In-Depth Exploration of Welding Coatings and Their Impact
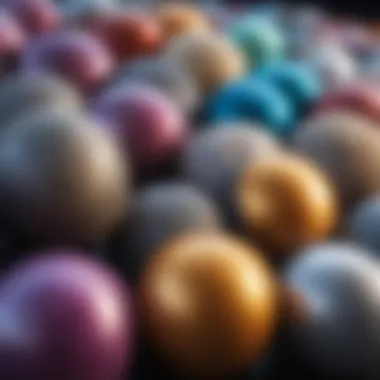
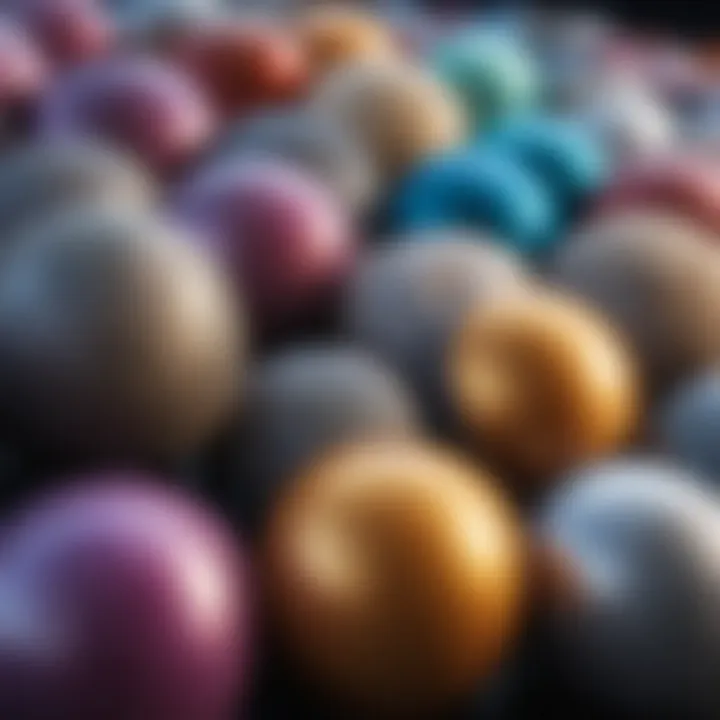
Intro
Welding coatings are often overlooked in conversations surrounding welding processes, yet they play a monumental role in ensuring the quality and longevity of welded joints. These coatings serve various functions, from preventing oxidation during the welding process to enhancing corrosion resistance in the finished product. The significance of understanding the different types of coatings, their application methods, and the chemistry behind them cannot be understated, especially for those who operate in demanding environments where metal fatigue and failure can have costly consequences.
As industries evolve, so do the requirements for welding coatings. With an increasing focus on environmental impact and sustainability, today's professionals must be equipped with knowledge that spans both traditional and avant-garde methods of coating application. This article will leverage technical insights, research findings, and practical advice, catering to an audience comprised of students, educators, and seasoned professionals alike. Together, we will delve into the multifaceted applications and underlying principles of welding coatings and their influence on every facet of welding integrity.
Key Findings
The exploration of welding coatings reveals notable insights that are crucial for enhancing welding procedures:
- Types of Coating Materials: Various coatings exist, including but not limited to organic, inorganic, and composite materials. Each type has its own unique set of properties and applications.
- Impact on Weld Integrity: Properly chosen and applied coatings significantly reduce risks of weld defects, enhance mechanical properties, and extend service life in corrosive or high-temperature environments.
- Technological Advancements: Innovations in coating chemistry and application technology have led to the development of more effective materials that comply with current environmental regulations.
"A well-chosen welding coating is akin to a well-fitted suit; it ensures maximum performance, durability, and style in the field."
Major Results
The findings highlight that over time, the performance of welded joints is intricately linked to the quality and type of the applied coating. For instance, organic coatings excel in providing a protective layer from UV damage, while inorganic ones often offer stronger thermal stability. With the interplay of welding parameters and coating selection outlined, the following outcomes were noted:
- Improved corrosion resistance in atmospheric applications.
- Enhanced mechanical strength of weld joints.
- Better compatibility with various post-weld treatments.
Discussion of Findings
The implications of these key findings suggest that welding professionals need to maintain an adaptable approach when selecting coatings. Recommendations also indicate that ongoing education and training in the selection and application methods of coatings are vital for keeping pace with industry advancements. As coatings technology becomes more sophisticated, understanding their application can provide a significant competitive advantage.
Methodology
To present a comprehensive examination of welding coatings, a rigorous methodology was employed, focusing on empirical research and practical application.
Research Design
The research design utilized a mixed-method approach, combining quantitative data from testing various coatings with qualitative insights gained from industry experts. This allows for a balanced view of the efficacy of different coatings across various scenarios.
Data Collection Methods
A variety of data collection methods were implemented, including:
- Experimental Testing: Lab tests to compare the performance of different coatings under controlled conditions.
- Surveys and Interviews: Gathering firsthand accounts from professionals regarding their experiences and preferences with coatings.
- Literature Review: Examination of current scientific literature and case studies to contextualize findings among existing knowledge.
With this methodology, the article aims not just to inform but also to prepare readers for the evolving landscape of welding technologies and environmental considerations.
Prolusion to Welding Coatings
Welding coatings play a crucial role in the field of metallurgy, influencing not just the appearance of a weld but significantly altering its durability and performance. As intriguing as it may sound, these coatings are more than just a protective layer; they are vital for ensuring the longevity and integrity of welded joints. Let's delve into what welding coatings encompass and why they matter so much.
Definition and Purpose
At its core, a welding coating refers to a material applied to the surface of welded joints and base metals before, during, or after the welding process. The primary purpose is to enhance properties such as corrosion resistance, wear resistance, and, in some cases, even aesthetic appeal. Imagine it like putting on a sturdy raincoat before stepping out in unpredictable weather. The coating serves as a barrier against the elements, preserving the integrity of the structure beneath.
The effectiveness of coatings varies widely depending on their composition and application method. For instance, organic coatings primarily use polymers that can offer good flexibility and adhesion. Conversely, inorganic coatings utilize ceramics or metal oxides which provide outstanding heat resistance but may lack flexibility. This distinction is essential, as selecting the appropriate type can dramatically influence the success of a welding project.
In addition to enhancing properties, coatings also play a role in the welding process itself; they can aid in the fusion of metals, influence the arc stability, and even reduce spatter. By understanding the definition and purpose of these coatings, professionals can tailor their techniques and materials to any specific requirements of a project.
Historical Context
The journey of welding coatings began centuries ago, with the earliest examples dating back to ancient civilizations. Take, for example, the Egyptians, who often used protective layers on their metal artifacts, albeit rudimentarily. As metallurgy advanced, so did the knowledge on how coatings could influence weld quality.
In the modern era, particularly post-World War II, the industrial demand for stronger and more durable materials exploded. The coatings adapted, shifting from simple protective finishes to complex chemical formulations designed for specific environmental challenges. It was during this period that manufacturers began to explore various combinations of organic and inorganic materials, significantly changing the landscape of welding coatings.
Today, the evolution of these coatings represents a fascinating intersection of chemistry and engineering. More recent developments have included smart coatings capable of adapting to environmental changes, showing just how far this field has evolved. Understanding the historical context helps appreciate the current technology in welding coatings, paving the way for future innovations.
"The evolution of welding coatings is a testament to human ingenuity, where practical needs led to scientific advancements."
Types of Welding Coatings
Welding coatings play a fundamental role in enhancing both the durability and functionality of welds. Understanding the various types of coatings helps in selecting the right one for specific applications. Each type has its unique characteristics, advantages, and limitations that significantly influence the final output of welding projects. Below, we will dive deeper into the four main categories: Organic, Inorganic, Metallic, and Hybrid coatings.
Organic Coatings
Organic coatings are primarily formulated from carbon-based compounds. They offer a level of protection against rust and corrosion while also providing an appealing finish. Common examples include paints and varnishes that contain resins.
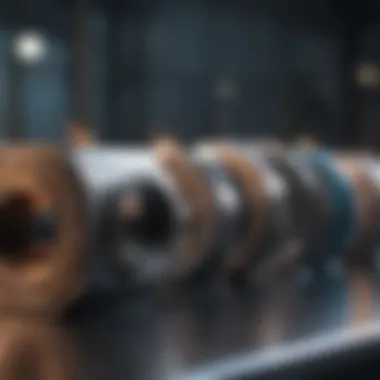
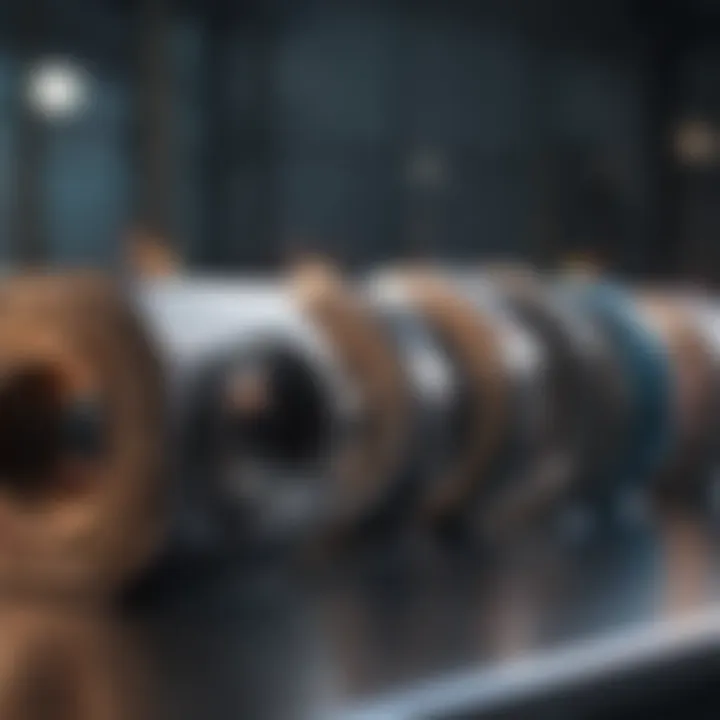
- Advantages: Organic coatings provide flexibility and good adhesion, making them suitable for various substrates. They can be applied easily through spraying or brushing. Furthermore, they often come in a broad range of colors and finishes, allowing for aesthetic versatility.
- Considerations: On the downside, organic coatings may not withstand high temperatures as effectively as other types. They might also require regular maintenance to ensure their protective features remain intact, especially in harsh environments.
Inorganic Coatings
Inorganic coatings are built on mineral-based compounds, such as silicates, ceramics, or oxides. Due to their strong resistance to heat and corrosion, they are often used in high-temperature applications.
- Advantages: These coatings are remarkably stable and resilient. They are well-suited for areas that experience extreme temperature fluctuations or corrosive substances, making them ideal for heavy industries and power plants. Moreover, inorganic coatings tend to have a longer lifespan compared to organic ones.
- Considerations: However, they can be more challenging to apply and may not offer as much color variety. Their application often requires specialized skills and equipment, which can add to labor costs.
Metallic Coatings
Metallic coatings involve the application of a layer of metal onto the base material. This can be achieved through processes like galvanizing or electroplating. Common metallic coatings include zinc, aluminum, and chrome.
- Advantages: The primary attraction of metallic coatings is their outstanding properties in preventing corrosion and wear. They are especially effective in environments exposed to moisture, altering the nature of the surface and thereby enhancing performance. Additionally, they can provide conductivity when necessary.
- Considerations: The main drawback lies in the potential for moisture entrapment, which could lead to under-coating corrosion or deterioration. Application techniques may also require precision to ensure uniformity and adherence.
Hybrid Coatings
Hybrid coatings combine elements from organic and inorganic categories to achieve superior benefits from both.
- Advantages: The innovative aspect of hybrid coatings lies in their versatility. They present a unique balance between aesthetics and protection. This combination can result in improved scratch resistance and durability. Their capacity to withstand varying environmental conditions makes them a favorite in numerous applications—from automotive to construction.
- Considerations: Despite their many benefits, hybrid coatings can be pricier than traditional options due to their complex formulation and application requirements.
Understanding the types of welding coatings helps in making informed decisions when selecting materials for different welding applications.
In sum, the choice of a specific type of welding coating hinges on the distinct needs of the project. Whether seeking protection from corrosion, aesthetic appeal, or functionality under extreme conditions, knowing the pros and cons of each coating type aids in achieving optimal welding results.
Application Methods for Coatings
The way coatings are applied in welding processes carries significant weight in determining the efficiency and effectiveness of the weld. The choice of application method can affect not just the quality of the weld but also numerous other factors, such as operational costs, material waste, and environmental impact. Each method presents its own set of advantages and challenges, catering to both specific project needs and desired outcomes. Understanding these methods helps professionals make informed decisions tailored to their unique requirements and goals.
Spraying Techniques
Spraying is often touted as one of the most versatile methods in coating application. It involves atomizing the coating material and projecting it onto the surface using compressed air. The benefits are manifold: it creates a fine finish, reduces the need for extensive surface preparation, and can cover complex geometries with relative ease. Yet, it’s not all sunshine and rainbows—this method can lead to overspray, which not only wastes material but can also require additional cleanup.
Spraying techniques can vary:
- Air Spray: Uses air to atomize the coating. It’s great for thin coatings.
- Airless Spray: Involves high pressure to spray without air. This can produce thicker layers rapidly.
- Electrostatic Spray: Applies an electric charge to the paint particles, attracting them to the surface, reducing waste.
This method's flexibility tackles diverse materials and coatings, making it appealing across different industries.
Dipping Processes
Dipping, as it sounds, requires submerging the item in a coating solution. This method is particularly effective for achieving uniform coverage on intricate and smaller parts. It ensures that every nook and cranny is reached—a real boon when dealing with items that have complex shapes.
Advantages of dipping methods include:
- Consistent thickness of coating
- Reduces the chance of air entrapment, which can lead to defects in the weld
- Suitable for batch processing, enhancing productivity
On the flip side, there are limitations, like a longer curing time and the potential for run-off or pooling, which can lead to weak spots if not managed properly. As with many techniques, balancing efficiency and coverage quality is key.
Electroplating Methods
Electroplating is a unique application method where metal ions are deposited onto a surface following principles of electrolysis. This method excels in creating a thick, even, and durable coating which enhances corrosion resistance and structural strength. It can be particularly useful for parts that will experience harsh environmental conditions.
Key considerations around electroplating include:
- Material Compatibility: Not all substrates can undergo electroplating, requiring careful selection.
- Surface Preparation: Items must be meticulously cleaned to promote adhesion of the electroplated layer.
The benefits here are clear: enhanced weld integrity and corrosion resistance, but careful handling and preparation can be labor-intensive and time-consuming.
Powder Coating Techniques
Powder coating techniques employ dry powder, which is electrostatically charged and then sprayed onto the workpiece. Once applied, the piece is heated in an oven, causing the powder to melt and form a dense, resilient coat. This method shines in terms of durability and aesthetic appeal, making it a common choice for decorative metalwork and automotive parts.
Benefits of powder coating include:
- Higher resistance to scratching, chipping, and fading compared to traditional liquid coatings.
- Environmentally friendly; less volatile organic compound emission.
- Variety in color and texture options enhances visual quality.
However, powder coating does have its drawbacks. The process requires specific equipment and may not be suitable for every job, especially where thin coatings are necessary.
The choice of application method can greatly influence both the outcome of the welding project and its economic viability.
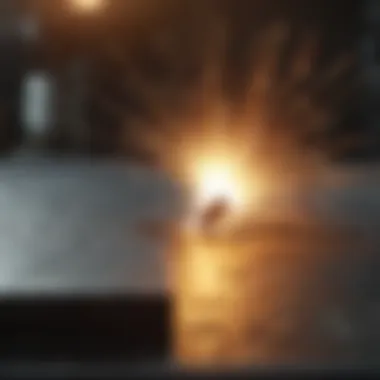
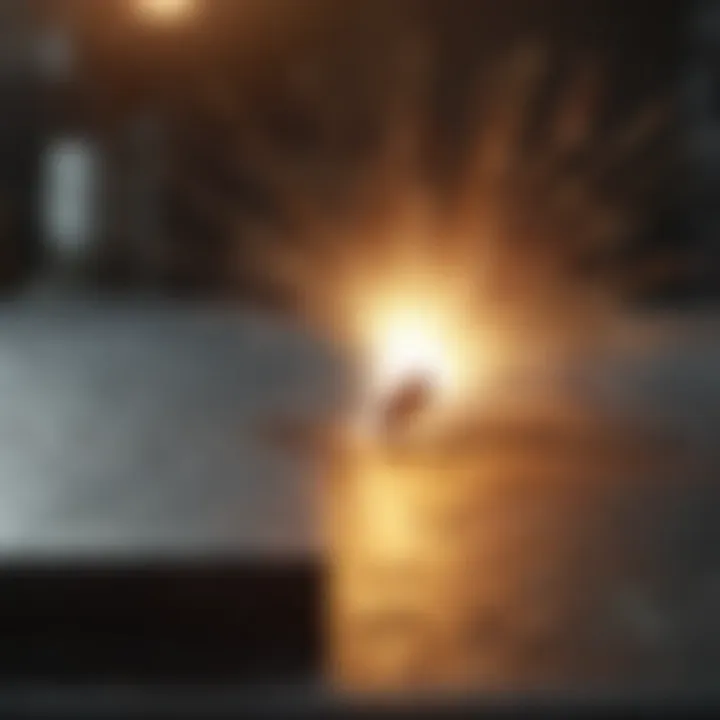
Ultimately, understanding these application methods equips welders and engineers with the insight necessary to optimize coatings for their unique applications. By analyzing the specific mechanical properties and environmental factors related to each method, decisions can be made that not only align with industry standards but also drive innovation in welding practices.
Chemical Composition of Coatings
Understanding the chemical composition of welding coatings directly impacts the effectiveness and durability of welded joints. It plays a pivotal role in determining how these coatings interact with both the base metal and the welding environment. When we talk about chemical composition, we don't just mean the basic materials; we are also referring to the specific arrangements and ratios of these materials. The right formulation can lead to enhanced adhesion, improved corrosion resistance, and better weld quality.
The chemistry behind welding coatings involves a variety of elements that serve functional purposes. For instance, the mix of organic compounds and inorganic compounds can significantly affect the physical properties of the coating. This relates directly to the performance of the weld itself, where structural integrity under various conditions—be it heat, moisture, or mechanical stress—becomes critical.
Key Components
Coatings often comprise a selection of key components that work together to provide desirable traits:
- Base Material: This forms the foundation of the coating. Common base materials include epoxies, polyurethanes, and vinyls. Each of these serves distinct properties that influence adhesion and flexibility under stress.
- Pigments: Add some color (and sometimes specific protective qualities). Certain pigments can enhance UV resistance, which is vital in outdoor applications.
- Resins: They bond the other components together. Resins give coatings their hardness and resistance to environmental factors. Different resins offer different characteristics; for example, phenolic resins often excel in high-temperature applications.
- Fillers: Added for cost reasons or to modify certain properties. Fillers can affect the coating's thickness, texture, and, interestingly, its thermal conductivity.
Each component needs careful consideration, as even small changes in formulation can lead to notable differences in performance.
Additives and Their Functions
Additives are the unsung heroes of welding coatings. They facilitate numerous important functions that can significantly enhance the qualities of the primary components.
- Stabilizers: Vital in preventing degradation over time, stabilizers help preserve the integrity of the coating by resisting environmental factors like UV rays and moisture.
- Thickeners: Used to improve the application properties. They help to ensure that the coating adheres well to vertical surfaces without sagging.
- Anti-settling Agents: These ensure uniform distribution of components. They help keep pigments and fillers from settling, ensuring consistency in application.
- Wetting Agents: They alter the surface tension of the coating mixture to improve the coating's ability to spread evenly on the substrate, leading to a smoother finish.
When you combine these additives with the key components, you create a highly functional and efficient coating that can withstand not just the rigors of welding processes but also the environment in which welded structures are placed.
"The chemistry of coatings is more than just a recipe; it's a fine dance of elements that meet the demands of modern engineering."
In summary, understanding the chemical composition of coatings, with an emphasis on key components and additives, is essential for professionals looking to ensure the success of their welding operations. This knowledge not only enhances weld performance but also contributes significantly to longevity and reliability in various applications, from construction to aerospace.
Impact of Coatings on Welding Performance
Welding coatings play a pivotal role in the overall performance of welding operations. Understanding their impact sheds light on several critical elements, including the integrity of the welds, resistance to environmental stresses, and overall durability. In a world where structural integrity cannot be compromised, coatings offer a layer of protection that is indispensable for successful operations. If you ever find yourself pondering whether investing time and resources into coatings is worth it, the answer lies in their proven benefits.
Enhancing Weld Quality
One of the foremost advantages of using coatings in welding is the enhancement of weld quality. Coatings can significantly influence the mechanical properties of the welds, affecting strength, ductility, and toughness. When the right coating is applied, it can act as a buffer against impurities, which often lead to defects such as porosity or cracking.
Applications of coatings often provide:
- Improved adhesion between the base metal and filler materials: This ensures a seamless fusion of materials that can withstand greater loads.
- Controlled heat input during welding: Some coatings can be engineered to dissipate heat more evenly, reducing the risk of thermal distortion.
- Filler metal protection from atmospheric conditions: Coatings can keep contaminants at bay, resulting in cleaner welds with fewer defects.
In sum, the enhancements offered through coatings not only improve the final appearance of welds but also contribute to their longevity. This warrants thorough consideration when designing welding projects, as the implications stretch far beyond just the immediate results.
Corrosion Resistance
Corrosion is a natural foe of welded constructions, and coatings act as a robust shield against it. Various environmental factors, including moisture, temperature fluctuations, and exposure to chemicals, can lead to rapid deterioration of welds. This is where corrosion-resistant coatings shine.
When we talk about corrosion resistance, we refer to the ability of a coating to protect underlying metal from harmful reactions. Key benefits include:
- Barrier properties: Coatings form a physical barrier between the metal surface and the environment, drastically lowering the chances of rust and oxidation.
- Cathodic protection: Certain types of coatings can even provide cathodic protection. This is crucial when working with metals like steel, which are prone to galvanic corrosion in the presence of other metals.
- Extended lifespan of structures: Employing the right corrosion-resistant coating can multiply the lifespan of welded assemblies, leading to considerable savings on maintenance and replacement costs.
"Investing in quality coatings can yield returns that far exceed the initial investment, turning potential costly repairs into a distant memory."
Furthermore, coatings are not a one-size-fits-all solution. Depending on the service environment—be it marine, industrial, or residential—these coatings can be tailored to meet specific requirements. By understanding the nuances of each application, professionals can select coatings that best fit their needs, ensuring durability and reliability of the welded structures.
Environmental Considerations
Environmental considerations are not just a passing fancy; they are essential factors that play a significant role in the adoption and use of welding coatings within the industry. The exploration of these considerations gives a robust understanding of how coatings not only influence performance but also align with sustainable practices and regulatory expectations.
Regulatory Standards
Regulatory standards set the stage for what is acceptable in terms of environmental impact, health concerns, and overall product safety. These standards vary across regions but generally focus on reducing volatile organic compounds (VOCs) and other harmful emissions released during the application and curing processes of coatings. Commonly adopted regulations like the Environmental Protection Agency's (EPA) guidelines dictate limits on VOC content in paints and coatings, pushing the industry toward more environmentally friendly materials.
The importance of adhering to these regulatory frameworks cannot be overstated. Standards such as ISO 14001 provide a structured approach to managing environmental responsibilities in welding operations. Companies that comply with these standards not only avoid legal repercussions but also enhance their marketability and credibility in a world increasingly focused on sustainability.
"Without a doubt, companies that take the environmental route find themselves ahead in the game, attracting both consumers and clients who prioritize greener solutions."
Sustainability in Coating Materials
Moving toward sustainability in coating materials is imperative as it ensures that the environmental footprint of welding processes is minimized. The pursuit of eco-efficient materials has led to innovations in both organic and inorganic coatings. For example, many manufacturers are exploring bio-based resins as an alternative to traditional petroleum-based compounds. These bio-inspired materials can reduce the carbon footprint associated with production and application.
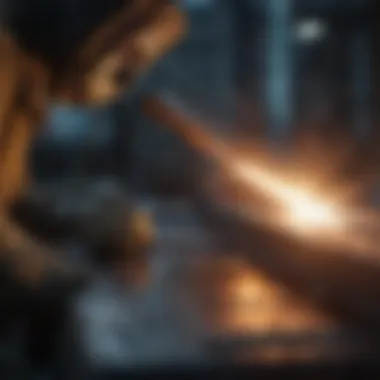
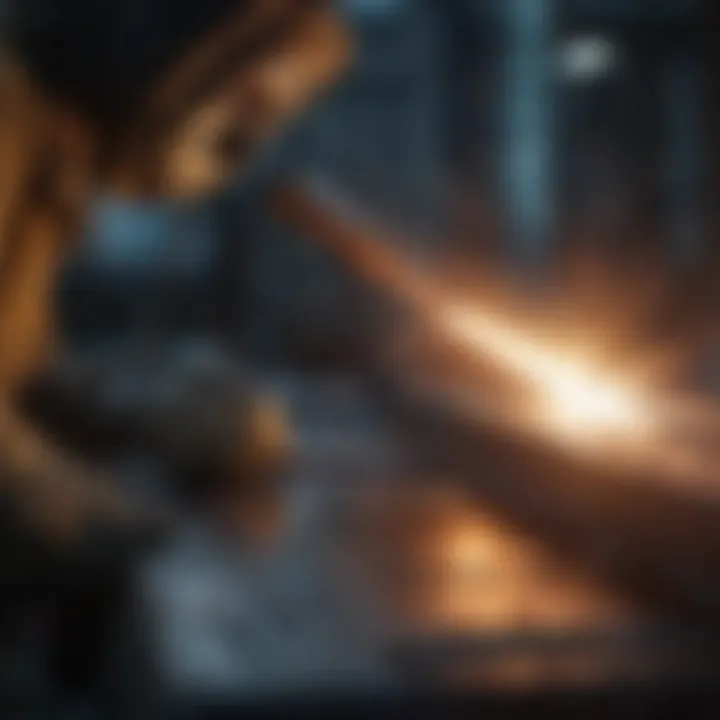
Furthermore, companies are increasingly emphasizing recyclability and lifecycle impacts of welding coatings. Materials that can be repurposed or recycled at the end of their life cycle are becoming preferred choices. Using powder coatings, which generate less waste and require fewer harmful solvents than liquid alternatives, is a prime example of how the industry is moving toward sustainability.
- Key aspects of sustainability in welding coatings include:
- Reducing reliance on non-renewable resources.
- Enhancing energy efficiency in production processes.
- Ensuring safe disposal or repurposing of used materials.
By considering sustainability from the outset, the welding industry can not only meet current regulatory demands but also shape future practices that align with broader environmental goals.
Future Trends in Welding Coatings
Welding coatings are in a constant state of evolution, shaped by both technological advancements and the ever-changing demands of various industries. Understanding the future trends in welding coatings is crucial, not only for those who work directly with welding processes but also for stakeholders involved in related fields. These trends reflect broader shifts in material science and application methods, making it easier to predict how these innovations can benefit welding integrity and efficiency.
Innovations in Materials
One of the most significant shifts in the landscape of welding coatings comes from the development of new materials. As industries increasingly lean towards high-performance and specialized applications, material scientists are busy experimenting with various composites and polymers. For example, the introduction of nanomaterials can significantly enhance coatings' wear resistance and thermal stability.
- Nanocomposites: These materials feature nanoscale particles that improve strength and decrease weight, which is vital for applications in aerospace and automotive sectors.
- Bio-based Coatings: There's a growing emphasis on sustainability. Companies are exploring biopolymer-based coatings made from renewable resources, minimizing environmental impact while providing effective protection.
- Self-Healing Coatings: Imagine a coating that can repair itself after a scratch or wear. This technology, though still in its infancy, shows potential for increasing the longevity of welds by automatically mending breaches in the coating.
The key benefit of these innovations is not just about enhancing the performance but also about addressing regulatory hurdles that require more environmentally friendly products. As these materials become commercially viable, they will likely redefine best practices in the welding industry.
Advancements in Application Techniques
Right alongside the material innovations sit advancements in various application techniques. These contemporary methods promise to streamline processes and improve the performance of coatings. Among these advancements, several stand out:
- Robotic Coating Systems: Automation has made significant inroads into welding processes. Robotic systems can apply coatings with precision and consistency that human hands cannot match, ensuring uniform thickness and coverage.
- Ultrasonic Spray Coating: This technique employs high-frequency sound waves to create fine droplets of coating material. It allows for better control over application thickness and minimizes overspray, thus saving materials and reducing waste.
- Laser Cladding: A more recent technique where the surface of a component is melted using a laser and coated with a powder at the same time. This allows for exceptional bonding between substrate and coating, enhancing durability.
These advancements support both efficiency and quality. With tighter tolerances and enhanced adhesion properties, the overall outcome is improved weld performance and lifespan. As techniques like these gain traction, they may eventually become standards within the industry, further solidifying the importance of coatings in welding practices.
The future of welding coatings is not just bright; it's innovative and essential. As industries adapt to new challenges, the right materials and techniques will be key to maintaining quality and performance in welds.
Case Studies on Coating Applications
The realm of welding coatings is underscored by a variety of applications across different industries. Understanding how specific coating technologies have been employed in real-world scenarios helps articulate their importance and effectiveness. Case studies provide tangible evidence of the advancements and challenges faced when integrating coatings into welding processes. They illuminate the practical benefits, such as enhanced performance, increased durability, and improved resistance to environmental factors. Moreover, these examples serve as a blueprint for industry professionals looking to informed decisions when selecting or employing coatings.
Industry-Specific Examples
Case studies can shine a light on unique applications of welding coatings, tailored to meet the specific needs of various industries. Below are a few notable examples:
Automotive Industry
In car manufacturing, protecting surfaces from corrosion is paramount. For instance, a leading automotive manufacturer implemented a zinc-rich primer coating on their vehicle bodies. This choice significantly curbed rust formation, thus extending the lifespan of vehicles by about 10 years. The performance of the primer was thoroughly evaluated, and a marked improvement in customer satisfaction was noted due to the reduced maintenance costs required over time.
Marine Applications
In maritime settings, vessels are exposed to aggressive environments, making protective coatings indispensable. A renowned shipbuilder utilized a polyurethane-based coating for their fleet. This coating was particularly effective in resisting the harsh effects of saltwater, leading to a 20% reduction in maintenance downtime. The study highlighted not just performance but also the economic advantage of fewer repairs and less repainting.
Aerospace Sector
In the aerospace industry, lightweight and durable solutions are often the crux of manufacturing. A case study involving titanium alloys showed that applying a ceramic coating resulted in improved thermal stability and wear resistance, which are crucial for aircraft components. Engineers found that this coating decreased wear-related failures by 40%, which ultimately enhanced aircraft safety and reliability.
Oil and Gas Sector
The oil and gas industry faces challenges regarding exposure to extreme temperatures and corrosive elements. An offshore drilling company integrated thermal spray coatings on drilling rigs. These coatings help mitigate wear caused by sand and other debris, proving so effective that the rigs’ operational lifespan increased by approximately 30%. It also minimized downtime, thereby allowing for more continuous operations.
In summary, these case studies illustrate the impressive effectiveness of welding coatings across various industries. They serve as a critical resource for industry practitioners aiming to optimize their processes and tools.
Epilogue on Case Studies
The examination of industry-specific examples underscores the significance of tailored solutions in welding coatings. Each sector has its unique demands, and understanding these through practical applications not only helps in making better decisions but also pushes the envelope on what's possible with these coatings. By reviewing successful case studies, professionals can gain invaluable insights into selecting the right welding coating that meets both immediate and long-term needs.
Ending
Understanding welding coatings is paramount in today’s industrial landscape. Coatings not only enhance the performance and longevity of welds but also contribute significantly to the overall safety and reliability of various welded structures. In this article, we have unpacked the diverse types of coatings, explored varied application methods, and discussed the chemical intricacies that play a vital role in weld integrity.
Summary of Key Points
- Definition and Purpose: Welding coatings serve as protective layers, providing resistance to corrosion, wear, and heat. By understanding the fundamental purpose, manufacturers can select the most suitable coatings for their specific needs.
- Types of Coatings: The world of welding coatings includes organic, inorganic, metallic, and hybrid options. Each type possesses unique characteristics tailored for different applications and environments.
- Application Methods: Methods such as spraying, dipping, and electroplating are crucial in achieving optimal coating adhesion. Each technique impacts the performance of the welds differently, and recognizing these differences can enhance application outcomes.
- Chemical Composition: Knowledge of key components and the role of additives helps in fine-tuning the properties of coatings, ensuring they meet the performance demands of specific welding processes.
- Environmental Considerations: With increasing regulations surrounding environmental impact, selecting sustainable coating materials has become more critical than ever. This consideration is vital for compliance and for appealing to a more eco-conscious market.
- Future Trends: Ongoing innovations in materials and application techniques promise to elevate the standards of welding coatings, enhancing performance while also meeting stringent environmental regulations.
Future Research Directions
As we look ahead, several areas warrant further exploration:
- Advanced Coating Materials: Developing coatings with improved resistance to extreme conditions could be a game-changer for industries such as aerospace and offshore engineering.
- Smart Coatings: Research into smart coatings could lead to surfaces that can detect and respond to environmental changes, offering real-time feedback on the integrity of welds.
- Biodegradable Options: Investigating biodegradable coatings can reduce environmental impact without compromising performance, an essential next step as sustainability continues to be a focal point in materials science.
"Future direction in welding coatings is not only about meeting current needs but also about anticipating future challenges."
In summary, a deeper understanding of welding coatings is crucial for professionals in the field. Balancing performance, safety, and environmental standards can lead to advancements that may redefine industry practices. As research continues to unfold, the potential for innovation in this area remains vast and inspiring.