Flat Panel Heat Exchangers: Design and Applications
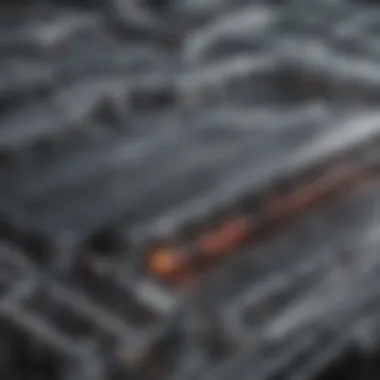

Intro
Flat panel heat exchangers are an essential component in a wide range of applications, from industrial processes to residential heating and cooling systems. Their unique designs and innovative principles offer several advantages over traditional heat exchangers, making them a topic of increasing relevance in engineering and energy efficiency discussions. These systems are designed to maximize thermal transmission while minimizing energy loss, which is critical in today’s world that strives for sustainability and cost-effectiveness.
As industries face heightened pressures to reduce energy consumption and minimize environmental impact, the importance of efficient heat exchange cannot be overstated. This article explores the fundamental principles governing flat panel heat exchangers, their diverse applications, and emerging technologies that are reshaping their landscape. Understanding the components that contribute to their efficiency can provide insight into how these systems play a role in the broader context of energy management.
Key Findings
An examination of the operational principles and applications reveals significant findings:
- Design Efficiency: The flat panel design contributes to greater surface area exposure for heat transfer, enhancing thermal efficiency. This contrasts with cylindrical tubular models that often suffer from lower heat exchange rates.
- Material Selection: Choosing suitable materials like stainless steel or polymer composites is crucial for ensuring durability and optimal performance across various temperature and pressure conditions.
- Maintenance Programs: Regular maintenance schedules are vital for extending the lifespan of heat exchangers and ensuring they remain energy-efficient over time.
- Emerging Technologies: Advances in material science and manufacturing processes are introducing new possibilities for the development of more effective and compact heat exchange systems.
To summarize, the overall efficiency of flat panel heat exchangers lies in their innovative designs, optimal material usage, and the impact of technology on future applications.
Methodology
In investigating flat panel heat exchangers, the following methodology was employed to structure the research:
Research Design
A qualitative approach was chosen to explore the operational principles and applications of flat panel heat exchangers comprehensively. This allowed for in-depth analysis of different case studies highlighting real-world applications.
Data Collection Methods
- Literature Review: A thorough review of existing academic and industry literature formed the backbone of the research, providing theoretical insights and contemporary advancements in flat panel heat exchanger technology.
- Case Studies: Examples from various sectors, including chemical processing and HVAC systems, provided concrete illustrations of the operational effectiveness and versatility of flat panel designs.
In creating this narrative, the aim is to strip away the technical jargon and provide a clear understanding that resonates with both seasoned professionals and newcomers to the field.
Preamble to Heat Exchangers
Heat exchangers are pivotal to various engineering applications, acting as the bridge that enables efficient thermal management across distinct systems. They facilitate the transfer of heat between two or more fluids without mixing them, which is crucial for optimizing energy use. Understanding these devices is not merely a matter of theoretical knowledge; it's central to the progress of industries ranging from power generation to food processing. In our exploration, we will dissect the core elements and specific types of heat exchangers, with an emphasis on flat panel designs, which have gained prominence due to their superior efficiency and compact footprint.
Through this discourse, one will appreciate how heat exchangers epitomize the principles of thermodynamics in action, illustrating real-world applications where comfort, safety, and energy efficiency converge. Effectively deploying these tools translates into cost savings and environmental benefits, making the study of heat exchangers particularly relevant in light of current sustainability efforts.
Fundamental Concepts
At the heart of heat exchange is the principle of thermal transfer, which can occur through conduction, convection, or radiation. Designers often focus on maximizing the effective surface area while minimizing thermal resistance. Factors such as temperature gradients, fluid velocities, and the properties of the conducting materials play crucial roles in how well a heat exchanger operates. By dissecting these concepts, engineers can innovate with designs that yield significant performance improvements.
Moreover, concepts like the overall heat transfer coefficient and fouling are essential. Fouling, for instance, refers to the accumulation of unwanted material on the heat exchanger surfaces which can reduce efficiency; understanding this plays a crucial role in maintenance and operational longevity.
Types of Heat Exchangers
Diving into the types of heat exchangers, we find a spectrum of designs that cater to specific needs and conditions. Each type boasts unique features that make it suitable for particular applications. Let’s look closer at a few prominent ones:
Shell and Tube Heat Exchangers
Shell and tube heat exchangers consist of a series of tubes, one set carrying the hot fluid and the other the cold fluid. Their main appeal lies in their robust design and ability to handle high pressures and temperatures. Because of this, they are often found in industries such as oil refineries and power plants.
A key characteristic that sets shell and tube heat exchangers apart is their adaptability. They can be designed for various flow configurations—counterflow, parallel flow, and even crossflow—which allows for flexibility in meeting specific process needs. Additionally, they can be cleaned and maintained with relative ease, which is a predominant advantage in many applications.
However, they do come with their downsides. Their larger footprint can be a limitation, especially in spaces where real estate is at a premium. Moreover, their complex design can lead to higher initial costs compared to simpler heat exchangers.
Plate Heat Exchangers
Plate heat exchangers, on the other hand, utilize thin plates stacked together to create a large surface area while minimizing the volume occupied. These are often praised for their efficiency in thermal transfer due to the increased surface area and turbulent flow patterns.
The standout feature of plate heat exchangers is their compact design, making them a delightful choice where space is limited, such as in food processing or HVAC applications. Their modular layout allows for easy cleaning and expansion, which is a significant selling point.
Nonetheless, they may face restrictions in dealing with high pressure applications as compared to shell and tube designs. Furthermore, their susceptibility to fouling can necessitate frequent cleaning, which could affect operational continuity.
Air Coolers
Switching gears, air coolers are devices that utilize ambient air to dissipate heat from fluid systems. They serve a critical function in applications where water is either scarce or expensive, providing an effective means of thermal exchange.
The core advantage of air coolers is their simplicity and low operating costs. They reduce the need for water resources, which is increasingly important in regions experiencing droughts or water shortages. Moreover, they can be designed to operate efficiently in a wide range of environmental conditions.
Nonetheless, they can be less efficient in high-temperature settings where the ambient air might not be able to absorb enough heat effectively. They are also limited in terms of the size of the installed cooling area, which could affect their cooling capacity for larger systems.
In summary, these various types of heat exchangers serve distinct roles across multiple sectors. Understanding their individual characteristics helps in selecting the right technology that aligns with operational needs, efficiency demands, and sustainability targets.
Understanding Flat Panel Heat Exchangers
Flat panel heat exchangers have carved a niche in various sectors because of their unique design and operational efficiencies. This section aims to deepen your understanding of their principles and applications, highlighting the benefits and critical considerations inherent to these systems. Whether in industrial plants or residential setups, knowing how flat panel heat exchangers function can offer insights into improving efficiency and sustainability.
Design Principles
Geometry and Layout
The geometry and layout of flat panel heat exchangers play a crucial role in their efficiency. Unlike traditional heat exchangers, which often feature complex shapes, flat panels simplify the design, providing greater surface area per volume. This streamlined geometry allows for effective heat transfer without taking up an inordinate amount of space.
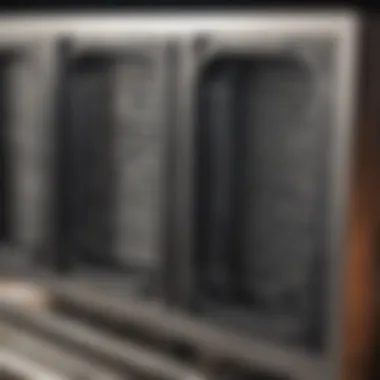
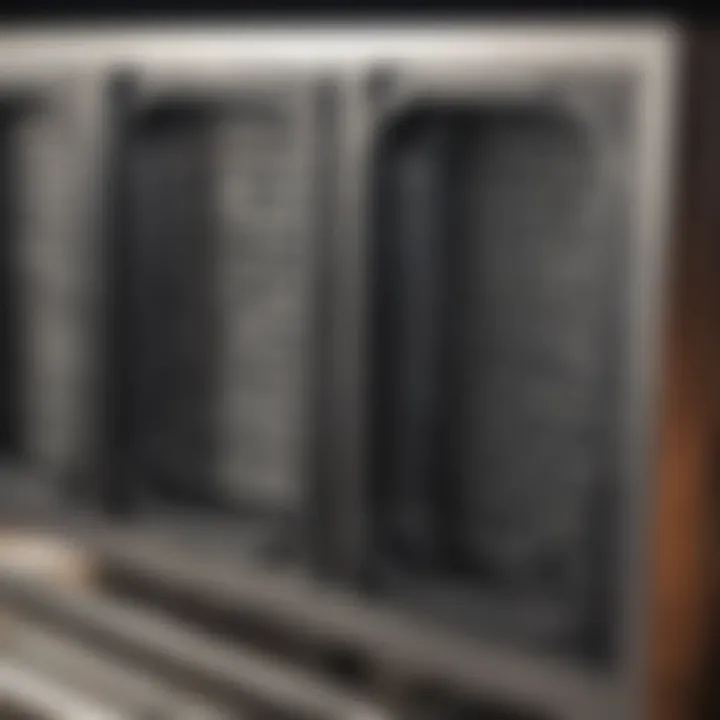
One of the key characteristics of this geometric design is its planar configuration. A benefit of this setup is the facilitated maintenance and cleaning process; dirt and scale can be easily accessed and removed. This stands in stark contrast to shell-and-tube designs, where accessing internal surfaces can be a cumbersome task. However, it’s worth noting that while flat panels excel in applications requiring compact spaces and efficient heat exchange, they may not be as robust in very high-pressure scenarios.
Another aspect to consider is the flexibility in layout. For instance, heat exchangers can be arranged in multiple configurations, optimizing flow paths depending on specific process requirements.
Surface Area Considerations
Surface area is a linchpin in enhancing the efficiency of heat transfer in flat panel heat exchangers. The larger the surface area, the more effective the heat exchange can be, and in these exchangers, the design allows for maximizing heat transfer through increased surface area. A unique feature is the use of fins or corrugated patterns that enhance the heat exchange effectiveness without significantly increasing the unit size.
A primary advantage of prioritizing surface area is that it encourages greater contact between the fluids involved. This characteristic makes flat panels a preferred choice in applications ranging from food processing to chemical production. However, it is essential to wisely balance surface area with pressure drops; an excessive focus on expanding the surface area could impede fluid flow, leading to inefficient operation.
Operating Mechanisms
Heat Transfer Modes
Understanding the modes of heat transfer in flat panel heat exchangers is essential for grasping their overall functionality. Generally, heat transfer occurs through conduction, convection, and sometimes radiation. The unique design allows for effective conduction through the panels while enhancing convection with increased surface area.
One key aspect of heat transfer modes in these systems is their high efficiency. Enhanced convection due to surface modification means temperatures can equalize quickly across fluids, which is crucial for processes needing rapid heat transfer. However, this efficiency comes with the trade-off of potentially higher material costs for specialized surfaces or coatings designed for optimal heat transfer.
Fluid Flow Dynamics
Fluid flow dynamics can make or break the performance of any heat exchanger, and flat panel designs are no exception. Here, flow characteristics—whether they follow a laminar or turbulent path—greatly influence the heat exchange efficiency. A fundamental feature of flat panel systems is their ability to promote turbulent flow, enhancing heat transfer rates.
Having a turbulent flow regime aids in minimizing thermal resistance, which is advantageous for processes needing steady temperature control. Nevertheless, careful consideration should be given to the potential for flow maldistribution, which can lead to ineffective heat exchange in certain areas and is something one should keep in mind when designing or selecting these systems.
"The adoption of efficient heating and cooling systems is not merely about cost-saving; it's about embracing a sustainable future."
Materials and Construction
When diving into the world of flat panel heat exchangers, the materials and construction are akin to the backbone of the whole system. Without the right materials, even a well-designed heat exchanger can fail to operate effectively, impacting efficiency and causing unexpected breakdowns. Every decision regarding materials affects overall performance, durability, and maintenance requirements, making it essential for proper selection and fabrication techniques.
Material Selection
In a nutshell, material selection plays a key role in ensuring that flat panel heat exchangers not only function well but also have a long lifespan. Two essential aspects of this selection process are corrosion resistance and thermal conductivity.
Corrosion Resistance
When talking about corrosion resistance, it’s about choosing materials that can withstand harsh conditions without deteriorating. Stainless steel is a standout option in this regard, celebrated for its ability to resist corrosion due to the presence of chromium. This quality ensures a longer lifespan and less frequent replacements, particularly in environments where heat and moisture are prevalent, like in chemical processing plants.
A unique feature of corrosion-resistant materials is their high resistance to pitting and crevice corrosion, common in heat exchangers exposed to aggressive fluids.
- Benefits:
- Low maintenance costs: Reduced need for repairs means savings over time.
- Longevity: Durable materials lead to fewer replacements.
However, they can be pricier upfront compared to less durable materials, which could be a hurdle for some projects.
Thermal Conductivity
On the flip side, thermal conductivity reflects how well a material can conduct heat. This characteristic is crucial, as we want heat exchangers to transfer heat efficiently without losing much energy. Copper and aluminum shine in this area due to their excellent thermal conductivity, making them popular choices in many applications.
- Advantages of Using Copper:
- Advantages of Using Aluminum:
- Superior heat transfer: Ensures higher efficiency.
- Ease of soldering and welding: Facilitates fabrication without complications.
- Lightweight: Easier to handle during installation.
- Cost-effective: Typically a cheaper option than copper.
Yet, copper has a downside: it can corrode, especially if exposed to certain environments, which means its performance can take a hit without proper care.
Fabrication Techniques
After selecting the right materials, fabrication techniques are the next layer in the construction of flat panel heat exchangers. How components are put together can vastly influence the final product’s performance. In this context, we will focus on welding and stamping as two prominent methods.
Welding
Welding is one of the most common fabrication methods, allowing for strong and durable joints. TIG (Tungsten Inert Gas) welding is widely used in the heat exchanger industry due to its clean and precise results. It provides significant strength and reliability, making it a popular choice for critical applications where leaks can be catastrophic.
The benefit of welding is its ability to join a variety of materials seamlessly, maintaining structural integrity under high pressures and temperatures.
- Advantages:
- Versatility: Useful across different materials.
- Strength: Creates robust connections.
However, some critics point out that the heat from welding can alter the material’s properties and introduce weak spots if done incorrectly.
Stamping
Stamping is another effective technique, often used to create complex shapes more efficiently than traditional machining. This method involves pressing metal sheets into desired shapes, reducing waste and improving production speed.
- Benefits of Stamping:
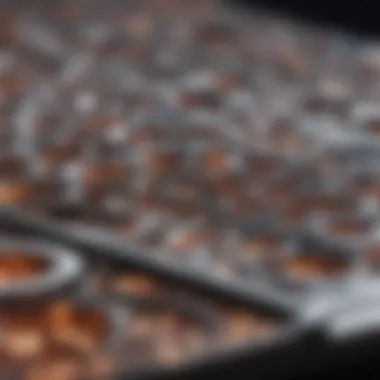
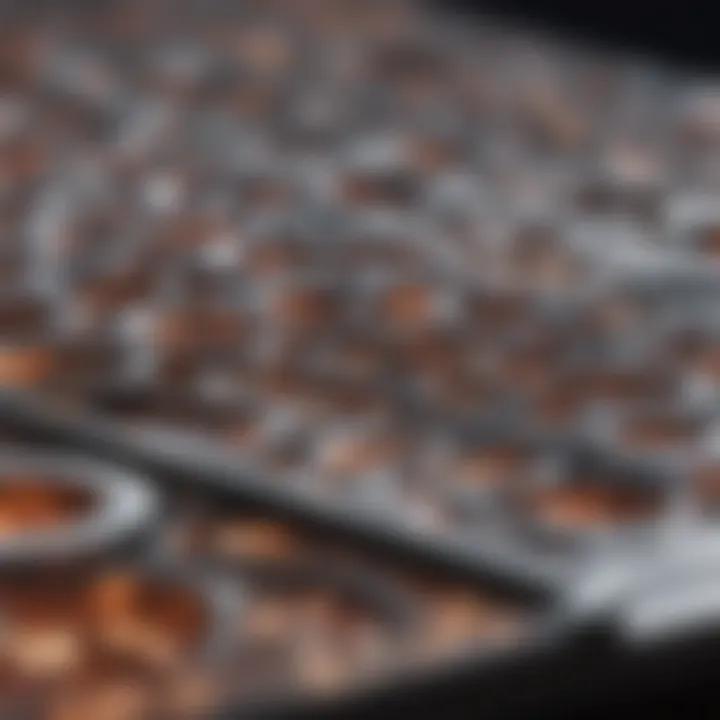
- Cost-effective for mass production: Reduces overall manufacturing costs.
- Consistent quality: Ensures uniformity in parts produced.
Yet, the limitations of stamping include a reduced flexibility in changing designs once production has begun, which could lead to inefficiencies if adjustments are needed.
Understanding these materials and fabrication techniques is vital, as they dictate how well a heat exchanger will perform in its intended applications, shaping both durability and efficiency.
Applications of Flat Panel Heat Exchangers
Flat panel heat exchangers serve a pivotal role in diverse fields, allowing for efficient thermal regulation. These devices are designed not just to withstand, but to excel in environments where effective heat transfer is essential. Their applications span across industries and residential settings, showcasing their versatility and effectiveness. By examining the different domains of use for flat panel heat exchangers, we can appreciate how they enhance systems and contribute to energy efficiency.
Industrial Applications
Power Generation
In the realm of power generation, flat panel heat exchangers play a critical role in maximizing energy output and minimizing losses. In many facilities, these heat exchangers are used to recover waste heat from processes, allowing operators to harness extra energy that might otherwise go to waste. This is a standout characteristic because wasted energy can represent significant operational costs. The ability of flat panel designs to incorporate a large surface area in a compact package means that they can efficiently transfer heat in a space-saving manner.
Their unique feature lies in their geometry, providing increased heat exchange capability compared to traditional tube designs. However, they might present some challenges in terms of pressure drop, especially in high-viscosity situations. Thus, it’s crucial for engineers in this industry to conduct proper assessments for optimal configuration.
Chemical Processing
Turning to chemical processing, flat panel heat exchangers are indispensable for their enhanced efficiency in heat recovery and temperature control. The hot and cold fluids that frequently circulate within chemical plants require precise temperature management; here, flat panel designs shine. Their key characteristic is their ability to accommodate a variety of substances, from gases to corrosive liquids, without significant degradation. This flexibility is valuable in processes that demand stringent thermal regulation.
What makes flat panel heat exchangers particularly beneficial is the reduced space requirement, which means that facilities can maximize their operational footprint. However, the trade-off comes in the form of less robustness compared to some larger systems, which can affect service life under extreme conditions.
Residential Usage
Heating Systems
When we consider heating systems in a residential setting, flat panel heat exchangers offer an elegant solution to home temperature management. They provide an efficient means to transfer heat from hot water systems to indoor air, facilitating comfortable living conditions. Their design allows for effective heat exchange while taking up minimal space, making them a favorable choice for cozy apartments or compact homes.
The primary advantage of incorporating these systems is their energy efficiency; they can significantly reduce heating bills compared to conventional radiators. Still, users must be mindful of the potential for scaling in hard water areas, which might reduce efficiency over time and require standard maintenance practices.
Cooling Solutions
Moving onto cooling solutions, flat panel heat exchangers also prove valuable in residential air conditioning systems. They facilitate heat away from the indoor environment and help to maintain pleasant temperature levels. A crucial aspect of these exchangers is their capability to optimally manage fluid flow, ensuring that cool air is distributed evenly throughout a space.
This particular setup can be cost-effective while maintaining temperatures with lower energy consumption. An obvious downside might be the potential for higher initial installation costs compared to simpler fan systems. But the long-term energy savings often outweigh these upfront expenses, making them an appealing option for energy-conscious homeowners.
Advantages of Flat Panel Heat Exchangers
Flat panel heat exchangers have carved a niche in modern thermal management systems, standing out for their innovative designs and increased functionality. Understanding the advantages they present over traditional heat exchangers is not just academic; it's essential for engineers, researchers, and end-users alike who seek efficiency, reliability, and sustainability in their operations. This section delves into the two primary benefits: enhanced efficiency and space optimization, detailing why these factors are pivotal in various applications.
Enhanced Efficiency
Efficiency is the name of the game when it comes to heat transfer technologies. Flat panel heat exchangers typically possess a higher heat transfer rate per unit area compared to conventional designs. This is primarily due to their increased surface area-to-volume ratio and the strategic arrangement of their plates which promotes turbulent flow, thereby facilitating more effective heat exchange.
- Better Heat Transfer: The geometry of flat panels, often characterized by thin plates with grooves or corrugated surfaces, maximizes contact between the hot and cold fluids, allowing for higher heat exchange coefficients.
- Lower Energy Consumption: Because of their efficiency, these systems can reduce energy use, translating to lower operational costs over time.
- Adaptivity to Process Variation: Whether it’s a sharp spike in temperature or varying flow rates, flat panel exchangers are more adaptable and can maintain efficiency under different operating conditions than their bulky counterparts.
A study found that integrating flat panel heat exchangers can lead to energy savings of up to 30% in thermal systems compared to shell and tube designs.
These advantages make flat panel exchangers discerning choices in tasks ranging from large-scale industrial heating to compact residential cooling. Their ability to deliver consistent performance across varied operational scenarios is particularly valued in settings such as power plants and chemical refineries.
Space Optimization
In today’s fast-paced world, real estate—be it physical or operational—is at a premium. Flat panel heat exchangers shine in scenarios where space is limited. Their compact design not only conserves valuable real estate but also simplifies installation processes.
- Space-Saving Design: The flat profile means these exchangers can fit into smaller footprints without compromising functionality, making them ideal for urban and constrained environments.
- Integration Ease: Their design allows for easier integration within existing systems, reducing the need for significant modifications to infrastructure.
- Streamlined Maintenance: Compact systems are generally easier to access and service; this means reduced downtime and labor costs associated with maintenance and inspection.
For example, in a high-density city setting where building space is tight, installing a flat panel heat exchanger can lead to efficient energy utilization without the necessity of expansive mechanical rooms. This capability not only meets regulatory demands for energy efficiency but also provides an aesthetic advantage, keeping facilities looking tidy and contemporary.
Maintenance and Performance
The efficiency and longevity of flat panel heat exchangers hinge significantly on rigorous maintenance and performance monitoring. Regular upkeep ensures optimal functioning, preventing costly breakdowns and inefficiencies. Over time, neglect can lead to various issues that diminish performance and increase operational costs, thus making maintenance not just a practical necessity but also a strategic approach in preserving the integrity of these systems.
Routine Maintenance Practices
Inspection Protocols
A pivotal aspect of routine maintenance is the implementation of robust inspection protocols. These protocols entail a systematic review of the heat exchanger's condition, focusing on signs of wear, corrosion, and potential leaks. Such inspections are crucial as they aid in identifying issues before they escalate into significant problems.
Key Benefit: Continuous checks allow for timely interventions, thus minimizing downtime and repair costs.
Moreover, these inspection protocols are beneficial because they help in maintaining the efficiency of heat transfer. A unique feature is the thoroughness with which these inspections can be conducted, often using advanced tools like thermal imaging cameras to assess performance without direct physical contact.
While the advantages are numerous, one must also consider the potential drawbacks. For instance, depending on the complexity of the heat exchange system, inspections may require specialized training and tools.
Cleaning Techniques
Equally important is the implementation of effective cleaning techniques. These methods are designed to remove fouling and scaling that can accumulate on the heat transfer surfaces over time. Keeping the surfaces clean is crucial for maintaining high thermal efficiency and prolonging the life of the exchanger.
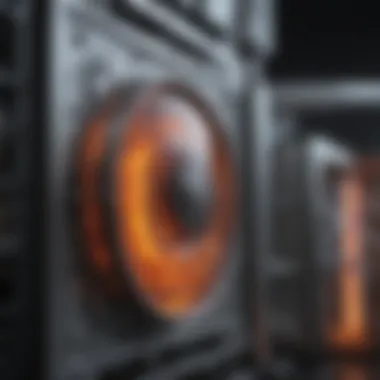
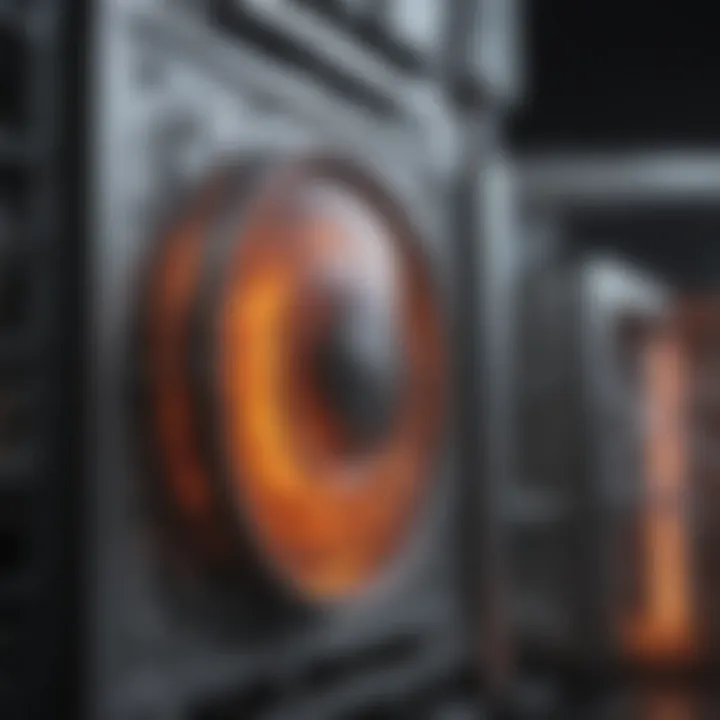
Why It is Popular: Cleaning techniques, such as chemical cleaning or high-pressure washing, enable the restoration of heat exchangers to optimal operating conditions. Regular cleaning prevents issues like reduced heat transfer rates, which can lead to inefficient operations.
The unique aspect of these cleaning techniques is that they can be tailored to the specific needs of the system, whether it be based on the type of fouling or the material composition of the heat exchanger. However, one downside could be the potential for damaging sensitive components if not executed properly.
Performance Monitoring
Performance monitoring encompasses the metrics and processes used to gauge the efficacy of flat panel heat exchangers during operation. This monitoring is critical as it provides insights into how well the system is meeting its intended thermal performance goals.
Heat Transfer Efficiency
Heat transfer efficiency is a core metric in performance monitoring. It measures how effectively a heat exchanger transfers heat from one fluid to another. The better the heat transfer efficiency, the less energy is wasted, which translates to cost savings in energy bills.
Key Characteristic: This measurement allows for an immediate understanding of system performance, making it a popular choice among professionals. Tools and systems are available that can continuously track this efficiency, providing real-time data for decision-making.
A unique feature of monitoring heat transfer efficiency is the ability to derive insights about the overall system's condition and functioning. It helps in devising proactive maintenance strategies that can preemptively address performance dips. Nevertheless, a potential downside is the need for sophisticated sensors and data analysis capabilities, which may require investment.
Pressure Drop Analysis
Lastly, pressure drop analysis represents another vital aspect of performance monitoring. It assesses the resistance encountered by the fluid as it flows through the heat exchanger. A significant increase in pressure drop can signal fouling or scaling, indicating that maintenance is due.
Why It Is Beneficial: Regularly conducting pressure drop analysis helps maintain operational efficiency and reduces the risk of damaging hydraulic shocks that can occur with fluctuating pressures.
One unique feature of this analysis is the ability to visually map the pressure profiles within the heat exchanger, providing valuable insights into fluid dynamics. However, this method's downside is that it may require complex calculations and calibrated equipment for accurate readings.
Future Trends in Flat Panel Heat Exchangers
The realm of flat panel heat exchangers stands at a crossroads of innovation and practicality. As industries strive for greater efficiency, the trends shaping these devices are not merely anecdotal; they carry the weight of significant advancements that promise to enhance both performance and sustainability. The importance of this discussion is crystal clear: understanding these trends is paramount for anyone involved in thermal engineering, product design, or facility management. We will explore a couple of major trends that are steering the development of flat panel heat exchangers.
Technological Advancements
Smart Sensors
Smart sensors are becoming the unsung heroes of flat panel heat exchangers. These devices monitor temperature, pressure, and even flow rates in real time, allowing for data that can inform operational adjustments and predict maintenance needs. Their ability to capture data on the fly means they can respond to changes almost instantaneously, which secures not just efficiency but also safety.
One key characteristic of smart sensors is their integration with IoT. This connectivity allows them to communicate with other devices and systems, promoting smarter decision-making processes.
A significant advantage is their capability to reduce downtime. By preemptively signaling maintenance issues, they help avoid those pesky surprises that can interrupt operations. However, these sensors also come with a caveat: they can be costly to implement and require a good understanding of data analytics to truly harness their potential.
Automation in Monitoring
Speaking of automation, monitoring is getting a serious upgrade with these technologies. The trend is moving towards fully automated systems that take monitoring out of manual hands and rely instead on software algorithms to track performance metrics.
The efficiency is undoubtedly one of the source’s benefits. Automated monitoring can provide consistent oversight without human error, thus ensuring optimal performance. Moreover, this automation can free up staff, allowing them to focus on strategic tasks instead of routine checks.
However, deploying automated systems can be a double-edged sword. These systems often require an initial financial bite that may not be immediately justifiable for smaller operations. Besides, without careful planning, there can be a learning curve associated with adopting automated monitoring technologies.
Sustainability Considerations
Energy Efficiency Initiatives
The push for energy efficiency is not just idealistic—it's essential for addressing global climate challenges. Such initiatives are becoming a focal point for industries looking to reduce their carbon footprints.
Energy efficiency combines cutting-edge design with practical operational strategies, leading to significant cost savings over time. Not only do these initiatives help organizations save on energy bills, but they also enhance public image, demonstrating a commitment to sustainability.
One unique feature is their adaptability; systems can be tweaked to improve efficiency without complete overhauls. Despite these advantages, the implementation of energy efficiency initiatives often takes time and resources that can be a burden for some sectors.
Recyclability of Materials
As the sector evolves, recyclability of materials is gaining traction. In an age where waste management is front and center in many discussions, materials that can be easily recycled minimize environmental impact and resource depletion.
One of the standout characteristics is how recyclable materials can be repurposed into new heat exchangers. This cyclic nature of material use reduces the demand for raw resources, making it a popular choice among environmentally-conscious businesses.
The only drawback here is the initial acquisition costs of materials that are recyclable, which can sometimes be higher compared to traditional options. Choosing sustainability involves weighing immediate costs against long-term benefits.
"Adopting flat panel heat exchangers isn't just smart—it's a step toward a greener future."
In summary, the future of flat panel heat exchangers looks promising. Technological advancements like smart sensors and automation in monitoring are leading the way for more efficient operations. Coupled with sustainability considerations such as energy efficiency initiatives and recyclability of materials, these trends are crucial for addressing both operational challenges and environmental concerns.
End
In the field of heat exchange technology, understanding flat panel heat exchangers is not just another academic endeavor; it’s pivotal for innovation and efficiency across numerous industries. The conclusion of this article synthesizes the core ideas presented in previous sections, highlighting their significance and exploring the avenues they open for future advancements.
Summary of Key Points
Throughout this discussion, we’ve journeyed through the intricate workings and applications of flat panel heat exchangers. Here’s a quick recap of the primary points that have been addressed:
- Design Principles: The geometry and layout of flat panel exchangers contribute significantly to their efficiency. This is achieved through thoughtful surface area considerations that allow for optimal heat transfer.
- Material Choice: Choosing the right materials ensures durability and performance. Properties like corrosion resistance and thermal conductivity play a crucial role in the longevity and efficiency of these systems.
- Operational Insights: Understanding the mechanisms of heat transfer and fluid flow dynamics impacts how effectively these exchangers perform their duties.
- Real-World Applications: Their role in both industrial contexts (like power generation and chemical processing) and residential applications (heating and cooling) showcases the versatility of flat panel design.
- Maintenance and Monitoring: Regular maintenance and smart monitoring practices help maintain their efficiency over time, ensuring they operate at peak performance.
- Future Directions: As technology evolves, we see more integration of smart sensors and sustainable practices influencing the effectiveness and applicability of flat panel heat exchangers.
Implications for Future Research
Flat panel heat exchangers represent a crossroads for numerous research opportunities. As industries increasingly prioritize sustainability and efficiency, exploring the implications of these exchangers could lead to significant breakthroughs. Some potential research avenues include:
- Enhancing Materials: Investigating novel materials that offer better thermal conductivities or improved resistance to corrosive environments could revolutionize how these exchangers are built and operated.
- Integration of Advanced Technology: With the rise of IoT, there is a great opportunity for research into smart systems that not only monitor but also optimize heat exchange processes in real-time.
- Sustainability Studies: Addressing how to recycle materials used in these exchangers can contribute positively to circular economy efforts in the manufacturing sector.
- Performance Benchmarking: Developing robust methodologies for evaluating the performance of flat panel exchangers as compared to traditional systems could provide concrete evidence for their benefits.
Understanding flat panel heat exchangers is not merely about grasping their current applications; it’s about acknowledging their potential to inform future developments in energy efficiency and sustainability. As we look forward, those diving into this field will likely uncover ways to harness their capabilities for a more energy-conscious world.