Understanding the Copper Smelting Process: A Detailed Guide
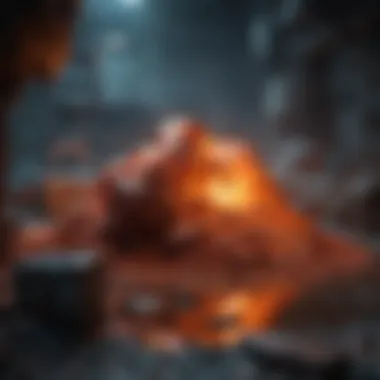
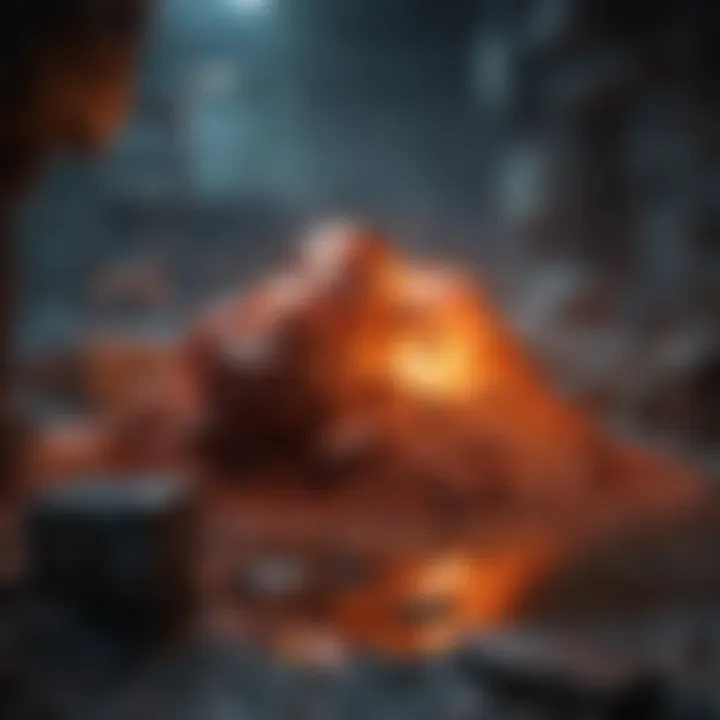
Intro
Copper smelting is not merely a technical process; it is the beating heart of metallurgy with profound implications for modern industry and technology. It is a crucial procedure that takes the raw materials from the earth and transforms them into one of the most crucial metals in various applications. Throughout history, copper has been used for making tools, coins, and electrical wiring because of its durability and excellent conductivity.
The journey from copper ore to usable copper metal involves numerous stages, each with its own intricate details and importance. Understanding the copper smelting process is vital for anyone engaged in the field, as it encompasses historical techniques that have paved the way for today’s advancements, whilst also addressing pressing environmental concerns associated with the industry.
The aim here is to dissect each aspect of this multifaceted process, providing insights into both the technical and the pragmatic elements involved. By delving deep, readers will grasp the relevance of copper smelting not only in metallurgical contexts but also in broader economic and environmental frameworks.
Key Findings
- Major Results: The copper smelting process is governed by a series of chemical reactions that convert ores into pure metal, effectively revealing the complexity of chemical metallurgy. A variety of furnaces and technologies such as flash smelting, are pivotal to optimizing efficiency in ore processing. As a result, this sector has progressively moved towards more sustainable practices to mitigate environmental impact.
- Discussion of Findings: The balance between traditional methods and modern technologies showcases a landscape that is constantly evolving, often blending the old with the new to ensure both productivity and sustainability. Through this article, readers will see the challenges faced in terms of resource management and ecological preservation, alongside the innovations that address these issues.
The findings present a layered understanding of copper smelting, illuminating its significance and offering a focused lens through which to examine the state of the industry. The exploration of historical methods alongside contemporary advancements reveals a narrative that is both rich in detail and forward-looking, setting the foundation for further discussion on the potential future of copper smelting.
A thorough understanding of the copper smelting process is integral to not only appreciating metallurgy's historical context but also the direction it is heading towards in response to contemporary challenges.
Methodology
- Research Design: This article employs a qualitative research design, which is essential for discussing the intricate details of the smelting process. Through literature reviews, case studies, and expert interviews, the article maps the historical evolution and modern techniques in this field.
- Data Collection Methods: Information was gathered from reputable sources including academic papers, industry reports, and interviews with professionals in metallurgy. Online resources, such as those available on Wikipedia and Britannica, provided a foundational understanding of both historical contexts and modern advancements in the copper smelting process.
Prolusion to Copper Smelting
Copper smelting stands as a cornerstone of the metallurgical industry, playing a crucial role in the transformation of copper ores into pure, functional metal. This process is not merely an industrial operation; it encapsulates centuries of technological advancement, cultural significance, and economic mechanics that directly impact modern society. Understanding copper smelting requires diving into its historical roots and recognizing the essential role copper plays in various industries today.
Historical Context
Copper has been a vital resource since the dawn of civilization. The first known uses date back to around 9000 BCE, when ancient peoples began utilizing native copper for tools and ornaments. As civilizations advanced, the methods of extracting and refining copper evolved remarkably, leading to the development of smelting techniques. Early smelting operations were primitive by today’s standards; they typically included small furnaces made from clay or stone that utilized charcoal to heat copper ores. Over time, these techniques became more sophisticated.
The advent of the Bronze Age, characterized by the alloying of copper with tin, marked a turning point in metalworking. It was during this era that systematic smelting practices emerged. Archaeological sites across the Middle East and Europe have revealed remnants of large-scale smelting operations, indicative of the increasing demand for copper ores.
By the 19th century, industrialization signified a new chapter in copper smelting. The introduction of processes like the Bessemer method revolutionized the industry and significantly increased copper production capacity. Such advancements allowed for greater efficiency, paving the way for the widespread use of copper in electrical applications and other high-tech industries. Understanding this historical context is crucial; it illustrates how current practices have built upon the lessons and failures of the past.
Importance of Copper in Industry
Copper is often referred to as the backbone of modern industry, and for good reason. This versatile metal is renowned for its excellent conductivity, malleability, and resistance to corrosion. These properties make copper indispensable in several sectors, including:
- Electrical Systems: Copper wiring is fundamental in power generation, transmission, and in various electronic devices.
- Construction: Copper plumbing and roofing materials are valued for their durability and resistance to weathering.
- Automotive: The automotive industry relies heavily on copper for electrical connections and components.
- Renewable Energy: With the rising focus on sustainable energy, copper plays a vital role in solar panels and wind turbines.
In a world increasingly leaning on technology and sustainable solutions, the demand for copper shows no signs of slowing down. As such, understanding copper smelting not only provides insight into how this metal is produced but also highlights the importance of sustainable practices in the industry. As we progress through this exploration, the narrative around copper smelting will reveal both the challenges faced in its production and the environmental considerations that are now at the forefront of the industry.
"Copper is a metal that, much like the veins in our bodies, connects various sectors, powering and supporting our technological growth."
The above understanding heightens the relevance of the copper smelting process, bridging the gap between historical techniques and modern industrial demands.
Copper Ore Sources and Composition
Copper ore plays a pivotal role in the copper smelting process. Understanding the various sources and the specific composition of copper ores not only lays the groundwork for effective processing but also highlights the challenges and opportunities in the ever-evolving landscape of metallurgy. The selection of ores directly influences the efficiency and outcome of smelting, making this knowledge essential for students, researchers, and industrial professionals alike.
Overview of Copper Ores
Copper ores are found abundantly in various geological formations across the globe. They are generally classified into two main types: sulfide ores and oxide ores.
- Sulfide Ores: These contain copper in a combined state with sulfur. Major examples include chalcopyrite, bornite, and chalcocite. Sulfide ores are crucial as they usually yield higher copper content than their oxide counterparts. Their extraction often requires extensive treatment due to the presence of additional elements and compounds.
- Oxide Ores: These ores comprise copper combined with oxygen; malachite and azurite are prime examples. While they typically have lower copper concentrations, they can be more straightforward to process. Oxide ores present unique extraction techniques, often involving leaching processes.
The geographical distribution of copper ores varies, with significant deposits found in countries like Chile, the US, and Australia, each contributing uniquely to the global supply chain. For instance, the Grasberg mine in Papua, Indonesia, stands out as one of the largest copper and gold mines in the world, driving significant economic activity in the region.
Chemical Composition of Copper Ores
The chemical makeup of copper ores is shaped by their mineral structure. The most critical component is, of course, copper, but it's essential to consider the other elements and materials present, which can affect processing techniques:
- Copper Content: The percentage of copper in the ore can differ significantly, affecting the smelting approach. Higher copper content means more efficient processing.
- Impurity Elements: Ores often contain impurities such as iron, arsenic, lead, and sulfur. These elements can influence both the quality of the smelted copper and the environmental efficacy of the smelting process. For instance, high levels of sulfur can lead to more sulfur dioxide emissions during smelting, necessitating more rigorous emission controls.
- Additional Minerals: Other minerals can affect not only copper extraction but also the resultant alloy's characteristics. Exposure to these elements can change the physical and chemical properties of the copper produced, impacting market value.
Understanding the nuances of these compositions allows processors to optimize methods for extraction and treatment accordingly.
"The extraction of copper from various ores is a balance between maximizing yield and minimizing environmental impact. Each source demands a unique approach, reflective of its individual characteristics."
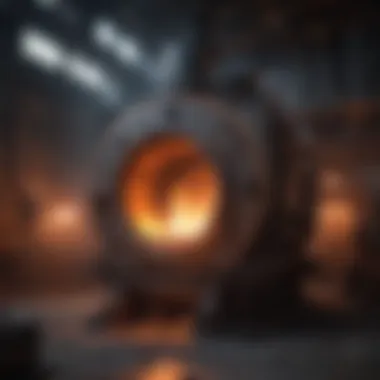
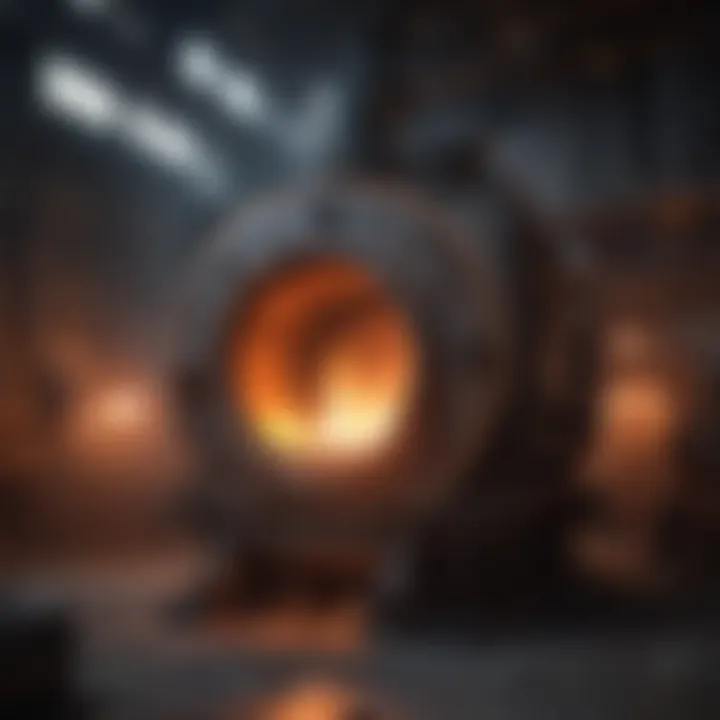
This intricate interplay between the source and chemical makeup of copper ores underscores their significance in the smelting process, guiding both current practices and future innovations in the copper industry.
Initial Processing Techniques
The initial processing techniques play a significant role in the copper smelting process. They set the stage for how effectively the copper can be extracted from its ore, influencing not just the yield but also the efficiency and economic viability of the entire operation. Understanding these early steps is essential for those interested in metallurgy, engineering, and environmental science, as they encompass both the physical and chemical transformations that copper ore undergoes before reaching the smelting furnaces.
Crushing and Grinding
Crushing and grinding are the first steps in the initial processing of copper ore. These processes are critical for liberating the copper minerals from the waste rock, a task akin to breaking down a tough nut to get to the seed inside. During crushing, large ore chunks are reduced to smaller pieces using heavy machinery such as jaw crushers or gyratory crushers.
Once the ore is crushed, the grinding process follows, which further reduces the size of the minerals. Grinding is often performed in mills, which can be either rod mills or ball mills. This two-pronged attack not only increases the surface area of the copper minerals but also prepares them for the subsequent concentration processes.
"The liberation of valuable minerals from waste materials is the cornerstone of effective processing."
A few critical points about crushing and grinding include:
- Energy Consumption: Both crushing and grinding are energy-intensive processes. Careful selection of machinery and optimization of these stages can greatly reduce energy consumption and associated costs.
- Size Distribution: Effective grinding ensures that the particles achieved a size suitable for flotation or other concentration methods. If the particles are too large, the recovery rates drop.
- Wear and Tear: Milling equipment can face significant wear from the continuous motion and the abrasive properties of the ore. Regular maintenance and advancements in grinding technology can mitigate these issues.
Concentration Methods
Following crushing and grinding, the next natural step is the concentration of the copper minerals. This step serves to increase the copper content of the ore and is often vital for enhancing the economic viability of mining operations. Concentration methods typically hinge on the properties of the minerals in the ore, such as their density, hydrophobicity, and magnetic characteristics.
Several methods are employed in this stage, including:
- Flotation: This is the most widely used method where crushed and ground ore is mixed with water, and chemical reagents are added to create a froth. The copper minerals attach to air bubbles and float to the surface, allowing them to be skimmed off.
- Gravity Separation: Utilizing differences in density, this method separates heavier copper minerals from the lighter waste material. It often uses equipment like jigs and spirals.
- Magnetic Separation: Though less common in copper processing, if magnetic minerals are present, they can be efficiently separated using magnetic fields.
The choice of concentration method directly influences the overall recovery rate, cost, and environmental impact. The aim is always to maximize the yield of copper while minimizing losses and environmental degradation, which is crucial for sustainable mining practices.
In summary, the initial processing techniques—crushing, grinding, and the various concentration methods—lay the groundwork for a successful copper smelting process. Each step is interconnected, with efficiency in one area leading to better outcomes in the next. Understanding these foundational processes helps illuminate the complexities of refining copper into a usable metal.
The Smelting Process
The smelting process has a crucial role in the transformation of copper ore into a form that is applicable for various industrial uses. It involves a series of intricate steps that separate the metal from its ore, which is not only technically fascinating but also significant for the economic value of the metal. By understanding these steps, one gains insight into the efficiency and effectiveness of copper extraction and the environmental impacts associated with it.
Copper smelting is a vital industrial operation that not only impacts the production of copper but also has wider implications for the economy. The extraction stages, from ore to metal, are optimized to ensure maximum yield with minimal waste. The process fundamentally relies on a combination of heat and chemical reactions to separate metals from the unwanted elements found in the ore.
Roasting
Roasting is typically the first stage of the smelting process, where finely crushed copper ores are subjected to high temperatures in the presence of oxygen. This step is crucial as it helps in reducing the sulfur content of the ore, forming sulfur dioxide gas in the process. This gass can be captured and processed to comply with environmental regulations.
At its core, roasting serves multiple purposes:
- Oxidation: The main aim of roasting is to oxidize sulfide minerals, which changes them into oxides that are easier to reduce in subsequent phases.
- Removal of Volatile Compounds: Heating the ore allows certain volatile materials to escape, which may otherwise interfere with the purity of the final copper product.
- Preparation for Melting: This process prepares the ore for the melting stage by making it easier to subsequently extract copper.
Roasting can decrease the amount of energy required in later steps of the smelting process, ultimately enhancing efficiency.
Melting
Following roasting, the next step is melting, where the roasted ore is mixed with a flux in a furnace that can reach extremely high temperatures. During this phase, the materials are heated until they reach a molten state. The flux, typically made up of silica or limestone, plays an essential role by helping to separate the molten metal from impurities, creating what is often termed as 'slag'.
The melting stage is notable for its multiple benefits:
- Separation of Metal and Slag: The intended copper sinks to the bottom of the furnace, while the lighter slag floats on top, ready for removal.
- Efficiency of Heat Usage: Modern furnaces are designed to make the most out of the heat generated, ensuring a quick melting process that minimizes energy loss.
- Enhanced Quality of Product: By achieving high temperatures, impurities are largely eliminated, yielding high-quality copper.
Reduction Reactions
In the reduction phase, the challenge is to convert the copper oxides present in the material back into metallic copper. This is often achieved through the introduction of a reducing agent, which could be carbon or other similar materials, into the molten mix. The chemistry of this process is fascinating, as it involves intricate reactions:
- Copper(I) Oxide Reduction: The reduction of copper(I) oxide is a vital reaction that converts Cu2O back to copper metal.
- Formation of Carbon Dioxide: As carbon reacts with oxygen from the copper oxides, carbon dioxide is produced, which escapes into the atmosphere, further purifying the copper.
- Temperature Control: Careful regulation of temperature and reducing agent concentration is essential to optimize the reactions and achieve the desired output.
Mastering the reduction reactions is not just about obtaining the metal; it directly affects the overall yield and quality of the copper produced, which can significantly influence market dynamics and industry practices.
Key Equipment in Copper Smelting
Copper smelting is a blend of art and science, where raw minerals undergo precise transformations. The equipment used in this process is not just tools; they are the backbone of efficiency and effectiveness. The choice of machinery dictates the quality of the output, energy consumption, and overall operational costs.
Furnaces
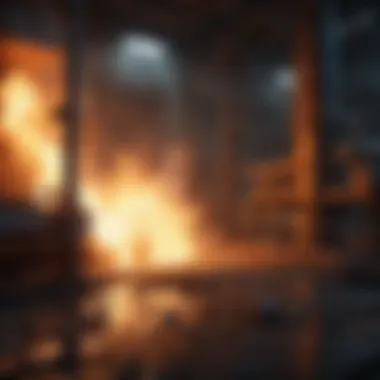
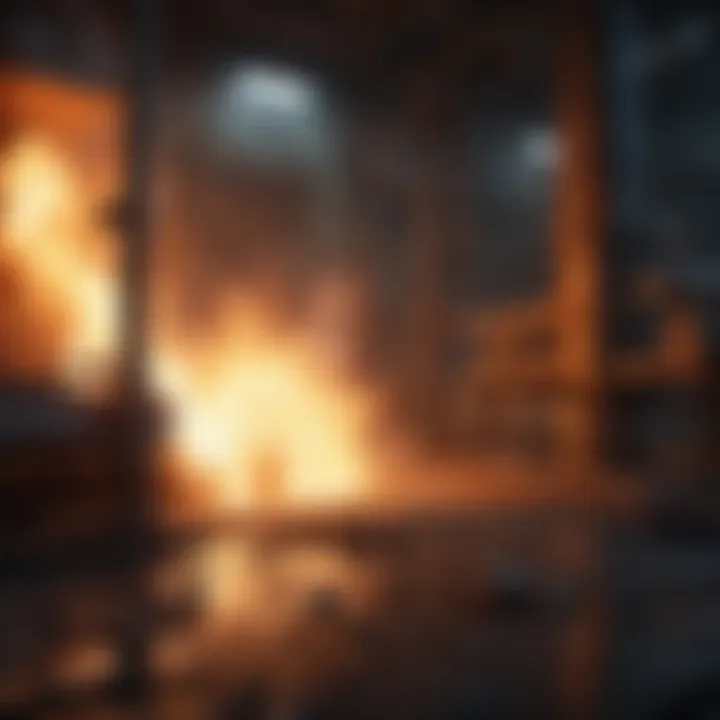
Furnaces are the heart of copper smelting operations. They are where the initial transformation happens, melting ore to separate the copper from other materials. There are several types of furnaces, each with its own set of advantages and operational characteristics.
Types of Furnaces
The key characteristics of furnaces can greatly influence their selection. For instance:
- Blast Furnaces: These are commonly used due to their ability to handle large quantities of ore and produce a high output of molten copper. Their robust design makes them suitable for continuous operations.
- Flash Furnaces: A unique feature here is that they inject ore into a hot gas stream, allowing for rapid heating and transformation. This option consumes less energy but may have limitations on raw material inputs.
Choosing the right type of furnace can enhance efficiency and reduce costs, making them popular choices in the industry. Understanding the specific operational requirements and characteristics of each furnace type is essential for optimizing the smelting process.
Operational Principles
Operational principles vary with furnace types, but some core elements remain constant. The basic functioning involves:
- Heating through combustion: Utilizing fuel to generate the required temperature.
- Controlled atmospheric conditions: Managing levels of oxygen and other gases to facilitate the chemical reactions necessary for extracting copper.
One key characteristic here is temperature regulation. Maintaining precise temperatures ensures the effective melting of ore without damaging the copper’s quality. This kind of control can be either an advantage or disadvantage, depending on the furnace type used.
Cooling Systems
Cooling systems are crucial in managing the heat generated during smelting. They ensure that the process remains safe and efficient. Various methods, such as water cooling and air cooling, are employed based on the furnace type and operational needs. Effective cooling prevents overheating, which can lead to equipment failure or safety hazards.
Understanding the balance between heat generation and cooling is vital. Too much heat can jeopardize the integrity of the copper, while inefficient cooling can lead to operational downtime. As such, investing in appropriate cooling systems not only maintains a stable working environment but also enhances overall productivity.
Environmental Considerations
Understanding the environmental impact of copper smelting is crucial in today's industrial landscape. This section digs into how the smelting process not only alters the natural world but also highlights the approaches the industry takes towards minimizing its footprint. Considering the intricate relationship between economic growth and ecological health, addressing these environmental concerns is not just beneficial—it’s imperative for the sustainable development of the copper industry.
Emissions and Pollution
Copper smelting comes with its share of challenges, especially concerning air and water pollution. The process releases a concoction of compounds into the atmosphere, including sulfur dioxide—a notorious player in creating acid rain. The unfortunate consequence is that these emissions can lead to significant ecological damage. In the vicinity of smelting plants, heavy metals such as arsenic and lead often find their way into both soil and waterways, posing health risks to local communities and ecosystems alike.
Measuring these emissions is essential. Many firms now utilize scrubber technologies to mitigate the release of harmful substances. These systems work by chemically absorbing pollutants before they escape into the atmosphere.
Some industry leaders have made strides towards reducing their ecological footprint by adopting cleaner technologies, yet challenges remain. Regulations often fluctuate, and not every facility complies with the strictest standards. This disparity points to the need for a unified approach towards emission control and environmental responsibility within the copper smelting sector.
"It’s crucial to balance economic pursuits with environmental safeguards. The health of our planet relies heavily on this equilibrium."
Sustainable Practices
In response to growing concerns regarding environmental degradation, the copper smelting industry is gradually shifting towards more sustainable practices. Recycling and reusing materials are at the forefront of this movement. Much of the copper smelting today incorporates recycled copper scrap, which demands significantly less energy compared to smelting copper from virgin ores.
The concept of circular economy is gaining traction, weaving sustainability into the very fabric of industrial processes. Here are some sustainable practices being explored:
- Waste Reduction: Lowering the volume of waste generated during the smelting process is a priority. Techniques such as optimizing the ore blending process can lead to improved yields and reduced waste.
- Water Management: Implementing advanced recycling systems within facilities allows for the reuse of water, thus decreasing the total demand on local resources.
- Alternative Fuels: Some smelting operations are researching the viability of using alternative fuels, such as biofuels, which can lead to fewer carbon emissions than traditional fossil fuels.
Quality Control and Assessment
Quality control and assessment play a crucial role in the copper smelting process. The essence of this topic lies in ensuring that the final product meets both industry standards and customer expectations. Without a robust quality control system, the smelting process could result in subpar copper that fails to serve its intended purpose, leading manufacturers to incur significant financial losses. Beyond monetary implications, poor quality metal can pose risks in various applications, particularly in construction, electronics, and motors—areas where copper is relied upon for its conductivity and durability.
The benefits of implementing stringent quality control methods are manifold. Firstly, by identifying impurities during the smelting process, companies can prevent contaminated copper from reaching the market. Secondly, consistent quality assessment can minimize waste, enhancing efficiency in production. Finally, maintaining high-quality standards not only builds trust among clients but can also lead to a competitive edge in the market.
Some considerations when addressing quality control within copper smelting include the precision in monitoring raw materials, the execution of various testing methods, and the compliance with established copper quality standards. The intricate relationship between these components underscores the importance of a meticulous approach throughout the smelting process.
Testing Methods
Quality assessment in copper smelting heavily relies on various testing methods aimed at determining the properties of copper and the presence of contaminants. Common techniques deployed include:
- Spectroscopy: This method is pivotal for analyzing the elemental composition of copper samples. Techniques such as atomic emission spectroscopy or X-ray fluorescence can provide detailed information on the metal's purity levels.
- Chemical Analysis: Conducting chemical tests helps in identifying specific impurities present in the copper. For example, certain assays can pinpoint traces of lead or arsenic—elements detrimental to copper's quality.
- Mechanical Testing: These tests involve assessing the physical properties of the copper, including tensile strength and ductility. Understanding the mechanical characteristics ensures that the metal can withstand the demands of its end application.
Monitoring these properties throughout the smelting process allows for timely interventions, ultimately safeguarding the quality of the final product.
Standards for Copper Quality
Adherence to established standards for copper quality is pivotal in ensuring both safety and consistency within the industry. Organizations like ASTM International and the International Organization for Standardization (ISO) provide guidelines that outline acceptable levels of purity and performance criteria for copper products.
Key standards include:
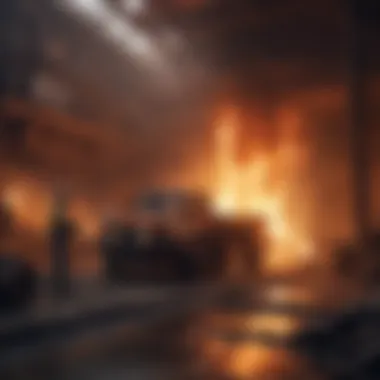
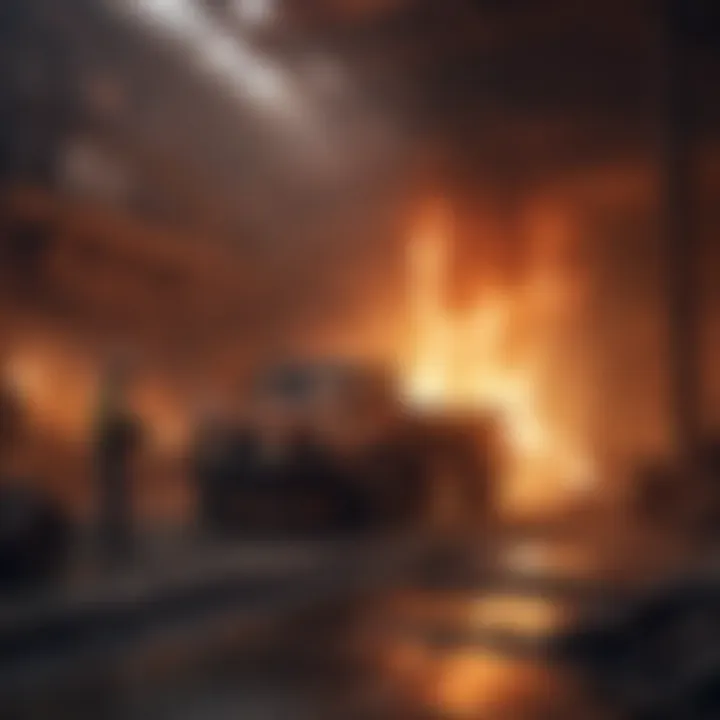
- ASTM B170: Specifies copper’s purity levels, delineating the acceptable percentage of copper versus impurities.
- ISO 2211: Focuses on the mechanical testing of copper and its alloys, emphasizing the material's performance in industrial applications.
In many regions, compliance with these standards isn’t merely a best practice—it's legally required to ensure safety and quality in metal production.
Maintaining these standards facilitates smooth trading across borders, as buyers can be assured of uniformity in the copper they source. Regular audits and inspections help in sustaining compliance, ultimately benefiting both producers and consumers in the global copper market.
Modern Advancements in Copper Smelting
The field of copper smelting has seen significant advancements in recent years. These enhancements are crucial, not just for improving efficiency but also for addressing the growing concerns surrounding environmental sustainability. With the increasing demand for copper across industries, the push for modern methods that yield better results while minimizing ecological footprints has never been more pressing. This section will delve into two specific areas: innovative technologies that are reshaping the smelting landscape and the automation processes that are becoming integral to modern operations.
Innovative Technologies
Advancements in technology have radically transformed the copper smelting process. One standout example is the introduction of flash smelting, which stands out for its efficiency. This method, pioneered in the late 20th century, allows for the direct processing of copper concentrates using less energy than traditional methods. Flash smelting not only increases overall copper recovery rates but significantly reduces air emissions associated with the process.
Moreover, the use of oxygen-enriched air instead of regular air in the combustion process enhances the overall temperature and efficiency of the operation. This innovative approach cuts down on the sulfur dioxide emissions, which are a major concern in traditional smelting and can lead to severe environmental repercussions.
Another noteworthy technology is the use of bioleaching, which employs certain bacteria to extract copper from its ore. This technique can be more environmentally friendly, as it reduces the need for high-energy processes and chemicals. While still not mainstream, it represents a step away from conventional practices and acknowledges environmental consciousness.
"Technological innovation in copper smelting is critical not only for maintaining competitive advantage but also for aligning with sustainability goals crucial to our future."
Automation in Processes
As copper smelting facilities strive for higher efficiency, automation has emerged as a key player. The integration of smart systems into smelting operations determines optimal conditions in real-time, ensuring that every aspect from temperature control to material feed rates is expertly managed. This results in not just consistent quality but also increased throughput.
Robotics also play an essential role, especially in tasks that are hazardous to human workers. Automated machinery is now capable of handling molten metal and other dangerous materials, reducing injury rates and enhancing workplace safety. These innovations lead to less downtime and improved productivity. Moreover, data-driven analytics provide insights that can lead to proactive maintenance of equipment, thus avoiding costly breakdowns.
Additionally, companies are exploring the implementation of artificial intelligence in decision-making processes. AI can analyze vast quantities of operational data to suggest improvements or alert personnel to any inefficiencies that may arise. By employing these modern processes, the copper smelting industry can not only adapt to current demands but also anticipate future challenges.
Future Challenges in the Copper Industry
The copper industry stands at a crossroads, grappling with numerous challenges that could influence its future. As the global demand for copper rises – driven by its pivotal role in everything from electrical systems to renewable energy – the industry faces pressing issues that go beyond mere production. Understanding these challenges is crucial for stakeholders, as they hold significant ramifications for economic stability, technological advancements, and environmental responsibility.
Through this section, we will explore the complexities surrounding resource depletion and sustainability as well as the ever-changing market dynamics that shape the global copper landscape.
Resource Depletion and Sustainability
Copper is not a limitless resource. Over the years, intensive mining and processing has led to significant depletion of easily accessible copper ores. As high-grade ores dwindle, mining companies are forced to excavate lower grade ores or explore deeper into the Earth, which complicates the extraction process and increases operational costs.
But it’s not just about the quantity available. Sustainability in mining practices has become an essential talk in the boardrooms. Additionally, the need to align with environmental regulations has led the industry to rethink its operational strategies. Some key points around this challenge include:
- Increased Extraction Costs: Methods such as open-pit and underground mining are becoming more resource-intensive, leading to higher costs per ton of extracted copper.
- Environmental Footprint: Mining activities can leave lasting scars on the landscape, affecting local ecosystems and water supplies. This has spurred a recent shift towards more sustainable practices.
- Recycling Efforts: To counteract depletion, industries are emphasizing the recycling of copper, as scrap metal can often provide quality copper without the extensive environmental costs associated with mining.
"In view of the increasing demand for copper and its finite resources, finding effective recycling methods becomes all the more crucial. Recycling offers a viable path forward, given its potential to decrease the reliance on mining."
As companies invest in sustainable practices and innovate recycling technologies, they might find a more balanced approach to meet the growing demand while preserving resources for future generations.
Market Dynamics and Global Influence
The copper market is a complex web of factors, ranging from economic trends to geopolitical tensions. These dynamics have a profound impact on pricing, availability, and ultimately the stability of the industry. Understanding these elements is vital:
- Global Economic Conditions: Economic booms and downturns can significantly influence copper demand. For instance, during periods of infrastructure spending, copper typically sees a surge in consumption. Conversely, recessions can lead to decreased demand, affecting prices and production levels.
- Geopolitical Factors: Political stability in copper-producing countries can directly influence output. Countries like Chile and Peru, major copper producers, can affect global supply through policy changes, strikes, or shifts in trade agreements.
- Technological Advancements: Emerging technologies can rapidly change the landscape. Innovations in extraction methods or processing could lead to more cost-effective solutions, easing some current market pressures.
Moreover, the increasing climate policies around the world are creating a ripple effect in the industry. Sustainable technologies are increasingly being viewed not just as beneficial but as essential to staying relevant in an evolving marketplace.
The future snap may not seem straightforward. However, those involved in the copper industry must keep their ears to the ground and adapt to shifting sands of resource management, market trends, and sustainability concerns. As we delve deeper into these issues, awareness will be key to ensuring a resilient and thriving copper economy.
Ending
The conclusion serves as the final word in our exploration of the copper smelting process, tying together the numerous threads woven throughout the article. This section emphasizes not only the significance of understanding copper smelting, but also the broader implications it holds for various sectors, including industry and environmental management. Having traversed the detailed stages of smelting, from the initial processing techniques to modern advancements, it is clear how critical this knowledge is for students, researchers, educators, and professionals alike.
Summary of Key Points
- Historical Context: We began by tracing the roots of copper smelting, revealing its evolution alongside human civilization.
- Technical Processes: We dissected the smelting process into digestible parts, exploring roasting, melting, and reduction reactions in detail.
- Environmental Concerns: It is crucial to acknowledge the balance between copper production and environmental sustainability. The impacts of emissions and the adoption of sustainable practices were explored comprehensively.
- Quality Assurance: Emphasizing the critical quality control measures, this section highlighted the techniques that must be adhered to in order to maintain high copper standards.
- Future Outlook: We discussed challenges facing the copper industry, stressing resource depletion and market fluctuations that threaten its sustainability.
This detailed examination of these key points demonstrates how interconnected the different stages and elements of copper smelting are, creating a holistic understanding of the process.
Implications for Future Research
Moving forward, several avenues beckon deeper investigation:
- Sustainable Technologies: Researchers should focus on the development of cleaner, more efficient methods in copper smelting to minimize environmental impacts. Innovations in reduction techniques and the introduction of alternative energy sources can mitigate pollution levels significantly.
- Economic Analysis: A thorough economic study on the cost-effectiveness of various smelting technologies, including automation, may yield crucial insights for industrial stakeholders.
- Resource Management: Understanding the long-term sustainability of copper sources is imperative. Exploration into the recycling processes of copper could reveal opportunities for resource conservation.
- Health Assessments: Future studies should also strive to evaluate the health impacts associated with copper smelting on workers and communities adjacent to smelting facilities, thereby enhancing workplace safety.
By addressing these topics, researchers can contribute to a more sustainable and economically viable copper industry, which will be of paramount importance in our ever-evolving world.