Digital Tachometer: Comprehensive Insights and Impact
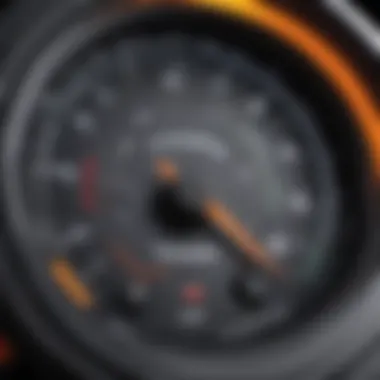
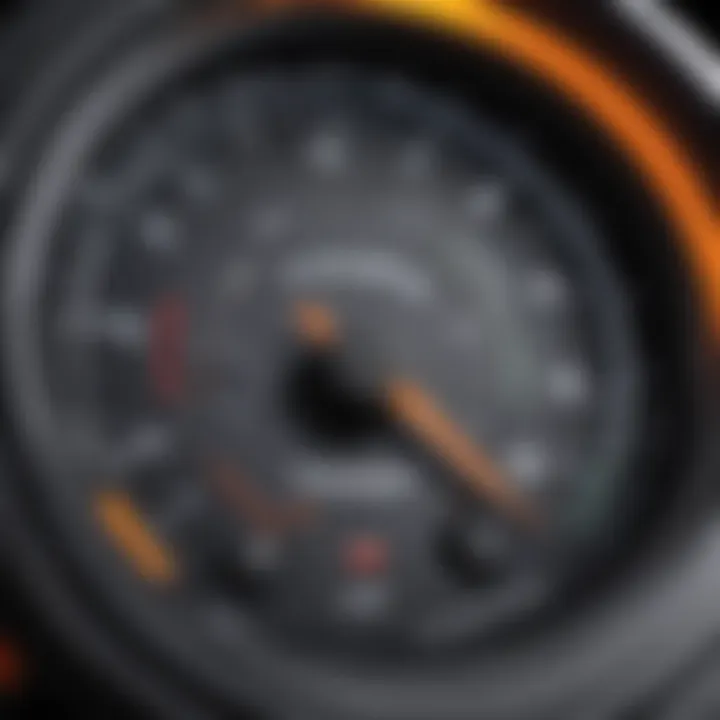
Intro
Digital tachometers are essential tools in various fields of engineering and manufacturing. They measure the rotational speed of an object, providing critical information for performance assessment. Understanding their operational principles and technologies can be very useful for students, researchers, educators, and professionals.
The rise of digital tachometers has transformed how industries approach speed measurement. Unlike their analog counterparts, digital versions offer improved accuracy, better data visualization, and advanced functionality. This article will explore these aspects in detail, focusing on technological advancements, applications, and limitations in current designs.
Further, this exploration will clarify the significance of digital tachometers in the context of modern engineering processes. As industries continue to move towards automation and data-driven decision-making, the relevance of these devices will only increase.
Readers can expect to gain insights into technical specifications, advantages of digital over analog mechanisms, and future trends that may shape this area of technology.
Prelude to Digital Tachometers
Digital tachometers have become integral in many precision-focused industries. This segment aims to explore their importance, offering insights into their definition, historical context, and applications. Understanding digital tachometers can reveal their operational advantages in monitoring rotational speed and performance metrics, significantly enhancing efficiency in various engineering fields.
Definition and Purpose
A digital tachometer is an electronic device that measures the rotational speed of an object, often displayed in revolutions per minute (RPM). Unlike mechanical tachometers, digital versions utilize advanced tech, allowing for rapid and accurate readings. The primary purpose of a digital tachometer is to provide real-time speed data, which is crucial for monitoring and maintaining optimal operational efficiency in machinery and vehicles.
This device serves multiple roles across industries, from guaranteeing safety in automotive engineering to ensuring the integrity of industrial machinery. By providing precise measurements, digital tachometers help optimize performance and reduce the risk of equipment failure. In scenarios of high-speed machinery, this accuracy becomes even more crucial, as improper readings can lead to malfunctions or accidents.
Historical Development
The evolution of tachometers is a fascinating journey through engineering advancement. The first tachometers emerged in the late 19th century, primarily as mechanical devices. These instruments were rudimentary, relying on gears and mechanical linkages. However, with the progression of electronic technology in the mid-20th century, a transformation began to take place.
The introduction of electronic tachometers marked a significant shift in measurement accuracy. Early electronic models utilized analogue signals, allowing for improved speed reading but still lacked the precision offered by current technologies. Over time, the implementation of digital circuits in the 1980s led to the development of modern digital tachometers.
Today, digital tachometers benefit from microcontroller technology, enhancing their functions. They are now capable of delivering faster and more reliable readings, mitigating errors introduced by mechanical components. This progression reflects a broader trend in industrial equipment towards more precise and efficient measurement systems.
Understanding Tachometric Principles
Understanding tachometric principles is central to grasping how digital tachometers function and their role in various applications. This section elucidates the fundamental operating mechanisms and measurement accuracy which are pivotal in ensuring the reliability of data provided by these devices. Delving into these principles helps illustrate the technological advantages of digital tachometers over older analog systems and emphasizes their significance in precision engineering and manufacturing.
Basic Operating Principles
Digital tachometers operate by converting the rotational speed of an object into a digital signal. This conversion occurs through the use of input sensors, typically based on optical or electromagnetic principles. Common sensors include Hall effect sensors or optical encoders, which detect the rotation of an object and send corresponding signals to a processing unit.
Once the signals are captured, the tachometer's internal processing unit interprets the data. This data conversion process often involves algorithms that filter out noise, ensuring the readings are as accurate as possible. Most modern digital tachometers present the information on a digital display, providing technicians with immediate and clear information about rotation speeds.
Several factors influence the operation of a digital tachometer. First, the choice of sensor plays a significant role in determining the accuracy and reliability of measurements. Different applications may require different sensing techniques to optimize performance. The calibration process is also vital, as any miscalibration can lead to significant deviations in the readings.
Measurement Accuracy
Measurement accuracy is a critical component in the performance of digital tachometers. High accuracy ensures that the speed readings are reliable and useful for making informed decisions in industrial applications. To achieve high standards of accuracy, a combination of high-quality sensors, effective signal processing, and precise calibration techniques is needed.
In practice, there are various parameters affecting the accuracy of measurements in digital tachometers:
- Sensor Quality: Higher quality sensors tend to provide more consistent and accurate readings.
- Environmental Factors: External conditions, such as temperature and electromagnetic interference, can influence sensor performance.
- Calibration Techniques: Regular calibration is essential to maintain the accuracy over time.
Regular calibration of digital tachometers is not just recommended; it is essential for maintaining data integrity.
Techniques like zeroing and span adjustment can significantly enhance the system's overall precision. Understanding the sources of measurement errors helps in developing robust solutions to mitigate these issues.
In summary, understanding the basic operating principles and the factors influencing measurement accuracy is vital for leveraging digital tachometers effectively. This knowledge enables users to select the appropriate devices and maintain optimal performance standards, crucial in today's precision-dependent industries.
Comparison with Analog Tachometers
Comparing digital tachometers with their analog counterparts is essential for understanding their unique advantages and applications. Digital tachometers have generally surpassed analog systems due to their ability to process data in real time, providing more accurate readings that are easily interpretable. This section delves into the technological differences and the accuracy and calibration aspects that differentiate these two types of tachometers.
Technological Differences
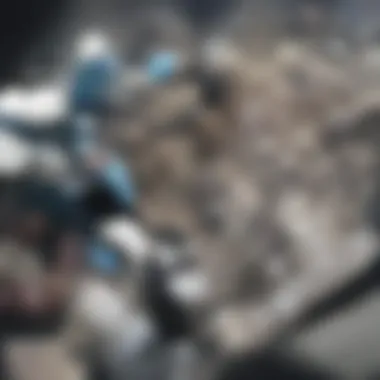
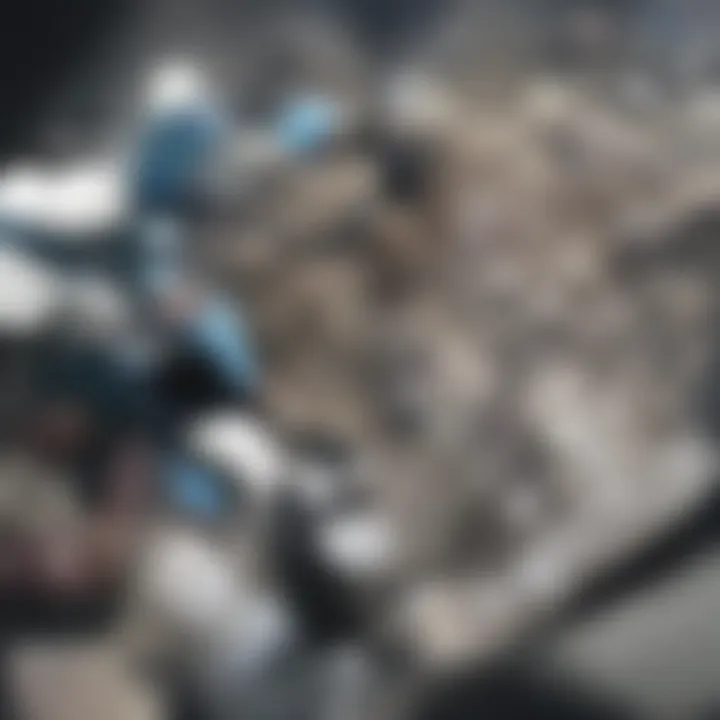
Digital tachometers utilize electronic sensors to detect the rotational speed of a shaft or engine, converting this data into digital output. This method typically involves the use of gear teeth sensors, optical sensors, or magnetic sensors. Each of these technologies comes with its own strengths. For instance, optical sensors may offer greater accuracy in applications requiring fine measurements, whereas magnetic sensors are often favored for their robustness in adverse conditions.
In contrast, analog tachometers rely on mechanical components to display speed. They often use a needle that moves along a graduated dial. This system can be less precise and may suffer from lag or drift over time. Furthermore, analog devices might require recalibration more frequently and do not provide the versatility offered by digital readouts. Digital tachometers can also sometimes interface directly with computers and other digital equipment, allowing for more advanced monitoring and control features.
Moreover, the display interfaces of digital devices offer various visual representations, such as graphs or numeric displays, enhancing user interpretation of data. This capability contrasts with the often limited display functionality of analog tachometers, making the latter less intuitive for immediate data assessment.
"Technology has evolved to prioritize accuracy and sensory feedback, making digital tachometers more aligned with the needs of modern industries."
Accuracy and Calibration
The accuracy of a tachometer is fundamental to its utility, and digital tachometers excel in this area. They provide real-time updates on speed, allowing for adjustments and optimizations in various engineering processes. Calibration plays a critical role in ensuring that tachometers provide reliable measurements. Digital tachometers typically feature built-in self-diagnostics and automated calibration mechanisms. This not only helps maintain accuracy but also reduces the need for manual intervention.
On the other hand, analog tachometers may involve more extensive manual calibration efforts, which can be prone to human error. Additionally, as analog systems age, their accuracy may diminish due to wear and tear on mechanical components. Therefore, industries striving for precision should consider the superior calibration capabilities of digital systems.
Key Components of Digital Tachometers
Understanding the key components of digital tachometers is essential for grasping how these devices function. Each element plays a crucial role in ensuring the tachometer operates effectively and delivers accurate performance readings. The significance of these components extends beyond mere operation, as they collectively contribute to reliability, precision, and user experience. Focusing on these critical elements allows for better insights into the device's efficiency and utility across various fields.
Input Sensors
Digital tachometers rely heavily on input sensors to capture the rotational speed of machinery or vehicles. Common types of these sensors include inductive sensors, optical sensors, and Hall-effect sensors. Each type has advantages based on specific application needs.
- Inductive sensors detect magnetic fields produced by moving components. They are suitable for harsh environments.
- Optical sensors employ light to gauge the speed of the rotating object. This sensor type is generally accurate but can be limited by environmental conditions.
- Hall-effect sensors work on the principle of magnetic fields and are known for their compact size and affordability.
In most cases, the choice of sensor directly affects accuracy and responsiveness. The ability to select appropriate sensors is therefore vital for optimal performance, especially in high-precision applications such as automotive engineering and aerospace.
Signal Processing Modules
Once the input sensors gather data, the next step involves signal processing. This is delivered by specific modules designed to convert the raw data obtained from sensors into meaningful information. Signal processing modules filter out noise and refine the readings to enhance accuracy.
These modules utilize advanced algorithms to interpret signals and translate them into digital formats. Important functions performed by these modules include:
- Filtering out interference and noise.
- Amplifying weak signals to improve reliability.
- Converting analog signals to digital data, which is essential for displaying results comprehensibly.
The effectiveness of signal processing plays a critical role in the performance of digital tachometers. Accurate signal interpretation allows for timely decision-making and enhances overall system efficiency.
Display Interfaces
The final component of digital tachometers involves display interfaces. These interfaces translate the processed data into user-friendly formats, aiding operators in real time. Common display types include Liquid Crystal Display (LCD) and Light Emitting Diode (LED).
Display interfaces are essential for presenting speed information clearly and understandably. Factors to consider when evaluating display interfaces include:
- Readability: Ease of understanding the displayed data is vital, especially in high-stakes environments.
- Response Time: The quicker a display updates with new information, the better it can aid operational adjustment.
- Additional Features: Some displays may offer illuminated backgrounds or touch capabilities for enhanced usability.
Proper selection of display interfaces enhances the user experience significantly. It enables better management of machinery and ultimately supports the goals of efficiency and precision in various industries.
Applications of Digital Tachometers
Digital tachometers play a critical role in various industries by providing accurate rotational speed measurements. Their ability to deliver real-time data enhances operational efficiency and safety. In this section, we will delve into the specific applications of digital tachometers across different domains, emphasizing their benefits and importance.
Industrial Machinery
In the industrial sector, the use of digital tachometers is widespread. They are essential in monitoring the performance of heavy machinery. Accurate readings help prevent over-speed conditions, which can lead to equipment failure. For instance, in manufacturing plants, motors and generators are often equipped with digital tachometers to ensure optimal functioning.
Aside from performance monitoring, digital tachometers facilitate predictive maintenance. By analyzing speed trends, maintenance teams can schedule services before significant issues arise. This proactive approach reduces downtime and maintenance costs.
Digital tachometers contribute to improved process control and operational reliability in industrial settings.
Automotive Engineering
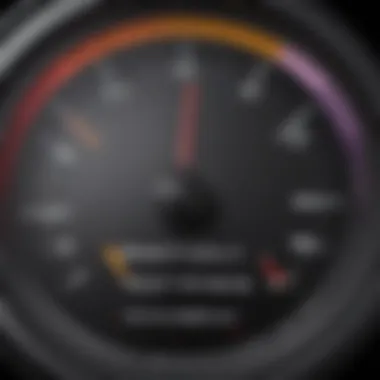
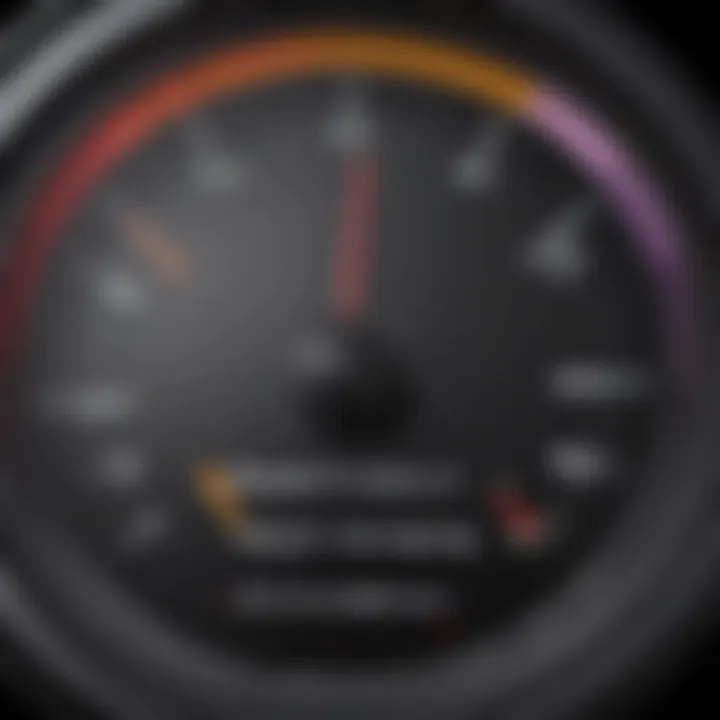
The automotive industry leverages digital tachometers for various applications, including engine diagnostics and performance tracking. They provide precise information about engine RPM, which is crucial for both fuel efficiency and emissions control. Engineers utilize this data to design engines that maximize performance while minimizing environmental impact.
Moreover, digital tachometers are integral in the development of advanced driver assistance systems (ADAS). Functions such as adaptive cruise control depend on real-time speed feedback from tachometers. This technology supports safer driving conditions by allowing vehicles to adjust speed automatically based on traffic.
Aerospace Applications
In aerospace, digital tachometers are vital for ensuring the safe operation of aircraft engines. They measure rotational speeds, providing critical data that pilots and engineers analyze for performance assessments. The information gathered is indispensable for flight safety and operational efficiency.
Furthermore, digital tachometers assist in monitoring rotor speeds in helicopters. Accurate speed readings are essential during flight operations to maintain stability and control. The aviation industry's strict safety standards make tachometers an integral component of any aircraft's instrumentation.
Benefits of Digital Tachometers
Digital tachometers present numerous advantages that enhance their utility across various fields. Understanding these benefits is crucial for industries that rely on precise measurements of rotational speed. This section delves into key aspects such as real-time monitoring, data logging, analysis capabilities, and improved user interfaces. These elements underscore the significance of digital tachometers in advancing operational efficiency and accuracy.
Real-Time Monitoring
One of the primary benefits of digital tachometers is their ability to monitor rotational speed in real-time. This feature allows users to observe performance metrics instantly, facilitating immediate adjustments to machinery if needed. In industries like manufacturing, where timing and precision are critical, real-time monitoring helps prevent equipment malfunctions, reducing downtime and maintenance costs.
Additionally, real-time data can generate alerts for anomalies, enabling swift responses to abnormal operation conditions. This capability is especially important in safety-sensitive environments, where maintaining operational integrity is vital. The speed and accuracy of the data provided by digital tachometers support better decision-making and operational management.
Data Logging and Analysis
Data logging is another significant advantage offered by digital tachometers. These devices can store large amounts of data for future reference and analysis. By capturing historical data, organizations can identify patterns and trends in machinery performance over time. This information is invaluable for predictive maintenance strategies, which help to anticipate potential points of failure before they occur.
Furthermore, data analysis enables engineers and technicians to enhance processes. They can assess the effectiveness of operational adjustments and make informed decisions based on empirical evidence. This systematic approach reduces guesswork, leading to optimized performance and resource allocation. The capability to analyze and visualize data can also support compliance with regulatory requirements, by documenting key operational metrics.
Improved User Interface
Digital tachometers often come equipped with user-friendly interfaces. This improves accessibility for operators with varying levels of technical expertise. A clear display helps in quick comprehension of readings, facilitating straightforward interpretation of machine performance metrics.
Many modern digital tachometers include features such as touchscreens and customizable displays. These improvements enhance user engagement and reduce operational errors. Operators can focus on critical data without being overwhelmed by unnecessary information.
Improved interfaces not only foster better comprehension but also contribute to more efficient training for new staff.
In summary, the benefits of digital tachometers lie in their real-time monitoring abilities, effective data logging, and analysis features, as well as user-friendly interfaces. These aspects collectively elevate the role of tachometers in enhancing accuracy, efficiency, and operational reliability across various industries. As more industries embrace these advanced tools, the potential for innovation and improvement in performance becomes increasingly significant.
Limitations of Digital Tachometers
Despite the numerous advantages offered by digital tachometers, it is crucial to recognize their inherent limitations. Awareness of these constraints can help users make more informed decisions when selecting measurement instruments. Understanding these challenges is essential for students, researchers, educators, and professionals who are exploring this technology and its impact on various fields.
Cost Implications
One prominent limitation of digital tachometers is their cost. Generally, digital models are more expensive than their analog counterparts. This higher price tag can deter small businesses or organizations with budget constraints from adopting this technology. The costs involved include not just the purchase of the tachometer itself, but also expenses related to installation, maintenance, and training. In some cases, companies may find it challenging to justify the investment, especially if they are already using satisfactory analog tachometers.
In addition, ongoing expenses related to software upgrades and system integrations can increase the total cost of ownership. Organizations must evaluate whether the benefits such as improved accuracy and enhanced functionality outweigh the financial investment required for digital tachometers.
"Cost considerations often dictate the choice between digital and analog systems in various industries."
Susceptibility to Interference
Another significant limitation of digital tachometers is their susceptibility to electromagnetic interference. This can affect the accuracy and reliability of readings. Various environmental factors, such as nearby high-power equipment, can introduce noise into the system, resulting in erroneous data output. This interference can come from other electronic devices, power lines, or even grounding issues.
To mitigate this issue, manufacturers often incorporate shielding and filtering techniques, but such measures can add complexity and cost to the system. In high-precision applications, failing to account for potential interference can lead to critical errors. Ensuring that the environment where the tachometer operates is free from such disturbances is essential for maintaining measurement integrity.
In summary, while digital tachometers present several advantages, it is important to consider their limitations, particularly regarding cost implications and susceptibility to interference. Recognizing these challenges can lead to more effective utilization of this technology in various applications.
Future Trends in Digital Tachometry
The future of digital tachometry holds substantial promise as technology continues to evolve rapidly. The integration of emerging technologies enhances the functionality and application range of digital tachometers. Focusing on future trends is essential for understanding how these devices will adapt to industry demands and advancements.
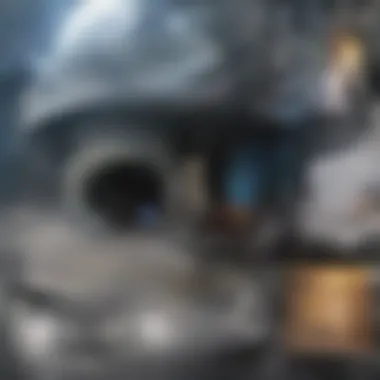
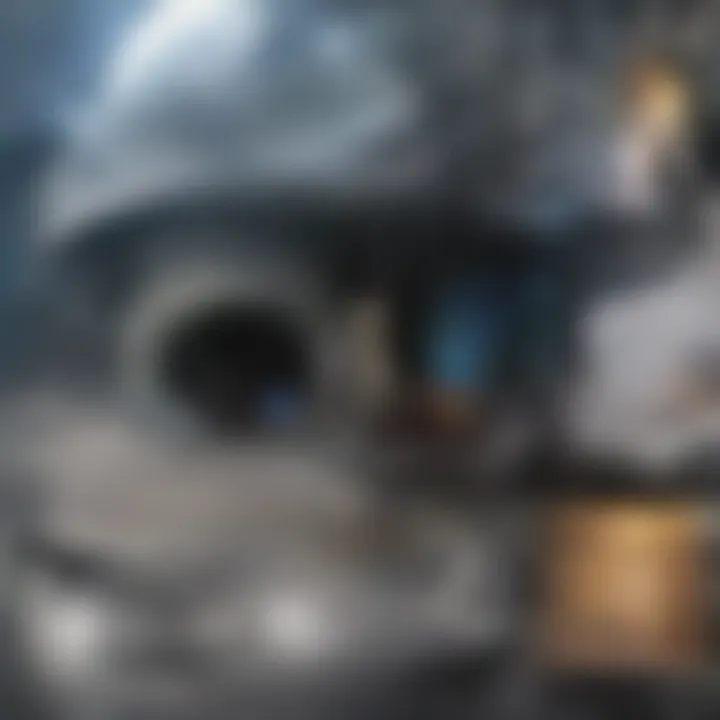
Integration with IoT
Integrating digital tachometers with the Internet of Things (IoT) represents a significant leap forward in measurement technology. IoT enables devices to connect and communicate over the internet, allowing for real-time data monitoring and analysis.
- Remote Monitoring: With IoT integration, users can monitor tachometer readings from anywhere. This remote accessibility is crucial for large manufacturing operations where machinery may be spread across multiple sites.
- Data Analytics: Access to vast amounts of data allows for sophisticated analytical models. Organizations can analyze performance trends to improve operational efficiency.
- Predictive Maintenance: IoT enables predictive maintenance by providing insights into machinery conditions. Adjustments can be made proactively before failures occur, reducing downtime and repair costs.
The advantages of IoT integration are vast. However, it also raises considerations about cybersecurity and the need for secure data transmission. A strong cybersecurity framework ensures that sensitive operational data stays protected.
Advancements in Sensor Technology
Enhancements in sensor technology are transforming the capabilities of digital tachometers. The movement towards more accurate, reliable, and faster sensors offers a range of benefits.
- Higher Precision: Newer sensors provide improved accuracy in measuring rotational speed. This precision is critical for applications where even slight variations can impact performance.
- Miniaturization: Advances in manufacturing allow for smaller but powerful sensors. Miniaturization facilitates installation in compact or hard-to-reach areas, expanding the usage cases for digital tachometers.
- Enhanced Durability: Modern sensors are engineered to withstand harsh operational environments, such as extreme temperatures or high vibration. This durability translates to longer service life and decreased maintenance needs.
Collectively, these advancements increase the reliability and effectiveness of digital tachometers. Future enhancements in sensor technology will likely continue to shape how these devices are used across various industries.
Looking Ahead: As digital tachometers continue to evolve, they will play a critical role in the automation and efficiency of various industrial processes.
Case Studies in Digital Tachometer Implementation
Digital tachometers serve as vital tools within various industries. Their functionalities extend beyond mere measuring of rotational speed. In this section, we will explore case studies that highlight their application in specific sectors, particularly manufacturing and automotive. Understanding these implementations helps to underscore the benefits and considerations associated with digital tachometer use.
Manufacturing Sector
In manufacturing, precision and efficiency are crucial. Digital tachometers play a significant role in maintaining both. For example, a manufacturing plant might integrate digital tachometers into its machinery to monitor spindle speed in real-time. This data allows operators to adjust processes immediately, ensuring optimal performance.
Benefits observed include:
- Enhanced Accuracy: Digital tachometers provide precise measurements, reducing errors that can occur during manual checks.
- Increased Productivity: Real-time monitoring allows for quicker adjustments, minimizing downtime and improving workflow.
- Data Analysis: The ability to log speeds over time enables trend analysis, helping to identify opportunities for process improvements.
A case study in a Chicago-based automotive parts manufacturing facility reveals that implementing digital tachometers led to a 20% increase in overall production efficiency. By accurately measuring machine speeds and optimizing them, the facility could produce parts faster without sacrificing quality. This underscores the transformative impact of digital tachometers in complex manufacturing environments.
Automotive Industry
The automotive industry has also embraced digital tachometers due to the increasing complexity of modern vehicles. In this context, they are leveraged to enhance performance monitoring and diagnostics. For example, a major automotive manufacturer employed digital tachometers in engine testing facilities to ensure that new engines meet stringent performance specifications.
Key considerations include:
- Integration with Systems: Digital tachometers can be integrated with on-board diagnostics to provide comprehensive data for engineers.
- Performance Monitoring: Continuous speed measurement helps in assessing engine performance, leading to better design and troubleshooting.
- Regulatory Compliance: Many automotive standards require precise measurements during the testing phase, making digital tachometers essential.
In a successful instance, a digital tachometer system was employed in a testing laboratory of a leading car manufacturer. This system provided vital speed metrics for various engine prototypes. The immediate feedback facilitated rapid adjustments and refinements to designs. Consequently, this led to a quicker time to market and ensured compliance with international standards.
"The integration of digital tachometers into testing processes not only aids in performance evaluation but also accelerates innovation in product development."
Overall, these case studies illustrate the multifaceted benefits of digital tachometers in both the manufacturing and automotive sectors. They enable a level of precision and efficiency that is invaluable in today's competitive landscape. This in-depth analysis sets the stage for further exploration of digital tachometers, paving the way for future advancements and applications.
Finale
In this article, we have established the significance of digital tachometers within various industries. As a key component in monitoring and regulating rotational speeds, they bring precision and efficiency. Understanding the functionalities and applications of digital tachometers can lead to quality improvements in both manufacturing and engineering practices.
Summary of Key Points
Digital tachometers exhibit numerous advantages over their analog counterparts. First, they provide greater accuracy and can offer real-time data logging. This is essential for industries that rely on meticulous performance measurement.
- They integrate easily with modern machinery, enhancing automation.
- User interfaces are typically more intuitive, allowing for quicker data interpretation.
- Their adaptability in various sectors—spanning from aerospace to manufacturing—illustrates their versatility.
Moreover, as technology progresses, the integration of Internet of Things (IoT) capabilities into digital tachometers is set to reshape how data is collected and analyzed. This advancement promises heightened efficiency and better operational insights.
Implications for Future Research
Future exploration in the field of digital tachometry presents exciting opportunities. Research may focus on the following areas:
- Enhanced Sensor Technologies: Innovations in sensor design could lead to improved accuracy and responsiveness, adapting to even more complex machinery and environmental conditions.
- Data Integration Methods: Developing more sophisticated algorithms for data processing may enable contextual analysis that draws on a wider array of operational data points.
- User-Centric Design: As the industry demands simplicity while retaining functionality, future studies should consider designing interfaces that harmonize advanced features with ease of use.
The evolution of digital tachometers remains a pivotal subject. It is vital for researchers, engineers, and industry professionals to continue exploring this technology. Keeping pace with advancements ensures the continual enhancement of measurement efficiency across various fields.