FEP vs PTFE: Key Differences and Uses Explored
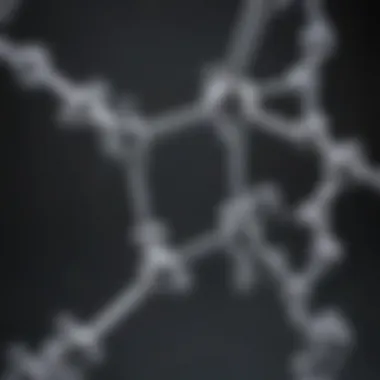
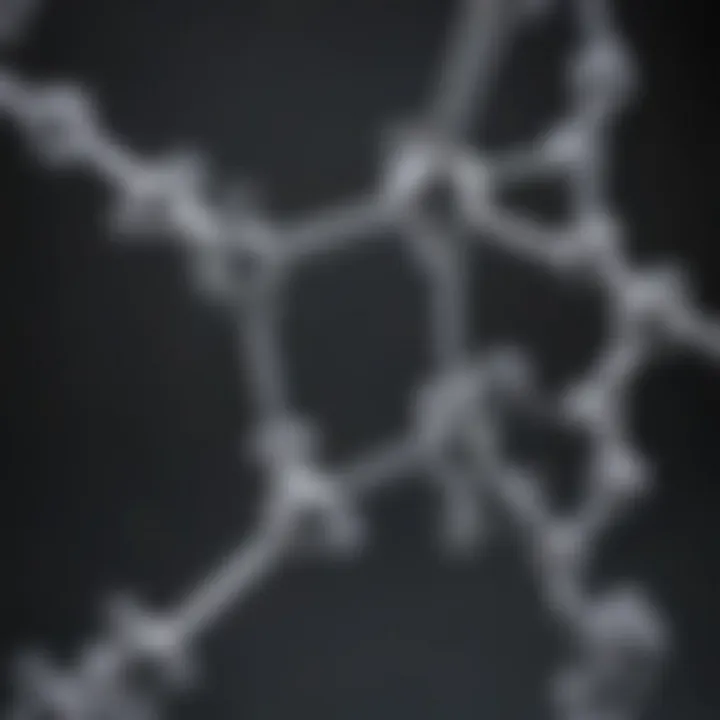
Intro
In the realm of industrial applications, understanding the materials we work with is crucial. When it comes to fluoropolymers, two names frequently pop up in discussions: Fluorinated Ethylene Propylene (FEP) and Polytetrafluoroethylene (PTFE). Both serve vital roles across different sectors, yet they possess distinct characteristics that can significantly influence decision-making processes in their applications.
FEP and PTFE share some core attributes, being made from fluorinated ethylene, a component known for its superior chemical resistance. However, the differences between them become evident when one dives deeper into their unique properties, applications, and cost-effectiveness. This narrative is designed not just to skim the surface but to dig deeper into these materials, laying out the fundamental differences that can help researchers, students, and professionals alike make informed choices based on specific needs.
As we journey through this analysis, we will uncover the chemical structures that set these two materials apart, explore their respective strengths and weaknesses, and highlight scenarios where one may dramatically outperform the other. By the end of this exploration, readers will gain invaluable insights into the nuances of FEP and PTFE, enhancing their understanding and application of these crucial materials.
Preamble to Fluoropolymers
Fluoropolymers are a unique class of polymers distinguished primarily by the presence of fluorine atoms in their structure. This characteristic sets them apart and endows them with remarkable properties impossible to achieve in many other plastics. Understanding these fluoropolymers, especially Fluorinated Ethylene Propylene (FEP) and Polytetrafluoroethylene (PTFE), is crucial as they play pivotal roles across diverse applications, from aerospace to electronics. Their chemical structure dictates how they behave under various conditions, directly affecting their suitability for specific tasks.
Definition and Characteristics
Fluoropolymers are synthetic polymers that have a backbone of carbon atoms, but crucially, they also contain fluorine. This inclusion greatly enhances their inertness, heat resistance, and ability to withstand extreme environments.
- Chemical Structure: Here, the most common types are fluorinated versions of ethylene and propylene, contributing to the unique molecular structure. These structures often exhibit high tensile strength and superior thermal stability, making them unmatched in certain scenarios.
- Properties:
Their properties include excellent chemical resistance, electrical insulation, and a low friction coefficient, which can be likened to having a protective shield against corrosive substances.
- Low Friction: Ideal for applications needing minimal resistance, like in piping systems.
- Thermal Stability: Functional at high temperatures where others fail.
- Chemical Resistance: Resistant to solvents, acids, and bases, making them a staple in hazardous environments.
Importance in Modern Industry
The significance of fluoropolymers in today’s industries cannot be overstated. Their durability and effectiveness allow for the advancement of technology in ways not previously thought possible.
- Aerospace:
Here, the demand for lightweight, heat-resistant materials is catapulting fluoropolymers into prominence, where they are used for coatings and insulation. - Electronics:
In electronics, these compounds are key for insulating wires and protecting components from harsh environments, ensuring longevity and reliability. - Medical Applications:
In the med field, fluoropolymers are utilized for various devices and tubes, thanks to their reliability and corrosion resistance.
"Fluoropolymers stand at the cutting edge of material science, providing solutions that are critical for safety, efficiency, and performance across multiple industries."
In sum, the introduction of fluoropolymers into industrial applications has made significant impacts owing to their unique properties. As industries evolve, having a thorough grasp of these materials is essential for innovation and efficiency.
Overview of FEP
Fluorinated Ethylene Propylene, commonly known as FEP, holds a pivotal role in the realm of fluoropolymers, particularly in applications where specific physical and chemical characteristics are paramount. This section provides an in-depth exploration of FEP, shedding light on its unique chemical composition, physical properties, and thermal stability. Understanding these facets is essential for professionals seeking to leverage the benefits of FEP in their respective fields.
Chemical Composition
FEP is a copolymer, primarily comprising two monomers: tetravinylidene fluoride (TVF) and hexafluoropropylene (HFP). The combination of these chemical compounds gives FEP its distinct molecular structure that makes it different from other fluoropolymers. One defining feature is the incorporation of both vinyl and propylene units, facilitating a versatile interaction with various environments.
This molecular configuration not only enhances its chemical resilience but also contributes to properties like low surface energy—rendering it hydrophobic and making it resistant to a plethora of chemicals, solvents, and cleaning agents. This versatility in wetting and resistance is significant for industries where contamination and material degradation pose severe risks.
Physical Properties
When it comes to physical characteristics, FEP stands out due to its transparency and low density, making it appealing in specific applications. The density of FEP is around 2.1 g/cm³, which is lighter than many comparable materials. This attribute helps in minimizing the overall weight of constructs in aerospace and automotive applications, proving beneficial where every gram counts.
Moreover, FEP exhibits excellent flexibility and impact resistance, even at low temperatures. This is vital for maintaining integrity in challenging environments, such as those faced in the medical field where reliability is paramount.
The material also boasts a high dielectric strength, making it an excellent electrical insulator, which is especially crucial for electronics and wiring applications.
Thermal Stability and Performance
FEP is renowned for possessing exceptional thermal stability, capable of withstanding temperatures extending up to 200 degrees Celsius (392 degrees Fahrenheit) without significant degradation. This resilience permits its application in environments where heat is a constant concern. The material maintains its mechanical properties across a wide temperature range, offering reliability in dynamic scenarios.
Besides temperature endurance, FEP operates effectively across a broad spectrum of chemical interactions, making it a go-to choice in sectors like chemical processing and aerospace. Its performance under oxidative and reductive conditions is commendable, ensuring longevity and durability in various applications.
FEP's ability to maintain mechanical integrity and chemical resistance at elevated temperatures underscores its value in stringent applications.
In summary, the overview of FEP highlights its unique properties derived from its chemical composition, which collectively allows it to serve critical functions across numerous industries. Understanding these elements prepares professionals to capitalize on FEP’s distinct advantages, ensuring appropriate choices are made in material applications.
Overview of PTFE
Understanding PTFE, or Polytetrafluoroethylene, is critical for grasping its pivotal role in various industries. Known for its unique properties, PTFE is widely recognized in both industrial and consumer applications. With a focus on its chemical structure, physical characteristics, and high resistance to heat and wear, PTFE presents numerous benefits. It's not just a hype product; the way it interacts with different environments and materials offers real insights for engineers and purchasing managers alike.
Chemical Structure
PTFE is made up of a chain of carbon atoms, each one bonded to two fluorine atoms. This arrangement results in a polymer that exhibits remarkable chemical stability and inertness. The simplicity of its structure conceals a plethora of functionality. One might say that its simple design has a complex impact. Because of these strong carbon-fluorine bonds, PTFE has a negligible affinity for other materials which is significant when considering its chemical resistance.
The molecular weight of PTFE can vary significantly, leading to different physical manifestations of this polymer. Longer chains can increase its thickness, which can be beneficial in applications requiring more substantial insulation or wear properties.
Physical Characteristics
When it comes to physical characteristics, PTFE stands out for its low friction coefficient, making it an ideal candidate for bearings and seals. The surface energy is quite low, meaning it has very little stickiness. For example, very few adhesives can bond effectively to PTFE, making it an excellent choice in situations where materials must glide smoothly against one another.
Additionally, PTFE has a very high melting point, typically around 327 degrees Celsius, and it retains its structural integrity across a wide range of temperatures. This quality is a game-changer in applications ranging from cooking pans to aerospace components.
- Non-stick properties: PTFE is well-known for its use in non-stick cookware. This is where it shines and has garnered much of its fame.
- Lightweight: Even though PTFE stands up to heat and pressure, it doesn't weigh much, giving it an edge in sensitive applications.
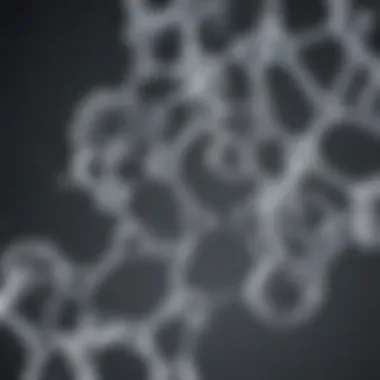
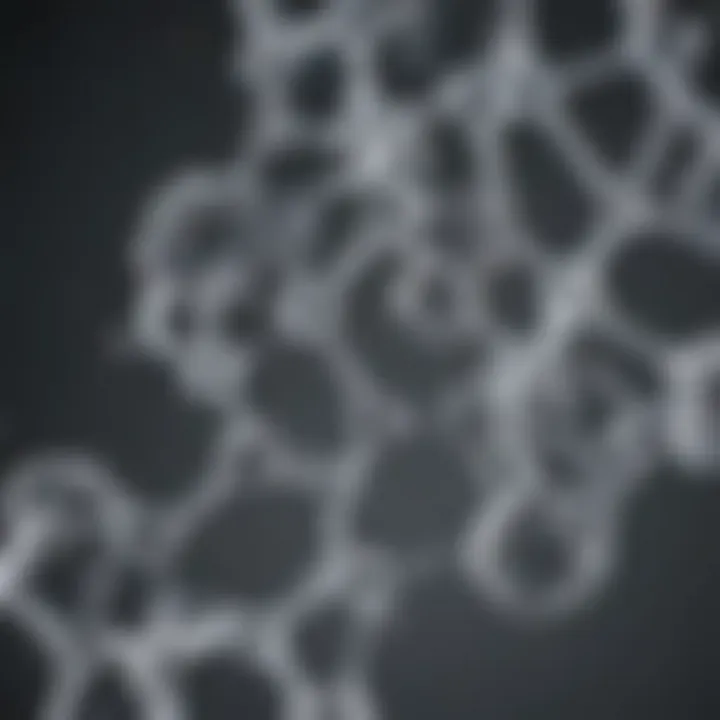
Durability and Temperature Resistance
Durability is one of PTFE’s hallmark qualities. It can withstand harsh chemicals and extreme temperatures without degrading. This makes it a staple in chemical processing industries where safety and reliability are non-negotiable requirements.
"In environments where other materials might crumble, PTFE remains steady, offering resilience that assures longevity and efficacy."
Notably, PTFE maintains its physical properties over a temperature range spanning from -200 degrees Celsius to +260 degrees Celsius. The temperature resistance of PTFE allows it to be utilized in various applications, whether it's in the demanding conditions of aerospace technology or the modest needs of home kitchens.
In summary, PTFE’s chemical structure, complemented by its unique physical characteristics and durability, makes it a material of choice across various sectors. Its seemingly simple design belies its multi-functionality and effectiveness, making it an invaluable component in both high-performance applications and everyday products.
Comparative Properties of FEP and PTFE
Understanding the specific properties of FEP and PTFE is crucial for those navigating industrial applications. Each fluoropolymer holds its own set of characteristics that makes it uniquely suitable for distinct environments. From chemical resistance to mechanical robustness and electrical insulation, examining these properties allows users to determine their best fit for various projects and needs. Making informed choices can lead to enhanced performance and significant cost savings in the long run.
Chemical Resistance
Both FEP and PTFE exhibit remarkable chemical resistance, which is one of their standout features. These polymers can withstand aggressive chemicals, including acids, bases, and solvents. However, there are nuances that set them apart.
- FEP is generally favored in environments where chemical exposure is a concern, thanks to its exceptional tolerance to corrosive agents. It can perform well under both high and low pH conditions.
- PTFE, on the other hand, offers even broader chemical resistance. It is often considered the gold standard for chemical resistance, capable of enduring even the harshest chemicals, including strong oxidizers.
This makes PTFE a common choice in chemical processing applications where maximum durability is required. The slight decrement in performance of FEP versus PTFE in this area can be attributed to its slightly different polymer structure, which may allow some reactive species to interact with the polymer chains.
"The best choice in chemical environments can mean the difference between a successful operation and catastrophic failure."
Mechanical Strength
When it comes to mechanical properties, both FEP and PTFE deliver impressive tensile strength, but their applications may differ based on the specific needs of a project.
- FEP tends to have a slight edge in flexibility, which allows it to be manufactured into films and heat shrink tubes. Its lower density compared to PTFE makes it easier to manipulate and shape without compromising strength.
- PTFE, though, excels in terms of overall strength and rigidity. It is ideal for applications requiring heavy-duty performance. The material can withstand greater forces and loads without deformation, which is critical in industrial machinery and equipment.
In practice, if you're working on applications that involve bending or shaping, FEP might be the more viable option. But when you’re after raw strength and durability, PTFE reigns supreme.
Electrical Insulation Properties
Electrically, both FEP and PTFE are impressive insulators, and choosing between the two boils down to specific application needs.
- FEP has excellent dielectric properties, making it favorable in cables and wire insulation. Its transparency offers added benefits for visualization during installation or inspection, an uncommon trait in the world of polymers.
- PTFE sets a high bar for electrical insulation. It maintains its insulating properties over a broader temperature range and is less prone to breakdown under extreme conditions. This makes it a go-to for applications in electronics and specialized electrical environments.
To sum up, while both materials serve well in electrical insulation, PTFE’s superior thermal performance gives it an edge in more challenging applications.
Applications of FEP
Fluorinated Ethylene Propylene (FEP) has carved a niche for itself in various industries, thanks to its unique properties. Understanding the importance of FEP applications is crucial, particularly in sectors where reliability and performance are paramount. Utilizing FEP means leveraging its excellent chemical resistance, flexibility, and thermal stability.
The applications are not just limited to a few areas; they spread across fields such as aerospace, electronics, and healthcare. Each field benefits differently but synergistically from FEP's traits, leading to innovations and improved functionalities. Here's a deeper look at some prominent sectors where FEP is applied.
In Aerospace and Automotive Industries
FEP plays a significant role in the aerospace and automotive sectors. The need for materials that can withstand harsh environments here cannot be overstated. FEP is favored for its lightweight and durability, making it ideal for aerospace insulation and protective coatings. In automotive, it finds its use in cable and wire insulation due to its high-temperature resistance and low friction properties, ensuring safety and efficiency.
- Key Considerations:
- Weight-to-strength ratio: Critical for flight safety and performance.
- Thermal management: Ensures equipment operates within safe temperature ranges.
FEP also allows for precision in application, reducing the likelihood of system failures, which can be catastrophic in aviation.
Electronics and Wiring
In the realm of electronics and wiring, FEP is hailed for its superb electrical insulation properties. It guarantees that the wires and circuits remain functional under extreme conditions. Products like FEP-coated wires are used extensively in high-frequency and high-voltage environments.
- Key Benefits:
- Low dielectric constant: Aids in signal integrity.
- Chemical resistance: Protects wiring systems from corrosive substances.
- Flexibility: Facilitates intricate designs where space is at a premium.
The seamless integration of FEP in these applications enhances the overall performance of electronic devices, providing durability and reliability that’s hard to match.
Medical Applications and Devices
When it comes to medical applications, FEP is indispensable. The healthcare sector demands materials that are not only reliable but also hygienic and safe. FEP is utilized in medical devices due to its resistance to harsh cleaning chemicals and ease of sterilization.
- Benefits in Medical Applications:
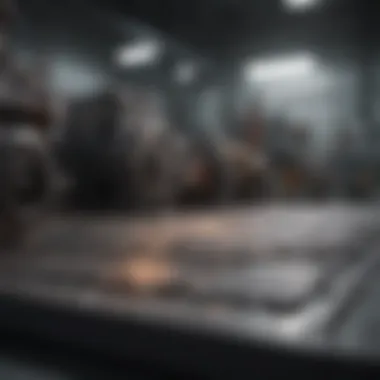
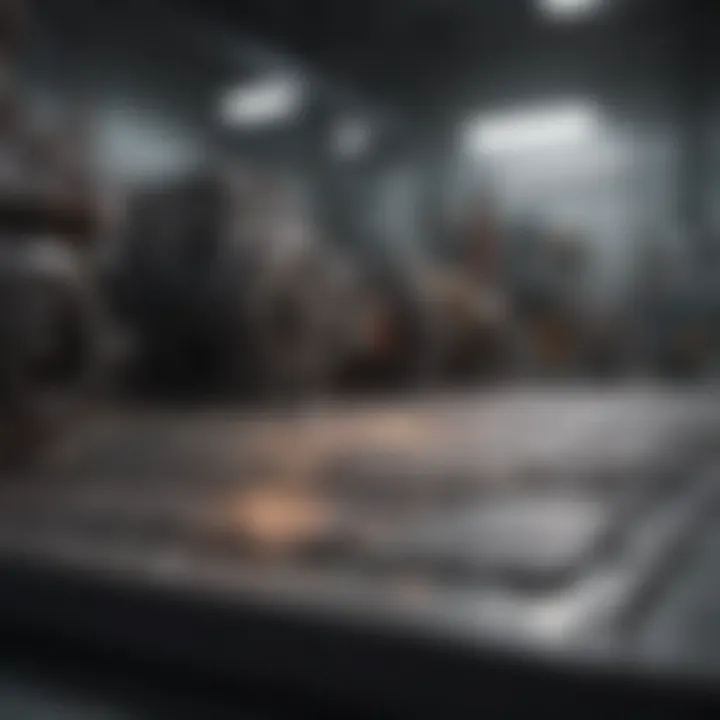
- Biocompatibility: Ensures safety for patient use.
- Transparency: Allows for easy monitoring during procedures.
- Temperature resistance: Essential for autoclaving.
From catheter tubing to surgical instruments, FEP's range of use has positively impacted the effectiveness of many medical functions. With innovations just around the corner, its future in healthcare seems promising.
Overall, FEP’s diverse applications across varied industries underscore its significance as a material of choice, reflecting its role in advancing technology and improving quality of life.
Applications of PTFE
PTFE, commonly known as Teflon, has positioned itself as a staple across a variety of industries thanks to its unique properties. Not only is it known for its non-stick nature, but it also exhibits excellent resistance to heat and chemicals, making it invaluable in diverse applications. This section explores the significance of PTFE applications, detailing its benefits and considerations, which underline its role in contemporary manufacturing and everyday use.
Culinary and Cookware Uses
One of the most familiar uses of PTFE is found in the kitchen. Equipped with non-stick frying pans and baking sheets, PTFE provides a surface that allows food to cook evenly without sticking, creating less hassle during meal preparation and cleanup. This property is not just about convenience; it promotes healthy cooking as well, requiring less oil or fat when frying or sautéing.
Benefits:
- Ease of cleaning: PTFE products are generally easy to wipe down, which saves not just time but also ensures a more hygienic cooking environment.
- Durability: Many PTFE-coated cookware items can withstand high temperatures, maintaining their integrity over time if properly cared for.
However, it’s crucial to be mindful of the temperatures at which PTFE can safely be used. Overheating it can release fumes that may be harmful if inhaled. Therefore, using these products according to manufacturer guidelines is a must.
Important Note: A simple rule of thumb is to avoid cooking with PTFE pans at temperatures above 500°F (260°C) to prevent the risk of damaging the coating.
Industrial Equipment and Seals
PTFE's characteristics extend far beyond the culinary realm. In industrial settings, its application shines in gaskets, seals, and various components that require robust materials. PTFE’s chemical resistance allows it to be used in harsh environments, from chemical plants to oil refineries.
Key Considerations:
- Temperature resilience: It retains its form and function even under extreme heat, making it ideal for high-temperature applications.
- Extensive chemical compatibility: Unlike many materials, PTFE doesn't react with most chemicals, allowing it to function in environments where other seals might fail.
This reliability ensures that equipment can operate at optimal levels without frequent replacements or downtime, enhancing productivity.
Chemical Processing Applications
The chemical processing industry demands materials that can withstand aggressive chemicals without degrading. PTFE fits the bill perfectly, making it a popular choice for pipes, valves, and reaction vessels. Its ability to resist corrosive substances protects both the materials and the operators involved in such processes.
Advantages:
- Longevity: With minimal reactivity, PTFE components can last a long time, requiring less frequent maintenance or replacement.
- Safety: Given its non-reactive nature, PTFE reduces risks associated with chemical handling, providing a safer working environment.
Moreover, in fluid handling systems where precision is essential, PTFE's low friction properties also enable smooth flow, reducing energy costs and enhancing system efficiency.
Advantages of FEP over PTFE
When comparing the two fluoropolymers, FEP and PTFE, understanding their distinct advantages can be crucial for varying applications. FEP, or Fluorinated Ethylene Propylene, has carved its niche in industries that value ease of processing and certain aesthetic features. This flexibility is particularly valuable when industries grapple with the demand for efficiency and cost-effectiveness. Here, we will explore two primary advantages of FEP over PTFE, namely its processing ease and appealing transparency.
Processing Ease
One of the standout features of FEP is its processing ease, which makes it a favored choice in many manufacturing environments. Unlike PTFE, which requires specialized equipment and processes due to its high viscosity and melting point, FEP can be processed with standard thermoplastic techniques. This facilitates its use in injection molding and extrusion, making it relatively simple to integrate into existing manufacturing lines.
The ability to mold FEP into complex shapes without the need for excessive energy or advanced machinery can drastically lower production costs. This ease of use translates into quicker turnaround times for manufacturers, allowing them to respond to market demands more swiftly. When time is money, as it often is in production environments, this becomes a significant advantage.
Moreover, FEP can be handled at lower temperatures compared to PTFE. This thermal adaptability reduces the risk of damaging materials during processing. As a result, it opens the door for innovative products that leverage FEP's unique properties while maintaining high production efficiency.
Transparency and Aesthetics
Moreover, FEP has an edge in terms of its transparency and aesthetics. This fluoropolymer typically exhibits a clear, glass-like appearance that many industries find beneficial, especially in applications where visual appeal matters. For instance, it's often used in scenarios where seeing the content is necessary, such as in certain tubing applications. Whether it’s for consumer products or medical devices, having materials that are not only functional but also visually appealing can sway the choice towards FEP.
In the world of product design, aesthetics can play a pivotal role in attracting customers. Products that utilize FEP can also be more easily color-coded, allowing for better identification and application differentiation. This visual distinction can be vital in industries like pharmaceuticals or food processing, where product integrity and safety are paramount.
"The remarkable clarity of FEP not only enhances product visibility but also contributes significantly to brand perception in competitive markets." - source
In summary, FEP’s advantages over PTFE—in terms of processing ease and aesthetic properties—provide significant benefits for industries looking to innovate while keeping production streamlined. Understanding these differences can greatly assist professionals in making informed decisions regarding materials for specific applications.
Advantages of PTFE over FEP
When evaluating fluoropolymers, many professionals focus on finding the right material for specific applications. Polytetrafluoroethylene (PTFE) has distinct advantages over Fluorinated Ethylene Propylene (FEP) that can be crucial for industrial settings. PTFE's unique properties make it an asset in various fields, and understanding these benefits can help guide decisions in material selection.
Higher Temperature Resistance
One significant advantage of PTFE is its ability to withstand higher temperatures compared to FEP. PTFE maintains its integrity at temperatures reaching up to 260°C (500°F), while FEP generally caps out around 205°C (401°F). This characteristic is particularly advantageous in environments where thermal stability is non-negotiable.
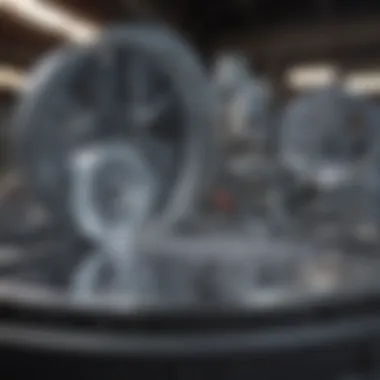

For applications involving high-heat processes—like those found in the manufacturing of chemical reactors or oil and gas exploration—this property can mean the difference between a reliable product and one that fails under stress. Users often find that PTFE's robustness in such scenarios provides peace of mind and reduces maintenance needs significantly.
Superior Chemical Resistance
In addition to its thermal advantages, PTFE also boast significantly higher chemical resistance than FEP. This quality allows PTFE to thrive in environments filled with corrosive substances. For industries dealing with strong acids, bases, or organic solvents, the choice of material can have serious implications.
A prime example can be seen in the chemical processing sector, where equipment requires a lining that does not react adversely with the substances being handled. PTFE’s ability to resist degradation when in contact with chemicals is an essential factor that many engineers consider essential when designing systems.
"Choosing the right polymer can dictate both the safety and efficiency of chemical processes. With PTFE's superior chemical resistance, users approach these challenges with greater confidence."
To summarize, both the superior temperature resistance and chemical robustness of PTFE lend immense practical value across diverse applications. As we further navigate the realm of fluoropolymers, it becomes clear that while FEP has its strengths, PTFE stands out in crucial areas, asserting itself as a preferred choice in many high-stakes environments.
Limitations and Challenges
In examining the landscape of Fluorinated Ethylene Propylene (FEP) and Polytetrafluoroethylene (PTFE), it is crucial to surface the limitations and challenges these materials pose. While they both boast impressive features, the practicalities surrounding their usage can at times burgeon with complications. Understanding these nuances aids stakeholders—be it in research, production, or application—navigate the intricate realities of working with these fluoropolymers.
Cost Considerations
When it comes to budgeting for FEP and PTFE, the variations can be pretty stark. FEP tends to command a more wallet-friendly price point compared to PTFE. The reasons for this discrepancy often boil down to the manufacturing processes. FEP typically involves less intensive processing and has a higher yield during production, making it more economical for many businesses.
On the flip side, PTFE is often considered the gold standard when it comes to chemical resistance and high-temperature performance. As a result, its costs can escalate rapidly. Companies might find themselves paying extra not just for the product itself but also for specialized equipment required to manipulate it, since PTFE’s properties often require more stringent handling and processing protocols. Here are some key takeaways regarding cost considerations:
- Initial Investment: FEP generally has lower upfront costs.
- Processing Costs: PTFE may require more sophisticated tools, leading to higher processing outlays.
- Long-Term Value: While PTFE can be more expensive, its durability may justify the investment in applications where reliability is non-negotiable.
Understanding these cost dynamics is essential for decision-making, especially when projects demand specific performance characteristics under various environmental conditions.
Environmental Impact
Both FEP and PTFE carry aspects of environmental impact that merit attention, thanks to their widespread industrial use. As global awareness about sustainability rises, the implications of utilizing these materials in various applications cannot be ignored.
FEP is often perceived as having a relatively lower environmental footprint compared to PTFE, primarily due to its processing methods. The production of FEP tends to emit fewer harmful byproducts, an aspect that's increasingly valuable in today's eco-conscious marketplace. Despite this, some concerns exist surrounding the disposal and degradation of fluoropolymers in general, since they do not biodegrade easily.
Conversely, PTFE has come under scrutiny for its environmental implications. During its production and incineration, harmful substances can be released into the environment. The production process of PTFE may involve perfluorooctanoic acid (PFOA), a substance linked to various health concerns. Here are the notable environmental impacts:
- Durability vs. Degradability: Both materials are durable, but that durability results in significant waste management challenges.
- Manufacturing Concerns: The methods for creating these materials sometimes entail substances that are harmful to the environment.
- Regulatory Challenges: Pending regulations may further impact the production practices related to fluoropolymers.
Future Trends in Fluoropolymer Use
The landscape for fluoropolymers is continually evolving, and understanding the future trends is crucial for industries relying on FEP and PTFE. As we navigate through an age defined by innovation and environmental scrutiny, the demand for materials like FEP and PTFE will see significant shifts. These shifts are not just about performance but also about adaptability to new challenges, including regulatory changes and market dynamics.
Innovations in Material Science
Material science is the bedrock of advancements in fluoropolymer technologies. Researchers are constantly on the lookout for ways to improve the properties of FEP and PTFE. A noteworthy trend is the development of hybrid materials that blend the superior qualities of both polymers. For instance, incorporating fillers or modifying the surface characteristics could enhance thermal and mechanical strengths. This approach enables applications in extreme conditions, pushing the boundaries of where these materials can be utilized.
Moreover, breakthroughs in nano-materials have caught the attention of manufacturers. Using nanotechnology, there's potential for creating more robust coatings, improving friction properties, and even enhancing the barrier qualities of fluoropolymers. These advancements could make FEP and PTFE even more appealing in sectors like aerospace, where weight and performance are critical.
Sustainability Considerations
As industries face increasing pressure to adopt sustainable practices, fluoropolymers are also undergoing scrutiny. While FEP and PTFE are known for their durability, their environmental impacts, particularly at the end of their lifecycle, are raising eyebrows. The future will undoubtedly see a push towards developing bio-based alternatives or enhancing the recyclability of traditional fluoropolymers.
Key considerations include:
- Recycling Techniques: New methods aimed at reclaiming fluoropolymers after their use could drive the future of the industry.
- Reduction of Environmental Footprint: Efforts are being made to reduce greenhouse gas emissions during production and improve the overall lifecycle management of FEP and PTFE products.
- Biodegradable Options: Research is ongoing to formulate biodegradable fluoropolymers without compromising on performance.
Understanding these trends is vital for industries as they adapt and innovate. The blend of science with sustainability will likely dictate the direction of fluoropolymer utilization.
In summary, the future of fluoropolymer use hinges on innovative advancements in material science and a committed approach towards sustainability. By keeping an eye on these trends, professionals can better navigate the challenges and opportunities that lie ahead, ensuring their applications remain relevant and effective.
The End
In this article, we have thoroughly explored the characteristics, applications, and comparative advantages of Fluorinated Ethylene Propylene (FEP) and Polytetrafluoroethylene (PTFE). The significance of these materials cannot be overstated, as they play critical roles across various industries. Understanding their unique properties is paramount for professionals tasked with selecting the appropriate fluoropolymer for specific applications.
Summary of Key Points
- Chemical Structures: Both FEP and PTFE are fluoropolymers, but their chemical makeup leads to distinct properties.
- Applications: FEP is favored in aerospace and medical devices, while PTFE shines in culinary and industrial applications.
- Advantages: FEP offers advantages like ease of processing and aesthetic transparency. In contrast, PTFE excels in temperature resistance and chemical resilience.
- Limitations: Cost and environmental concerns present challenges for both FEP and PTFE.
- Future Trends: Ongoing innovations and sustainability efforts may reshape how these materials are used in the future.
In synthesizing this information, a clear understanding emerges regarding the roles these materials play and how they are applied in real-world scenarios.
Implications for Industry
The implications of this comparative analysis stretch far and wide across industries. For instance, manufacturers in sectors such as aerospace and electronics must consider the properties of both FEP and PTFE to optimize both function and safety. FEP may be the material of choice for lightweight, transparent applications, while PTFE’s unrivaled thermal stability offers peace of mind in high-stakes, temperature-critical environments.
Furthermore, the insights gained from understanding the limitations of each material can guide decision-making. Companies can strategize on material utilization, aligning their goals with sustainability practices by choosing appropriate fluoropolymers based on their operational needs.
Practitioners in the field should always weigh performance, cost, and environmental impact as part of their material selection process. Being knowledgeable about these nuances not only aids in efficient project execution but also supports long-term sustainability objectives in manufacturing and production.
Through a comprehensive approach to analyzing FEP and PTFE, professionals can make better-informed decisions, ultimately enhancing product outcomes and contributing to a more efficient industrial landscape.