Comprehensive Study of Displacement Measurement Techniques
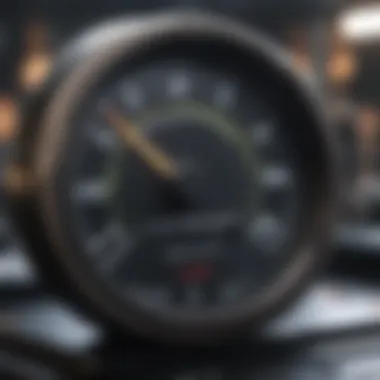
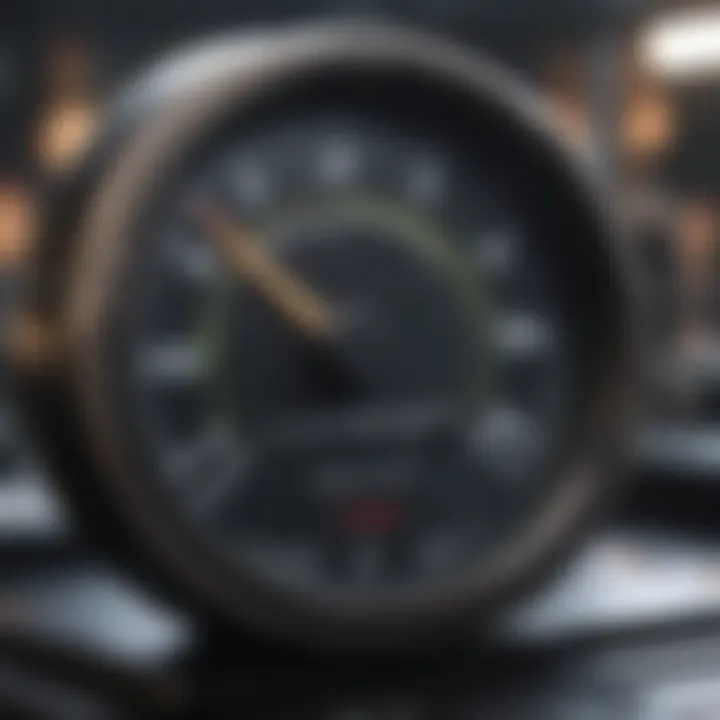
Intro
Displacement measurement is a fundamental aspect within various scientific and engineering disciplines. From ensuring precise movements in manufacturing to monitoring minute shifts in structural engineering, understanding the nuances of these measurement techniques is essential. Not only does it enhance product quality, but it also bolsters safety and efficiency across numerous applications.
Despite its importance, the field of displacement measurement can be labyrinthine, with a plethora of methods and technologies intertwining in complex ways. This complexity underscores the necessity for a broad yet detailed exploration of the fundamental principles, critical methodologies, and innovative advancements that define displacement measurement today.
In this exploration, we will uncover key findings that illuminate the significance of these techniques, methodologies that provide a clear roadmap for realization, and the prospects for future innovations aimed at enhancing accuracy. As such, this article aims to bridge the gap between theoretical understanding and practical application.
Key Findings
Major Results
Displacement measurement plays a pivotal role in various domains:
- Precision Engineering: Enhances the accuracy of components in manufacturing processes.
- Structural Health Monitoring: Detects shifts in buildings and bridges, aiding in maintenance and preventive care.
- Medical Applications: Offers crucial insights in biomechanics and rehabilitation technologies, ensuring better patient outcomes.
The methods employed span traditional mechanical systems to advanced optical techniques, each with its own set of advantages and limitations. For example, while dial indicators are simple to use, they might not capture minute displacements as effectively as laser triangulation methods.
Discussion of Findings
Analyzing the chosen methods reveals intricate details. For instance, laser displacement sensors not only provide high accuracy but are also capable of measuring displacements at considerable distances without contact. This feature is particularly advantageous in hazardous environments where direct contact is risky. Conversely, technologies such as capacitive sensors have a more limited range but excel in high-precision applications where minor displacements are critical.
The trade-offs inherent in these methodologies lead to a broader conversation about selecting the appropriate measurement technique based on specific requirements. Understanding these nuances will empower researchers and professionals alike to make informed decisions in their respective fields.
Methodology
Research Design
This exploration assembles a comprehensive overview through a combination of literature review and case study analysis. The literature review draws from relevant academic journals, articles, and industry reports to collate data on current techniques and their applications.
Data Collection Methods
Data was gathered via several methods, including:
- Review of Existing Literature: Incorporating findings from well-regarded sources like Britannica and Wikipedia to synthesize current knowledge.
- Case Studies: Analysis of specific instances in which displacement measurement has had significant impact, observed from industry reports and academic research.
This methodological framework assures a robust understanding of displacement measurement techniques aligned with diverse industry needs. By assembling insights from historical applications and current advancements, we lay the groundwork for future research trajectories and technological advancements aimed at improving accuracy and efficiency in displacement measurement.
Prologue to Displacement Measurement
Displacement measurement is a cornerstone of many scientific and engineering disciplines, playing a pivotal role in how we understand and interact with the world around us. When we think about the movement of objects—whether in a laboratory setting, during industrial manufacturing, or even in the realm of civil engineering—the importance of accurately measuring this motion cannot be overstated. It’s not just about numbers; it’s about ensuring that structures are safe, products meet quality standards, and that innovations are developed with precision.
To grasp the full impact of displacement measurement, one must first consider its definition.
Definition of Displacement
In its simplest terms, displacement refers to the change in position of an object. It is a vector quantity, meaning it has both magnitude and direction. For instance, if an object moves 10 meters to the east, its displacement is described as 10 meters in that direction. This shift can occur due to various forces—be it gravitational pull, mechanical movement, or even thermal expansion.
Understanding this concept is vital because, in practical applications, knowing not just how far something has moved but also in what direction is crucial. For example, in robotics, if a robotic arm needs to position an object precisely on a conveyor belt, it is not enough to just know how much the arm has moved; the accuracy of its vector movement determines how effectively it can perform its intended task.
Importance in Scientific and Engineering Contexts
The significance of displacement measurement extends across various fields, illustrating its utility in both scientific research and engineering practices. Here are some key points highlighting its importance:
- Quality Control: In manufacturing, precise displacement measurements can directly influence quality control processes. A slight misalignment in parts can lead to product failures or safety hazards, making the measurement crucial.
- Structural Integrity: In civil engineering, monitoring displacement can signal potential structural failures in buildings or bridges. Understanding how materials respond under stress allows engineers to diagnose issues before they become catastrophic.
- Research Advancements: Scientific studies often rely on the accuracy of displacement measurements. In fields like physics or materials science, the nuances of atomic movements or material degradation require precise data interpretation.
"Accurate displacement measurement is not merely a technical necessity; it’s the backbone of safety and reliability in numerous applications."
Utilizing advanced measurement techniques, from mechanical methods to cutting-edge digital technologies, provides engineers, researchers, and industry professionals with the tools they need to ensure effectiveness and reliability.
In the sections that follow, this article will delve deeper into the fundamental principles and contemporary methods used in displacement measurement, illustrating how each contributes to the field. The understanding of these concepts lays the groundwork for appreciating their applications and the challenges faced in measurement technologies.
Fundamental Principles of Displacement Measurement
When discussing displacement measurement, understanding its fundamental principles becomes crucial. These principles lay the groundwork for the various methods and applications explored later in the article. They are the crucial building blocks that give context to how we perceive and quantify motion and position. Grasping these concepts helps professionals in fields like engineering, manufacturing, and research develop more accurate and efficient measurement systems.
In the realm of displacement measurement, two primary concepts take center stage: linear measurement and angular displacement. Familiarity with these ideas ensures one can appreciate the intricate workings behind sophisticated tools and technologies. They are not merely academic notions; they underpin practical applications, impacting accuracy in various industries.
Concept of Linear Measurement
Linear measurements refer to the straight-line distance between two points. This is more than just a numerical value; it encapsulates the essence of countless engineering and scientific endeavors. For example, when designing a bridge, precise linear measurements are necessary to ensure structural integrity and stability. The accountability of these measurements can mean the difference between safety and catastrophe.
Why is linear measurement so important? Here's a brief rundown:
- Precision: In fields like aerospace engineering, where every millimeter counts, linear measurements dictate the success of designs.
- Simplicity: Many linear measurement devices, such as rulers and tape measures, are user-friendly and widely applicable.
- Reproducibility: Linear measurements can be replicated across various contexts, leading to consistent results.
Tools for linear measurement vary in complexity. Simple devices like tape measures serve everyday needs, while advanced tools like laser distance meters offer higher precision for professional applications. The integration of digital readouts and sensor technology has revolutionized how linear measurement is conducted, providing real-time data and reducing human error.
Understanding Angular Displacement
Angular displacement, on the other hand, addresses the rotation around a fixed point or axis. When we talk about something spinning or rotating, such as a wheel or a gear, angular displacement comes into play. It’s expressed in degrees or radians, showcasing how far an object has moved from its original position.
This concept matters significantly in various applications:
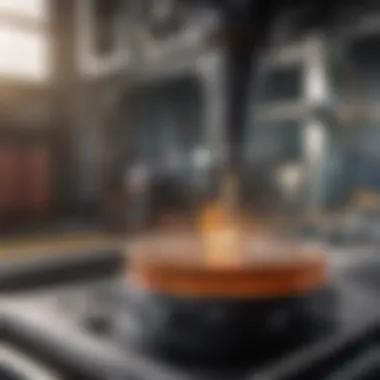
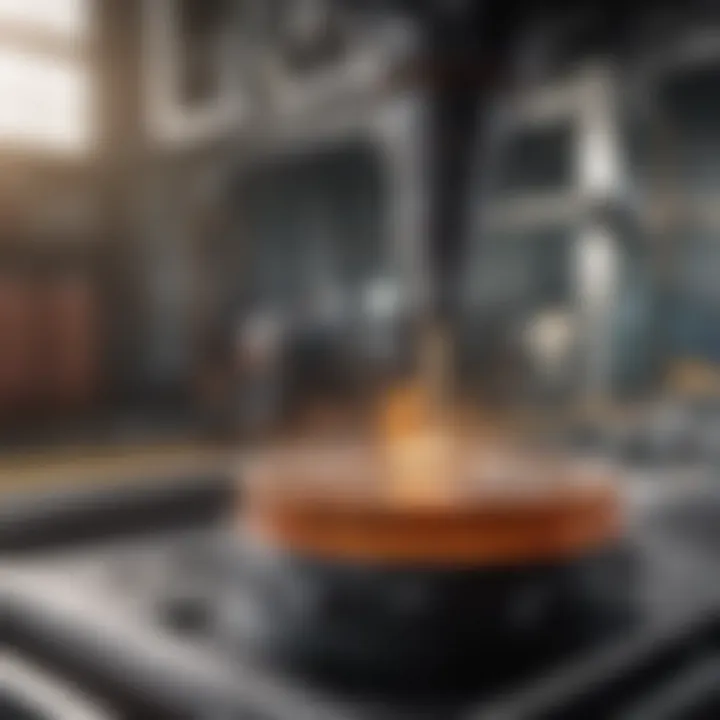
- Mechanical Engineering: Understanding how parts rotate and the angles involved can optimize machinery design.
- Robotics: Precise control over rotation is necessary for accurate and efficient robotic movement.
- Architecture: Calculating the angular shift of structural elements is vital for stability analyses, especially in seismic zones.
Usually measured using protractors or goniometers, angular displacement can also be captured digitally via encoders. These devices translate rotational motion into proportional electrical signals, allowing for more precise control in automated systems.
"Measuring angular displacement isn't just about getting the angle right; it's about ensuring everything fits together like a well-oiled machine."
Contemporary Methods of Displacement Measurement
In today’s fast-paced world, the precision of displacement measurement holds paramount importance in industries like manufacturing, automotive, and civil engineering. Contemporary methods not only enhance accuracy but also improve reliability and efficiency in the measurement process. As technology continues to develop, the tools and techniques for measuring displacement have advanced dramatically. With a shift towards automation and real-time monitoring, using modern measurement techniques can provide significant advantages in both production environments and research settings.
Mechanical Methods
Dial Indicators
Dial indicators are instruments designed to measure small distances or changes in position. They are often used in workshops for tasks that require precise measurements. This method is beloved for its simplicity. A significant aspect of dial indicators is their analog readout, which makes it easy to interpret the measurement without any electronic components involved. The primary characteristic that sets dial indicators apart is their mechanical simplicity. This makes them a beneficial choice for many applications where digital calibration isn't feasible.
Dial indicators have a unique feature in their ability to detect minute displacements, making them essential in quality control processes, often ensuring that parts conform to specifications.
However, while dial indicators come with a rugged design, they can be susceptible to human error. When read through the eye of an operator, slight parallax errors can occur, affecting accuracy.
Linear Variable Differential Transformers
Linear Variable Differential Transformers (LVDTs) are highly specialized sensors. Their main job is to determine linear displacement through inductance changes. What makes LVDTs stand out is their electromechanical design, which translates a change in position into a measurable electrical signal. This characteristic contributes significantly to their popularity in applications where precise measurements are crucial, such as aerospace and automotive engineering.
A key aspect of LVDTs is their unique ability to provide continuous measurements without contact, which reduces wear and tear. Another advantage is their great resolution; they can detect very small changes in position.
Despite these advantages, LVDTs can be sensitive to environmental factors like temperature, which can lead to drift in measurements.
Electromagnetic Techniques
Laser Displacement Sensors
Laser displacement sensors represent a step forward in precision measurement technologies. They utilize laser beams to gauge distance accurately, making them invaluable in industrial applications and research. One critical aspect of these sensors is their ability to deliver non-contact measurements, which minimizes the chance of damage to the object being measured.
The laser’s high precision makes it a favored tool for tasks where minute deviations must be tracked. A unique feature of laser displacement sensors is their adaptability; they function effectively over various surfaces and materials, which adds to their utility.
Their main drawback could be their dependency on a clean environment; dust or interference can affect the measurements, so extra attention needs to be given to cleaning and maintaining setups.
Capacitive Sensors
Capacitive sensors measure displacement by detecting changes in capacitance caused by position shifts. What makes them widely utilized is their sensitivity; even minor displacements can trigger responses. This attribute is crucial in applications ranging from process control to automated manufacturing. With capacitive sensors, the distance to an object can be calculated in real time, which is a notable benefit in production lines where real-time data is pivotal.
A defining feature of capacitive sensors is their compactness, allowing for easy integration into existing systems. However, one disadvantage is that these sensors can be impacted by environmental factors, such as humidity or temperature changes, which may lead to errant readings.
Optical Methods
Interferometry
Interferometry is a high-precision measurement method that employs the interference of light waves. This technique is crucial for measuring displacements at a microscopic level. The unique characteristic of interferometry is its unmatched accuracy, often applicable in scientific research and precision engineering contexts.
It allows for measuring very small shifts in position due to its reliance on the wavelength of light; this can translate to incredibly high resolution. However, a downside is the complexity of setup and the need for stable environmental conditions, as any external vibrations could lead to inaccurate results.
Vision Systems
Vision systems offer an innovative approach to measuring displacement using cameras and image processing algorithms. They provide a versatile means of capturing real-time data from various surfaces and are used widely in robotic applications. The primary benefit is their ability to measure complex geometries without physical contact, making them ideal for delicate parts.
A unique feature of vision systems is their capability to assess multiple points simultaneously, drastically increasing measurement efficiency. On the flip side, the reliability of these systems can be affected by lighting conditions and requires constant calibration for accurate results.
Advanced Digital Techniques
Digital Encoders
Digital encoders are devices that convert the angular position or motion of a shaft into a digital signal. They are widely regarded for their precision, often utilized in robotics and industrial automation for effective displacement tracking. Their primary feature is their ability to provide high-resolution outputs, imperative for tasks needing rigorous position feedback.
The main advantage of digital encoders is their robustness against noise; they deliver reliable outputs even in electrically noisy environments. One concern, however, is their dependence on proper installation and alignment; if this is neglected, the accuracy can be compromised.
3D Scanners
3D scanners are at the pinnacle of measurement techniques, enabling the capture of an object's dimensions in three-dimensional profiles. Their significance lies in their ability to gather vast amounts of data swiftly, which can be crucial in fields like archaeology and manufacturing. They utilize light and radar technology, making them versatile in different environments.
One of the standout features is their capability to recreate a detailed digital model of the object, allowing for extensive analysis and improvements in design and manufacturing processes. However, the high initial costs and the complexity of data management can present challenges for smaller firms.
In a world where precision is crucial, contemporary methods of measuring displacement continue to evolve, promising greater accuracy, efficiency, and versatility.
Applications of Displacement Measurement
Displacement measurement plays a crucial role across various industries, acting as the backbone of quality control, safety, and technological advancement. Understanding displacement isn't only about dimensions; it is about precision, consistency, and the ability to monitor changes that could impact performance or safety. The significance of this field is multi-dimensional and offers various benefits, influencing processes in manufacturing, civil engineering, biomedical fields, and the automotive sector.
In manufacturing and quality control, for instance, keeping an eye on minute displacements ensures that components are produced within specified tolerances. If a part strays even slightly from its intended measurements, it could cause a cascade of failures down the line. This highlights the advantage of using sophisticated sensors and measurement techniques in the production phase. On the other hand, in civil engineering, monitoring structures for displacement can preempt catastrophic failures. Buildings and bridges, for example, are continually under stress, and knowing how and when they shift helps prevent disasters.
Similarly, in the biomedical field, displacement measurement allows for the development of precise medical devices, impacting patient outcomes directly. Devices such as surgical robots or prosthetics must function with exactitude to ensure safety and effectiveness. Finally, in the automotive industry, displacement measurement is instrumental in enhancing vehicle safety features and performance metrics. Technologies that monitor displacement can alert drivers to potential mechanical failures or ensure airbags deploy accurately during collisions.
Overall, the integration of advanced displacement measurement techniques not only improves efficiency but also builds a safety net across these crucial sectors, making it an area ripe for research and innovation.
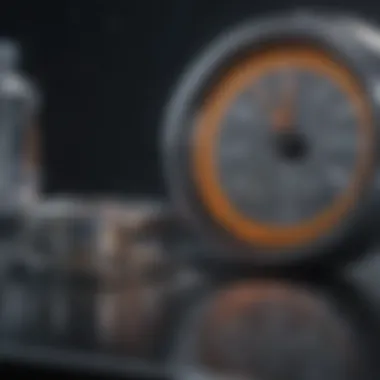
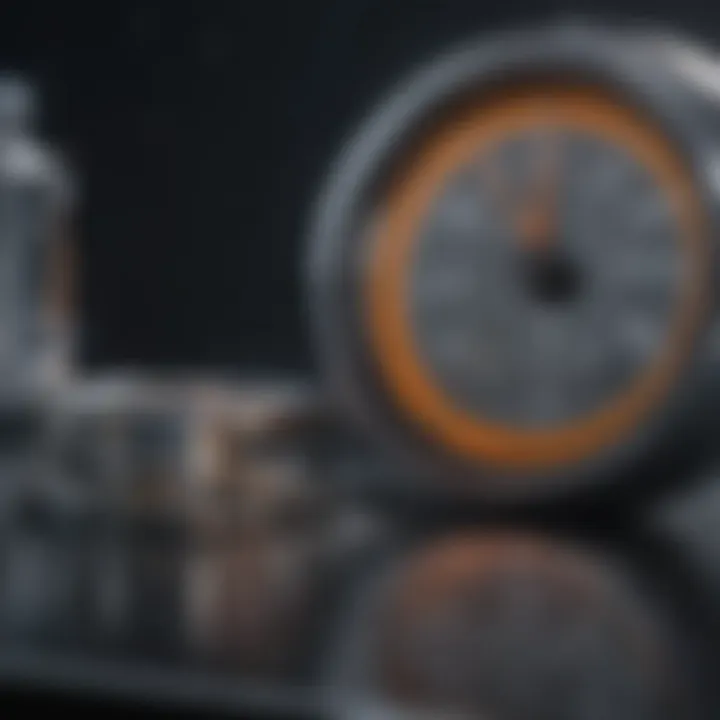
Manufacturing and Quality Control
In manufacturing, precision is king. Every millimeter or fraction of an inch can mean the difference between an effective product and one that fails prematurely. Manufacturers rely on displacement measurement for ensuring that parts meet design specifications and tolerances. Techniques such as using dial indicators and laser sensors provide real-time feedback during the assembly process, allowing for immediate adjustments.
Moreover, quality control teams can utilize data from displacement measurements to analyze trends over time. This trend analysis helps in predicting when a machine may require maintenance or when it could start producing defective parts.
Key advantages of applying displacement measurement in manufacturing include:
- Enhanced Quality Assurance: Catching errors early ensures only the best products roll off the assembly line.
- Reduced Waste: Accurate measurements can lead to less material squandered due to inaccuracies.
- Improved Productivity: Automated systems that utilize real-time displacement measurement can operate more consistently and minimize downtimes.
Civil Engineering and Construction
In the realm of civil engineering, displacement measurement serves as the watchdog, keeping structures safe and sound. Buildings and bridges experience shifts due to various factors like ground movement or heavy loads. Monitoring these displacements is pivotal to maintaining structural integrity and avoiding potential failures.
One common application involves geotechnical sensors. These instruments can measure ground displacement around excavation sites or landslide-prone areas, providing essential information that informs construction strategies. The insights gained can dictate when to halt activities or if reinforcements are needed.
- Critical Monitoring: Sensors can detect minute shifts in structures that might go unnoticed during visual inspections.
- Safety Compliance: Adhering to displacement monitoring standards helps meet regulatory requirements, ensuring public safety.
Overall, the importance of displacement measurement in civil engineering cannot be overstated. It safeguards both human life and investments in infrastructure.
Biomedical Applications
When it comes to healthcare, accurate displacement measurement can be life-saving. Innovations in surgical techniques and medical devices hinge on the precision with which medical professionals can measure and respond to changes in the human body.
For instance, in robotic-assisted surgeries, precise measurements ensure that surgical tools function optimally, allowing for smaller incisions and quicker recovery times. Prosthetics, too, have seen a revolution with the use of displacement sensors that adapt to the individual’s movements and adjust functioning accordingly. This kind of customization not only improves user experiences but also impacts rehabilitation outcomes.
Key aspects include:
- Enhanced Patient Safety: Accurate measurements reduce risks during complex surgical procedures.
- Customized Solutions: The ability to fine-tune medical devices leads to better fit and function for patients.
This intersection of technology and medicine showcases how displacement measurement continually paves the way for advancements in healthcare, emphasizing the significant contributions it offers.
Automotive Industry
In the automotive industry, displacement measurement is central to innovation and safety. Modern vehicles are equipped with a plethora of sensors that track various parameters, and displacement measurement systems contribute significantly to vehicle dynamics and crash safety features.
Real-time displacement data helps manage systems that ensure stability, control braking, or deploy outcomes of safety systems like airbags. Additionally, as the industry shifts towards electric vehicles, the precise measurement of movements and adjustments becomes even more critical in managing battery efficiency and overall performance.
Some advantages for this industry include:
- Safety Enhancements: Advanced safety systems rely on accurate displacement to prevent accidents.
- Performance Metrics: Enhanced understanding of vehicle dynamics allows for performance optimization.
Challenges in Displacement Measurement
Displacement measurement presents its own unique set of challenges, which can significantly influence the accuracy and reliability of results in various scientific and engineering domains. These challenges arise from a confluence of external and internal factors, raising the need for practitioners to remain vigilant and informed. Understanding these challenges not only helps in implementing better measurement strategies but also aids in developing innovative solutions that can maximize the potential of existing technologies.
Environmental Factors
Environmental conditions can greatly affect the outcome of displacement measurements. Temperature fluctuations, humidity levels, vibrations, and even electromagnetic interference pose distinct problems. For instance, a precision sensor exposed to high temperatures may experience thermal drift that alters its readings. Similarly, in a factory setting with large machinery, vibrations can mimic displacement, causing incorrect readings.
To mitigate these issues, it is essential to:
- Select measurement tools specifically designed for harsh environmental conditions.
- Implement isolation methods that can dampen vibrations.
- Utilize shielding techniques to protect sensors from electromagnetic interference.
By being mindful of these environmental factors, engineers and researchers can ensure a more reliable data collection process, preventing costly errors in critical applications.
Material Limitations
Another important consideration is the material being measured. Different materials expand or contract at varying rates in response to environmental changes. For example, metals might expand more than plastics when subjected to heat, leading to a misalignment in displacement readings. Additionally, when using mechanical methods such as dial indicators, the flexibility of the material can cause bending or deformation, further complicating measurement accuracy.
To address these material limitations, practitioners might need to:
- Choose appropriate materials that have low thermal expansion coefficients.
- Regularly monitor surface conditions to ensure accuracy in measurements.
- Incorporate compensating features in instruments that accommodate material variability.
This proactive approach can greatly enhance the reliability of displacement measurements in practical scenarios.
Calibration Issues
Calibration forms the backbone of any measurement system, ensuring that the tools used deliver accurate results. Calibration problems may arise from prolonged use, environmental changes, or improper handling of equipment. A sensor that has drifted from its calibrated state might provide spurious results, leading to misinformed decision-making.
To maintain calibration integrity, it's vital to:
- Conduct regular calibration checks as part of a maintenance routine.
- Utilize reference standards that are traceable to national measurements.
- Document all calibration activities to maintain a clear history that can be analyzed over time.
Given the complexities involved, addressing calibration challenges is key to preserving the accuracy and reliability of displacement measurement techniques, ensuring they perform optimally in various applications.
In summary, understanding and addressing the challenges in displacement measurement is fundamental for achieving high precision across different fields.
By considering environmental factors, material limitations, and calibration issues, professionals can enhance their strategies and implement effective solutions that lead to improved measurement outcomes.
Technological Advancements in Measurement Techniques
The landscape of displacement measurement has undergone a seismic shift due to various technological advancements. As industries strive for greater precision and efficiency, it’s imperative to recognize the profound impact of these innovations. The integration of smarter systems not only enhances the accuracy of measurements but also streamlines operations and fosters greater data analytics capabilities. This section delves into two pivotal advancements: the incorporation of the Internet of Things (IoT) in measurement systems and the application of machine learning for predictive analytics.
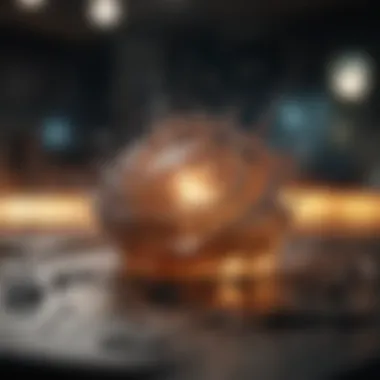
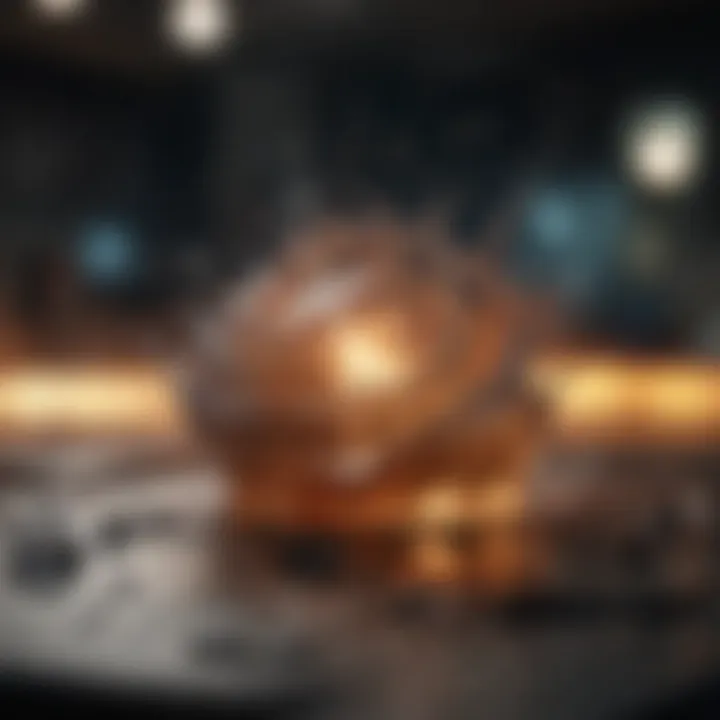
Integration of IoT in Measurement Systems
IoT represents a quantum leap in how measurements are taken and analyzed in real-time. When sensors are connected through the IoT, they generate vast amounts of data that can be gathered, analyzed, and utilized to optimize processes in manners that were previously undreamed of.
- Remote Monitoring: With IoT-enabled displacement sensors, professionals can now monitor changes from afar. For instance, a manufacturing facility can track the alignment of equipment without being physically present. Such access brings flexibility and allows for quick responses to potential issues.
- Data Integration: Sensors powered by IoT can communicate with each other and amalgamate data streams, providing a holistic view of operational metrics. This integration can lead to insights that simply wouldn’t surface in traditional measurement paradigms.
- Predictive Maintenance: Coupled with analytics tools, IoT systems enable predictive maintenance strategies. For example, if a sensor detects unusual displacement patterns, it can trigger an alert, allowing preemptive action to avert costly downtimes.
In essence, IoT not only makes measurement smarter but it also enhances decision-making processes in various fields including manufacturing, healthcare, and civil engineering.
"IoT is not just about connecting machines; it's a revolution in how we comprehend and interact with data.”
Use of Machine Learning for Predictive Analytics
Machine learning (ML) acts as the brain behind the analysis of vast datasets generated by modern measurement techniques. By employing algorithms that can learn from data trends, machine learning is taking displacement measurement into uncharted territories.
- Pattern Recognition: The first step in ML's application is the ability to recognize patterns within large sets of data. For instance, if a manufacturing plant collects displacement data from various stages of production, ML can identify trends that align with defects in finished products.
- Automated Decision Making: By processing real-time data, machine learning algorithms can make automated decisions about when to intervene in a manufacturing process. If a sensor linked to displacement measurement detects anomalies, the system could autonomously reorder materials or alert technicians.
- Tailored Solutions: Machine learning also facilitates custom solutions. Different industries require varied approaches to displacement measurement, and ML can adapt its predictions and recommendations based on specific industry needs, leading to optimized operational efficiency.
Case Studies in Displacement Measurement
Exploring case studies in displacement measurement illuminates not only the effectiveness of various methods but also the real-world applications that confirm their value. By delving into specific scenarios where these techniques are employed, we gain insights into the nuances, benefits, and challenges of displacement measurement in practice. This exploration is essential because it highlights how theoretical principles translate into actionable, impactful solutions across industries.
Industrial Automation
In the realm of industrial automation, displacement measurement technologies hold paramount significance. Companies like Siemens and Bosch have implemented precise measurement systems to enhance product quality and operational efficiency. For instance, a factory may utilize linear variable differential transformers (LVDTs) to monitor the position of a robotic arm. Such precision ensures that the robotic movements are repeatable, minimizing errors that can lead to costly defects.
Moreover, as production lines evolve toward smart factories with integrated IoT devices, displacement sensors play a crucial role. They not only provide real-time positioning data but also contribute to predictive maintenance. By analyzing displacement data, machines can predict potential failures, which helps prevent outages and prolongs equipment life. Thus, the implementation of these displacement measurement techniques shows substantial operational benefits while also promoting sustainability through reduced waste.
Geotechnical Monitoring
Displacement measurement is vital in geotechnical monitoring, particularly in assessing the stability of structures such as dams, tunnels, and slopes. In one notable case, the monitoring of a large dam's displacement using towed extensometers allowed engineers to detect early signs of rock movement. This proactive approach is crucial—catching changes early can save lives and reduce the risk of catastrophic failures.
Tools like inclinometers and settlement plates are often employed to accurately gauge soil movement or shifts in structural integrity. For example, during the construction of a new residential area built over a former landfill, continuous monitoring of ground displacement has been critical. By analyzing the measurements over time, engineers can make informed decisions on foundation adjustments, ensuring long-term safety and stability.
In complex environments where ground conditions can change rapidly, these measurement techniques also afford stakeholders a chance to act on data-driven insights, strengthening both safety protocols and engineering practices.
Robotics and Mechatronics
Robotics and mechatronics combine mechanical engineering, electronics, and computer science, making precise displacement measurement an absolute necessity. In the development of autonomous robots, effective navigation relies heavily on accurate displacement sensing. Companies like Boston Dynamics leverage advanced displacement sensors to enable their robots to interact seamlessly with their environments.
Take, for instance, a scenario where a robot is tasked with assembling small components on a production line. Utilizing optical displacement sensors, the robot can adjust its movements in real-time based on feedback, ensuring that components are placed with minute accuracy. This not only augments the efficiency of the manufacturing process but also allows for more complex operations that were previously thought impractical.
Furthermore, the integration of displacement measurement within robotic systems has led to enhanced capabilities in various fields—from healthcare, where precision is crucial for surgeries, to agriculture, where robots are now capable of delicate tasks like planting seeds at optimal soil depth.
Ultimately, these case studies not only demonstrate the significance of displacement measurement in diverse industries but also reveal the potential for ongoing advancements. As technologies develop, the continual enhancement of these measurement techniques will pave the way for smarter solutions in the future.
Future Trends in Displacement Measurement
As we step into an era dominated by technological evolution, the realm of displacement measurement is not left behind in the dust. Recognizing the pivotal role this field plays across various sectors, from industrial settings to healthcare, exploring future trends is both timely and essential. In this section, we shall delve into the shifts that promise to enhance accuracy, accessibility, and adaptability in displacement measurement techniques, making it more relevant than ever.
Miniaturization of Sensors
The movement towards miniaturization of sensors is now more prevalent, reflecting a broader trend in technology where smaller, yet highly efficient instruments take center stage. This trend is not just about shrinking physical size but integrating additional functionalities while maintaining or even improving precision. For instance, sensors used in environments where space is a premium—like in robotics or in applications within the human body—are embracing compact designs.
Some key advantages of this trend include:
- Improved integration into existing systems: Smaller sensors can easily nestle into complex machinery or devices without requiring significant design overhauls.
- Cost-effective solutions: Smaller sensors often equate to lower production costs, potentially passing savings to consumers.
- Enhanced performance: Innovations in materials mean these tiny devices can still deliver accurate readings, thanks to advancements in micro-electromechanical systems (MEMS) technology.
Adapting to miniaturization can cater to specific sectors like healthcare, where wearable devices need accurate displacement measurements sans bulkiness. Think of fitness trackers that can monitor bodily movement with precision while being almost unnoticeable.
Enhanced Data Analytics Techniques
In the age of big data, the importance of effective data analytics techniques cannot be overstated. Gone are the days when data collection was the endgame. Today, we’re in a battle of sifting through information efficiently to glean actionable insights, and this holds true for displacement measurement as well.
With the integration of advanced analytics, here's how the field is evolving:
- Predictive Maintenance: By analyzing displacement data over time, industries can anticipate equipment wear and tear, allowing for proactive maintenance strategies, thereby reducing downtime.
- Real-time Monitoring: Advanced algorithms enable real-time data processing, which is crucial in applications that require immediate responses—like in asset tracking systems or monitoring structural integrity in real-time in civil engineering.
With these developments, the importance of collaboration between data scientists and engineers becomes clear. Together, they can innovate strategies that not only enhance measurement accuracy but also harness the power of data for better decision-making across industries.
"In a world where precision and data are king, the collaboration of disciplines will unlock the doors to a smarter future in displacement measurement."
These emerging trends signify the blueprint for the future of displacement measurement techniques. By focusing on miniaturization and enhancing analytics, we’re on the brink of breakthroughs that promise to redefine how we approach measurement and its applications.
Culmination
In the realm of scientific research and engineering, the significance of accurate displacement measurement cannot be understated. This article has delved into various aspects of this essential topic—from the fundamental principles that lay the groundwork to the contemporary techniques that enhance precision across numerous fields. Displacement measurement plays a crucial role in ensuring safety, efficiency, and quality across industries like manufacturing, civil engineering, and biomedical applications.
By grasping the nuances of different methods, whether mechanical or electromagnetic, professionals can select the most appropriate tools for their specific needs. Moreover, this exploration of displacement measurement reflects on the advancements that have redefined the landscape, like the incorporation of IoT technologies and predictive analytics.
Notably, understanding the challenges presented by environmental factors or calibration issues can allow practitioners to mitigate risks and make informed decisions when selecting measurement techniques.
Summary of Key Insights
- Diverse Techniques: This piece illustrated a variety of displacement measurement methods, such as dial indicators, laser sensors, and digital encoders, highlighting their respective benefits and applications.
- Industry Relevance: Industries heavily depend on accurate displacement measurement for quality control and innovation, proving that precision is non-negotiable in success.
- Technological Evolution: The article emphasized advancements like machine learning integration, pushing the boundaries of what's possible in measurement technologies and driving industry growth toward smarter solutions.
Final Thoughts on Future Research Directions
The future of displacement measurement technology appears promising, with several avenues ripe for exploration. There’s a clear trend toward miniaturization, making sensors even more accessible for applications where space is at a premium. Future research could focus on:
- Integration with Smart Systems: As devices become interconnected, displacement measurement systems could leverage real-time data analysis.
- Enhanced Materials: Advancements in materials science may yield sensors that are not only more robust but also capable of operating in harsher environments.
- User-Centric Design: As technology rapidly evolves, there's room for user-focused innovations, ensuring that even non-specialists can accurately utilize sophisticated measurement tools.