques such as viscosity checks and contaminant analysis, helps ensure that machinery operates at peak efficiency. Industrial oils can come in various formulations designed for specific environments.
Aerospace Applications
In aerospace, oil lubrication is essential for both safety and performance. Aircraft engines operate under extreme conditions, where effective lubrication can mean the difference between success and failure. The oil used in aviation must have high thermal stability and be resistant to breakdown over time. Special additives further enhance the oil's performance under pressure.
Moreover, oil systems in aircraft are subject to strict regulations due to safety concerns. Maintenance practices in aerospace ensure that oil integrity is checked frequently. The implications of oil performance directly affect fuel efficiency and operational safety, making this an area of intense focus.
Marine Equipment
Marine equipment, such as ship engines and gear systems, also depends heavily on oil lubrication. The harsh marine environment necessitates oils that can withstand saltwater exposure and corrosive conditions. Marine oils are formulated to provide not only lubrication but also protection against corrosion and rust, which are critical in prolonging equipment life.
In these applications, regular maintenance, including oil changes and filtration checks, is of utmost importance. It helps in optimizing performance while minimizing costly repairs or operational downtime. The implications in the marine sector of oil lubrication extend to environmental considerations as well, highlighting the need for proper waste disposal and management of oil spills.
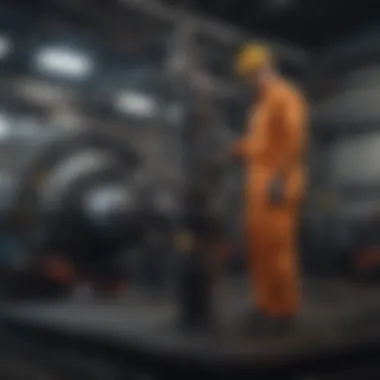
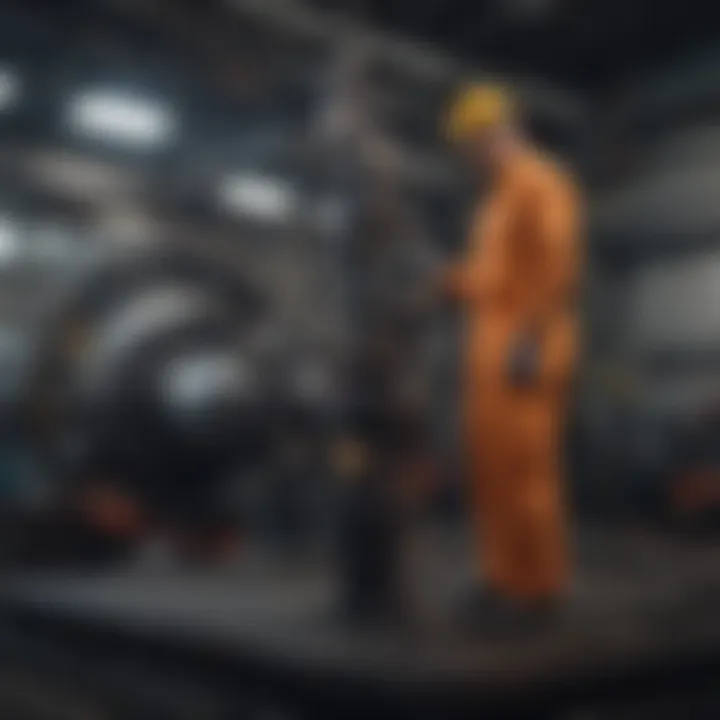
Benefits of Oil Lubrication
Oil lubrication plays a crucial role in mechanical systems. Understanding its benefits is essential for professionals and researchers in various fields. The key advantages of oil lubrication include a significant reduction of friction between moving parts, effective heat dissipation, enhanced resistance to corrosion, and increased longevity of components. These benefits not only improve the performance of machinery but also reduce maintenance costs and failures.
Reduction of Friction
Friction is a natural consequence of two surfaces sliding against each other. In machinery, high friction can lead to wear and tear, resulting in inefficiency and potential failure. Oil lubrication creates a thin film between these surfaces, minimizing direct contact. This film prevents the surfaces from grinding against each other, which leads to smoother operation. As a result, oil lubrication can decrease energy consumption, which directly contributes to operational efficiency.
Heat Dissipation
As machinery operates, it generates heat due to friction, which could lead to overheating and eventual breakdown. Oil plays a vital role in heat dissipation. It absorbs heat generated from friction, transferring it away from critical components. Additionally, oil circulation within the system helps maintain a constant temperature. Proper heat management not only prolongs equipment life but also enhances overall system reliability.
Corrosion Resistance
Corrosion is a common issue in mechanical systems that can compromise their functionality. Oil lubricants often contain additives that provide a protective layer to metal surfaces. This barrier prevents moisture and contaminants from causing rust and degradation. Using oil lubrication thus contributes to better durability of parts in hostile environments. Systems subjected to extreme conditions, such as those found in marine or industrial applications, particularly benefit from this protective quality.
Component Longevity
All the benefits mentioned come together to support one main outcome: extended component longevity. Reduced friction, effective heat management, and corrosion resistance work in harmony to lower the rate of wear. This means machinery can operate longer without frequent replacements or repairs. Longer-lasting components lead to reduced downtime and maintenance costs, which is beneficial for both manufacturers and operators alike.
In summary, the benefits of oil lubrication are vital for machinery efficiency, safety, and longevity. Understanding these aspects is essential for making informed decisions about lubrication practices.
Challenges in Oil Lubrication
Oil lubrication plays a crucial role in maintaining the efficiency and longevity of machines and systems. However, it is not without its challenges. Understanding these challenges is necessary for addressing issues that may arise over time, enhancing operational effectiveness, and aiming for improvements in technology. This section explores several significant challenges related to oil lubrication, emphasizing the implications these challenges have across various applications.
Environmental Concerns
One of the foremost challenges regarding oil lubrication involves environmental issues. Many traditional oils, especially mineral oils, can be detrimental when they enter ecosystems. Spills, leaks, and incorrect disposal practices often lead to soil and water contamination. The petroleum-based nature of many lubricants contributes to this risk. Emission of volatiles from oils can also harm air quality.
Industry regulations are tightening concerning permissible levels of oil contaminants in industrial discharges. Companies must navigate these environmental regulations and focus on sustainable practices to mitigate their impact.
- Many manufacturers are exploring biodegradable oils that can break down more safely in nature.
- The implementation of secondary containment measures can help prevent pollution from occurring.
Ultimately, careful planning in oil usage embodies a shift toward sustainable practices. Enhancing environmental awareness creates a pathway for safer lubrication methods in various sectors.
Degradation Over Time
Degradation is another pressing concern in oil lubrication systems. Over time, oil can lose its effectiveness due to physical and chemical changes at the molecular level. Factors such as high temperatures, exposure to air, and contamination can accelerate degradation.
The consequences of oil degradation can include:
- Increased friction and wear of machine components.
- Formation of sludge and varnish that can clog filters and passages.
- Reduction in the lubricant's ability to resist oxidation.
Regular monitoring and scheduling of oil changes become paramount. Employing advanced filtration systems can help. Additionally, implementing condition-based maintenance practices assists in identifying when oil degradation has reached critical levels.
Compatibility Issues
Compatibility between different types of lubricants and machinery components remains a critical factor. When switching oils or mixing products, one may introduce unforeseen challenges. Not all oils are compatible with each other, and mixing can lead to chemical reactions that may alter performance.
- It is essential to verify the lubricant compatibility before use.
- Conducting tests and using specialized lubricants can enhance reliability.
Misunderstanding compatibility can result in operational failures and increased maintenance costs. For industries where downtime is expensive, ensuring proper lubricant selection is vital.
Maintenance Practices
In oil-lubricated systems, maintenance practices are crucial for ensuring optimal performance and longevity. These practices involve regular attention to various components of the lubrication system to prevent issues that can arise from wear, contamination, and oil degradation. Proper maintenance can significantly reduce costs associated with equipment failure and downtime while improving overall efficiency. Understanding the key elements of maintenance practices helps technicians and engineers optimize their operations and extend the life of their machinery.
Regular Oil Changes
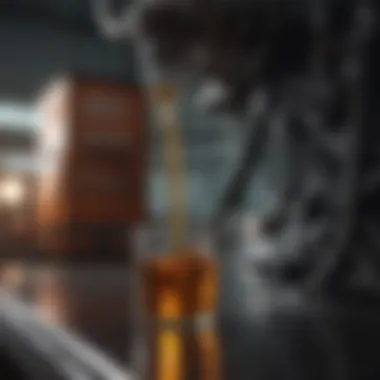

Regular oil changes are vital in any oil lubrication system. Over time, oil can become contaminated with dirt, metal particles, and moisture. This degradation can lead to reduced lubrication effectiveness, increased friction, and ultimately, damage to the machinery. Therefore, it is essential to follow a schedule for changing oil, which usually varies by manufacturer recommendations and the specific application of the equipment.
Benefits of regular oil changes include:
- Enhanced mechanical performance
- Lower operational costs due to reduced wear
- Prevention of oil-related failures
To determine the appropriate intervals for oil changes, factors such as operating conditions, type of lubricant, and the specific machinery's requirements must be considered. Monitoring the oil quality through physical and chemical tests can also provide valuable insight into whether an oil change is necessary.
Filtration Systems
Filtration systems play a crucial role in maintaining the integrity of oil in lubrication systems. They remove impurities such as dirt, debris, and metal shavings that accumulate over time. A good filtration system can prevent these contaminants from circulating in the system, thereby protecting components from wear and tear.
Some key points regarding filtration include:
- Types of filters: There are various types of filters including mechanical, magnetic, and electrostatic, each serving different purposes based on the needs of the system.
- Filter replacement: Regularly replacing filters is critical. Clogged filters can restrict oil flow and reduce the effectiveness of the lubrication.
- Monitoring performance: Regularly checking filter efficiency can identify potential problems early. A drop in pressure or oil flow can indicate a need for filter replacement or system cleaning.
Monitoring Techniques
Monitoring techniques are essential for assessing the overall health of an oil-lubricated system. Various methods can be employed to gather data on oil condition and system performance, including sensors that measure viscosity, temperature, and particle count.
Some effective techniques include:
- Wear debris analysis: This technique involves inspecting the oil for wear particles, thus detecting mechanical problems before they escalate.
- Viscosity measurement: The viscosity of oil is a critical parameter. Monitoring this helps in assessing the lubricant's performance and suitability for the application.
- Oil analysis: Routine oil analysis can provide insight into the degradation of oil and can indicate when a change is necessary.
Maintaining proper monitoring routines can significantly enhance the reliability of lubrication systems and reduce unexpected failures.
Future of Oil Lubrication
The future of oil lubrication is essential to consider, especially in today’s rapidly changing technological environment. Advances in lubricant technology not only aim to improve performance but also to address sustainability concerns. As industries strive for better efficiency, there is a shift in focus toward eco-friendly alternatives and innovations that can help reduce the environmental footprint of oil use. The importance of this topic lies in its potential to enhance operational efficiency and contribute to an overall sustainable future.
Innovations in Lubricant Technology
Innovations in lubricant technology are driving a transformation in oil lubrication systems. Increased efficiency and improved performance are at the forefront of these innovations. New formulations are being developed to enhance various properties of lubricants, such as thermal stability, oxidation resistance, and viscosity characteristics.
Some significant innovations include:
- Nano-lubricants: Incorporating nanoparticles can enhance the performance of conventional oils, providing better wear protection and reducing friction.
- Additives: Modern additives help in improving the lifespan of lubricants and preventing degradation under extreme conditions.
- Hybrid lubricants: The merging of synthetic and mineral oils yields products that utilize the best of both worlds.
Such advancements not only lead to better lubrication but also align with the evolving demands of industries aiming for greater sustainability.
Shift Toward Sustainable Practices
The shift toward sustainable practices is another crucial aspect of the future of oil lubrication. As awareness of environmental issues grows, industries are compelled to rethink their lubrication strategies. This shift is characterized by:
- Biodegradable oils: These oils break down more readily in the environment, reducing pollution and impact on ecosystems. They provide an effective alternative to conventional lubricants.
- Recycling programs: Many companies are focusing on the recycling of used lubricants, which helps in reducing waste and conserving resources.
- Energy-efficient systems: Innovations in machinery using oil lubrication can significantly enhance energy efficiency, thereby lowering overall consumption and emissions.
"The evolution of oil lubricants reflects a growing consciousness in industries, aiming to meet performance needs without compromising environmental integrity."
This pivot in focus is not just beneficial for companies but also essential for the planet's well-being.
Closure
The conclusion of this article is crucial for synthesizing understanding of oil-lubricated systems. It serves as a final reflection on the myriad aspects covered, reiterating the significance of effective oil lubrication in various industries. This section allows readers to grasp how these systems function, the benefits they offer, and the challenges they face. Moreover, it highlights future possibilities within the field.
Summary of Key Insights
In summary, oil-lubricated systems are integral to numerous applications, ranging from automotive engines to industrial machinery. By reducing friction, dissipating heat, and providing corrosion resistance, oil lubrication contributes significantly to the longevity and efficiency of equipment. Key insights include:
- Types of Oil Lubricants: Each type, whether mineral, synthetic, or biodegradable, has distinct properties suited for different applications.
- Application Areas: These systems have vast applications including automotive, aerospace, and marine industries, showcasing their versatility.
- Maintenance Practices: Regular oil changes and filtration are vital to keep the systems running effectively.
- Challenges: Environmental issues and the degradation of lubricants over time are persistent concerns that need attention.
"Understanding the complexities of lubrication can lead to better maintenance practices and innovations in technology."
The Way Forward
The way forward in oil lubrication is marked by innovation and a shift towards sustainable practices. Research is focusing on developing more environmentally friendly lubricants without compromising performance. As industries evolve, incorporating biodegradable oils and advanced synthetic alternatives will be essential. This will not only reduce environmental impact but also ensure ongoing efficiency and reliability in lubrication systems.
It is imperative that researchers, engineers, and companies work collaboratively to push the boundaries of lubricant technology. Continuous learning and adaptation will drive the industry toward more effective and sustainable solutions.