Molds and Dies: Principles and Innovations in Manufacturing
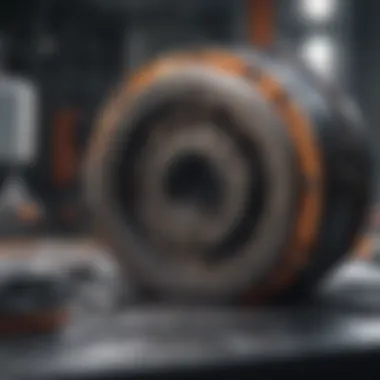
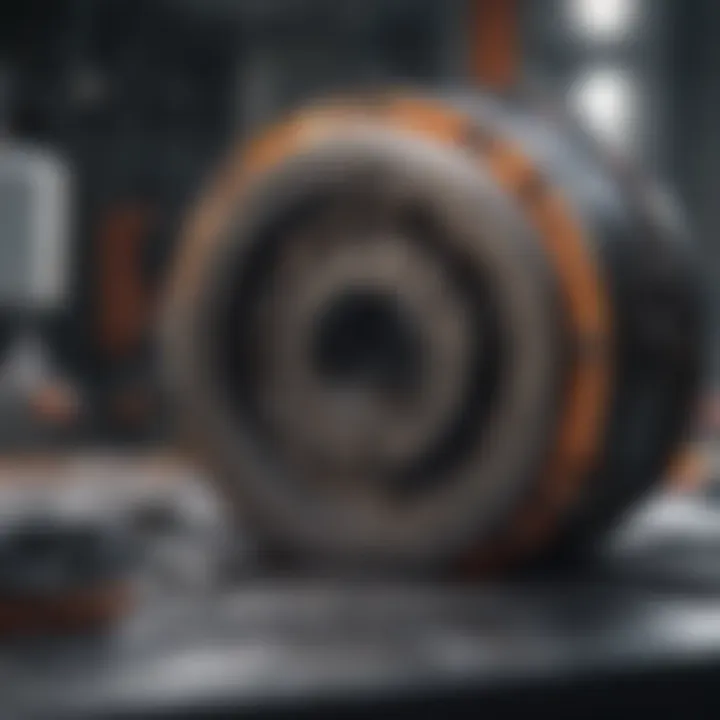
Intro
In the realm of manufacturing, molds and dies serve as the backbone that supports the processes of creating intricate components with precision and efficiency. They may not always be in the spotlight, but their importance cannot be overstated. Whether it’s crafting automotive parts or consumer electronics, these tools are indispensable.
The terms molds and dies often get blended together, yet they denote distinct functions. A mold is typically used to shape materials into three-dimensional objects, while a die is aimed at cutting, shaping, or forming materials—think of a cookie cutter versus a stamp. This article will explore their underlying principles, various types, and their applications across diverse industries.
By diving into advanced manufacturing techniques, we will uncover the innovations shaking things up in this domain. From 3D printing to smart materials, the evolution of molds and dies reflects broader technological trends. The challenges inherently tied to mold design will also be discussed, shedding light on what engineers must navigate.
With an eye on key materials and design aspects, this exploration aims to give scholars, professionals, and anyone interested a thorough understanding of molds and dies. Let's delve deeper into the insights garnered from research and practice.
Prologue to Molds and Dies
The world of manufacturing owes much of its efficiency and precision to molds and dies. These essential tools are used for shaping materials into specific forms during production processes. Understanding how molds and dies function is imperative for those venturing into various industrial fields. They are not just mechanical contraptions; they are the backbone of a plethora of products we engage with daily, ranging from the simplest plastic container to intricate automotive components.
By delving into the principles and applications of molds and dies, we can grasp their significance in optimizing processes, enhancing product quality, and driving innovation in manufacturing. This intricacy in design and function highlights the importance of proper selection, maintenance, and understanding the materials involved, all of which can lead to heightened efficiency and lower costs.
Defining Molds and Dies
Molds and dies, while mentioned in the same breath, have distinct roles in manufacturing. Simply put, molds are hollow shapes that materials like plastic or metal are poured into, allowing them to solidify into the desired form. In contrast, dies serve as tools that cut or shape materials under pressure. Think of it this way: if molds are the containers for creation, dies are the sculptors, carving out the form from raw material.
Types of molds can range from injection molds, often used in mass production of plastic parts, to blow molds utilized for making hollow objects like bottles. Dies too come in various types, with stamping dies shaping metal and cutting dies used for producing precise component shapes. Knowing these distinctions can enhance comprehension of the entire manufacturing landscape.
Historical Context
To appreciate the present, it’s essential to look back at history. The use of molds dates back to ancient civilizations. The Egyptians, for instance, created molds for pottery and metalwork, laying the groundwork for techniques that would evolve over thousands of years. By the time the Industrial Revolution rolled around, the introduction of steam power and mechanization brought about a seismic shift in manufacturing processes.
The mass production era birthed sophisticated mold and die technologies, enabling higher production rates and consistency in quality. For example, the invention of the assembly line by Henry Ford transformed automotive production, allowing for molds and dies to be used more efficiently on a large scale. Today, with advancements in materials and technologies like 3D printing, the landscape of molds and dies continues to evolve, reflecting a constant demand for better, faster, and more cost-effective manufacturing processes.
Types of Molds
Understanding the different types of molds is crucial in grasping the broader spectrum of manufacturing processes. Molds are the backbone of the production line, serving as the vessel into which materials are injected or poured to create a specific shape or form. Selecting the most suitable type of mold can lead to improvements in efficiency, cost management, and product quality.
Each type of mold possesses unique characteristics that meet specific needs depending on the product being manufactured. By examining these types, one can appreciate their applications and understand the considerations necessary for optimal production.
Injection Molds
Injection molds are widely popular in the manufacturing sector, especially for producing large quantities of intricate and precise parts. They operate by injecting molten material—most often plastic—into a closed mold. This process allows for exceptionally complex designs, making it possible to create detailed items such as bottle caps or casing for electronic devices.
A significant advantage of injection molding is its speed. Once the mold is created, it can produce items quickly, enhancing productivity. Furthermore, the precision involved means that each part is consistent, thus minimizing defects. One must consider, however, the initial cost of creating the mold, which can be substantial, particularly for custom designs.
Compression Molds
In contrast to injection molds, compression molds work by placing pre-measured material into an open mold cavity, which is then closed and heated. The heat causes the material to melt and fill the mold, after which it cools and sets into the final shape. This method is commonly employed for rubber and thermosetting plastics.
Compression molding can be less expensive than injection molding, especially for lower volume production. It's also an excellent option for large and heavy parts, such as automotive components. However, the process tends to be slower than injection molding, making it less ideal for high-volume items.
Blow Molds
Blow molds are specifically designed for manufacturing hollow items. The process involves forming a tube of hot plastic, which is then inflated into the mold to take on its desired shape. This technique is the go-to for creating bottles, containers, and similar products made from materials like PET.
What’s notable about blow molding is its material efficiency. The process can produce lightweight containers, thus saving on raw materials. Another perk is the ability to use clear materials, which can enhance product visibility. On the flip side, the design possibilities are somewhat limited compared to solid molding methods, requiring careful consideration of the product's end-use.
Extrusion Molds
Last, but certainly not least, we have extrusion molds. This type is predominantly used for continuous profiles, such as pipes, tubes, and sheets. The process involves forcing softened material through a die, creating a long continuous shape that can be cut to the required length.
Extrusion molding is well-regarded for its efficiency and ability to produce uniform products with minimal waste. The downside, however, is that it is primarily suitable for products with constant cross-sections. Also, complex shapes are a challenge, often requiring additional processing steps.
Understanding these various types of molds reveals the intricacies of the manufacturing process. Each type has its place, and the right choice ultimately hinges on the product requirements, efficiency needs, and cost considerations.
Types of Dies
Diving into the realm of dies is akin to peering into the very machinery that propels the manufacturing world. Dies serve as molds for shaping materials, and understanding their various types paves the way for grasping their significance in the wider context of production. Each type of die has specific roles, advantages, and considerations that make them invaluable. They affect the efficiency, precision, and ultimately, the cost-effectiveness of manufacturing processes.
Stamping Dies
Stamping dies are a crucial component in the metalworking industry. They are used to transform flat sheets of metal into precisely shaped parts through a punching or pressing process. This approach is widely employed in sectors such as automotive and electronics, where parts must be manufactured in large volumes with consistent quality.

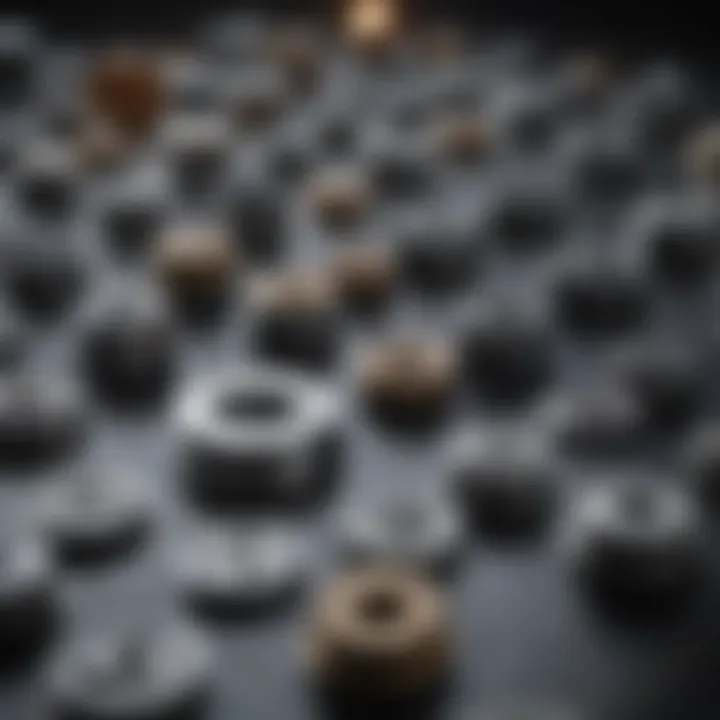
The benefits of stamping dies are numerous:
- Speed: They can operate at a rapid pace, allowing high-volume production while maintaining accuracy.
- Consistency: Once set up, they produce identical parts with minimal variation.
- Cost-Effective: Although the initial investment may be significant, the long-term production efficiency leads to lower costs.
It’s essential to consider the design of stamping dies, as factors like material thickness, die clearance, and press capacity play a pivotal role in achieving the desired outcome. Want to dive deeper? Explore more about this topic on Wikipedia.
Forming Dies
Forming dies, on the other hand, are used to shape metal material into various configurations without cutting. They play a key role in processes such as bending, drawing, and flanging. In essence, forming dies are the hands of manufacturers, capable of taking raw material and giving it a purpose.
The advantages of using forming dies include:
- Material Efficiency: They can create complex shapes without sacrificing much material, making them an eco-friendly choice.
- Strength: The resulting formed parts often have superior mechanical properties, which enhance durability.
- Versatility: They can produce a wide range of shapes, fitting various applications from industrial parts to consumer goods.
Understanding the distinct applications of forming dies is crucial, especially in industries requiring specialized components. These dies are an indispensable part of modern manufacturing, often leveraging advanced materials for even better performance.
Cutting Dies
Cutting dies are like the scissors of the manufacturing world; they slice through materials to produce specific shapes and sizes. They are essential in a variety of applications, from packaging design to automotive parts production.
Here are the main considerations when it comes to cutting dies:
- Precision: Cutting dies are engineered for high precision, ensuring clean edges and the right dimensions every time.
- Durability: Over time, the wear and tear on cutting dies can affect performance. Investing in quality materials can mitigate this risk.
- Application-Specific: Different projects might require different types of cutting dies. Whether it be rotary dies for continuous operations or flat dies for sheet metal, the right choice is crucial.
In summary, a comprehensive understanding of these die types—stamping, forming, and cutting—enables professionals to make informed decisions in their manufacturing processes. As industries continue to evolve, so too does the technology behind dies, which influences efficiency and effectiveness across the board.
Manufacturing Processes Utilizing Molds and Dies
The interplay between molds, dies, and various manufacturing processes is a cornerstone of modern production techniques. By utilizing these tools, industries can achieve precision, efficiency, and cost-effectiveness in their operations. Understanding how these processes work is significant for the continuous innovation that drives the market.
Casting
Casting is one of the oldest manufacturing methods, yet it remains an essential process today due to its versatility and effectiveness. The fundamental principle of casting involves pouring a liquid material—often metal or plastic—into a mold where it solidifies into a desired shape.
Benefits of Casting:
- Complex geometries: Casting allows for the creation of intricate designs that would be hard to achieve using other methods.
- Material efficiency: Utilizes minimal material compared to subtractive manufacturing techniques, reducing waste.
- Cost-effectiveness: Particularly for large production runs, casting can be more economical than other methods due to lower labor costs and the ability to produce multiple parts simultaneously.
Different types of casting methods, such as sand casting, investment casting, and die casting, each come with their unique advantages and considerations. For instance, in die casting, molten metal is forced into a mold cavity under high pressure, which leads to tighter tolerances and smoother surfaces. However, this method requires significant upfront investment in mold creation, making it ideal for high-volume production.
Molding Techniques
Molding techniques cover a broad range of processes that can shape materials using molds. Techniques such as injection molding and compression molding are widely utilized in industries ranging from automotive to consumer goods.
Injection Molding
Injection molding involves injecting molten material into a pre-designed mold. This method is lauded for its ability to produce parts with excellent repeatability and surface finish.
- Applications: Commonly used for manufacturing plastic components, such as bottle caps and part housings.
- Efficiency: High production rates make it an appealing option for projects with large volumes.
However, there are some trade-offs, including longer lead times for mold creation and limitations related to the materials used.
Compression Molding
Conversely, compression molding presses material into molds and utilizes heat to harden it. This technique is often employed for rubber and thermoset plastics.
- Advantages: It is particularly effective for large and thick parts.
- Considerations: Requires careful material selection to ensure compatibility with the process and final application.
Machining Applications
Machining is another significant avenue where molds and dies come into play. Often applied to enhance molded parts, machining processes like milling and turning ensure that the final products meet exact specifications.
- Tolerances: Machining allows for tighter tolerances than many other manufacturing methods.
- Surface finsh: It can significantly improve the surface finish of parts that might otherwise be rough or imprecise.
Through processes such as CNC (Computer Numerical Control), manufacturers can produce components with unparalleled accuracy. While machining typically incurs higher costs due to the lower production rates and material waste, it plays a vital role in industries where precision is non-negotiable, such as aerospace and medical device manufacturing.
To summarize, molds and dies are not merely tools but essential components that enhance various manufacturing processes like casting, molding, and machining. Their roles significantly contribute to achieving efficiency, scale, and precision in manufacturing settings.
Material Selection for Molds and Dies
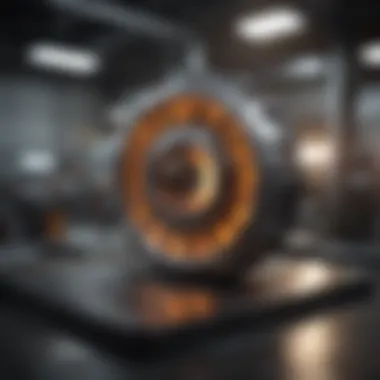
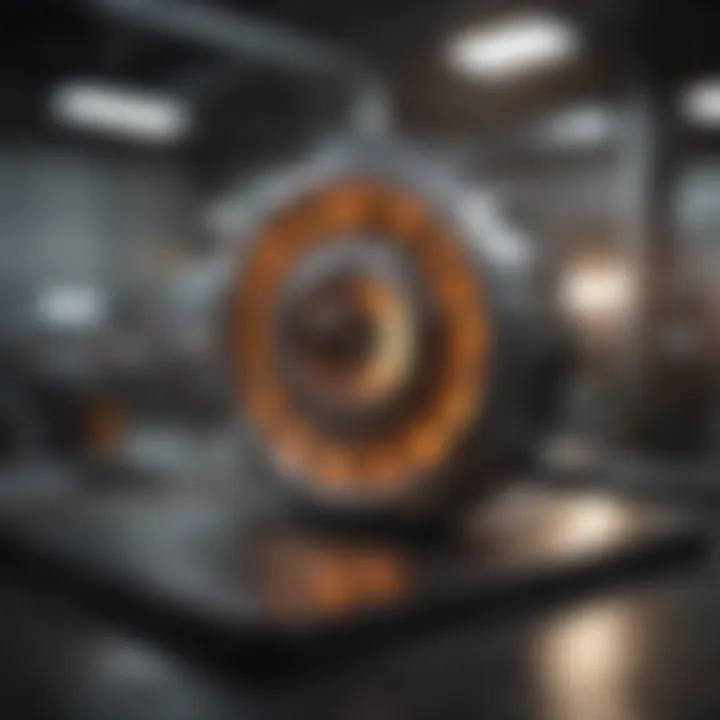
Choosing the right material for molds and dies is a cornerstone of effective manufacturing. This selection isn’t merely a technical decision; it threads through the entire manufacturing process, impacting not only the durability and efficiency of production but also the overall quality of the end products. The importance of material selection is underscored by several key benefits that it brings to the table. These include:
- Durability: Molds and dies face intense conditions during their operation, including high pressure and temperatures. Selecting materials that can withstand such conditions ensures longevity.
- Cost-Effectiveness: The right material helps in achieving optimal use of resources, ultimately lowering costs associated with frequent replacements or repairs.
- Quality of Output: Quality of the molded or stamped product is greatly influenced by the material's performance, directly affecting surface finish and dimensional accuracy.
Thus, understanding the specific requirements of the molding or die application is crucial. The choice must consider factors such as the type of material being processed, the production volume, and environmental conditions which the molds and dies will encounter.
Common Materials
In the realm of molds and dies, common materials typically include:
- Steel: Generally regarded as the go-to material. Its robustness makes it suitable for high-volume production, particularly in injection molding.
- Aluminum: Lighter and easier to machine compared to steel, aluminum is often favored for lower volume runs. It can reduce cycle times due to its thermal conductivity, facilitating quicker cooling.
- Bronze and Copper Alloys: Known for their excellent thermal conductivity, these materials are beneficial in applications where heat dissipation is critical.
Despite their widespread use, it's worth noting that while these materials are effective, they come with their own set of challenges. For instance, steel molds can be expensive to manufacture, leading to a longer break-even time. Aluminum, although cheaper, may not withstand as much wear and tear as steel, thus necessitating careful consideration depending on the production needs.
Advanced Materials
As technology advances, the selection of materials also evolves to include more advanced options, like:
- Composite Materials: These are engineered combinations that offer tailored properties. For instance, fiber-reinforced composites can provide a balance between strength and weight, making them advantageous for specialized applications.
- High-Performance Polymers: Suitable for molds that require a combination of heat resistance and flexibility. These polymers can retain their shape under temperature fluctuations, which is vital for consistent production.
- Tool Steels: They undergo special treatments to enhance their properties, making them ideal for highly demanding applications. They can offer superior wear resistance and toughness, contributing to a longer lifespan.
In summation, material selection in mold and die manufacturing is a nuanced process that requires educating oneself on both common and advanced materials. This choice affects durability, cost, and ultimately, product quality. The importance of these considerations cannot be overstated, as they lay the foundation for successful manufacturing practices in various industries.
Design Considerations
Design considerations play a critical role in the successful manufacturing of molds and dies, influencing everything from initial design sketches to final production quality. To grasp the full scope of molds and dies, it's vital to look closely at specific elements within design that can affect the performance and longevity of these tools. This encompasses aspects such as the selection of materials, geometric configurations, cooling and heating systems, and the integration of modern design tools.
Effective design not only streamlines the production process but also minimizes costs and increases the product lifecycle. Therefore, having a robust design strategy is tantamount to ensuring that molds and dies can efficiently produce high-quality components. Beyond basic functionality, the right design helps in sustaining productivity and reducing waste during manufacturing. Here, I will explore further into two key components of design: the application of CAD software and the critical nature of tolerances.
CAD Software in Design
Computer-aided design (CAD) software has revolutionized the way molds and dies are created, providing manufacturers with precision tools that facilitate complex and intricate designs. In contrast to traditional hand-drawn methods, CAD enables engineers to model their ideas in 3D before a single piece of material is cut. This capability is paramount in identifying potential flaws early in the design process.
Several significant benefits come from utilizing CAD:
- Precision: CAD software allows for millimeter accuracy, ensuring that every dimension conforms to specifications.
- Visualization: Designers can create visual representations of finished products, allowing for better critique and modification before physical production.
- Simulation: With tools integrated into CAD for stress testing and performance evaluation, potential issues can be diagnosed before they become costly errors in the production stage.
"CAD is not just a tool; it's a pathway to realizing design potential that was once locked away in an engineer's mind."
Importance of Tolerances
Tolerances in mold and die design are essential parameters that dictate the allowable deviation from specified dimensions. They are crucial not only for ensuring parts fit together properly but also for maintaining consistent quality across large production runs. Tight tolerances can be the difference between a well-functioning component and a malfunctioning one.
Here are a few reasons why tolerances cannot be overlooked in design considerations:
- Compatibility: Ensuring components fit together without interference or excessive gaps often requires established clear tolerances.
- Interchangeability: In industries where parts are swapped frequently, defining tolerances assists in producing interchangeable components, simplifying repairs and replacements.
- Cost Efficiency: Balancing tight tolerances with production costs is a subtle art. While tighter tolerances often lead to increased production costs, too loose can mean failures and hence, costs in repairs.
Designing molds and dies may seem like the nuts and bolts of manufacturing, yet it requires a significant understanding of geometry, material properties, and modern technology. Integrating the use of CAD along with meticulous attention to tolerances ensures that molds and dies function optimally in actual manufacturing settings.
Challenges in Mold and Die Manufacturing
When discussing the realm of molds and dies, it is crucial to recognize the myriad challenges faced in their manufacturing process. These challenges are not merely hurdles; they are fundamental issues that can affect productivity, cost, and ultimately, product quality. Understanding these challenges gives insight into what drives innovation in mold and die production, and why constant advancements are necessary in this field.
Wear and Tear
Wear and tear on molds and dies is a persistent issue that rears its head throughout their lifecycle. As these tools are extensively used in various applications, they often experience significant physical degradation. The materials that make up molds and dies, despite being designed for durability, can suffer from repeated stress, leading to issues such as dimensional changes and surface imperfections. This deterioration affects the quality of the final product, resulting in defects that can cascade through the manufacturing process.
To mitigate wear and tear, employing advanced materials like high-strength steel or carbide is often a step in the right direction. It is also beneficial to implement regular maintenance schedules and adopt the latest surface treatment technologies. These technologies can significantly enhance the lifespan of molds and dies, making the initial investment more viable. Engaging in proactive maintenance not only saves costs in the long run but also ensures consistency in product quality.
Cost Management
Cost management is another significant concern in the mold and die manufacturing sector. The complexity involved in designing and fabricating these tools can lead to unexpected expenses. Companies may encounter hidden costs associated with material waste, labor, and the procurement of specialized components. Additionally, market fluctuations can impact the costs of raw materials, ultimately squeezing profit margins.
To better manage these expenses, organizations need a robust financial strategy that takes into account not just the direct costs of manufacturing but also the indirect costs. Several techniques can assist in this regard:
- Lean Manufacturing: Adopting lean practices minimizes waste and optimizes production workflows.
- Digital Technology: Implementing software solutions can enhance cost tracking and help identify areas for improvement.
- Supplier Relations: Strong partnerships with suppliers might lead to better pricing and material options.
Quality Control Issues
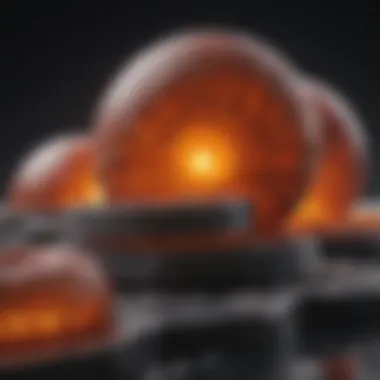
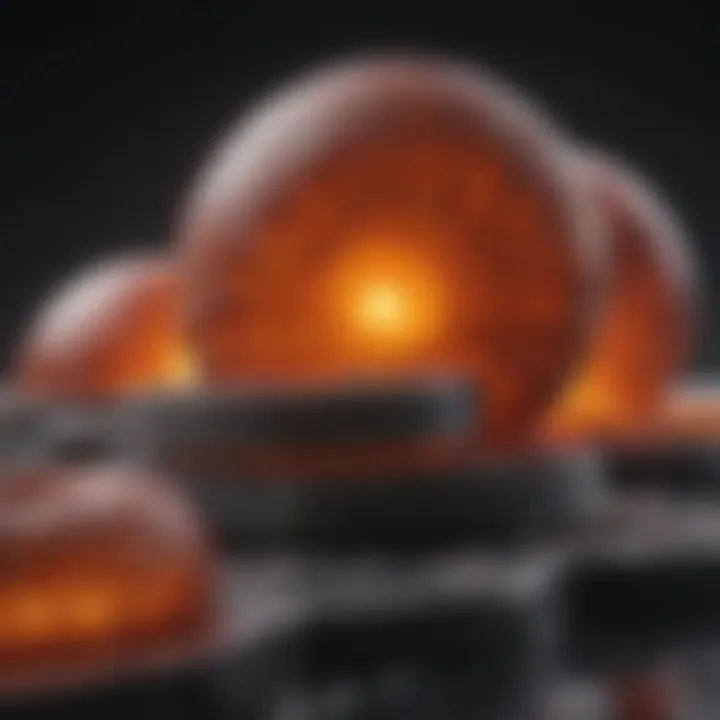
Quality control in the mold and die manufacturing process is paramount, yet it can also be fraught with challenges. Ensuring that molds and dies meet stringent specifications requires meticulous attention to detail at every stage of production. Any lapse can result in defective products that end up costing not only money but also reputation.
One common issue in quality control is the lack of standardized testing procedures. Inconsistent practices can lead to various defects, including dimensional errors and surface flaws. To address this, manufacturers should consider establishing comprehensive quality management systems, employing statistical process control (SPC) methods, and using advanced diagnostic tools.
Moreover, training personnel on quality standards is also vital. A well-trained workforce can identify potential issues before they escalate. As highlighted in a recent industry report, "Quality control should not be an afterthought. It's a vital part of ensuring long-term success."
In sum, the challenges of wear and tear, cost management, and quality control in mold and die manufacturing are intricately linked. Addressing them is not only vital for operational efficiency but also essential for maintaining competitive advantage in a fast-evolving manufacturing landscape.
The Role of Technology in Molds and Dies
Technology plays a foundational role in the field of molds and dies, driving innovation and efficiency in manufacturing processes. The seismic shifts brought about by modern technology have revolutionized traditional methods, enabling manufacturers to create more intricate designs while also reducing time and costs. This interplay between advanced tech and mold-making is not just a trend; it is an essential evolution that caters to the competitive demands of today’s market.
3D Printing Applications
3D printing, also known as additive manufacturing, has started to carve out a significant niche in mold and die creation. It allows for the production of prototypes and even final products with remarkable precision and speed. The beauty of 3D printing lies in its ability to create complex geometries that may be challenging or even impossible to achieve with traditional molding methods.
- Speed: It dramatically reduces lead times. Instead of waiting weeks to produce a die, a functional prototype can be printed in a matter of hours, allowing for faster iteration.
- Cost-Effectiveness: The materials used in 3D printing, like thermoplastics or resin, often come at a lower cost compared to traditional metals or alloys.
- Customization: Each mold can be tailored to specific applications, reducing waste and leading to a more sustainable manufacturing process.
However, the transition to 3D printing is not without hurdles. One must consider the limitations concerning the materials and the mechanical properties of the printed items. Despite these challenges, industries are increasingly looking toward 3D printing for its potential to enhance productivity and creativity in mold design.
"Technology is not just a tool; it's a partner in design and manufacturing, reshaping the possibilities of what can be achieved with molds and dies."
Automation and Efficiency
The advent of automation in mold making brings another layer of efficiency that was previously unattainable. Automated machinery allows manufacturers to streamline operations, reducing both human error and production time.
- Precision: Automated processes ensure that every cut, every mold, and every assembly comes out perfect, significantly enhancing quality control.
- Scalability: Automated systems can easily scale up production without significant adjustments, accommodating fluctuating demand effortlessly.
- Data Integration: By incorporating IoT and smart technology, manufacturers can track the performance and condition of molds in real-time. This leads to proactive maintenance, ultimately increasing the lifespan of molds and dies and preventing costly downtime.
Nonetheless, implementing automation comes with its own set of considerations. Initial investments can be high, and there might be a learning curve associated with the new technology for workers. Balancing human oversight with automated efficiency is crucial to reap the full benefits without losing the craftsmanship that molds and dies require.
In summary, the integration of technology in molds and dies—particularly through 3D printing and automation—has changed the landscape of manufacturing. It not only improves efficiency but also enables creativity and customization to flourish, catering to the evolving needs of various industries.
Future Trends in Molds and Dies
The realm of molds and dies is not static; it’s a constantly evolving landscape fueled by innovation and the pressing need for sustainability. In recent years, a notable shift has been observed towards integrating smarter manufacturing processes alongside eco-friendly practices. Understanding future trends in molds and dies is paramount as these changes promise to not only enhance efficiency but also reduce environmental impact in production lines.
Sustainability Practices
The importance of sustainability in the manufacturing sector is no longer a mere buzzword; it’s a directive that shapes industry standards. Manufacturers are increasingly pushed to minimize their ecological footprints, and this applies directly to the design and production of molds and dies. Implementing sustainable practices can take multiple forms:
- Material Selection: Utilizing recyclable materials or compostable compounds in the fabrication of molds reduces waste that often ends up in landfills. Biodegradable polymers can serve as an alternative without compromising functionality.
- Energy Efficiency: Production processes can be optimized to consume less energy. For instance, newer mold designs allow for quicker cycle times and lower heat requirements. This efficiency not only decreases operational costs but also aligns with global energy conservation goals.
- Waste Reduction Techniques: Manufacturers are adopting methods such as Lean Manufacturing to minimize waste during production processes. This means every scrap of material is considered and either reused or recycled, creating a more circular economy.
Transitioning towards sustainable molds and dies is more than just a trend; it’s a crucial step towards ensuring a viable future for manufacturing.
"Sustainable practices in mold and die production not only pivot us towards a greener planet but also often lead to cost savings in the long run."
Smart Manufacturing
The integration of smart technology in the manufacturing sector stands at the forefront of the next industrial revolution. Smart manufacturing encapsulates the use of automated systems, data analytics, and the Internet of Things (IoT) to make production processes more intelligent and interconnected. Key elements of this trend include:
- Automation: Employing robotic systems can streamline repetitive tasks in the mold and die production. This not only speeds up the process but also enhances precision, as machines can often perform tasks with higher accuracy than human hands.
- Real-Time Monitoring: IoT devices allow for real-time data collection and analysis. By monitoring mold performance and wear, manufacturers can anticipate failures before they happen, leading to less downtime and better overall machine health.
- Predictive Maintenance: Using advanced analytics, production teams can predict when molds or dies may fail and need maintenance. This predictive capability shifts maintenance practices from reactive to proactive, maximizing efficiency.
Finale and Implications
The exploration of molds and dies reveals their vital role in manufacturing processes across various sectors. As we dissected the principles, applications, and innovations associated with these tools, it becomes clear that they are more than mere implements; they are the backbone of production in industries from automotive to consumer goods. The efficiency with which we design and utilize molds and dies directly affects product quality, manufacturing cost, and time to market.
One of the most significant takeaways from this article is the continuous advancements in materials and technologies. We live in an age where traditional processes meet cutting-edge tech. Innovations like 3D printing not only optimize design but also make customization more accessible. This is a game-changer for manufacturers looking to keep up with fast-changing consumer demands.
Moreover, the implications of sustainable practices are becoming increasingly apparent. The emphasis on reducing waste and energy consumption provides an avenue for companies to enhance their reputations and profitability. Adopting greener manufacturing techniques, such as recyclable molds or energy-efficient machinery, isn’t just an ethical choice; it's also a business strategy that can yield financial returns.
"Efficient molds and dies not only streamline production but also contribute to sustainability."
Another key element is the importance of quality control. With the enhanced precision that modern die-making technologies offer, the challenge is not just about creating parts but ensuring they meet stringent quality standards. Technologies that assist in real-time quality assessment can undoubtedly mitigate risks and improve outcomes.
In summary, molds and dies are integral to the landscape of modern manufacturing. They symbolize not just tools of the trade but also reflect how innovation and sustainability can coexist in the industry.
Summary of Key Insights
- Technological Advancements: Innovations, like 3D printing, allow for rapid prototyping and customization while improving efficiency.
- Material Choices: The shift toward advanced materials enhances durability and reduces costs.
- Sustainability: Producers are adopting eco-friendly practices that not only reduce harm to the environment but also provide competitive advantages.
- Quality Assurance: With enhanced precision comes the need for robust quality control systems to avoid production errors.
Looking Forward
Moving ahead, the future is bright for molds and dies as they evolve in tandem with manufacturing technologies. Industries are beginning to focus on integrating smart technologies into traditional practices. For instance, the implementation of IoT in manufacturing can help monitor the efficiency and performance of molds and dies, providing data that can lead to better decision-making.
Furthermore, the rise of personalized products indicates a shift towards bespoke manufacturing solutions. As consumer preference leans toward individualized items, molds and dies may need to become more adaptable and multi-functional.