Heat Treatment of Aluminium Alloys Explained
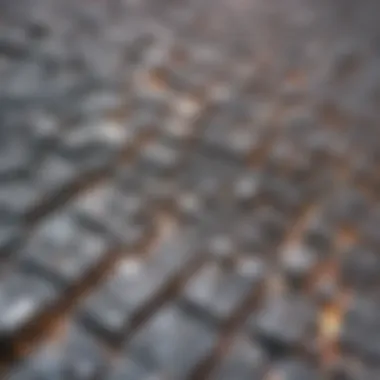
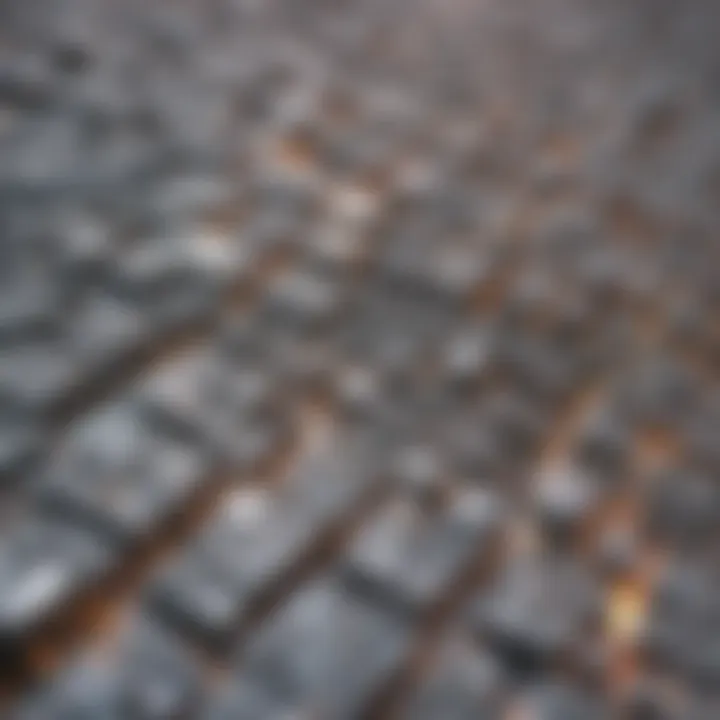
Intro
The heat treatment of aluminium alloys is a specialized process that significantly influences the mechanical properties of these materials. It involves various heating and cooling techniques to change the physical characteristics and improve performance under different conditions. Aluminium alloys are widely used in industries such as aerospace, automotive, and construction due to their lightweight and high strength. Understanding heat treatment is crucial for optimizing these properties.
Heat treatment entails several distinct processes, such as annealing, quenching, and aging. Each method serves a specific purpose, aimed at enhancing certain attributes of the alloy. For example, quenching is employed to increase hardness, while annealing generally improves ductility and stress relief.
As industries continue to demand materials that excel in performance and efficiency, the effective use of heat treatment becomes even more paramount. This article aims to elucidate the intricacies of heat treatment methods, their rationale, and their resultant microstructural changes.
The importance of this exploration lies in the backdrop of ongoing technological advancements and the practical application of aluminium alloys in modern engineering solutions.
Prolusion to Heat Treatment
Heat treatment is an essential process in metallurgy, particularly in the context of aluminium alloys. This section aims to unpack the fundamental aspects of heat treatment and underscore its significance in the performance of these materials. Understanding heat treatment is crucial for students, researchers, educators, and industry professionals, as it directly influences the mechanical properties and overall durability of aluminium alloys used widely in various applications.
Definition of Heat Treatment
Heat treatment refers to a controlled process of heating and cooling metals to alter their physical and sometimes chemical properties. The goal is primarily to enhance the strength, durability, and corrosion resistance of the alloys. In the case of aluminium alloys, heat treatment is often carried out using processes like solution treating, quenching, and aging. Each of these stages involves specific temperature ranges and times to achieve desired outcomes in the material's microstructure.
The heat treatment process generally follows these steps:
- Heating: The alloy is raised to a specific temperature where certain phases become soluble.
- Soaking: The alloy is held at that temperature for a given time to ensure uniform transformation.
- Cooling: It is rapidly cooled to lock in the desired structure.
Through these controlled processes, aluminium alloys exhibit improved characteristics that are tailored for a wide range of applications.
Purpose of Heat Treatment in Alloys
The purpose of heat treatment in aluminium alloys is multifaceted, primarily aimed at optimizing performance in various environments. The main objectives include:
- Enhancing Mechanical Properties: Heat treatment increases yield strength and hardness, allowing aluminium alloys to handle stress more effectively.
- Improving Machinability: The resulting microstructure can enhance the ease of machining and forming.
- Achieving Desired Electrical Conductivity: Specific treatment cycles can favorably affect the electrical characteristics of the alloy.
- Reducing Residual Stresses: Controlled heat treatment can relieve internal strains that develop during processing.
- Tailoring Corrosion Resistance: Heat treated alloys usually offer better resistance against corrosive environments.
By understanding the purpose and process of heat treatment, professionals can make informed decisions regarding alloy selection and treatment methods, ensuring optimal performance in their specific applications.
"Heat treatment is not merely a process; it is a strategic tool to unlock the full potential of aluminium alloys."
This introduction sets the stage for a deeper exploration of aluminium alloys and their intricate heat treatment processes, which will be discussed in subsequent sections.
Aluminium Alloys Overview
Understanding aluminium alloys is crucial in discussions about heat treatment, as their properties directly influence performance in various applications. These alloys are lighter than many metals, offer high strength-to-weight ratios, and have excellent corrosion resistance. Their flexibility makes them ideal for numerous industries including aerospace, automotive, and construction.
Both the classification and application of aluminium alloys play significant roles in their functionality. Comprehending the different types helps identify the specific alloy best suited for a particular use. The transformation of mechanical properties through heat treatment is deeply intertwined with the alloy’s characteristics. Therefore, a thorough overview is imperative for making informed decisions in selecting and treating these materials.
Classification of Aluminium Alloys
Aluminium alloys can be primarily categorized into two groups: wrought and cast alloys.
- Wrought Alloys: These alloys are shaped through mechanical processes and are generally available in various forms such as sheets, plates, and extrusions. Wrought alloys are further subdivided into series based on their alloying elements. For example, the 1000 series consists mostly of pure aluminium, while the 2000 series incorporates copper.
- Cast Alloys: These alloys are formed by pouring molten aluminium into a mold. Commonly used cast alloys include the 3000 and 4000 series, which contain elements like manganese and silicon, respectively.
The classification not only aids in identifying the alloys but also helps predict their behavior under heat treatment. Different series react variably to thermal processes, influencing their final properties.
Common Applications of Aluminium Alloys
Aluminium alloys find extensive use across many sectors for their beneficial properties. Some notable applications include:
- Aerospace Industry: Alloys such as 7075 are favored for their high strength and low weight, essential in aircraft designs.
- Automotive Sector: Lightweight alloys help increase fuel efficiency while maintaining safety standards in vehicle construction.
- Construction and Infrastructure: In building frameworks and facades, these alloys enhance longevity and reduce the overall weight of structures.
The versatility of aluminium alloys demonstrates why they are integral in so many high-performance applications. Heat treatment improves their mechanical properties, leading to enhanced performance in their respective fields. A deeper exploration of specific alloys and their treatment will further elucidate their significance.
Heat Treatment Processes
Heat treatment processes are integral to optimizing the mechanical properties of aluminium alloys. These methods involve specific temperature and time conditions applied to alloys to induce physical and structural changes that improve strength, toughness, and resistance to corrosion. Each process serves a unique purpose and comes with its own considerations, making them essential for producing high-quality materials that meet industry demands.
Solution Treatment
Solution treatment is a crucial step in the heat treatment of aluminium alloys. This process requires heating the alloy to a temperature that facilitates the dissolution of alloying elements into the aluminium matrix. The specific temperatures vary depending on the alloy composition, but they commonly range between 480°C to 550°C.
The objective of solution treatment is to create a uniform solid solution. This condition allows for greater strength to be achieved during subsequent processes. Rapid cooling, known as quenching, usually follows solution treatment to maintain this dissolved state at room temperature.
Benefits of solution treatment include:
- Improved Strength: The solid solution increases the alloys strength.
- Enhanced Ductility: Allows for better workability of alloys.
- Microstructural Homogeneity: It creates a more consistent microstructure.
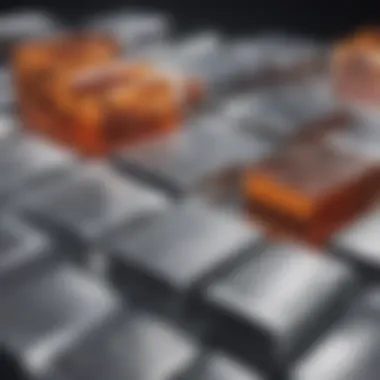
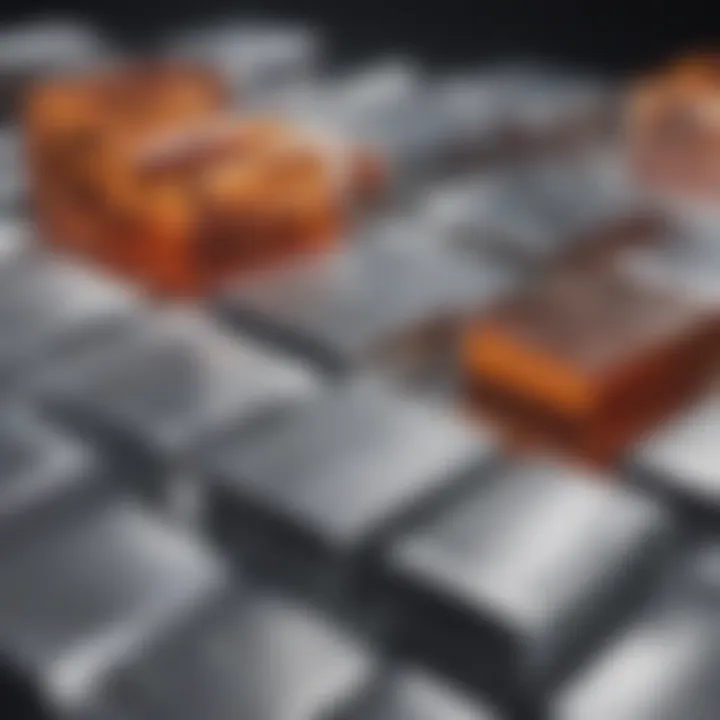
Quenching
Quenching is the rapid cooling process that follows solution treatment. In this step, the heated aluminium alloy is immersed in a cooling medium such as water, oil, or air. The choice of medium affects the cooling rate, directly influencing the mechanical properties of the alloy.
This process freezes the microstructure in a super-saturated condition. It ensures that the dissolved elements remain in solution instead of precipitating out. The speed of cooling is a critical factor, as it can profoundly impact hardness and yield strength.
Considerations for quenching include:
- Quenching Medium Selection: Different mediums (like water or oil) can provide different cooling rates.
- Part Size and Shape: The geometry can affect how uniformly a part is cooled.
- Warpage and Distortion Risks: Rapid cooling may lead to residual stress.
Quenching is often the most critical step that determines the final properties of aluminium alloys. Proper technique must be observed to avoid defects.
Aging
The aging process follows quenching and is vital for enhancing the alloy’s mechanical properties. Aging can be classified into two categories: natural aging and artificial aging.
Natural aging occurs at room temperature over time while artificial aging involves reheating the alloy to a specified temperature, then maintaining that temperature for a defined period. This encourages precipitation hardening, where fine particles form within the matrix, locking in strength and hardness.
Key aspects of aging include:
- Duration and Temperature: Careful control of aging time and temperature is essential for optimizing properties.
- Microstructural Changes: This stage transforms the grain structure, providing improved strength.
- Industry Specific Approaches: Different industries may require varying aging times and temperatures tailored to specific applications.
Factors Influencing Heat Treatment
Heat treatment of aluminium alloys is a multifaceted process. Several factors can significantly affect the overall outcome of this treatment. Understanding these factors is paramount for achieving desired mechanical properties and ensuring performance reliability in applications. Each aspect of heat treatment interacts with the alloy's inherent characteristics, thereby influencing its final properties. Here are three primary factors that play essential roles in the heat treatment process.
Alloy Composition
The alloy composition is a critical determinant of how an aluminium alloy reacts to heat treatment. Different alloys contain varying amounts of alloying elements, such as magnesium, silicon, copper, and zinc. Each element contributes unique properties and behaviors during heat treatment. For example, increasing copper content in Aluminium 2024 can enhance its strength post-treatment but may also lead to more sensitivity to stress corrosion cracking. Understanding the exact composition allows engineers to tailor heat treatment methods accordingly. The choice of heat treatment also considers the specific alloy's ability to undergo processes like solution treatment, aging, and precipitation hardening.
Temperature Control
Temperature during heat treatment plays a vital role. It directly affects the kinetics of metallurgical changes within the alloy's microstructure. Precise temperature management ensures that the alloy reaches critical transformation points without unnecessarily damaging its structure. Failure to maintain optimal temperatures can lead to under-treatment or over-treatment. In the case of quenching, for instance, if the temperature is too low, the desired hardness may not be achieved, while excessively high temperatures can result in undesirable grain growth. Therefore, controlling the treatment temperature is crucial for balancing strength and ductility, ultimately influencing applications in demanding environments.
Time Management
Time management during heat treatment affects the extent of the transformations occurring in the alloy. The duration of processes, such as solution treatment and aging, must be carefully documented and adhered to. For example, holding an alloy at a particular temperature for an insufficient period can hinder full dissolution of alloying elements. Conversely, prolonged exposure at high temperatures can lead to coarsening of precipitates and loss of strength. Effective time management supports consistent results and enhances the material’s performance in various applications. Predictable outcomes can also improve efficiency in production processes, reducing waste and costs.
In summary, understanding factors such as alloy composition, temperature control, and time management is essential for optimizing the heat treatment of aluminium alloys. This knowledge helps in enhancing mechanical properties and achieving desired performance.
Effects of Heat Treatment on Microstructure
The heat treatment of aluminium alloys significantly influences their microstructural attributes. Understanding these effects is crucial, as microstructure is directly linked to the mechanical properties that determine the performance of the material in various applications. When aluminium alloys undergo heat treatment, intricate changes occur at the microscopic level, which in turn affect the alloy's overall characteristics such as strength, ductility, and resistance to fatigue.
Grain Structure Changes
One essential aspect of heat treatment is the alteration of grain structure within aluminium alloys. The heating and cooling phases can lead to grain growth or refinement. Grain coarsening occurs during prolonged exposure to high temperatures, resulting in larger grain sizes that may decrease strength. Conversely, rapid cooling, or quenching, often leads to finer grain structures, enhancing strength through a higher surface area-to-volume ratio. The balance of these processes is critical, as fine grains typically improve toughness and strength but may also influence the alloy's plasticity and overall workability.
The phenomenon of recrystallization following solution treatment is another vital factor influencing the grain structure. This process repairs dislocations created during previous mechanical work, ultimately leading to a more uniform grain structure. When aluminium 6061 undergoes heat treatment, for instance, the resulting refined microstructure can enhance its application in high-pressure environments, where added strength is essential.
Precipitation Hardening Mechanisms
Precipitation hardening serves as a significant aspect of the heat treatment process, particularly for certain aluminium alloys like 7075 and 2024. Through aging, finely distributed particles precipitate from the solid solution, locking dislocations and providing significant strength improvements. The size and distribution of these particles are crucial; fine particles generally enhance the alloy's strength due to their ability to impede dislocation movement.
In this context, two main aging processes are noticeable: natural aging, which occurs at room temperature, and artificial aging, conducted under controlled thermal conditions. The artificial aging of aluminium 2024, for example, can optimize its performance for aerospace applications, yielding properties that exceed those of many competing materials.
Impact on Mechanical Properties
The mechanical properties of aluminium alloys can be dramatically altered as a result of heat treatment. Key factors include yield strength, tensile strength, elongation, and fatigue resistance. Heat treatment practices can lead to increased strength via solid solution strengthening and precipitation hardening, but they may also result in reduced ductility.
"The right heat treatment process can vastly improve mechanical performance, making components suitable for demanding applications."
For instance, aluminium 7075 exhibits higher yield and tensile strength when undergoes proper heat treatment, making it desirable for aircraft fuselages and high-stress components. However, it's vital to consider trade-offs; an alloy’s toughness might sacrifice for increased hardness, depending on the treatment chosen. Thus, selecting an appropriate heat treatment process is essential to achieving desired mechanical properties that suit specific applications effectively.
Common Aluminium Alloys and Their Treatment
The treatment of common aluminium alloys represents a foundation for understanding how heat treatment processes affect material performance. These alloys, which are formulated for various applications, exhibit distinct characteristics based on their composition and treatment methods. Recognizing the significance of this topic is crucial not only for engineers and manufacturers but also for students and researchers focusing on materials science. The benefits associated with optimizing heat treatment for each alloy can lead to improvements in mechanical properties, such as strength and corrosion resistance.
Moreover, when considering aluminium alloys, it is important to note their widespread use across industries like aerospace, automotive, and construction. Tailoring the heat treatment processes for specific alloys can open avenues for better product designs and enhanced functionality. By examining individual alloys and their unique treatment protocols, a comprehensive understanding of this field emerges.
Aluminium
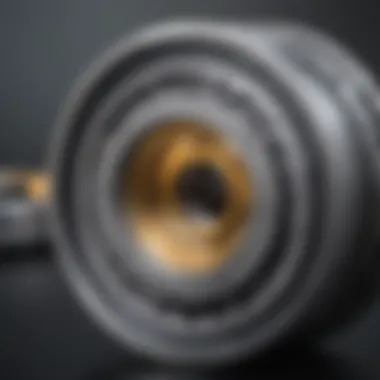
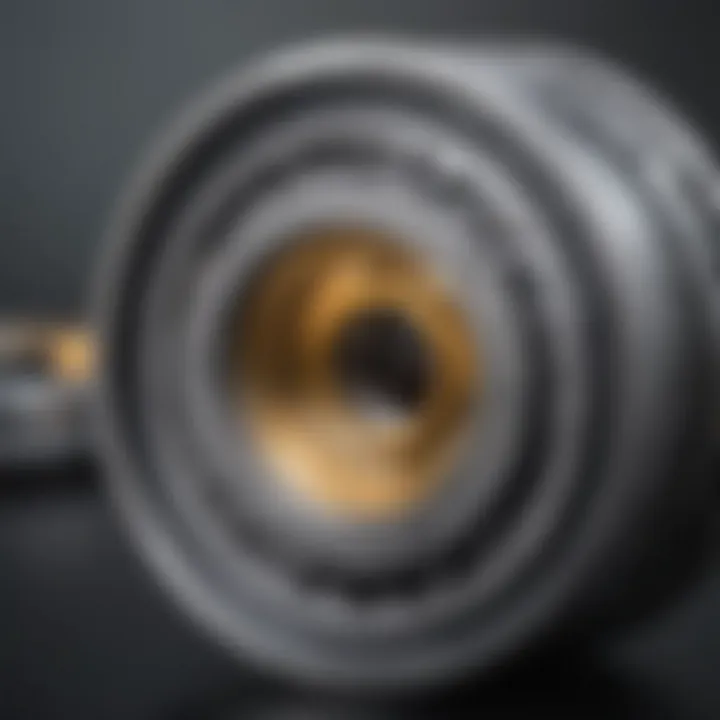
Aluminium 6061 is one of the most versatile aluminium alloys. It is widely used due to its good mechanical properties and weldability. This alloy belongs to the 6000 series, which means it is alloyed primarily with magnesium and silicon. When subjected to heat treatment, particularly the T6 temper, Aluminium 6061 exhibits significant increases in tensile strength and hardness. The heat treatment includes solution heat treatment, followed by aging.
In practical applications, Aluminium 6061 is commonly found in structural components, marine environments, and transportation. The ability to heat treat this alloy allows manufacturers to tailor its properties to suit specific demands. Its response to heat treatment plays a vital role in ensuring that the material can perform reliably under varying conditions.
Aluminium
Aluminium 7075 is well-known for its high strength, especially in the T6 condition. This alloy contains zinc as the primary alloying element, along with smaller amounts of magnesium and copper. The heat treatment process for Aluminium 7075 also involves solution treatment followed by quenching and aging. This sequence maximizes its mechanical performance.
Due to its exceptional strength-to-weight ratio, Aluminium 7075 is frequently used in aerospace applications, where performance and reliability are paramount. However, it is worth noting that this alloy can be susceptible to stress-corrosion cracking, making the heat treatment process critical for mitigating such risks. Properly executed, heat treatment enhances not only the strength but also the stability of this alloy under stress.
Aluminium
Aluminium 2024 is another high-strength heat-treatable alloy that is primarily alloyed with copper. This alloy offers excellent fatigue resistance and is often utilized in aerospace structures where weight reduction is crucial. Heat treatment for Aluminium 2024 typically involves the T3 and T4 tempers, achieving high strength through solution heat treatment and aging.
The specific heat treatment process for Aluminium 2024 impacts its mechanical properties significantly. Both static and dynamic properties are enhanced, which is critical in demanding applications. However, it is essential to recognize that this alloy has lower corrosion resistance compared to other high-strength aluminium alloys, which can necessitate additional protective measures in service environments.
Applications in Various Industries
The applications of aluminium alloys across diverse industries highlight the significance of understanding heat treatment processes. The unique characteristics of these alloys, combined with proper heat treatment, allow for enhanced performance and reliability in critical applications. Therefore, exploring the integration of aluminium alloys in various fields underscores the practical benefits, alongside the engineering considerations necessary for their optimal use.
Aerospace Industry
In the aerospace sector, weight reduction and strength are paramount. Aluminium alloys, known for their excellent strength-to-weight ratio, have become a preferred choice for aircraft manufacturing. The heat treatment processes, such as solution treatment and aging, optimize these alloys, ensuring they can withstand high-stress environments.
For instance, alloys like 2024 and 7075 are frequently used in airframes and other structural components. Their performance improves significantly once heat treated. Specifically, the aging phase enhances their yield strength, which is crucial for flight safety.
Moreover, the aerospace industry continues to push for innovations. Recent advancements, such as improved aging techniques, enhance the alloy characteristics even further. This commitment to improving heat treatments directly impacts the longevity and safety of aircraft.
Automotive Sector
Aluminium alloys are increasingly used in the automotive sector due to their potential to improve fuel efficiency and reduce emissions. The heat treatment of these alloys is crucial as it directly impacts the mechanical properties needed for strength and durability.
Alloys like 6061 are commonly seen in various automotive applications. These alloys benefit from heat treatment by becoming lighter while maintaining necessary performance standards. Quenching and aging processes contribute to minimizing weight without compromising strength. This balance is essential given the industry’s shift towards lighter materials to meet environmental regulations and consumer preferences.
The automotive industry is also exploring more advanced heat treatment technologies. Techniques such as rapid cooling and new aging cycles promise improved performance and quicker production processes. Consequently, the proper application of heat treatment technology contributes to the evolving demands of the automotive market.
Construction and Infrastructure
Similar to aerospace and automotive sectors, the construction industry benefits immensely from heat-treated aluminium alloys. These materials are valued for their corrosion resistance and structural integrity. The use of alloys in buildings and bridges means that the performance of heat-treated aluminium is critical.
For example, alloys are often utilized in applications for windows, doors, and other structural elements. Heat treatment processes enhance their durability, ensuring they withstand environmental stressors over time. Effective heat treatment methods, therefore, play a key role in maintaining the safety and longevity of infrastructures.
In addition, as construction practices evolve, there is a move towards more sustainable materials. Aluminium alloys, particularly those improved through heat treatment, offer green building solutions. Their recyclability and lower weight contribute to less resource-intensive projects. Thus, the importance of heat treatment in this context cannot be overstated as it aligns with global sustainability goals.
"The integration of heat-treated aluminium alloys in these industries is crucial for achieving both efficiency and safety."
Advancements in Heat Treatment Technology
The landscape of heat treatment technology is continuously evolving. Recent advancements have significantly improved the efficiency and effectiveness of treatments applied to aluminium alloys. These changes are not merely incremental; they often reflect a fundamental shift in how industries approach the heat treatment processes. Understanding these advancements is crucial for optimizing material properties and ensuring quality control in various applications.
Innovations in Heat Treatment Equipment
Modern heat treatment equipment has seen substantial innovations. Manufacturers have focused on enhancing precision and control in heating processes. Induction heating, for instance, allows for rapid and targeted heating, reducing energy consumption and improving consistency. Moreover, vacuum furnaces are increasingly employed for their ability to eliminate oxidation during the heat treatment process. This is vital for achieving superior surface quality in sensitive applications.
Another notable development is the implementation of computer-aided systems that monitor and automate the treatment cycles. These systems enable real-time adjustments to temperature and time parameters. This leads to a more consistent product outcome and reduces the likelihood of human error.
Process Optimization Techniques
Optimizing processes in heat treatment is essential for maximum efficiency and material performance. Mathematical modeling is one technique that has gained traction. By simulating different heat treatment processes, researchers can predict the outcomes and tailor treatments to specific alloys. This saves time and resources compared to trial-and-error approaches.
Furthermore, employing data analytics aids in understanding the relationship between process variables and mechanical properties. Analyzing large datasets allows professionals to identify patterns and inform decision-making. This analytic approach leads to better refinement of heat treatment protocols over time.
Research Trends and Future Directions
Current research in heat treatment is focusing on a few key areas. There is a growing interest in alternative energy sources for heating processes, such as microwave and laser technologies. These methods promise to deliver precise control over heating, with potential reductions in processing time and energy usage.
Additionally, studies on alloy modification during heat treatment processes are being explored. Researchers are investigating how adjusting alloy compositions can further enhance the effects of heat treatment. For instance, mixing different alloying elements may improve hardening effects or increase ductility in aluminium.
"The continuous evolution of heat treatment technology is paramount for adapting to the demands of modern industries."
As the landscape of heat treatment evolves, it is clear that staying informed about advancements will be crucial for professionals engaged in material science and engineering. By understanding these developments, experts can better apply innovative techniques to their work, leading to improved performance in aluminium alloys across multiple industries.
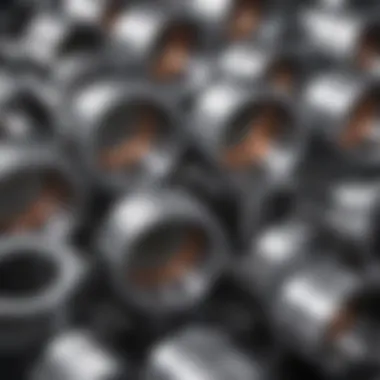
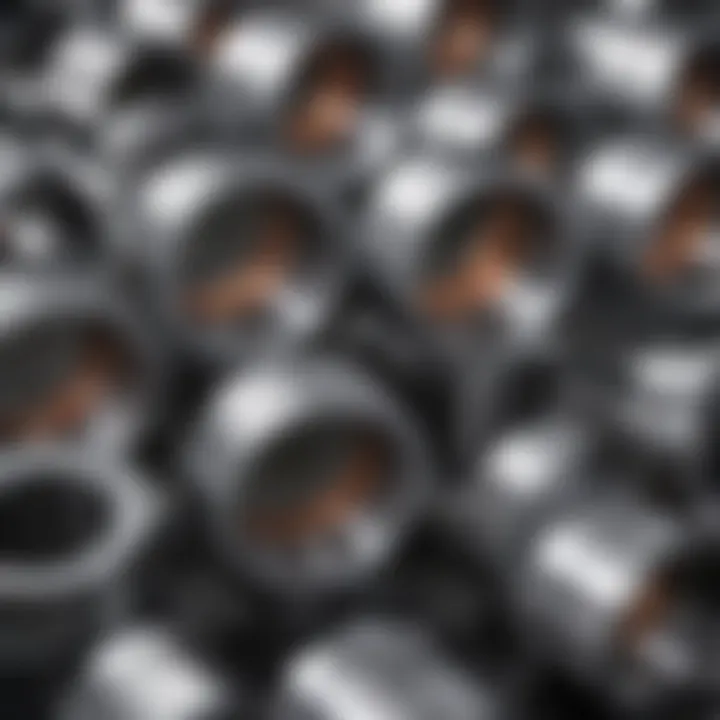
Challenges in Heat Treatment of Aluminium Alloys
Heat treatment of aluminium alloys is a complex procedure, and it does not come without challenges. Understanding these issues is crucial for optimizing heat treatment processes. The challenges can impact the quality, performance, and cost-effectiveness of the alloys produced. In this section, we will explore three key challenges: quality control issues, environmental considerations, and material cost implications. Each of these factors plays a significant role in the effectiveness of heat treatment practices.
Quality Control Issues
Quality control is fundamental in the heat treatment of aluminium alloys. Inconsistent heating, cooling rates, and treatment times can lead to variances in microstructure. These variations can alter mechanical properties, leading to failures in applications where performance is critical. Maintaining uniformity in heat treatment processes requires sophisticated monitoring and strict adherence to protocols.
Common problems include overshooting or undershooting temperature, which could cause incomplete softening or excessive hardness. Defects may arise in the form of unwanted precipitates or residual stresses. To mitigate these risks, investing in advanced furnaces and thorough training for operators is essential. Proper calibration and regular maintenance of heat treatment equipment can also help in achieving more reliable results.
Environmental Considerations
The environmental impact of heat treatment processes is an increasingly important consideration. Heat treatment often involves high energy consumption and emission of pollutants. Conventional fossil fuel-based heating methods contribute to greenhouse gas emissions. Therefore, more sustainable alternatives are being sought.
Some companies are turning to renewable energy sources for their heat treatment processes. This shift not only contributes to environmental sustainability but can also improve the corporate image and compliance with regulatory standards. Moreover, innovations in process efficiency that lower energy use and reduce waste can simultaneously enhance profitability and environmental performance.
Material Cost Implications
Material costs are a vital factor in any production process, and heat treatment is no exception. The expense of energy, equipment, and materials directly influences the overall cost of aluminium alloys. High-quality alloys often require precise control and extensive heat treatments, leading to elevated costs. For small-scale operations, these costs can be prohibitive.
To combat these concerns, manufacturers often seek economies of scale or invest in technology that reduces costs in the long run. Lean manufacturing principles can help streamline operations and minimize waste. However, these strategies require initial investment and sometimes lead to a temporary increase in costs.
Regulatory Standards in Heat Treatment
The regulatory standards in heat treatment are crucial for ensuring quality, safety, and performance of aluminium alloys. These standards govern the processes used in various heat treatment methods, thus providing a framework for manufacturers to adhere to. Understanding these standards is essential for industries utilizing aluminium alloys, as it influences both production efficiency and the final product's performance.
Regulatory standards can vary significantly between countries or regions. They establish baseline criteria for processes like solution treatment, quenching, and aging of aluminium alloys. Compliance with these standards can lead to improvements in product reliability and customer satisfaction. Furthermore, they can help mitigate legal risks and enhance a company's reputation.
In a global marketplace, staying compliant with regulatory standards is not optional. It is integral for businesses wishing to compete effectively.
"Adhering to regulatory standards is not just a matter of avoiding penalties, but also a strategic approach in enhancing product quality and customer trust."
Industry Standards Overview
Industry standards provide specific guidelines regarding the heat treatment of aluminium alloys. Organizations such as the American Society for Testing and Materials (ASTM) and the International Organization for Standardization (ISO) develop and publish such standards. These guidelines cover topics including the specific heat treatment procedures, allowable tolerances, and documentation requirements.
Some notable standards that relate to aluminium alloys include:
- ASTM B918: This standard outlines the requirements for solution heat treatment of aluminium alloys.
- ISO 9001: A general standard that includes quality management principles applicable to heat treatment processes.
- MIL-HDBK-5: Provides design properties of aluminium alloys, which is crucial when considering heat treatment.
Compliance with these industry standards assures that the heat treatment processes are consistent and reliable, which is vital for maintaining product integrity.
Certification Processes
Certifications play an important role in the heat treatment sector. They validate that facilities are operating in accordance with established standards and guidelines. The process often involves both an initial assessment and regular audits. For manufacturers, obtaining certification is a significant investment, but it is one that pays off in terms of credibility and market acceptance.
Typically, the certification process includes:
- Application: Organizations must apply through the respective certifying body.
- Assessment: An assessment team evaluates the operations, quality processes, and compliance with standards.
- Audit: Regular audits are conducted to ensure ongoing compliance.
- Certification Issuance: Once the organization meets all the requirements, a certificate is issued.
Several certification bodies are recognized globally, including AS9100 for aerospace manufacturers and ISO 13485 for medical devices. These certifications assure clients of a commitment to high standard practices in heat treatment processes.
Case Studies of Successful Applications
The study of case studies regarding the applications of heat-treated aluminium alloys provides crucial insights into real-world efficiencies and performance enhancements. These examples help to illustrate the direct impact of heat treatment processes on the mechanical properties and reliability of aluminium components in various industries. By exploring specific instances where heat treatment significantly improved product functionality, we can better understand its importance in the design and manufacturing processes.
High-Performance Aerospace Components
In the aerospace industry, the performance of materials is of utmost importance. Aluminium alloys such as 7075 can have their properties drastically altered through precise heat treatment. A notable case is the application of heat-treated Aluminium 7075-T6, which is commonly used in aircraft structures. This alloy exhibits exceptional strength and a favorable strength-to-weight ratio, making it ideal for components where these factors are critical.
One key benefit of utilizing heat treatment for this alloy is its ability to enhance fatigue resistance, which is essential for aircraft subjected to constant stress cycles. Notably, companies like Boeing have successfully employed heat-treated aluminium in various aircraft models, demonstrating improved lifespan and reliability. The optimization of heat treatment parameters, including temperature and time, allows for tailored mechanical properties that suit specific applications, whether it be airframes or engine components.
Innovative Automotive Solutions
In the automotive sector, the integration of heat-treated aluminium alloys is similarly transformative. A prime example is the use of heat-treated Aluminium 6061 in high-performance vehicles. This alloy is known for its excellent corrosion resistance and good weldability. Manufacturers such as Audi and Porsche utilize this alloy in their chassis and structural components, capitalizing on its lightweight characteristics while maintaining stringent performance metrics.
Heat treatment enhances the mechanical strength of 6061, leading to better safety features and fuel efficiency. Research has shown that vehicles constructed with heat-treated aluminium can achieve significant weight savings, contributing to lower emissions and improved handling performance. The case of the Audi A8 exemplifies how the implementation of refined heat treatment processes results in a superior product that meets both consumer expectations and environmental regulations.
Overall, these case studies reveal the critical role of heat treatment in the advancement of aluminium alloys across industries. By showcasing successful applications, we can ascertain how these processes contribute to enhanced performance, safety, and sustainability.
Closure
In summarizing the heat treatment of aluminium alloys, it becomes clear that this process is pivotal in optimizing the performance and applications of these materials. The importance of heat treatment cannot be overstated; it directly influences the mechanical properties such as strength, hardness, and ductility. Understanding the specific heat treatment processes allows manufacturers and researchers to select optimal conditions that align with the intended application of the alloy.
Summary of Key Points
- Heat treatment encompasses various processes, including solution treatment, quenching, and aging, each playing a distinct role in altering the microstructure of alloys.
- The influence of alloy composition and controlled processing conditions is critical for achieving desired mechanical characteristics.
- Research into new treatment technologies and advancements continues to reshape how industries approach aluminium alloy usage.
- Environmental considerations and regulatory standards are essential factors that impact the implementation of heat treatment processes in real-world applications.
- Effective heat treatment can lead to significant improvements in performance across critical sectors such as aerospace and automotive industries.
These elements collectively underscore the significance of heat treatment in the realm of metallurgical engineering and industry applications. By continuing to innovate and optimize heat treatment strategies, stakeholders can enhance alloy performance, meet regulatory requirements, and address the demands of modern engineering challenges.