Exploring Ni Steel: Properties, Applications, Innovations

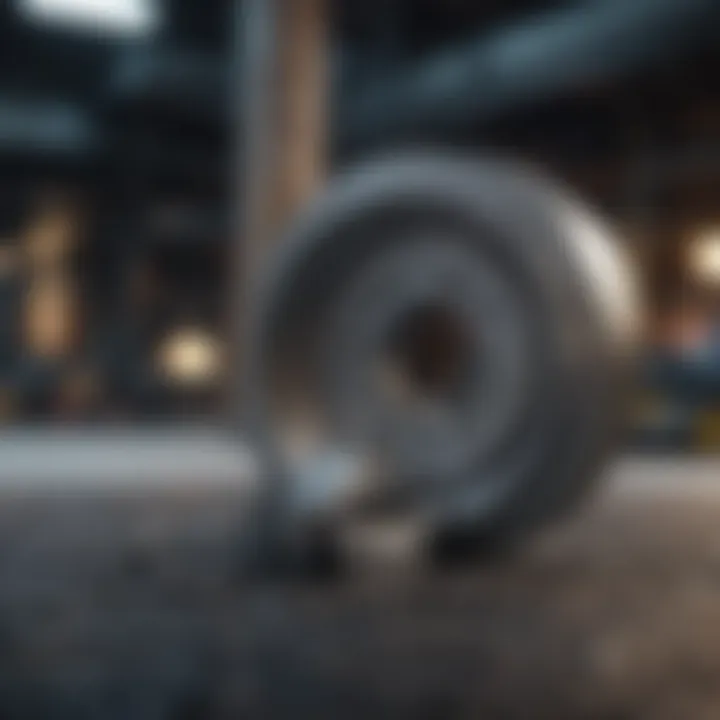
Intro
Nickel steel, an alloy composed primarily of iron and nickel, showcases a remarkable combination of properties that make it invaluable across various industries. Known for its superior strength and corrosion resistance, nickel steel has established itself as an essential material in modern engineering applications. This article explores the key aspects of nickel steel, focusing on its properties, applications, and the innovations emerging within the field.
Understanding the intricacies of nickel steel not only aids in its effective usage but also sheds light on future developments. By examining the composition, manufacturing processes, and applications, readers can gain insights into why this alloy is so widely utilized, particularly in sectors such as aerospace, automotive, and construction.
With advancements in technology and material science, nickel steel is constantly evolving. The ongoing research into its thermal treatment options and mechanical properties presents new opportunities for enhanced performance. As we delve deeper into these topics, this article aims to provide a clear and concise overview that serves both educational and practical purposes.
Intro to Ni Steel
Nickel steel, commonly referred to as Ni steel, possesses unique characteristics that render it essential across various industrial applications. Its ability to withstand harsh environments while maintaining structural integrity is a significant benefit for engineers and manufacturers. This section introduces the concept of Ni steel, outlining its fundamental properties, historical significance, and the evolving innovations surrounding its use.
Definition and Overview
Ni steel is an alloy composed primarily of iron and nickel, with nickel content typically ranging from 3% to 25%. This specific composition gives Ni steel remarkable strength and corrosion resistance, making it suitable for demanding environments. The inclusion of nickel enhances ductility, allowing the steel to deform under stress without fracturing.
There are various grades of nickel steel, often categorized based on the percentage of nickel and the additional alloying elements used. These variations allow for tailored mechanical properties, ensuring optimal performance in specific applications.
In summary, Ni steel is renowned in industries for both its tensile strength and resilience against wear. It stands as a material that balances performance and versatility, making it indispensable in sectors such as aerospace and automotive manufacturing.
Historical Context
The roots of Ni steel trace back to the late 19th century, coinciding with the industrial revolution. Initially, its use was limited, mainly in specialized tools and machinery. However, advancements in metallurgy in the early 20th century facilitated broader applications.
During World War II, the demand for stronger materials surged, bringing Ni steel into the spotlight. Military vehicles, aircraft, and armaments benefited from the material's exceptional strength-to-weight ratio, marking a pivotal moment in its adoption across various sectors.
Post-war, the aerospace and automotive industries began recognizing the advantages of Ni steel, leading to an increased focus on its properties and manufacturing methods. Today, its use encompasses a diverse range of sectors, supported by ongoing research and innovation aimed at enhancing its capabilities further.
"Nickel steel has evolved alongside technological advancements, reflecting both the needs of the present and the possibilities of the future."
This ongoing evolution signifies that Ni steel will continue to play a major role in modern engineering and technology.
Composition of Ni Steel
The composition of nickel steel is critical to its performance and application across various industries. The blend of nickel with iron and other elements bestows unique properties that define its strength, ductility, and corrosion resistance. Understanding the specific composition is essential not only from a material science perspective but also for practical applications in various engineering fields.
Nickel Content
Nickel is the primary alloying element in ni steel, typically comprising about 3% to 20% of the overall composition. This addition significantly influences the mechanical properties of the alloy. Nickel enhances toughness and improves the ductility of steel, making it less likely to fracture under stress. The presence of nickel also enhances the alloy's resistance to corrosion and oxidation, which is especially important in demanding environments such as marine applications or chemical processing.
Moreover, nickel contributes to the stability of austenite structure at higher temperatures. This stability is crucial during heat treatments, allowing for the production of desired mechanical properties. However, the level of nickel must be carefully controlled, as excessive amounts can lead to issues such as reduced machinability and increased cost.
Other Alloying Elements
While nickel is paramount, other elements are often included in the composition of ni steel to optimize specific characteristics. Common alloying elements include:
- Chromium: Enhances hardness and wear resistance.
- Manganese: Improves hardenability and tensile strength.
- Silicon: Increases resistance to oxidation at high temperatures.
- Molybdenum: Provides additional strength at elevated temperatures and enhances corrosion resistance.
These elements each play a role in fine-tuning the properties of nickel steel, allowing metallurgists to tailor the alloy for its intended application. For instance, a mixture with increased chromium may be more suitable for high-stress components in the aerospace sector.
Chemical and Physical Properties
The chemical and physical properties of nickel steel are a direct result of its composition. The following characteristics are worth noting:
- Corrosion Resistance: The combination of nickel and chrome promotes resistance to a variety of corrosive environments. This is vital in industries where exposure to harsh chemicals is a concern.
- High Strength: The alloy exhibits impressive tensile strength due to its unique microstructure, especially after thermal treatments which can further enhance these properties.
- Ductility: Nickel steel's ability to deform under tensile stress without breaking is crucial for applications where flexibility is required.
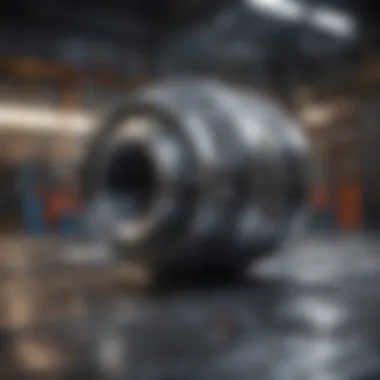
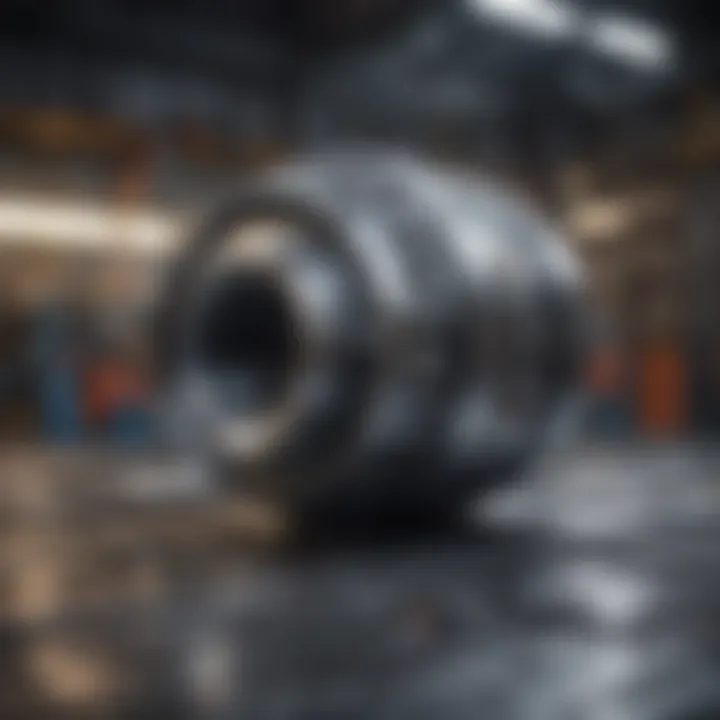
"The successful application of nickel steel depends significantly on its composition and the properties derived from it."
In summary, the composition of nickel steel not only defines its inherent properties but also governs its effectiveness in various applications, from aerospace to automotive and beyond. Understanding these nuances is essential for professionals working with this versatile alloy.
Manufacturing Processes
The manufacturing processes of nickel steel are essential for its final properties and applications. These processes dictate the mechanical characteristics, quality, and reliability of the resulting alloy. Understanding how Ni steel is produced, processed, and formed provides insights into its versatility across various industries. Each step must be carefully executed to ensure the material meets rigorous standards of performance and safety.
Extraction and Processing of Raw Materials
The first step in creating nickel steel involves the extraction of raw materials. Nickel, iron, and other alloying elements must be sourced from natural deposits or recycled materials. The extraction can be through mining methods, such as open-pit or underground mining.
After extraction, the raw materials undergo several processing steps:
- Crushing and Grinding: This is to break down the ore into a manageable size for further processing.
- Concentration: This step separates nickel from other minerals, usually done through flotation or magnetic separation methods.
- Refining: The concentrated nickel undergoes additional processing for purity. This can involve smelting, leaching, or electrolysis.
Attention to detail in these initial processes ensures that the high-quality nickel is stanched for the subsequent steps in alloy production. The purity of nickel significantly influences the mechanical properties, corrosion resistance, and overall performance of Ni steel.
Melting and Alloying Techniques
Once the materials are prepared, the next phase is melting and alloying. This process often occurs in an electric arc furnace, which allows for precise temperature control. The primary steps include:
- Melting the Base Material: Iron is the main component and is melted first to form a molten pool.
- Addition of Nickel and Other Elements: Nickel, along with other elements like chromium, molybdenum, and manganese, is introduced. This requires careful calculation to maintain the desired composition.
- Homogenization: The mixture is stirred to ensure that the alloying elements are evenly distributed throughout the molten steel.
The melting and alloying techniques are crucial as they determine the alloy's final chemical structure. Any variation in composition can lead to significant differences in performance. The process requires a high degree of control to create a product that meets the specific requirements of the application it is intended for.
Casting and Forming Methods
The final stage in manufacturing is casting and forming the nickel steel into usable shapes. This can include a variety of methods such as:
- Casting: The molten steel is poured into molds to form ingots or other shapes. Different casting methods, like sand casting or investment casting, can be used depending on the desired complexity and finish.
- Rolling: Once cooled, the cast materials can be reheated and rolled into sheets, plates, or bars. This process improves material strength and flexibility.
- Forging: Involves applying compressive forces to shape the steel. This helps refine the grain structure, enhancing toughness and overall durability.
Each forming method carries its own advantages and disadvantages. For example, forging typically leads to better mechanical properties than casting. Ultimately, the choice of method depends on the specific requirements of the application and desired characteristics of the finished product.
The manufacturing processes of nickel steel play a pivotal role in determining its properties, emphasizing the need for precision and care at every step.
Mechanical Properties of Ni Steel
The mechanical properties of Ni steel are crucial for understanding its behavior in various applications. These properties directly affect the performance, longevity, and reliability of components made from this alloy. High tensile strength and good ductility contribute to its effectiveness in extreme conditions, while hardness and toughness enhance its resistance to wear and impact. Recognizing these traits aids designers and engineers in selecting the appropriate material for specific projects. Additionally, fatigue resistance is essential in applications where the material faces repeated stress over time.
Tensile Strength and Ductility
Tensile strength and ductility are two of the most important mechanical properties of nickel steel. Tensile strength defines how much pulling stress the material can withstand before failing. Ni steel typically exhibits high tensile strength, making it suitable for structures that must bear heavy loads. This property is vital in industries such as construction and automotive, where safety and durability are paramount.
Ductility, on the other hand, measures how much a material can be stretched without breaking. Ni steel shows a remarkable ability to deform under stress instead of fracturing, ensuring that components can absorb shock and distribute loads evenly. This attribute allows for more complex designs without the risk of sudden failures. Together, these properties make Ni steel highly advantageous in applications requiring resilience and performance under high-stress conditions.
Hardness and Toughness
Hardness and toughness are also essential properties of Ni steel. Hardness refers to a material's resistance to deformation, particularly permanent ones like scratching and indentation. Ni steel often has a high hardness level, which enhances its wear resistance. This makes it particularly useful in applications such as cutting tools and bearings, where contact with abrasive materials is common.
Toughness, however, describes a material's ability to absorb energy and deform plastically without fracturing. Ni steel maintains an excellent balance between hardness and toughness. While hard materials can be brittle, Ni steel's toughness ensures it can withstand impacts and sudden forces. This combination is vital in applications such as machinery parts and structural components, where both wear resistance and impact strength are necessary.
Fatigue Resistance
Fatigue resistance is a critical consideration for materials used in dynamic applications. It measures how well a material can withstand cyclical loading and the potential for failure after repeated stress. Ni steel performs exceptionally well in this regard.
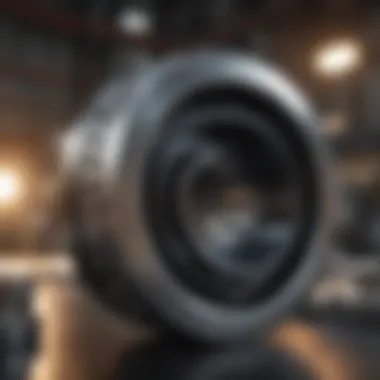
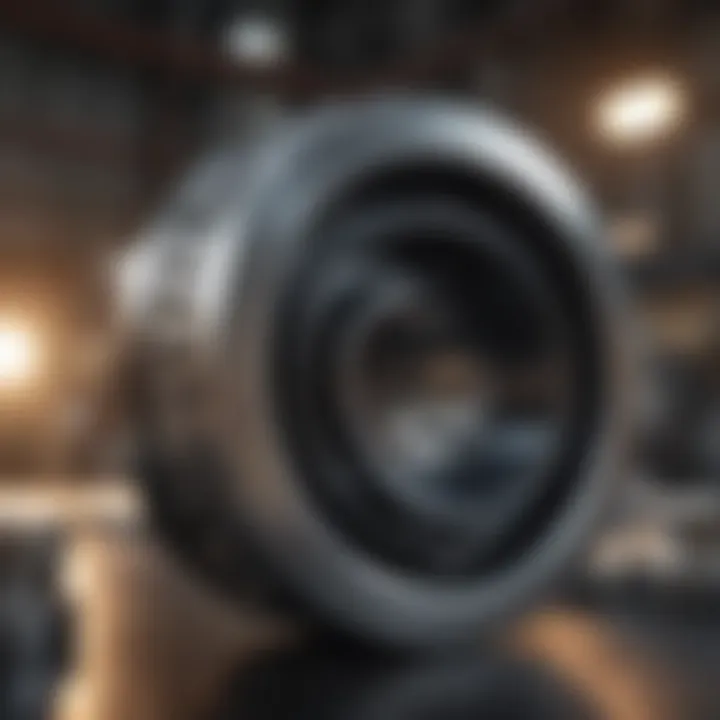
This is largely due to its composition and microstructural characteristics. The inclusion of nickel contributes to a more uniform distribution of stress, reducing the likelihood of cracks forming under cyclic loads. For industries like aerospace and automotive, where components are subjected to continuous stress and fatigue, the fatigue resistance of Ni steel is a major asset. It allows for longer service life and improved safety margins in critical applications.
"The mechanical properties of Ni steel define its versatility and effectiveness across a broad range of applications. Understanding these properties is essential for anyone working with this alloy."
Thermal Treatments and Heat Treatments
Thermal treatments and heat treatments are crucial in the ni steel production process. These methods enhance the mechanical properties of the alloy, ensuring its suitability for demanding applications. Heat treatments involve controlled heating and cooling cycles to manipulate the metal's microstructure. These changes can significantly alter properties like hardness, ductility, and strength. The purpose of using thermal treatments in ni steel is not just to improve these properties, but to optimize performance in various environments and applications.
Annealing Processes
Annealing is a heat treatment technique designed to relieve internal stresses in ni steel, enhance ductility and improve toughness. This process involves heating the alloy to a specified temperature, usually between 550 and 850 degrees Celsius. It is then held at this temperature for a predetermined time before cooling.
This treatment results in several benefits:
- Enhanced Ductility: The process increases the material's ability to deform without breaking.
- Reduced Hardness: Annealing typically softens the steel, making it easier to machine or form into desired shapes.
- Stress Relief: Removing internal stresses helps prevent warping or cracking during later processing steps.
Considerations for the annealing process include the precise temperature and time control to avoid over-softening the material or failing to relieve stress adequately. Additionally, different grades of ni steel may require unique annealing conditions to achieve optimal performance.
Quenching and Tempering
Quenching and tempering are two interconnected heat treatment processes. Quenching involves rapidly cooling the ni steel, usually in water or oil, from a high temperature. This rapid cooling transforms the material's microstructure, typically producing a harder but more brittle state.
Once quenched, tempering follows. This involves re-heating the steel to a lower temperature, around 200 to 600 degrees Celsius, and then cooling it again. The tempering process has several advantages:
- Increased Toughness: Tempering significantly improves toughness without compromising hardness.
- Control of Hardness: The final hardness of the material can be tailored by adjusting the tempering temperature and duration.
- Prevention of Brittle Fracture: By reducing internal stresses developed during quenching, tempering lowers the risk of brittle failure.
Understanding the nuances of quenching and tempering is crucial for engineers. They need to select the appropriate method based on the specific application of the ni steel, ensuring that the end product meets the required performance standards.
"The right heat treatment process not only affects the final properties of ni steel but also its long-term performance in the field."
Through a careful consideration of these thermal and heat treatments, manufacturers can harness the full potential of ni steel, pushing the boundaries of its applications.
Applications of Ni Steel
Nickel steel is a versatile alloy with a broad range of applications across several industries. Its unique properties, which combine remarkable strength with corrosion resistance, make it highly valuable in demanding environments. Understanding the applications of Ni steel is vital, as it not only showcases how this material serves various sectors but also highlights the ongoing innovations in alloy technologies.
Aerospace Industry
In the aerospace sector, Ni steel plays a critical role. The materials used in this industry must withstand extreme conditions, including high temperatures and varying pressures. Using nickel steel allows for the creation of lightweight yet durable components. These can include various engine parts, structural frameworks, and even fasteners. The alloy's strength-to-weight ratio is especially advantageous, as it helps improve fuel efficiency while maintaining safety standards.
Furthermore, the resistance to fatigue and stress corrosion makes Ni steel an ideal candidate for components that face repeated loading cycles. Manufacturers invest heavily in research to enhance the performance of Ni steel in aerospace applications. Recent developments focus on combining nickel steel with other materials to formulate even more robust solutions.
Automotive Sector
The automotive industry also significantly benefits from the properties of Ni steel. Auto manufacturers utilize this alloy for producing critical components such as axles, gears, and frames. The high tensile strength of Ni steel allows for the lightweight construction of vehicles without sacrificing structural integrity. This is particularly relevant given the industry's push towards energy-efficient models.
Additionally, nickel steel's toughness contributes to overall safety in design. In crash tests, parts made from this alloy have shown superior performance under impact, reducing the risk of catastrophic failure. As automakers explore electric and hybrid vehicles, innovations in Ni steel production aim to create batteries and supporting structures that leverage the alloy's favorable properties.
Construction and Infrastructure
Ni steel's application in construction and infrastructure is equally noteworthy. It is employed in the fabrication of beams, columns, and reinforcements in buildings and bridges. Its durability and strength allow for longer spans and higher loads, which can lead to more ambitious architectural designs.
Considerations regarding corrosion resistance are paramount in structural applications. Buildings located in coastal areas or regions with heavy rainfall can benefit from the protective properties of nickel steel. In challenging climates, the longevity offered by Ni steel leads to lower maintenance costs over time.
Moreover, with sustainability taking center stage in construction practices, Ni steel aligns well with these initiatives. Integrating advanced alloys can lead to reduced resource consumption and energy efficiency during both production and usage stages.
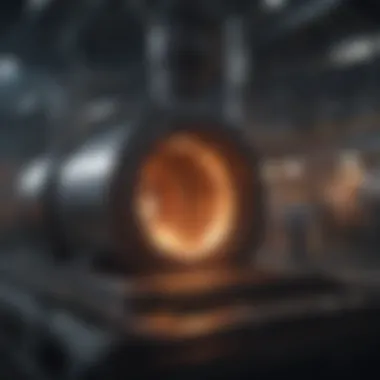
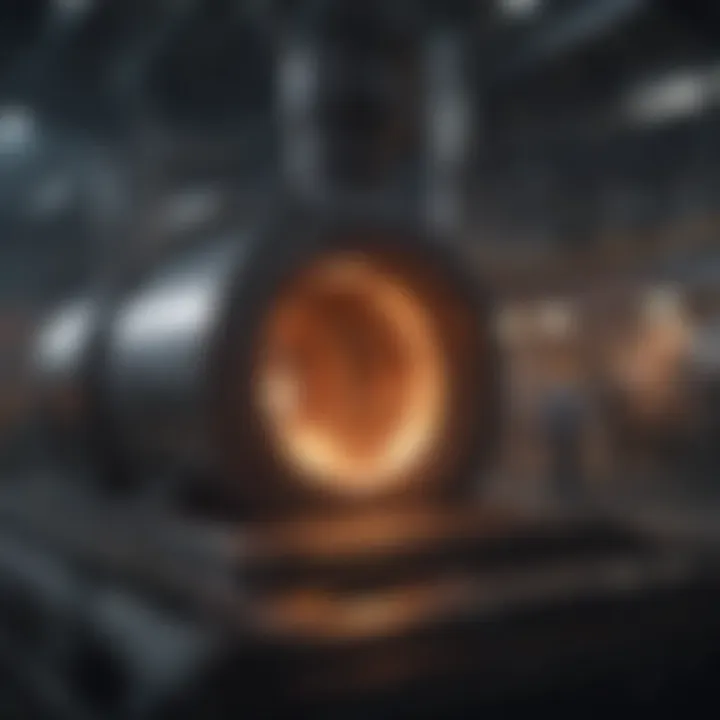
Ni steel provides essential properties that significantly enhance the performance, safety, and sustainability of various applications across key industries.
In summary, the applications of Ni steel across aerospace, automotive, and construction sectors underline its importance in modern engineering. Continuous innovations in the alloy not only address current challenges, such as environmental considerations, but also pave the way for new capabilities and improvements in these vital industries.
Research and Innovations in Ni Steel
Research and innovations in ni steel are crucial for enhancing its performance and meeting the demands of various industries. As technology progresses, industries seek materials that provide not just strength but also sustainability, efficiency, and versatility. Ni steel has long been celebrated for its excellent mechanical properties, but continuous research is needed to optimize its characteristics and broaden its application scope.
The importance of investigating new formulations and processing methods can lead to significant advancements in performance. Innovations can address challenges such as producing lighter structures or improving corrosion resistance. Enhanced properties not only contribute to safer and more reliable products but also can have a profound economic impact for manufacturers and users alike.
Recent Developments
In recent years, there have been several notable developments in the field of ni steel research.
- Advanced Alloys: Researchers are experimenting with varying nickel content and integrating other elements. These newer alloys show improvements in durability and thermal resistance.
- Eco-Friendly Manufacturing: The industry is exploring greener production methods. Techniques that reduce waste and energy consumption are gaining traction, aligning with global sustainability goals.
- Additive Manufacturing: The integration of 3D printing technology with ni steel has opened new possibilities. This method allows for intricate designs and tailored properties, which are not easily achievable through traditional methods.
Such developments provide the foundation for more efficient tools and components, critical in sectors like aerospace and automotive.
Future Prospects
The future of ni steel holds numerous prospects driven by ongoing research and innovations.
- Smart Materials: Integrating sensor technologies into ni steel could lead to smart materials that respond to environmental changes or structural stress. This could vastly increase safety and maintenance efficiency.
- Increased Application Fields: As electrical components evolve, ni steel could find more uses in energy applications, such as in batteries or magnetic devices, due to its electrical properties.
- Global Demand Growth: With continued improvements, the demand for ni steel is expected to rise. The potential for lighter, stronger materials makes it ideal for modern engineering challenges.
"Innovation in ni steel is not just about maintaining strength; it is about anticipating future needs and evolving accordingly."
Overall, the ongoing research and innovations in ni steel represent not just a response to current challenges, but a proactive endeavor to lead the future of materials science.
Challenges Faced by Ni Steel Industry
Environmental Concerns
The nickel steel industry has faced increasing scrutiny regarding its impact on the environment. The major issue stems from the mining and processing of nickel and other raw materials. These processes can result in land degradation, deforestation, and biodiversity loss, leading to significant ecological disturbances.
Moreover, emissions from nickel processing plants contribute to air pollution. Chemicals used in extraction, such as sulfur dioxide, pose risks to both health and environment. There is also the challenge of contaminating water sources due to runoff from mining sites. As industries and consumers grow more conscious of sustainable practices, the demand for environmentally friendly production methods in nickel steel manufacturing is intensifying.
To address these challenges, industry stakeholders must consider adopting greener technologies. This approach can reduce hazardous waste and limit emissions significantly. The development and implementation of cleaner extraction methods could alleviate some of these environmental pressures, making nickel steel production more sustainable.
Economic Factors
Economic considerations are vital for the nickel steel industry. Fluctuating prices of raw materials, including nickel, influence production costs. When prices soar, manufacturers may face reduced profit margins, impacting their competitiveness in the market. Additionally, the heavy investment required for maintaining the production facilities can strain financial resources, especially during periods of economic downturn.
The global demand for nickel steel has been rapidly rising due to its applications in various sectors, but this demand comes with complexities. For example, supply chain disruptions or geopolitical tensions can lead to scarcity and increased costs, further complicating the economic landscape.
Therefore, companies must adapt to these changing circumstances by diversifying their supply sources and improving operational efficiencies. Seeking innovation in production techniques may also reduce dependency on expensive raw materials and lead to more stable pricing.
Ending
In summary, the significance of concluding the exploration of nickel steel cannot be overstated. The comprehensive analysis throughout this article encapsulates the extraordinary qualities of nickel steel, its applications across various industries, and the ongoing innovations that shape its future. Understanding the properties and challenges associated with nickel steel illuminates its relevance in modern engineering, guiding professionals and students alike in making informed decisions and predictions.
Summary of Key Points
- Nickel steel is a vital alloy with exceptional strength, durability, and versatility.
- Its composition, primarily characterized by nickel content and other alloying elements, directly influences its mechanical and thermal properties.
- Various manufacturing processes, including melting and casting, play crucial roles in producing nickel steel of different grades.
- The material finds extensive use in aerospace, automotive, and construction sectors.
- Recent research and innovations suggest promising developments in its application and efficiency.
- Challenges, such as environmental concerns and economic factors, must be addressed for a sustainable future.
Final Thoughts
Concluding this exploration of nickel steel leads to a broader understanding of its importance in technology and industry. As innovations continue to emerge, the potential for enhancing the uses of nickel steel also grows. The key takeaway is the necessity to remain informed about the advancements and challenges this material faces, ensuring its optimal utilization in sustainable, efficient ways moving forward.
"Nickel steel serves not just as a material, but as a foundation for the future of engineering."
This refined perspective on nickel steel, maintained through precise analysis and critical insight, serves as a guide for scholars and professionals. It encourages the ongoing study of its properties and applications to ensure that the potential of nickel steel is fully realized.