Non-Destructive Testing of Welds: An In-Depth Study
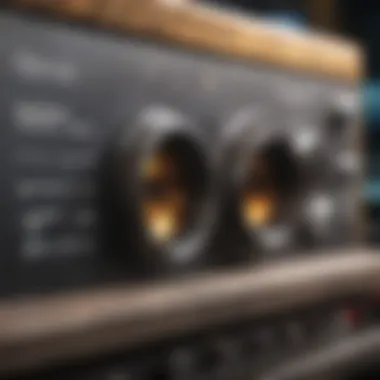
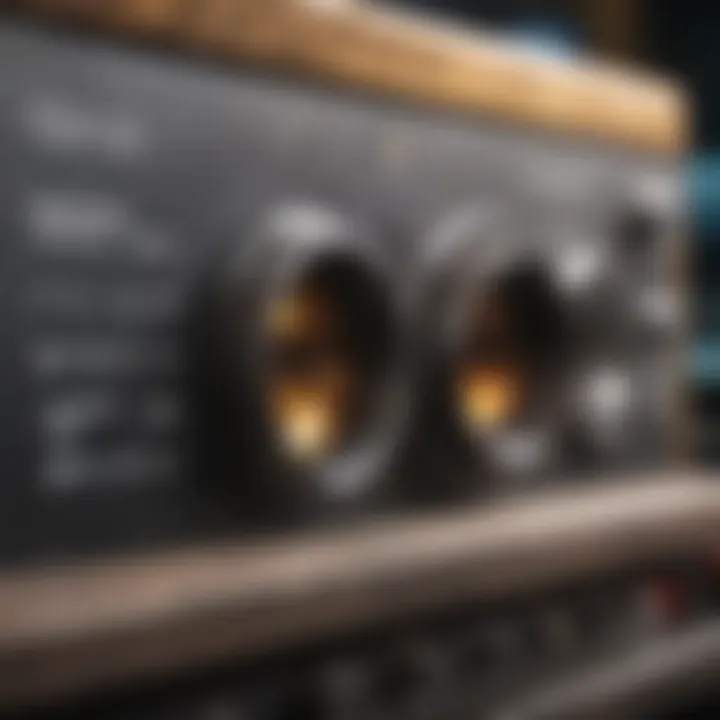
Intro
Non-destructive testing (NDT) plays a critical role in evaluating the integrity of welded structures. It is essential for identifying defects that could compromise structural safety without causing damage to the component being tested. The application of various NDT methods is widespread in industries such as construction, manufacturing, and aerospace. This article examines these methodologies and frameworks to deepen understanding of how NDT contributes to maintaining safety standards in engineering.
Understanding NDT is vital for professionals involved in quality control, safety inspection, and compliance with industry standards. By analyzing existing techniques and their effectiveness, the readers will gain insight into future innovations and trends in the field.
Key Findings
Major Results
The investigation into NDT methods reveals a variety of approaches used to assess weld quality. Among the most prevalent methods are ultrasonic testing, radiographic testing, and magnetic particle testing. Each of these techniques serves a unique purpose and exhibits different strengths and weaknesses. For instance:
- Ultrasonic testing is revered for its ability to detect internal flaws in welds and is non-invasive, preserving the integrity of the weld.
- Radiographic testing can provide a permanent record of the weld integrity but requires careful handling of radiation safety.
- Magnetic particle testing is effective for detecting surface and near-surface discontinuities, especially in ferromagnetic materials.
These findings illustrate the importance of selecting appropriate NDT methods based on specific project requirements and material characteristics.
Discussion of Findings
The analysis underscores the critical role that NDT plays in ensuring both quality and safety in welded constructions. Adopting these methodologies not only meets regulatory requirements but also prevents costly failures that could arise from undetected flaws. Furthermore, advancements in technology are continually reshaping the landscape of NDT. For example, the emergence of digital radiography and phased array ultrasonics has improved accuracy and efficiency in inspections.
"Non-destructive testing ensures the reliability of structures and minimizes risks, safety has no compromise."
Moreover, the integration of NDT within the lifecycle of a welded component—from design to maintenance—facilitates better decision-making at every stage, effectively influencing project outcomes.
Methodology
Research Design
This article utilizes a qualitative research approach, focusing on existing literature and case studies on NDT applications in welding. This design allows for a comprehensive understanding of both theoretical and practical considerations relevant to the subject matter.
Data Collection Methods
Data was gathered through a combination of primary and secondary sources. Primary data consisted of interviews with industry experts and practitioners, while secondary data included analysis of peer-reviewed journals, industry reports, and relevant online resources. The synthesis of this information provides a robust framework for understanding NDT's role in welding.
By employing these research methods, the article delivers a detailed and insightful exploration into non-destructive testing processes, emphasizing their importance in engineering contexts.
Preface to Non-Destructive Testing
Non-destructive testing (NDT) plays a vital role in many industries, particularly in the realm of welding. Its significance lies in its ability to assess the integrity of materials and structures without causing any damage. This quality is crucial in ensuring the safety and reliability of welded joints, which are often subjected to extreme stress and environmental factors. Understanding NDT is not merely an academic exercise; it is essential for engineers, inspectors, and technicians who are responsible for maintaining high safety standards.
The introduction of NDT offers insights into various methods and best practices. This knowledge is particularly relevant in a world where regulatory compliance is increasingly stringent. Enhancing the reliability of welds through NDT not only helps avoid catastrophic failures but also promotes operational efficiency.
Definition of Non-Destructive Testing
Non-destructive testing refers to a set of techniques used to evaluate the properties of a material, component, or assembly without causing any damage. This assessment enables individuals to gauge variables such as strength, integrity, and quality before the material is put into service. Various methods, like ultrasonic testing, radiographic testing, and visual inspection, fall under the umbrella of NDT.
One key feature of NDT is that it provides immediate feedback on welded joints and other components. The ability to detect flaws such as cracks, voids, or misalignments allows for timely interventions, leading to significant cost savings over the lifecycle of a structure.
Historical Development of NDT Techniques
The roots of non-destructive testing can be traced back to the early 20th century, when x-ray technology began to gain traction. Initially used in medical fields, its application soon expanded to industrial sectors. Early efforts in x-ray inspection laid the foundation for radiographic testing. As the technology advanced, other methods like ultrasonic testing emerged during World War II for evaluating welds in military equipment.
The post-war era marked a significant boost in NDT adoption across various industries, prompted by the need for enhanced safety standards. In the decades that followed, techniques further evolved, influenced by advancements in technology and materials science.
Today, NDT combines traditional inspection methods with cutting-edge technology like computer imaging and artificial intelligence. This evolution reflects an ongoing commitment to improving safety and understanding in welding and material testing.
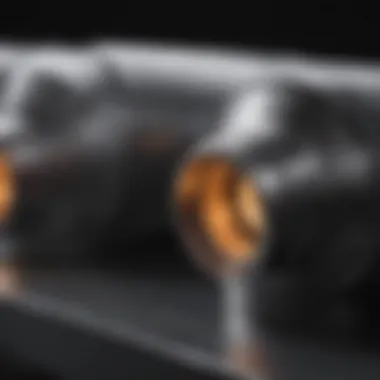
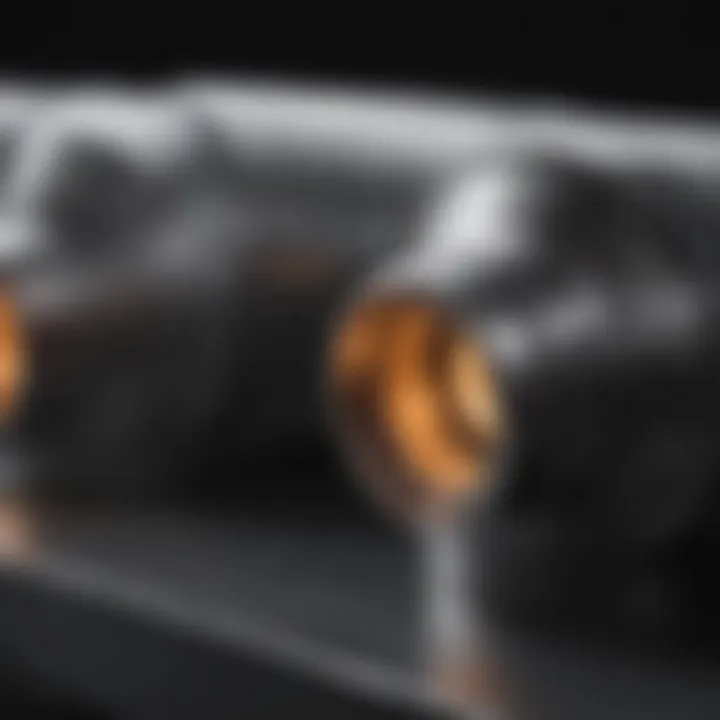
Importance of NDT in Welding
Non-destructive testing (NDT) plays a vital role in the welding industry. It ensures that welds meet the necessary standards and perform as required under various conditions. This importance can be examined through several key elements, including structural integrity and regulatory compliance.
Ensuring Structural Integrity
Structural integrity is a critical factor in maintaining safety and reliability in engineering. Welds are often the weakest points in a structure. Thus, assessing their quality is necessary. NDT methods allow for the inspection of welds without causing damage. This non-invasive evaluation is crucial for identifying potential failures caused by material defects, improper techniques, or environmental stressors.
Through techniques such as ultrasonic testing and radiographic testing, defect types like cracks, porosity, or incomplete fusion can be detected. Early detection of these issues can prevent catastrophic failures and accidents. For instance, in bridge construction, ensuring that each weld is well-executed can prevent structural collapse. Therefore, NDT ensures longevity, reliability, and safety of welded structures.
Regulatory Compliance and Standards
Regulatory compliance is another critical aspect of NDT in welding. Various industries are governed by strict standards, such as the American Welding Society (AWS) and numerous international regulations. These standards ensure that welds are performed to specific safety and quality benchmarks. NDT contributes to compliance by providing objective and reliable assessment methods that adhere to these regulations.
By implementing NDT, companies not only meet legal obligations but also protect their reputation. The consequences of failing to comply can be severe, leading to legal repercussions and financial losses. Moreover, maintaining high-quality standards enhances trust with clients and stakeholders. In some industries, such as aerospace and nuclear, the stakes are even higher, making NDT essential for routine inspections and quality control.
"NDT not only assures quality control but also acts as a safeguard against potential failures in welded structures."
In summary, the importance of NDT in welding cannot be overstated. The techniques applied are indispensable tools for ensuring structural integrity and complying with industry standards. As technology evolves, the methods used in NDT will continue to advance, further enhancing the reliability and safety of welded connections.
Common NDT Methods for Welds
The assessment of welded joints through non-destructive testing (NDT) methods is vital in maintaining the safety and reliability of structures. Non-destructive testing methods help identify potential flaws without compromising the integrity of the material, thereby ensuring the longevity of welded components. Each NDT method has unique advantages, working principles, and applications. This section will explore the most widely used NDT techniques for weld inspections, presenting their benefits and considerations.
Visual Inspection
Visual inspection is the most basic and widely implemented non-destructive testing method. It involves examining the weld surface for visible defects such as cracks, porosity, and undercuts. This technique is often the first step in the inspection process due to its simplicity and low cost.
The effectiveness of visual inspection lies in the operator’s experience and knowledge of the welding process. Special tools like magnifying glasses or specialized lighting can enhance visibility. This method, while limited in detecting subsurface defects, plays a crucial role in the initial assessment of weld quality and is often a requirement in comprehensive inspection protocols.
Ultrasonic Testing
Ultrasonic testing (UT) uses high-frequency sound waves to detect irregularities in welds. These sound waves transmit into the material and reflect back when encountering a flaw. An ultrasonic transducer generates and receives these waves, translating the data into an image that reveals hidden defects within the weld.
This method is highly sensitive and capable of detecting minute cracks and inclusions. Unlike visual inspection, UT can assess subsurface conditions, making it ideal for critical weld areas. While preparation and equipment can be expensive, the trade-off lies in its precision and depth of analysis, making it indispensable in many industrial applications.
Radiographic Testing
Radiographic testing (RT) employs ionizing radiation to examine welds and structural components. By exposing a weld to X-rays or gamma rays and capturing the resultant imagery on film or digital detectors, inspectors can visualize internal flaws such as pores or cracks.
This technique is effective for showcasing internal geometrical information of the weld joint. However, it requires specific safety measures due to exposure to radiation. The interpretation of radiographs necessitates highly trained personnel as subtle defects may go unnoticed without keen analysis. Radiographic testing provides clear, permanent records that can be valuable for future inspections.
Magnetic Particle Testing
Magnetic particle testing (MPT) is used for detecting surface and near-surface defects in ferromagnetic materials. This method involves magnetizing the weld area and applying magnetic particles, usually in a liquid suspension, which cluster at the site of defects, creating visible indications.
MPT is advantageous due to its speed and relatively low cost. It can quickly identify issues such as cracks and laps. However, it is limited to magnetic materials and may require thorough surface preparation to be effective. An understanding of the weld characteristics and proper technique is crucial for accurate interpretations.
Dye Penetrant Testing
Dye penetrant testing (DPT) is a liquid-based method that detects surface-breaking defects. A colored dye is applied to the surface of the weld and seeps into any cracks or voids. After a waiting period, excess dye is removed, and a developer is applied, typically revealing defects through contrasting colors.
This method is straightforward, cost-effective, and non-toxic, making it suitable for various applications. However, it cannot detect subsurface defects and is less effective on porous materials. Its simplicity promotes its popularity, especially for welds that require quick evaluations of surface integrity.
Eddy Current Testing
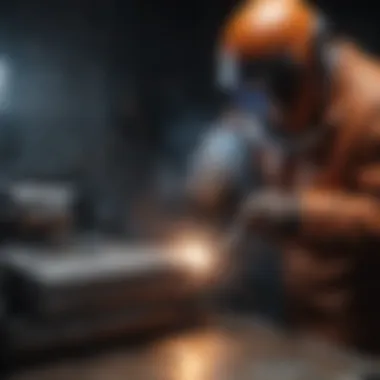
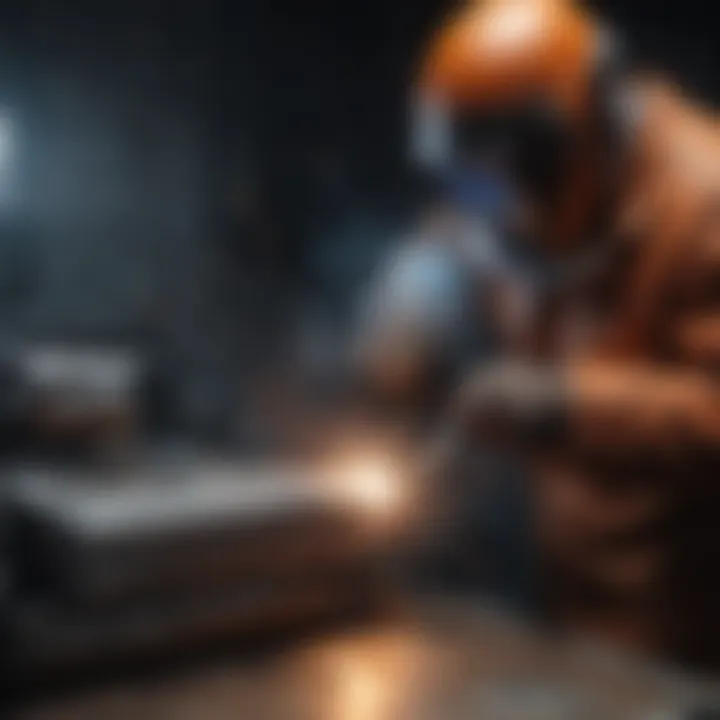
Eddy current testing (ECT) employs electromagnetic induction to detect flaws in conductive materials. By introducing an alternating current in a coil placed over the weld, eddy currents are induced in the material. Changes in the flow of these currents due to flaws can be measured and analyzed.
This method is sensitive to surface and near-surface defects and can assess material properties as well. It is particularly effective in inspecting non-ferromagnetic materials such as aluminum and titanium. The equipment for ECT can be expensive; however, its rapid inspection capabilities and informative data analysis often justify the investment.
Theoretical Framework of NDT Techniques
The theoretical framework of non-destructive testing (NDT) techniques serves as a foundation for understanding how various methods evaluate weld integrity without causing damage to the material. This knowledge is essential for students, researchers, educators, and professionals in engineering and related fields. By grasping these principles, stakeholders can better select appropriate NDT methods for specific applications, ensuring both safety and efficiency in operations.
Basic Principles of NDT
The basic principles of non-destructive testing involve using different physical phenomena to identify defects within welded joints. Understanding these principles is crucial for effective application of NDT methods. The core components include:
- Material Properties: The response of a material to stresses is key. Different materials display unique behaviors under various testing conditions.
- Detection Methods: Each NDT method, such as ultrasonic or radiographic testing, relies on specific principles to detect flaws like cracks or voids. This includes capturing reflections, absorption, or emissions based on the material's condition.
- Calibration: Accurate results require proper calibration of equipment. Calibration helps in adjusting the tools to align with known standards or reference materials.
When these principles are well applied, NDT can reveal critical insights into weld quality. This ensures that even sophisticated structures can be assessed without compromising their integrity.
Interpreting NDT Results
Interpreting results from nondestructive tests involves analyzing signals or images produced during inspection. This step is vital, yet it often presents complexities. Effective interpretation requires:
- Knowledge of Standards: Familiarity with relevant standards, such as those from the American Society for Nondestructive Testing, ensures that results are evaluated against accepted criteria.
- Understanding Signal Patterns: Each NDT method generates specific patterns. For instance, in ultrasonic testing, different amplitudes and time delays can indicate various types of defects. An expert needs to decipher these patterns accurately.
- Experience and Training: Skilled personnel are essential. Their understanding of both the method used and the material characteristics greatly influences result interpretation.
A thorough understanding of how to interpret NDT results leads to more reliable assessments, promoting safety and productivity in welding projects.
Challenges in Non-Destructive Testing
Non-destructive testing (NDT) is crucial in ensuring the reliability and safety of welded structures. However, it is not without its challenges. Understanding these challenges is essential for improving NDT practices and outcomes. There are two significant aspects to consider: the limitations of current methods and the skill requirements for personnel.
Limitations of Current Methods
Each NDT method has its unique benefits and drawbacks. Awareness of these limitations is necessary when selecting a testing technique for a specific application.
- Resolution and Detection Limits: Some NDT methods, like ultrasonic testing, can miss small defects due to resolution issues. This can lead to undetected flaws in welds, posing risks.
- Material-Specific Challenges: Certain methods may not be suitable for particular materials. For example, magnetic particle testing is ineffective on non-ferromagnetic materials.
- Surface Preparation: Techniques like dye penetrant testing require specific surface conditions. Poor surface preparation can compromise results.
- Environmental Factors: Conditions such as temperature, humidity, and dust can affect the accuracy of readings.
Despite these challenges, understanding the limitations allows for better planning and comprehensive assessments.
Skill Requirements for NDT Personnel
NDT does not solely rely on technology; the skill of the personnel conducting the tests is equally important. The effectiveness of NDT depends largely on the experience and knowledge of the individual performing the inspections.
- Training and Certification: Technicians must undergo rigorous training and obtain certifications. This ensures they can effectively interpret results and handle equipment.
- Understanding Material Properties: Personnel should have a solid understanding of welding metallurgy and the properties of the materials being tested. This knowledge aids in accurate assessments and decisions.
- Data Interpretation Skills: Analyzing data from tests requires a skilled eye. NDT personnel must be capable of discerning between acceptable variations and potential defects.
Thus, the challenges in non-destructive testing highlight the need for continued education and training in this domain to enhance methodologies and outcomes. Effective training programs and clear understanding of NDT limitations contribute greatly in addressing the existing concerns.
Applications of Non-Destructive Testing
The applications of non-destructive testing (NDT) are critical in various fields, particularly in welding. NDT allows for the inspection and evaluation of materials without causing any harm or altering their properties. This capability is essential for maintaining safety and quality in constructions and industrial processes. By identifying potential flaws early, NDT can prevent catastrophic failures, minimize downtime, and ensure compliance with safety regulations.
In the domain of welding, effective NDT methods directly contribute to the quality assurance process. When applied consistently, NDT techniques improve the reliability of welded structures, thus safeguarding human lives and valuable infrastructure. Moreover, NDT serves as a means of reducing costs related to repairs and replacements, making it a financially prudent choice for businesses.
Industrial Applications
NDT finds extensive use in various industries due to its ability to assess weld integrity without damaging the components. Here are some specific areas where NDT is applied:
- Oil and Gas: Pipelines and offshore platforms rely on NDT to detect defects that could lead to leaks or failures.
- Aerospace: Components in aircraft must meet strict safety standards. NDT helps ensure that welds are flawless.
- Manufacturing: In heavy machinery production, maintaining weld integrity is crucial for performance and safety.
- Power Generation: Nuclear and conventional power plants use NDT to inspect welds and joints critical in operation.
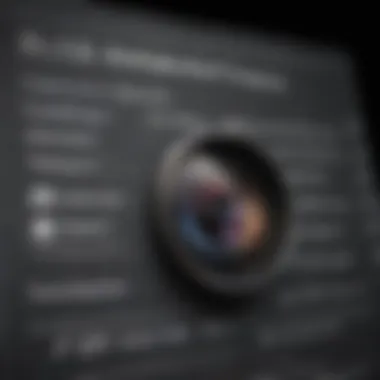
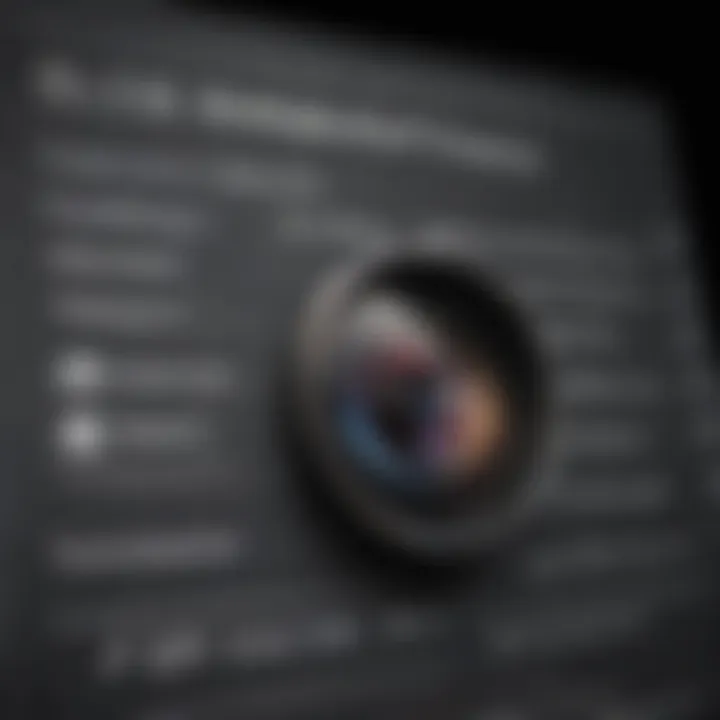
These applications highlight how NDT acts as a cornerstone of safety and efficiency across industries, where weld quality could have dire implications.
NDT in Construction and Infrastructure
In construction and infrastructure development, the application of NDT is indispensable. Inspectors utilize various methods to evaluate welded joints in structural projects. Some of the key benefits include:
- Structural Safety: Regular NDT checks help ensure that welding meets necessary standards before heavy loads are applied.
- Long-Term Durability: Early detection of defects enhances the lifespan of structures, which is vital for public safety.
- Regulatory Compliance: Many construction projects must adhere to strict regulations regarding material integrity. NDT supports compliance efforts effectively.
More specifically, NDT methods such as ultrasonic testing and radiographic testing are frequently employed to ensure that welds on bridges, buildings, and other structures are sound and free from serious defects.
"Non-destructive testing is a proactive approach to quality control in construction, mitigating risks before they escalate into severe issues."
In the future, advancements in NDT technologies will likely continue to enhance its applications in construction, leading to improved methodologies and tools.
Overall, understanding the applications of NDT in various sectors reveals its essential role as a key component in safeguarding and enhancing the quality of welded constructions.
Future Trends in Non-Destructive Testing
Future trends in non-destructive testing (NDT) are crucial to understanding how the field evolves to meet modern engineering challenges. As industries seek higher efficiency and reliability, advances in technology are reshaping NDT methodologies. These trends are important not only for enhancing testing precision but also for improving overall workflow in various applications, particularly in welding of structural components.
Adopting emerging technologies and innovative approaches can significantly influence how weld integrity is monitored. Understanding these trends allows engineers and inspectors to stay ahead in a rapidly changing landscape, ensuring that best practices are applied and maintained.
Emerging Technologies in NDT
Emerging technologies in NDT include a variety of advanced tools and techniques that leverage innovation to address current limitations in traditional NDT methods. One significant area of advancement is the improvement of imaging techniques. For instance, new ultrasonic testing devices offer enhanced resolution and deeper penetration, capable of detecting minute flaws in welds that conventional methods might miss. Additionally, portable radiography is becoming more efficient, utilizing digital detectors to cut down exposure times while increasing image quality.
Another noteworthy trend is the integration of robotics in NDT processes. Robotic systems equipped with NDT sensors can assess welds in hazardous or hard-to-reach environments, improving safety and efficiency. Furthermore, drones are increasingly used for large infrastructure inspections, providing access to difficult areas without extensive scaffolding or manual inspection.
The collaboration between various sectors, such as aerospace and automotive, fosters a cross-pollination of ideas. Techniques that prove successful in one industry can often be adapted for others, thereby promoting innovation throughout the NDT field. The growth of IoT (Internet of Things) technologies also plays a role, enabling real-time data collection and analysis.
Artificial Intelligence and NDT
Artificial intelligence (AI) is poised to revolutionize non-destructive testing by enhancing the analysis of inspection data. AI-powered algorithms can process vast amounts of data collected during NDT, identifying patterns and irregularities that might escape human notice. This capability not only improves defect detection but also reduces the time needed for analysis.
Machine learning techniques can adapt and improve over time based on historical data, leading to more accurate predictions and assessments of weld integrity. Many industries are beginning to apply predictive maintenance strategies, where AI helps forecast potential failures based on data trends observed over time.
Furthermore, AI can assist in automating decision-making processes, streamlining workflows in inspection protocols. This is especially pertinent in environments where time and precision are critical, such as oil and gas, aerospace, and nuclear sectors.
In summary, the future of non-destructive testing is shaped by emerging technologies and the integration of artificial intelligence. These advancements are crucial for the welding industry to maintain high levels of safety and reliability while adapting to the complex demands of modern engineering. By embracing these trends, professionals can ensure that they are well-equipped to tackle the challenges that lie ahead.
Summary and End
The field of non-destructive testing (NDT) plays a crucial role in the integrity and safety of welded structures. This section synthesizes the previous discussions, emphasizing the importance of employing NDT methodologies effectively in weld examination. With advances in technology and increased regulatory demands, the relevance of NDT is enhanced, making it a vital aspect of engineering practices.
Non-destructive testing is imperative for identifying defects without compromising the integrity of materials. The need for robust infrastructure means that NDT, specifically in welding, cannot be understated. Techniques range from visual inspection to advanced methods like ultrasonic and radiographic testing. Each carries unique benefits, but together they create a reliable system for ensuring that welds meet demanding standards.
Furthermore, understanding the complexities of various NDT methods enables professionals to choose the appropriate technique for each situation. Factors such as material type, weld location, and expected load conditions dictate the method. Awareness of future trends also positions engineers to adapt to new technologies that promise greater efficacy and accuracy in testing.
"Understanding and implementing NDT techniques is an essential investment in the safety and longevity of structures."
As the industry continues to evolve, the integration of artificial intelligence and emerging technologies presents exciting possibilities. The assurance of compliance with industry standards remains a priority, and NDT not only supports regulatory commitments but also fosters trust among stakeholders. Thus, a thorough grasp of NDT principles and practices leads to enhanced decision-making, ultimately contributing to the success of engineering projects.
Key Takeaways
- Non-destructive testing is critical for maintaining the integrity of welded structures.
- A variety of NDT methods are available, each with specific applications and advantages.
- Knowledge of NDT techniques is essential for preventing structural failures and ensuring compliance with regulations.
- Future advancements, including artificial intelligence, will likely enhance the capabilities of NDT.
- Effective implementation of NDT fosters trust and reliability in engineering outcomes.
The Future of NDT in Welding
The future of non-destructive testing, particularly in welding, is characterized by rapid advancements in technology. The integration of artificial intelligence and machine learning is set to revolutionize the field. These tools can optimize testing processes, allowing for faster and more accurate defect detection.
Emerging technologies, such as drone-based inspections and automated testing solutions, are gaining traction. This streamlining of inspection processes promises to reduce human error while improving efficiency. Moreover, sensors and real-time data analytics are poised to transform the way inspections are conducted, providing instant feedback and facilitating proactive decision-making.
The growing emphasis on sustainability in engineering is also influencing NDT practices. As industries move towards more eco-friendly options, NDT can help in the evaluation of new materials and techniques that minimize waste and environmental impact. The role of NDT in composite material assessments will likely expand, leading to further innovations.