Types of Jaw Crushers: An In-Depth Analysis
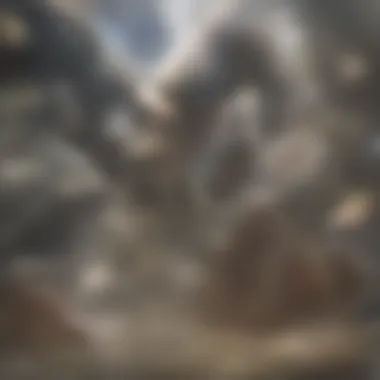
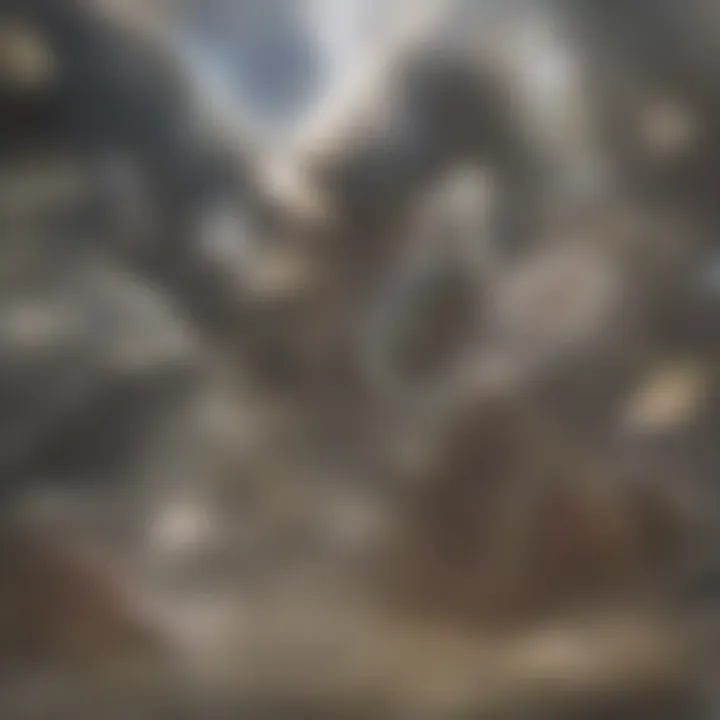
Intro
Jaw crushers are integral to the material handling industry. Their ability to process a variety of materials makes them essential in various applications ranging from mining to construction. Each type of jaw crusher has distinct design elements that contribute to its functionality, efficiency, and suitability for specific tasks. Understanding these differences is important for selecting the right equipment in any project.
In this discussion, we will explore the different varieties of jaw crushers, examine their operational principles, and highlight the various contexts where they are best utilized. We aim to provide valuable insights into their construction, performance characteristics, and recent technological advancements that could influence future design and effectiveness.
This information serves not only to illuminate industry practices but also to assist stakeholders, including engineers, project managers, and students pursuing careers in engineering and material sciences, to make informed decisions about jaw crusher selection and application.
Prolusion to Jaw Crushers
Jaw crushers play a pivotal role in various industries, particularly in the realms of mining, construction, and recycling. Understanding jaw crushers is crucial for professionals who engage with material processing equipment. This section delves into the fundamental concepts of jaw crushers, their historical context, and purpose.
Definition and Purpose
Jaw crushers are heavy-duty machines used to crush larger rock materials into smaller, manageable sizes. Their design typically includes a fixed jaw and a mobile jaw that oscillates to create a compressive force, breaking down materials through mechanical processes. These machines are essential for various applications such as quarrying and metal ore processing. By reducing materials, jaw crushers facilitate easier handling and further processing, thereby improving operational efficiency. Their effectiveness in size reduction and material processing makes them essential tools in many industrial sectors.
Historical Development
The evolution of jaw crushers dates back to the 19th century. The first successful jaw crusher was developed by Eli Whitney Blake in 1858. Its design and subsequent improvements laid the groundwork for modern variations. Over the years, engineers continued to refine jaw crushers, enhancing their performance and adaptability to different materials and conditions. By analyzing the historical progression, one can understand how technology impacted jaw crushers. This insight is valuable for industry practitioners seeking to leverage the most efficient models available today.
Mechanics of Jaw Crushing
Understanding the mechanics of jaw crushing is crucial in grasping how different types of jaw crushers function and their roles in industrial applications. The mechanics reveal the principles of operation, emphasizing efficiency and effectiveness in material reduction. This section discusses the basic working principles and components key to jaw crushers, providing insight into their design and functionality. Comprehending these mechanics aids operators and engineers in optimizing crusher performance and maintenance.
Basic Working Principle
The basic operation of a jaw crusher involves a two-part structure: the stationary jaw and the movable jaw. When the movable jaw moves closer to the stationary jaw, material is crushed. This crushing occurs as the material passes through the jaws. The motion used is typically a back-and-forth action, often also referred to as a reciprocating motion. This allows for the decrease in size of the input material, usually rocks or ore, into a smaller output.
Importantly, the force applied by the jaws creates compression, which is the essential force needed for effective crushing. The design ensures that as the jaw opens and closes, the material does not merely slide out, but gets further reduced in size upon the closing stroke. As the gaps narrow, the crushed material exits the crusher at the bottom. This mechanism defines the efficiency of the process and impacts productivity.
Key Components
Several essential components work together to ensure the jaw crusher operates smoothly. Here are the main parts:
- Jaw Plates: These are the surfaces where crushing occurs. The design, material, and wear patterns of these plates can significantly influence the performance of the crusher.
- Toggle Mechanism: This component transmits motion and force between the jaws. It affects the power efficiency and the stroke of the movable jaw.
- Frame: This is the main structure that supports all other components. A strong frame is essential for durability and stability, allowing the crusher to handle heavy loads of materials.
- Flywheel: It stores kinetic energy during the motion of the jaw and helps in maintaining a steady stroke, aiding in the 'momentum' required for crushing.
- Bearing: Bearings facilitate the movement of the movable jaw, allowing for smooth operation with minimal friction.
Each of these components plays a crucial role in ensuring the overall efficiency and effectiveness of jaw crushers. An understanding of these mechanics is essential for predicting how a specific jaw crusher performs in various applications, facilitating better selection for industry needs.
"The effectiveness of a jaw crusher largely relies on its mechanical design and the precision of its components, showcasing their importance in industrial material handling."
Types of Jaw Crushers
Understanding the types of jaw crushers is vital for selecting the right equipment for specific applications. Each type has distinct features that cater to different material sizes and properties. Recognizing these differences can lead to better operational efficiency and cost savings in various industries, from mining to construction.
The primary types of jaw crushers are singledoggle, doubletoggle, and composite. These classifications arise from the design and mechanism of the crushers. Their performance metrics, such as throughput, energy consumption, and product size distribution, also differ significantly. Thus, knowing which type is the most suitable is essential for optimizing productivity.
Singletoggle Jaw Crushers
The singletoggle jaw crusher is a well-established piece of equipment characterized by its simplicity in design and operation. This type uses a single moving jaw that exerts force on a stationary jaw plate. When materials are fed into the chamber, the moving jaw compresses the materials against the fixed plate. This mechanism allows for a high reduction ratio, making it efficient for various tasks.
Advantages of Singletoggle Jaw Crushers:
- Simpler design facilitates easy operation and maintenance.
- Lower operating costs due to fewer moving parts.
- Can achieve a high throughput with less power consumption.
Limitations:
- Less effective for harder materials compared to doubletoggle models.
- The wear on the plate can lead to more frequent replacements.
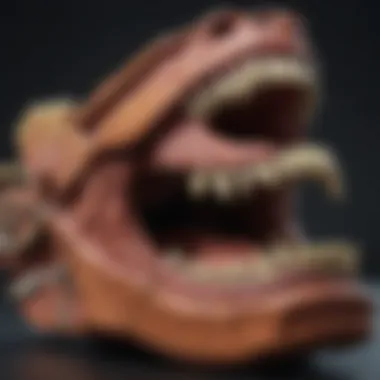
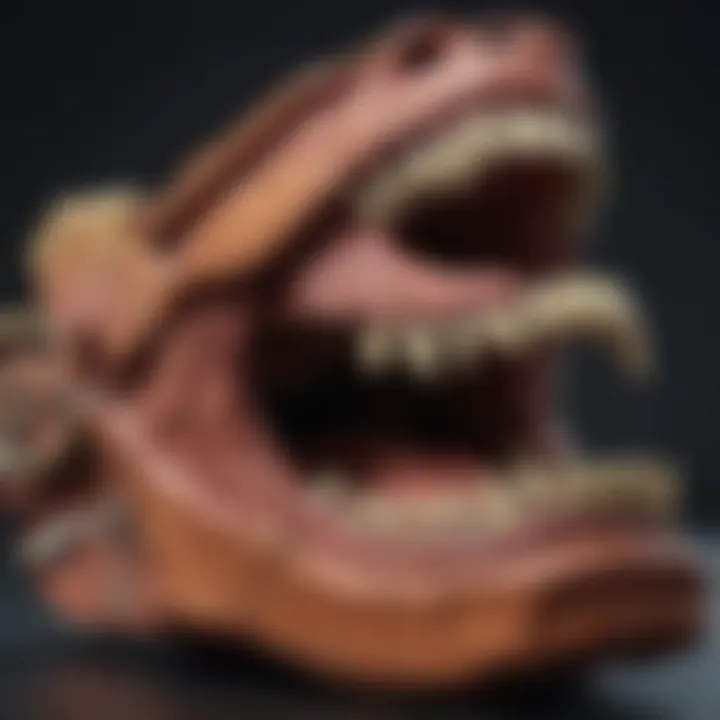
Doubletoggle Jaw Crushers
Doubletoggle jaw crushers feature a more complex mechanism. Two toggle plates are used, allowing for a more powerful crushing action. The added toggle plate also allows the jaw to make an elliptical movement. This results in a much higher crushing capacity, making it suitable for processing tougher materials.
Advantages of Doubletoggle Jaw Crushers:
- Greater crushing force allows for better processing of hard materials.
- More robust structure generally results in longer service life.
- Enhanced ability to handle larger rocks.
Limitations:
- More expensive and complex design leads to higher maintenance costs.
- Requires more space, potentially limiting its application in smaller facilities.
Composite Jaw Crushers
Composite jaw crushers combine elements from both singletoggle and doubletoggle designs. They utilize a unique hybrid mechanism that aids in crushing a wider range of materials effectively. This type is becoming increasingly popular for its versatility and adaptability to different environments and applications.
Advantages of Composite Jaw Crushers:
- Offers a balance between high capacity and reduced operating costs.
- Flexibility in processing a variety of materials with differing properties.
- Improved efficiency through enhanced design features.
Limitations:
- May not have the same level of efficiency as specialized models.
- Potentially higher initial costs due to advanced technology integration.
"The selection of the right type of jaw crusher significantly impacts operational outcomes, emphasizing the importance of understanding each type's design and functionality."
Comparative Analysis of Jaw Crusher Types
Understanding the differences between various types of jaw crushers is paramount for making informed decisions in material processing. The comparative analysis sheds light on how each type operates under different conditions, what advantages they bring, and where their limitations lie. Thus, this section aims to highlight key performance metrics among the types, such as efficiency and durability, while also considering cost implications. This knowledge aids manufacturers and operators to match the right equipment to their specific operational requirements.
Efficiency and Performance
Efficiency is a crucial metric when selecting a jaw crusher. It generally refers to the crusher's ability to convert energy into useful work. A high-efficiency jaw crusher not only reduces operational costs but also enhances overall productivity. The efficiency often varies among single toggle, double toggle, and composite jaw crushers.
- Single Toggle Jaw Crushers are typically more efficient at lower capacity levels. They have a simpler mechanism, which often translates into less energy consumption.
- Double Toggle Jaw Crushers, while more robust and capable of handling bigger volumes, tend to be less efficient. Their design results in higher energy use, but they excel in crushing harder materials.
- Composite Jaw Crushers provide a middle ground. They blend the mechanics of the former two types but still face limitations depending on material hardness.
Overall, efficiency varies based on design, operating speed, and material characteristics, making performance testing essential for optimal operations.
Cost-effectiveness
The investment in a jaw crusher machine goes beyond the initial purchase price. Considering total cost of ownership is vital for evaluating cost-effectiveness. This includes maintenance, consumables, and energy consumption over time.
- Single Toggle Jaw Crushers usually cost less initially and offer lower maintenance costs due to fewer moving parts. However, their capacity is often limited, potentially leading to higher operational costs over time if multiple units are necessary.
- Double Toggle Jaw Crushers tend to be pricier and require more maintenance due to their complex design. Their longevity and ability to handle larger rocks can offset costs in high-demand settings.
- Composite Jaw Crushers can prove cost-effective when performance meets operational demands without the expense of additional machines.
Evaluating cost-effectiveness requires careful analysis of both upfront costs and ongoing operational expenses, guiding prudent investment choices in the long run.
Maintenance and Durability
The long-term reliability of jaw crushers is significantly tied to maintenance regimes and the durability of their components. Choosing the right type can minimize downtime and prolong life cycles.
- Single Toggle Jaw Crushers are generally easier to maintain. Their straightforward construction allows for quicker repairs or part replacements, reducing downtime.
- On the other hand, maintenance for Double Toggle Jaw Crushers can be labor-intensive. They require regular checks to ensure all moving parts function smoothly, which can lead to increased operational interruptions.
- Composite Jaw Crushers offer durability but share the maintenance challenges of both other types. Their diverse components may require specialized knowledge for repairs.
Ultimately, the right choice depends on balancing the immediate operational needs with long-term sustainability and the ability to maintain the machines without excessive cost or downtime.
Applications of Jaw Crushers
The applications of jaw crushers are diverse, reflecting their importance in various industrial sectors. Understanding these applications helps in appreciating how jaw crushers fit into the larger framework of material handling and processing. In this section, we will examine the specific roles that jaw crushers play in mining, construction, and recycling. Each application highlights the unique benefits they offer and considerations for their effective use.
Mining and Quarrying
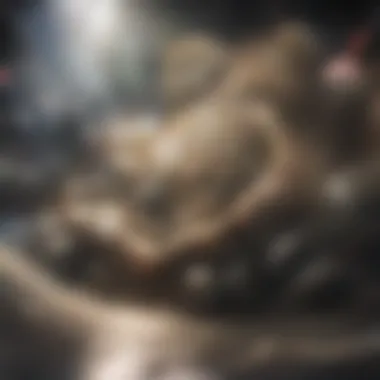
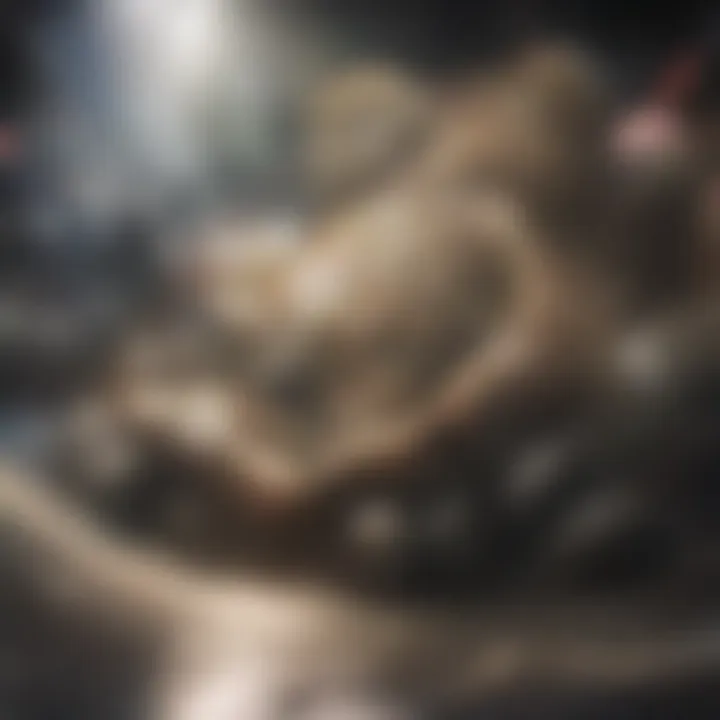
In the mining and quarrying industries, jaw crushers are used mainly for the reduction of large rocks into smaller, manageable sizes. This size reduction is crucial for further processing and extraction of valuable minerals. The efficiency of jaw crushers in this sector lies in their ability to handle tough materials, such as granite and basalt, while maintaining consistent output sizes.
- Primary Crusher Function: Jaw crushers serve as primary crushers, breaking down raw material before it undergoes secondary processing.
- Durability: Built to endure extreme conditions, jaw crushers are often designed from robust materials. This longevity contributes to lower operational costs in the long run.
- Ease of Maintenance: Regular maintenance ensures optimal performance, a vital aspect in high-output environments like mines.
Exploring jaw crushers in mining emphasizes the machinery's capability to influence productivity and operational effectiveness.
Construction and Demolition
Jaw crushers play a pivotal role in construction and demolition projects, where they are applied to crush concrete, bricks, and other materials generated from construction sites. Their utility in these scenarios is considerable as they facilitate material recycling and help reduce waste in landfills.
- Material Recycling: Using jaw crushers to break down demolition waste aids in recovering valuable materials which can be reused in new construction projects.
- Mobility: Many jaw crushers are mobile, allowing them to be transported easily to various construction sites, enhancing operational efficiency.
- Versatility: They can handle a variety of materials and are effective in different stages of the construction process, from initial crushing to final shaping.
The adaptability of jaw crushers thus resonates with the evolving needs of construction and demolition practices.
Recycling Materials
Recycling is a critical aspect of waste management, and jaw crushers contribute significantly by enabling the processing of various recyclable materials. These crushers help in transforming waste into raw materials that can be circulated back into production systems.
- Waste Reduction: By crushing plastic, wood, metals, and concrete, jaw crushers assist in reducing the volume of waste, which is increasingly important in urban environments.
- Job Creation in the Recycling Sector: The presence of efficient crushing technologies supports a growing recycling industry, creating jobs and fostering sustainability.
- Economic Viability: Companies investing in jaw crushers for recycling often find an increase in profitability due to the reduced costs of sourcing raw materials from recycled sources.
In summary, the applications of jaw crushers across mining, construction, and recycling sectors illustrate their versatility and effectiveness. These machines not only contribute to operational efficiencies but also support sustainability efforts in material handling.
Technological Advancements in Jaw Crushers
Technological advancements in jaw crushers play a crucial role in increasing efficiency and enhancing performance across various industrial applications. As the demand for more effective material handling solutions rises, innovations in design and functionality have become essential. These developments not only improve operational capabilities but also address challenges related to safety, maintenance, and environmental concerns. Insights into these advancements help stakeholders, including students and professionals, make informed decisions on equipment selection.
Automation and Control Systems
The integration of automation and control systems in jaw crushers marks a significant shift in how these machines operate. Automation allows for real-time monitoring and adjustment of crushing parameters, which directly impacts productivity and efficiency. For instance, systems employed in modern jaw crushers can automatically adjust the closed side setting, optimizing the size of the output material based on feed variations.
The benefits of these advancements are numerous:
- Increased Precision: Automating the control of crushing processes results in more consistent output.
- Reduced Labor Costs: Automation minimizes the need for manual interventions, thus lowering labor expenses.
- Improved Safety: With remote monitoring capabilities, operators can maintain a safer distance from potentially hazardous environments.
- Enhanced Fuel Efficiency: Automated systems can reduce energy consumption by optimizing operational cycles, contributing to lower operational costs.
Enhancements in Materials
Recent advancements in materials used for constructing jaw crushers have significantly improved their durability and longevity. Modern jaw crushers often utilize composites and high-strength alloys that can withstand the intense wear and tear experienced in crushing operations.
Some notable material enhancements include:
- High-Carbon Steel: This material offers superior strength and wear resistance, allowing for longer service life of crusher components.
- Quenched and Tempered Steel: Used in key elements of the jaw crusher, this steel maintains toughness and flexibility, handling mechanical stress better.
- Ceramic Reinforced Material: These materials are increasingly being integrated to reduce friction and improve overall efficiency.
As a consequence of these advancements, the following advantages are noted:
- Extended Equipment Life: Improved materials drastically reduce the frequency of repairs and replacements.
- Higher Throughput: Enhanced durability enables crushers to handle larger volumes without declining performance.
- Lower Operating Costs: With less frequent need for replacements, operational costs decrease, making jaw crushers more economically viable.
"Technological innovations in jaw crushers provide essential enhancements that lead to substantial operational improvements and long-term cost savings."
In summary, the continual evolution of automation and material technology in jaw crushers plays an integral role in shaping their future. By embracing these advancements, the industry can enhance productivity while addressing significant operational challenges.
Impact of Regulatory Standards
Regulatory standards have a significant influence on the operation and design of jaw crushers. These standards often arise from the need to ensure safety and environmental protection. They dictate the operational parameters that equipment manufacturers must follow to guarantee that their products are safe and efficient to use. In the context of jaw crushers, this is particularly important as these machines operate in demanding environments, often involving heavy loads and substantial wear and tear. Compliance with these regulations can enhance not only safety but also device reliability and longevity.
Safety and Environmental Regulations
Safety regulations are paramount in industries that utilize jaw crushers. These regulations are designed to protect workers from potential hazards related to heavy machinery. For instance, the Occupational Safety and Health Administration (OSHA) emphasizes the importance of proper training and safety equipment when operating crushers.
Additionally, environmental regulations focus on minimizing the adverse effects of crusher operations on the environment. This includes controlling dust emissions, reducing noise pollution, and ensuring proper waste disposal. For example:
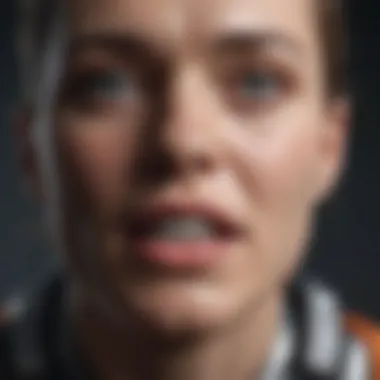
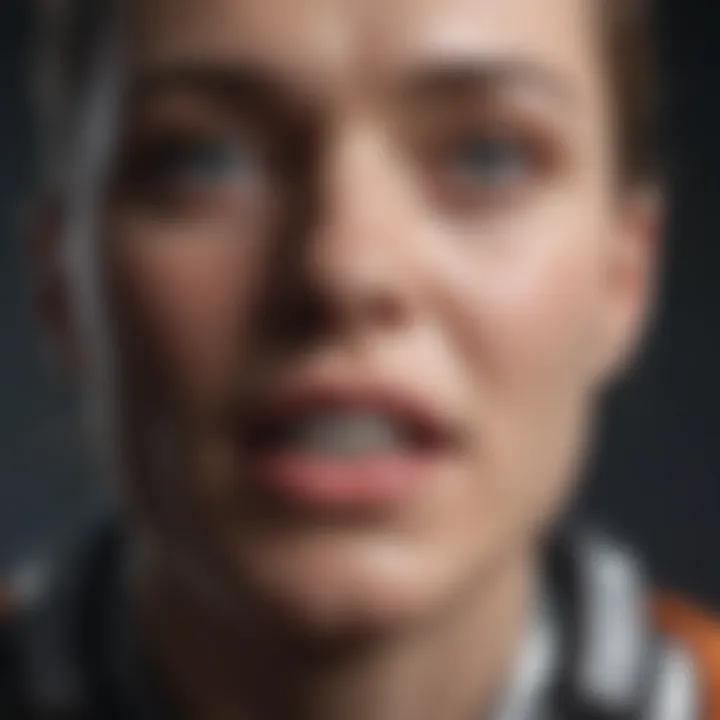
- Dust Control Measures: Systems such as water sprays or dust collectors help mitigate dust during operations.
- Noise Control: Implementing noise barriers or soundproofing technologies ensures that sound pollution is kept within permissible limits.
- Waste Management: Regulations require proper disposal of waste materials generated from crushing operations, promoting recycling whenever possible.
Overall, adhering to these safety and environmental regulations not only fosters a safer workplace but also enhances the credibility of the operations and manufacturers involved.
Challenges of Compliance
While compliance with regulatory standards is essential, it also presents several challenges. First, staying updated with regulatory changes can be overwhelming for companies, especially in fast-evolving industries. Regulations are frequently updated, which may necessitate modifications in equipment and processes. The following points elucidate some hurdles faced by operations:
- Financial Costs: Upgrading equipment to meet safety standards can be costly. This includes purchasing safety gear, acquiring new technology, and implementing training programs.
- Training Requirements: Ensuring that all personnel are adequately trained on the latest safety protocols can require significant time and resources.
- Increased Oversight: Higher levels of compliance increase the need for rigorous inspections and audits, which can disrupt regular operations.
In summary, while regulatory standards play a critical role in maintaining safety and environmental integrity, the path to compliance can present various obstacles that require strategic planning and resource allocation.
Future Prospects for Jaw Crushers
The future of jaw crushers is undeniably crucial in the realm of material handling. As industries evolve and demand for efficiency rises, jaw crushers must adapt to new challenges. Understanding these prospects helps stakeholders make informed decisions regarding equipment selection and application.
Emerging Trends in Design
Design advances in jaw crushers are pivotal for improving their functionality and performance. Manufacturers are increasingly integrating innovative materials that enhance durability while reducing weight. This leads to better fuel efficiency and easier transport.
One notable trend is the evolution of modular design. Modular crushers can be easily assembled or disassembled for transportation. This feature proves beneficial for operations in remote areas or where rapid setup is necessary.
Automation is another significant aspect. With the rise of smart technology, jaw crushers are becoming more integrated with control systems. These systems not only optimize performance but also provide real-time data on operation conditions.
- Flexibility: Modern designs allow for versatile applications.
- Smart technology: Enhances operational insights and maintenance scheduling.
Incorporating sustainability measures is also becoming the norm. For instance, designs focused on minimizing waste and energy consumption are increasingly preferred. The shift towards eco-friendly practices can significantly influence market competitiveness.
Market Demand Dynamics
Market demand for jaw crushers is influenced by several factors, including global economic trends and advancements in technology. As infrastructure projects continue to rise, so does the need for efficient crushing solutions.
The push for recycling of materials has spurred the development of machines capable of handling various materials, such as concrete and metal. This trend reflects the growing emphasis on sustainability in construction practices.
Different regions experience varying demand based on their industrial growth. For example, developing nations may seek cost-effective solutions, while established markets often prioritize efficiency and advanced features.
"The adaptability of jaw crushers to meet changing market needs is essential for their sustained relevance."
- Geographical variations: Regional demands can shape product offerings.
- Economical solutions: Cost-effectiveness remains a key factor in purchase decisions.
Ending
The conclusion serves as a pivotal component of this comprehensive overview, encapsulating the essential insights drawn from our exploration of jaw crushers. By synthesizing the discussions from previous sections, it draws attention to the key attributes that differentiate the various types of jaw crushers. These differences are not merely academic; they have practical implications for their usage in different industrial contexts. This segment underscores the importance of understanding these differences when selecting the appropriate type for specific applications.
Moreover, the conclusion emphasizes the advantages and limitations inherent within each type. Recognizing these can provide industry practitioners with the framework needed to make informed decisions. As the landscape of materials handling continues to evolve, the implications of technological advancements and regulatory standards must also be considered.
The potential for improved performance, sustainable practices, and enhanced safety in the operation of jaw crushers is significant. Consequently, practitioners are equipped to navigate the complexities of material processing with greater confidence. Ultimately, this section reinforces the vital role of jaw crushers in various industries, highlighting their adaptability and significance in achieving operational efficiency.
Summary of Key Insights
Several key insights emerge from our analysis. First, the distinction between the types—singletoggle, doubletoggle, and composite jaw crushers—is crucial for tailoring the equipment to meet specific operational requirements. Each type has unique design features that impact efficiency, performance, and cost-effectiveness.
- Singletoggle Jaw Crushers: Known for their simpler design, they are less complicated to operate and maintain, making them suitable for smaller projects.
- Doubletoggle Jaw Crushers: While they offer higher efficiency, they come with increased complexity and costs. They are ideal for larger operations where durability and power are essential.
- Composite Jaw Crushers: These are increasingly favored for their balance of efficiency and complexity, catering to diverse applications.
Additionally, the role of technological advancements cannot be overstated. Automation and enhanced control systems are transforming the operational landscape, promoting not just efficiency but also adherence to safety regulations.
The continuous evolution of jaw crushers may redefine industry standards, pushing boundaries on what is feasible in material handling.
Implications for Industry Practitioners
For industry practitioners, the implications of the findings are multifaceted. Being equipped with a clear understanding of the types and their operational contexts is paramount for optimizing machine selection. An informed choice can lead to significant increases in operational productivity, cost savings, and compliance with safety regulations.
- Practitioners should evaluate the specific materials they handle and their processing needs. This analysis will determine the most suitable jaw crusher type.
- Understanding the latest technological advancements is crucial as well. Practitioners should invest in training and adapting their operations to implement new technologies effectively, making the most of automation and material enhancements.
- Regulatory pressures mean that practitioners must stay informed about evolving environmental and safety standards affecting equipment choice and operation.
In summary, the implications of selecting the right jaw crusher extend beyond financial considerations. They encompass broader concerns regarding efficiency, compliance, and the environmental impact of material processing. This comprehensive understanding can help practitioners navigate the complexities of modern materials handling.