Optimal Temperature Settings for PEEK 3D Printing
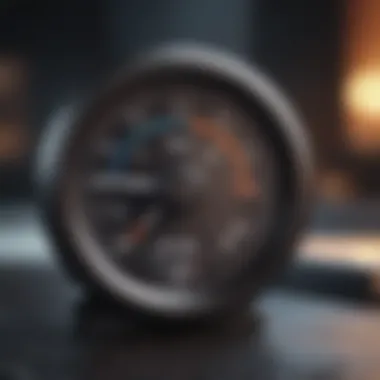
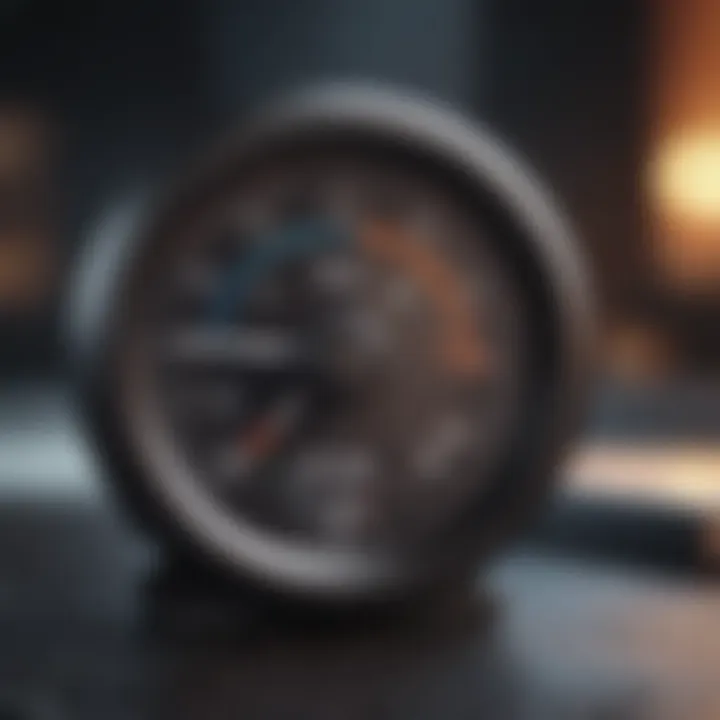
Intro
3D printing has revolutionized a vast array of industries, and polyether ether ketone (PEEK) stands out as one of the most advanced thermoplastics available today. Its remarkable thermal stability, chemical resistance, and mechanical strength make it suitable for demanding applications in aerospace, medical, and automotive fields. However, achieving optimal print quality with PEEK requires careful consideration of temperature settings during the printing process.
Setting the right temperature is crucial. It affects not only adhesion to the print bed but also layer bonding and the overall structural integrity of the finished product. Given its unique properties, the recommended temperatures for both the nozzle and print bed can differ significantly from other common filament materials. Thus, understanding the optimal temperature settings is essential for achieving superior results while working with PEEK.
This article will unpack important findings regarding optimal temperature settings when working with PEEK, including a detailed examination of how temperature variations can influence print quality and the physical characteristics of the final product. With insights drawn from recent research and expert recommendations, we aim to provide a resource that is beneficial for students, researchers, and industry professionals alike.
Key Findings
Major Results
Research indicates that the optimal printing parameters for PEEK typically involve a nozzle temperature ranging from 360°C to 420°C and a heated bed temperature between 90°C and 120°C. The exact temperatures chosen depend on factors like the specific printer model and the characteristics of the filament being used. Manufacturers often provide guidelines, but real-world testing often leads to adjustments that produce better results.
Moreover, it is noted that using a high-performance extruder capable of maintaining consistent nozzle temperatures is vital. Any significant fluctuation can cause extrusion issues, impacting print quality.
Discussion of Findings
The relationship between temperature and the performance of PEEK in 3D printing is multifaceted. Insufficient nozzle temperatures can lead to poor layer adhesion, resulting in delamination. Conversely, excessive temperatures can degrade the material, creating issues such as stringing or oozing.
It is equally important to consider the cooling down period post-printing. Waiting for the printed object to cool at a controlled rate can help in mitigating internal stress within the finished part. Proper temperature settings can enhance the durability and functionality of the final product, making it an essential aspect to consider during 3D printing with PEEK.
For those who aim to push the boundaries of traditional manufacturing, understanding and mastering these temperature settings can open the door to innovative applications with PEEK.
Methodology
Research Design
The research undertaken for this article involved a review of existing literature on PEEK 3D printing techniques, coupled with a synthesis of insights gathered from practitioners in the field. This holistic approach provided broad input regarding temperature settings that yield superior results.
Data Collection Methods
Data was collected through a mix of primary and secondary sources. Interviews with industry professionals provided firsthand accounts of their experiences with different settings of temperature, while peer-reviewed articles contributed to a theoretical foundation. Online forums such as Reddit and various industry publications also offered valuable, crowd-sourced insights, further enriching the research.
Understanding the interplay between material properties, machine settings, and external conditions is a complex task. However, with careful analysis, one can arrive at conclusions that will equip practitioners and enthusiasts to refine their processes accordingly.
Prolusion to PEEK in 3D Printing
Polyether ether ketone, commonly known as PEEK, has emerged as a standout material in the realm of 3D printing. This high-performance thermoplastic presents remarkable durability, chemical resistance, and thermal stability, making it particularly suited for demanding applications across various industries. Understanding PEEK’s characteristics and the pivotal role temperature plays in printing processes is essential for achieving the best results.
One of the significant advantages of PEEK is its ability to endure extreme environments. This property opens avenues for its application in sectors like aerospace, automotive, and medical. However, the processing of PEEK involves distinct challenges. It requires specific temperature settings to ensure successful layer adhesion and minimize defects during the printing process.
Therefore, this article explores optimal temperature settings for PEEK 3D printing. A focus on how historical development shaped the use of PEEK will set the stage for further discussion. Moreover, we will analyze current trends that highlight PEEK's growing significance in modern manufacturing.
Historical Context of PEEK Development
The development of PEEK can be traced back to the 1980s, where it was primarily envisaged for high-performance applications due to its remarkable properties. Initial research focused on its fabrication and processing, unveiling its incredible stability and strength. By the 1990s, PEEK began making waves beyond traditional applications, such as industrial sectors, into sectors demanding high standards, including aerospace and medical devices. The continuous improvement in processing techniques and product formulations led to increased accessibility, facilitating PEEK’s adoption in 3D printing.
Current Trends in PEEK Usage
In recent years, the adoption of PEEK in 3D printing has shown substantial growth. Industries are increasingly leveraging the benefits of PEEK, primarily due to its lightweight and high strength-to-weight ratio. This trend is particularly notable in aerospace, where reducing weight can drastically improve fuel efficiency. Additionally, the medical field is witnessing a surge in PEEK utilization for creating patient-specific implants and components due to its biocompatibility.
Further, technological advancements in 3D printing equipment allow for improved temperature control and material processing, enhancing the capability to print with PEEK. As a result, professionals across different domains are gaining interest in mastering the nuances of PEEK printing.
"PEEK represents a significant advancement in 3D printing materials, reflecting the ongoing evolution in technology and application demands."
By understanding these historical contexts and current trends, stakeholders can navigate the complexities of PEEK 3D printing more effectively.
Material Properties of PEEK
Understanding the material properties of polyether ether ketone (PEEK) is crucial for optimizing its use in 3D printing. PEEK is known for its unique combination of thermal stability, mechanical strength, and chemical resistance. These properties not only influence the performance of printed components but also dictate the temperature settings necessary for successful prints. Mastery of these aspects can enhance print quality, reduce common printing issues, and ultimately lead to higher performance in specialized applications.
Thermal Stability and Resistance
PEEK exhibits remarkable thermal stability. This characteristic allows it to withstand high temperatures without undergoing significant degradation. The material's glass transition temperature is around 143 °C, and its melting temperature is typically between 335 °C and 340 °C. This means that during 3D printing, specific settings must remain above these thresholds to achieve effective melting and flow of the filament, ensuring proper layer bonding.
The resistance to thermal degradation makes PEEK suitable for various high-temperature environments where other materials might fail. For instance, maintaining a consistent nozzle temperature within the recommended range not only facilitates efficient melting but also ensures that the material retains its mechanical properties upon cooling. This is essential in applications where components must endure rigorous thermal cycling.
Mechanical Strength and Durability
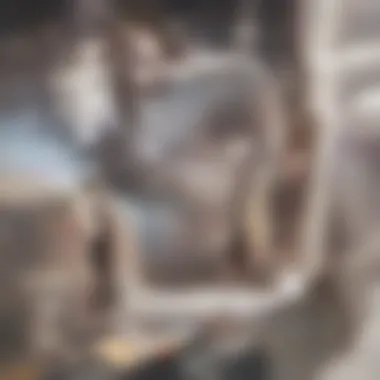
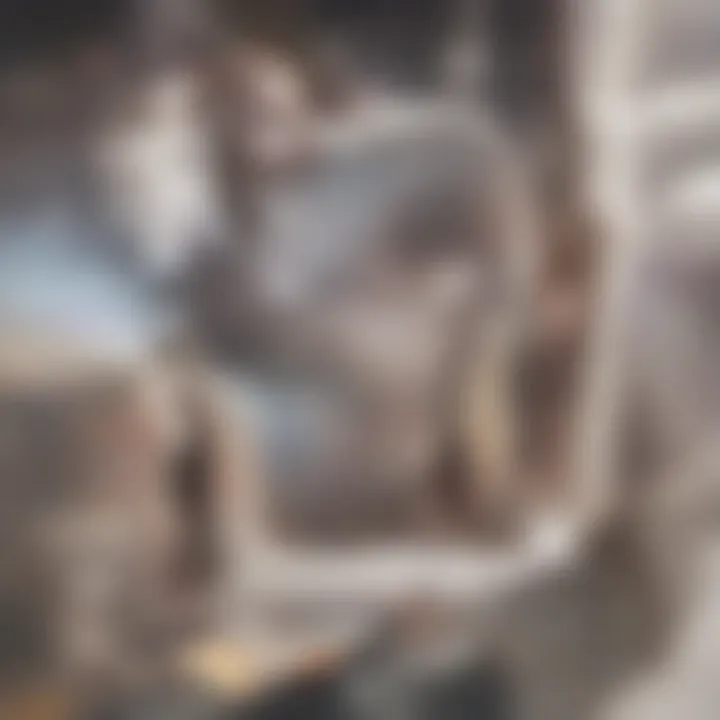
The mechanical properties of PEEK are noteworthy. It boasts high tensile strength and rigidity, rendering it ideal for applications that require durable components. When printing with PEEK, optimal nozzle temperatures can significantly influence mechanical integrity. At the right temperatures, the filament can attain better interlayer adhesion, which is crucial for structural stability in final prints.
Moreover, PEEK's excellent fatigue resistance means that parts made from this material can withstand repeated loading without failure. This characteristic is beneficial for components used in aerospace and automotive industries, where durability is non-negotiable. Understanding the relationship between print temperatures and mechanical properties is vital for engineers aiming to produce reliable PEEK components.
Chemical Resistance
PEEK is renowned for its exceptional chemical resistance, making it a popular choice for environments where exposure to harsh chemicals is inevitable. The polymer is resistant to a wide range of solvents, acids, and bases, maintaining its integrity even in challenging conditions. This chemical resilience is essential for parts used in the medical field, chemical processing, and other sensitive applications.
To achieve the desired chemical resistance in 3D printed items, temperature settings play an important role. Higher processing temperatures enable the material to flow and bond effectively during the printing process. However, exceeding the upper limits can lead to degradation, affecting the chemical properties of the final product. Hence, careful calibration of print temperatures is crucial to maintaining the desirable traits of PEEK while optimizing for 3D printing.
Importance of Temperature in PEEK 3D Printing
Understanding the significance of temperature in the context of PEEK 3D printing is paramount. This material presents unique challenges and opportunities that are closely linked to how temperature variations affect its properties and performance. Proper temperature management can lead to improved print quality, optimized adhesion between layers, and minimized warping and defects during the printing process.
Understanding Glass Transition and Melt Temperature
PEEK, or polyether ether ketone, possesses a specific range of temperatures where it transitions between solid and liquid states. The glass transition temperature (Tg) is a critical point where PEEK changes from a rigid state to a more flexible one. For PEEK, this temperature typically hovers around 143°C. Beneath this threshold, the polymer may brittle and fail to deform adequately, which is vital for the creation of precise components.
Conversely, the melt temperature (Tm), generally around 343°C, signifies the point where the polymer begins to flow in a molten state. Operating within these temperature ranges allows for effective extrusion and proper material flow through the nozzle, ensuring uniform filament deposition. Additionally, exceeding the Tm can result in undesired degradation of the polymer, negatively affecting the mechanical properties of the final print. Understanding these thermal markers is essential for achieving successful results in PEEK 3D printing.
Effects of Temperature on Layer Adhesion
Layer adhesion is influenced heavily by the temperatures set during the printing process. When the nozzle temperature is optimized to be within the recommended range, it aids in achieving excellent interlayer bonding, reducing the likelihood of layer delamination. This is particularly important in applications that demand structural integrity under stress.
When layers adhere properly, the end product not only possesses enhanced strength but is also more resistant to environmental factors. However, if the temperature is set too low, layers may not fuse adequately, causing weak points. Similarly, excessively high temperatures can lead to excessive flow, resulting in over-extrusion and defects in the print.
To achieve optimal results, following recommended temperature settings and conducting tests on specific printer setups are essential. This careful adjustment can help in fine-tuning the performance of PEEK in various applications, ensuring reliability and efficiency.
Proper management of print temperature is key to maximizing the unique benefits of PEEK as an advanced engineering material.
Optimal Nozzle Temperature Settings
When considering PEEK for 3D printing, optimal nozzle temperature settings are critical for achieving desirable outcomes. The nozzle temperature directly influences the molten state of the filament, impacting flow rate and overall print quality. A precise temperature regime is vital for enhancing layer adhesion, reducing print defects, and ensuring that the mechanical properties of the printed part are preserved. Understanding the nuances of these settings leads to superior performance and efficiency in the printing process.
Recommended Temperature Ranges
The recommended temperature range for PEEK nozzle settings typically falls between 340°C to 400°C. Setting the nozzle temperature within this range facilitates adequate melting of the material, allowing it to flow smoothly through the nozzle. It is essential to adjust the temperature based on the specific formulation of PEEK used, as slight variations in the polymer composition can alter melting behavior.
- 340°C: Suitable for standard PEEK filaments in stable environments, ensuring a well-controlled thermal environment.
- 360°C to 380°C: Often used for higher-performance grades or in scenarios requiring improved layer adhesion and mechanical properties.
- Above 380°C: Should only be used with caution, as prolonged exposure to very high temperatures could lead to degradation of the polymer.
Impact of Nozzle Temperature on Print Quality
The impact of nozzle temperature extends beyond mere melting. A well-calibrated nozzle temperature enhances layer bonding and results in a smoother finish. Higher temperatures tend to improve flow characteristics, reducing the chances of clogging or inconsistent extrusion. However, excessively high temperatures may lead to thermal degradation, which can compromise printed part strength.
Factors to consider regarding temperature impact on quality include:
- Layer Adhesion: Higher temperatures can promote better fusion between layers, which is particularly crucial in applications demanding high strength.
- Print Speed: Higher temperatures can allow for faster print speeds while maintaining accuracy, contributing to improved productivity.
- Surface Finish: Temperature directly influences the texture of the printed surface; optimal settings lead to fine detailing and lesser defects such as rough patches or sagging.
Optimizing nozzle temperature for PEEK printing is thus a careful balance, requiring consideration of material characteristics and desired print outcomes.
Optimal Bed Temperature Settings
The bed temperature in PEEK 3D printing is crucial for achieving satisfactory adhesion and minimizing distortion during the printing process. An optimal bed temperature can significantly enhance the print quality, reduce warping, and ensure a smooth workflow. Since PEEK is a high-performance polymer with unique thermal characteristics, understanding the appropriate bed temperature settings can save time and material waste for both professionals and enthusiasts alike.
Recommended Bed Temperatures
When working with PEEK, recommended bed temperatures typically range between 80°C and 120°C. These temperatures facilitate proper adhesion to the print bed while allowing the material to maintain its structural integrity throughout the printing process. Specifically:
- 80°C: This lower end of the spectrum is beneficial for smaller prints or when using certain bed surfaces like glass or PEI (Polyetherimide).
- 100°C - 120°C: Higher settings are advantageous for larger components or when minimizing warping is critical. At these temperatures, the bed can effectively combat the cooling stresses inherent in PEEK, thus reducing the chances of deformation.
It is important to note that the optimal bed temperature can vary based on specific printer and material configurations. Therefore, running tests to find the most suitable temperature for individual applications is recommended.
Bed Surface Material Compatibility
The choice of bed surface material plays a significant role in ensuring successful PEEK prints. Not all surfaces interact equally with PEEK, and understanding compatibility can aid in achieving the best possible outcomes. Here are some common bed surface materials:
- Glass: Offers excellent flatness and low adhesion, often requiring higher bed temperatures to maintain adhesion during the print process.
- PEI: Highly compatible with PEEK, it provides a surface that ensures strong adhesion without excessive difficulty in removing prints post-production. The recommended bed temperature should fall within the higher end of 100°C to 120°C.
- Kapton Tape: This polyimide film can be effective but may require additional care in maintaining high temperatures during prints. It also helps to prevent the warping of PEEK, but it might not provide as much grip as PEI.
"Understanding bed surface compatibility with PEEK is essential for optimal adhesion and print success."
Optimal bed temperature coupled with the right surface materials will greatly enhance the 3D printing experience with PEEK and maximize the potential of this advanced thermoplastic.
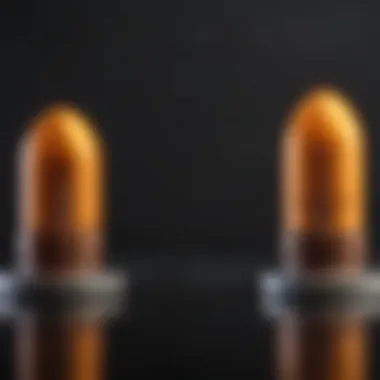
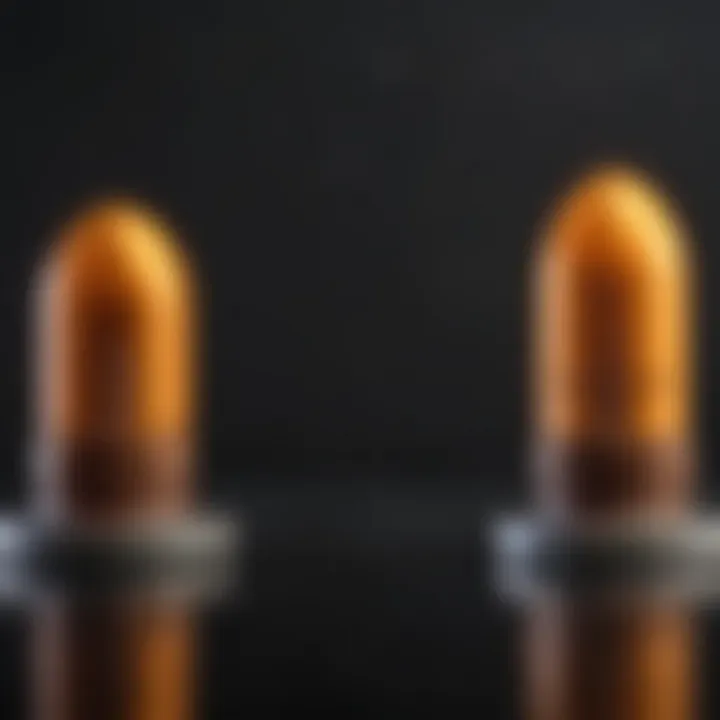
3D Printer Configurations
Understanding the differing configurations of 3D printers is crucial when working with PEEK. This material requires precise temperature settings and printer types to optimize the 3D printing process. Awareness of specifics such as filament feed mechanisms, temperature regulation capabilities, and construction type can significantly influence the quality of the printed object. PEEK's unique properties necessitate attention to detail in these configurations for successful implementation.
Differences Between FDM and Other Technologies
Fused Deposition Modeling (FDM) is one of the most prevalent methods for 3D printing with PEEK. FDM works by melting filament and depositing it layer by layer. Key aspects to consider are:
- Material Compatibility: PEEK's high melting temperature demands printers capable of reaching and maintaining this heat. FDM printers generally meet this requirement, while other technologies may not adequately support PEEK due to issues with thermal degradation.
- Print Resolution and Speed: FDM offers a balance of print speed and precision. Other methods like Stereolithography (SLA) provide higher detail but may struggle with PEEK's thermal constraints and layer adhesion.
- Layer Adhesion: The thermal properties of PEEK can cause issues with adhesion between layers. FDM printers, especially those designed with a heated bed, have shown efficacy in addressing this challenge.
Overall, choosing FDM over other technologies impacts final print properties, surface finish, and material integrity with PEEK.
Printer Modifications for PEEK Printing
When using PEEK, some modifications can enhance printer functionality. Not all 3D printers are ready to handle high-performance thermoplastics without tweaks. Consider the following modifications:
- Upgrading Hot End: A high-performance hot end designed for high-temperature filaments is essential. This upgrades the printer's capability to extrude PEEK effectively ultimately improving print quality.
- Enhanced Insulation: Proper insulation around the hot end and the filament path mitigates temperature drops as it travels through the extruder. This careful approach reduces the possibility of filament jamming.
- Dust-Free Environment: Establishing a clean printing environment can significantly influence print results. PEEK is sensitive to contaminants, which can degrade print quality; thus, a clean operating space is recommended.
- Calibration and Testing: Regularly calibrate the printer for optimal settings tailored to PEEK. Testing print profiles with different parameters ensures improved results over time.
In summary, adjustments to printer configurations are significant when aiming to print successfully with PEEK. It transforms the process from challenging to manageable, allowing users to harness the advantages of this advanced material effectively.
Common Issues Faced While Printing PEEK
3D printing with polyether ether ketone (PEEK) is promising due to its exceptional properties. However, certain challenges can arise during the printing process. Understanding these common issues is crucial for professionals and enthusiasts aiming for high-quality prints. This section outlines major concerns such as warping, stringing, and layer delamination, along with strategies to mitigate these problems.
Warping and Curling
Warping and curling are often the most reported issues when printing with PEEK. These phenomena occur due to the material’s high thermal expansion coefficient. As the print cools, different sections may shrink at varied rates, leading to deformation. This can result in poor adhesion to the build plate and affect overall print accuracy.
To combat warping, consider the following strategies:
- Controlled Bed Temperature: Keeping the print bed at an optimal temperature can minimize differential cooling rates. A heated bed can help maintain a uniform temperature throughout the print.
- Use of Adhesive Agents: Applying adhesive agents like PVA glue or specialized adhesives can improve bed adhesion. This drastically reduces the risk of curling during cooling.
- Enclosed Print Volume: Printing in an enclosed environment can help maintain ambient heat, which slows down cooling and reduces warping.
"Understanding the dynamics of temperature is key to overcoming warping and ensuring print integrity."
Stringing and Blobs
Stringing refers to the unwanted strands of filament that appear between printed features, while blobs occur when excess material oozes out during printing pauses. Both issues can detract from print quality and precision.
To reduce stringing and blobs:
- Retraction Settings: Adjusting the retraction distance and speed can reduce excess material from traveling during non-extrusion periods.
- Temperature Control: Lowering the nozzle temperature slightly can lessen the melt viscosity, helping to limit the amount of filament that oozes out.
- Print Speed Adjustments: Increasing print speed during travel moves can also minimize the time the nozzle spends over open areas, reducing stringing.
Layer Delamination
Layer delamination occurs when layers do not adhere properly to one another, which can lead to weakened structures. This issue is particularly common with high-temperature materials like PEEK.
Key factors influencing layer adhesion include:
- Insufficient Temperature: Ensuring the extruder operates at the appropriate temperature is essential. Lower temperatures can prevent layers from bonding effectively.
- Print Speed: Slower print speeds may enhance layer adhesion, allowing for better melting and fusing of the layers.
- Cooling Rate: Rapid cooling can contribute to delamination. Media like inert gas or controlling airflow can help maintain optimal conditions while printing.
Understanding these common issues faced while printing PEEK can significantly improve the success rate of prints. As technology evolves, so do strategies for overcoming these challenges.
Post-Processing Techniques for PEEK Prints
PEEK, or polyether ether ketone, is a highly favored material in 3D printing due to its excellent properties. However, achieving optimal results often requires not only careful attention to printing parameters but also effective post-processing techniques. This section is crucial because post-processing can greatly enhance the mechanical properties and aesthetic quality of PEEK prints. Adopting the right techniques can significantly improve print performance and longevity, making this an essential topic for practitioners.
Annealing Procedures
Annealing is a thermal treatment method that helps to relieve internal stresses in printed PEEK parts. This process is essential, as PEEK parts can suffer from warping and dimensional inaccuracies due to the high cooling rates experienced during printing.
In an annealing procedure, the printed part is heated to a specific temperature, generally below its melting point, and held there for a predetermined period before it is cooled slowly. This controlled heating process leads to a more uniform crystalline structure in the material. It helps optimize the properties, ranging from mechanical strength to thermal stability.
Regarding practical implementation, here are some key steps for effective annealing:
- Preheat the oven to the recommended annealing temperature, usually around 150 to 220 °C, depending on the desired properties.
- Place the printed part in the oven and maintain the temperature for 30 minutes to several hours, based on part thickness and application requirements.
- Allow the part to cool down gradually inside the oven to avoid thermal shock, which can lead to cracking.
After annealing, users often notice an improvement in the overall mechanical properties of the part. For instance, tensile strength can increase, making the end product more reliable in critical applications.
Surface Finishing Methods
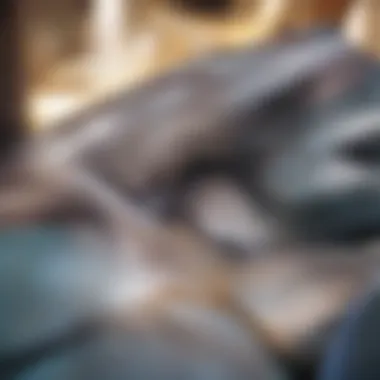
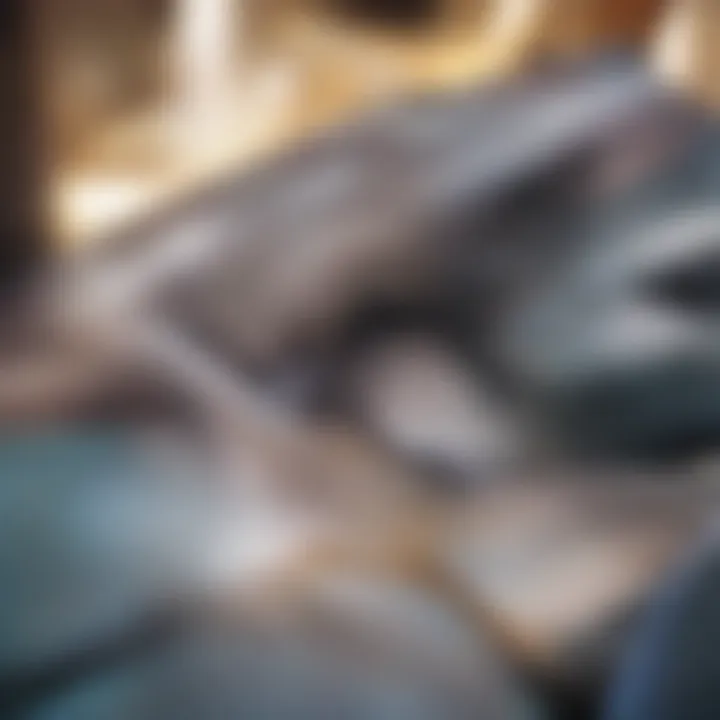
Surface finishing is another important post-processing technique for PEEK. It aims to improve the surface quality of prints, thereby enhancing their appearance and functionality. Given PEEK's natural characteristics, achieving a smooth surface finish can be challenging. However, several methods are available to tackle this:
- Mechanical Finishing: This includes sanding or machining to smooth down the surface. A finer grit sandpaper can be used to achieve a polished finish, but care must be taken to avoid altering the part's dimensions.
- Chemical Finishing: Applying specific chemical solutions may help achieve a smoother surface. However, the user must verify compatibility since PEEK is known for its chemical resistance. Using incompatible solutions can result in damage.
- Coating: Coating is another viable option where a thin layer of paint or resin is applied to the surface. This can enhance the appearance and provide protection from environmental factors. It's an effective method for applications requiring aesthetic appeal.
With proper surface finishing, PEEK components can meet or exceed the desired specifications for various applications, particularly where surface quality plays a critical role, such as in medical or aerospace devices.
In summary, efficient post-processing of PEEK prints can significantly contribute to their overall functionality and reliability, making it an important focus area for professionals engaged in high-performance 3D printing.
By understanding and leveraging these post-processing techniques, practitioners can maximize the utility of their PEEK components, ensuring they meet the demanding standards expected in specialized sectors.
Applications of PEEK 3D Printing
The applications of PEEK in 3D printing span various industries, each leveraging the unique properties of this material. Understanding these applications is crucial as it highlights the practical benefits and considerations associated with using PEEK for manufacturing critical components. PEEK’s remarkable thermal stability, chemical resistance, and strength make it suitable for demanding environments. Organizations recognize its potential in several fields, making it a material of choice for prototypes and end-use parts.
Aerospace and Automotive Industries
In the aerospace industry, weight reduction is crucial. PEEK offers high strength with lighter weight compared to metals, contributing to overall vehicle efficiency. Components made with PEEK can withstand extreme temperatures and pressures, which is essential during flight. Parts like brackets, housings, and fittings benefit from PEEK’s durability and longevity, leading to lower maintenance costs.
The automotive sector similarly benefits from PEEK’s characteristics. With a push for lightweight materials that do not compromise safety or performance, PEEK serves roles in both structural and non-structural parts. Engine components, connectors, and even interior trim pieces can be 3D printed, enhancing design flexibility and leading to faster production cycles.
Medical and Dental Applications
The medical and dental fields are set to gain significantly from PEEK. When used in implants and prosthetics, PEEK's biocompatibility reinforces its value. It mimics natural bone properties, offering a smoother transition for the body. Customizing implants through 3D printing allows for precise fit and reduced surgical time. Moreover, PEEK’s chemical resistance ensures that these components remain sterile, enhancing patient safety.
In dentistry, PEEK can be used for crowns and bridges, providing a strong yet aesthetic solution. This material demonstrates durability that resists wear and tear, crucial for dental applications where stress is common.
Electronics and Insulation Components
PEEK’s insulating properties make it suitable for electronic applications. Its ability to retain performance under thermal and electrical stress makes it ideal for connectors, insulators, and components within devices that require superior reliability. With the growing trend towards miniaturization in electronics, PEEK helps in fabricating smaller, more efficient components without sacrificing performance.
Moreover, the thermoplastic nature of PEEK allows for complex geometries, enabling the design of intricate parts that were previously challenging to achieve. This results in enhanced reliability and performance in electronic devices, ultimately contributing to advancing technology in numerous sectors.
"The versatility of PEEK in 3D printing underscores its significance across various industries, driving innovation and efficiency."
In these applications, the choice of proper temperature settings during 3D printing is essential to maximize the performance and quality of the final products. Therefore, understanding the implications of PEEK’s material properties is vital for successful implementation in these demanding fields.
Future Trends in PEEK 3D Printing
The exploration of future trends in PEEK 3D printing is critical. As industries continue to demand higher performance materials, the evolution of PEEK technology responds to these needs. Developers and manufacturers look at enhancing material properties and developing new processes that optimize PEEK’s capabilities in additive manufacturing. Understanding these trends not only helps in manufacturing but also challenges existing paradigms in materials science.
Advancements in Material Science
Recent advancements in material science are shaping the future of PEEK 3D printing. Researchers are focusing on creating modified PEEK composites that offer improved mechanical properties. This includes increasing impact resistance, flexibility, and resistance to high temperature environments. New formulations are being studied to enhance flow characteristics during printing, allowing for quicker print times without sacrificing quality.
In addition, nanotechnology is being integrated into PEEK formulations. The introduction of nanoparticles can significantly enhance thermal and mechanical properties. Studies show that adding graphene oxide to PEEK can improve conductivity and strength. Furthermore, there is an ongoing investigation of bio-based PEEK materials, which aim to reduce environmental impact without compromising performance.
Potential New Applications
The potential new applications for PEEK 3D printing are vast and varied. In the medical field, biocompatible PEEK is already being utilized for implants and prosthetics. Future developments foresee its use in more complex applications such as drug delivery systems or even tissue engineering, which could revolutionize patient care.
In the aerospace industry, PEEK’s lightweight and high-strength qualities make it suitable for components that require both efficiency and durability. Developments in additive manufacturing techniques could lead to the production of customized parts that meet specific aerodynamics requirements.
Lastly, the electronics sector is expected to benefit significantly. PEEK’s insulating properties and stable performance under varying temperatures make it a prime candidate for electrical housings and insulation layers. This trend could open new avenues for PEEK use in electronic components, enhancing reliability in critical applications.
"The integration of advanced materials technology is set to redefine the boundaries of what is achievable with PEEK in 3D printing."
By staying updated on these trends, professionals can adapt their practices and materials usage to remain at the forefront of innovation in this rapidly evolving field.
Closure
The conclusion serves as a pivotal element in this exploration of PEEK 3D printing, unifying the various discussions and insights presented throughout the article. It encapsulates the critical reasons that underscore the importance of optimal temperature settings in achieving successful prints. By synthesizing the various temperature factors, such as nozzle and bed temperatures and their specific ranges, the conclusion emphasizes how these aspects influence print quality and the structural integrity of the PEEK material.
Addressing potential challenges, such as warping, delamination, and other common printing issues, highlights the relevance of temperature management. A well-rounded conclusion not only summarizes the important findings but also reinforces the necessity of adhering to the recommended settings. This serves to benefit both novice and experienced users in the field.
Understanding the temperature settings is not merely an academic exercise; it directly correlates with enhanced performance and opens up the potential for new applications in various sectors, such as aerospace, medical, and automotive industries.
Summarization of Key Points
- PEEK Material Properties: The importance of recognizing the thermal stability, mechanical strength, and chemical resistance of PEEK.
- Temperature Influence: How both nozzle and bed temperatures directly affect the adhesion of layers and the final print quality.
- Recommended Ranges: The recommended temperature ranges that assist practitioners in fine-tuning their settings for optimal results.
- Common Challenges: Identification of common issues that stem from incorrect temperature settings, such as warping and layer delamination.
Recommendations for Practitioners
For practitioners aiming to optimize their PEEK 3D printing processes, the following recommendations are essential:
- Consistent Monitoring: Regularly check and calibrate printer settings to ensure they align with the recommended temperature ranges.
- Experimentation: Conduct controlled experiments with varying temperatures to determine what works best for specific applications or setups.
- Utilize Proper Filament: Always use high-quality PEEK filament, as this can significantly influence printing success.
- Document Results: Maintain a log of printing conditions and outcomes to build a reference for future projects.
- Join Communities: Engage with online forums and groups, such as those found on reddit.com or specialized Facebook groups, to share experiences and learn from fellow practitioners.
By implementing these strategies, practitioners can enhance their understanding of PEEK 3D printing and improve the quality of their outputs.