An In-Depth Exploration of Tungsten Carbide Ball Mills
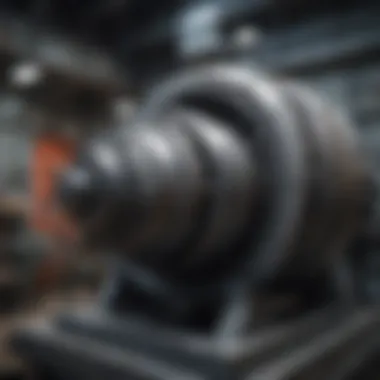
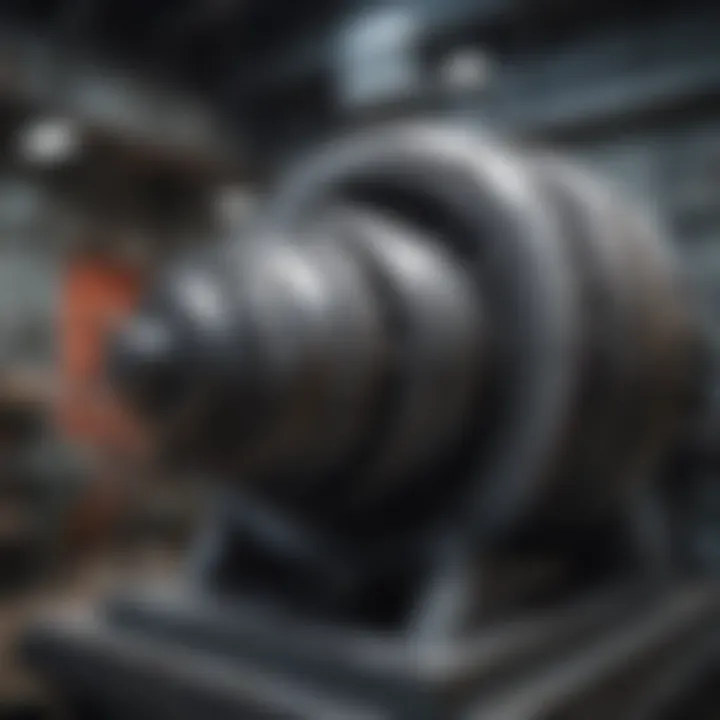
Intro
In the domain of material processing, tungsten carbide ball mills stand out for their durability and efficiency. This article aims to dissect the essential characteristics of these mills, exploring their construction, functionality, and the various sectors where they find application. The effectiveness of tungsten carbide in milling processes arises from its unique material properties, offering solutions to a range of industrial challenges.
Key Findings
Major Results
Research indicates that tungsten carbide ball mills provide superior wear resistance compared to traditional materials. Their robust nature allows for extended periods of operation without significant degradation. Additionally, the grinding efficiency of tungsten carbide is noteworthy, leading to finer particle sizes and improved product quality.
Discussion of Findings
The findings suggest that the material properties of tungsten carbide greatly influence the performance of ball mills. Its high hardness and strength contribute to the overall effectiveness in grinding minerals, metals, and other materials. Furthermore, the ability to maintain precision in particle size and consistency has significant implications for industries such as mining, metallurgy, and ceramics.
Operating Principles
Understanding the operational principles of tungsten carbide ball mills is crucial for proper utilization. These mills operate on the principle of impact and attrition, utilizing heavy balls to crush and grind materials. The design allows for efficient loading and unloading, optimizing productivity.
Applications Across Industries
Tungsten carbide ball mills have found significant applications in various sectors, including:
- Mining: For grinding ores and minerals.
- Manufacturing: In the production of advanced materials.
- Ceramics: For achieving fine particle sizes in ceramic compositions.
- Pharmaceuticals: Where precision in particle sizes is critical.
Maintenance Considerations
Maintenance of tungsten carbide ball mills involves regular checks and timely replacement of worn parts. Factors to consider include:
- Grinding media integrity.
- Inspection of the mill lining for wear.
- Regular lubrication of moving parts.
Recent Advancements
The field of milling technology has seen advancements like automation and improved control systems. These innovations aim to enhance efficiency and monitor performance in real-time.
Future Trends
Future developments may focus on incorporating smart technology, potentially leading to more efficient and user-friendly milling processes. Research into alternative materials may also expand the applications of ball mills, providing more options to industries.
The significance of tungsten carbide ball mills in modern industry cannot be understated; as technology progresses, their role is likely to expand further.
The in-depth exploration of tungsten carbide ball mills presented in this article aims to provide valuable insights and data to students, researchers, and industry professionals. A comprehensive understanding of their construction, operation, and applications will enhance knowledge and contribute to continued advancements in milling technologies.
Prolusion to Tungsten Carbide Ball Mills
Tungsten carbide ball mills hold significant relevance in modern manufacturing and materials processing. Their unique material properties create a combination of durability and performance that is especially valuable in grinding applications. When exploring the topic of tungsten carbide ball mills, it is essential to consider their definitions, history, and the evolution of their design and function.
The purpose of this section is to underline the importance of tungsten carbide ball mills in industrial settings. These devices are essential for various activities, including the milling of hard materials in the production of ceramics, powders, and metal compounds. Such applications extend beyond simple grinding; they involve precision engineering where the quality of the final product is paramount. Understanding the nature of these mills provides insights into their advantages, operational efficiency, and the potential limitations that users may encounter.
Definition and Overview
Tungsten carbide ball mills are specialized grinding machines that employ balls made of tungsten carbide for the milling process. Tungsten carbide is a high-density, hard metal compound known for its remarkable resistance to wear and tear. This makes ball mills crafted from this material exceptionally efficient for grinding tasks, especially for hard and abrasive materials.
In simple terms, a ball mill consists of a hollow cylindrical shell that rotates around its axis. The material to be ground is placed inside along with the tungsten carbide balls. As the cylinder rotates, the balls tumble, colliding with the material and each other, leading to particle size reduction. The use of tungsten carbide enhances the performance and lifespan of the mill, allowing for high-throughput, effective processing.
History and Development
The development of tungsten carbide ball mills is intertwined with advancements in materials science and milling technology. The use of tungsten carbide as a milling medium began gaining traction in the mid-20th century when manufacturing requirements began to evolve toward high-performance standards. Prior to the incorporation of tungsten carbide, milling processes relied heavily on softer metals, which often wore down quickly under high operational stresses.
In the 1930s, researchers first explored tungsten carbide’s potential in tooling and cutting applications. By the 1950s and 1960s, the industrial sector recognized the benefits of using this robust material in milling processes. Over the decades, manufacturers have refined the design of ball mills, optimizing their construction and operational mechanisms to improve efficiency and reliability.
The introduction of automation in the late 20th century further transformed the landscape of milling technology. Enhanced precision in the design of tungsten carbide ball mills has vastly improved the productivity and consistency of outputs across various industries.
As tungsten carbide continues to evolve in response to market demands, ongoing research and development efforts may lead to new innovations in the field, thereby solidifying its status as a critical component in material processing.
"The use of tungsten carbide in ball mills revolutionized grinding applications, notably increasing efficiency and durability in various industries."
Overall, understanding the definition, overview, and historical development of tungsten carbide ball mills is crucial for appreciating their importance in today's advanced manufacturing landscape.
Material Properties of Tungsten Carbide
The material properties of tungsten carbide play a crucial role in determining its effectiveness in the construction of ball mills. This section will delve into key aspects such as its chemical composition, physical characteristics, and mechanical strength.
Chemical Composition
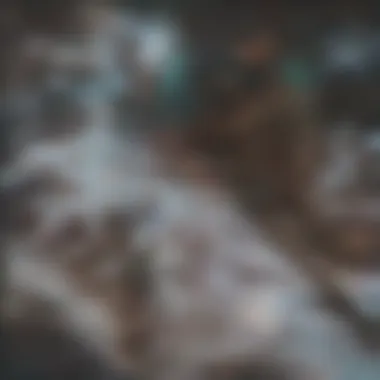
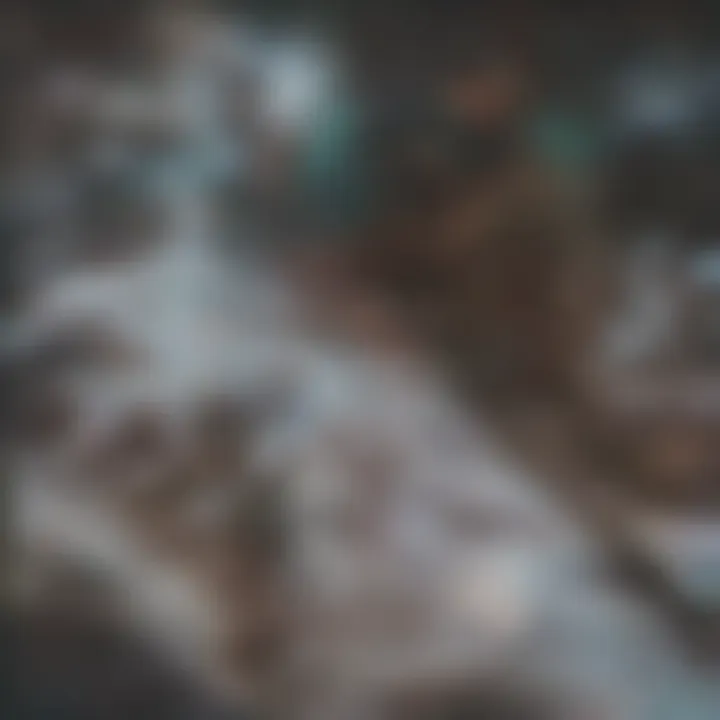
Tungsten carbide is primarily composed of tungsten and carbon. The standard chemical formula is represented as WC, which indicates one tungsten atom bonded with one carbon atom. This simple yet robust composition underpins the remarkable properties that make tungsten carbide highly effective in industrial applications.
In refining the composition, small percentages of other elements like cobalt may be added. Cobalt acts as a binder, improving the toughness and durability of the material. This careful balance ensures the resulting tungsten carbide maintains its hardness while being able to withstand high-stress conditions.
Physical Characteristics
Tungsten carbide displays several physical characteristics that enhance its utility. It has a high density, usually around 15.6 g/cm³, making it one of the densest materials available. This density contributes to its stability and weight in milling operations. Additionally, tungsten carbide has a notable hardness, rated around 9 on the Mohs scale.
These properties translate into great wear resistance, which is essential for any milling equipment subject to constant grinding motion. Its thermal conductivity is also noteworthy, enabling heat dissipation during intense milling processes. Furthermore, tungsten carbide exhibits a low thermal expansion coefficient, reducing the risk of dimensional changes under temperature fluctuations.
Mechanical Strength
The mechanical strength of tungsten carbide is one of the most revered attributes. It possesses a high compressive strength, generally around 6000 MPa, making it capable of enduring substantial forces without deforming. Such properties are vital for ball mills which consistently experience intense pressure during operation.
Tungsten carbide also exhibits excellent toughness, particularly when combined with cobalt. This helps in minimizing brittleness, allowing the material to absorb shock without fracturing. The wear resistance, coupled with its mechanical endurance, results in longer lifespan for the tungsten carbide components in the milling process. In summary, the mechanical properties contribute immensely to the efficiency and productivity of tungsten carbide ball mills, making them a favorable choice in diverse industries.
"With its unparalleled hardness and strength, tungsten carbide is a cornerstone material in some of the most challenging industrial applications."
By understanding these attributes, professionals in materials science and engineering can better appreciate how tungsten carbide contributes to the advancements in milling technology.
Construction of Tungsten Carbide Ball Mills
The construction of tungsten carbide ball mills is essential for understanding their functionality and effectiveness. The design and materials used in these mills directly influence their performance, and awareness of these factors provides insights into their operation. A well-constructed ball mill ensures durability, efficiency, and precision in grinding processes, which is crucial in various industrial applications.
Design Features
A significant aspect of tungsten carbide ball mills lies in their design features. These mills are generally cylindrical in shape with a rotating structure that houses the grinding media and material to be processed. The design aims to optimize the milling process, ensuring that the materials are subjected to a uniform grinding action.
Key design features include:
- Shape and Size: The cylindrical shape allows for a consistent flow of materials throughout the milling process. Varying sizes can accommodate different production volumes.
- Internal Linings: The technology often uses linings made from a variety of materials, including rubber or ceramic, which protect the mill's structure and enhance the grinding process.
- Shaft and Motor Placement: The placement of the shafts and motors optimizes energy consumption and improves the grinding efficiency.
Each of these features is vital in achieving a balance between productivity and longevity. A well-designed ball mill minimizes wear and tear, thus reducing downtime due to maintenance.
Components and Materials Used
The success of tungsten carbide ball mills heavily depends on the components and materials that comprise them. Generally, several critical components are necessary for effective operation:
- Ball Mill Shell: The shell is often made from high-grade steel or other tough materials. Tungsten carbide is often used for specific applications where durability and resistance to wear are essential.
- Grinding Media: This typically includes tungsten carbide balls, which provide the milling action. Their density and composition play a role in the efficiency of the grinding process.
- Drive Mechanism: This includes motors and gears that control the rotation of the mill. Electric motors are common, and the choice of motor influences the operational speed and energy efficiency.
- Seals and Bearings: Seals prevent dust and debris from entering the mill, while bearings support the rotating parts, ensuring smooth operation.
Choosing the right materials is critical. Tungsten carbide’s superior hardness and wear resistance compared to other materials make it a prime choice for components exposed to high-stress conditions.
"The efficiency and durability of ball mills can greatly influence production outcomes in a variety of sectors, emphasizing the need for high-quality construction."
Understanding these elements, and their integration within the structure of tungsten carbide ball mills, is fundamental for optimizing performance and ensuring the longevity of these industrial tools.
Operational Principles of Ball Mills
The operational principles of ball mills are crucial for understanding the efficiency and effectiveness of tungsten carbide ball mills. These principles dictate how material is processed within the milling equipment, influencing its ability to achieve the desired particle size and uniformity. The operation involves several key components, including the mechanics of milling and the grinding techniques utilized.
Mechanics of Milling
The mechanis of milling in ball mills revolves around the motion and impact of the grinding media, typically hard balls made from tungsten carbide, against the material being processed. When the ball mill rotates, centrifugal force generates energy that propels the balls towards the inner wall of the mill. As the balls fall back into the material, they impact it with significant force, executing a combination of grinding, crushing, and mixing action.
- This process is characterized by:
- Rotation speed: An important factor that influences the grinding efficiency. Optimal speeds ensure that the balls are lifted effectively and dropped with sufficient force.
- Ball size: The diameter of the balls affects the energy transfer and the resulting particle size. Larger balls will provide more force, leading to better fragmentation.
- Material load: The volume of material present in the mill impacts how well the balls can collide with it. An adequate load enhances the milling process.
The design of the mill also plays a role. Features such as the shape of the drum and the type of lining affect the ball motion, leading to varying outcomes in milling efficiency.
Grinding Techniques Utilized
Different grinding techniques can be employed within tungsten carbide ball mills to optimize performance and output. Understanding these techniques allows operators to tailor the milling process to specific applications.
- Wet milling: This technique involves adding a liquid, such as water or a solvent, to the milling process. It aids in reducing dust, enhances energy transfer, and allows for finer particle sizes. Wet milling is often used in mineral processing.
- Dry milling: In contrast, dry milling operates without liquid adding, focusing more on pulverizing solids. This method can be advantageous for certain materials that may react with moisture or for applications requiring a dry end product.
- Batch milling: This method processes a specific quantity of material before stopping to empty the mill. It is suitable for smaller production runs or research applications where precision is needed.
- Continuous milling: Opposite to batch milling, continuous milling allows for a constant flow of material in and out of the mill. This is effective for large-scale operations, optimizing production throughput.
The principles of operation for tungsten carbide ball mills translate directly to their performance. Understanding these fundamentals helps ensure optimal use in various applications.
By mastering these operational principles, users can enhance efficiency, reduce energy consumption, and achieve consistent results in their milling processes.
Performance Characteristics
The performance characteristics of tungsten carbide ball mills play a significant role in their effectiveness for grinding and milling applications. Understanding these characteristics helps users select the right equipment for their specific needs. In this section, we will detail the efficiency of tungsten carbide ball mills and compare their performance with other milling materials.
Efficiency of Tungsten Carbide Ball Mills
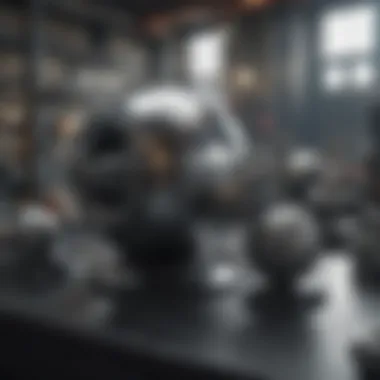
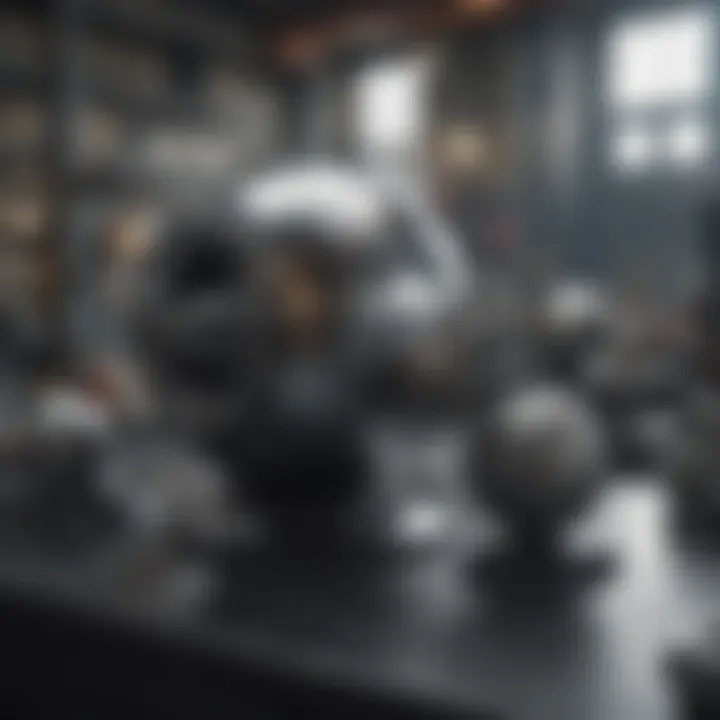
Tungsten carbide ball mills are known for their high efficiency in milling operations. This efficiency is primarily attributed to the material properties of tungsten carbide. Its hardness allows for superior resistance against wear and deformation during the milling process. As a result, these ball mills can maintain their performance over extended periods, leading to lower operational costs.
Several factors contribute to the efficiency of tungsten carbide ball mills:
- High Density: Tungsten carbide's density enhances its weight, which improves the impact force during grinding.
- Durability: These mills can withstand abrasive materials, reducing the need for frequent replacements.
- Reduced Energy Consumption: The efficient design reduces the energy required to achieve the desired particle size.
In practice, this means that industries utilizing tungsten carbide ball mills often experience increased productivity. On average, the milling process can be completed in a shorter time compared to other materials, yielding better results per hour. This efficiency underscores the value of tungsten carbide in various applications from micro-particles in pharmaceuticals to bulk materials in construction.
Comparison with Other Milling Materials
When comparing tungsten carbide ball mills with other milling materials, several elements come to light. This analysis includes factors like durability, cost-effectiveness, and performance under different conditions.
- Material Durability:
- Cost-Effectiveness:
- Heat Resistance:
- Versatility:
- Tungsten carbide exhibits superior durability compared to steel and ceramic milling media. While steel balls may wear down more quickly, tungsten carbide maintains its integrity longer, providing a consistent grinding performance.
- Though tungsten carbide balls might have a higher initial cost, their longevity and reduced downtime for maintenance make them more cost-effective in the long run. Industries benefit not only from lower replacement costs but also from improved processing speeds.
- Tungsten carbide can operate effectively at higher temperatures, making it suitable for processes that generate heat, unlike some ceramic materials that may degrade under intense conditions.
- Tungsten carbide can be utilized across various industries while maintaining structural integrity, unlike other materials that may be suitable only for specific applications.
This analysis shows that while each material has its unique strengths, tungsten carbide stands out for its combination of durability and efficiency, ultimately making it a preferred choice in the milling industry.
Applications of Tungsten Carbide Ball Mills
Tungsten carbide ball mills play a significant role across various industries, making their applications crucial to the understanding of this technology. Their effectiveness in comminuting materials, combined with their unique material properties, has led to their widespread use in diverse fields. This section will explore significant elements, benefits, and essential considerations regarding the applications of tungsten carbide ball mills.
Industrial Uses
Tungsten carbide ball mills are utilized in manufacturing processes where high durability and performance are required. Their capacity to grind materials efficiently makes them essential in sectors such as:
- Mining: They are used for grinding ores, allowing for the extraction of valuable minerals. The wear resistance of tungsten carbide ensures that the mills have a long lifespan, reducing operational costs.
- Ceramics: These mills are effective in grinding ceramic materials for tile production and other applications. The ability to achieve fine particle sizes is critical in ensuring the quality of the final products.
- Pharmaceuticals: In the pharmaceutical industry, tungsten carbide ball mills are used to create fine powders from raw materials. The precise control over particle size is crucial in drug formulation.
- Chemical Processing: They facilitate the mixing and grinding of chemical compounds in producing various materials, from fertilizers to plastics. The inert nature of tungsten carbide prevents contamination.
There are multiple factors that contribute to the preference for tungsten carbide ball mills, such as their efficiency, precision, and adaptability to different materials.
Research and Development
In the realm of research and development, tungsten carbide ball mills provide essential support in experimentation and innovation. They are frequently employed in:
- Material Sciences: These mills help researchers investigate the properties of new materials. By applying controlled milling processes, scientists can study how specific compounds behave under various conditions.
- Nanotechnology: In the production of nanomaterials, tungsten carbide ball mills enable the grinding of materials to the nanoscale. Such applications are essential in developing advanced materials with unique properties.
- Innovative Coatings: The ability to finely grind and mix powders of different substances aids in creating new coating materials. Researchers can explore new combinations that enhance performance in various applications such as automotive and aerospace industries.
The role of tungsten carbide ball mills in R&D not only advances technological boundaries but also impacts various applications that rely on precise material characteristics. Overall, the versatility and effectiveness of these mills make them invaluable tools in both industrial settings and innovative research laboratories.
Maintenance Considerations
Maintenance considerations are vital for the longevity and efficiency of tungsten carbide ball mills. Proper maintenance routines not only ensure optimal performance, but they also safeguard the integrity of the equipment. Regular maintenance helps to identify potential issues before they escalate into significant problems, thus minimizing downtime in industrial settings. In industries where precision and efficiency are paramount, the implications of neglecting maintenance can result in costly repairs and loss of productivity.
Having structured maintenance protocols aids in enhancing the overall efficacy of the milling operation. These protocols can lead to improved grinding efficiency, extended equipment lifespan, and reduced unexpected failures. Moreover, a well-maintained ball mill can contribute to higher quality output, important in competitive markets.
Regular Maintenance Protocols
Establishing regular maintenance protocols is essential for any facility using tungsten carbide ball mills. Here are key components of effective maintenance:
- Daily Inspections: Conduct visual inspections to check for any obvious signs of wear or damage.
- Lubrication: Ensure that all moving components are adequately lubricated. This reduces friction and wear.
- Calibration: Regularly calibrate the mill to ensure it operates at the desired specifications.
- Cleanliness: Maintain cleanliness around the machinery to prevent dust and debris accumulation, which can affect performance.
- Documentation: Keep detailed records of maintenance activities, inspections, and repairs to facilitate future assessments.
By adhering to these protocols, operators can establish a consistent routine that promotes reliability and performance.
Common Issues and Troubleshooting
Despite precautions, various issues can arise in the operation of tungsten carbide ball mills. Awareness of common problems allows for swift action to mitigate them. Here are some frequent issues:
- Overheating: This can be due to inadequate lubrication or excessive grinding friction. Ensure timely lubrication and adjust operational speeds as necessary.
- Noise Levels: Unusual noises may indicate mechanical issues or loose components. A thorough inspection can determine the cause.
- Vibration: Excessive vibration often points to misalignment or imbalance. Regular checks can prevent prolonged complications.
- Decreased Efficiency: If the mill is not grinding efficiently, it may require recalibration, especially if parameters have changed.
- Material Clogging: Accumulation of materials in the mill can hinder performance. Regular cleaning is crucial to prevent this problem.
Once issues are identified, troubleshooting steps should be taken promptly. Engagement with qualified technicians can facilitate effective solutions, further ensuring minimal disruption in operations.
Recent Advancements in Milling Technology
Recent advancements in milling technology have significantly enhanced the efficiency and effectiveness of tungsten carbide ball mills. The evolution of this technology is paramount for industries that rely on precise material processing and grinding. Innovations in materials and automation are reshaping how these mills operate, providing solutions that not only improve performance but also address concerns about sustainability and operational cost.
Innovation in Materials
The development of new materials has played a crucial role in advancing the performance of tungsten carbide ball mills. The incorporation of advanced composites and coatings has been particularly advantageous. These materials can withstand the intense wear and tear that occurs during grinding operations.
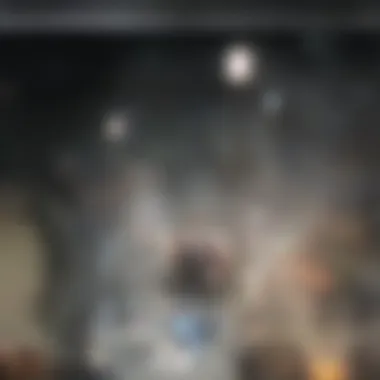
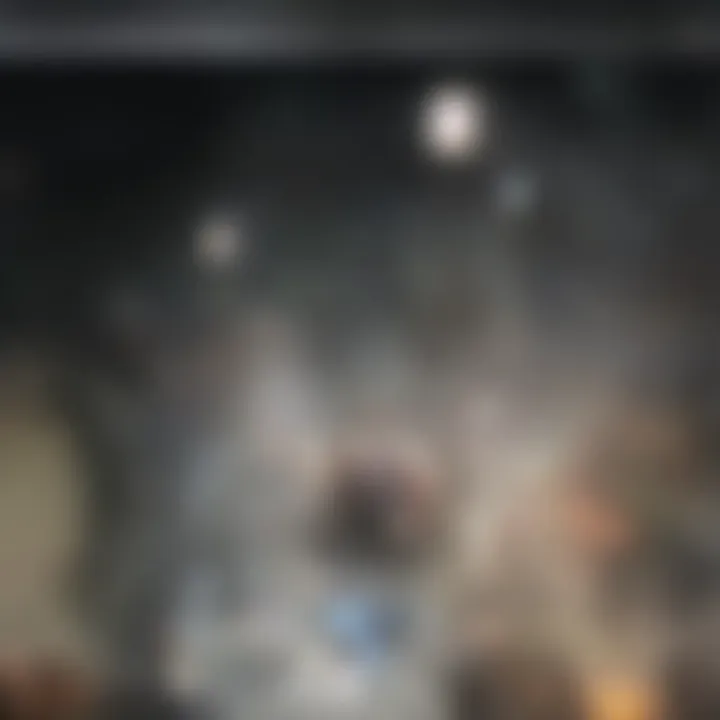
- Nanostructured Materials: One notable trend is the use of nanostructured tungsten carbide. This innovation enhances hardness and toughness, which leads to better milling outcomes.
- Coatings: Enhanced coatings are also seen as a game changer. For instance, using diamond-like carbon coatings can significantly reduce friction, allowing for smoother processes.
This innovation not only boosts productivity but also decreases the rate of equipment degradation. Hence, operators can expect a longer lifespan from their machinery, which translates into lower replacement costs over time.
Automated Milling Solutions
Automation has become an indispensable part of modern manufacturing processes. In the realm of tungsten carbide ball mills, automated milling solutions provide several benefits, enhancing overall operational efficiency.
- Real-Time Monitoring: These solutions enable real-time monitoring of milling processes. Data analytics can inform operators about equipment status and performance metrics, allowing for proactive maintenance.
- Optimized Operations: Automated systems can adjust operational parameters based on the material being processed. This adaptability ensures optimal performance across different operational scenarios.
- Labor Savings: By reducing the need for constant manual supervision, automation contributes to labor savings. This allows skilled workers to focus on more complex tasks, enhancing overall productivity.
Adopting automated milling solutions is not merely a trend but a clear indication of where the industry is heading. It represents a shift toward more intelligent, responsive, and efficient operations.
The integration of innovative materials and automated systems marks a critical step forward in the operation of tungsten carbide ball mills, driving productivity and sustainability in industrial processes.
Future Trends in Tungsten Carbide Milling
The importance of future trends in tungsten carbide milling cannot be overstated. As global industries evolve, the demand for advanced milling technologies continues to rise. Tungsten carbide ball mills are at the forefront of this evolution. They offer unique advantages in terms of efficiency and precision. Understanding these trends assists stakeholders in making informed decisions.
Emerging Technologies
Emerging technologies in milling address the need for greater efficiency and reduced environmental impact. One notable development is the integration of advanced automation. Automated systems can significantly enhance the precision of milling operations. This results in less material wastage and improved quality of the final product.
Moreover, innovations in monitoring systems allow for real-time data analysis. By utilizing smart sensors and IoT technology, operators can gather insights on performance metrics. This intelligence can be crucial for predictive maintenance, minimizing downtime.
In addition to automation, the exploration of additive manufacturing presents exciting possibilities. Combining traditional milling processes with additive techniques can create more complex shapes and features. This hybrid approach can bring cost savings and improved design flexibility.
- Automation: Enhances precision and reduces waste.
- IoT Integration: Facilitates real-time monitoring and maintenance.
- Hybrid Techniques: Combines milling and additive manufacturing for innovative designs.
Market Projections
Market projections for tungsten carbide milling are optimistic. Analysts foresee consistent growth driven by the demand from various sectors. Industries such as aerospace, automotive, and medical are seeking highly durable materials. Tungsten carbide's strength, coupled with advancements in milling technology, positions it favorably.
The global market for tungsten carbide tools is expected to expand significantly. Factors contributing to this growth include rapid industrialization and technological advancement. Also, the shift towards precision engineering processes amplifies the need for high-performance milling equipment.
According to a recent report, the tungsten carbide tools market could reach a valuation of $5 billion by 2030, reflecting a CAGR of around 6% during the forecast period.
Key aspects of market projections include:
- Increased Demand: Driven by industrial expansion.
- Technological Advances: Continuous improvements in milling efficiency.
- Emerging Markets: Growth in developing regions enhances opportunities.
In summary, understanding future trends in tungsten carbide milling enables stakeholders to prepare for what lies ahead. Emerging technologies and positive market projections indicate a thriving landscape for tungsten carbide ball mills.
Environmental Considerations
Environmental considerations play a pivotal role in the discussion of tungsten carbide ball mills. As industries strive for higher efficiency and productivity, the implications of manufacturing methods on the environment cannot be overlooked. The use of tungsten carbide, with its unique properties, presents both opportunities and challenges related to environmental sustainability.
Sustainability in Manufacturing
Sustainability has become a guiding principle in modern manufacturing practices. In the context of tungsten carbide ball mills, it involves the adoption of processes that minimize waste, reduce energy consumption, and limit harmful emissions. Several important aspects are considered:
- Material Efficiency: Tungsten carbide is known for its durability and longevity. Using this material in ball mills means that products can last significantly longer, which reduces the need for frequent replacements or repairs.
- Recycling Practices: Recycling tungsten carbide reduces the environmental footprint. Reclaimed tungsten carbide powder can be reused in the manufacturing of new tools and parts. This reduces the reliance on raw materials and fosters a circular economy.
- Energy Consumption: The production of tungsten carbide typically requires substantial energy. However, advancements in manufacturing technologies aim to optimize processes and lower energy use, mitigating the overall environmental impact.
"Sustainable practices in the manufacturing of tungsten carbide can yield both economic and environmental benefits."
By focusing on sustainability, companies can not only comply with environmental policies but also enhance their brand reputation among increasingly eco-conscious consumers.
Regulatory Framework
A strong regulatory framework is essential to ensure that the industry adheres to environmental standards. Regulations dictate how materials are sourced, how emissions are managed, and how waste is disposed of. Key elements of the regulatory framework in tungsten carbide manufacturing include:
- Environmental Regulations: Compliance with local and international environmental laws, such as the Resource Conservation and Recovery Act (RCRA) in the United States, ensures that practices in the industry do not lead to environmental degradation.
- Emission Standards: Manufacturers are subject to standards that require them to limit emissions of harmful substances during production. These measures help protect air and water quality, benefiting public health and the environment.
- Lifecycle Assessments (LCA): Regulatory bodies may require LCA to assess the ecological impact of tungsten carbide products throughout their entire lifecycle, from raw material extraction to disposal.
Incorporating these regulatory factors not only helps in maintaining compliance but also promotes a more sustainable approach to production, ultimately benefiting the environment and enhancing the industry's overall credibility.
End
The conclusion is a critical section of this article as it encapsulates the main findings and insights gained from the earlier discussions on tungsten carbide ball mills. Throughout this exploration, we have reiterated the unique properties of tungsten carbide that make it a preferred choice in milling technologies. This section serves as a synthesis of the key elements addressed earlier, focusing on their benefits and significance in various industries.
Summary of Key Points
In the prior sections, we have delved into a range of topics concerning tungsten carbide ball mills. The following key points summarize our findings:
- Material Properties: Tungsten carbide is noted for its exceptional hardness, chemical stability, and wear resistance, which are pivotal in enhancing milling performance.
- Construction Details: The design features and the choice of components directly impact the efficiency and durability of these ball mills.
- Operational Principles: Understanding milling mechanics and techniques reveals how tungsten carbide optimizes the grinding process.
- Applications Across Industries: From metallurgy to pharmaceuticals, the versatility of tungsten carbide ball mills addresses diverse industrial needs.
- Maintenance Strategies: Regular checks and maintenance ensure longevity and consistent operation of milling equipment, minimizing downtime.
- Technological Advancements: Innovations in milling technology signal a future where productivity and efficiency are further enhanced.
- Environmental Impact: Emphasizing sustainability and adhering to regulations illustrates the industry's commitment to eco-friendly practices.
Final Thoughts
The exploration of tungsten carbide ball mills emphasizes their importance in manufacturing processes. As industries evolve, these mills offer vital capabilities that enhance production efficiency and product quality. Future advancements in milling technologies will likely focus on automation and smarter solutions that further optimize the use of tungsten carbide in grinding applications.
"In the competitive field of manufacturing, the choice of milling equipment has profound implications on efficiency, cost, and output quality."
For those interested in the future of milling technology, staying informed on innovations and advancements will be essential. An effective approach to both current and future challenges in materials processing can yield competitive advantages, ensuring sustained growth and relevance in an ever-evolving marketplace.