Understanding Deep Drawing Tools in Manufacturing Processes
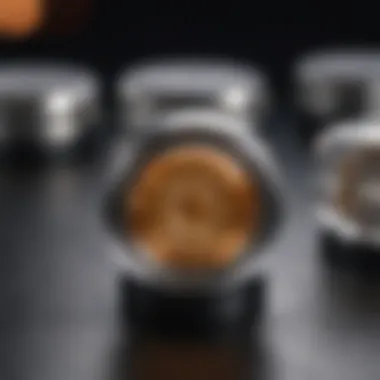
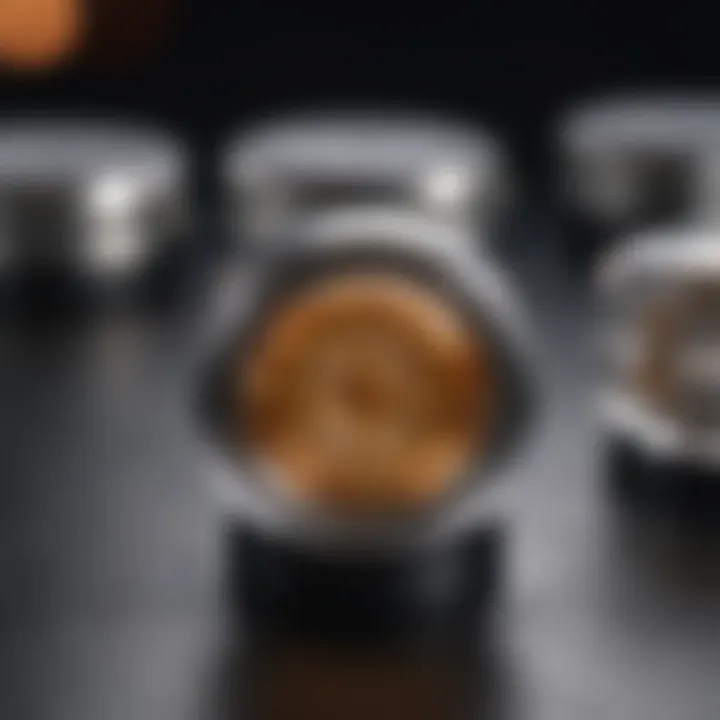
Intro
Deep drawing is a fundamental process in metalworking that allows for the creation of complex shapes. This technique plays a pivotal role in various manufacturing sectors including automotive, aerospace, and household appliances. The tools used in deep drawing are critical, as they enable precision and quality in production. Understanding these tools is essential for anyone involved in manufacturing and engineering.
In this article, we will examine the various aspects of deep drawing tools. This includes their types, materials used, design considerations, and the challenges faced during the process. Additionally, we will look into the advancements in tooling technology that are enhancing performance in deep drawing operations.
Key Findings
Major Results
- Deep drawing tools are categorized into various types such as punches, dies, and blanks. Each type serves a specific purpose in the process.
- The materials used in the construction of these tools significantly affect their performance. Common materials include tool steel and carbide.
- Design considerations include the tool geometry, wear resistance, and the intended application.
- The industry faces numerous challenges, including tool wear and material flow issues, which can impact product quality.
Discussion of Findings
The analysis reveals that selection of the right tool is essential for successful deep drawing operations. For instance, using high-quality tool steel can enhance tool life and reduce downtime for replacements. Environmental factors, like temperature and humidity, also have a direct impact on tool performance and must be controlled during manufacturing.
"Understanding the intricacies of deep drawing tools allows for better decision-making in tool procurement and design, ultimately impacting the efficiency of the manufacturing process."
Successful deep drawing processes rely on continual innovation and understanding of material properties. Manufacturers are increasingly incorporating advanced materials and techniques to overcome traditional challenges. Innovations, especially in tooling technology, are transforming how these processes are executed, contributing to higher efficiency and reduced costs.
Methodology
Research Design
The research combines qualitative and quantitative methods to analyze the effectiveness of various deep drawing tools. Discussions with industry experts and case studies from manufacturing environments provide insights into real-world applications.
Data Collection Methods
Data collection includes surveys targeting manufacturing professionals, observations of deep drawing processes, and analysis of existing literature. Collecting diverse perspectives ensures a comprehensive understanding of both the challenges and advancements in the field.
Preface to Deep Drawing Tools
Deep drawing tools play a significant role in metal forming. Understanding these tools is essential for grasping their function within various manufacturing processes. They help shape materials into intricate forms necessary for diverse applications, spanning from automotive to consumer goods. The modern manufacturing landscape increasingly relies on these tools to create parts that are both complex and efficient. Optimizing the understanding of deep drawing tools can lead to improved design, production techniques, and ultimately, better products.
Definition and Overview
Deep drawing is a manufacturing process that transforms flat metal sheets into three-dimensional shapes. The operation involves using various tools such as punches and dies. These tools work together to exert pressure on the sheet metal, causing it to deform and take the desired shape. This method is widely used due to its capacity for mass production and ability to create lightweight yet strong components. The process is instrumental in the production of items like automotive body panels, kitchen sinks, and chassis components.
Historical Context
The origins of deep drawing can be traced back to early metalworking practices. Initially, artisans used basic tools to form metal into simple shapes. As industrialization progressed during the 19th and 20th centuries, the demand for more complex components grew. This led to advancements in tooling technology.
The development of specialized materials for toolmaking improved the longevity and performance of deep drawing tools. In modern times, computer-aided design (CAD) has further refined the design process, allowing for precise and efficient tool creation. This progression demonstrates the ongoing evolution of deep drawing and its tools, reflecting broader trends in manufacturing.
Types of Deep Drawing Tools
Understanding the various types of deep drawing tools is crucial for manufacturing within the metalworking sector. Each type of tool has its unique function, application, and benefits. By comprehending these differences, manufacturers can optimize their processes for efficiency, precision, and quality. It enhances product development and ensures that components meet design specifications, which is vital in various industries such as automotive and electronics.
Punches
Punches in deep drawing are essential for initiating the forming process. They apply force to the blank material, pushing it into the die cavity to form the desired shape. The design of a punch affects how well it performs during production. Factors like the punch's geometry, material hardness, and surface finish are significant.
Manufacturers often select their punches based on the thickness of the metal, shape complexity, and required production rates. For instance, a punch must have a sharp edge to minimize the effort required for deformation.
Dies
Dies work in tandem with punches to provide the necessary support during the drawing process. They define the shape of the final product and must be designed with precision. Material selection for dies is critical. Tool steels such as D2 or A2 are common due to their hardness and wear resistance. The die design must also incorporate relief areas to prevent fractures or excessive wear during operation.
Proper die alignment with the punch is necessary. Misalignment can lead to defective parts and increased wear on tools. Understanding die maintenance is key to ensuring longevity and performance, maintaining the integrity of the manufacturing process.
Blank Holders
Blank holders play a crucial role in ensuring the material stays in place during the drawing operation. They exert uniform pressure on the blank, preventing wrinkling and ensuring the metal flows smoothly into the die cavity. The design of the blank holder needs to consider factors such as the type of material, its thickness, and the drawn part's complexity.
Using a dynamically adjustable blank holder can offer benefits, as it allows for variations in material thickness throughout a single run. This adaptability enhances the quality and consistency of the produced parts while minimizing scrap material.
Guides and Supports
Guides and supports are vital to maintaining the correct alignment and positioning of the tools involved in deep drawing. They ensure that punches and dies remain engaged throughout the forming process.
Without proper guides, there is a risk of tool misalignment, leading to defects or failures in the finished product. These components can be simple metal plates or more complex arrangements, depending on the scale and complexity of the operation. Investing in robust guides and supports is essential, particularly in high-volume production environments.
Materials Used in Deep Drawing Tools
The choice of materials utilized in deep drawing tools profoundly influences both the quality of manufactured products and the efficiency of production processes. Understanding the specific materials is crucial in ensuring that tools can withstand the mechanical stresses encountered during deep drawing operations. High-performance materials enhance tool life, improve precision, and reduce downtime, making the selection of suitable materials a fundamental consideration for manufacturers.
Tool Steels
Tool steels are predominantly used in the production of deep drawing tools due to their excellent wear resistance and hardness. These steels, which typically contain high carbon and alloying elements, allow for better performance under extreme conditions. The properties of tool steel can be customized through heat treatment, enabling manufacturers to select the appropriate hardness and toughness for their specific application.
Benefits include:
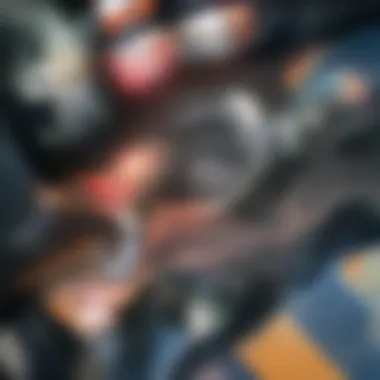
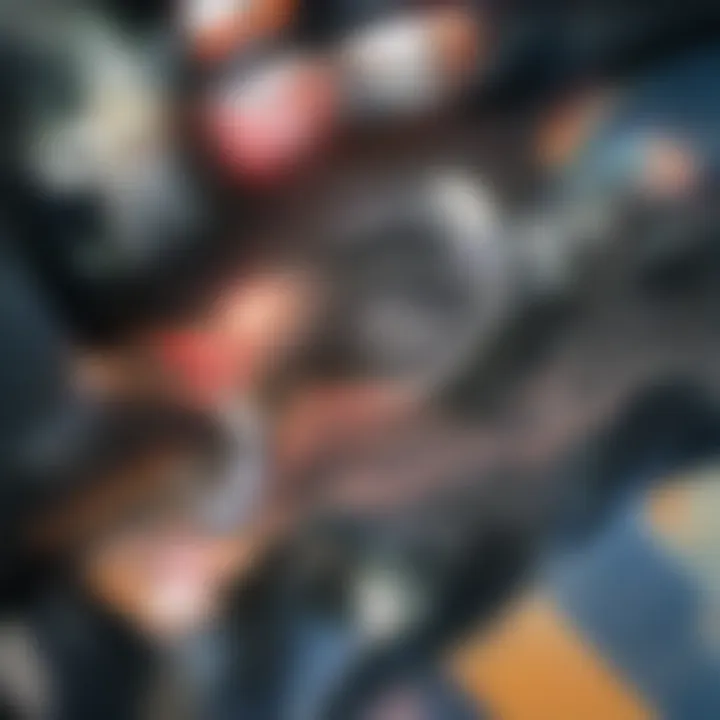
- High wear resistance ensures longer tool life.
- Good dimensional stability preserves the accuracy of the components produced.
- Heat-treated tool steels can withstand high pressures from the drawing process.
However, tool steels can also be more expensive than other materials. Additionally, they may require more extensive machining, impacting production time. Manufacturers must weigh these factors when choosing tool steels for their applications.
Aluminum Alloys
Aluminum alloys are another significant material used in deep drawing tools. They are particularly valued for their lightweight and corrosion-resistant properties. Aluminum tools can enhance the efficiency of the drawing process as they are easier to handle and maneuver than heavier steel counterparts.
Considerations include:
- Lower density reduces overall tool weight, aiding in handling and setup.
- Excellent corrosion resistance prolongs the lifespan of tools used in challenging environments.
- Some aluminum alloys offer good strength-to-weight ratios, making them suitable for certain applications.
Despite their advantages, aluminum alloys can exhibit lower wear resistance compared to tool steels. Therefore, they are often used in less demanding applications where extreme pressures are not a factor.
Coatings and Treatments
Coatings and surface treatments are critical in enhancing the performance and lifespan of deep drawing tools. These treatments improve properties such as wear resistance, reduce friction, and help protect against corrosion.
Common coatings and treatments include:
- Nitride Coating: Increases hardness and wear resistance, ideal for high-stress applications.
- PVD (Physical Vapor Deposition): Creates a thin film on the tool, improving surface hardness and lowering friction.
- Chromate Treatments: Provide corrosion resistance while helping to maintain the tool's lightweight and physical properties.
Ultimately, the application of coatings can significantly influence the overall cost-efficiency of the deep drawing process. However, it is essential to consider the compatibility of coatings with the base materials and the specific requirements of the production environment.
In summary, the selection of materials for deep drawing tools is a critical factor that determines their effectiveness and longevity. Tool steels and aluminum alloys each offer unique benefits, while coatings and treatments provide additional enhancements to performance. Understanding the intricacies of these materials ensures better decision-making in tool design and application.
Design Considerations for Deep Drawing Tools
In the realm of manufacturing, particularly within the context of deep drawing, the design of tools plays a pivotal role in determining the efficiency and quality of the produced components. This section delves into key design considerations necessary for ensuring successful deep drawing operations. Each element of design must be approached with precision, as the interplay of these factors significantly influences the outcomes in terms of production rates, material integrity, and overall device functionality.
Geometric Design Principles
The geometric design of deep drawing tools is fundamental for achieving desired shapes and dimensions in metal components. The angles, radii, and contours of punches and dies must be meticulously calculated to facilitate the optimal flow of material during the drawing process.
Misalignment or improper geometric features can lead to excessive thinning or defects like wrinkling. Therefore, when designing a tool, engineers must utilize simulations and models to predict how the materials will respond to various forces. The geometric principles must align with the properties of the materials used, ensuring compatibility to minimize failures during production.
Tolerances and Fits
Tolerances refer to the permissible limits of variation in a component's dimensions. In deep drawing, tight tolerances are often required to ensure that parts fit together correctly in final assembly. The design must consider the manufacturing capabilities and the characteristics of the materials utilized.
Selecting the right fit is critical; an excessively tight fit may complicate the drawing process, while a loose fit can lead to increased wear on the tools. Therefore, thorough analysis during the design phase can help to prevent complications during production, extending tool life while ensuring high-quality products.
Stress Distribution
Understanding how stress is distributed across deep drawing tools is crucial for their design. When forming metal components, uneven or excessive stress can lead to tool failure or deformation. Effective design must incorporate features that allow for uniform stress distribution across the surface of the tool.
Critical factors include the choice of materials and the geometric setup of the punch and die. By conducting stress analysis through finite element modeling, designers can evaluate how stress propagates through the tool under load conditions. Addressing these factors helps ensure both the durability of the tools and the integrity of the formed parts.
"Design considerations such as geometric principles, tolerances, and stress distribution form the backbone of effective deep drawing tools, impacting performance and product quality significantly."
Applications of Deep Drawing Tools
The applications of deep drawing tools illustrate their vital role in modern manufacturing. In various industries, these tools enable the production of precise metal components that meet specific design and functionality requirements. Understanding the applications can provide insights into the importance of deep drawing as a forming technique.
One significant aspect of deep drawing tools is their ability to produce complex shapes. The automotive industry, consumer electronics, and medical devices benefit from these capabilities. Each sector relies on deep drawing to create parts that are not only functional but also cost-effective to manufacture.
Automotive Industry
The automotive industry is one of the largest users of deep drawing technology. Components such as automotive body panels, engine parts, and chassis are often produced using this method. The necessity for lightweight yet durable materials in vehicles has increased the demand for deep drawing tools.
- Benefits:
- Cost efficiency in mass production.
- Ability to create intricate designs that improve aerodynamics.
- Enhanced material utilization, reducing waste.
For example, the production of door panels and fenders requires both high accuracy and strength. Here, deep drawing facilitates the creation of these components with minimal material deformation. The ability to produce large volumes of components quickly also contributes to the scalability of production.
Consumer Electronics
In the consumer electronics sector, deep drawing is crucial for manufacturing housing and enclosures. Devices like smartphones, laptops, and other gadgets rely on precise metal parts for both aesthetics and functionality.
- Advantages:
- High precision and repeatability in part production.
- Flexibility to adapt designs based on market trends.
- Integration of design elements that enhance user experience.
For instance, aluminum casings for laptops are often created through deep drawing. This method ensures that the casings are lightweight while providing the necessary protection. The visual appeal achieved through this process also plays a significant role in consumer preferences.
Medical Devices
The medical device industry also benefits immensely from deep drawing tools. Items such as surgical instruments, medical trays, and implant components require exact specifications for safety and performance.
- Key Considerations:
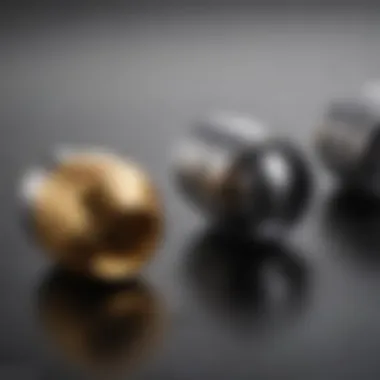
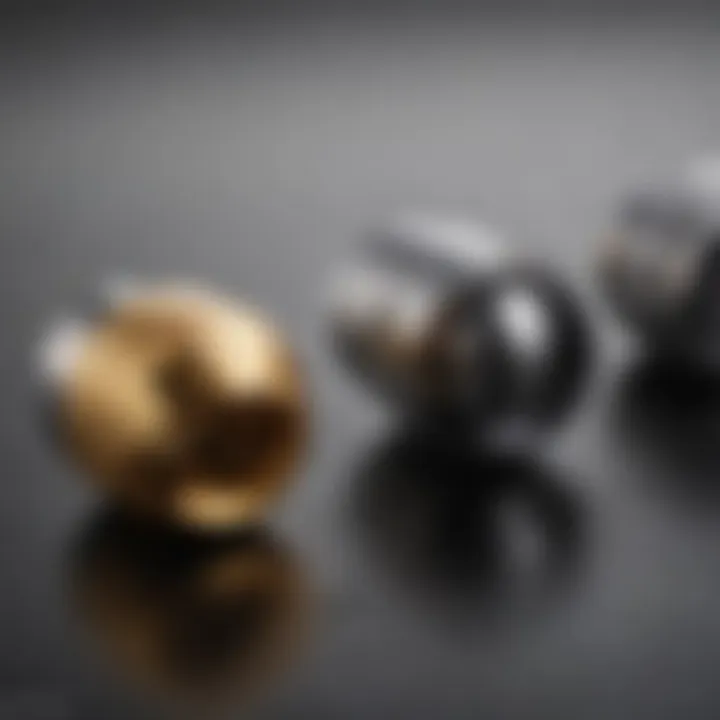
- Strict compliance with health regulations and standards.
- Necessity for precise shapes that ensure functionality.
- Ability to work with specialized materials designed for biocompatibility.
Deep drawing processes in this sector must adhere to stringent quality control measures. For example, surgical tools need to meet high levels of sterility and precision to function correctly.
In summary, the applications of deep drawing tools across industries not only highlight their essential functions but also underscore the relevance of advanced manufacturing techniques in meeting modern production demands.
"Deep drawing is not just about creating shapes; it's about innovating the future of manufacturing processes."
Understanding these applications is crucial for professionals looking to leverage deep drawing technology effectively in their respective fields. By recognizing how these tools fit into various industries, one can appreciate their significance in shaping the modern landscape of manufacturing.
Challenges in Deep Drawing Processes
Deep drawing is a vital manufacturing process used widely in the production of metal components. However, it is not without its challenges. Understanding these challenges is crucial for improving efficiency and quality in production. This section will discuss critical issues such as material thinning, wrinkling, defects, tool wear, and maintenance, providing insights that can assist in troubleshooting and optimizing deep drawing operations.
Material Thinning
Material thinning occurs when the metal sheet stretches during the deep drawing process. As the material conforms to the shape of the die, its thickness can decrease significantly. This has several implications. Thinner materials can reduce the mechanical properties of the final product, impacting strength and durability. To minimize thinning, it is essential to select appropriate materials and control process parameters effectively. An analysis of the following strategies can help mitigate material thinning:
- Material Selection: Choosing the right type of metal can help in managing thinning. For instance, aluminum alloys can be more forgiving than high-strength steels.
- Process Control: Monitoring and adjusting parameters such as punch speed and blank holder force may significantly reduce material deformation.
Employing simulation tools during the design phase can also forecast thinning effects before the actual manufacturing begins.
Wrinkling and Defects
Wrinkling occurs mainly due to uneven material flow and insufficient blank holding force during drawing. It presents both aesthetic and functional issues in the final product. Defects from wrinkling not only compromise the product's appearance but can also lead to failures under load. To combat this issue, manufacturers can employ several techniques:
- Optimal Blank Holder Force: Balancing the blank holder force ensures even material flow, preventing wrinkles from forming during drawing.
- Tool Geometry: Altering the shape of punches and dies can promote better material flow and minimize the risk of wrinkling.
- Controlled Speed: Operating the punching process at controlled speeds can reduce the likelihood of defects by ensuring a smooth material transition.
Continuous monitoring and real-time adjustments during the process can contribute significantly to reducing wrinkles, leading to enhanced product quality and performance.
Tool Wear and Maintenance
Tool wear is a common challenge in deep drawing processes, impacting both productivity and cost-effectiveness. As tools undergo repeated use, they experience wear, leading to reduced precision and increased defect rates. Regular maintenance and timely inspections become essential to prolong tool life. Some critical aspects related to tool wear include:
- Material Selection for Tools: Using high-quality tool steels, such as D2 or M2, can help improve the lifespan of the tools significantly.
- Surface Treatments: Application of coatings like titanium nitride can increase hardness and wear resistance.
- Regular Inspection: Establishing a routine for inspection can help in early detection of wear, allowing for timely repairs or replacements before quality suffers.
Maintaining adequate tool conditions is fundamental for ensuring consistent production quality and reducing downtime in operations.
Advancements in Deep Drawing Tool Technology
The landscape of deep drawing tool technology is evolving quickly. Innovation in this field brings substantial benefits for manufacturers. By implementing advanced tools, it is possible to achieve greater efficiency and improved product quality. Hence, the discussion of advancements in deep drawing tool technology is pertinent for anyone involved in the manufacturing sector. Understanding these advancements allows professionals to make informed decisions on tool selection and technology integration.
Computer-Aided Design (CAD) Integration
Integrating Computer-Aided Design (CAD) in deep drawing tool development marks a significant milestone. CAD software enables designers to create precise 3D models of tools before they are manufactured. This capability reduces errors in the design phase, ensuring more accurate fit and function. With CAD, designers can simulate the deep drawing process. This simulation helps identify potential issues, such as stress points or inefficiencies, allowing for modifications before actual fabrication.
Additionally, CAD promotes enhanced communication among teams. Engineers, designers, and manufacturers can collaborate effectively using shared digital models. This collaboration streamlines the design process and reduces lead times. The analytical capabilities of CAD also allow for optimization of parameters, such as thickness and material use, further increasing efficiency during production.
Additive Manufacturing Techniques
Additive manufacturing, commonly known as 3D printing, is transforming the landscape of deep drawing tools. This technology allows for the creation of complex geometries that are often unattainable with traditional manufacturing methods. With additive manufacturing, manufacturers can produce tools directly from digital models. This process minimizes waste, as only the material needed is used.
Moreover, additive manufacturing facilitates rapid prototyping. Engineers can quickly design and test new tool configurations without the lengthy production times associated with conventional methods. This agility is vital for staying competitive in a fast-paced manufacturing environment. The ability to customize tools efficiently also enhances adaptability, meeting various industry requirements with ease.
Enhanced Materials
The development of enhanced materials is crucial for the next generation of deep drawing tools. Manufacturers are increasingly utilizing advanced alloys and composites that offer superior strength, durability, and thermal resistance. These materials can withstand the extreme conditions of deep drawing processes, such as high pressures and abrasive wear.
By incorporating enhanced materials, manufacturers can reduce tool wear and increase their lifespan. This improvement leads to lower maintenance costs and less downtime due to tool replacements. Furthermore, innovative coatings can improve material properties, such as reducing friction or enhancing corrosion resistance. These advancements ensure that tools maintain peak performance even in challenging production environments.
"The integration of advanced materials in deep drawing tools is critical for improving efficiency and product quality."
In summary, advancements in deep drawing tool technology are pivotal for enhancing productivity and quality in manufacturing. The integration of computer-aided design, additive manufacturing, and the use of enhanced materials not only improves the performance of tools but also aligns with the modern needs of the industry. Understanding these trends empowers professionals to make informed decisions that can lead to more efficient and effective manufacturing processes.
Future Trends in Deep Drawing Tools
Future trends in deep drawing tools significantly shape the manufacturing landscape. As industries demand more complex shapes and improved efficiency, the evolution of deep drawing technologies is critical. By examining these trends, professionals can better prepare for upcoming challenges and opportunities in the sector.
Sustainability Practices
Sustainability has become a key concern in manufacturing. The incorporation of recyclable materials and waste reduction methods improves the environmental impact of deep drawing processes. Companies are exploring how to minimize the carbon footprint associated with tool production. For example:
- Use of renewable energy sources in manufacturing plants.
- Development of tools that generate less waste during production.
- The adoption of materials that can be recycled efficiently.
The shift towards sustainable practices not only helps the environment but also enhances the brand image of manufacturers, appealing to conscious consumers and investors alike.
Smart Tooling Solutions
Technological advancements are leading to the rise of smart tooling solutions. These tools utilize sensors and data analytics to enhance operational efficiency. There are various benefits to integrating smart technology into deep drawing tools:
- Real-time monitoring: Sensors can track performance metrics, allowing for immediate adjustments.
- Predictive maintenance: Data analysis can predict tool wear, reducing downtime.
- Increased precision: Smart features enable more accurate adjustments during the forming process.
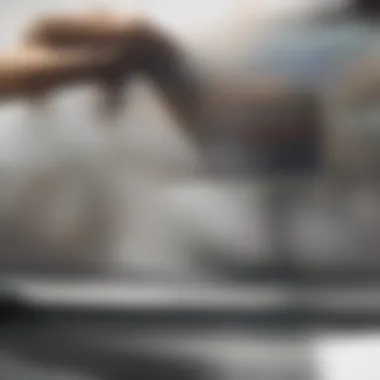
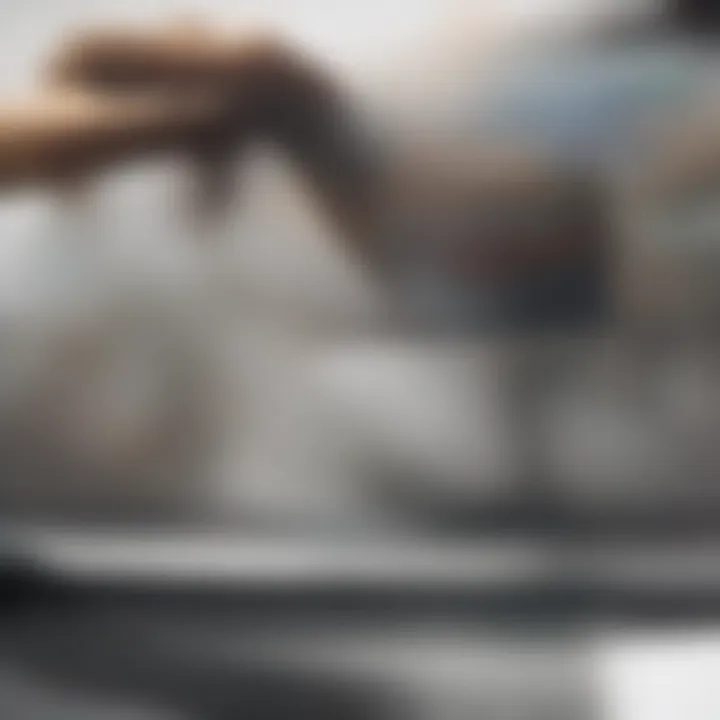
Such innovations help manufacturers reduce costs and improve product quality, aligning well with industry demands.
Industry 4. Implications
The concept of Industry 4.0 encapsulates the digital transformation of manufacturing. Deep drawing technologies are benefitting from this shift, leading to several noteworthy implications:
- Automation: Increasing reliance on robotics to handle repetitive tasks improves efficiency and reduces human error.
- Data integration: The use of IoT devices allows for seamless data sharing between tools, enhancing decision-making processes.
- Customization: Greater flexibility in production processes allows manufacturers to cater to specific client needs easily.
Embracing these Industry 4.0 changes can provide competitive advantages in a market that increasingly values speed and adaptability.
As manufacturing evolves, staying attuned to these trends is essential for anyone involved in deep drawing processes. Innovations in sustainability, smart tooling solutions, and Industry 4.0 are not just enhancements; they are necessities for future success.
Case Studies: Successful Implementations
Understanding case studies in the context of deep drawing tools is essential for comprehending their practical application in various industries. These case studies provide real-world insights into the benefits and challenges of using these tools. They highlight how companies have successfully integrated deep drawing processes into their manufacturing lines to produce complex metal components efficiently. By examining specific implementations, we can extract valuable lessons about optimization, cost-effectiveness, and innovation in deep drawing.
The significance of case studies for manufacturers and researchers cannot be overstated. Through detailed analysis of successful projects, stakeholders gain a clearer picture of best practices, common pitfalls, and the strategic advantages of employing advanced deep drawing techniques. This exploration also allows one to assess the full scope of potential applications across different sectors.
One key advantage of studying successful implementations is the opportunity to learn from actual scenarios rather than theoretical models. These insights can guide future projects and help companies avoid costly mistakes. Moreover, they underscore the need for continuous improvement and adaptation in manufacturing processes.
"The true learning in manufacturing comes from case studies that illuminate the path of innovation and practical application."
Automotive Part Production
Automotive manufacturers heavily rely on deep drawing techniques to create precise and robust components such as body panels and structural parts. The case of Ford Motor Company serves as an illustrative example. They implemented specialized deep drawing tools that allowed for the high-volume production of complex shapes with improved quality consistency.
The choice of advanced materials and sophisticated dies enabled Ford to significantly reduce production time while enhancing structural integrity. Additionally, precision in the design and execution processes has led to reductions in waste and lower costs, demonstrating the effectiveness of deep drawing in automotive manufacturing.
Key elements from this case include:
- The use of advanced materials like high-strength steel, which benefits the shaping process.
- The integration of automated systems that streamline production and enhance precision.
- Continuous monitoring of the drawing process to mitigate challenges such as material thinning and defects.
By leveraging deep drawing tools effectively, Ford exemplifies how automotive manufacturers can balance efficiency and quality in a competitive market.
Electronic Component Fabrication
In the realm of electronic components, companies like Apple Inc. have harnessed deep drawing processes to produce intricate parts required for devices. Precise fabrication of components like housings and enclosures is critical to the functionality and aesthetics of electronic products. In Apple's case, employing aluminum deep drawn enclosures has provided both durability and lightweight characteristics that are crucial for modern portable devices.
Apple's focus on sustainability also illustrates the broader implications of deep drawing in electronics. By utilizing recycled aluminum and optimizing the production process, the company achieves environmental goals while maintaining high-quality standards.
Important aspects of this case study include:
- Commitment to using sustainable materials, enhancing the company's eco-friendly profile.
- Advanced tool designs that allow for the efficient production of complex shapes required for compact devices.
- Deployment of quality control measures during production to eliminate defects and ensure durability.
The case of Apple represents how deep drawing tools not only meet production goals but also align with contemporary values around sustainability and innovation in electronics.
In-Depth Analysis of Deep Drawing Tool Selection
The selection of deep drawing tools is a critical aspect in the manufacturing process. Tools such as punches, dies, and blank holders each play a vital role in how efficiently and effectively a product is made. Understanding what to consider when selecting these tools can greatly affect productivity, final product quality, and overall costs.
Choosing the right tools involves not just matching tools to the design but also evaluating their materials, manufacturing methods, and how they will be maintained over time. This section will delve deeper into specific elements influencing tool selection, their benefits, and relevant considerations.
Criteria for Selection
When selecting deep drawing tools, several criteria come into play:
- Material Compatibility: The tool materials should be compatible with the workpiece material. For instance, if the workpiece is aluminum, the tool must withstand the drawing process without causing defects.
- Geometric Design: The design of the tool must match the shape and complexity of the final product. This requires precise engineering to ensure that the resulting shape meets specifications without flaws.
- Durability and Wear Resistance: Tools undergo significant stress during production. Selecting tools made from high-quality, wear-resistant materials ensures longevity and reduces the frequency of replacements, thus saving costs in the long run.
- Cost-Effectiveness: The initial investment in tools must be weighed against expected returns in production efficiency and product quality. This analysis includes both upfront costs and expected lifecycle expenses.
- Production Volume: High-volume production may justify the need for custom tools, while lower volumes might require more generic solutions. The selected tool should align with the production forecast to optimize resources.
These criteria help manufacturers ensure that they are choosing the most suitable tools for their specific applications.
Cost Analysis
Cost analysis is essential in determining the feasibility of deep drawing tool selection. The total cost encompasses several factors:
- Initial Investment: The upfront cost of purchasing tools can vary widely, influenced by the type and complexity of the tool.
- Operating Costs: These include factors such as energy consumption, maintenance frequency, and the time required for setup and changes between jobs.
- Cost of Tooling Changes: In production environments, changes to tooling can lead to downtime. An analysis should factor in potential losses from halted production.
- Quality of Output: Investing in higher-quality tools often results in fewer defects and reworks, which can significantly reduce costs in the entirety of the production process.
Manufacturers must conduct detailed cost assessments to find a balance between initial investment and ongoing expenses. This detailed analysis ensures that the selected tools provide value throughout their operational lifespan.
Understanding the nuances of tool selection not only streamlines the production process but also enhances the overall quality of manufactured products.
Culmination and Summary
In this article, the exploration of deep drawing tools highlights their crucial role in manufacturing processes. Understanding these tools extends beyond mere definitions; it encompasses the grasp of their types, materials, and design considerations that significantly impact production efficiency and quality. By focusing on deep drawing, industries can achieve unique component shapes that fulfill specific functional needs.
The key benefits discussed in this article include enhancing production efficiency, improving product quality, and minimizing costs. Proper selection of tools contributes to reducing material waste and maintaining tolerances, which are essential for high-precision applications. Moreover, addressing challenges like material thinning and wrinkling is vital β as they can hinder successful outcomes in deep drawing processes.
The insights shared throughout indicate that advancements in technology, such as computer-aided design integration and smart tooling solutions, are transforming traditional practices. These innovations pave the way for sustainability in manufacturing, which is becoming increasingly essential in today's industry landscape.
"A comprehensive understanding of deep drawing tools enables manufacturers to exploit their full potential in crafting complex components."
As we synthesize the information presented, it is clear that a meticulous approach to tool selection and process management is critical for success in deep drawing. This article serves as a foundational guide for students, researchers, educators, and professionals looking to deepen their knowledge and enhance their practical skills in this specialized area of manufacturing.
Recap of Key Insights
- Types of Tools: Different tools like punches, dies, and blank holders play instrumental roles in shaping materials.
- Material Selection: The choice of tool materials, such as tool steels and coatings, can significantly affect durability and performance.
- Design Considerations: Geometric design principles and tolerance assessments are essential for optimizing the deep drawing process.
- Challenges: Common issues like material thinning and wrinkling require strategies for prevention and mitigation.
- Technological Advancements: Innovations in CAD and additive manufacturing techniques are redefining how tools are designed and implemented.
Final Thoughts
Understanding deep drawing tools is not only beneficial but necessary for those aiming to thrive in the manufacturing sector.