Exploring Magnesium Alloys: Properties and Applications
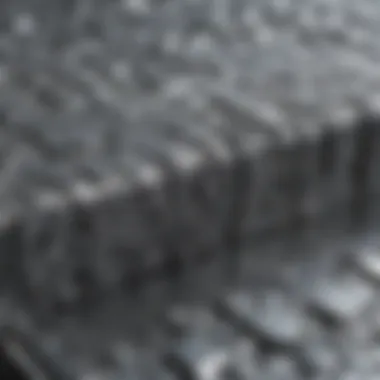

Intro
Magnesium alloys have carved out a significant niche in modern engineering, transportation, and various structural applications. Light yet strong, these materials present an intriguing alternative to traditional metals. In an age where efficiency and sustainability are paramount, understanding the properties and applications of magnesium alloys becomes essential for anyone involved in material science or industrial engineering. The journey of exploring magnesium alloys begins with an appreciation of their unique chemical and physical characteristics.
Key Findings
Major Results
Magnesium alloys are primarily composed of magnesium combined with other elements such as aluminum, zinc, and manganese which enhance their strength and corrosion resistance. The relative lightweight of these alloys—about one-third the weight of aluminum—provides a substantial advantage in applications requiring weight reduction, such as automotive and aerospace industries.
One of the standout features of magnesium alloys is their excellent machinability, which allows for intricate designs that can be milled or cast with relative ease, thus opening a gateway to innovative engineering solutions. Moreover, magnesium exhibits a unique property known as damping capacity, which reduces vibration and noise. This is particularly useful in sectors like transportation where sound dampening translates to a more comfortable user experience.
Discussion of Findings
The versatility of magnesium alloys cannot be overstated. In the automotive industry, manufacturers have increasingly turned to these materials for components such as wheels and transmission casings, driven by stringent fuel economy requirements. Moreover, in aerospace, magnesium’s favorable strength-to-weight ratio contributes to fuel efficiency, directly impacting operational costs.
"The true potential of magnesium alloys lies in their adaptability to core engineering challenges, promising innovative future solutions."
With ongoing research initiatives focused on improving magnesium’s recycling processes and performance characteristics, the horizon looks bright for these alloys. Engineers and researchers are meticulously studying phase transformations and alloying effects to push the boundaries of what is possible. Their efforts lead to advancements not only in performance but also in reducing environmental impacts, ultimately paving the way for sustainable development in various industries.
Methodology
Research Design
This article employs a comprehensive review methodology, analyzing current literature and case studies to delineate the multifaceted applications of magnesium alloys. By synthesizing findings from various sources, we construct a cohesive understanding of how these alloys impact industrial practices.
Data Collection Methods
Data was collected through extensive secondary research, including:
- Scholarly articles and journals
- Industry reports focused on material applications
- Online platforms like Wikipedia and Britannica for background information
- Discussion forums on Reddit for insights into real-world applications and user experiences.
Through this methodological approach, we aim to generate a thorough narrative on the properties and evolving applications of magnesium alloys, informed by both academic and practical perspectives.
Prolusion to Magnesium Alloys
Magnesium alloys are not just a footnote in the world of materials. Rather, they stand as a testament to cutting-edge engineering and a response to the pressing demands of modern industries. These alloys, primarily made up of magnesium and varying alloying elements, boast exceptional properties that set them apart from other materials. With a keen interest in sustainability and performance, sectors like aerospace, automotive, and consumer electronics increasingly rely on magnesium alloys to meet rigorous standards while being cognizant of weight and environmental impact.
Definition and Composition
At its core, magnesium is a lightweight metal, with an atomic number of 12. When combined with other elements—such as aluminum, zinc, or manganese—it forms magnesium alloys. These combinations enhance certain properties, making them more suitable for various applications. For instance, when magnesium is alloyed with aluminum, the result is an increase in strength and corrosion resistance.
The typical composition of magnesium alloys, based on the desired properties, often includes:
- Aluminum (Al): Boosts strength and reduces weight.
- Zinc (Zn): Enhances hardness and improves machining capabilities.
- Manganese (Mn): Improves corrosion resistance and ductility.
- Silicon (Si): Aids in casting and reduces oxidation.
The beauty of magnesium alloys lies in their versatility; tweaking the alloying elements can lead to specific characteristics tailored for particular uses.
Historical Context and Development
The journey of magnesium alloys is both fascinating and revealing. The first known extraction of magnesium dates back to 1808, but it wasn't until the early 1900s that the alloys started to gain traction. Early applications were limited due to the high cost of production and the challenges related to corrosion and workability. However, during World War II, engineers discovered their potential in aircraft production, valuing the significant weight reduction they offered. At that time, magnesium was dubbed the “metal of the future.”
As technology advanced, researchers began exploring ways to enhance the properties of magnesium alloys further. The post-war period saw a surge in innovation, with substantial findings in alloy composition, resulting in stronger and more durable materials. Today, ongoing research continues to unlock new possibilities, ensuring magnesium alloys retain their status in modern manufacturing and engineering practices.
"As we aim for lighter, more efficient designs, magnesium alloys serve as a critical component in achieving these goals."
From aerospace to automotive, understanding the definition and historical context of magnesium alloys sets the blueprint for exploring their fundamental properties and wide-ranging applications.
Fundamental Properties of Magnesium Alloys
Understanding the fundamental properties of magnesium alloys is crucial, as these characteristics dictate their performance in various applications. Magnesium is the lightest structural metal used in engineering, making it highly valuable in industries looking to reduce weight without compromising strength. Its unique properties offer numerous benefits that engineers and designers can leverage for more efficient and innovative solutions. This section will break down the mechanical and physical properties of magnesium alloys, exploring how they influence their application and versatility.
Mechanical Properties
Tensile Strength
Tensile strength evaluates the ability of a material to withstand pulling forces. For magnesium alloys, this characteristic is particularly significant as it reveals how well they can perform under stress. Magnesium alloys usually exhibit a tensile strength that, while lower than that of stronger metals like titanium, is still commendable when considering their density.
The key feature of tensile strength is that it allows magnesium alloys to endure significant loads while remaining comparatively lightweight. This property makes them a favored choice in fields such as aerospace and automotive, where every kilo counts. However, the trade-off can be the need for reinforcement in high-stress applications, which sometimes requires combining them with other materials to enhance their overall strength.
Hardness
Hardness, a measure of a material's resistance to localized plastic deformation, also plays a vital role in magnesium alloys. The hardness level determines how well these alloys can withstand denting or scratching, particularly in demanding environments. This characteristic is essential for manufacturing processes that put parts through rigorous tasks, such as machining or operating under friction.
A notable feature of hardness in magnesium alloys is their ability to be heat-treated, which optimizes this property further. As a result, they can become suitable for applications where surface integrity is paramount. Yet, this advantage can come with its own set of challenges, especially if the hardness leads to brittle behavior under certain conditions.
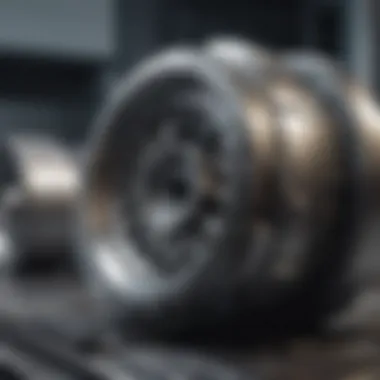

Ductility
Ductility refers to the extent to which a material can deform under tensile stress. It’s a quality that speaks volumes about how magnesium alloys can be manipulated without breaking, giving designers flexibility when creating parts. Magnesium alloys typically exhibit good ductility, allowing them to be shaped into complex geometries – an appealing aspect for many applications.
The prime advantage of ductility is the potential for intricate designs that can enhance the functionality of products. However, excessive ductility can sometimes lead to issues like warping or deformation under load in certain conditions. Finding the right balance, therefore, is critical in utilizing this property effectively.
Physical Properties
Density
Density, the mass per unit volume of a material, is a cornerstone property of magnesium alloys. Magnesium is naturally lightweight compared to other metals, which is a significant boon for applications that prioritize reduced weight. The low density contributes to improved fuel efficiency in vehicles and aircraft, delivering substantial savings in operating costs.
Since density affects the overall performance in applications, it’s advantageous for components to maintain low weight without compromising structural integrity. However, while low density is beneficial, it must be paired with sufficient strength to avoid failures under load, making the engineering choices surrounding alloying elements crucial.
Thermal Conductivity
Thermal conductivity measures a material's ability to conduct heat. Magnesium alloys' efficiency in conducting heat is a key characteristic, especially where heat dissipation is a concern, such as in electronics. Good thermal conductivity helps prevent overheating, making magnesium an attractive option for consumer devices.
The unique thermal conductivity of magnesium alloys can also be a double-edged sword. While it aids in thermal management, it necessitates careful design considerations to avoid thermal fatigue in high-temperature applications. Engineers need to strategize around this property to ensure durability and performance.
Electrical Conductivity
Electrical conductivity indicates how well a material can conduct an electric current, which can be especially important for certain applications in electronics and electrical engineering. Magnesium alloys don’t have the highest electrical conductivity compared to metals like copper, but they still possess sufficient conductive properties for various uses.
The beneficial aspect of electrical conductivity in magnesium alloys is initially attractive in lightweight and portable devices. However, when deciding on using magnesium alloys in circuit boards or similar applications, careful attention must be paid to their limitations regarding conductivity to ensure they meet the electrical demands of the devices they are used in.
Corrosion Resistance
Corrosion resistance is a significant factor influencing the deployment of magnesium alloys. Magnesium, while being an excellent material for lightweight applications, is susceptible to corrosion, especially in harsh environments. This vulnerability might limit its use in areas exposed to moisture or salt.
To counteract this disadvantage, engineers often integrate protective coatings or surface treatments to enhance corrosion resistance. Despite these enhancements, the natural tendency of magnesium to corrode remains a consideration in design stages. As such, ongoing research aims to improve and innovate surface treatments, aiming for both functional performance and longevity of magnesium alloy components.
"The balance of properties in magnesium alloys is essential for creating effective, lightweight components that thrive in demanding situations. Careful consideration of these aspects can lead to groundbreaking applications that solve problems in a range of industries."
By gaining a thorough understanding of these fundamental properties, stakeholders can make informed decisions about the implementation of magnesium alloys in various sectors, pushing the envelope of technology and engineering.
Types of Magnesium Alloys
When delving into the realm of magnesium alloys, understanding their classifications becomes paramount for researchers and engineers alike. Each type bears distinct characteristics that cater to specific applications, ensuring that the unique properties of magnesium can be harnessed effectively. The two primary categories of magnesium alloys are wrought alloys and cast alloys, each with its own set of advantages and considerations.
Wrought Alloys
Wrought magnesium alloys are notable for their malleability, allowing them to be shaped through mechanical processes such as rolling or forging. This category is often chosen for applications where high strength and good ductility are crucial. The processed materials can be used to create intricate components that must endure significant mechanical stress.
Key characteristics of wrought alloys include:
- Versatility in Manufacturing: The ability to be shaped into complex forms gives wrought alloys an edge, especially in aerospace and automotive sectors.
- Enhanced Mechanical Properties: The refining of microstructures through wrought processing results in improved tensile strength and ductility, essential for components subjected to dynamic loads.
One widely recognized example of a wrought magnesium alloy is AZ31, which is popular for its balance of strength and weight. Due to its favorable properties, it's frequently incorporated in vehicle frames and various structural applications. Overall, wrought alloys have emerged as a staple in industries that prioritize lightweight yet robust components.
Cast Alloys
In contrast, cast alloys are produced by pouring molten metal into molds, allowing for complex shapes and larger components to be created with relative ease. This method is favored in scenarios where intricate designs or significant mass is needed, particularly in automotive and aerospace applications.
The benefits of cast magnesium alloys include:
- Cost-Effectiveness for Large Parts: Casting is often more economical for producing larger components since it minimizes material wastage during fabrication.
- Diversity in Alloys: Different alloying elements can be incorporated during the casting process, enabling customization to meet specific performance requirements.
An example of a cast magnesium alloy is AZ91, which showcases high fluidity and good corrosion resistance, making it an ideal choice for components like engine blocks and other cast parts. Despite facing challenges such as lower strength compared to wrought alloys, cast alloys occupy a unique position, meeting specific needs across various industries.
The choice between wrought and cast magnesium alloys ultimately hinges on the requirements of the application, factoring in aspects like weight, strength, and manufacturing considerations.
Applications of Magnesium Alloys
Magnesium alloys play a crucial role across multiple industries, showcasing their versatility and unique characteristics. With their lightweight nature, these alloys contribute significantly to advancements in aerospace, automotive, consumer electronics, and sporting goods. Understanding how and why these alloys are utilized can guide further innovations and applications, and provide insights into their broader significance in modern engineering and design.
Aerospace Industry
Weight Reduction
One of the most prominent benefits of magnesium alloys in the aerospace industry is weight reduction. This is pivotal when it comes to aircraft design. A lighter aircraft can lead to enhanced performance and increased payload capacity. In this context, magnesium's low density is a key characteristic, making it a favored material for various components. Aircraft manufacturers are keenly adopting magnesium alloys for elements such as brackets, housings, and some structural components, underscoring its vital role.
Magnesium alloys offer a sweet spot: they provide strength while keeping the overall weight down, which is paramount in aviation where every ounce counts. However, this trait also comes with a caveat; engineers must ensure that the strength-to-weight balance is maintained, which sometimes requires combining magnesium with other materials. This careful balancing act is what makes magnesium alloys a popular choice, as manufacturers and engineers seek the perfect blend of performance and efficiency.
Fuel Efficiency
Fuel efficiency is another key aspect where magnesium alloys shine in the aerospace sector. A lighter aircraft not only lifts off with less energy but also consumes less fuel during flight. Given the backdrop of rising fuel costs and environmental concerns, utilizing magnesium alloys can substantially lower operational expenses while decreasing carbon emissions.
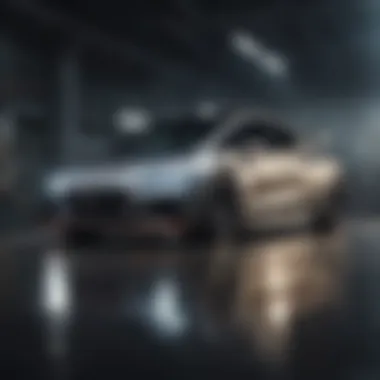

The ability of magnesium alloys to contribute to a more sustainable future is significant. Airlines and manufacturers are increasingly recognizing this attribute and are adopting these alloys to improve their ecological footprint. However, while these benefits are compelling, challenges like the manufacturing process and recycling still persist. The potential for innovation in production techniques remains high, promising a future where magnesium alloys may play an even larger role in the industry.
Automotive Sector
Chassis Components
In the automotive world, magnesium alloys are steadily gaining traction, especially in chassis components. Their lightweight nature enables vehicles to achieve superior performance metrics, such as enhanced handling and stability. As safety regulations evolve, minimizing weight without compromising structural integrity has become a priority in car design.
The low density of magnesium alloys allows for the creation of complex geometries that are strong yet lightweight. This flexibility is attractive to automakers who seek to improve fuel efficiency while maintaining safety standards. However, a fair share of challenges exists, primarily regarding cost and availability that could hinder broader adoption. Despite these hurdles, the automotive sector's shift towards lightweight materials clearly emphasizes the growing acceptance of magnesium alloys.
Engine Parts
Engine parts made from magnesium alloys also deserve mention due to their crucial role in performance. By being lighter than traditional materials, these components can lead to a more agile engine response and better overall vehicle performance. The potential for reducing vibrations creates a smoother ride, which is increasingly important to consumers.
However, the durability of magnesium engine components is often a concern. While they can withstand high temperatures, special consideration must be given to how these parts are treated to avoid corrosion. Engineers are actively working on surface treatments to enhance durability, which will ultimately dictate how widely these alloys can be incorporated into future engine designs.
Consumer Electronics
Portable Devices
In consumer electronics, magnesium alloys significantly contribute to the design of portable devices. Their lightweight properties allow electronics manufacturers to create thinner and more portable gadgets without losing structural integrity. The aesthetic appeal of magnesium—often combined with sleek designs—further enhances its desirability.
Magnesium’s capability to absorb impacts can also lead to increased longevity of products, a feature valued by consumers. However, considerations around cost and manufacturability remain important. Balancing these factors is key for companies looking to innovate while keeping prices competitive.
Durability
Durability is a characteristic that can't be overlooked in the realm of consumer electronics. Magnesium alloys not only provide sturdiness but also tend to withstand everyday wear-and-tear better than many conventional materials. This durability is crucial for various applications, especially when it comes to devices that are constantly on the move.
Though durability is a strong selling point, the susceptibility of magnesium to corrosion poses challenges. Coating and surface treatment innovations are ongoing, aimed at enhancing the lifespan of products without compromising their lightweight benefits. It’s this delicate balance of properties that defines the utility of magnesium alloys in electronics.
Sporting Goods
Performance Equipment
When it comes to sporting goods, magnesium alloys are making a mark, particularly in performance equipment. Athletes benefit from the lightweight characteristics of such equipment—from bicycles to fishing rods—allowing for enhanced performance and agility. The rigidity of magnesium contributes to improved efficiency in motion, making it a go-to choice among sports manufacturers aiming to give athletes an edge.
Yet, where there's a benefit, there are challenges, too. The cost of production and potential problems with material fatigue over time can be issues that brands need to address as they work on delivering quality sporting goods.
Lightweight Structures
In the realm of sports, lightweight structures crafted from magnesium alloys provide distinct advantages. Structures, such as frame components for bikes or ski equipment, exhibit remarkable strength while maintaining low weight. This is key for athletes who require optimal performance without the hindrance of excessive gear.
However, the manufacturing complexities associated with producing lightweight magnesium structures are significant. Innovations in fabrication processes are essential for overcoming these barriers, paving the way for a broader application of these materials in high-performance sports equipment.
"The unique balance of strength and weight in magnesium alloys makes them a game-changer across various fields, driving innovation and sustainability" – Industry expert.
Advantages of Using Magnesium Alloys
Magnesium alloys stand out in the landscape of materials engineering due to their notable advantages. These benefits make magnesium alloys an attractive option in various applications, especially where weight and performance are paramount. Let’s delve into the specific elements of their advantages and how these properties can greatly influence future innovations in material usage across industries.
Lightweight Characteristics
One of the most immediate attributes of magnesium alloys is their lightweight nature. Being the lightest structural metal, magnesium weighs roughly two-thirds less than aluminum and one-fourth that of steel. This makes it ideal for applications where reducing mass is critical.
In transportation sectors, for instance, lighter materials contribute significantly to efficiency. Reducing weight can enhance fuel economy in vehicles. Take, for example, the use of magnesium components in cars, like door frames and seat structures. The lighter these parts are, the less energy the vehicle requires to operate. Hence, from an environmental perspective, optimizing weight with magnesium alloys leads to lower carbon footprints.
High Strength-to-Weight Ratio
Closely linked to its lightweight properties is the impressive strength-to-weight ratio of magnesium alloys. Their ability to retain strength while minimizing mass is invaluable. This means that when manufacturers choose magnesium, they can achieve significant structural integrity without the drawbacks of bulkier materials.
When you think about aerospace applications, this property is crucial. Components like engine casings and airframes benefit immensely from magnesium's high strength-to-weight ratio. For example, using magnesium alloys in airplane manufacturing not only makes the aircraft lighter, which improves fuel efficiency, but also increases payload capacity. Developing alloys that enhance this strength further can lead to even more robust designs in future aerospace projects.
Recyclability and Sustainability
As industries push towards more sustainable practices, the recyclability of magnesium alloys shines as a key advantage. These alloys can be recycled without loss of properties, which aligns perfectly with a growing demand for sustainable materials. This aspect is becoming more critical, considering the global focus on reducing waste and conserving resources.
From an economic perspective, recycling magnesium can be beneficial for companies, as less energy is required to process recycled magnesium compared to extracting raw components. Additionally, recycling aligns with the principles of the circular economy. By adopting processes that prioritize the reuse of materials, industries can reduce their environmental impact while also cutting costs.
"The recyclability of materials is not just an option; it's a necessity in the modern manufacturing landscape."
In summary, the advantages of magnesium alloys position them as a dynamic choice for a variety of industries. Their lightweight characteristics, high strength-to-weight ratio, and recyclability contribute positively to sustainability efforts in engineering, manufacturing, and beyond. The move towards incorporating these alloys more extensively could reshape future material application landscapes.
Challenges in Magnesium Alloy Applications
While magnesium alloys hold remarkable potential in a variety of applications, several challenges hinder their widespread utilization. It's crucial to navigate these hurdles to maximize their benefits, ensuring that this lightweight metal can be integrated effectively into future technological advancements. Understanding these challenges—particularly corrosion issues, machinability difficulties, and cost considerations—can help guide researchers and industry professionals towards viable solutions.
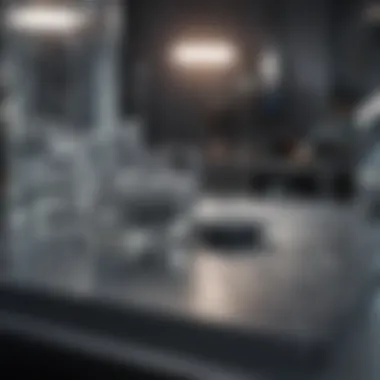

Corrosion Issues
One of the most significant challenges in magnesium alloys is their susceptibility to corrosion. Unlike metals like aluminum, magnesium tends to corrode more readily, especially in environments that are either salty or acidic. This property can be problematic, particularly in applications involving aerospace and automotive components where durability is critical.
- Electrochemical Behavior: Magnesium's position in the galvanic series makes it more anodic compared to many other metals, leading to galvanic corrosion when in contact with metals like steel.
- Protective Coatings: Various coatings, such as conversion treatments or sacrificial anodes, are used to mitigate this issue. However, the effectiveness of these coatings can vary.
- Strategies for Resistance: Ongoing research is focused on improving corrosion resistance through the development of novel coatings and alloying techniques. This area is ripe for innovation, with multimodal approaches combining surface treatments and alloy optimization emerging as promising solutions.
Machinability Difficulties
Machining magnesium alloys can be quite the chore. They exhibit a tendency to chip rather than cut, which can be frustrating during production processes. This characteristic can lead to inefficient processes that affect output quality.
- Brittleness: Some magnesium alloys can become brittle at high temperatures, complicating machining operations. This brittleness leads to challenges like blade wear and workpiece fragmentation.
- Tool Wear: Magnesium alloys can cause rapid wear on standard cutting tools, demanding specialized tools that are more durable yet costlier.
- Process Optimization: Folks in manufacturing are investigating ways to optimize machining parameters, such as speed, feed rate, and coolant use. In addition, developing alloy compositions that enhance machinability is a priority.
Cost Considerations
Lastly, the economic aspect of using magnesium alloys cannot be overlooked. Although they offer weight-saving benefits that translate into fuel efficiencies and performance improvements, their initial cost can deter some industries.
- Material Cost: The cost of raw magnesium, while fluctuating, generally tends to be higher than other commonly used metals. This can make manufacturers hesitant to adopt magnesium alloys, especially for low-margin products.
- Processing Costs: The additional costs tied to specialized tooling and surface treatments further exacerbate the financial burden. It pushes the overall price beyond what many companies might be willing to pay.
"While magnesium alloys present undeniable advantages, the cost and challenges associated with their processing necessitate a clear understanding of the value versus expense in their application."
- Long-Term Savings: It’s essential for decision-makers to look at through a long-term lens, considering the potential savings in fuel efficiency and maintenance.
Innovations in Magnesium Alloy Research
Research into magnesium alloys has seen a shift in recent years, fueled by increased demand for lighter, stronger materials across various sectors. Innovations in this field are particularly crucial due to magnesium's unique properties, which offer benefits that traditional metals cannot match. Enhancements in alloy composition and treatment processes are paving the way for more durable and versatile applications, aligning with the ongoing push towards sustainable engineering practices.
Alloy Development
The development of new magnesium alloys is at the forefront of research efforts. Industry experts are exploring ways to tailor the composition of magnesium to better meet the rigorous demands of modern applications. By integrating elements like lithium or rare earth metals, researchers can create alloys with improved strength, better fatigue resistance, and enhanced corrosion performance. These alloy modifications not only bolster the mechanical properties but also open doors to new applications in fields as diverse as aerospace, automotive, and even biomedical engineering.
An emerging area in alloy development is the concept of designed microstructures. Employing advanced techniques such as three-dimensional printing allows for the precise control of the alloy's makeup at a microscopic level. This adaptability can lead to materials that are considerably lighter yet robust enough to withstand severe conditions.
Research into these tailored alloys has shown promise, demonstrating significant enhancement in characteristics needed for specific applications.
Surface Treatments and Coatings
Surface treatments and coatings represent another significant angle in the innovations surrounding magnesium alloys. Because magnesium is more susceptible to corrosion compared to other metals, protective strategies are critical to extending the life and maintaining the integrity of these materials.
Common surface treatments include anodizing, electroplating, and chemical conversion coatings, each offering distinct advantages in terms of corrosion resistance, wear resistance, and overall durability. For instance, anodizing not only strengthens the surface layer but also adds aesthetic value, making the alloy suitable for consumer electronics and automotive applications where visual appeal is paramount.
The development of advanced coatings that are both thin and lightweight yet provide robust protection is a hot topic of research. Techniques such as sol-gel coatings and nanostructured materials are being investigated for their potential to protect against various environmental challenges while maintaining the desirable lightweight properties of magnesium.
By enhancing surface characteristics, manufacturers can broaden the application range of magnesium alloys, reducing shipping costs and improving overall efficiency in various industries. Innovations in surface treatment techniques are thus a vital component of the ongoing journey to optimize magnesium alloys for future demands.
Future Trends in Magnesium Alloys
The exploration of future trends in magnesium alloys holds paramount importance in both academic and industrial contexts. As we navigate through an era increasingly demanding sustainable solutions, magnesium alloys stand at the forefront due to their lightweight nature and high versatility. The continuous evolution of these materials not only optimizes performance across various sectors but also enhances their potential to contribute to environmental sustainability. This section examines the advancements poised to reshape manufacturing and market dynamics surrounding magnesium alloys.
Advancements in Manufacturing Processes
Manufacturing processes for magnesium alloys are undergoing significant transformations. With technology advancing at lightning speed, researchers and engineers are focused on innovative methods that enhance the efficiency and quality of production. Some of the noteworthy advancements include:
- Additive Manufacturing: Techniques like 3D printing are being employed to create complex geometries that were previously infeasible. This allows for precision in producing lightweight yet strong components tailored for specific applications.
- Die Casting Innovations: New developments in die casting techniques reduce wastage and improve the mechanical properties of cast magnesium alloys. By optimizing cooling rates and controlling the injection process, manufacturers can achieve superior grain structures, enhancing strength and ductility.
- Extrusion Technologies: Advanced extrusion methods utilize better control over temperature and speed, allowing for improved surface finish and material integrity in final products. This trend helps in minimizing defects, ultimately leading to longer-lasting end products.
These advancements not only streamline production but also lead to cost efficiencies. Furthermore, they allow for the production of more intricate designs while maintaining the characteristically low weight of magnesium alloys.
Potential Market Growth
One cannot underestimate the potential market growth associated with magnesium alloys. Several factors point towards a robust expansion in this field:
- Increased Demand in Automotive Applications: The automotive sector is on a relentless journey to reduce vehicle weight to enhance fuel efficiency. Magnesium alloys are becoming increasingly attractive alternatives thanks to their strength and lower environmental impact during manufacturing compared to heavier metals.
- Aerospace Industry Expansion: With the aerospace industry continually seeking materials that offer higher performance with lower weight, magnesium alloys are anticipated to see a substantial increase in demand. Their ability to improve overall fuel efficiency in aircraft is a strong selling point.
- Consumer Electronics Surge: The boom in consumer electronics with a focus on portability and durability means that manufacturers are actively exploring magnesium alloys. Their lightweight characteristics align perfectly with the industry's needs for long-lasting and portable devices.
"The future of magnesium alloys is not just a trend; it’s a pivotal shift toward eco-friendly practices across multiple booming industries."
Culmination
In summing up the insights presented in this article, it's crucial to underscore the multifaceted nature of magnesium alloys. These materials, often overshadowed by other metals like aluminum and steel, are carving out a distinct niche in various industries due to their unique properties. The conversation around magnesium alloys is not just about their lightweight characteristics or high strength-to-weight ratio; it spans their role in enhancing fuel efficiency and promoting sustainable practices.
Recapitulation of Key Points
Throughout this article, we've discussed several pivotal aspects:
- Composition and Properties: Magnesium alloys boast remarkable mechanical and physical properties, including low density and excellent corrosion resistance. These traits make them suitable for demanding applications, particularly where weight savings are vital.
- Applications Across Industries: From aerospace to consumer electronics, the application of magnesium alloys is vast. Their use in lightweight chassis for vehicles or as structural components in aircraft significantly impacts performance and energy consumption.
- Innovations and Research: The ongoing innovations in alloy composition and manufacturing processes open the door to even more applications. Researchers are actively exploring ways to enhance these materials' abilities, especially in relation to sustainability and recyclability.
By outlining these key points, we establish a coherent understanding of the current state of magnesium alloys and the dynamic potential they hold for the future.
Implications for Future Research and Development
The horizon for magnesium alloys looks promising, yet it is tempered by challenges that need addressing:
- Enhanced Corrosion Resistance: Future research must focus on improving the resistance of magnesium alloys to corrosion, especially in environments that demand high durability. This could pave the way for their application in automotive and marine settings where exposure to harsh conditions is common.
- Cost-Effective Production: As we explore new manufacturing techniques, there’s a need to balance performance with production costs. Finding cost-effective methods to produce high-quality magnesium alloys could facilitate their adoption across wider markets.
- Eco-friendly Treatments: With an ever-growing emphasis on sustainability, future developments should investigate surface treatments that minimize environmental impact. Green coating technologies can enhance properties while aligning with modern environmental standards.
In summary, the future of magnesium alloys hinges on addressing their current limitations while capitalizing on their strengths. As research progresses, these materials are likely to play an even more substantial role in advancing technology and promoting sustainability across various sectors. Their ongoing evolution is a testament to the ingenuity of materials science, and it promises a future filled with potential applications that could redefine how we approach engineering challenges.