The Evolution and Impact of 3D Printing Fabrication
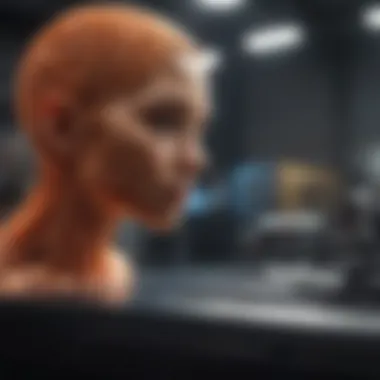
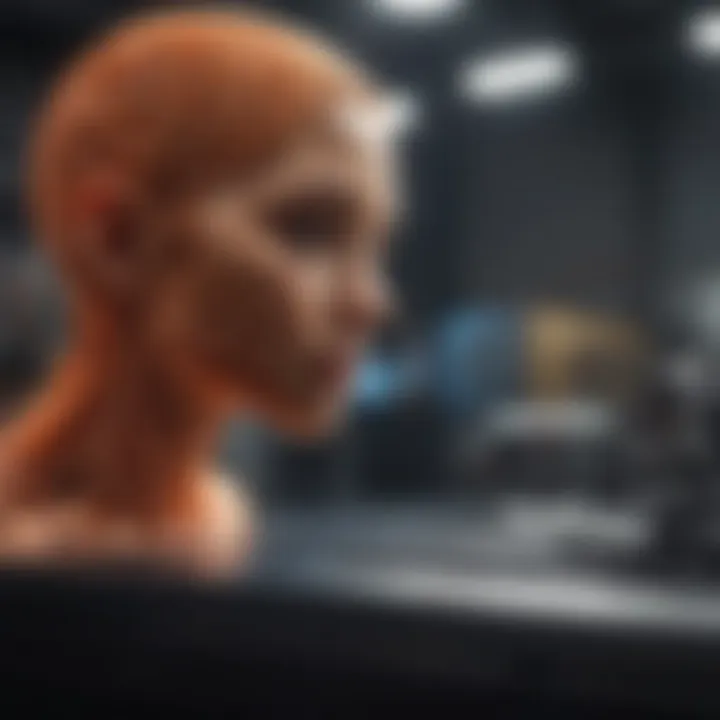
Intro
3D printing fabrication represents a significant shift in the paradigm of manufacturing. This technology, known also as additive manufacturing, allows for the creation of objects from digital files through a layer-by-layer construction process. Over the years, its evolution has been remarkable, driving innovation across a range of industries such as healthcare, automotive, aerospace, and consumer goods. Understanding the development of 3D printing and its consequent impact on production processes is essential for grasping future implications in these sectors.
By exploring this topic, readers will gain insights into how 3D printing is reshaping manufacturing and design, encountering both the benefits and risks associated with its adoption.
Intro to 3D Printing Fabrication
The topic of 3D printing fabrication holds significant relevance in contemporary manufacturing and design processes. This technology, commonly referred to as additive manufacturing, allows the creation of objects through the layering of materials. The importance of this topic extends beyond simple production; it challenges traditional methods and introduces a novel approach that adjusts to the evolving needs of various industries.
Advantages of utilizing 3D printing include customization, rapid prototyping, and reduced waste. Customization is vital in sectors like healthcare, where personalized solutions can significantly enhance patient outcomes. Rapid prototyping accelerates the design process, enabling companies to test and iterate on prototypes without extensive lead times.
When discussing introduction to 3D printing fabrication, one must also consider its implications on both costs and sustainability. Traditional fabrication methods often involve significant material sourcing and waste, while 3D printing can optimize these elements. Adopting this technology can lead to lower overall costs for production and an environmentally friendly approach to creating goods.
Historical Context
The origin of 3D printing dates back to the early 1980s. Chuck Hull, an American engineer, is credited with inventing stereolithography, the first 3D printing technology, in 1983. Initially used primarily for prototyping, the technology has transformed dramatically since its inception. The evolution of 3D printing saw many advancements, including new technologies and materials emerging over the decades. By the 1990s, techniques such as fused deposition modeling (FDM) originated, making the technology accessible to a broader audience. These historic developments laid the groundwork for the industry we see today.
The timeline also highlights pivotal moments like the establishment of 3D Systems, which further propelled the commercialization of this technology. Presently, 3D printing encompasses a wide array of applications, from biomedical fields to aerospace manufacturing. Each advancement showcases the potential of 3D printing to innovate and expand various sectors continuously.
Understanding Additive Manufacturing
To fully grasp the concept of 3D printing, one must understand additive manufacturing. This technique contrasts with subtractive manufacturing methods, which involve cutting away material from a solid block. Instead, additive manufacturing builds products layer by layer, starting from a digital model.
The process begins with a Computer-Aided Design (CAD) model. This digital representation is critical as it directs how each layer of material will be applied. After slicing the model into thin horizontal layers, the printer begins its working process, depositing material precisely as designated by the model.
Additive manufacturing offers flexibility in design that is often unattainable with traditional methods. Complex geometries, internal structures, and lightweight constructs are achievable without additional complexity or cost. Moreover, the ability to use various materials, such as plastics, metals, and composites, enhances functionality and application across multiple fields.
The adaptability of 3D printing leads to revolutionary changes in how products are designed and manufactured across industries.
Understanding these foundational elements is crucial for anyone looking to explore the ongoing impact of 3D printing on our world.
Technological Foundations of 3D Printing
Understanding the technological foundations of 3D printing is essential to grasping its impact on production and design today. This section outlines significant technologies behind 3D printing and their material counterparts, emphasizing how they shape the industry.
Types of 3D Printing Technologies
Stereolithography (SLA)
Stereolithography, or SLA, is one of the earliest forms of 3D printing technology. It utilizes a laser to cure liquid resin into hardened plastic in a layer-by-layer fashion. This method is particularly known for its high precision and ability to produce intricate details. A key characteristic of SLA is the smooth surface finish it provides, which is often superior to other methods. Its ability to create complex geometric shapes makes it a popular choice in industries like jewelry and dental applications.
Advantages of SLA include:
- High resolution and accuracy
- Versatile for different applications
However, SLA has disadvantages such as:
- The need for post-processing
- Limited material options compared to other methods
Fused Deposition Modeling (FDM)
Fused Deposition Modeling, or FDM, works by extruding thermoplastic filament through a heated nozzle. This technology is one of the most accessible and widely used 3D printing techniques, especially among hobbyists and startups. A distinct aspect of FDM is its cost-effectiveness and a wide range of compatible materials. It allows for rapid prototyping and easy workflow integration, making it ideal for producing functional prototypes.
Advantages of FDM include:
- Affordability and availability
- Diverse material options like ABS and PLA
However, the disadvantages comprise:
- Lower precision compared to SLA
- Layering and surface finish issues
Selective Laser Sintering (SLS)
Selective Laser Sintering, or SLS, employs a laser to fuse powdered materials, usually plastics, metals, or ceramics, into solid structures. This method is notable for its ability to print complex geometries without the need for support structures. The unique feature of SLS is its capability to use a variety of materials, leading to stronger and more durable end products. SLS is often chosen for manufacturing functional parts in industries like aerospace.
Advantages of SLS include:
- Strong and functional parts
- No support structures needed
The disadvantages are:
- Higher costs of equipment and materials
- Longer build times compared to FDM
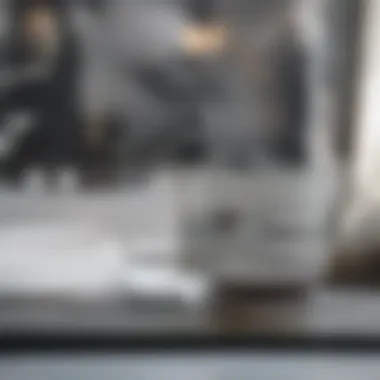
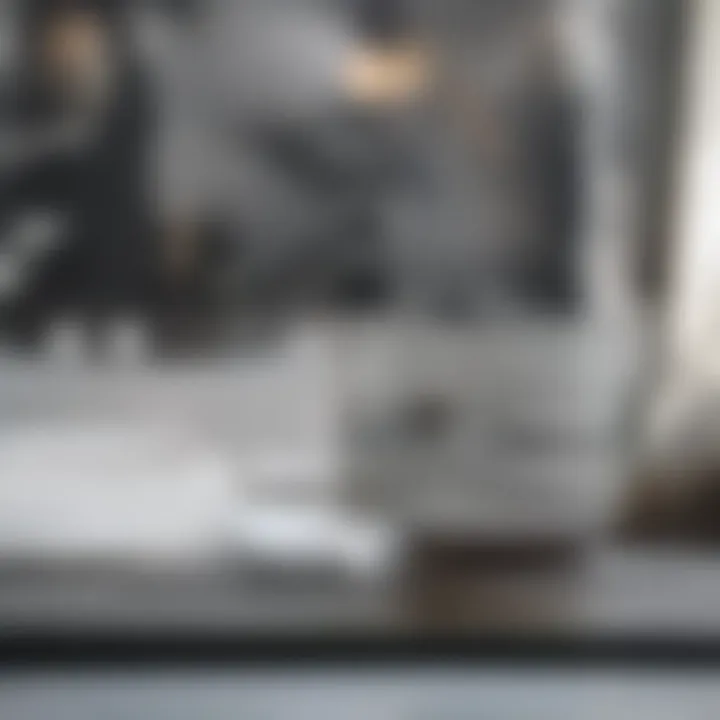
Materials Used in 3D Printing
The choice of materials in 3D printing directly affects the performance and application of printed parts. Each category of materials has its strengths and weaknesses, making it crucial to select the right one for specific uses.
Plastics
Plastics are the most commonly used materials in 3D printing. They include thermoplastics like PLA and ABS, which are favored for their ease of use and availability. Key characteristics of plastics allow for a range of applications, from prototypes to end-use products. Their affordability and lightweight nature make them beneficial for broader usage.
Advantages of Plastics include:
- Availability and ease of use
- Lightweight and low cost
However, disadvantages consist of:
- Limited heat resistance
- Susceptibility to deformation under stress
Metals
Metal 3D printing is gaining traction due to its capacity to produce high-strength and durable components. Technologies like SLS and direct metal laser sintering (DMLS) enable the creation of complex metal parts that are otherwise difficult to achieve with traditional manufacturing. A significant advantage of metals is their applicability in industries requiring high-performance materials such as aerospace and automotive.
Advantages of Metals include:
- Exceptional strength and durability
- Suitable for demanding applications
On the other hand, disadvantages are:
- High material and equipment costs
- Complex post-processing requirements
Composites
Composite materials blend different materials to achieve superior properties. In 3D printing, composites combine plastics with additives like carbon fiber or glass fibers. This combination enhances mechanical properties such as strength and stiffness. The key characteristic of composites is their versatility, allowing designers to optimize materials for specific performance requirements.
Advantages of Composites include:
- Improved mechanical properties
- Reduced weight without sacrificing strength
The disadvantages might include:
- Higher costs due to material processing
- Potential complexity in the printing process
In summary, understanding the technology and materials behind 3D printing is critical for anyone involved in the field. These foundations set the stage for innovation and application across various industries.
With the technological foundations established, we can move into real-world applications of 3D printing fabrication.
Applications of 3D Printing Fabrication
The applications of 3D printing fabrication span across various fields, illustrating the technology's versatility and transformative nature. In this section, we examine diverse ways this technology integrates into medical, industrial, and consumer domains. Each application showcases the benefits and considerations relevant to its adoption, contributing to a deeper understanding of its impact on modern practices.
Medical Applications
Prosthetics
Prosthetics stand out in the medical applications of 3D printing fabrication. The ability to create custom and affordable prostheses is crucial for individuals who have lost limbs. One key characteristic of 3D printed prosthetics is their customization. This ensures that the prosthetic device fits the user's body perfectly. Custom fit results in better comfort and functionality, making it a popular choice among healthcare providers.
The unique feature of 3D printed prosthetics lies in their rapid production process. Compared to traditional methods, which can be time-intensive and costly, 3D printing can significantly reduce production times. Additionally, materials used in 3D printing can be lightweight and durable, allowing for greater mobility for users.
However, there are some disadvantages. The technology is still evolving, and issues such as long-term durability and the quality of materials can sometimes pose challenges. Thus, healthcare professionals must weigh the benefits against potential drawbacks when recommending 3D printed prosthetics.
Tissue Engineering
Tissue engineering represents another significant medical application of 3D printing. This field focuses on creating biological tissues that can replace or restore damaged ones. A notable characteristic of tissue engineering with 3D printing is the precision in structuring cells and biocompatible materials. This allows for the fabrication of complex tissue architectures that mimic natural tissue.
The unique feature of this application is its potential to revolutionize regenerative medicine. By using 3D printing, researchers can experiment with various cell types and materials. This can lead to advancements in treatments for conditions such as organ failure or severe injuries. The benefits are profound, as it may shorten recovery times and improve the quality of life for many individuals.
On the downside, challenges remain, particularly in scaling up the processes for practical medical use. Producing large, functional tissues or organs is still a significant hurdle within the field. Ethical considerations surrounding the use of stem cells and bioprinting are also critical conversations that need ongoing attention.
Industrial and Mechanical Applications
Tooling
In industrial settings, tooling applications of 3D printing are pivotal. Tooling involves creating jigs, fixtures, and molds needed for various production processes. One essential characteristic of 3D printing in tooling is its ability to produce intricate geometries that are difficult or impossible to achieve with conventional methods. This granularity allows companies to streamline production processes and reduce lead times significantly.
A unique feature here is the reduction in material waste. Traditional manufacturing often results in excess scrap material, whereas 3D printing adds material layer by layer, thus optimizing usage. Moreover, tooling produced via 3D printing can be lighter, which may reduce overall production costs.
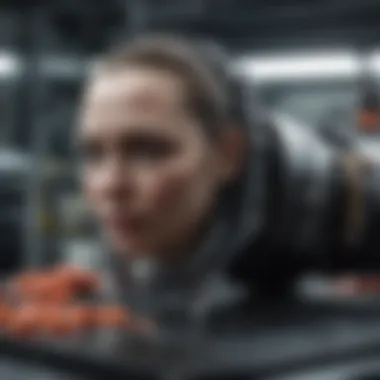
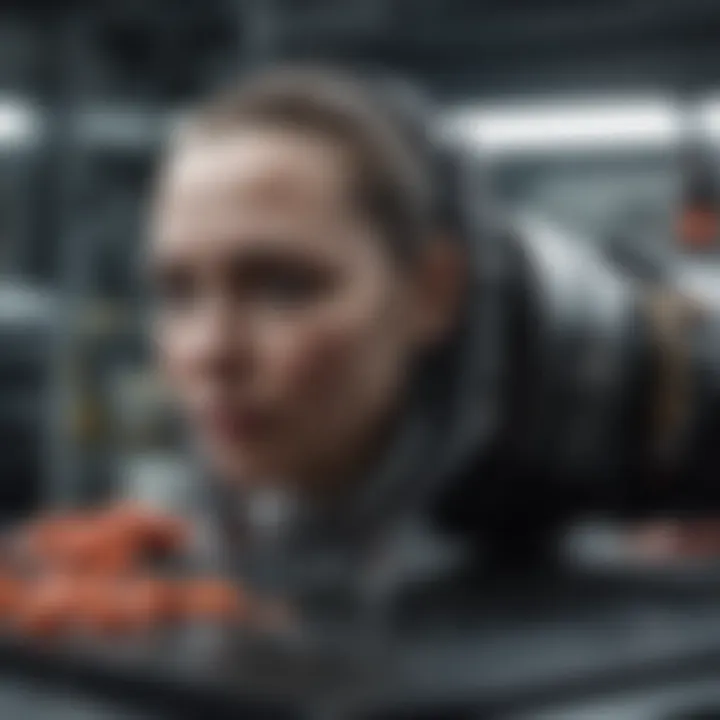
However, the initial investment in technology can be substantial for some businesses, to efficiently transition to additive manufacturing. There remains a learning curve associated with the technology that can pose difficulties for some companies.
Part Production
Part production is another industrial application widely recognized for its efficiency. 3D printing allows manufacturing of complex components on demand, significantly reducing inventory needs. Its key characteristic is the flexibility in design, permitting rapid prototyping and production of customized components without the need for extensive retooling.
The unique feature of 3D printed parts is their lightweight potential. In industries such as aerospace and automotive, weight reduction is crucial for improving fuel efficiency. The incorporation of lattice structures in designs can achieve this without compromising strength.
Despite these advantages, challenges persist regarding the material limitations of 3D printing. Not all traditional industrial materials are suitable for additive manufacturing. Additionally, speed can be a limiting factor when producing larger quantities of parts under tight deadlines.
Consumer Goods and Art
Fashion
In the realm of fashion, 3D printing is becoming an integral part of design and production processes. Its key characteristic is the ability to create bespoke apparel and accessories tailored to individual preferences. This customization appeals to consumers who seek uniqueness in their fashion choices.
The unique feature of 3D printed fashion items is their innovative designs. Designers can experiment with shapes and structures that are unattainable through conventional means. This leads to the creation of avant-garde pieces that challenge traditional norms.
However, production scalability remains a concern. Delivering mass-market quantities of 3D printed garments in a timely manner can be problematic. Additionally, the comfort and wearability of printed materials can vary, necessitating thorough testing before mass production.
Home Decor
Home decor is another area where 3D printing shines. This application offers consumers the ability to personalize their living spaces through unique furnishings and decorative items. The key characteristic of 3D printed home decor is its adaptability to various styles and preferences, catering to a diverse audience.
The unique feature of this application is the potential for artisanal designs produced at scale. Home decor items can easily integrate intricate patterns and textures that resonate with individual aesthetic values. The advantages include quick design iterations and reduced lead times compared to traditional methods.
Nevertheless, consumer acceptance is not uniform. Potential users may still be skeptical about the quality and durability of 3D printed decor compared to traditional handcrafted items. This perception can pose challenges for designers aiming to penetrate mainstream markets.
Design Considerations in 3D Printing
Design considerations play a crucial role in the effectiveness and efficiency of 3D printing. The journey from concept to final product involves various factors that impact quality, functionality, and manufacturability. Understanding these considerations can lead to better designs and consequently, more successful outcomes in additive manufacturing.
Software and Design Tools
CAD Software
Computational-Aided Design (CAD) software is essential for creating digital models used in 3D printing. This tools allow users to design intricate structures with precision. One key characteristic of CAD software is its ability to offer parametric modeling. This means designers can create models that can be easily adjusted and refined. Popular options include SolidWorks and AutoCAD, well suited for both beginners and experts.
The unique feature of CAD software is the simulation and analysis functions. These tools enable designers to assess stress points and optimize material usage before printing. However, the complexity of some CAD systems may be a disadvantage for novice users, as it can lead to steep learning curves and initial frustration.
Mesh Editing Tools
Mesh editing tools are also vital in the design process. They focus on manipulating the meshes that define the surface of 3D models. One of the key characteristics of these tools is their capability to repair and refine mesh data. Applications like MeshLab and Blender are popular because they offer a range of editing options.
The unique feature of mesh editing tools is their ability to convert 3D scanned data into 3D printable models. This feature is particularly useful in industries that require custom or tailored pieces. However, users may find that these tools can struggle with complex meshes, leading to print errors if not handled properly.
Optimizing Designs for Additive Manufacturing
Optimizing designs for additive manufacturing is essential. This process involves adjusting the design to maximize the advantages of 3D printing. Key factors include minimizing material usage while maintaining strength. Designers must consider support structures, layer height, and orientation during printing. Every decision can affect print time and quality.
- Layer Height: Thinner layers produce smoother finishes but increase print time. Balancing layer height with detail is vital.
- Orientation: The position of the model during printing can influence strength. Understanding load paths can improve performance.
- Support Structures: Designing to minimize the need for supports can save time and reduce post-processing work.
Challenges and Limitations of 3D Printing
The world of 3D printing brings with it a naive appeal, often highlighted by its innovative capabilities and possibilities. However, an honest exploration of this technology must also consider the challenges and limitations it presents. Recognizing these aspects is critical not only for proponents of this technology but also provides a realistic perspective for potential users. Understanding the hurdles related to technical performance, economic investments, and ethical dilemmas will guide the evolution and growing integration of 3D printing into broader industrial applications.
Technical Challenges
Print Quality
Print quality is a vital component in evaluating the performance of 3D printing systems. It determines the fidelity and resolution of the final product. A significant aspect of print quality is layer adhesion and detail resolution. These parameters can greatly affect the usability of printed objects. When the print quality is inconsistent, it can lead to structural weaknesses or aesthetic issues in the final prints. Potential users often seek high-quality outputs for both practical and commercial purposes. Therefore, achieving exceptional print quality remains a key factor for advancing the respectability of 3D printing.
One unique feature of print quality is its reliance on materials and technology used in the printing process. For instance, different types of filament or resin may yield varying results in strength and finish. The disadvantage, however, is that achieving high quality often means sacrificing speed and increasing production costs. Thus, balancing print quality with other factors is a constant challenge in the industry.
Speed of Production
Speed of production in 3D printing is another critical factor affecting its scalability and overall adoption. The time taken to produce an object often hinges on its complexity and size. Faster production speeds allow for rapid prototyping and quicker turnaround times, which are essential benefits in competitive industries.
A key characteristic of speed of production is the influence of technology type. Fused Deposition Modeling tends to be slower than Selective Laser Sintering. While speed is beneficial for allowing swift design iterations or final product deliveries, it can also lead to compromises on print quality or material stability. Hence, improving the speed of production without incurring quality losses poses an ongoing challenge for developers and manufacturers.
Economic Factors
Cost of Materials
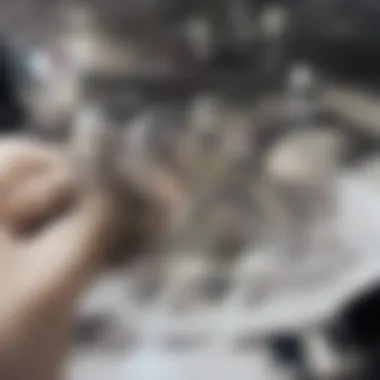
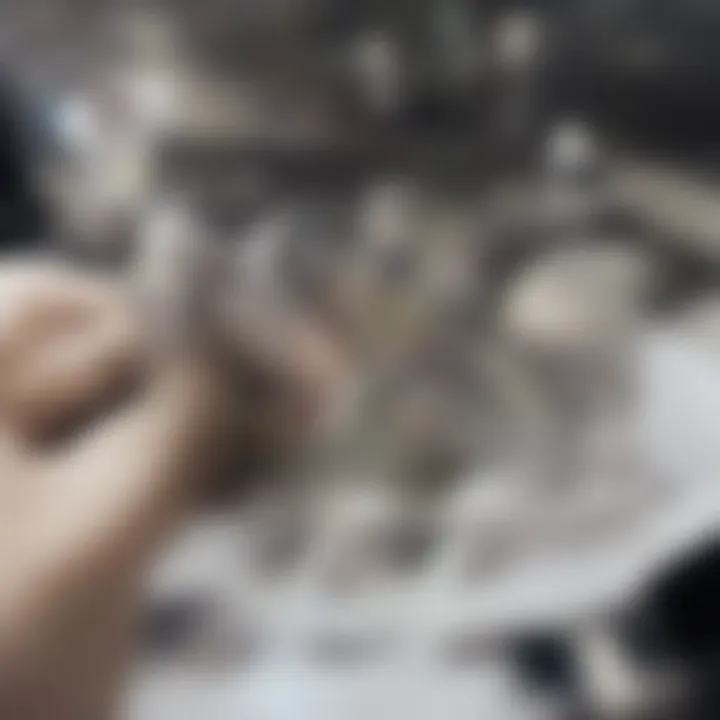
Cost of materials can heavily influence the overall feasibility of 3D printing projects. This aspect is critical since a large portion of the budget may be allocated to filaments or resins. Each material varies in price, quality, and application, which affects decision-making regarding production methods.
Materials such as PLA or ABS are often more affordable but might not offer the same functionality or durability as more advanced options like nylon or metal-infused filaments. The trade-off between cost-effectiveness and performance leads to complex decisions for businesses and individuals. Therefore, the cost of materials must be critically assessed to ensure that projects remain economically viable.
Investment in Technology
Investment in technology encompasses the initial capital required for purchasing 3D printers or related software, as well as ongoing maintenance and operation costs. The high cost of advanced machines can deter smaller companies or independent creators from embracing this technology. This can result in a steep learning curve as well, limiting the potential of newcomers in the field.
Notably, while the initial investment can be significant, there is a potential for long-term savings. Businesses might realize cost reductions in manufacturing processes over time. However, the divide in affordable versus high-end technology continues to impact accessibility and innovation within the sector.
Ethical Considerations
Intellectual Property Issues
Intellectual property issues are an increasing concern as 3D printing revolutionizes the way products are designed and produced. The ease of duplication using 3D models raises questions about ownership rights. For instance, a designer might create a unique design that can be reproduced without consent. This could undermine creativity and innovation in various industries.
Moreover, regulation regarding intellectual property is still evolving, leading to potential legal uncertainties. Intellectual property protections are critical for fostering an environment where designers can share their work without fear of unauthorized reproduction. This characteristic makes it an essential topic in discussions about the future of 3D printing.
Environmental Impact
Environmental impact is a significant ethical concern tied to the materials and energy used in 3D printing processes. Dependence on non-renewable resources for filament or resin manufacturing poses harmful effects on the planet. Furthermore, there's additional concern about plastic waste from failed prints and excess materials that can accumulate over time.
However, some advancements aim to mitigate these concerns. New biodegradable materials emerge regularly, and research into recycling waste filament is gaining traction. Recognizing and addressing the environmental impact of 3D printing is essential for establishing a more sustainable practice in this evolving industry.
The challenges and limitations of 3D printing are substantial, yet they offer insights into areas ripe for innovation. An understanding of these factors facilitates a more robust development framework, ensuring the long-term viability of this crucial technology.
Future Directions in 3D Printing Fabrication
As the domain of 3D printing fabrication continues to evolve, significant advancements and innovations are emerging. These developments not only enhance the capabilities of the technology but also broaden its applications across various industries. It is essential to understand these future directions as they represent a pivotal aspect of how 3D printing can influence production, design, and overall market trends.
Emerging Technologies
Bioprinting
Bioprinting is a revolutionary aspect of 3D printing that focuses on creating living tissues and organs through additive manufacturing. This technology shows promise in medical fields, particularly for regenerative medicine and personalized therapy. The key characteristic of bioprinting is its ability to use bioinks made from living cells. This uniqueness allows for the construction of complex biological structures that can mimic the natural architecture of tissues.
The advantage of bioprinting lies in its potential to produce functional human tissues, which can significantly impact organ transplantation and drug testing. However, the challenges involved in ensuring tissue viability and functionality after printing remain significant hurdles that need addressing.
Metal Printing
Metal printing is gaining traction as it allows for the fabrication of intricate metal parts with high precision. This process is particularly useful in aerospace and automotive industries, where the need for lightweight yet durable components is critical. The ability of metal printing to create complex geometries is a key characteristic that stands out.
The advantage of metal printing includes reducing material waste and enabling designs that would be impossible with traditional manufacturing techniques. Yet, the costs associated with the technology and the need for specialized equipment can be barriers for widespread adoption.
Integration with Other Technologies
AI and Machine Learning
The integration of artificial intelligence (AI) and machine learning in 3D printing optimization represents a significant advancement. These technologies can analyze large datasets to improve printing processes, resulting in enhanced accuracy and efficiency. AI algorithms can aid in predictive maintenance, reducing downtime and increasing productivity.
The unique feature is the ability of AI to adapt models based on feedback from the printing process. This adaptability leads to continuous improvement, which is vital in a competitive market. However, some concerns around data privacy and the ethical use of AI remain prevalent.
Robotics
Robotics in 3D printing facilitates automation, which enhances production speed and consistency. Automated systems can handle repetitive tasks, allowing human operators to focus on high-value activities. The key characteristic of robotics integration is precision in executing intricate designs, which is essential in production environments.
The advantage of robotics includes lower labor costs in the long run and reduced human error. On the downside, initial setup costs can be high and may require specialized training for effective utilization.
As the field progresses, understanding these future directions is crucial for students, researchers, and professionals aiming to leverage 3D printing effectively in their respective domains.
Ending
The conclusion of this article encapsulates the multifaceted journey of 3D printing fabrication, emphasizing its significance in contemporary and future production landscapes. This technology, a product of relentless innovation, extends beyond mere convenience; it reshapes industries and redefines manufacturing principles. As we look back at the evolution chronicled throughout the sections, it becomes evident that 3D printing is not only about creating objects layer by layer.
Summarizing Key Insights
In reviewing the pivotal elements discussed, several insights emerge:
- Technological Impact: The advances in 3D printing technologies, such as Stereolithography and Fused Deposition Modeling, highlight the progression in speed, efficiency, and quality of production.
- Diverse Applications: From medical applications, like prosthetics and tissue engineering, to industrial tooling and consumer goods, the breadth of 3D printing applications demonstrates its versatility and potential in various fields.
- Challenges and Ethical Considerations: The journey is not without challenges. Technical limitations, economic factors, and ethical dilemmas present ongoing discussions that must be addressed as the technology matures.
"3D printing is a tool that transforms industries, yet it necessitates a careful approach to its integration and expansion."
Looking Ahead
Looking towards the future, the trajectory of 3D printing fabrication paints a promising yet complex picture. Key considerations include:
- Emerging Technologies: Innovations like bioprinting and advanced metal printing technologies are poised to revolutionize how we think about production and healthcare solutions.
- Integration with AI: As artificial intelligence and machine learning integrate with 3D printing processes, the efficiency, and accuracy of production is expected to improve significantly, enhancing capabilities and opening new avenues.
- Sustainability Concerns: Future developments must also prioritize sustainability. The environmental impact of materials used in 3D printing will likely drive research into more eco-friendly options and techniques.
As both seasoned professionals and newcomers navigate the evolving landscape of 3D printing, the ongoing dialogue about its implications and future directions will be crucial.