Comprehensive Insights into Finite Element Stress Analysis
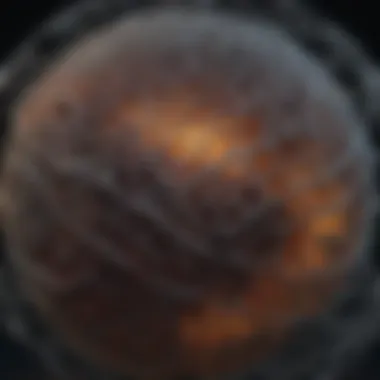

Intro
Finite Element Stress Analysis (FESA) stands as a pivotal element in the engineering toolkit. With increasing demands for performance and reliability in structural design, understanding how to evaluate stress conditions within materials and structures is essential. Engineers and researchers utilize FESA to predict how components will react under various external forces, thus enhancing both safety and design efficacy.
When employing FESA, one begins with a discrete representation of a continuous physical structure. By segmenting the structure into smaller, manageable elements, engineers can analyze how each part contributes to overall performance. This approach not only simplifies complex problems but also facilitates a detailed examination of critical stress points.
Key Findings
Major Results
The findings from recent applications of FESA indicate substantial advancements in predictive accuracy. Enhanced computational power and sophisticated algorithms have transformed the efficiency of analyses. Key results observed from various studies include:
- Improved stress distribution predictions leading to optimized material usage.
- Enhanced load-bearing capacity in redesigned structures.
- Increased lifespan of engineered systems due to better understanding of fatigue.
In practical applications, industries such as aerospace, civil engineering, and automotive have embraced FESA to optimize their designs, ensuring that safety standards are met and exceeded.
Discussion of Findings
The implications of these findings are profound. Industries leveraging FESA benefit from reduced material costs and decreased risk of failure. Furthermore, as software tools evolve, engineers are better equipped to visualize stress concentrations and potential failure points, minimizing the need for physical prototypes. This not only streamlines the design process but also accelerates time-to-market for new innovations.
Methodology
Research Design
The research design for understanding FESA typically follows a structured approach. It often includes:
- Defining the problem and determining the goals of the analysis.
- Selecting appropriate software tools that can handle the complexity of the model.
- Establishing boundary conditions and external load scenarios that the model will face.
Data Collection Methods
Data collection in FESA revolves around obtaining accurate material properties and refining the model. Common methods include:
- Laboratory testing of materials to gather stress-strain data.
- Using historical performance data from similar structures to inform assumptions.
- Leveraging simulations to predict responses to varied loading conditions.
Prelims to Finite Element Stress Analysis
Finite Element Stress Analysis (FESA) plays a crucial role in engineering design and evaluation. It equips engineers with the ability to predict how complex structures will respond to various forces and conditions. This systematic approach helps in optimizing designs, improving safety, and assuring reliability. Understanding the fundamentals of FESA is essential for engineers, students, and researchers who wish to explore this analytical method thoroughly.
Defining Finite Element Analysis
Finite Element Analysis (FEA) is a numerical method used to predict how structures react to environmental factors. This method divides a large system into smaller, simpler parts known as finite elements. By analyzing these elements, engineers can comprehensively understand the physical behavior of materials and structures under various conditions. This process allows for modeling complex geometries, loadings, and boundary conditions.
The finite element method involves several steps: discretization, application of boundary conditions, solving governing equations, and interpretation of results. Each step is critical to ensure accuracy and effectiveness. Discretization, the initial step, involves converting a continuous domain into a finite number of elements. This creates a mesh over the structure, where each node represents a key point for analysis.
Importance of Stress Analysis
Stress analysis is vital for ensuring structural integrity and safety. By understanding where and how stress concentrates within a structure, engineers can make informed decisions to mitigate risks. Stress analysis helps identify potential failure points, allowing for redesign or reinforcements where necessary.
The benefits of conducting stress analysis include:
- Safety Assurance: Ensuring that structures can withstand the applied loads without failure.
- Cost-Effectiveness: Preventing expensive damages and redesigns by identifying flaws early in the design process.
- Performance Optimization: Enhancing the design to perform well under specific conditions, improving functionality.
- Compliance with Standards: Meeting industry regulations and safety guidelines is essential.
"Understanding stress distribution within materials is fundamental in creating durable and safe structures."
Theoretical Background
The theoretical background is crucial in understanding finite element stress analysis (FESA). This knowledge sets the stage for how engineers and researchers approach the complexities of structural analysis. By grasping the fundamental principles and mathematical formulations, one can critically evaluate the results offered by FESA. A solid theoretical framework also aids in assigning meaning to empirical data, ensuring accurate interpretation when applied to real-world scenarios.
Principles of Mechanics
Principles of mechanics provide the foundation for FESA. They dictate how forces interact within a structural element. The basic laws include Newton's laws of motion and the principles of static and dynamic equilibrium. Understanding these concepts is essential.
- Static Equilibrium: This refers to the condition where a structure remains at rest under applied loads. The sum of forces and moments acting on the structure must equal zero.
- Dynamic Equilibrium: This focuses on structures in motion and requires analysis of inertia and acceleration, often needing consideration of time-dependent loads.
When applying the principles of mechanics to FESA, one can define the behavior of materials under various loading conditions. This leads to accurate stress distribution predictions. Importantly, these principles help define boundary conditions, an essential aspect when modeling complex systems.
Constitutive Laws
Constitutive laws describe the relationship between stress and strain within a material. They are key in defining how materials deform under loads. Understanding these laws helps engineers predict how materials behave without extensive experimental trials.
Different materials exhibit varied behaviors:
- Linear Elasticity: Common in metals, this assumes a direct relationship between stress and strain, following Hooke's Law.
- Plasticity: This applies when materials yield under stress but do not return to their original shape when the load is removed.
- Viscoelasticity: Important for polymers and biological materials, this considers time-dependent strain, affecting how materials respond to loads over time.
Understanding constitutive laws allows for a more nuanced approach to material modeling, resulting in more accurate finite element models and conclusions.
Thus, both principles of mechanics and constitutive laws form the backbone of any finite element analysis. Incorporating these elements into FESA ensures accuracy and reliability, making it a powerful tool in engineering.
Mathematical Formulations
Mathematical formulations are the backbone of finite element stress analysis. They provide the necessary framework to understand and interpret the behavior of materials under various load conditions. By translating physical problems into mathematical equations, engineers can develop models that represent real-world scenarios. This process is critical because it allows for the evaluation of complex structures and materials that would be impossible to compute using traditional analytical methods.
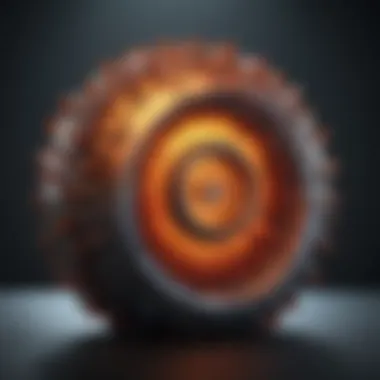

Key benefits of mathematical formulations include:
- Precision: They offer precise calculations that predict how structures respond to forces and moments.
- Flexibility: Formulations allow for a variety of geometrical configurations and material properties.
- Efficiency: Solvers can process these formulations to produce results faster, saving time in design and assessment.
In summary, mathematical formulations are essential in the finite element analysis process, linking theoretical constructs with practical applications.
Discretization Process
The discretization process involves breaking down a continuous domain into a finite number of elements. This step is essential because it enables the numerical solution of differential equations that govern structural behavior. Each element represents a small part of the structure, and together, these elements approximate the entire domain.
The process includes:
- Defining the shape and size of elements.
- Determining nodal points where displacements and forces are calculated.
- Ensuring the mesh is fine enough to capture variations in stress accurately, while not so fine that computational resources are wasted.
Choosing the correct approach in the discretization process is crucial for achieving accurate results in finite element stress analysis.
Finite Element Equations
Finite element equations arise from the discretization of the domain. They are integral to solving the governing equations of the physical problem, providing a system of equations that can be solved simultaneously. The equations encompass different components, notably the stiffness matrix, load vector, and nodal displacement.
Stiffness Matrix
The stiffness matrix represents the relationship between nodal displacements and the forces applied to the system. It quantifies how a structure resists deformation when subjected to loads. The main characteristic of the stiffness matrix is its ability to incorporate the mechanical properties of materials and geometry into the equations.
- Benefits: A well-constructed stiffness matrix ensures accurate load distribution across elements and is a key part of stability analysis.
- Unique Feature: The matrix is often symmetric for linear problems, allowing for efficient numerical solutions.
- Considerations: While stiffness matrices are powerful tools, they can become large and complex, leading to increased computation time for very large systems.
Load Vector
The load vector consists of the forces acting on the nodal points of the mesh. It provides the input necessary for an accurate representation of loads in the analysis. Each component reflects the external forces applied to each node, ensuring the global equilibrium of the structure.
- Key Aspect: Its main utility lies in correctly modeling how loads impact the response of the entire system.
- Unique Feature: The load vector can represent various load types, including point loads and distributed loads, translating them into the finite element framework.
- Advantages: Implementing an accurate load vector can significantly affect the precision of the results, enhancing overall confidence in the analysis.
Nodal Displacement
Nodal displacement describes how much each node moves, which is essential for calculating stresses and strains within the structure. It serves as the primary unknown that the analysis aims to solve. Understanding nodal displacement is critical because it allows engineers to derive valuable insights about the internal responses of structures.
- Key Characteristic: Nodal displacement provides a direct link to understanding how structural changes will manifest under given loads.
- Importance: Accurate nodal displacement calculations are crucial for evaluating performance under operational conditions.
- Disadvantages: Precision in calculation may require sophisticated algorithms, which can pose challenges for very complex models.
In short, mathematical formulations and their components play a vital role in finite element stress analysis. Their effective application enables precise modeling of real-world structures, facilitating better design and safety evaluations.
Types of Finite Element Models
Finite Element Analysis (FEA) benefits from various types of finite element models. Understanding these models is crucial for selecting the appropriate approach for a given engineering problem. Each model type can significantly affect the results obtained and the overall analysis process. The choice between different models influences accuracy, computational efficiency, and the ability to account for specific physical phenomena.
Linear vs. Nonlinear Analysis
Linear analysis assumes that material properties remain constant and changes in geometry do not occur. This simplification can lead to solutions that are often quicker to obtain. In linear analysis, the response of the material is directly proportional to the applied loads. Commonly, linear static analysis is sufficient for many cases, especially when dealing with small deformations and elastic materials. The use of this approach can streamline calculations and reduce computational demand.
On the other hand, nonlinear analysis addresses situations where assumptions made in linear analysis do not hold. This can occur due to large deformations, yielding materials, or even contact between bodies. Nonlinear behavior can significantly complicate simulations. As a result, models must often incorporate more sophisticated numerical techniques. This type of analysis can reveal much-needed insights into failure mechanisms and material behavior under extreme loads. Nonlinear analysis is essential in fields like structural engineering and automotive design, where real-world conditions often lead to non-linear responses.
Some engineers may choose to start with linear models to quickly gauge system behavior before delving into more complex nonlinear analysis when required. Understanding when to apply each type of analysis is essential for effective FEA.
Static vs. Dynamic Analysis
Static analysis evaluates the response of a structure under steady loading conditions. This method accounts for loads that do not change over time, such as the weight of a building. Static analysis simplifies the calculations needed, as time-dependent factors are not considered. It is often a first step in examining structural integrity because it can efficiently determine critical stresses and deformations in systems.
In contrast, dynamic analysis involves evaluating structures under time-varying loads or conditions. Such loads might include impacts, vibrations, or seismic events. Dynamic analysis requires much more complex formulations as it must take into account inertia and damping characteristics of materials. These factors can drastically influence how structures perform under realistic conditions. Performing dynamic analysis is essential for applications involving machinery, aerospace, and earthquake engineering, where load conditions can change rapidly.
In summary, the type of finite element model chosen has profound implications on the accuracy and applicability of the results. Whether using linear or nonlinear solutions, or focusing on static versus dynamic analysis, engineers must consider the specific requirements of their projects for optimal outcomes. The selections made here affect the final design's efficacy and safety.
Boundary Conditions and Load Applications
Boundary conditions and load applications are central themes in finite element stress analysis. They dictate how a structure interacts with its environment and how forces are transferred within it. Understanding these elements is vital to ensure accuracy and reliability in analysis results. Properly defined boundary conditions and load applications help in modeling realistic behavior of materials and structures under stress. They are foundational for predicting structural performance and ensuring the safety of engineering designs.
Essential and Natural Boundary Conditions
Essential boundary conditions, often associated with displacement constraints, specify the values that certain displacements must take at boundaries. For instance, in a cantilever beam, the fixed end is assigned zero displacement to represent a complete restraint. This is crucial in defining how the model reacts under load.
On the other hand, natural boundary conditions, which typically involve forces or tractions, allow the scientist to define how surfaces interact with the surrounding environment. For example, applying a pressure load to a surface is modeled through natural boundary conditions. These two categories work together to provide a comprehensive understanding of how structures will behave under various load scenarios.
Load Types and Applications
Point Loads
Point loads represent a concentrated force acting on a specific location. This aspect is fundamental because point loads simplify the analysis of complex structures by allowing focus on singular forces. The key characteristic of point loads is their localization; they act over infinitesimally small areas. This makes them a beneficial choice when modeling situations like a load being applied by a weight at a specific position.
However, one unique feature of point loads is the potential for stress concentration at the application point. While they offer simplicity in modeling, this can lead to inaccuracies if not approached with caution. Thus, understanding the balance between ease of calculation and potential pitfalls is crucial for accurate finite element stress analysis.
Distributed Loads
In contrast, distributed loads spread force over an area, providing a more realistic representation of how forces affect structures. This is particularly relevant in cases like loads from water or snow, which accumulate over surfaces rather than impacting at a single point. The key characteristic of distributed loads is their continuum nature, which reflects real-life conditions more closely than point loads.
The unique feature of distributed loads is their ability to reduce stress variations throughout the structure. This advantage outweighs the complexity involved in their calculations. When used properly, they can provide a more accurate assessment of how structures will perform under load. However, incorrect application can lead to operational issues. It is important to assess the loading conditions carefully and select the appropriate load type that reflects the intended scenario.
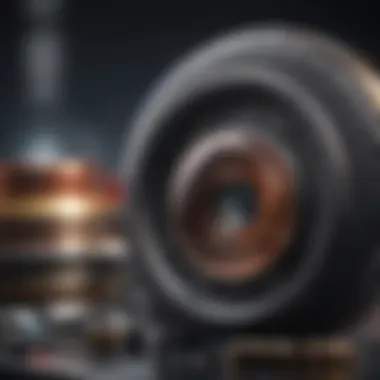

In finite element stress analysis, understanding boundary conditions and load applications is key to developing realistic and accurate models.
The nuanced selection and implementation of these elements are what differentiate effective analysis from inadequate evaluations. By comprehending how essential and natural boundary conditions interact with point and distributed loads, engineers can produce models that not only adhere to theoretical principles but also represent practical realities.
Numerical Methods in FESA
Numerical methods play a crucial role in Finite Element Stress Analysis (FESA). These techniques allow engineers and researchers to solve complex problems that cannot be approached through analytical methods. In practice, numerical methods provide the tools necessary to model and analyze physical structures under various loading conditions. They enable the evaluation of stress distributions, which is vital for structural integrity and safety assessments.
The significance of numerical methods is underscored by their ability to handle non-linear behavior, multiple materials, and various boundary conditions. Understanding these methods is key to making informed decisions in engineering design and analysis.
Finite Element Method (FEM)
The Finite Element Method is perhaps the most widely recognized numerical method in FESA. At its core, FEM involves dividing a complex structure into smaller, manageable parts known as finite elements. This discretization process simplifies the math involved, allowing users to apply equations that govern mechanical behavior.
One key aspect of FEM is its flexibility. It can accommodate various geometries and material properties, making it suitable for a vast array of engineering problems. The method is especially useful in static and dynamic simulations, highlighting its versatility in different scenarios. Additionally, its iterative nature allows for progressive refinement of solutions, improving accuracy over successive runs.
Other Numerical Techniques
While FEM is the standard, there are several other numerical techniques utilized in conjunction with or as alternatives to it. Two prominent methods are the Boundary Element Method and Meshless Methods.
Boundary Element Method
The Boundary Element Method (BEM) focuses on the boundaries of a structure instead of its entire volume. This characteristic is significant because it reduces the dimensionality of the problem. By transforming volume integrals into surface integrals, it simplifies certain complex analyses, particularly in problems dealing with potential fields, like heat conduction or fluid flow.
BEM is often considered beneficial because it requires less computational resources compared to volume-based methods like FEM. This efficiency makes it particularly popular in engineering applications with large domains or infinite geometries. However, it has its drawbacks, such as difficulties in dealing with non-linear problems and requiring the formulation of boundary integral equations.
Meshless Methods
Meshless Methods represent an innovative approach that eliminates the need for mesh generation altogether. By utilizing point clouds or other distributions of free points, these methods provide greater flexibility when modeling complex geometries or dynamic situations.
The main advantage of Meshless Methods is their intrinsic ability to handle large deformations and fluid-structure interaction problems. They adapt smoothly to changes in the geometry without the need for re-meshing, which can be time-consuming and error-prone. However, the complexity of implementation and the requirement for robust algorithms can pose challenges for practitioners.
"Numerical methods illuminate pathways through the intricacies of Finite Element Stress Analysis, revealing the hidden stresses and behaviors of materials under load."
This exploration of numerical methods in FESA, especially FEM, BEM, and Meshless Methods, reflects the diverse approaches available to engineers. Each method carries its unique characteristics, advantages, and challenges. Understanding these nuances helps practitioners choose the most appropriate technique for their specific applications, ultimately leading to better designs and safer structures.
Software Tools for Finite Element Stress Analysis
Software for finite element stress analysis plays a vital role in engineering design and assessment. These tools enable engineers to simulate the physical behavior of structures and materials under various loading conditions. Using software tools can significantly enhance the accuracy and efficiency of stress analysis, saving time and cost during the design process. Understanding the options available helps practitioners choose the right tool for their specific needs. This part will cover both commercial and open-source software tools relevant to finite element stress analysis.
Commercial Software Overview
ANSYS
ANSYS is a leading software used extensively for finite element stress analysis. One specific aspect of ANSYS is its ability to model complex physical phenomena, including nonlinear material behavior and dynamic loads. The key characteristic of ANSYS is its user-friendly interface, making it accessible for both beginners and seasoned professionals.
Moreover, ANSYS provides robust simulation capabilities, allowing for high-quality results in structural analysis. A unique feature of ANSYS is its integration with various modules like ANSYS Mechanical and ANSYS Fluent. This integration allows engineers to perform multiphysics simulations, which combine structural and fluid analysis. However, the comprehensive nature of ANSYS comes with a steep learning curve and significant cost, which can be a barrier for some users.
Abaqus
Abaqus is another powerful tool in the realm of finite element stress analysis. A notable aspect of Abaqus is its advanced capabilities for simulating complex nonlinear behavior in materials. The primary characteristic of Abaqus is its focus on advanced materials, which makes it suitable for applications in fields like automotive and aerospace engineering. Its ability to perform cohesive zone modeling is particularly advantageous when analyzing the toughened interfaces of advanced composite materials.
Abaqus also features a strong solver for handling large deformation as well as dynamic loading scenarios. Despite its advantages, the software can be resource-intensive in terms of computational power, necessitating a robust computing environment. Additionally, the licensing costs for Abaqus can be high, making it less accessible for smaller organizations.
Open Source Alternatives
While commercial software provides excellent features, open-source alternatives can be a good option for many users. These tools often come with lower costs and flexibility.
OpenFOAM
OpenFOAM is an open-source software primarily used for computational fluid dynamics but also includes capabilities for finite element stress analysis. One important aspect of OpenFOAM is its versatility in defining custom solvers and simulations. The key characteristic of OpenFOAM is that it provides a complete environment for fluid flow and solid mechanics simulations. It is widely recognized for its adaptability, allowing users to customize features according to their requirements.
A unique feature of OpenFOAM is its public availability, enabling collaboration among users and developers. This can be advantageous for smaller institutions or those without extensive budgets. However, the lack of graphical user interfaces compared to commercial products may deter some users.
CalculiX
CalculiX is another significant open-source option specifically tailored for finite element analysis. It allows users to carry out linear and nonlinear analyses of solids. One of the main advantages of CalculiX is its ease of use and efficiency, particularly for structural problems. Its key characteristic is the availability of a graphical pre- and post-processor called cgx, which enhances user experience.
CalculiX's unique ability is to run efficiently on standard computational hardware, making it accessible to many engineers. However, it does lack the extensive documentation and community support that larger platforms offer, which could hinder the learning curve for some.
Validation and Verification in Finite Element Analysis
Finite Element Stress Analysis (FESA) relies heavily on validation and verification. Both processes are integral to ensuring that FESA results are credible and reliable. Validation checks whether the model accurately represents the real-world physical behavior that it aims to simulate. Verification, on the other hand, assesses whether the computational processes and numerical methods employed in the analysis are correctly implemented. This distinction is pivotal in fostering trust in simulation results.
The importance of validation and verification can be seen in many ways. First, they provide assurance that simulations yield meaningful results which can guide critical engineering decisions. In high-stakes fields like aerospace and construction, even minor inaccuracies can lead to significant failures or safety hazards.
Factors to consider include the following:
- Confidence in predictions made using FESA
- Enhanced safety and reliability of designs
- Reduction in costs associated with experimental testing
- Improved performance during the design process
Ultimately, thorough validation and verification processes serve to bolster the integrity of the results and promote a dependable engineering practice.
Importance of Validation
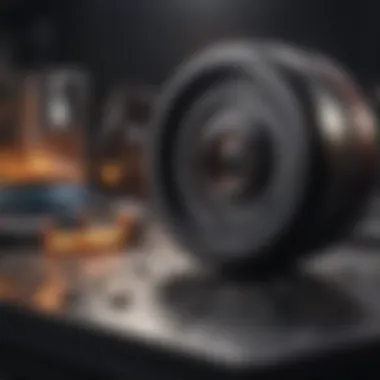

Validation represents a cornerstone of credible finite element analysis. By comparing the simulation results with experimental or real-world data, engineers can ascertain whether the chosen models and assumptions align with reality. This step is critical for multiple reasons.
- Confidence in Results: A validated model inspires confidence in stakeholders. It assures them that the predictions made regarding stress conditions in structures are accurate.
- Quality Assurance: Validation acts as a form of quality control. It verifies that the methodologies employed function appropriately under the specified conditions.
- Reduction of Errors: By identifying discrepancies between model predictions and actual behavior, errors can be flagged and corrected prior to real-world implementation.
Without these validation processes, engineering designs may rest on assumptions that are fundamentally flawed, which could lead to catastrophic failures. Therefore, engaging in thorough validation practices is not optional; it is an obligation to ensure public safety and structural integrity.
Techniques for Verification
Verification, while distinct from validation, is equally as critical in finite element analysis. The primary objective of verification is to confirm that the computational methods yield the correct results as prescribed by the mathematical formulations. Several techniques can be employed to achieve this.
- Code Verification: Ensure that the numerical algorithms are implemented correctly. This can involve checking mathematical proofs against code to confirm that equations are solved accurately.
- Solution Verification: Utilize convergence studies. By refining the mesh and observing how the solution changes, one can determine if the solution is approaching a stable result. The standard practice involves:
- Benchmark Problems: Compare simulation results with established benchmark solutions that are widely accepted within the engineering community. This helps to highlight any discrepancies in the numerical approach.
- Assessing the effects of mesh refinement on stress results
- Confirming that results stabilize with increased mesh density
"In finite element analysis, verification is crucial for ensuring that numerical models perform faithfully to theoretical expectations."
Case Studies of Finite Element Stress Analysis
Case studies in Finite Element Stress Analysis (FESA) are vital for dissecting practical applications and demonstrating the effectiveness of the methodology in real-world scenarios. These case studies provide concrete examples of how FESA can aid engineers and designers in understanding complex stress behaviors in varied materials and structures. The insights gained through these analyses offer significant benefits, such as improving designs, minimizing risks, and enhancing overall safety. By examining specific cases, students and professionals alike can appreciate the nuances of the methodology while gaining practical knowledge applicable to their fields.
Structural Engineering Applications
In structural engineering, finite element stress analysis plays an integral role in evaluating the performance of various structures, such as bridges, buildings, and dams. One prominent case study involved the analysis of a steel bridge. FESA was utilized to determine potential stress concentrations during peak load conditions. The analysis helped identify areas requiring reinforcement and facilitated the optimization of material usage, thus saving costs and ensuring safety.
Another significant application is in the reassessment of existing buildings. As structures age, understanding stress distributions becomes crucial. Using finite element models allows engineers to simulate dynamic loading conditions, such as earthquakes or high winds. A noteworthy example includes the analysis of an aging hospital building. Engineers discovered unexpected stress points by simulating various scenarios. This led to critical updates in the structural integrity assessment and preventative maintenance planning.
Biomedical Engineering Applications
Finite Element Stress Analysis extends beyond traditional engineering realms and proves beneficial in biomedical applications. This field leverages FESA for analyzing the mechanical behavior of biological tissues and implants. For instance, one illuminating case study focused on the development of a new knee implant. Engineers performed FESA to evaluate how the implant interacts with surrounding bone and cartilage under physiological loading conditions.
The results highlighted potential failure modes that might arise from improper design or material selection. Consequently, adjustments were made to the implant design, ensuring better integration with human anatomy and enhancing patient outcomes. This application underscores how FESA can reduce surgical risks and improve the longevity of medical devices, ultimately leading to better healthcare solutions.
"Finite Element Stress Analysis provides a crucial link between theoretical modeling and practical applications across diverse engineering fields."
Common Challenges in Finite Element Stress Analysis
Finite Element Stress Analysis (FESA) is a powerful method, yet it is not without its challenges. Understanding these challenges is crucial for achieving accurate analyses and results. Various issues may arise during the FESA process, impacting the reliability of the analysis. Addressing these challenges not only enhances the quality of the results but also leads to safer and more efficient engineering designs.
Mesh Sensitivity Issues
Mesh sensitivity is a fundamental challenge encountered in finite element stress analysis. The discretization process relies on dividing the physical domain into smaller elements, known as mesh. However, the quality of this mesh can significantly influence the accuracy of the results. An overly coarse mesh may overlook critical stress concentrations or provide inaccurate predictions of behavior under loads. Conversely, a mesh that is too fine can lead to unnecessary computational complexity and longer processing times without substantial improvements in accuracy.
Several aspects need to be considered when dealing with mesh sensitivity:
- Element Type: Different element types—such as tetrahedral or hexahedral elements—can result in different stress distributions. Choosing the right type is important.
- Mesh Density: Adjusting mesh density in areas of high stress concentration—like notches or holes—is vital. This often requires a refined mesh in critical regions while maintaining coarser elements elsewhere.
- Convergence Testing: Ensuring that the solution converges as the mesh is refined is critical. This confirms that the analysis is accurate and not an artifact of the mesh size.
By focusing on these factors, engineers can enhance the accuracy of FESA, leading to better predictive outcomes in structural performance.
Nonlinear Material Behavior
The nonlinear behavior of materials presents another significant challenge in finite element stress analysis. Many materials do not follow linear elastic behavior, especially under high-stress conditions. Instead, they may exhibit plastic deformation, viscoelasticity, or time-dependent properties. Ignoring these behaviors can lead to misleading conclusions about material performance.
When dealing with nonlinear materials, considerations include:
- Material Models: Selecting the appropriate constitutive model is essential. Models can range from simple bilinear stress-strain curves to complex models accounting for temperature and rate effects.
- Load Application: Understanding how loads are applied and the sequence of loading can influence the material response significantly.
- Computational Demand: Nonlinear analyses often require more computational resources and time. This necessitates a balance between detail and efficiency.
Failure to accurately account for nonlinear behavior can result in unsafe designs and unexpected failures. Thus, a thorough grasp of material characteristics is essential for reliable FESA outcomes.
Proper understanding of challenges like mesh sensitivity and nonlinear behavior in FESA is crucial for successful outcomes in engineering design.
Future Trends in Finite Element Analysis
The field of finite element stress analysis is continually evolving. As technology progresses, so do the methodologies and tools available to engineers. Understanding the future trends in this domain is crucial for professionals and students alike. These trends not only signify advancements in analysis capabilities, but they also enhance overall design and safety assessments in various applications.
Integration with Machine Learning
Machine learning is poised to revolutionize finite element stress analysis. By incorporating algorithms that can learn from data, analysts can improve model predictions significantly. This integration allows for:
- Predictive Modeling: Machine learning can predict stress responses based on historical data, making it easier to assess various conditions without extensive recalibration of the models.
- Material Behavior Analysis: With large datasets on material properties, machine learning can uncover hidden patterns in material behavior under different stresses, aiding in the selection of appropriate materials in designs.
- Optimization Techniques: Machine learning algorithms can assist in optimizing designs by searching through vast design spaces faster than traditional methods.
These advancements result in reduced computational times and increased accuracy, offering engineers new tools to tackle complex problems.
Advancements in Computational Power
The rapid advancement in computational power has a significant impact on finite element analysis. With improvements in hardware capabilities, practitioners can handle more complex simulations. The benefits of these advancements are evident in several areas:
- High-Performance Computing: Parallel processing and multicore systems enable the analysis of larger models that include intricate details. This leads to better capturing of stress distributions across structures.
- Real-time Analysis: The ability to perform simulations in real time allows engineers to make swift decisions during the design process. This real-time feedback can be crucial in time-sensitive projects.
- Cloud Computing: Utilizing cloud platforms for computation provides scalable resources, which means that teams can access extensive computational power without significant investments in physical infrastructure.
Finale
In the realm of engineering, understanding finite element stress analysis (FESA) is vital. This section summarizes the key takeaways from the preceding discussions and highlights why FESA is crucial in design and evaluation processes.
Recap of Key Concepts
Finite element stress analysis involves breaking down complex materials into smaller, manageable parts. This division simplifies the calculations required to evaluate stress and strain. Through the exploration of different models, boundary conditions, and software tools, we addressed how these elements contribute to accurate assessments. The importance of validation and verification was emphasized, ensuring that results align with real-world behavior.
Final Thoughts on FESA
FESA stands as a cornerstone in modern engineering practices. As industries evolve, the integration of new technologies like machine learning is anticipated to enhance the capabilities of FESA. Furthermore, awareness of challenges such as mesh sensitivity and nonlinear material behavior remains critical for practitioners. By grasping the multifaceted aspects of finite element stress analysis, students and professionals can significantly improve their approach to engineering designs, ensuring safety and efficiency in their projects.