Finned Tube Cross Flow Heat Exchanger Explained
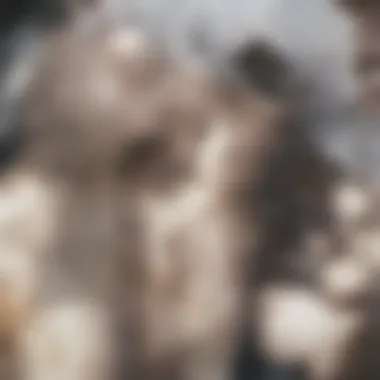
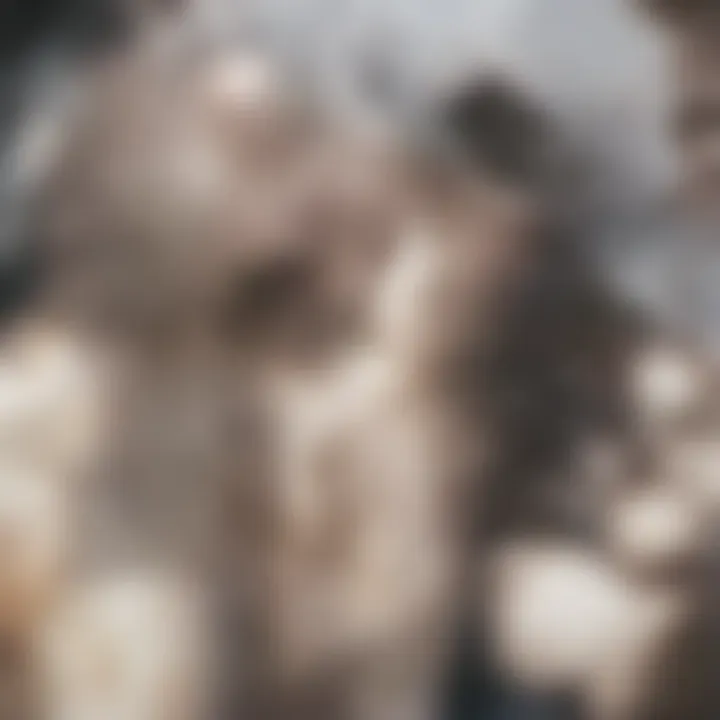
Intro
Finned tube cross flow heat exchangers play a vital role in numerous industrial applications. Their design optimizes heat transfer between two fluids, enhancing efficiency in thermal management systems. This article aims to dissect the various components that contribute to their functionality, provide insight into applications, and discuss emergent trends in technology.
Understanding these systems can help professionals make informed decisions regarding their implementation and optimization in various settings.
Key Findings
Finned tube heat exchangers are characterized by their ability to maximize surface area, facilitating improved heat exchange. Some key findings related to their efficiency and applications include:
- Effective Thermal Performance: Finned tubes significantly enhance heat transfer rates due to increased surface area.
- Versatility: They can be utilized in various sectors including HVAC, chemical processing, and food industries.
- Material Selection: Choosing suitable materials is crucial. Copper and aluminum are common due to their favorable thermal properties.
"Understanding the fundamental principles behind finned tube design can lead to significant improvements in industrial heat management."
Major Results
Research shows that finned tube designs can reduce energy consumption in heat exchange systems. Performance can be evaluated based on:
- Heat Transfer Coefficients: A measure of the effectiveness of the heat exchanger. Higher coefficients indicate better performance.
- Pressure Drop: Analyzing pressure drops helps understand the energy efficiency of the flow processes.
Discussion of Findings
The first observation is the influence of design configurations on both heat transfer and pressure drop. Studies indicate that a balance must be struck between maximizing heat transfer and minimizing energy loss. As such, fin efficiency becomes a critical parameter in design decisions. Future developments may focus on advanced coatings and design improvements.
Methodology
This section outlines the methods employed to gather relevant data and insight regarding finned tube cross-flow heat exchangers.
Research Design
A combination of empirical studies and computational modeling was employed. This dual approach facilitates a comprehensive understanding of performance metrics.
Data Collection Methods
Data was gathered from various sources, including:
- Industry reports on heat exchanger performance.
- Academic journals focusing on thermodynamics.
- Interviews and surveys with professionals in the field.
Preamble to Finned Tube Cross Flow Heat Exchangers
Finned tube cross flow heat exchangers are critical components in various industrial applications. These devices facilitate efficient heat transfer between two fluids, significantly driving energy efficiency. Understanding their functionality and design is vital for professionals engaged in fields such as chemical processing, HVAC, and power generation. This section introduces the essence of finned tube cross flow heat exchangers and emphasizes their significance in modern engineering.
Definition and Concept
Finned tube cross flow heat exchangers comprise tubes that are equipped with fins, enhancing the heat transfer surface area. This design optimizes the exchange of heat between two fluids moving in a perpendicular direction. The core principle relies on the increased surface area provided by the fins, allowing for greater heat transfer efficiency. Typically, one fluid remains in the tubes while the other flows around them, following a cross flow pattern. This configuration allows for more effective thermal interaction between the fluids than non-finned designs. The application of these heat exchangers leads to improved thermal performance in numerous systems, making them essential in achieving economic and operational efficiency.
Historical Development
The evolution of finned tube cross flow heat exchangers can be traced back to the early 20th century. As industries grew, the demand for more effective heat transfer systems increased. Initially, simple tube designs were utilized, but limitations in efficiency prompted further innovation. The introduction of fins marked a significant advancement, allowing for enhanced surface area and improved heat transfer rates. Over the decades, myriad designs emerged, catering to specific industrial needs. Contemporary designs leverage advanced materials and engineering techniques, optimizing both performance and lifespan. Today, finned tube cross flow heat exchangers have become an integral part of thermal management in various sectors, illustrating their ongoing importance and relevance.
Fundamental Principles
Understanding the fundamental principles behind finned tube cross flow heat exchangers is crucial for optimizing their design, functionality, and overall efficiency. These principles involve several aspects of heat transfer and fluid dynamics that play a fundamental role in how these systems operate. Discussion of these principles not only aids engineers in designing more effective heat exchangers but also cultivates a deeper comprehension of their operational mechanics. It serves as a foundation for innovation and advancement in the heat exchanger technology realm.
Basic Heat Transfer Principles
Conduction
Conduction refers to the heat transfer through solid materials, relying on molecular interactions. In finned tube heat exchangers, conduction occurs within the tube walls. The primary characteristic of conduction is its efficiency in transferring heat when the temperature gradient is high. This characteristic makes conduction particularly advantageous for situations where direct contact between two surfaces is inevitable.
The unique feature of conduction is that it is primarily dictated by the properties of the material, such as thermal conductivity. Metals like copper and aluminum are commonly used due to their high thermal conductivity. However, one of the disadvantages of conduction is that it can be somewhat slow over longer distances, leading to inefficiencies in larger systems.
Convection
Convection is the process of heat transfer through fluid motion. It becomes essential in finned tube heat exchangers as it facilitates heat exchange between the fluid inside the tubes and the surrounding environment. The key characteristic of convection is its ability to enhance heat transfer rates when compared to conduction alone. This characteristic is crucial for optimizing the performance of heat exchangers.
In a finned tube setup, the fins increase the surface area, promoting better convective heat transfer. This unique feature significantly enhances the overall efficiency of heat exchange. However, one downside can be that convection requires fluid movement, which can add complexity in some operational scenarios.
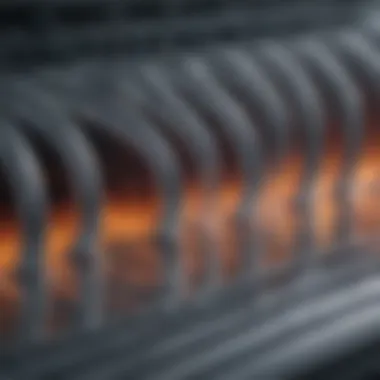
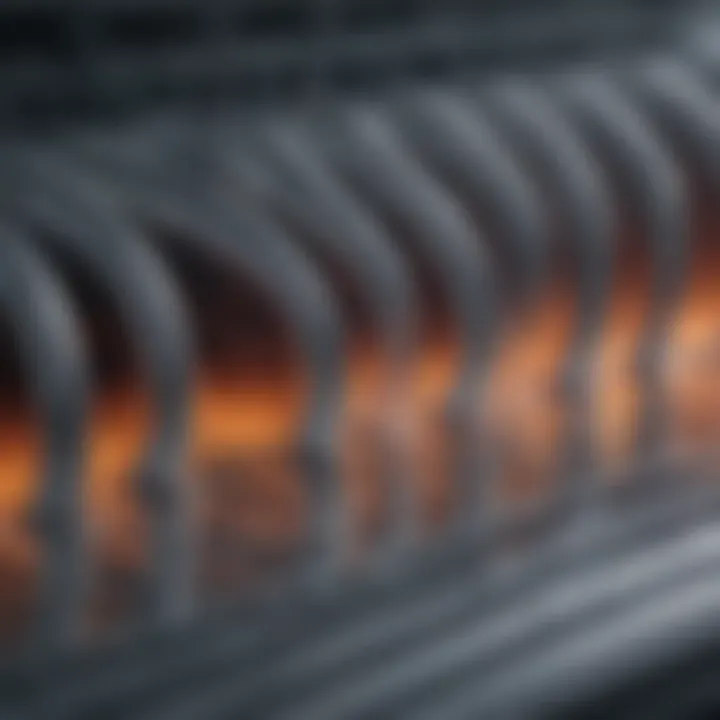
Radiation
Radiation is the heat transfer through electromagnetic waves and does not require a medium. In the context of heat exchangers, radiation is less significant compared to conduction and convection. The notable characteristic of radiation is that it can transfer heat even in a vacuum, making it essential for certain high-temperature applications.
In finned tube heat exchangers, radiation generally has a minor role due to the relatively low operating temperatures. Nonetheless, the unique feature of radiation is the ability to influence efficiency in particular setups or under certain conditions. The disadvantage is that radiation is less controllable and predictable compared to conduction and convection, making it a less favorable option in many applications.
Fluid Flow Dynamics
The dynamics of fluid flow significantly affect the efficiency and performance of heat exchangers. Understanding these dynamics assists in optimizing design and function, enabling more effective heat transfer processes.
Laminar Flow
Laminar flow is characterized by smooth and orderly fluid motion. In the context of a finned tube cross flow heat exchanger, laminar flow may not promote high heat transfer rates as the fluid layers slide past one another without significant mixing. This flow type is often more straightforward to analyze but might limit efficiency in certain applications.
The key characteristic of laminar flow is that it provides a very predictable and stable pattern of motion. In some designs, this predictability can assist in modeling and simulations. A unique advantage is less energy loss due to lower turbulence; however, the disadvantage is that this flow often results in higher thermal resistance compared to turbulent flow, potentially reducing the overall effectiveness.
Turbulent Flow
Turbulent flow is characterized by chaotic and irregular fluid motion. In finned tube heat exchangers, this flow type enhances the heat transfer rate by promoting mixing within the fluid. The primary characteristic of turbulent flow is this chaotic behavior, which significantly enhances convection by breaking the thermal boundary layers.
The unique feature of turbulent flow is its ability to increase the contact surface area between the fluid and the heat exchanger surface. Despite its well-documented efficiency, turbulent flow can lead to increased pressure drop and energy consumption, making it less economical in specific applications.
In summary, a comprehensive grasp of conduction, convection, and radiation helps in tailoring finned tube heat exchangers for optimal performance. Additionally, understanding fluid flow dynamics—both laminar and turbulent—enables more effective system design and usage.
Design Considerations
The design of finned tube cross flow heat exchangers is a critical aspect that contributes significantly to their overall performance. Effective design choices ensure increased efficiency, optimized space usage, and improved heat transfer capabilities. This section scrutinizes key elements like geometric configuration and material selection, which are vital for achieving desired thermal outcomes in various applications.
Geometric Configuration
Tube Arrangement
The tube arrangement in a heat exchanger directly affects its heat transfer efficiency. A common choice is the inline arrangement, where tubes are aligned parallel to each other. This configuration enhances flow turbulence, which in turn improves heat transfer rates. The main characteristic of this arrangement is its ability to maximize surface area in contact with the fluids.
Moreover, an inline tube arrangement is easy to manufacture and maintain. However, while it offers strong performance in many scenarios, its effectiveness can drop in cases of low flow rates due to potential dead zones.
Fins Design
Fins play an important role in enhancing the overall heat transfer by increasing the surface area available for heat exchange. Common designs include straight, louvered, and wavy fins. Each type has its own advantages and is selected based on the specific requirements of an application. For example, louvered fins are known for their high performance in terms of heat transfer efficiency due to the alteration in airflow.
The unique feature of fins design is their flexibility in modifying thermal performance without altering the main structure of the heat exchanger. However, too many fins can also lead to increased pressure drop across the exchanger, making it less efficient under certain conditions.
Material Selection
Thermal Conductivity
Selecting materials with high thermal conductivity is crucial in the construction of effective finned tube heat exchangers. Copper and aluminum are common choices due to their superior heat transfer capabilities. A key characteristic of thermal conductivity is its direct correlation with efficiency; the higher the thermal conductivity, the more efficient the heat transfer process.
Copper, for instance, boasts excellent conductivity and is often chosen for applications requiring maximum heat transfer. Nevertheless, its higher cost can be a limiting factor compared to alternatives like aluminum, which also provides good performance at a lower price point.
Corrosion Resistance
Corrosion resistance is essential, especially in industries that deal with corrosive fluids. Materials that can withstand chemical degradation, such as stainless steel or specially coated metals, are preferred in these scenarios. The main characteristic of corrosion-resistant materials is their ability to maintain structural integrity over time.
Choosing corrosion-resistant materials eliminates maintenance challenges and extends the lifespan of the heat exchanger. However, these materials can come at a higher initial cost, which might be a consideration for some manufacturers.
Selecting the right materials for finned tube heat exchangers ensures not only efficiency but also longevity and reliability in demanding environments.
In summary, understanding the detailed aspects of design considerations, including geometric configurations and material selection, is crucial for optimizing the performance of finned tube cross flow heat exchangers. This helps industries appreciate the trade-offs involved in the design and make informed choices that align with their operational objectives.
Operational Mechanism
Understanding the operational mechanism of finned tube cross flow heat exchangers is essential for grasping how these systems efficiently manage heat transfer. The operational mechanism encompasses the heat transfer process and the flow arrangements that dictate the exchanger's performance. This section explains the intricacies of these processes, emphasizing their significance in optimizing overall heat exchange efficiency.
Heat Transfer Process
The heat transfer process in finned tube cross flow heat exchangers is a complex interplay of conduction, convection, and sometimes radiation. When fluid flows through the tubes, heat is transferred from the hot fluid to the fins and, subsequently, to the cooler fluid surrounding the tubes.
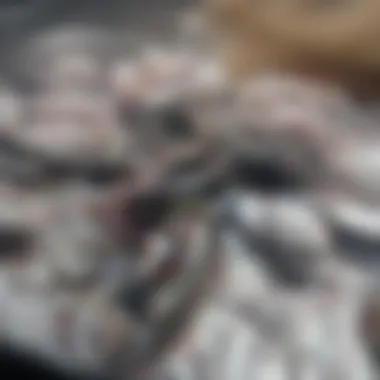
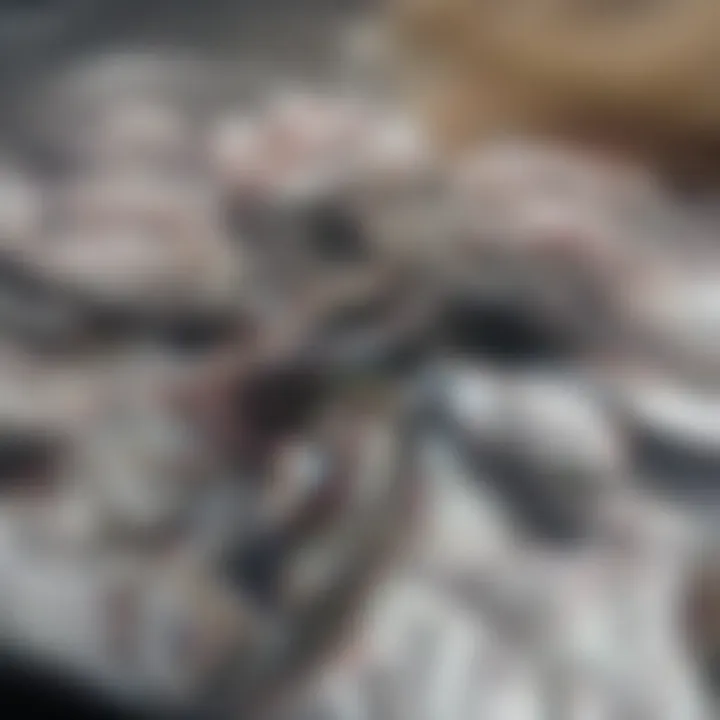
- Conduction occurs when heat moves through the material of the tube walls. The thermal conductivity of the materials used is crucial here. Materials with high thermal conductivity, such as copper or aluminum, are often preferred to maximize heat transfer.
- Convection plays a significant role in the heat exchange process. It involves the movement of fluids and the resultant heat transfer. In finned tube designs, fins enhance the effective surface area, allowing for increased heat transfer rates between the fluids. The effectiveness of convection is influenced by fluid velocity, density, and viscosity, which affect how heat is exchanged.
Key Insight: The design and arrangement of the fins directly correlate with heat transfer efficiency. A well-optimized fin design can significantly improve the performance of the heat exchanger.
Flow Arrangement and Patterns
Flow arrangements and patterns are vital elements in the operational mechanics of finned tube cross flow heat exchangers. The arrangement determines how the fluids interact with the heat transfer surfaces, impacting efficiency and performance metrics.
Finned tube heat exchangers can be designed to facilitate several flow arrangements, including:
- Counterflow: In this arrangement, the two fluids flow in opposite directions. This setup often yields the highest thermal efficiency as the temperature difference between the fluids is maintained across the length of the heat exchanger.
- Parallel flow: Here, both fluids move in the same direction. While simpler in terms of design, this configuration generally results in lower heat transfer efficiency compared to counterflow.
- Crossflow: In this configuration, one fluid flows perpendicularly to the other. This type is often used in applications where space is limited. While crossflow configurations may not achieve the thermal performance of counterflow designs, they can be advantageous in certain installation contexts.
Each arrangement has its own set of advantages and limitations that must be navigated based on specific operational requirements. A careful analysis of flow patterns and heat exchange efficiency helps in selecting the most appropriate design for the intended application.
Applications in Various Industries
Finned tube cross flow heat exchangers play a significant role across various industries. Their ability to enhance heat transfer efficiency has made them vital in many applications. Understanding these applications, their underlying benefits, and specific considerations is essential for professionals in engineering and technology. This section will provide insights into the areas where these heat exchangers are applied, showcasing their value and versatility.
Chemical Processing
In the realm of chemical processing, finned tube heat exchangers provide an efficient way to manage thermal energy. These systems handle the heat exchange between various fluids, crucial for maintaining operational temperatures across processes. Their design allows for a high surface area, which enhances the transfer of heat between hot and cold fluids. Such exchangers assist in reactions, heating, cooling, or even condensing processes.
Key benefits of utilizing finned tube exchangers in chemical processing include:
- Increased Efficiency: The finned design maximizes surface area, allowing for effective heat transfer with minimal energy loss.
- Space Optimization: They occupy less space compared to traditional exchangers, an important factor in many industrial setups.
- Customizability: Finned tube designs can be tailored to fit specific operational needs, whether in cooling towers or reactors.
HVAC Systems
In heating, ventilation, and air conditioning (HVAC) systems, finned tube cross flow heat exchangers serve as critical components. They are often applied in air handling units or in heat recovery systems where thermal efficiency is a priority. By facilitating heat exchange, these exchangers help in energy conservation and improving the overall HVAC performance.
The advantages of incorporating finned tube designs in HVAC systems are noteworthy:
- Energy Savings: They significantly lower energy consumption, which is increasingly essential considering the rising energy costs and environmental concerns.
- Enhanced Performance: Improved heat transfer rates contribute to better temperature control and indoor air quality.
- Longevity: Made with corrosion-resistant materials, finned tubes have a longer life span and require less maintenance.
Power Generation
In power generation, finned tube cross flow heat exchangers are indispensable. They are utilized in steam boilers, condensers, and cooling systems to improve efficiency in thermal cycles. Their efficient heat transfer capabilities optimize the conversion of thermal energy into electricity.
The role they play in power generation encompasses several aspects:
- Maximizing Output: They enhance the efficiency with which heat is converted to power, thereby increasing the overall output of power plants.
- Environmental Considerations: Improved efficiency leads to reduced emissions and better compliance with environmental standards.
- Versatility: They can be found in various sectors, from renewable energy plants to traditional thermal power stations.
"The versatility of finned tube cross flow heat exchangers across industries underscores their critical role in enhancing thermal efficiency and reducing energy consumption."
By understanding the applications in chemical processing, HVAC systems, and power generation, stakeholders can better appreciate how finned tube cross flow heat exchangers contribute to industry advancements. Their integration represents a commitment to efficiency and innovation.
Advantages and Limitations
The evaluation of advantages and limitations plays a crucial role in understanding finned tube cross flow heat exchangers. Evaluating these aspects helps professionals identify the suitability of this technology for specific applications. While finned tube heat exchangers offer remarkable heat transfer efficiency and versatility, several considerations must be addressed when implementing this technology in real-world scenarios.
Efficiency Benefits
Finned tube cross flow heat exchangers are renowned for their efficiency in enhancing heat transfer. The design incorporates extended surfaces, known as fins, which increase the surface area available for heat transfer. There are several key benefits:
- Higher Thermal Performance: The fins facilitate greater contact between the heat transfer fluid and the tube surface, leading to improved thermal performance.
- Optimized Space Utilization: By increasing efficiency, these heat exchangers can operate within smaller physical dimensions, making them suitable for confined spaces.
- Energy Savings: Enhanced heat transfer efficiency translates into reduced energy consumption for heating or cooling processes, leading to operational cost savings over time.
Furthermore, improved heat transfer characteristics make these exchangers ideal for applications requiring stringent thermal management, such as in power generation or chemical processing industries.
Economic Considerations
In the current economic landscape, economic implications of implementing finned tube heat exchangers should be analyzed comprehensively. Certain aspects warrant attention:
- Initial Investment: These exchangers, particularly when tailored for specific applications, can require a substantial initial investment. The costs associated with specialized materials and manufacturing processes are notable.
- Lifetime Costs: While the upfront costs may be high, potential reductions in energy consumption can offset these expenses over time. Hence, overall lifecycle costs tend to favor finned tube heat exchangers in suitable scenarios.
- Maintenance Expenses: Depending on the materials used and operating environment, maintenance costs may vary significantly. Corrosion resistance and longevity of the materials selected will influence these aspects.
Taking these factors into consideration can guide organizations in determining the long-term financial viability of using this technology.
Potential Drawbacks
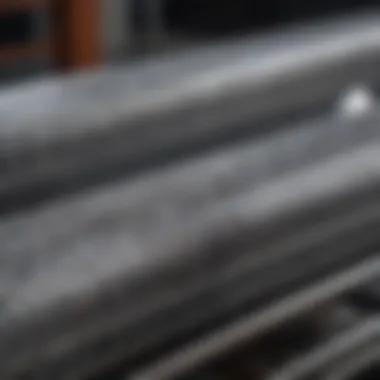
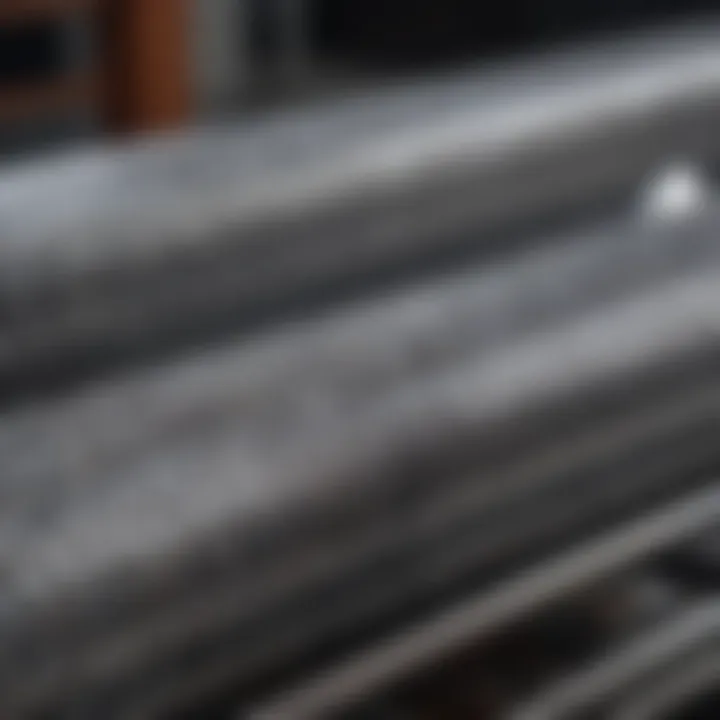
Despite their well-known advantages, finned tube cross flow heat exchangers can exhibit some limitations that are essential to consider. A few of these drawbacks include:
- Complexity in Design: Designing an effective finned tube heat exchanger requires careful consideration of various factors, including fluid dynamics and thermal transfer. This complexity can increase the risk of errors during design and implementation.
- Limited Effectiveness at Low Flow Rates: These exchangers may be less effective when operating at low flow rates. As a result, applications requiring minimal fluid movement might not benefit from fin configurations as intended.
- Potential for Fouling: Accumulation of debris on fins or tubes can hinder performance. Regular cleaning and maintenance practices become crucial to ensure sustained efficiency.
Understanding these potential drawbacks enables engineers and designers to make more informed decisions about the use of finned tube heat exchangers in specific settings. It is important to weigh the benefits against possible limitations tailored to the unique operational conditions.
Performance Optimization Techniques
Performance optimization is a crucial aspect of finned tube cross flow heat exchangers. The efficiency of these systems directly influences their applications in various industries, such as HVAC, chemical processing, and power generation. This section outlines specific techniques to enhance the overall performance of heat exchangers. Each technique provides unique benefits that can make a significant difference in operational efficiency and cost-effectiveness.
Enhanced Fin Designs
Fins are integral components of a heat exchanger. Their primary role is to increase the surface area available for heat transfer. Different fin designs can enhance thermal performance significantly. Here are a few relevant design strategies:
- Plate Fins: These fins are flat and provide ample surface area. Their design encourages better air flow and efficient heat dissipation.
- Lanced Fins: This type involves indentations in the fins that facilitate fluid mixing. It enhances turbulence, leading to a more effective heat transfer.
- Serrated Fins: This design increases surface area even further. The serrations disrupt boundary layers, improving convective heat transfer.
In summary, optimizing fin design can lead to more effective heat exchange, making systems more efficient and compact.
Fluid Flow Manipulation
Manipulating fluid flow is another powerful technique for optimizing performance in finned tube heat exchangers. The way fluids move through the system can affect heat exchange rates, pressure drops, and overall efficiency. Important considerations here include:
- Flow Rate Adjustment: Altering the flow rate can enhance heat transfer efficiency. However, higher flow rates may increase energy consumption, so a balance is necessary.
- Flow Arrangement: The configuration of the fluid path affects heat exchanger efficiency. Counterflow arrangements typically offer better performance than parallel flow designs, as they maintain a higher temperature differential.
- Use of Baffles: Baffles can create turbulence in the flow, increasing contact between the heat transfer surfaces and the fluid. This disruption helps maintain efficiency during the transfer process.
By focusing on these optimization strategies, engineers and designers can significantly improve the performance of finned tube cross flow heat exchangers, ensuring they meet the specific needs of their applications.
Future Trends in Finned Tube Technology
The field of finned tube cross flow heat exchangers is poised for substantial innovation and improvement. Understanding the future trends in this technology is vital for students, researchers, educators, and professionals who aim to stay ahead in the industry. These trends encompass advancements in materials and design software, which promise significant enhancements in efficiency, performance, and sustainability.
Innovations in Materials
Innovations in materials are pivotal for the evolution of finned tube heat exchangers. As industries strive for higher efficiency and longer service lives, new materials are being developed that offer improved thermal conductivity and corrosion resistance. For instance, the introduction of titanium and advanced alloys can lead to increased heat transfer efficiency under harsh conditions.
Some notable trends include:
- Expanded Use of Composite Materials: These materials can provide significant benefits in terms of weight reduction and heat transfer performance.
- Surface Treatments: Techniques such as coatings that enhance thermal exchange and protect against corrosion are being researched and implemented more frequently.
These advancements in materials not only improve performance but also contribute to lowering operational costs over time. Overall, the exploration of innovative materials holds great promise for enhancing the reliability and efficiency of finned tube heat exchangers.
Advancements in Design Software
The landscape of design software is rapidly changing, directly impacting the effectiveness of finned tube technology. Modern software solutions enable better simulation and modeling of heat exchangers, allowing for more sophisticated design strategies.
Key aspects of these advancements include:
- Computational Fluid Dynamics (CFD): This technology allows engineers to analyze and optimize fluid flow and heat transfer characteristics in greater detail than ever before.
- User-Friendly Interfaces: Software is becoming more accessible, making it easier for professionals who may not be experts in fluid dynamics to design efficient systems.
- Integration with AI and Machine Learning: These technologies help in predicting system performance and identifying optimal designs rapidly.
Such enhancements in design software lead to reduced design cycles and a more intuitive understanding of how-to configure heat exchangers for maximum efficiency. As a result, professionals can create models that adapt to varying operational conditions more accurately.
"The future of finned tube technology rests on the synergy between innovative materials and advanced design tools, unlocking new levels of performance for heat exchangers."
By keeping abreast of these future trends, stakeholders in various industries can ensure they leverage the full potential of finned tube cross flow heat exchangers. Doing so allows not only for improved performance but also contributes to a more sustainable and economically viable approach in the long term.
The End
The examination of finned tube cross flow heat exchangers culminates in a recognition of their significant role in optimizing thermal efficiency across various industrial applications. This conclusion synthesizes the main elements highlighted in the article, offering insights on the relevance and potential directions for future studies.
Summary of Key Points
Finned tube cross flow heat exchangers stand out for several reasons:
- Efficiency: They enhance the heat transfer process by increasing the surface area available for heat exchange, leading to better thermal performance.
- Versatility: These exchangers find applications in chemical processing, HVAC systems, and power generation, showcasing their functional adaptability.
- Design Considerations: The geometric configuration, including tube arrangements and fin designs, plays a critical role in determining their effectiveness and suitability for specific applications.
- Material Choice: The selection of materials based on thermal conductivity and resistance to corrosion influences the longevity and reliability of these heat exchangers.
- Optimization Techniques: Improved fin designs and manipulation of fluid flow conditions can significantly enhance performance.
This summary encapsulates the essence of finned tube cross flow heat exchangers. It highlights their operational principles, performance efficiencies, and various industrial applications.
Implications for Future Research
Future research should focus on several key areas:
- Material Innovations: Exploring new materials that offer higher thermal efficiency and improved corrosion resistance can enhance heat exchanger performance and lifespan.
- Advanced Design Models: Development of innovative design software can facilitate better simulations of heat transfer processes and fluid dynamics, leading to more efficient heat exchanger configurations.
- Sustainability Studies: Investigating the environmental impact of heat exchanger technologies, including lifecycle assessments can provide insight into their sustainability.
- Control Systems: Enhancements in control technologies can lead to better operational stability and efficiency in the varying conditions faced in industrial applications.
These trajectory touchpoints paint a promising landscape for the evolution of finned tube cross flow heat exchangers, urging researchers and practitioners to delve deeper into technological advancements and methodologies.