Exploring Properties and Applications of Titanium Alloys

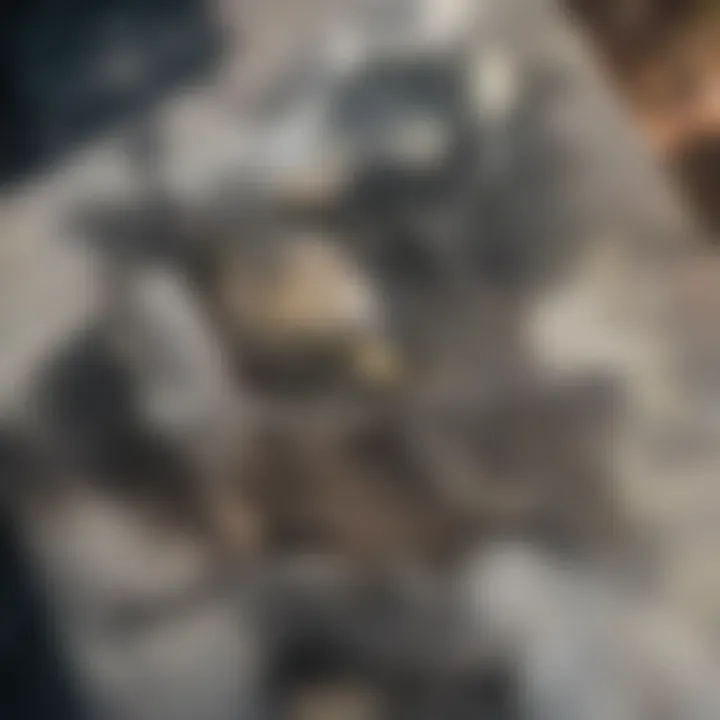
Intro
Titanium alloys play a crucial role in various industries due to their unique properties. These materials offer a favorable combination of strength, low density, and corrosion resistance. These characteristics make them ideal for applications in aerospace, medical, and automotive fields. Understanding titanium alloys involves exploring their classifications, compositions, and performance metrics.
The significance of titanium alloys cannot be overstated. In the aerospace industry, for example, components must endure extreme conditions while maintaining structural integrity. Similarly, in medical applications, titanium’s biocompatibility enhances the effectiveness of implants and surgical tools. This article will demystify titanium alloys, enabling readers to appreciate their applications and advantages.
Key Findings
Major Results
- Titanium alloys can be broadly classified into alpha, beta, and alpha-beta types based on their phase structure.
- The properties of titanium alloys vary significantly depending on their composition. Each type serves specific applications.
- Notable titanium alloys include Ti-6Al-4V, Ti-7Al, and Ti-6-2-4-6, widely acknowledged for their performance in demanding environments.
- The production methods for titanium alloys include melting techniques such as vacuum arc remelting and electron beam melting, providing different material properties.
Discussion of Findings
The diversity of titanium alloys allows for tailored applications. For instance, Ti-6Al-4V is a widely used alloy known for its excellent strength-to-weight ratio, making it suitable for aerospace components. Its performance metrics reveal that this alloy can withstand significant stress without deforming, which is essential in flight. In contrast, Ti-7Al is preferred in industries requiring higher temperature resistance.
Examining these findings, it becomes apparent that the choice of titanium alloy significantly affects performance across applications. By understanding the characteristics of different alloys, researchers and professionals can make informed decisions, impacting material selection profoundly.
Methodology
Research Design
The exploration of titanium alloys involves both experimental studies and literature reviews. By synthesizing findings from previous research, this article aims to provide a thorough understanding of the subject.
Data Collection Methods
Data has been gathered from various sources, including academic journals, industry reports, and reputable websites such as Wikipedia and Britannica. These resources provide insight into the properties, uses, and production techniques for titanium alloys.
"The unique properties of titanium alloys make them invaluable in high-performance applications across diverse sectors."
In summary, this article serves as a comprehensive resource for those interested in titanium alloys, detailing not only their classifications but also their significance in various industries. Understanding these materials enhances knowledge within engineering and scientific communities.
Prolusion to Titanium Alloys
Titanium alloys are a critical material within various engineering fields, characterized by their exceptional combination of strength, lightweight, and corrosion resistance. The analysis of titanium alloys is essential, not just from a theoretical standpoint, but also for practical applications across industries such as aerospace, medicine, and automotive. Understanding titanium alloys lays a foundation for future innovations and improvements in material science. The significance of titanium alloys cannot be overstated; they directly impact performance metrics in applications where every gram counts and where durability is paramount.
Definition and Significance
Titanium alloys are metallic materials made primarily of titanium, combined with other elements to enhance their properties. These alloying elements may include aluminum, vanadium, and molybdenum, each providing unique characteristics. The definition of titanium alloys extends beyond the simple classification of materials; it encompasses a range of properties that make these alloys suitable for specific applications.
The significance of titanium alloys in modern engineering is undeniable. Their high strength-to-weight ratio means they can perform under stress without adding excessive weight, making them valuable in fields such as aerospace, where efficiency is critical. Furthermore, titanium's natural resistance to corrosion makes these alloys ideal for pharmaceutical and biomedical applications. The implications for research and industry continue to grow as advancements are made within the framework of titanium alloy technology.
Historical Context
The history of titanium alloys began in the 20th century, with the first significant extraction of titanium occurring in the 1930s. However, it wasn't until the 1940s and 1950s that the aerospace industry recognized titanium's potential. The development of titanium alloys was driven mainly by the need for durable and lightweight materials for military and aerospace applications.
Key milestones include:
- 1940s: Initial production and application of titanium in aerospace.
- 1950s: Introduction of titanium alloys, specifically in the form of Ti-6Al-4V, which remains highly popular.
- 1960s and 1970s: Expanded use in medical devices as the advantages of biocompatibility became recognized.
Over the decades, the understanding and usage of titanium alloys have evolved significantly. Today, research continues to explore innovative alloy combinations and processing techniques, striving for even higher performance and sustainability in applications. The historical journey of titanium alloys not only reflects technological advancements but also underscores the importance of continual research and development in material science.
Classification of Titanium Alloys
The classification of titanium alloys is essential for understanding their unique properties and potential applications. By categorizing titanium alloys based on their microstructure and phase composition, one can make informed decisions regarding their use in various industrial contexts. Classification helps in selecting the appropriate alloy for a specific application, thus enhancing performance and ensuring safety. Moreover, it contributes to ongoing research and development in the field of metallurgy.
Alpha Alloys
Alpha alloys are characterized primarily by their hexagonal close-packed (HCP) crystalline structure at all temperatures. The stability of this structure offers great advantages in terms of elevated temperature strength and oxidation resistance. Common alloying elements in alpha alloys include aluminum, tin, and zirconium. These additions contribute to improved strength without significantly impacting the alloy's weight.
Alpha alloys are less susceptible to embrittlement, making them suitable for high-temperature applications, particularly in the aerospace industry. For example, titanium 6-4, which contains both alpha and beta elements, displays remarkable strength while maintaining ductility. The ease of fabricating alpha alloys is also noteworthy, as they can be processed using common methods such as forging and rolling.
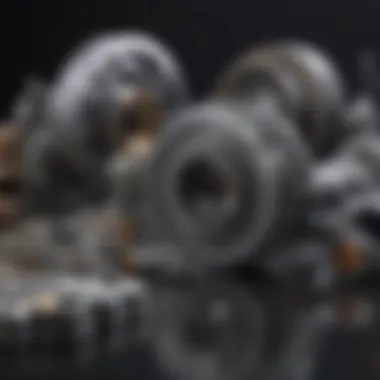
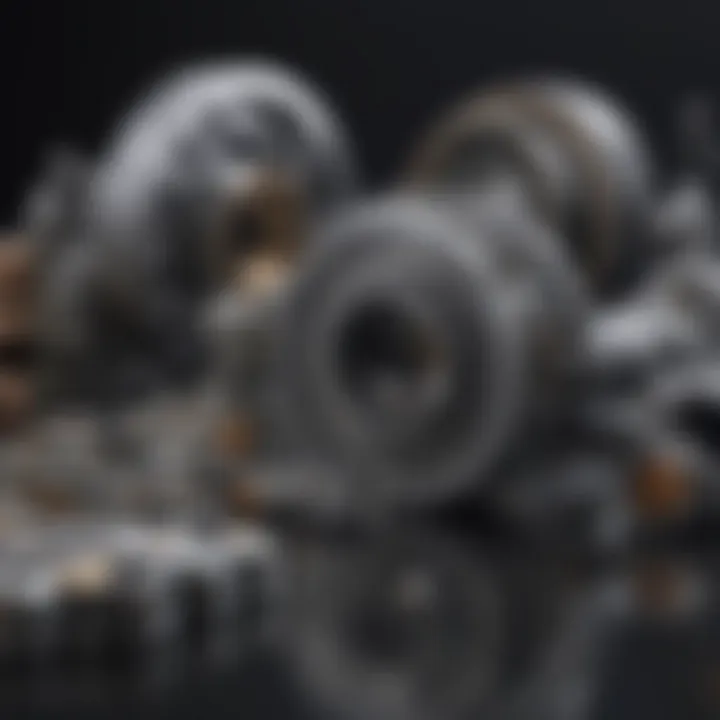
Beta Alloys
Beta alloys, on the other hand, possess a body-centered cubic (BCC) crystalline structure at room temperature, which allows them to be more ductile and formable compared to their alpha counterparts. The presence of beta-stabilizing elements, such as molybdenum, vanadium, and niobium, enhances the alloy's workability. As such, beta alloys are often employed in applications requiring complex shapes, such as aerospace components or automotive parts.
Another strength of beta alloys is their exceptional resistance to fatigue and cracking when subjected to cyclic loading conditions. This makes them advantageous in high-stress environments, where durability is critical. A notable example of a beta alloy is titanium 3-2.5, widely used in medical devices like implants and surgical tools due to its combination of strength and biocompatibility.
Alpha-Beta Alloys
Alpha-beta alloys contain a mixture of both alpha and beta phases, allowing them to offer a balanced combination of properties derived from each classification. These alloys typically exhibit a good compromise of strength, ductility, and weldability. The presence of alpha and beta phases in the microstructure can significantly enhance the mechanical performance of the alloy, making alpha-beta alloys suitable for various demanding applications.
Several common alloys belong to this category, with titanium 6-4 being the most prominent. Its exceptional strength-to-weight ratio has made it a preferred material in aerospace and military applications. The versatility provided by alpha-beta alloys is one of the main reasons for their widespread use, as they cater to numerous engineering requirements, balancing considerations of weight, strength, and workability.
"Understanding the classification of titanium alloys is the first step in leveraging their unique properties in innovation and industry."
Chemical Composition of Titanium Alloys
The chemical composition of titanium alloys is a foundational element that influences their performance and application across various industries. Understanding the specific elements that contribute to the alloy's properties can help in selecting appropriate materials for diverse engineering tasks. Each alloy's characteristics are directly affected by the elements that are present, which determine properties like tensile strength, corrosion resistance, and fatigue performance.
Key Elements and Their Effects
The fundamental elements in titanium alloys include titanium, aluminum, vanadium, iron, and others. Here are key components that significantly impact the performance:
- Titanium (Ti): Represents the base material. It provides the fundamental properties we associate with titanium alloys, including low density and high strength.
- Aluminum (Al): Commonly added to alpha alloys, it enhances oxidation resistance and improves tensile strength at elevated temperatures.
- Vanadium (V): A principal element in beta alloys, vanadium contributes to the stability of the beta phase, which in turn boosts the toughness of the alloy.
- Iron (Fe): Sometimes used as a minor alloying component, iron can influence the mechanical properties but may also reduce corrosion resistance if present in excess.
The interplay of these elements leads to specific benefits while also presenting some considerations. For instance, while aluminum may improve strength, excessive amounts can lead to decreased ductility.
Alloying Elements in Detail
Titanium alloys often incorporate various alloying elements to tailor their properties for specific applications. Below are some common alloying elements and their roles in titanium alloys:
- Molybdenum (Mo): Enhances strength and hardness at high temperatures, making it suitable for aerospace applications.
- Zirconium (Zr): Provides improved corrosion resistance, particularly in acidic environments, making it a valuable addition for chemical processing applications.
- Tin (Sn): Increases the strength and ductility of titanium alloys, facilitating the formation of specific microstructures.
- Hydrogen (H): While generally harmful in large quantities, controlled amounts can improve ductility and toughness.
The precise composition of titanium alloys ultimately determines their mechanical properties, influencing decisions in critical applications, from aerospace to biomedical devices.
Mechanical Properties
Mechanical properties are essential when discussing titanium alloys. These properties determine how materials react under various forms of stress, which affects their usability in different applications. Understanding the mechanical properties helps to optimize use in industries ranging from aerospace to medical. Key properties include tensile strength, fatigue resistance, and corrosion resistance.
Tensile Strength
Tensile strength refers to the maximum amount of tensile (pulling) stress that a material can withstand before failure. For titanium alloys, tensile strength is crucial because it defines their ability to bear loads while maintaining structural integrity. High tensile strength in titanium alloys, such as Ti-6Al-4V, makes them ideal for critical aerospace components and structures. This alloy exhibits a high yield strength, allowing it to perform well under extreme conditions, including high temperatures and variable loads.
Moreover, the ability to tailor tensile strength through alloy composition and processing methods expands the potential applications in engineering. The distinction between alpha, beta, and alpha-beta alloys plays a role here, as it directly influences the mechanical properties and overall performance of the created material.
Fatigue Resistance
Fatigue resistance is another significant property for titanium alloys. It describes the material's ability to withstand cyclic loads without experiencing failure. Given that components in environments such as aerospace and automotive regularly undergo repeated stress cycles, fatigue resistance is a necessity.
Titanium alloys generally exhibit excellent fatigue properties. For instance, low-fatigue crack propagation in alloys makes them suitable for use in high-stress environments. By using titanium alloys with specific microstructures, designers can enhance fatigue resistance. Proper understanding of factors like load paths and environmental conditions is important for applications that demand high reliability, such as in turbine blades or airplane fuselage structures.
Corrosion Resistance
Corrosion resistance is one of the standout features of titanium and its alloys. These materials develop a passive oxide layer that provides a natural barrier against corrosion. Titanium's resistance to both general and localized corrosion allows it to perform well in harsh environments, including marine settings and chemical processing.
The combination of corrosion resistance and mechanical properties enables titanium alloys to be used in medical implants, where they need to maintain integrity in the human body for extended periods.
"Corrosion resistance reduces maintenance costs, extends the lifespan of components, and assures performance reliability in challenging environments."
Production Methods
The production methods of titanium alloys are crucial in determining their final properties and suitability for various applications. Understanding these methods provides insight into how titanium alloys are manipulated to meet specific engineering demands. Furthermore, the effectiveness of each technique can significantly impact factors such as cost, material integrity, and the characteristics of the final product. By examining the different production processes, we can appreciate how each one contributes to the versatility and performance of titanium alloys across industries.
Powder Metallurgy
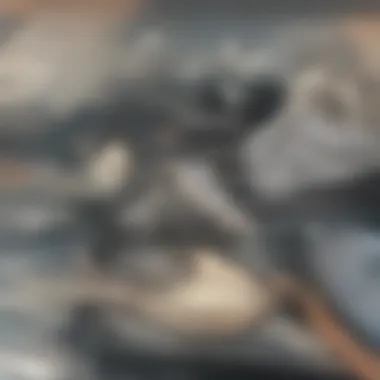
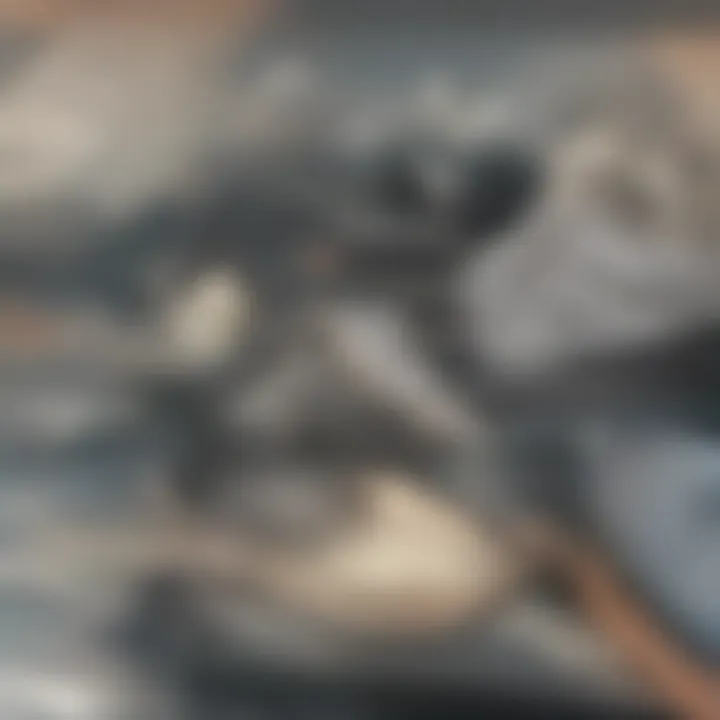
Powder metallurgy is becoming an increasingly popular method for producing titanium alloys. This technique involves forming metallic powders into solid structures through compaction and sintering. The advantages of powder metallurgy include the ability to create intricate geometries that are often unachievable with traditional methods. This method allows for a high degree of control over the microstructure and composition, which is essential for tailoring the mechanical properties of the alloy.
However, powder metallurgy does carry some challenges. The cost of producing titanium powders can be high, and the process requires precise control to prevent contamination. Additionally, the density of the final product can vary, affecting its strength and reliability in practical applications. As the demand for titanium materials continues, advancements in powder metallurgy techniques will likely play a key role in making titanium alloys more accessible.
Casting Techniques
Casting techniques are another foundational method in the production of titanium alloys. This process involves pouring molten titanium or its alloys into a mold, where it solidifies into the desired shape. Casting is useful for producing large components that are not easily created through other methods. It allows for significant design flexibility, supporting a range of applications from aerospace to automotive sectors.
While casting has many benefits, it also presents several challenges. Controlling the cooling process is essential to avoid defects such as porosity or unwanted phase formations. In addition, achieving uniform properties throughout the cast component can be difficult. The choice of casting technique—such as investment casting or sand casting—can also affect the material properties and final application. Despite these challenges, advancements in casting technology continue to improve the outcomes of titanium castings, making them more reliable and cost-effective.
Wrought Processes
Wrought processes refer to the methods of shaping titanium alloys through mechanical deformation. This category includes techniques like forging and rolling. Wrought processes can enhance the properties of titanium alloys significantly. By refining the grain structure, these processes improve overall strength, ductility, and toughness.
One of the primary advantages of wrought processing is that it allows for exceptionally high-performance materials to be produced. High-temperature applications often rely on wrought titanium due to its superior mechanical properties achieved through work hardening. However, these processes can be expensive and time-consuming.
Moreover, the heat treatment required in some wrought processes adds an additional layer of complexity. Care must be taken to avoid oxidation, which can diminish material integrity. Nevertheless, the continued development in wrought processing technologies holds promise for even greater effectiveness and applicability in the titanium alloy market.
Applications of Titanium Alloys
The applications of titanium alloys are pivotal to understanding their significance in modern materials science. These alloys are renowned for their strength, lightweight nature, and corrosion resistance, making them ideal for various industries. Their versatility allows them to be utilized in both critical and non-critical applications, leading to enhancements in performance and safety. Moreover, their unique attributes contribute to innovative designs and manufacturing processes.
Aerospace Industry
One of the most prominent areas where titanium alloys are used is the aerospace industry. These alloys play an essential role in aircraft construction due to their high strength-to-weight ratio. This characteristic is crucial for achieving fuel efficiency and reducing operational costs. Notable titanium alloys such as Ti-6Al-4V are employed in components like turbine blades, airframe structures, and fasteners.
The resistance of titanium alloys to extreme temperatures and pressures further amplifies their importance in aerospace applications. Their ability to maintain structural integrity under harsh conditions ensures safety and reliability in flight. As a result, aerospace engineers continually seek to replace heavier materials with titanium, thereby optimizing performance.
Medical Implants
In the medical field, titanium alloys are recognized for their biocompatibility, which is especially critical for implants. Due to their excellent corrosion resistance and ability to bond with bone, alloys like Ti-6Al-4V and commercially pure titanium are commonly used in orthopedic and dental implants. The interaction between these materials and biological tissues is an area of ongoing research, with the goal of improving patient outcomes.
Factors such as wear resistance and mechanical strength make titanium alloys favorable choices for long-term implants. These attributes ensure that devices like hip replacements and dental crowns withstand the stresses of daily use. The FDA has approved various titanium-based devices, affirming their reliability and safety in medical interventions.
Automotive Applications
The automotive industry has also embraced titanium alloys, particularly in high-performance and luxury vehicles. Their lightweight properties contribute to reduced vehicle weight, improving fuel efficiency and handling. Alloys like Ti-6Al-4V are used in components ranging from exhaust systems to engine parts, where strength and durability are mandatory.
Moreover, as governments enforce stricter emissions regulations, the shift towards lightweight materials is accelerating. Titanium alloys offer a solution that meets these regulatory requirements while enhancing overall vehicle performance. Some manufacturers are experimenting with advanced alloys to create parts that provide both increased durability and cost-effectiveness.
The use of titanium alloys in various sectors underscores their crucial role in advancing technology and improving product performance. Their unique properties allow for innovations that are transforming multiple industries.
Advantages of Titanium Alloys
Titanium alloys offer distinct advantages that make them preferable in various applications. Their unique properties include a favorable combination of strength, weight, and corrosion resistance. These qualities enhance their value across different industries, particularly aerospace and medical sectors. Understanding these advantages allows engineers and manufacturers to harness the full potential of titanium alloys in innovative ways.
High Strength-to-Weight Ratio
One of the most defining characteristics of titanium alloys is their high strength-to-weight ratio. This means they provide exceptional strength while remaining relatively lightweight. For aerospace applications, this property is particularly vital. Reducing the weight of aircraft components leads to significant improvements in fuel efficiency and overall performance.
- Enhanced Performance: Reduced weight allows for more efficient propulsion and increased payload capacity.
- Improved Durability: Unlike some metals that may weaken under stress, titanium maintains its integrity, making it suitable for critical structural components.
Moreover, in the automotive industry, this property is used to create lighter vehicles that do not compromise safety. This blend of strength and lightness also finds application in sports equipment, where performance is often contingent on the materials used.
Biocompatibility
Another significant advantage of titanium alloys is their biocompatibility. This refers to the ability of materials to perform with an appropriate host response in specific applications, especially medical. Titanium is widely recognized for its compatibility with human tissue, making it the material of choice for medical implants.
- Dental Implants: Titanium's properties allow it to bond well with bone tissue, important for stability and longevity of dental implants.
- Orthopedic Devices: For joint replacements and other surgeries, titanium extends the life of implants and reduces the risk of rejection by the body.
Using titanium ensures a lower risk of adverse reactions in medical applications. This factor contributes to better outcomes for patients and enhances the trust in medical technologies.
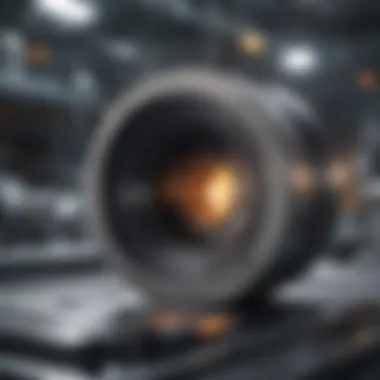
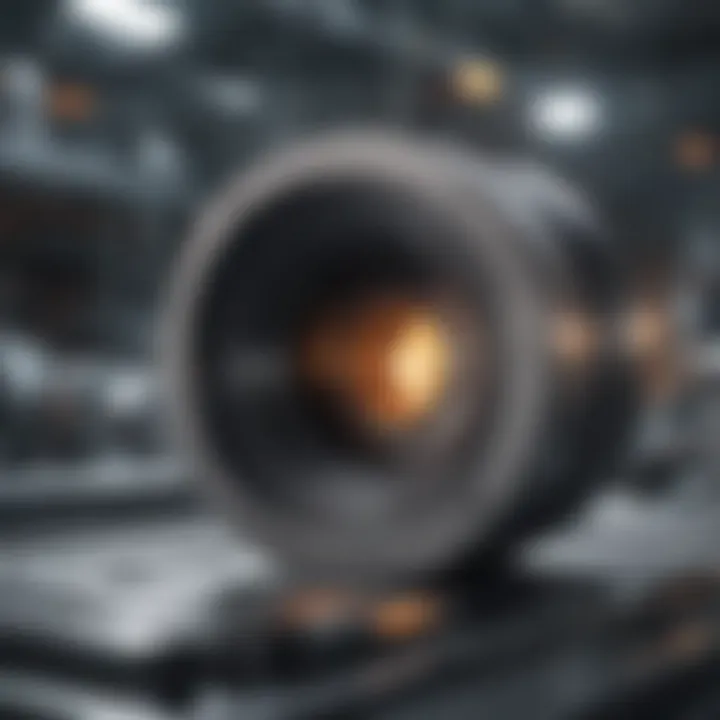
"The unique properties of titanium have made it a cornerstone in both aerospace and medical fields due to its unrivaled strength and biocompatibility."
In summary, the advantages of titanium alloys are pivotal to their widespread usage. Their high strength-to-weight ratio and biocompatibility are key drivers behind their selection in demanding environments where performance and safety are paramount. For professionals exploring material options, understanding these advantages is essential.
Challenges in Working with Titanium Alloys
The application of titanium alloys in various industries is remarkable, yet it comes with a set of challenges that need careful consideration. The complexities involved in working with these alloys can impact both production efficiency and product quality. Understanding these challenges is crucial for industries relying on titanium alloys, as they influence cost, material selection, and manufacturing processes.
Cost Implications
The use of titanium alloys is often associated with higher costs compared to other materials. This is primarily due to the expense of raw titanium and the intricate processes required for its extraction and alloying. Techniques like Kroll process, which involves converting titanium tetra-chloride into titanium sponge, contribute significantly to these initial financial burdens.
Additionally, the costs do not end with material acquisition. Equipment capable of machining titanium alloys must meet specific requirements to handle their unique properties. This leads to investments in specialized tools and technologies, increasing the overall expenses.
- Higher material costs compared to steel and aluminum.
- Need for advanced machining and manufacturing equipment.
- Increased labor costs due to skilled workforce requirement.
These cost implications can deter some companies from utilizing titanium alloys, affecting their competitive edge and overall production costs.
Processing Difficulties
Processing titanium alloys presents distinct challenges. The material’s low thermal conductivity means that it is prone to overheating during machining, which can lead to excessive tool wear and poor surface finish. This necessitates the use of specific cutting speeds and feeds, adding complexity to the machining process.
Furthermore, titanium’s tendency to react chemically with oxygen at elevated temperatures presents another challenge. Oxidation can lead to embrittlement, affecting the mechanical properties of the alloy.
To overcome these hurdles, manufacturers often employ:
- Controlled atmospheres during processes such as welding.
- Specific coolant systems during machining.
"The unique characteristics of titanium alloys demand careful attention to processing parameters to ensure product integrity and performance."
The combination of high costs and processing difficulties means that working with titanium alloys requires a well-planned approach. Investment in technology and skilled labor can mitigate some of these issues, making the use of titanium alloys more feasible. Ultimately, balancing these challenges against the benefits of using titanium alloys is essential for achieving optimal results.
Future Trends in Titanium Alloys
The study of titanium alloys is evolving. Understanding future trends is crucial not only for manufacturers but also for researchers and academics. These trends can lead to performance improvements and broaden applications. As industries continue to demand higher efficiency and sustainability, titanium alloys are poised for significant advancements. In this section, we will explore two critical areas shaping the future of titanium alloys: innovative alloy developments and sustainable practices.
Innovative Alloy Developments
Recent developments in titanium alloys focus on enhancing properties such as strength, corrosion resistance, and weight reduction. Researchers are experimenting with new combinations of alloying elements. This innovation leads to alloys with tailored characteristics for specific applications.
For example, advancements in titanium aluminides, like Ti-6Al-4V, are changing their performance profile. These alloys exhibit lower density and improved thermal stability. They are particularly attractive in the aerospace and automotive sectors, where every gram counts.
Another direction involves the use of advanced manufacturing techniques such as additive manufacturing. This process allows for more complex geometries and could significantly reduce waste in production. It is already being applied in sectors like aerospace, where intricate components can be lighter and more efficient than those produced through traditional methods.
"The potential of innovative alloy developments is vast. It can redefine the performance standards of titanium alloys across industries."
Sustainable Practices
Sustainability in manufacturing is becoming a key consideration for industries worldwide. Titanium alloys, traditionally seen as expensive and energy-intensive to produce, are now witnessing a shift towards more sustainable practices. One prominent approach is the recycling of titanium scrap. By recycling, manufacturers can reduce waste and conserve resources. This not only lowers production costs but also minimizes the environmental impact of mining new titanium.
Moreover, processes like Electron Beam Melting and Selective Laser Melting show promise for sustainability. These methods utilize less material and enable the use of recycled titanium more effectively. This shift aligns with a global emphasis on reducing carbon footprints and achieving greener manufacturing processes.
As we look to the future, integrating sustainability with alloy development will be crucial. Focusing on eco-friendly practices will likely influence regulatory standards and market demands. Therefore, researchers and manufacturers must adapt to these evolving trends to remain competitive.
The End
The importance of the conclusion within this article is multifaceted. It encapsulates the core findings on titanium alloys, while also drawing attention to their implications across various industries. By summarizing the essential points made throughout the text, the conclusion serves not just as a recap but as a synthesis of knowledge, inviting readers to reflect on what titanium alloys mean for current practices and potential future innovations.
Summary of Key Points
In summation, titanium alloys are distinguished by their unique strength, lightweight nature, and corrosion resistance. Here are the core topics discussed:
- Classification: The differentiation among alpha, beta, and alpha-beta alloys highlights the varied applications based on mechanical properties.
- Mechanical Properties: Key characteristics such as tensile strength and fatigue resistance underline why these materials are integral in aerospace, medical, and automotive sectors.
- Production Methods: Techniques like powder metallurgy and casting processes showcase the ongoing advancements in production capabilities.
- Advantages: The high strength-to-weight ratio and biocompatibility of these alloys cater specifically to demanding industries.
- Challenges: Understanding cost implications and processing difficulties is crucial for market accessibility.
- Future Trends: Innovative developments and sustainable practices are reshaping how these alloys will be utilized moving forward.
Implications for Future Research
The discourse surrounding titanium alloys opens several avenues for future inquiry. Research can aim to:
- Explore new alloy formulations that enhance specific properties tailored for niche applications.
- Investigate sustainable production practices, looking into recycling methods or eco-friendly processes.
- Focus on biomedical applications, given the rising demand for implants that can improve patient outcomes.
- Enhance comprehension of the long-term performance of titanium alloys under various conditions to predict longevity and reliability.