Exploring Anti Foaming Oil: Principles and Innovations
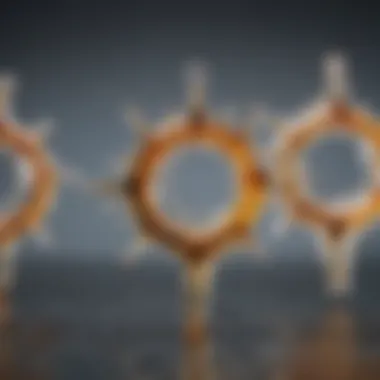

Intro
In various industrial processes, foam can present significant challenges that may hinder efficiency and product quality. Anti foaming oils emerge as essential tools to combat this issue, and understanding their properties, applications, and innovations is critical for both researchers and practitioners.
Foam formation occurs when air or gas is trapped within a liquid, creating a stable structure that can cause obstructions in mechanical systems like pumps and pipelines. Furthermore, excessive foam can lead to contamination in products, particularly in sectors like food and beverage, pharmaceuticals, and petrochemicals. Thus, the presence of effective anti foaming agents is vital.
Anti foaming oils work on the principle of disrupting the foam's stability, often achieved through surface tension reduction and altering the interfacial properties. This article aims to illuminate the various dimensions of anti foaming oils, from their chemical properties to their specific applications across multiple industries.
A thorough guide is not just beneficial for engineers and chemists but also offers invaluable insights for students and academics delving into the fields of material science and chemical engineering. By breaking down complex concepts and highlighting relevant case studies, we can build a bridge between theoretical knowledge and practical implementation.
Through this narrative, we will uncover the mechanisms behind foam control, methods of selecting suitable anti foaming agents, and the environmental implications driving ongoing research in this area. As industries continue to evolve and environmental regulations tighten, continuous innovation in anti foaming technologies must be prioritized.
This article endeavors to equip all readersāstudents, researchers, educators, and industry professionalsāwith a deep understanding of anti foaming oils and their multifaceted role in industrial applications.
Fundamentals of Anti Foaming Oil
Understanding the fundamentals of anti foaming oil is crucial for anyone delving into its applications, whether in industrial scenarios or more specific sectors like pharmaceuticals and food production. The primary function of these oils is to mitigate unwanted foam formation, which can complicate processes and affect product quality. By grasping the basic principles surrounding these oils, stakeholders can make informed decisions about their usage, leading to improved efficiency and cost-effectiveness.
Definition and Properties
Anti foaming oil can be defined as a substance used to inhibit the formation of foam in liquids. Foam, while often an indicator of vigor in processes such as mixing or fermentation, can lead to a host of issues. Foaming can create a barrier that inhibits oxygen transfer in fermentation processes or result in overflow in tanks. The properties of anti foaming oil include low surface tension, which allows it to break the bubbles as they form, and the ability to spread over the liquid's surface quickly. These oils are typically non-toxic and stable under varying temperatures and pH levels, making them suitable for different applications.
Chemical Composition
The composition of anti foaming oils varies significantly but generally includes several types of surfactants. Common ingredients are polysiloxanes, which are silicone-based compounds, and fatty acids derived from natural sources. These emulsions or solutions often contain additives that enhance their effectiveness, such as antioxidants that prolong shelf life or agents designed to improve spreading characteristics. For example, dimethyl polysiloxane is a popular silicone-based anti foaming agent celebrated for its longevity and effectiveness in diverse environments.
It is essential to note that the choice of chemical composition must align with the target application's requirements, factoring in aspects like compatibility with other substances and the environmental impact of the chosen materials.
Mechanisms of Action
Anti foaming oils function primarily by disrupting the formation and stability of foam. When introduced into a foaming solution, these oils reduce the surface tension, which is the essential property that allows bubbles to form. This reduction in surface tension means that as bubbles begin to form, they are less stable, leading them to break apart more easily.
Interestingly, the effectiveness of these oils can vary widely based on several factors, including the liquid's temperature, viscosity, and the nature of the foam. Typically, the introduction of anti foam agents will lead to a decrease in foam volume and an increase in the rate at which foam dissipates.
"Choosing the right anti foaming agent is not just a matter of efficacy; it's about understanding the intricate balance between chemical behavior and the specific process conditions."
In practice, this means thorough testing and evaluation must precede the application of any anti foaming oil, ensuring it aligns well with the production process's unique requirements. Ultimately, mastering these fundamentals not only helps to manage foaming but also enhances overall operational efficiency.
Types of Anti Foaming Agents
Understanding the types of anti foaming agents is crucial to grasping how they effectively mitigate foam across a variety of applications. The choice of anti foaming agent can significantly influence operational efficiency, product quality, and overall performance in industrial processes. Therefore, it's essential to delve into the distinct categories available, alongside their respective advantages and ideal scenarios for application.
Silicone-based Agents
Silicone-based agents stand prominent among anti foaming solutions due to their remarkable stability and effectiveness. These agents typically consist of polydimethylsiloxane compounds, which exhibit low surface tension. This property enhances their ability to spread and penetrate foam structures quickly. As a result, they can eliminate foam more effectively compared to many other types.
The advantages of silicone-based agents include their temperature stability and resistance to oxidation, allowing them to perform well in extreme conditionsāwhether itās high heat in food processing or varying pH levels in chemical applications. However, one must consider the potential for surface residue on certain substrates and the environmental implications of siloxanes, which requires careful selection based on specific use cases.
"Silicone-based agents are the go-to choice for delicate environments, providing reliability and superior foam control, although their environmental concerns can't be brushed aside."
Non-silicone Agents
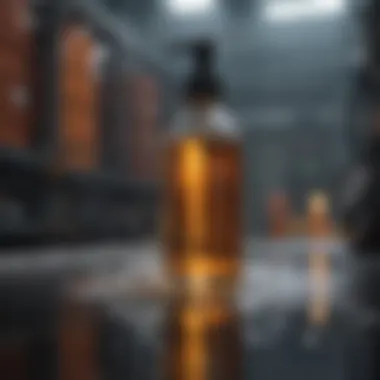

On the other hand, non-silicone agents encompass a broad range of substances, often including organic compounds or fatty acids. These agents can be effective in settings where silicone residues are undesired. They are versatile, serving well in industries like food and beverage, where natural formulations are more favorable.
One significant benefit of non-silicone agents is that they often present fewer environmental concerns while still delivering satisfactory foam control. Furthermore, they can offer cost advantages, depending on the specific agent employed. However, their performance may vary significantly based on the application, necessitating a more informed selection process. Testing and evaluation are essential to ensure they meet the specific demands of the industrial environment.
Natural Alternatives
The rising trend towards sustainability has propelled interest in natural alternatives for anti foaming agents. These often utilize plant-based ingredients or biodegradable compounds. They can effectively reduce foam while also being more acceptable from an environmental standpoint, appealing to organizations aiming to minimize their ecological footprint.
Natural alternatives may not always deliver the same level of performance as silicone-based or certain synthetic agents, yet they shine in applications where safety and compliance are paramount. Industries such as food processing or pharmaceuticals benefit greatly from utilizing natural solutions, aligning with health standards and consumer preferences for clean and green products.
Applications in Various Industries
The utilization of anti foaming oils spans a wide array of industries, each with specific needs and challenges. Understanding how these substances function within various contexts is critical for optimizing their effectiveness. From food production to the delicate formulations in cosmetics, the benefits of anti foaming agents are manifold, making them indispensable in modern manufacturing processes.
Food and Beverage Industry
In the food and beverage sector, the presence of foam can significantly interfere with both production efficiency and product quality. Uncontrolled foaming during processes such as brewing, boiling, or mixing not only causes overflow but also can create inconsistencies in texture and taste. Anti foaming oils play a crucial role in addressing these issues, ensuring smooth operations.
These agents help maintain the integrity of the product. For example, in beer production, excessive foam can lead to loss of product during filling processes. By incorporating silicone-based anti foaming agents, manufacturers can minimize this risk, thus enhancing yield and overall customer satisfaction. Furthermore, the regulatory oversight in this industry necessitates that any anti foaming agent used be safe for consumption, prompting ongoing research into natural and less chemically intensive options.
Pharmaceuticals
The pharmaceutical industry is particularly meticulous about the quality of its products, thus making the role of anti foaming agents vital. Foaming can complicate processes like tablet manufacturing and liquid formulation, leading to defects that could compromise the efficacy of medications. The appropriate use of anti foaming oils can facilitate smoother blending and filling operations, ultimately contributing to higher-quality products and safer medication delivery.
Moreover, the use of such agents must comply with stringent regulatory standards. A robust understanding of their safety profiles is essential, as any substances introduced into medication formulations directly affect patient health. Thus, the ongoing evaluation of existing agents and exploration of new alternatives underpins methodical advancements in this area.
Chemical and Petrochemical Sectors
In the chemical and petrochemical industries, foaming presents a challenge in numerous applications, from the production of emulsions to the refining of crude oil. The presence of foam can jeopardize the separation processes and reduce the efficiency of chemical reactions. Anti foaming oils not only address these systemic problems but also enhance the operational capacity of equipment, leading to better productivity.
Utilizing products like polysiloxanes and fatty alcohols can lower surface tension, thereby controlling foam formation. This not only streamlines processes but also cuts down on waste and resource consumption. As this sector evolves towards more sustainable practices, the demand for bio-based anti foaming solutions is gaining momentum, as firms seek to reduce their environmental footprint without sacrificing performance.
Cosmetics and Personal Care
The cosmetics and personal care industries are notable for their diverse formulations, many of which require impeccable consistency and texture. Foaming can disrupt the desired product performance in lotions, creams, and shampoos, which can adversely affect the user experience. Here, anti foaming oils function as a vital component, enabling smoother application and enhancing the overall sensory profile.
Formulators typically gravitate towards silicone-based solutions, as these can impart a luxurious feel without the drawbacks associated with other chemical agents. However, there is an increasing trend towards natural anti foaming alternatives, reflecting consumer demand for clean and environmentally friendly products. Striking this balance allows companies to maintain market competitiveness while adhering to evolving customer preferences.
Effective foam control in the cosmetics field is essential not just for product performance but also for customer loyalty.
As diverse as these sectors may appear, the foundational element remains the same: the need for effective foam management through the strategic application of anti foaming oils. By drawing upon advanced formulations and ongoing research into innovative alternatives, industries can continue to evolve, meeting both operational demands and consumer expectations.
Environmental and Safety Considerations
In todayās industrial landscape, environmental and safety considerations are paramount. Anti foaming oils, while effective in managing foam across various applications, also come with an obligation to minimize their impact on the environment and human health. As industries strive for efficiency, the importance of selecting anti foaming agents that align with both performance standards and environmental responsibilities cannot be overstated. This section delves into the regulatory guidelines, toxicology assessments, and sustainable practices that frame the safe application of anti foaming oils.
Regulatory Guidelines
Adhering to regulatory guidelines is not merely a bureaucratic requirementāit's a commitment to preserving public health and maintaining ecological balance. Different countries and regions have established various regulations regarding the use of chemicals, including anti foaming oils. For instance, in the European Union, the Registration, Evaluation, Authorisation and Restriction of Chemicals (REACH) acts as a standard that dictates the permissible use of substances in manufacturing.
Some key aspects include:
- Substance Registration: Manufacturers must register their products, providing extensive data on the chemical composition and potential uses.
- Risk Assessment: Companies must demonstrate that any risks posed by their product are mitigated through proper management practices.
- Usage Restrictions: Certain formulations may be restricted or banned if deemed hazardous to the environment or health.
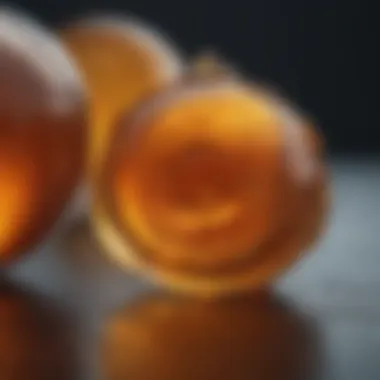

Complying with these regulations not only supports sustainability but may offer liability protection in cases where long-term impacts are assessed.
Toxicology Assessments
Toxicology assessments form the bedrock of safety in the use of anti foaming oils. The goal here is to ascertain the potential harmful effects these substances may have on humans and the ecosystem. Assessments typically consider various factors:
- Exposure Levels: How contact occursāwhether through inhalation, skin contact, or ingestionāand associated risks.
- Long-term Effects: Evaluating chronic effects from prolonged exposure is crucial; some substances may be safe in the short term but pose significant health risks over time.
- Environmental Impact: Understanding how these agents interact with aquatic and terrestrial ecosystems, including their biodegradability and toxicity to wildlife.
By conducting thorough toxicological evaluations, manufacturers can improve the safety profiles of their products, leading to better selection processes that favor low-risk alternatives.
Sustainable Practices
As industries increasingly shift towards greener solutions, sustainable practices in the production and application of anti foaming oils are becoming necessary. Implementing these practices could look like:
- Biodegradable Formulations: Developing anti foaming oils that break down more easily in the environment helps decrease their ecological footprint.
- Eco-Friendly Ingredients: Sourcing materials from sustainable or renewable origins decreases reliance on petrochemicals, which can be harmful to both people and ecosystems.
- Resource Efficiency: Optimizing formulation processes to minimize waste, energy consumption, and emissions is critical for sustainability.
Incorporating sustainable practices does not just align with environmental ethicsāit can enhance the brand's reputation, consumer loyalty, and, in many cases, lead to long-term cost savings.
"Embracing sustainable alternatives in anti foaming technology not only meets regulatory demands but also caters to the globally increasing consciousness about environmental stewardship."
Innovation in Anti Foaming Technologies
The realm of anti foaming technologies is like an intricate tapestry, woven with threads of chemistry, ingenuity, and practical necessity. As industries evolve, so too does the demand for effective foam control. Innovations in this field are not merely a matter of keeping production lines running smoothly; they embody a response to increasing market pressures, sustainability goals, and technological advancements. Staying ahead in foam control can give companies a significant competitive edge, whether it's in food processing, pharmaceuticals, or cosmetic formulations.
Recent Research Developments
Research in anti foaming oil is brisk, spurred by a combination of regulatory pressures and a push for efficiency. The focus has shifted towards exploring new formulations that yield higher performance while addressing safety and environmental concerns. For instance, a growing body of literature has emerged on next-generation silicone emulsions that enhance stability and foaming resistance. Techniques like microencapsulation have been researched to deliver active anti foaming components effectively, increasing their longevity and effectiveness in various applications.
"Innovation isn't just about creating new products; it's about creating better solutions that make a difference."
Formulation Enhancements
Formulation enhancements are critical in refining anti foaming oils, as they impact performance directly. Manufacturers are dipping their toes into the world of bio-based ingredients, linking up better sustainability practices with efficiency. For example, combining traditional silicone-based compounds with organic components can significantly optimize foaming control without sacrificing efficacy. Furthermore, the emergence of smart polymers that respond to environmental changesālike temperature or pHāoffers promising avenues for tailored foam control.
- Enhanced Stability: A focus on multi-component systems has shown to improve the stability and efficacy of anti foaming products.
- Compatibility: Greater research on the compatibility of various agents with solvents and emulsifiers ensures that the anti foaming agents perform effectively in specific processes.
Emerging Trends
Emerging trends are shaped by both customer needs and overarching environmental considerations. Green chemistry is now more than a buzzword; itās becoming a standard. Many organizations are keen on finding natural solutions that minimize ecological footprints. This shift has led to a rise in the popularity of plant-based anti foaming agents as viable alternatives. Moreover, digital technology plays a growing role in monitoring foam levels in real-time, allowing for more efficient management of resources and quicker responses to foaming issues.
- Digital Monitoring: The implementation of IoT devices in production facilities allows companies to track foaming occurrences and adjust anti foaming strategies proactively.
- Consumer Awareness: As consumers become more conscious about what goes into their products, the demand for transparency in product formulation is on the rise, influencing manufacturing choices.
This evolving trajectory highlights the pivotal intersection of innovation and practical applications in the anti foaming oil landscape, ensuring that industries can navigate the challenges of foam management while adhering to sustainability standards. The continuous advancements promise not just advancements in product efficiency but a commitment to addressing broader environmental truths.
Evaluating Anti Foaming Efficiency
Understanding the efficiency of anti foaming agents is crucial for industries that rely on these substances to ensure smooth operations. The effectiveness of an anti foaming oil can determine the quality of the product, from food items to industrial outputs. Evaluating anti foaming efficiency involves understanding how well these agents perform in their given environments, and this assessment can lead to better formulations, improved production processes, and reduced operational costs.
In essence, the evaluation process serves multiple purposes: it aids in identifying the right products for specific applications, helps predict behavior in various conditions, and ensures compliance with safety standards. This not only minimizes waste but also optimizes resource use, allowing manufacturers to operate at peak performance.
Testing Methods
The methods employed for testing anti foaming efficiency are diverse, aiming to address the unique characteristics of different foams and formulations. Common approaches include:
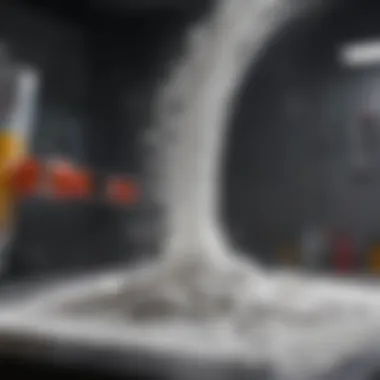

- Static Tests: These are performed by adding specific quantities of the anti foaming agent to a foam solution under controlled conditions to observe how quickly and effectively it breaks the foam.
- Dynamic Foam Tests: This method simulates actual conditions by continuously agitating the solution and monitoring foam collapse over time. It mimics the circumstances found in real-world applications, offering more reliable data.
- Submersion Tests: Useful in evaluating the performance in different fluid densities, this method measures how well a foaming agent works once submerged in a foaming solution under set pressures and times.
Each technique provides distinct insights, allowing practitioners to choose the most suitable approach based on their specific needs and desired outcomes.
Performance Indicators
Once the testing methods are carried out, quantifiable metrics or performance indicators give a clearer picture of how effective an anti foaming agent is. Some critical performance indicators include:
- Foam Reduction Rate: This metric measures the time taken by the agent to reduce foam volume in a defined time period. A quicker reduction indicates higher efficiency.
- Durability: This refers to how long the anti foaming agent maintains its effectiveness during prolonged exposure to foam conditions. A durable agent can significantly reduce costs by minimizing the need for constant replenishment.
- Concentration Versus Effectiveness: Evaluating how effective an agent is at different concentrations can help determine the most economical option without sacrificing efficacy.
- Compatibility with Other Ingredients: Understanding how an anti foaming oil interacts with other components in a formulation is vital. An effective agent should not compromise the product's quality or performance.
The efficient evaluation of anti foaming agents is not merely a procedural necessity; it directly influences operational costs, end-product quality, and overall production efficacy within various industries.
Case Studies and Practical Applications
Understanding the practical impact of anti foaming oils provides a real-world context that enriches the theoretical foundation laid elsewhere in this article. Case studies can unveil how various industries derive benefits from specific formulations tailored to their needs, thereby illustrating the importance of this topic.
Analyzing case studies often uncovers unique insights into the operational challenges faced by companies, while also showcasing innovative solutions achieved through the effective utilization of anti foaming agents. This empirical evidence not only serves as a guide for best practices but also illustrates the potential for further advancements and adaptations in these applications.
Food Processing Examples
In the food industry, the formation of foam can lead to several issues, including reduced product quality and increased processing time. For example, a dairy processing plant experimenting with different anti foaming oils discovered that the use of dimethyl silicone reduced foam significantly during milk homogenization. By incorporating a finely tuned application of this anti foaming oil, they reported not only smoother products but also enhancements in the efficiency of their processing equipment.
Similarly, in brewing, the right anti foaming agent is crucial. A brewery in the United States faced challenges with excessive foam in their fermentation tanks. After implementing a non-silicone based alternative specifically designed for use in beer production, they were able to maintain a balanced fermentation process without compromising the beerās flavor profile. This adaptability showcases how selecting the right anti foaming solution can make all the difference in food processing operations.
Industrial Cleaning Applications
Industrial cleaning often necessitates the usage of anti foaming oils to avoid operational disruptions. For instance, a major automotive manufacturer faced challenges with excessive foaming while using aqueous cleaning solutions to remove oils and contaminants from machinery. They conducted trials with various anti foaming agents, ultimately settling on a low-viscosity silicone-based product. The results were significant; not only did the foaming issue decrease, but the overall cleaning efficacy improved.
Furthermore, in the textile industry, a company experienced unsatisfactory cleaning results in their dyeing process due to foam build-up. After switching to a specific anti foaming oil that catered to their unique environmental conditions, they noted not only enhanced fabric quality but also reduced processing times. This efficiency translated into considerable cost savings, highlighting that a well-chosen anti foaming agent can indeed ripple out benefits far beyond immediate process improvements.
The right anti foaming oil can transform not just processes, but also cost efficiency and product integrity in various industries.
Through these case studies, it's evident that the careful selection and application of anti foaming oils can drive competitiveness and innovation across various sectors.
Future Perspectives
Discussing the future of anti foaming oil opens up an intriguing world where innovation meets necessity. As industries confront the realities of efficiency and sustainability, the demand for advanced anti foaming solutions is undeniable. Several key elements emerge when considering the future trajectory of this field, particularly research directions and market trends, which hold significant implications for both product development and environmental considerations.
The evolving landscape of anti foaming oils necessitates a continual shift towards more effective and eco-friendly formulations. Manufacturers are recognizing the need to balance product performance with consumer concerns about sustainability. This dynamic sets the stage for significant advancements in technology and science. Any entity that wishes to stay influential must adapt to these new realities.
Research Directions
In the realm of research, several directions are garnering attention. One area of focus is the optimization of existing anti foaming agents through improved formulation techniques. Researchers are delving into the molecular structure of silicone and non-silicone agents, aiming to enhance their efficiency while decreasing concentrations needed for effectiveness. This could lead to a decrease in overall material costs and environmental impact, a win-win for both producers and consumers.
Moreover, thereās growing enthusiasm around bio-based alternatives as companies look to mitigate the ecological footprint of their products. Investigations into natural oils and plant-based polymers are gaining traction, especially with the increasing demand for sustainable ingredients in food and personal care products. The quest for sustainable formulations aligns well with ongoing regulations and consumer expectations.
Understanding the interaction between anti foaming agents and diverse liquids and materials remains an essential research area. By probing deeper into this interaction, scientists can develop products that not only eliminate foam but also enhance performance across varied applications.
Market Trends
On the market side, several trends are shaping the future of anti foaming oils. The rise of green chemistry is creating substantial opportunities for companies willing to invest in rethinking their formulations. Customers are scrutinizing product labels more than ever before, preferring products that are not only effective but also environmentally responsible.
Additionally, the burgeoning demand for anti foaming agents in emerging economies presents new business opportunities. Industries such as textiles, cosmetics, and food processing in these regions are witnessing a rapid growth in production, leading to increased use of anti foaming agents. Importantly, these markets are often less saturated, allowing for more innovative distributions and marketing strategies of specialty products.
Furthermore, digital transformation and advanced analytics are influencing how companies approach product development and market strategy. Utilizing big data to monitor consumer preferences and predictive analytics to unveil trends helps businesses stay ahead of the competition, allowing them to tailor their offerings in real-time.
"The future landscape of anti foaming oils is shaped by an intricate interplay of innovation, environmental consciousness, and market exigencies."
In sum, the future perspective on anti foaming oils is ripe with possibilities. As industries look toward greater efficiency and sustainability, advancements in formulations along with market responsiveness will significantly guide the path forward. The horizon looks optimistic, yet it will require ongoing commitment from researchers, manufacturers, and regulatory bodies to ensure that both industry needs and environmental considerations are met.