Exploring Machine Vision Measurement Accuracy
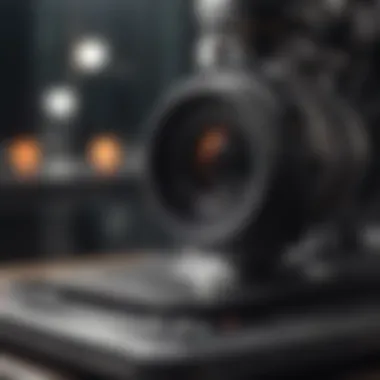
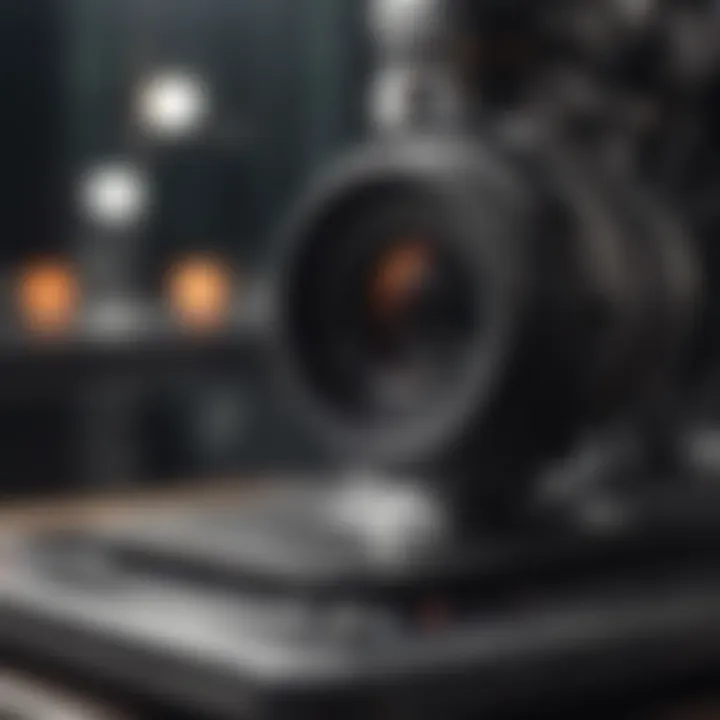
Intro
Measurement accuracy in machine vision systems is a crucial factor that influences the effectiveness of various applications, ranging from manufacturing to quality control. As industries increasingly rely on automation and machine vision technology, understanding the principles and factors affecting measurement accuracy becomes essential. This section briefly outlines the significance of this topic and introduces the main elements that will be discussed throughout the article.
Machine vision systems operate by capturing images of objects and processing these images to extract meaningful data. The ability to measure dimensions, positions, and other characteristics of objects precisely is necessary for ensuring quality and consistency in products. However, achieving high levels of accuracy is not straightforward and can be affected by multiple factors, including lighting conditions, camera resolution, and calibration techniques.
In this narrative, we will explore various aspects of machine vision measurement accuracy, delve into calibration methods, and examine how advancements in technology continue to improve performance. Through case studies and examples, the article will illustrate both the benefits of implementing machine vision systems and the challenges that may arise.
By providing a comprehensive exploration of this subject, the aim is to facilitate a nuanced understanding of measurement accuracy within machine vision among students, educators, researchers, and professionals in the field.
Prolusion to Machine Vision
Machine vision represents a significant leap in automation and precision across various industries. It involves the use of computer systems to interpret visual information from the environment, allowing machines to understand and react to their surroundings. The relevance of machine vision measurement accuracy cannot be overstated, as it plays a critical role in ensuring that systems operate efficiently and effectively. Accurate measurements can drastically reduce errors in manufacturing and quality control processes.
This introduction aims to outline the essential elements of machine vision. First, it emphasizes the need for precision in measurement. Inaccuracies might lead to substantial waste, rework, or even safety hazards. Furthermore, understanding machine vision can benefit not only manufacturing but also sectors such as healthcare, transportation, and agriculture through improved inspection methods and data analysis. The interplay of technology and measurement techniques in machine vision sets a foundation for advances in automation.
Defining Machine Vision
Machine vision can be defined as a technology that enables machines to interpret and analyze visual data. This is facilitated through different components such as cameras, sensors, and software. In essence, machine vision enables a machine to mimic the visual perception of human beings, but with added advantages of speed and accuracy. It is not just about capturing images; it's also about processing them to extract meaningful information. This capability allows for tasks such as object detection, classification, and measurement, which are vital in various applications.
Historical Development
The historical development of machine vision spans several decades, reflecting the evolution of technology and the increasing demand for automation. Initially, basic image processing techniques emerged in the 1960s. These early methods focused primarily on edge detection and basic object recognition. Over time, the introduction of sophisticated algorithms and computing power paved the way for advanced image analysis.
By the 1980s, machine vision started to gain traction in industrial applications, particularly in quality control within manufacturing. The integration of digital cameras and improved lighting techniques further enhanced measurement capabilities. Today, machine vision systems are integral to smart manufacturing and Industry 4.0 initiatives. The blend of machine learning and artificial intelligence with traditional machine vision will likely continue shaping its future.
Fundamental Principles of Measurement Accuracy
The concept of measurement accuracy is pivotal in the domain of machine vision. Understanding these principles lays the foundation for reliable and valid measurements, which are essential in various practical applications. Accuracy in machine vision impacts both production quality and operational efficiency. Thus, the principles that govern measurement accuracy deserve meticulous examination.
Geometric Measurement
Geometric measurement refers to the evaluation of physical dimensions and spatial properties. This includes length, width, height, and angles. In machine vision systems, geometric measurements are carried out through the use of specialized cameras and advanced algorithms. The importance of geometric measurement lies in its ability to ensure that components meet design specifications. This is vital in industries like automotive and aerospace, where even slight deviations can lead to catastrophic failures.
Factors such as lens distortion and camera calibration significantly influence geometric measurement accuracy. Errors may occur due to misalignment of the camera or improper lighting conditions. Hence, understanding these factors is crucial for enhancing precision.
To improve accuracy, the following considerations should be taken into account:
- Calibration and Setup: Regular calibration routines help in mitigating errors.
- Lighting: Correct lighting helps in minimizing shadows and reflections.
- Environment: Temperature and humidity can affect sensor performance and measurement precision.
Photometric Measurement
Photometric measurement focuses on the analysis of light and its interaction with surfaces. This involves quantifying attributes such as brightness, color, and contrast. In machine vision applications, photometric measurements are essential for tasks like quality control in manufacturing processes, where the visual appearance of a product plays a significant role.
The accuracy of photometric measurements is affected by various considerations. Sensor sensitivity and noise levels can impact the reliability of light measurements. Moreover, the calibration of photometric devices is crucial to ensure that measurements reflect true values.
Key elements to improve photometric accuracy include:
- Sensor Selection: Choosing the right sensor type for specific applications influences measurement accuracy.
- Calibration: Frequent calibration ensures that the equipment provides consistent and reliable readings.
- Environmental Factors: Control of external light sources is necessary to prevent interference and ensure accurate readings.
"In machine vision, precise measurement is not just a goal; it is a necessity for operational excellence and product reliability."
By exploring geometric and photometric measurement, one can grasp the fundamental principles that underlie accurate machine vision systems. This understanding is essential for implementing effective solutions across various industries.
Components of Machine Vision Systems
In the pursuit of precision in machine vision measurement, the components that make up the system play a foundational role. Understanding these components is essential as they directly impact the system's capability to deliver accurate and reliable measurements. Each element not only serves a unique function but also interacts with the others, establishing a cohesive ecosystem that drives the effectiveness of machine vision applications.
Cameras and Sensors
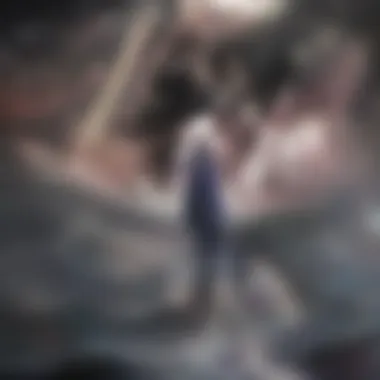
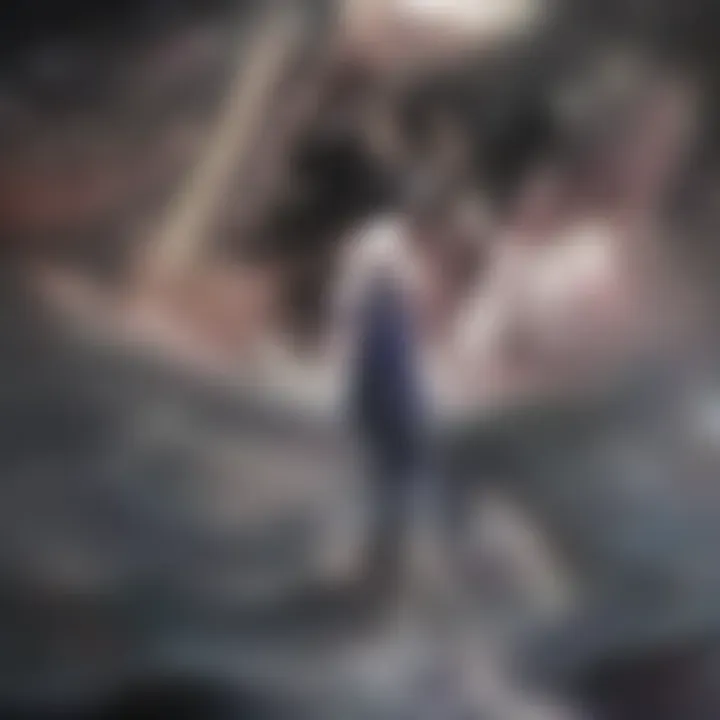
Cameras and sensors are the eyes of any machine vision system. They capture images and convert them into digital data for processing. Choosing the right camera is crucial as it significantly influences image quality and, consequently, measurement accuracy. Various types of cameras exist, including area scan cameras and line scan cameras.
Area scan cameras are suitable for static scenes and are used in applications where the entire field of view must be captured simultaneously. On the other hand, line scan cameras are ideal for high-speed applications or continuous productions, as they capture one line of pixels at a time.
Sensors in these cameras determine how well the camera can differentiate between various intensities and colors, directly affecting the quality of the captured images. With advances in technology, sensors have improved in sensitivity and dynamic range, leading to more accurate measurements in varying conditions. The alignment and calibration of the cameras also need precise management to ensure the system delivers consistent results.
Lighting Systems
Lighting is another critical component that often is overlooked yet vital for successful machine vision. Proper lighting enhances image contrast and highlights features that need measurement, improving the results of the capture. Different applications may require distinct lighting techniques, such as backlighting, front lighting, or even structured light. Each method serves a specific purpose and can dramatically affect the visible details in the captured images.
Key considerations in selecting lighting include the wavelength of light, intensity, and the positioning of the light sources. Consistent illumination helps in reducing shadows and reflections that can obscure critical details of the objects being inspected. With the advent of advanced lighting technologies, such as LED and laser-based systems, achieving optimal lighting conditions has become more efficient and customizable.
Processing Hardware and Software
Processing hardware and software bring together the functions of cameras and sensors and interpret the data collected. This component is responsible for analyzing images using algorithms to extract meaningful insights. The choice of processing hardware hinges on the complexity of tasks and the volume of images processed.
Graphic Processing Units (GPUs) are commonly utilized due to their ability to handle parallel processing tasks effectively, which is crucial for real-time applications. The software employed must be capable of implementing advanced algorithms, including machine learning techniques, to enhance measurement accuracy.
Moreover, it’s essential to consider integration with other systems, as this determines the flexibility and scalability of the machine vision solution. Processing capabilities can dramatically impact how quickly data is interpreted and how accurate measurements are derived.
"The effectiveness of a machine vision system hinges on its components working in unison to achieve precision in measurement."
Factors Influencing Measurement Accuracy
Measurement accuracy in machine vision systems is influenced by multiple factors that can either enhance or hinder performance. Understanding these elements is crucial for researchers, educators, and professionals who operate these systems. Factors impacting measurement accuracy include environmental conditions, calibration techniques, and image resolution and quality.
Environmental Conditions
Environmental conditions play a significant role in the overall accuracy of machine vision systems. Variations in lighting, temperature, and humidity can dramatically affect the results. For instance, highly reflective surfaces or shadows can distort the captured images. These distortions can lead to erroneous measurements that compromise the system's reliability.
- Lighting Variability: Adequate and consistent lighting is essential. Ambient light variations can introduce noise, resulting in unclear images. Employing controlled lighting can mitigate this issue, ensuring consistent image quality regardless of external conditions.
- Temperature Changes: Temperature fluctuations can impact camera sensors and lenses. Cameras may behave differently at extreme temperatures, leading to shifts in focus or lens distortion, affecting precision.
In summary, maintaining optimal environmental conditions can significantly enhance the accuracy of machine vision measurement, ensuring reliable and consistent results.
Calibration Techniques
Calibration techniques are fundamental to achieving the desired measurement accuracy in machine vision systems. Proper calibration ensures that the system accurately interprets input data and translates it into actionable information.
- Manual Calibration Methods:
These methods involve physically adjusting the system components based on a standard reference. This process can be time-consuming but allows for a customized setup, often producing high accuracy results. - Automated Calibration Solutions:
With advancements in technology, automated calibration solutions are becoming popular. These systems utilize algorithms to adjust and refine parameters in real time, reducing human error and increasing efficiency.
"Calibration is an essential element that transforms a machine vision system from a simple camera setup to a precise measurement tool."
Effectively implementing calibration techniques is vital for optimizing measurement accuracy across various applications.
Image Resolution and Quality
The resolution and quality of images captured by machine vision systems directly affect their measurement accuracy. High-resolution images provide more details, which are critical for precise analyses.
- Importance of Resolution:
In applications requiring high precision, such as quality control in manufacturing, high image resolution is necessary. Low-resolution images may omit important details, leading to misinterpretations. - Quality of Components:
The quality of cameras and lenses also contributes to the images taken. High-quality optics ensure clarity and reduce distortions, critical for accurate measurements.
Optimal image resolution and quality are crucial for the overall performance of machine vision systems. When these two factors are aligned harmoniously, they significantly enhance the system's measurement capabilities.
Calibration Techniques in Machine Vision
Calibration techniques play a significant role in ensuring measurement accuracy within machine vision systems. Proper calibration ensures that the data obtained from these systems is reliable and accurate. Calibration adjustments help to align the measured values with known references, which is particularly crucial in industrial applications where precision is paramount. The importance of these techniques lies not just in enhancing accuracy, but also in the adaptability and efficiency they offer in various operating environments. By regularly implementing calibration procedures, organizations can maintain optimal performance and accuracy in their machine vision systems.
Industrial Calibration Methods
Industrial calibration methods refer to the traditional techniques used to align and verify the performance of machine vision systems within industrial settings. Common approaches include:
- Rigid Body Calibration: This involves the use of precision fixtures to obtain geometric references which can help set up the system accurately.
- Checkerboard Calibration: Using a checkerboard pattern, this method calculates the camera parameters by capturing images from multiple angles. It determines lens distortion and helps achieve accurate depth information.
- 2D Target Calibration: This method utilizes flat 2D targets which have known dimensions to define a transformation between the image data captured and the actual size in the real world.
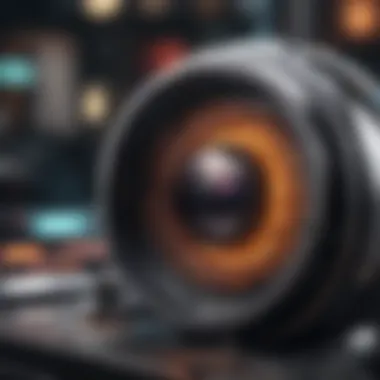
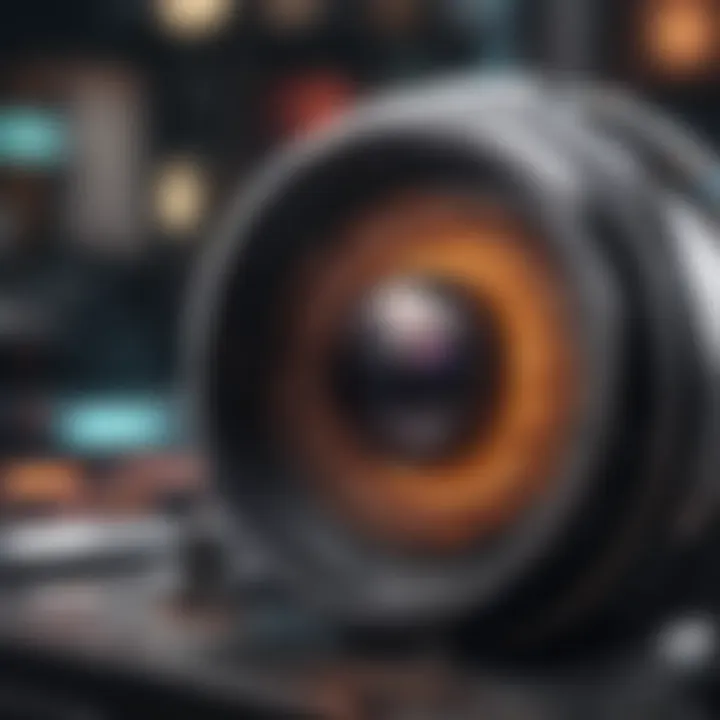
Industrial calibration methods provide the stability and reliability required to manage complex manufacturing tasks. These methods require skilled personnel to execute and monitor accuracy levels regularly.
Automated Calibration Solutions
Automated calibration solutions present a modern alternative to traditional calibration methods. They leverage advanced technologies to facilitate real-time calibration processes. Such solutions can include:
- Self-Calibration Algorithms: These algorithms enable machines to automatically correct themselves by analyzing incoming data and adjusting based on pre-set parameters.
- Robotic Systems: Robots equipped with vision systems can perform calibration tasks by themselves, reducing human error and increasing efficiency.
- Software Tools: Sophisticated software can analyze calibration results and make recommendations for adjustments without significant human intervention.
Automated calibration allows faster adjustments and is less prone to human error. This leads to less downtime and increased overall productivity. Industries that depend on precise and real-time measurements benefit immensely from these solutions.
"Calibration is not just about accuracy; it is about creating a consistent framework for measurements across various processes."
The combination of these industrial methods and automated solutions strengthens the framework of machine vision measurement accuracy, thereby enhancing system reliability and operational efficiency.
Advancements in Machine Vision Technology
In the intricate field of machine vision, advancements in technology play a pivotal role in enhancing measurement accuracy. Technology isn't static; it is constantly evolving. These innovations are reshaping the landscape of machine vision systems and positively impacting various industries. Emphasizing new tools and methods helps in overcoming challenges faced in measurements. As we delve into significant advancements, two key elements stand out: deep learning and AI integration, and real-time processing capabilities.
Deep Learning and AI Integration
Deep learning has emerged as a transformative force in machine vision. This subgroup of machine learning allows systems to analyze large sets of data with increased accuracy, improving object recognition and classification. AI algorithms learn from the data, refine their predictions, and adapt to new situations without explicit programming. This enables machine vision systems to operate effectively in complex environments where traditional programming might falter.
The benefits of integrating deep learning into machine vision are manifold:
- Higher Accuracy: AI can achieve levels of recognition and analysis that often surpass human capabilities.
- Versatility: Deep learning is applicable across diverse sectors, including healthcare, manufacturing, and retail.
- Continuous Improvement: As more data is processed, models can learn and improve accuracy over time.
Understanding how to harness this potential is crucial for practitioners in the field. It demands not only technical expertise but also foresight into how developments in AI can be utilized in specific applications.
Real-Time Processing Capabilities
Another significant advancement in machine vision technology is the enhancement of real-time processing capabilities. This ability to analyze and respond to visual data as it happens is critical for numerous applications. Industries that require immediate feedback from machine vision systems benefit greatly from fast and efficient data processing.
Benefits of real-time processing include:
- Increased Efficiency: Machinery can make decisions on-the-fly, optimizing production processes.
- Immediate Quality Control: Defects can be identified and addressed promptly, reducing wastage and ensuring product quality.
- Enhanced Safety: Systems can respond instantly to hazards, improving workplace safety for personnel.
Real-time analysis is no longer a luxury; it is a necessity for industries aiming to remain competitive and responsive.
As technology advances, the integration of improved processing capabilities will continue to reshape how we approach measurement accuracy in machine vision. Emphasis on real-time applications ensures that organizations utilize machine vision systems effectively, enhancing their operational output.
Case Studies: Machine Vision Measurement in Action
Case studies play a vital role in understanding how machine vision measurement processes are implemented across various industries. These practical examples illustrate not only the real-world applications of machine vision technology, but also its benefits, challenges, and the strategies used to overcome them. Engaging with specific case studies allows readers to grasp the complexities of implementing machine vision systems and the tangible outcomes they generate in terms of measurement accuracy.
By examining real-life contexts, we can uncover the direct impact of machine vision in enhancing operational efficiencies, improving product quality, and reducing costs. Moreover, case studies provide insights into the integration of advanced technologies like deep learning and AI, offering lessons from both successful implementations and challenges faced.
Manufacturing Applications
In the manufacturing sector, machine vision measurement is crucial. It streamlines processes, enhances accuracy, and improves productivity. One notable case study comes from the automotive industry, where companies like Ford have employed machine vision for assembly line inspection.
Through the use of high-resolution cameras and sophisticated image processing algorithms, Ford can conduct real-time inspections of car parts. This approach allows for quick detection of defects that might otherwise go unnoticed during manual inspections. The advantages here are significant:
- Enhanced accuracy: Machine vision systems can measure dimensions with high precision.
- Increased speed: Automated inspections occur faster than manual processes.
- Cost savings: Reducing defects minimizes waste and rework expenses.
The integration of these systems not only improves quality but also empowers teams to focus on more strategic tasks instead of repetitive inspections.
Quality Control Processes
Quality control is another sphere where machine vision measurement thrives. Case studies in food packaging illustrate this. Companies like Nestlé utilize machine vision to ensure packaging integrity and compliance with safety standards.
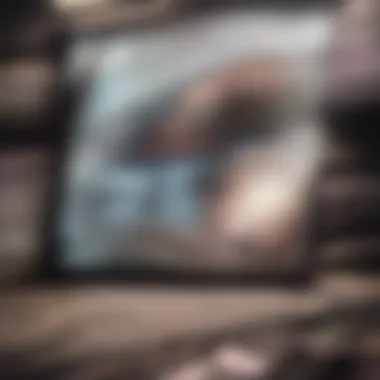
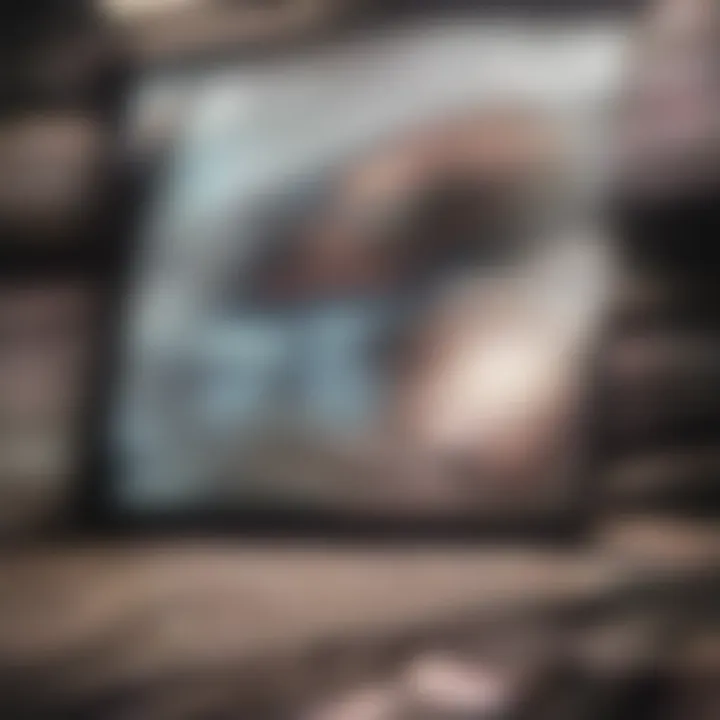
In these applications, machine vision systems verify correct labeling, detect foreign objects, and ensure that packaging is sealed correctly. Some benefits include:
- Consistency: Standardized inspections yield reliable results.
- Traceability: Issues can be traced back to specific batches, facilitating quick corrective actions.
- Regulatory compliance: Automation aids compliance with strict industry regulations.
The emphasis on quality control through machine vision demonstrates its effectiveness in not only safeguarding product quality but also in bolstering consumer trust in brands.
According to a study by the International Journal of Advanced Manufacturing Technology, implementing machine vision can increase quality control efficiency by over 30% across industries.
Navigating through these case studies provides readers a comprehensive view on the practical applications of machine vision measurement accuracy and its pivotal role in industrial settings.
Challenges in Achieving Measurement Accuracy
In the realm of machine vision, measurement accuracy is not merely a desirable feature; it is a fundamental requirement that can have significant implications across various sectors. This accuracy is challenged by multiple factors that affect system performance and the reliability of obtained data. Understanding these challenges helps in developing more robust systems and informs strategic planning in industries dependent on precision measurements.
System Integration Issues
The integration of machine vision systems within existing industrial frameworks often poses a major obstacle. Many companies have established processes that were not designed with contemporary machine vision technologies in mind. Therefore, integrating new systems may disrupt workflow or require substantial modifications to existing setups.
Moreover, compatibility between hardware and software components can lead to integration hurdles. For instance, mismatched sensors and processing units can compromise the quality of measurements, leading to inaccuracies. It is crucial to conduct a thorough assessment of system requirements before deploying machine vision technologies. A lack of proper alignment among components can result in faulty data interpretation, ultimately affecting quality control and product results.
Cost Implications
Cost is another significant factor when considering machine vision measurement accuracy. The initial investment in advanced systems can be substantial. High-resolution cameras, sophisticated lighting solutions, and powerful processing hardware all contribute to a higher budget. Additionally, ongoing costs related to maintenance, training, and possible upgrades should also be taken into account.
However, it is essential to consider the long-term benefits. Improved measurement accuracy through machine vision can lead to reduced waste, enhanced product quality, and higher customer satisfaction. Over time, the costs may offset the initial investments. Therefore, while upfront costs are an important consideration, a broader view of the overall financial impact provides a clearer picture of the fiscal implications of machine vision technologies.
"Addressing integration challenges and understanding cost factors are vital in implementing effective machine vision solutions that emphasize measurement accuracy."
Future Perspectives on Machine Vision Measurement Accuracy
As industries increasingly rely on precision measurement technology, understanding future perspectives on machine vision measurement accuracy becomes crucial. The advancements in this field promise to refine processes and improve productivity across sectors. It is not merely about understanding how current systems function, but also about anticipating how upcoming innovations will reshape measurement practices and their significance in quality assurance and operational efficiency.
Emerging Trends
Several emerging trends are gaining prominence in machine vision measurement accuracy. One notable trend is the integration of artificial intelligence (AI) and machine learning. These technologies enhance the ability to analyze images with greater precision, allowing for real-time adjustments and improved decision-making capabilities. AI algorithms can learn from vast datasets, identifying patterns that lead to more accurate measurements.
Another trend involves the move towards compact and intelligent sensors. Tiny, high-resolution cameras facilitate measurement tasks while being easier to integrate into existing systems. Companies are focusing on enabling these sensors to operate effectively in challenging environments, such as extreme temperatures or varying light conditions. This advancement can significantly expand the usability and accuracy of machine vision solutions.
Additionally, the field is witnessing a growing interest in cloud-based solutions. By harnessing cloud computing, manufacturers can store and analyze large volumes of data generated from machine vision systems. This centralization allows for better data management and easier access to analytical tools, which in turn improves measurement accuracy over time.
Research and Development Directions
The research and development directions in machine vision are aimed at addressing current challenges while preparing for future needs. Key areas of focus include developing novel algorithms that improve measurement accuracy under varying conditions. Researchers are exploring how to make these algorithms more robust against influences like motion blur or lighting changes, which traditionally compromise measurement reliability.
Another significant direction is enhancing user interface and experience. Simplifying the setup process and making operational controls intuitive allows users, regardless of technical background, to leverage complex machine vision systems fully. This user-centric approach can reduce the possibility of errors in measurement, as users can operate the technology without extensive training.
Moreover, a vital aspect of future development is the emphasis on sustainability. Researchers are striving to create more environmentally friendly technologies that consume less power and use recyclable materials. This innovation not only leads to better industry practices but also contributes to the overall advancement in machine vision systems by aligning with global sustainability goals.
In summary, the future of machine vision measurement accuracy looks promising, driven by various trends and research initiatives. Organizations that embrace these advances will likely achieve higher precision and improved operational insights, enabling them to adapt to an ever-evolving market landscape.
Epilogue
In any comprehensive analysis of machine vision measurement accuracy, the conclusion serves a critical purpose. It synthesizes the information presented throughout the article, reinforcing the importance of the discussed topics and highlighting key takeaways for the reader. This section contributes significantly to understanding how all the elements fit together in the broader landscape of machine vision systems.
Recap of Key Points
A summary of essential points can always benefit the reader's retention and comprehension:
- Definition of Machine Vision: Understanding what machine vision entails is foundational. This technology's capacity to process and analyze visual data allows for numerous applications across industries.
- Measurement Methods: Geometric and photometric measurements underpin machine vision accuracy. Each approach has its own set of best practices and technologies that will ultimately impact results.
- Calibration Techniques: Regular calibration remains essential for ensuring accuracy. Different methods exist, including both industrial and automated solutions, which provide flexibility in diverse settings.
- Factors Affecting Accuracy: Environmental conditions, image resolution, and post-processing are critical elements that can alter the precision of measurements. Recognizing these helps in developing robust systems.
- Technological Advancements: The integration of AI and real-time processing has transformed machine vision capabilities. Staying updated on these advancements can offer a competitive edge in any industry.
The Importance of Ongoing Innovation
Ongoing innovation is vital for sustaining the relevance and efficacy of machine vision systems. The rapid pace of technological progress necessitates a commitment to continuous development, ensuring that these systems remain efficient and accurate.
Investment in research and development not only enhances measurement accuracy but also leads to the discovery of new applications. As industries evolve, the demand for precise measurement grows alongside it. Failure to keep up with advancements may result in outdated practices and, ultimately, decreased competitiveness. Thus, fostering an environment that encourages innovation is essential for companies looking to maximize the impact of machine vision technology.
"The future of machine vision lies in its ability to adapt to changing needs and technologies."